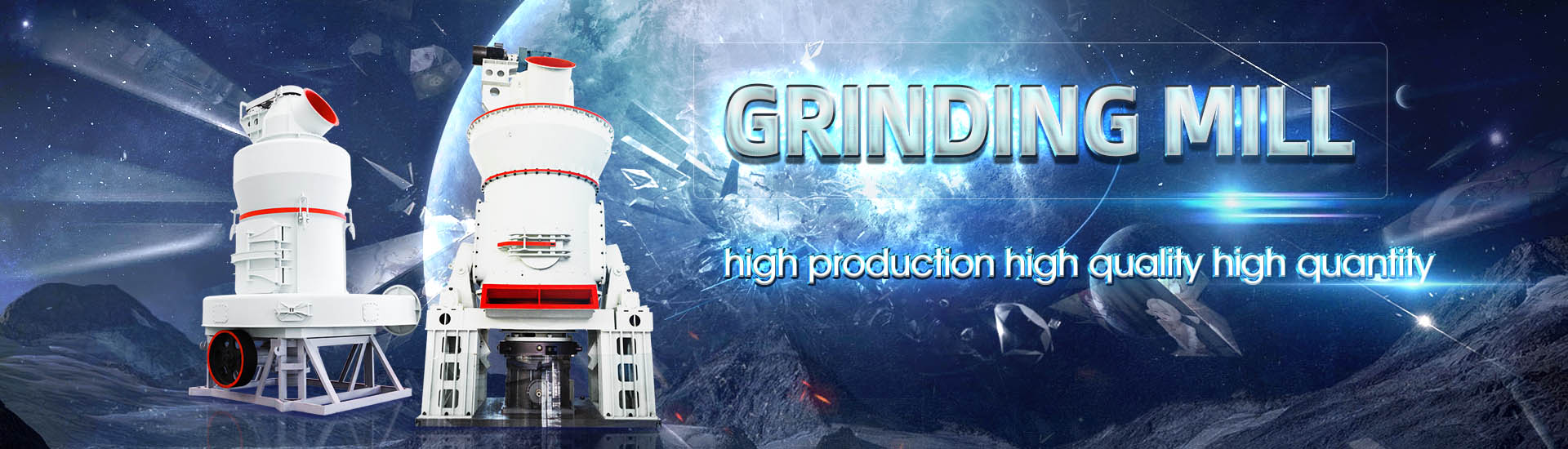
Slurry slag selfseparation mill
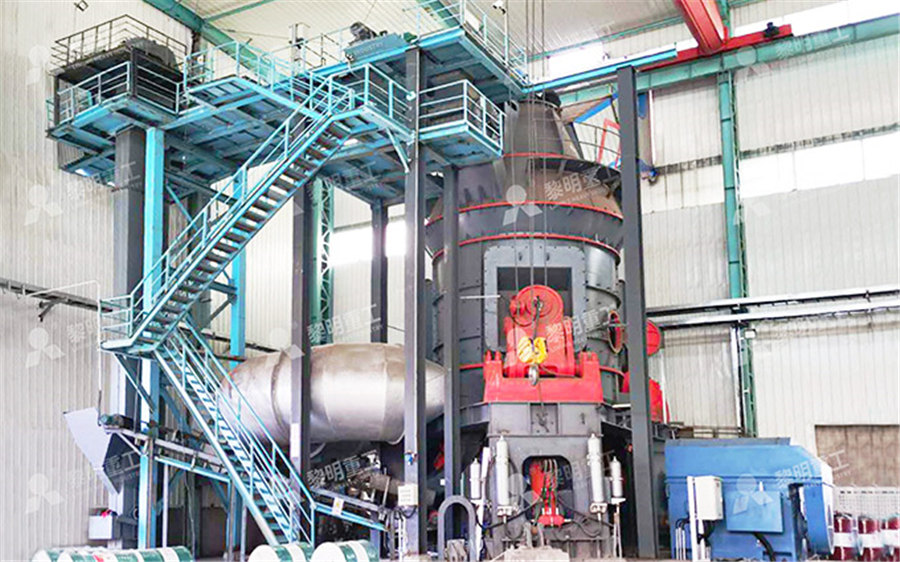
Influences of Ultrafine Slag Slurry Prepared by Wet Ball Milling on
The ultrafine slag slurry (UFSS) was obtained by the process of grinding the original slag in a wet ball mill, which was mixed in concrete directly The durations of grinding were 20 min, 40 min, 2020年11月18日 In the twostep mode, the slurry bearing the slag particles is first subjected to attrition under inert atmosphere and room temperature The slurry and grinding beads are then separated by screening, after which the Insights Into Nickel Slag Carbonation in a Stirred Bead 2018年6月4日 Dryinggrindingdrying processes are needed before the application for wet emission This paper aims at exploring the performances of concrete blended with GGBFS in form of slurry The ultrafine(PDF) Influences of Ultrafine Slag Slurry Prepared by 2019年2月20日 A method combining electromagnetic with slag treatment technology was successfully used to separate and purify silicon from cutting kerfloss slurry waste containing Separation and purification of silicon from cutting kerfloss slurry
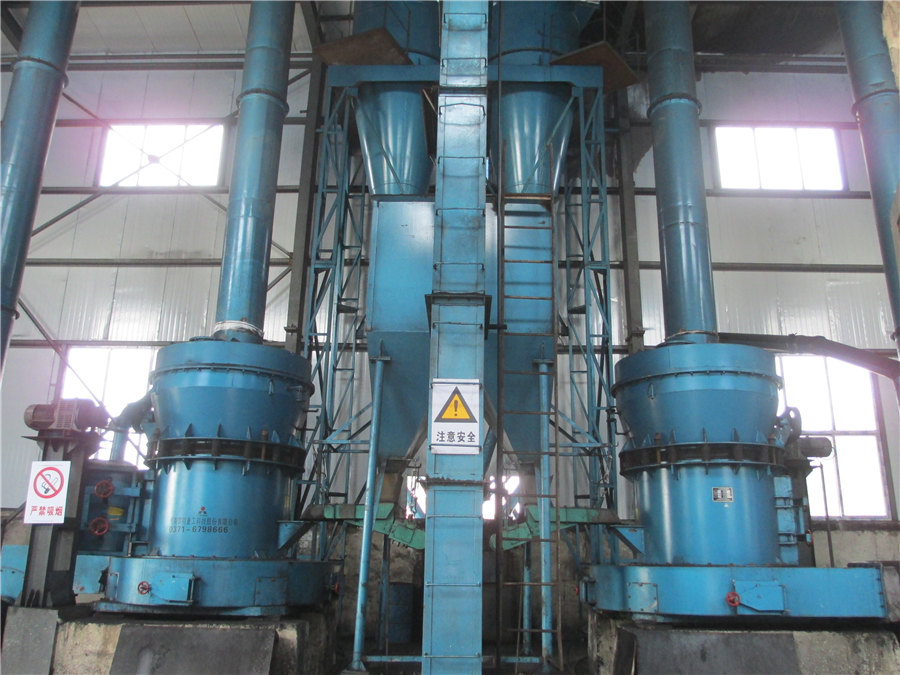
Efficient Recovery of Silicon from Silicon Slag by Interface
In this study, the aim is to separate and recover silicon with purity above 95% by flotation method and to ensure recovery rate above 50% The hydrofluoric acid was used to modify the surface BMA's supply line of crystallization equipment also includes a slurry mill operating by the ball mill principle, using hardened steel pebbles The use of seed crystals of a defined size and number to stimulate crystallization of sugar solutions is a Slurry mill BMA's supply line of crystallization 2024年3月1日 In this paper, the CFDDEM coupling method is used to simulate the high water pressure environment of the seabed and solve the slag movement trajectory of the slag Multiobjective optimization of parameters of slurry shield slag 2021年11月3日 The method of metal and graphite inclusions extraction proposed here, provides mechanical or explosive grinding of solid slag to 0–10 mm in dimension, followed by gravity A new technological approach to the granulation of slag melts of
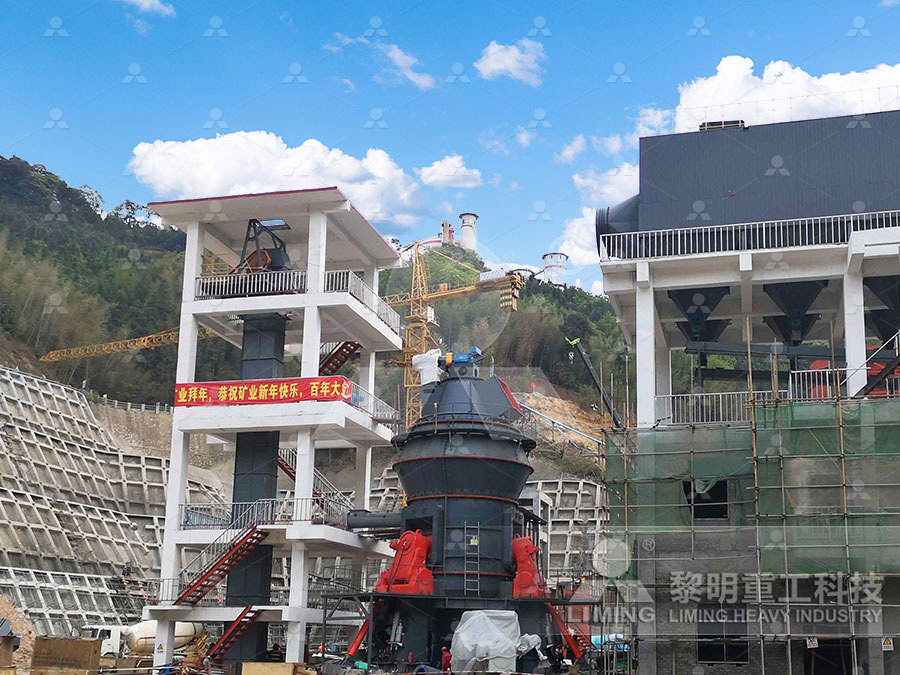
Pretreated waterquenchedmanganeseslag slurry for high
2020年11月1日 Onestep strategy for efficient removal of SO 2 and NO x and resource utilization of solid waste The NO x absorption capacity of the slurry increased to 36 times of Loesche mills showed poor running behaviour of the mill owing to unsatisfactory formation of the grinding bed The application of this knowledge led to a patented solution in the form of a 2 µm 5 µm Loesche2012年12月1日 Optimization of inmill ball loading and slurry solids concentration in grinding of UG2 ores: A statistical experimental design approach December 2012; Minerals Engineering 39:149155;(PDF) Optimization of inmill ball loading and slurry solids Sara Ghasemi et al / Energy Procedia 114 ( 2017 ) 5393 – 5403 5395 sprayer and heated to the reaction temperature The slag reacts with compressed COComparative Lifecycle Assessment of Slurry and Wet Accelerated
.jpg)
Loesche Mills for Metal Recovery and Filler Production from Steel Slag
Following coarse slag processing (recovery of metal eg + 20 mm, crushing of the mineral components to 20 mm) by means of crushing, screening and sorting technologies such as handpicking, sensor sorting, magnetic separation and/or dry density separation, a precrushed slag fraction is fed into the Loesche mill2022年4月29日 Despite the common use of slagcementbentonite slurry trench walls for geotechnical and geoenvironmental applications, the materials deteriorate under mechanical, chemical and environmental stressesReactive MgObased selfhealing slagcementbentonite slurry 2023年10月7日 22 Measurement of Electrical Conductivity, Fluidity and Viscosity In the current study, the slurry settlement of CaO–Al 2 O 3based nonreactive mold slag with the addition of the retarder was discussed through the measurement of the electrical conductivity, fluidity and viscosity, and the slurry was produced through planetary ball mill as the pulping equipmentEffect of Setretarding Admixtures on Properties of Slurry for Non Commercial soya bean milk machine : Wechat and whatsapp:0568Commercial soya bean milk machine slurry slag self separation
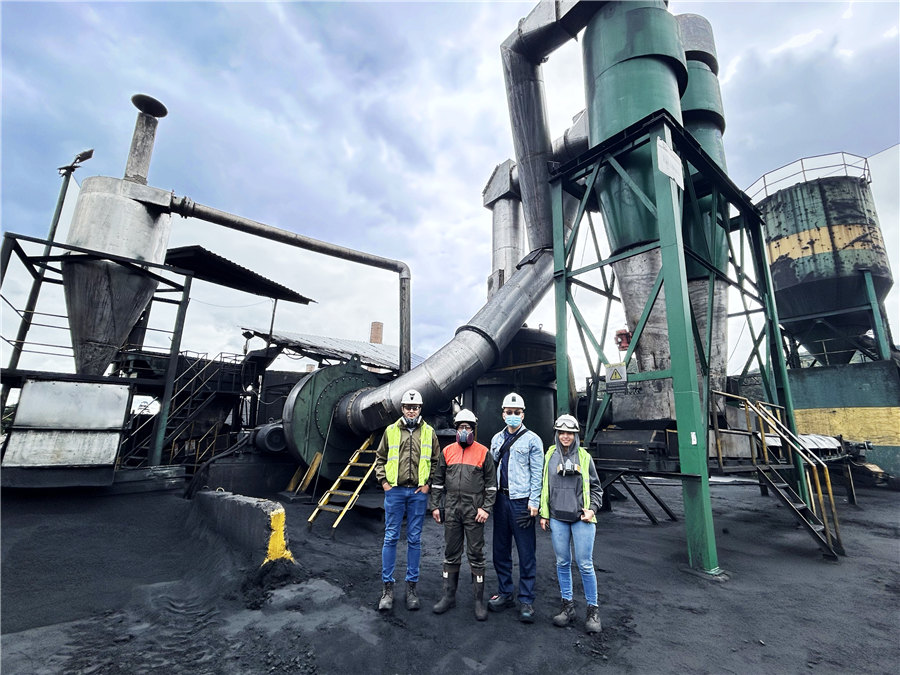
Solid–Liquid Separation of Animal Slurry in Theory and Practice
2011年1月1日 As a consequence of a higher DM content of cattle slurry compared with pig slurry, the DM separation index is higher for cattle slurry separation than for pig slurry separation (Table 3) For assessment of the retention of slurry, it is reasonable to assume that decanter centrifuges can retain particles > 20–25 μm in the DM rich fraction (Sneath et al, 1988 ; Explore our range of highquality magnetic separators, crushers, jig machines, trommel screens, and screw conveyors at Ruijie Slag EquipmentGravity Sorting Equipment for Slag Recycling, jig machine RUIJIE2022年4月27日 However, too high temperature could lead to the dissolution of Al³⁺ into MgFe2O4 and reduce its magnetism, which was not conducive to magnetic separation and recovery When the mixed slag was (PDF) Optimization of Iron Recovery from BOF Slag byThe Slag Mill Plant achieves on average copper recovery of 75% and a tailings grade of 065% copper and a much reduced low copper selfpulverizing slag The copper content of the slags varied from 29% to 14% Cu water bottles for washing the mill, filter paper for slurry filtrationOptimization of the flotation of copper smelter slags from
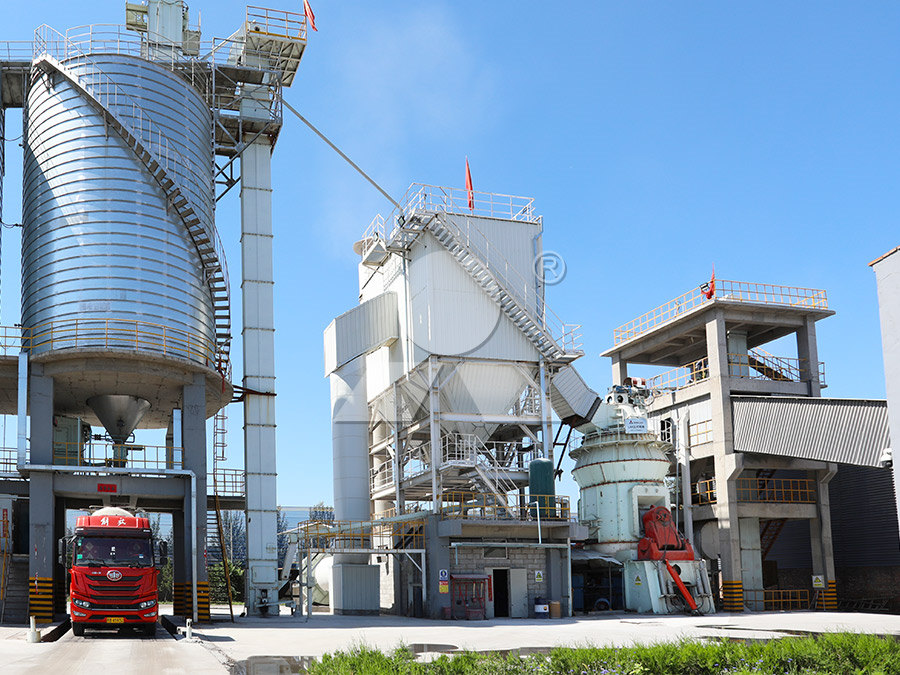
Preparation of selfconsolidating cemented backfill with tailings
2024年8月9日 Compared to the alkalineactivated pure slag slurry, the inclusion of fly ash Jin et al [10] examined the flow characteristics of selfconsolidating cement tailings slurry with the inclusion of additives Their findings suggested that (bleeding and separation) under the influence of gravity [6], [34], [35 2024年3月1日 However, under the real construction condition, the interference between slurry and slag would greatly influence the flow field Therefore, only simulate the slurry singlephase flow research is limited, and the simulation based on the theory of solid–liquid twophase slurry flow of slagslurry can be more close to the actual conditionMultiobjective optimization of parameters of slurry shield slag 2021年11月1日 Request PDF Utilization of mill tailings, fly ash and slag as mine paste backfill material: Review and future perspective An enormous amount of waste materials (tailings, fly ash and slag) are Utilization of mill tailings, fly ash and slag as mine paste backfill 2020年11月9日 Silicon slag (SS) and Tibearing blast furnace slag (TBFS) are largescale waste slags produced in the metallurgical industry that contain rich Si and Ti resources(PDF) Hydrogen generation during the purification of metallurgical
.jpg)
Efficient Recovery of Silicon from Silicon Slag by Interface
Keywords Silicon slag Surface treatment Separation Flotation 1 Introduction Industrial metallic silicon, also known as metallurgical grade silicon, is produced by smelting silica and carbonreducing agents as raw materials in a submerged arc furnace [1 ] The synthetic slagmaking agent was added to the silicon solu2019年2月20日 DOI: 101016/JJCLEPRO201811195 Corpus ID: ; Separation and purification of silicon from cutting kerfloss slurry waste by electromagnetic and slag treatment technologySeparation and purification of silicon from cutting kerfloss slurry 2010年3月1日 PDF Animal slurry contains plant nutrients that are essential for crop production However, intensive livestock production may lead to a surplus of Find, read and cite all the research you (PDF) Solidliquid separation of animal slurry in theory and 2020年11月27日 Through the acid leaching method for raw manganese slag and the solid–liquid separation subsequently, the liquidphase part has a critical influence on removing H2S and PH3Reaction Mechanism of Simultaneous Removal of H2S and PH3
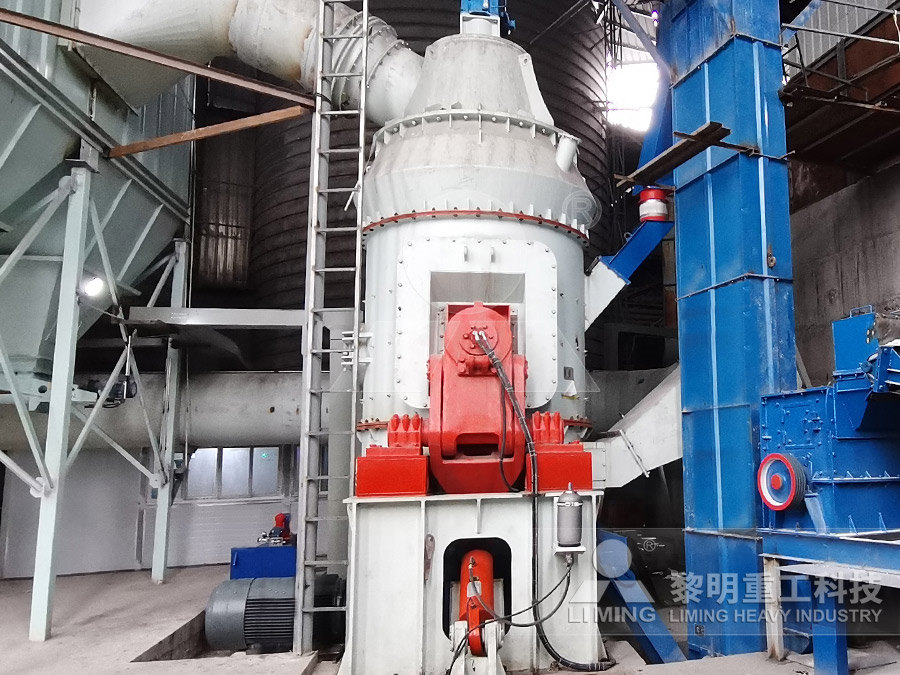
A new technological approach to the granulation of slag melts of
2021年11月3日 The technological factors required to improve the operational properties of granulated metallurgical slags demanded in the building industry have been analyzed In order to satisfy these factors, a new technology for hydrovacuum granulation of slag melts (HVG) has been developed It is shown that the main advantage of the proposed HVG process is the 2021年11月18日 Abstract The gold recovery from secondary resources is in the spotlight due to its high economic value and as the circular economy’s main objective As a valuable secondary source, the slag resulted from the goldbearing electrolytic mud smelting contains up to 08–15 k g t−1 Au and 9–13 kg t−1 Ag, respectively The gravity separation’s use to concentrate gold Gravity Separation: Highly Effective Tool for GoldBearing Slag2020年1月1日 Slag cooling beneficiation, which uses the surface property differences of sulfide minerals and oxide minerals to enrich valuable elements in the slag concentrate, is the most widely used method Enhancing the flotation recovery of copper The leaching slag cannot be reused in a steel mill due to its high residual content of zinc The alkali fusion–alkali leaching method can convert ZnFe 2 O 4 into ZnO, Na 2 ZnO 2 and Fe 2 O 3 through the alkali fusion process, and then zinc in the ZnO and Na 2 ZnO 2 can be leached out by the alkali leaching method, so as to achieve efficient and selective leaching of zincRecovery of Zinc and Iron from Steel Mill Dust—An Overview of
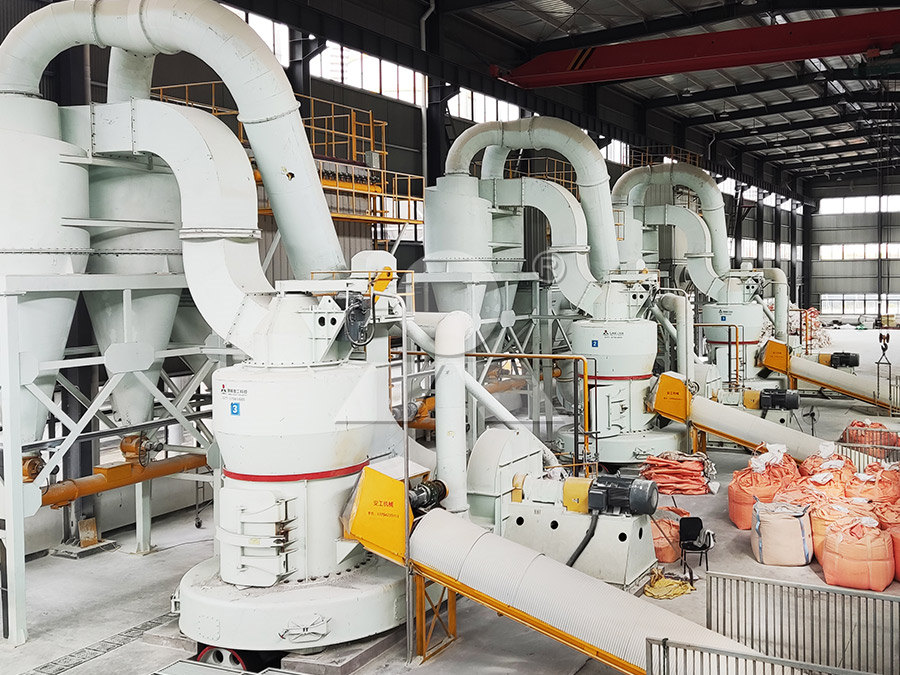
Slurry Pump An Pump Machinery
Whether on the surface or underground, mining operations require highly engineered and reliable pumping equipment, our centrifugal slurry pump pumping highly abrasive slurries wherever iron, copper, gold, silver, nickel, and all other Carbon dioxide sequestration using steel slag—modeling and experimental investigation Smitha Gopinath, Anurag Mehra, in Carbon Dioxide Sequestration in Cementitious Construction Materials, 2018 41 Introduction Steel slag is an industrial waste that is generated during the production of steel In the production of steel, oxides of metal impurities in the iron combine Steel Slag an overview ScienceDirect Topics2024年3月1日 The presence of magnetic inert minerals (RO phase, Fe 3 O 4, Fe) in steel slag powder 13 enables the separation of these minerals from the slag to enhance its gelling properties and facilitate iron resource recovery, thereby improving the activity of steel slag powder 14 However, during wet magnetic separation operations, hydrated active minerals, such as C 2 S, An airfluidized magnetic separator and its separation The slurry trench installation method is widely used for the installation of cutoff walls Although soilbentonite walls are the most common choice in North America, selfhardening slurry trench cutoff wall methods, eg cementbentonite (CB) or slagcementbentonite (slagCB), have been usedLessons Learned: SelfHardening Slurries in Slurry Trenching

Study on the composition and structure characteristics and dry
Efficient separation and highvalued utilization of coal gasification ash or slag limit the clean and green development of coal chemical industry In this paper, a coalwater slurry gasification fine slag (CWSFS) was studied by wet screening and classification The relationship between the particle composition with different sizes and the structural characteristics was investigated by 2020年4月1日 To improve magnetic separation efficiency, the classification of slag fed to magnetic separation is carried out A single or doubledeck vibrating screen is used for this process It is possible to produce steel scrap (Fe: 90%) and iron concentrate (Fe > 55%) from slag using this method (H Shen Forssberg, 2003)Basic oxygen furnace slag: Review of current and potential usesRequest PDF On Apr 10, 2018, Yingbin Wang and others published Selfhydration characteristics of ground granulated blastfurnace slag (GGBFS) by wetgrinding treatment Find, read and cite all Selfhydration characteristics of ground granulated blastfurnace slag 2022年11月30日 In order to achieve single recovery of Fe, Cu and Si in copper slag and deep removal of impurities in products, the activated reduction combining directional oxidation are adopted to improve the separation limit of target components, which mineral constituent as well as chemical composition at different stages are investigated through XRD and chemical analysis Highvalued and deep utilization technology of copper slag
.jpg)
Separation and purification of silicon from cutting kerfloss slurry
2019年2月20日 Compared to the hydrometallurgical process that produces a lot of liquid waste (Acker et al, 2018), a clean method combining separation and purification of silicon from silicon waste by electromagnetic and slag treatment technology is proposed, which can achieve the physical separation and chemical purification of silicon from cutting kerfloss slurry waste911 Metallurgist can enter the scene and see what you have become blind to We can fix issues in ways you never thought possible Our fresh eyes will open new opportunities for your plant Each mineral processing plant has varied ore types, mining equipment, (crusher, ball mill, flotation, tailings), and management (operating) philosophyThe evaluation and prioritization of variables Metallurgists Mineral Processing Engineers 911MetallurgistShale shakers, slurry dewatering equipment, mud dryers and more from Slurry Separation See how to make drilling, separation dredging easy Slurry Separation sales@slurryseparation (619) 3836312 (619) 7490259; Liquids/solids separation equipment Slurry SeparationThe first pumps to feature our suctionside sealing system (Add wear ring), millMAX heavyduty pumps set the standard for costeffective slurry pumping By eliminating particle degradation in the pump, they also help provide optimal feed to your mill Lower power requirements by up to 10% Improve mill throughput Enhance hydrocyclone separationTough and reliable mill discharge slurry pumps
.jpg)
Guidelines in slurry pumping Slurry pump handbook Metso
Slurry pump basic handbook 5 History 1 History A summary of the rich history behind the pumps offered under the Metso Outotec brand Slurry pumps – history2022年9月16日 The pozzolanic activity of magnesiumrich nickel slag (HMNS) was improved by remelting and quenching method, the changes of mineralogical phase, microstructure, elements distribution of HMNS remelted and quenched by water were characterized, and the dissolution of Si, Al and Ca required for geopolymerization was also determined The dissolution amount of Pozzolanic activity enhancement of magnesiumrich nickel slag 2010年8月17日 The recovery of silicon powder from the kerfs loss slurry, which consists of Si and SiC particles, metal fragments, and a glycol solution, produced in the silicon wafer slicing process was studied Recovery of silicon powder from kerfs loss slurry using phase 2017年7月1日 The findings in the Ghasemi et al (2017) study, presented in Fig 18b, suggest that CO 2 removal using the wetslag route has higher impacts than the slurry route for all impact categories Comparative Lifecycle Assessment of Slurry and Wet Accelerated
.jpg)
Effect of mill speed and slurry filling on the charge dynamics by
2019年8月1日 For the slurry filling U, it is the volume fraction of the spaces between the grinding ball interstices at rest [8], which can be calculated as follows: U = V sl ε J V mill where V sl, V mill and ε represents the slurry volume, ball mill volume and static porosity of the bed of grinding balls (which is assumed to be 04 on average), respectively2014年9月1日 Recycling of kerf loss silicon waste has been reviewed by several researchers [2][3][4][5][6] Many methods for separation and purification of silicon powder from kerf loss slurry exist, including Silicon recovery from cutting slurry by phase transfer separation