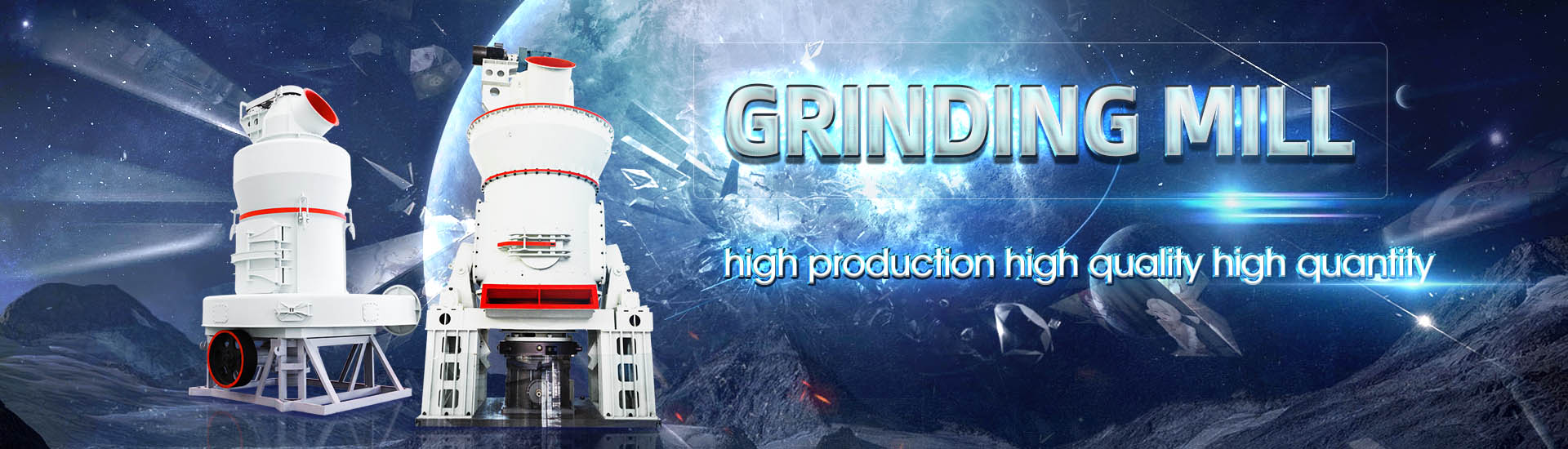
Brief description of the powder making process: in the silo
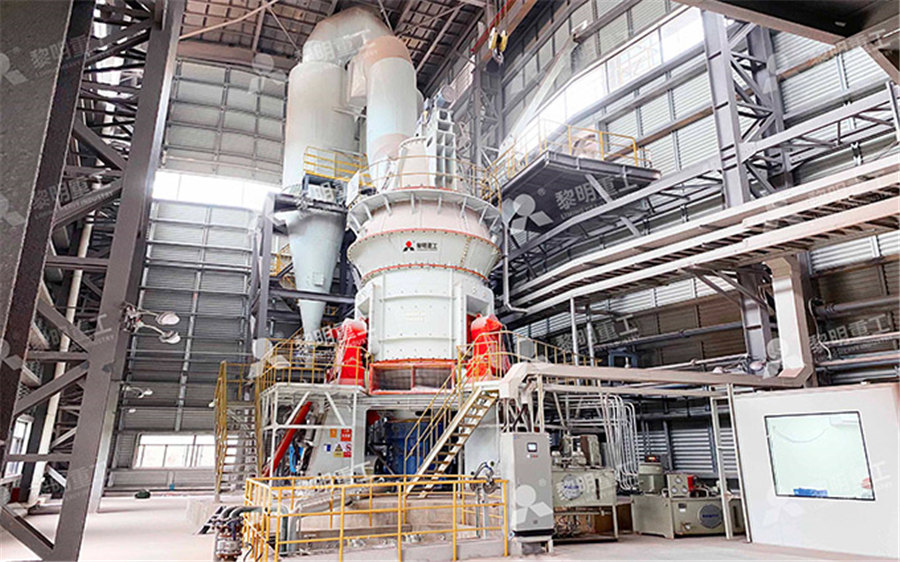
Storage of Powders and Bulk Solids in Silos
After a brief description of the problems that can arise in poorly designed silos, this essay deals with the basic rules for designing silos Figure 1 shows silos with the associated pressure and stress distributions While one usually speaks of pressure in the case of liquids, the “bulk solid Learn about designing silos and hoppers, calculating critical parameters, and selecting discharging aids Ensure reliable, controlled, and fast powder flow Discover methods to Mastering Powder Flow: A Comprehensive Guide to Solids Packaging of intermediate or final products Determined by interparticulate forces (eg adhesion forces, normal forces, friction forces) Currently described by methods of continuum Powder Flow, Measurement, and Silos (Phenomenology, Design, Powder processes provide a means to create simple as well as complex shapes from powder starting materials The engineering of powder processing methods requires an understanding Powder Process an overview ScienceDirect Topics
CFB石灰石脱硫剂制备64.jpg)
A concise summary of powder processing methodologies for flow
2023年6月1日 In this review, we discuss powder flow and its measurement techniques and mainly focus on various approaches to improve the cohesive powder flow property 1 The process engineering design of your silo system depends on your product and its properties These factors influence which flow profile is required for your silo system Possible alternatives include: Mass flow for "first in/first out" and Complete silo systems Hosokawa Solids2014年1月1日 This chapter provides an overview of powderforming methods for ceramics and metals Powder forming is distinct from traditional meltforming methods in that it involves Powder Processing of Bulk Components in Manufacturing2022年1月31日 In a silo, hopper, or bin, powder endures varying pressure levels as the upper layers consolidate the material below Unlike liquids, these pressures behave differently in powders In the conical section, powder acts Silo Design and Powder Flow Understanding Powder
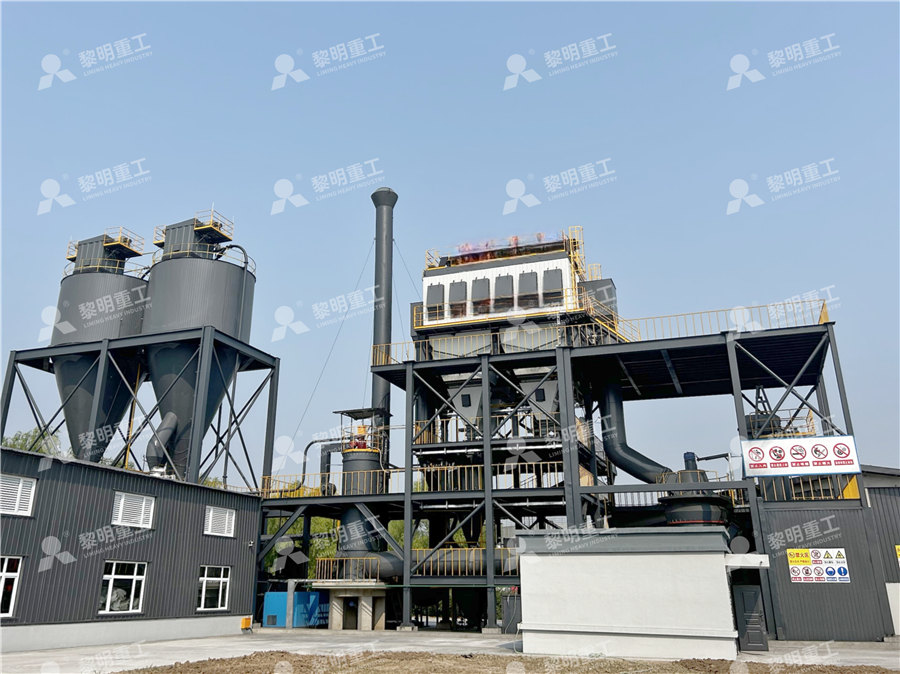
Atomization Process to Produce Powder SpringerLink
2024年1月8日 Atomization process is the liquid metal or alloy is broken into fine drips by impact of fastmoving fluid or other means, and then the droplets are condensed into solid particles so properties, silo geometry and pattern of flow desired In order to validate the theories of flow prediction and design of conical hoppers, the flow properties of two bulk solids were POWDER FLOW CRITERIA FOR DESIGN OF VERTICAL SILO WALLSAdvanced Technology: Spiral silo is constructed with special equipment when it was builtIn the process of rolling, the ektexine of the silo was made to a spiral convex band with thickness five times more than the material, and width of 30 to 40 mm, which highly strengthened the carrying capacity of the silo, and make the overall intensity, stability as well as shock resistance A Brief History of the Development of Steel Silo🕑 Reading time: 1 minute A silo is a pit structure used to store bulk materials like cement, carbon black, woodchips, etc in large industries Based on the bulk material it carries, the silos can have several types like bunker silos, tower Storage Silos – Types Advantages [PDF] The
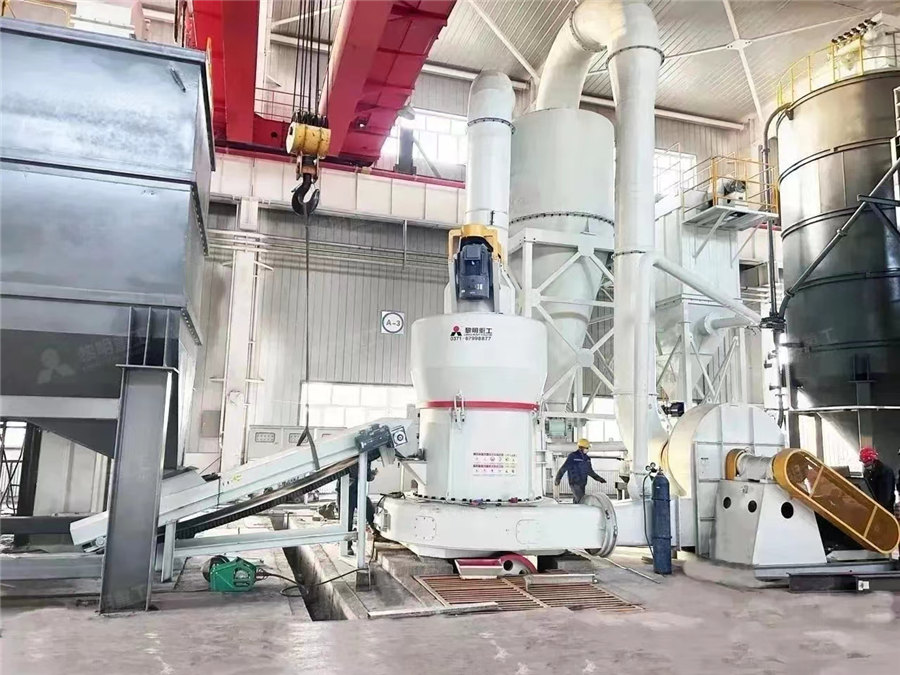
Calculations for Silo Design and Hoppers Croston
2021年5月3日 The flow of powder in a silo/ hopper is determined by 3 things the internal friction of the powder, how easily the powder can move on the surface of the silo walls, and how the powder compacts under the weight of the top The Manufacturing Process worldcementassociation 1 Limestone (CaCO3) is taken from a quarry 2 4 3 The limestone is fed into a crusher and then stored until needed The clinker is mixed with additives, such as gypsum, and then ground in a cement mill, which creates cement The cement is then packed and distributed to consumersCement Plant: The Manufacturing Process 4 5 World Cement 2020年9月1日 The powder bed fusion (PBF) process using Ti–6Al–4V powder has the specific application in additive manufacturing of a highperformance structural parts in the aerospace and medical industries(PDF) Powder bed fusion process: A brief review ResearchGateThe process of manufacturing of shaped components or semifinished products such as bar and sheet from metal powder is called as Powder metallurgy The technique of powder metallurgy combines unique technical features with cost effectiveness and generally used to produce sintered hard metals known as ‘carbides’ or ‘tungsten carbides’Introduction To Powder Metallurgy Principles of Powder Metallurgy Process
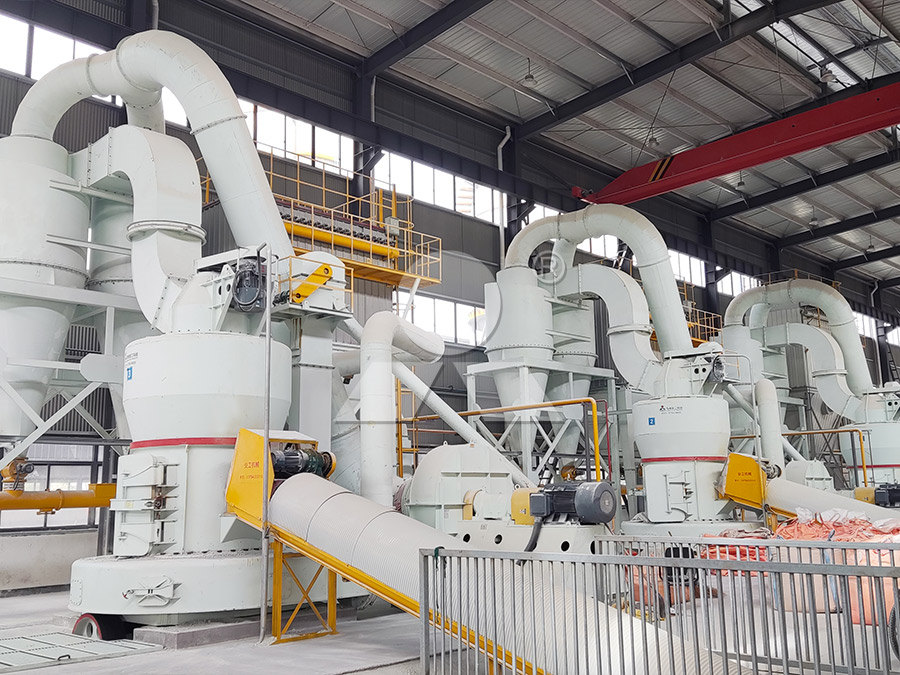
Powder caking or clumping review : causes and how to solve it
The caking of a powder can very weak, the powder being broken down in the subsequent process stages, which is not too problematic, or can be much harder, with the lumps being persistent and causing some operational problems in factories, or even consumer complaints if the material has been conditioned for being sold2023年6月13日 In addition to considering static pressures of the intended bulk storage material, silo engineers also determine reinforcement arrangements necessary for the silo size and silo construction type, Jumpform, Slipform, or StaveLoading and unloading needs are also important considerations, as the most critical portions of this design involve the lower part of the siloThe Essentials of Silo Engineering Marietta Silos2023年5月17日 Image of the molecular interpretation of gluten network and the effects of water addition and mixing (I) and a scanning electron micrographic image of the gluten network (II)The Fundamentals of Bread Making: The Science of BreadWhen most people think of the metalmaking process, they picture a stream of molten metal pouring into a mold it makes a nice visual for films and commercialsBut when you consider making parts with powder metal, it may be a little harder to picture the process or why one would bother with powder metal in the first placeHow Metal Powder Is Made: Step 1 of the Powder Metallurgy
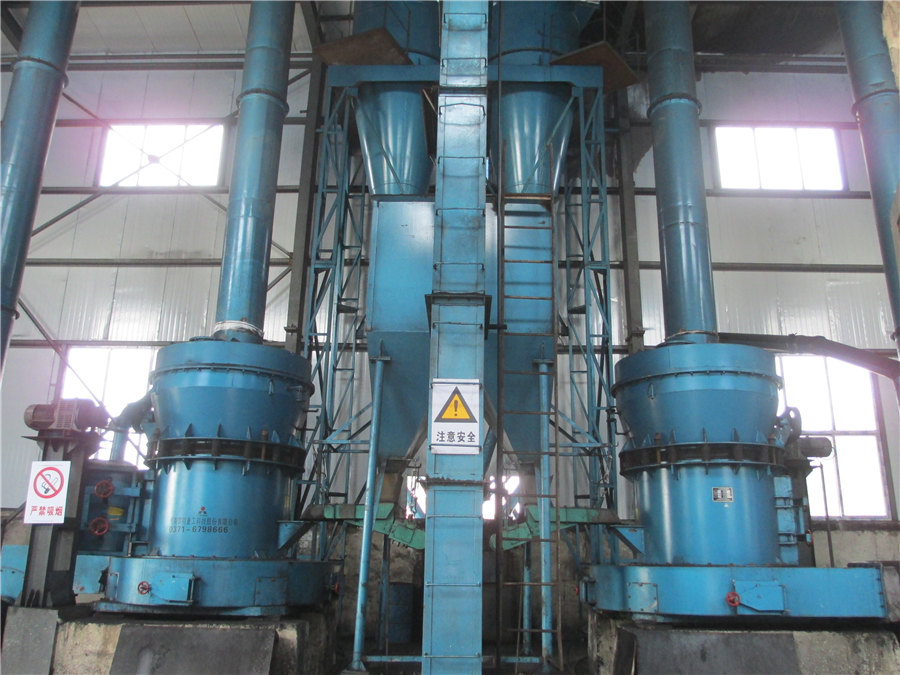
Investigation of discharging flow behavior of powder in the
2023年11月25日 In the fluidization process of nylon powder, maintaining a uniform flow of powder in the feed silo is crucial to reduce powder agglomeration and facilitate the fluidization process In this study, BINSERT was applied to improve the flow properties of powder in the feeding silo The discharge process of nylon powder in silos equipped with different dip angles 2024年2月5日 Apart from capsules, tablets is a popular oral dosage form, a reason you need to understand the tablet manufacturing process Knowledge on tablet manufacturing process is important for students studying pharmacy, Tablet Manufacturing: The Ultimate Guide SaintyTec2022年6月6日 The powder metallurgy process does not melt the material during the material production process, so it will not mix impurities brought by other substances Sintering is carried out in a vacuum and a chemically reducing What Is Powder Metallurgy? Introduce The 2023年2月22日 The powder metallurgy process cannot produce parts beyond 220 kilograms due to the fluidity of metal powder While part size is limited, quantity is not Mass production in PM is costeffective However, when producing in small batches, it can be very costlyPowder Metallurgy Process: Steps, Applications Limitations
.jpg)
Powder Metallurgy Processes and Making Metal Powder
2020年10月26日 This research includes a review of powder metallurgy processes, advantages and disadvantages, applications, and production methods of metal powder Powder metallurgy process steps consist of Once harvested, the wheat is transported to silos where it's dried and stored for several months It is then taken to the mills by truck, train, or canal boat, where it is stored in silos again Moulin Cyprien, vu depuis la Sarthe Île MoulinSart by Marine Rouchteau Communauté de Communes du Val de Sarthe FDMF Fédération des moulins de FranceThe milling process: from wheat to flour Google Arts CultureWilliam Aspdin made what could be called ‘mesoPortland cement‘ (a mix of Portland cement and hydraulic lime)Isaac Charles Johnson further refined the production of ‘mesoPortland cement’ (middle stage of development), and claimed to be the real father of Portland cement In 1859, John Grant of the Metropolitan Board of Works, set out requirements for cement to be used in What is the manufacturing process of Portland Cement?2023年11月28日 Description; Efficient storage: Silos maximize storage capacity, Firstly, silage has a higher energy and protein content compared to dried forage, making it an excellent source of nutrition for livestock and greater control over the storage process” —John Farmer, Silo Expert In addition to glasslined steel and square How Does A Silo Work? (Farming Storage) Tag Vault
.jpg)
A Comprehensive Guide to Designing and Installing Plant Silos
2024年4月15日 Designing Plant Silos The design process for factory silos is a critical phase that requires careful consideration of various factors Here are some essential steps and considerations in designing a plant silo: Assessment of Needs: Evaluate the type and volume of material to be stored, as well as the frequency of filling and emptying the silo2017年10月17日 Adjustable angle process connections allow for correct alignment to the angle of dry products in the silo Applications for 80 GHz FMCW instruments include silos with small process connections, as its higher frequency provides a smaller beam angle and allows for the use of smaller antenna sizesMeasuring the Level of Bulk Solids Stored in Silos2024年11月1日 The powder and the silo bottom cannot maintain a constant contact state during the vibration process, and they are separated for a certain period of time When the acceleration amplitude exceeds 1 g, there is separation and collision between the powder bed and the silo bottom This collision leads to a significant increase in the contact forceArch formation mechanism and discharge process of cohesive fine powder 2023年6月8日 In this article, you will learn what silos are, how they are caused, and strategies for breaking them What are silos? Silos are the obstacles and barriers that occur between the different teams within a company These silos Working in silos: Meaning and strategies for cross
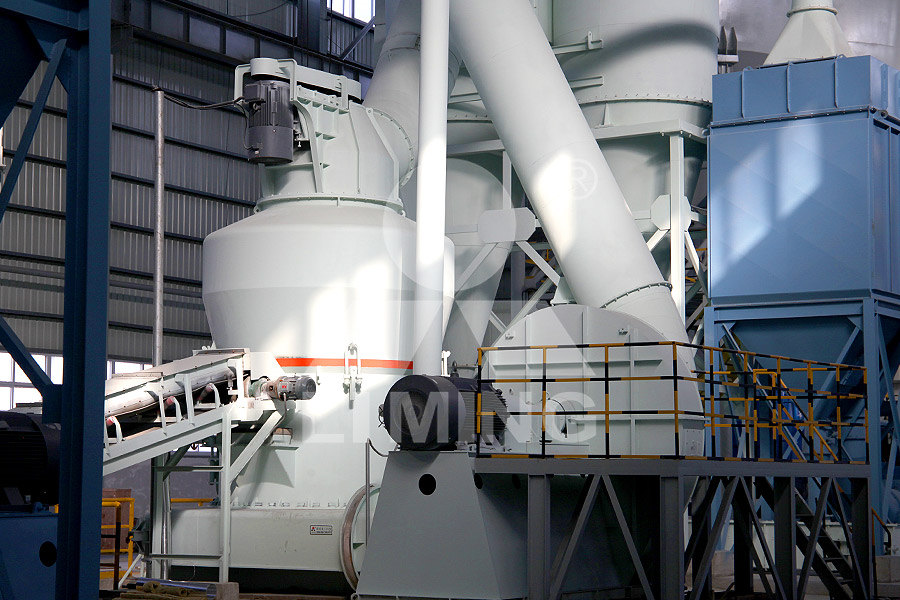
FLOW PROPERTIES FOR SILO DESIGN A REVIEW
pressures acting on silo walls and hoppers (JAGER et al, 2015) in addition to the estimation of the silo capacity (STASIAK et al, 2015) A common assumption is that the specific gravity is constant within a silo However, solids are porous materials, mainly grains, so the specific weight of the product varies with the pressure it isA silo is a cylindrical, hermetically sealed vertical structure constructed with galvanized steel powder materials Steel Requirement PreGalvanized plain and corrugated steel sheets of minimum 350 GSM coating, thickness 087 mm to 310 mm and minimum 350 MPa yield strengthSteel Silos : Modern and Improved Grain Storage Facility2020年11月17日 In particular, we use constitutive models implemented in a commercial ANSYS software package and employ them to simulate the silo discharge process Here, the analysis is focussed on the velocity and density profiles at the silo exit, while the numerical protocol is validated, comparing with experimental data of mass flow rateScaling Analysis and CFD Simulations of the Silos Discharge Process2021年10月1日 Flames and pressure will also propagate through the silo’s inlets and outlets and into other areas of the production process, resulting in a chain reaction of secondary explosions To protect the vessel from the initial deflagration, explosion vent panels are often installed near the top of the storage silo to quickly relieve the pressure from the explosionThe Challenges of Isolating Explosions in LargeVolume Silos
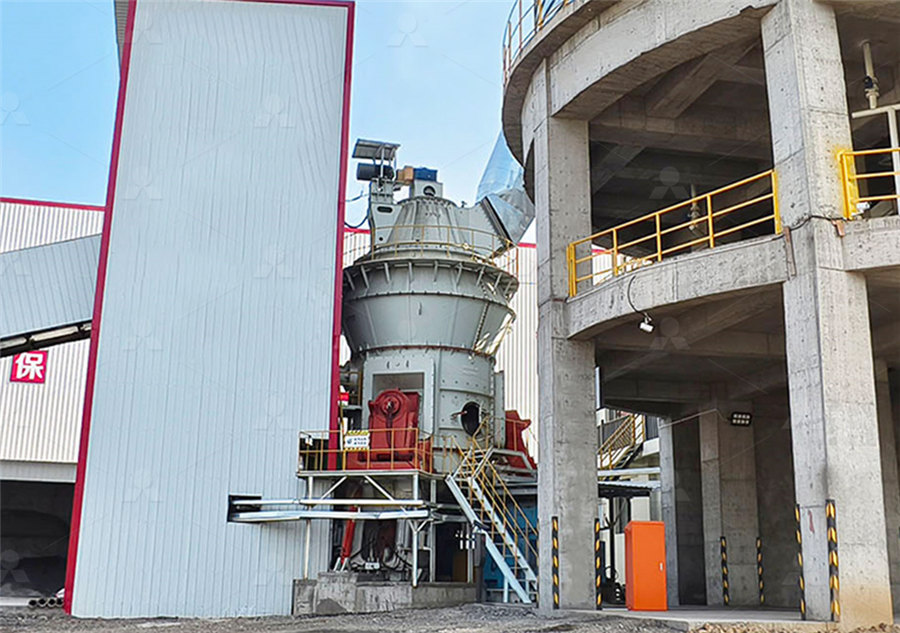
Powder Metallurgy: Definition, Process, Advantages, Applications
2023年8月21日 Fig 5: Conventional Powder metallurgy process In conventional powder metallurgy, the process closely follows the basic steps of powder metallurgy, involving powder mixing, compaction, and sintering, with the incorporation of modern technology Injection Moulding Injection moulding offers the advantage of producing complex shapes in large 2024年5月15日 The powder is first loaded into the hopper and pneumatically conveyed to the electrostatic test silo (6 m in body height, 3 m in diameter and 279 m 3 in capacity) before starting experiments 2 tons of powder are released from the electrostatic test silo and cyclically filled into the text silo through pneumatic conveyor line 2 (01 m in diameter, 25 m to 35 m in length) for Electrostatic discharge mechanisms and dynamic characteristics of material towards the centre of the silo so that it can be discharged The slidingframe silo is suitable for nonfreeflowing materials such as dewatered sewage sludge, wood chips, cellulose, gypsum and waste SLIDINGFRAME SILOS Available in highcapacity truck outloading, low flowrate pump or conveyor feed options SILOS AND SILO SYSTEMSSILOS AND SILO SYSTEMS SPIRACFrom this curve, different powder rheology characteristics can be calculated The graph obtained, called wall yield locus is shown below (example not an actual powder) The following powder properties can be determined from the graph obtained (called "Yield Locus") Table 2 : Flow Properties of Powders : An overview (Powder Physical and
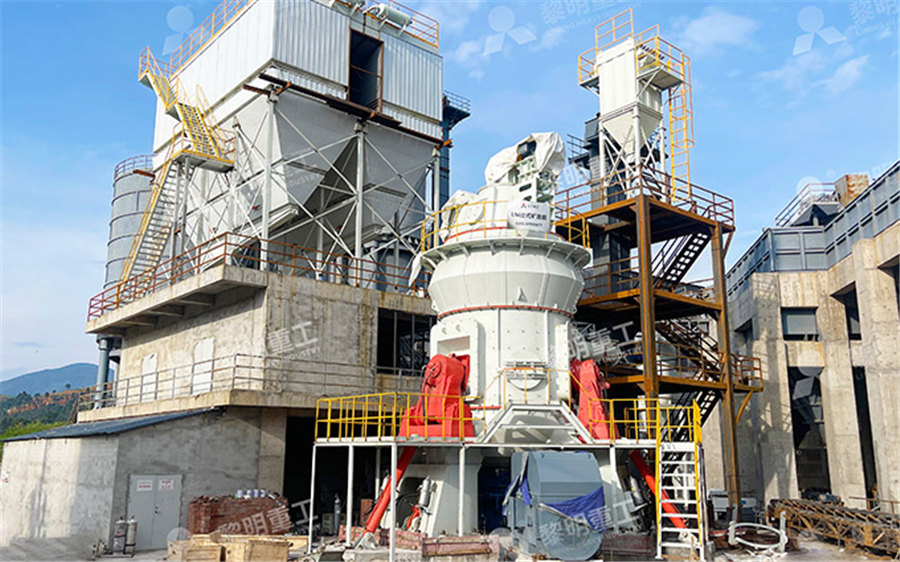
Numerical simulation of gas penetration and powder Springer
2024年10月17日 The powder consolidation and equipment damage caused by frequent pressurization of the lock hopper silo seriously affect stable powder discharge and transportation This paper investigated the powder compression and gas permeation characteristics during the silo pressurization by experiment and simulation The spherical glass powder and irregularly 1 What are the causes of powder flow problems in hoppers and silos ? Bridges and ratholes can cause partial or total blockage of the flow out of a siloIt is unfortunately not uncommon that bulk solids / powder processes operators How to solve powder flow problems in silos (bad Std Dev Of Silo feed / Std Dev Of Kiln feed • Automatic continuous samplers are installed at the silo feed point and silo extraction point • Samples are taken and analyzedregularly for monitoring the homogenizing efficiency of the silo and the final homogeneity of the kiln feed which is the most important parameter , to controlHOMOGENIZATION STRATEGY IN THE CEMENT INDUSTRYPulp and paper are manufactured from raw materials containing cellulose fi bers, generally wood, recycled paper, and agricultural residues In developing countries, about 60% of cellulose fi bers originate from nonwood raw materials such as bagasse, cereal straw, bamboo, reeds, esparto grass, jute, fl ax, and sisal (Gullichsen 2000)21 Introduction Brief Description of the Pulp and Paper Making Process
.jpg)
Calculation method to Design Hoppers and Silos Hopper and Silo
STEP 1 Get information on the powder The following data must be known in order to calculate the silo : The Powder Flow Function, the wall friction angle, the static angle of internal friction Knowing the characteristics of the product to discharge is the 1st and mandatory step to properly design a hopper2018年8月7日 Powder bed fusion (PBF) is an umbrella term for three separate threedimensional (3D) printing technologies; selective laser sintering (SLS), direct metal laser sintering (DMLS) and selective Powder Bed Fusion: The Working Process, Current Applications and 2018年5月9日 3 Common forms • Silos are generally circular in cross section, although different forms, such as square or rectangular cross sections are commonly adopted for shallow bins or bunkers • When calculating the size of a silo of a specified capacity, the unit weight of the material should not be overestimated and too small a value should not be assumed for the Design of silo PPT SlideShare2020年3月1日 Powder bed fusion process is one of the basic technique associated with additive manufacturing It follows the basic principle of manufacturing the product layer by layer and their fusionPowder bed fusion process in additive manufacturing: An overview
.jpg)
Silicon nanoparticles: fabrication, characterization, application and
2023年11月23日 Silicon nanoparticles have emerged as pivotal components in nanoscience and nanoengineering due to their inherent characteristics such as high energy capacity and outstanding optical properties Numerous fabrication and characterization techniques have been researched so far, while a range of applications utilizing them have been developed In this