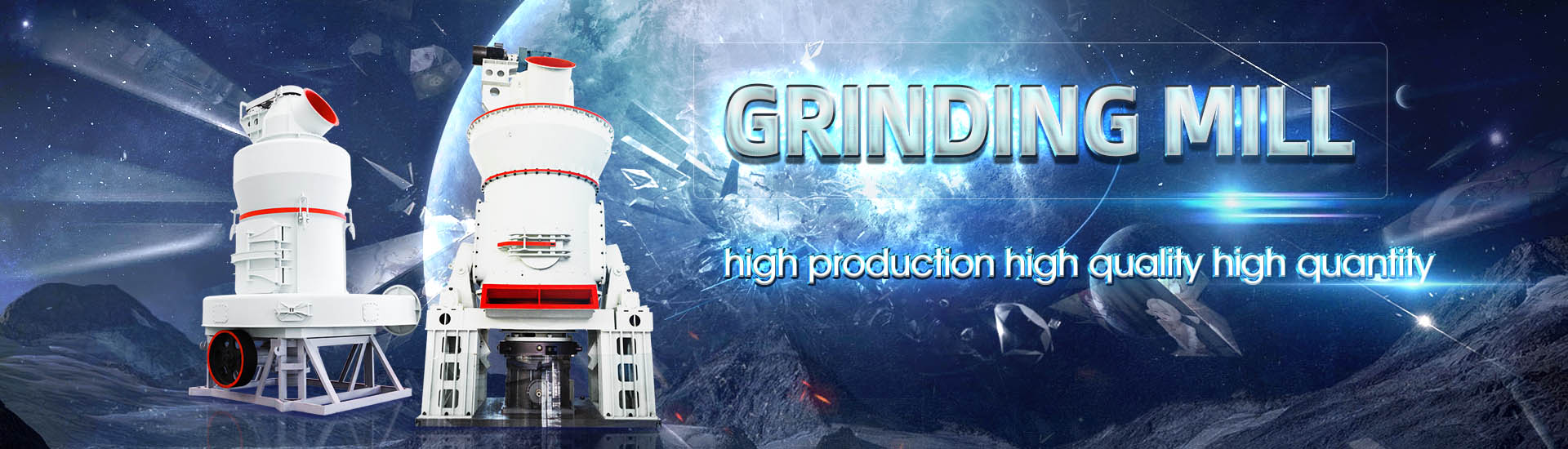
Cement clinker process
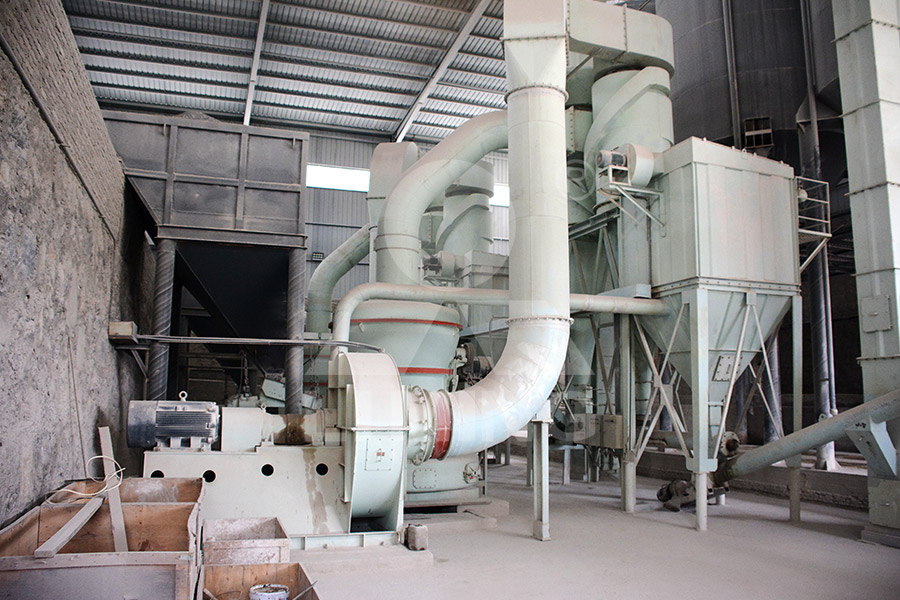
Clinker Production an overview ScienceDirect Topics
Clinker consists of calcium oxide and other mineral oxides (iron, aluminum, and silicon) and has cementious activity when reacted with water Clinker is produced by pyroprocessing in large The cement clinker manufacturing process traditionally involves intimate mixing and the subsequent heat treatment of a blend of calcareous rock, such as chalk or limestone, and Cement Clinker Production an overview ScienceDirect Topics2024年11月23日 There are four stages in the manufacture of portland cement: (1) crushing and grinding the raw materials, (2) blending the materials in the correct proportions, (3) burning the prepared mix in a kiln, and (4) grinding the Cement Extraction, Processing, ManufacturingPortland cement clinker is produced in a kiln from calcareous and siliceous raw materials and the primary cement clinker minerals are formed in a solid state at high temperature (c 1450°C) Portland Cement Clinker an overview ScienceDirect Topics
.jpg)
Process characteristics of clinker and cement production SINTEF
tested in the second campaign showing streamlines coloured by temperature Considerably high false air ingress through the cold clinker discharge system outlet No leakages of CO2–rich 2014年1月1日 The main goal of the clinkering process is to produce the material of designed phase composition, which is called Portland cement clinker Under the action of high Portland Cement Clinker SpringerLinkAs materials move through the kiln, a series of complex reactions take place resulting in a new substance called clinker Clinker leaves the kiln as grey balls about the size of marbles The clinker comes out of the kiln redhot with a How Cement is Made Portland Cement Association2023年10月16日 This study proposes a raw meal proportioning methodology for optimising coprocessing of natural feedstocks with alternative raw materials in clinker production, intending Thermodynamic modelling of cements clinkering process as a tool
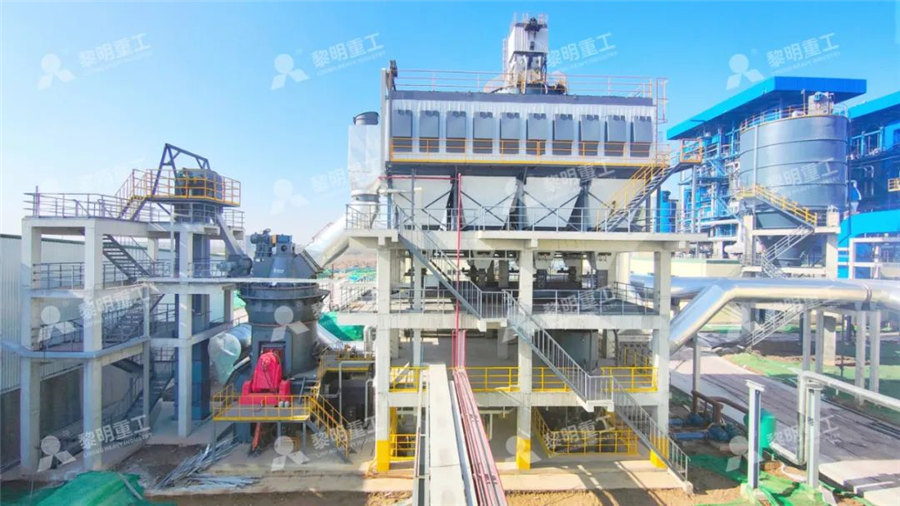
Cement Clinker: Production, Composition, Types, and
2023年6月6日 Types of Clinkers Cement producers create different clinkers based on variations in the raw materials and the manufacturing process Ordinary Portland Cement (OPC) Clinker – Portland clinker is the most common type of 2023年12月20日 Cement manufacturing is a complex process that begins with mining and then grinding raw materials that include limestone and clay, to a fine powder, called raw meal, which is then heated to a sintering temperature as The Cement Manufacturing Process Thermo Fisher 2019年8月27日 The major raw materials used as a source of CaO for cement manufacturing are limestone, chalk, marl, etc These raw materials by virtue of their natural occurrence contains other mineral impurities eg, MgO, SiO 2, Al 2 O 3, Fe 2 O 3, alkali compounds, and sulfidesThese impurities play an important role to influence the cement manufacturing Cement Manufacturing and Process Control SpringerLinkThe overall process of conversion from raw meal to clinker being endothermic demands a theoretical heat of about 380420 kcal/kgclinker However, the rest of the specific heat consumption as tabulated above constitutes heat losses from preheater exhaust gases, clinker, cooler exhaust gases, preheater dust and radiation lossesClinkerization Cement Plant Optimization
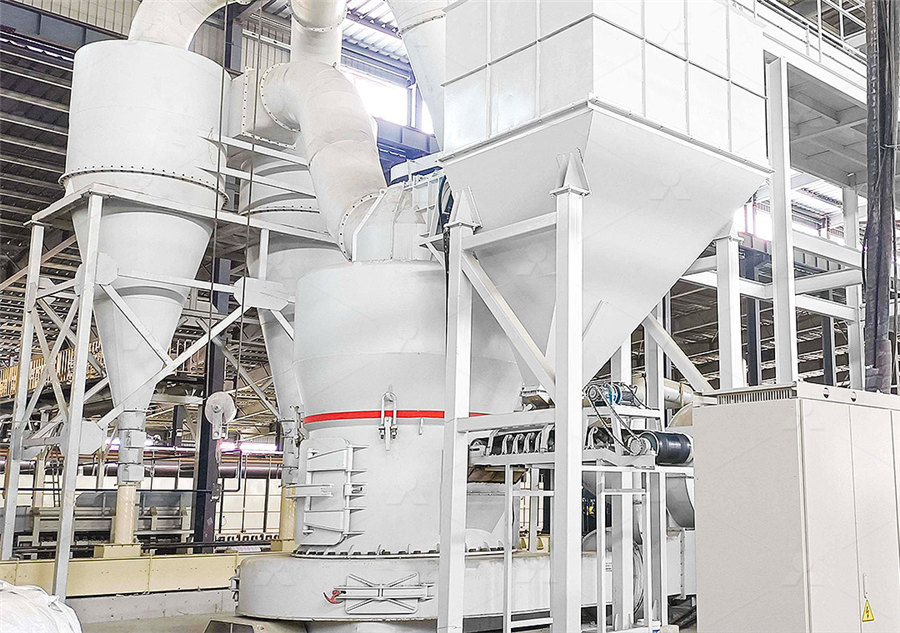
Process characteristics of clinker and cement production SINTEF
Continuous high temperature process in the cement industry: Calcination and cement clinker burning Calcination of raw material CaCO 3 => CaO + CO 2 Process emissions of raw material: = 054 t CO 2 /t clinker Endotherm reaction at 950 °C ca 1700 MJ/t clinker ≈ 50% of energy Cement clinker burning at 1450 °C formation of hydraulicThe process that cement raw materials is sintered in a kiln is the key to the quality of cement clinker In the sintering process of cement raw material, the useful components decomposed by various raw materials at 1000 °C are mainly: calcium oxide (CaO), silicon dioxide (SiO 2), aluminum oxide (Al 2 O 3), and ferric oxide (Fe 2 O 3)Portland Cement Clinker an overview ScienceDirect Topics2023年10月16日 The valorisation of waste or byproducts in Portland clinker production is a promising alternative for developing sustainable cements The complexity of the chemical reactions during clinkering Thermodynamic modelling of cements clinkering process as a Producing traditional cement clinker is an extremely energy and CO 2 intensive process In the EU, 90% of clinker is now made via the more energy efficient dry clinkermaking process (2) Older, less efficient wet kilns have almost been phased out In the more advanced dry process, raw ingredients are calcinated atDeep decarbonisation of industry: The cement sector Europa
.jpg)
Cement and Clinker Production by Indirect Mechanosynthesis Process
2022年9月21日 With this process, we manufactured cement and clinker from industrial and laboratory raw mixes, which had to be rectified by adding kaolinite in compliance with the different cement indicators The process that cement raw materials is sintered in a kiln is the key to the quality of cement clinker In the sintering process of cement raw material, the useful components decomposed by various raw materials at 1000 °C are mainly: calcium oxide (CaO), silicon dioxide (SiO 2), aluminum oxide (Al 2 O 3), and ferric oxide (Fe 2 O 3)Cement Clinker an overview ScienceDirect TopicsThe cement clinker calcination is an important step in the cement production process It mainly occurs in cement kiln and can be roughly divided into six reaction stages, namely drying, preheating, chemical decomposition, Cement Clinker Calcination in Cement Production 2022年4月12日 Measurement(s) carbon dioxide emission process Technology Type(s) computational modeling technique Factor Type(s) cement production • clinker production • the emission factor of clinker Sample China’s provincial process CO2 emissions from cement
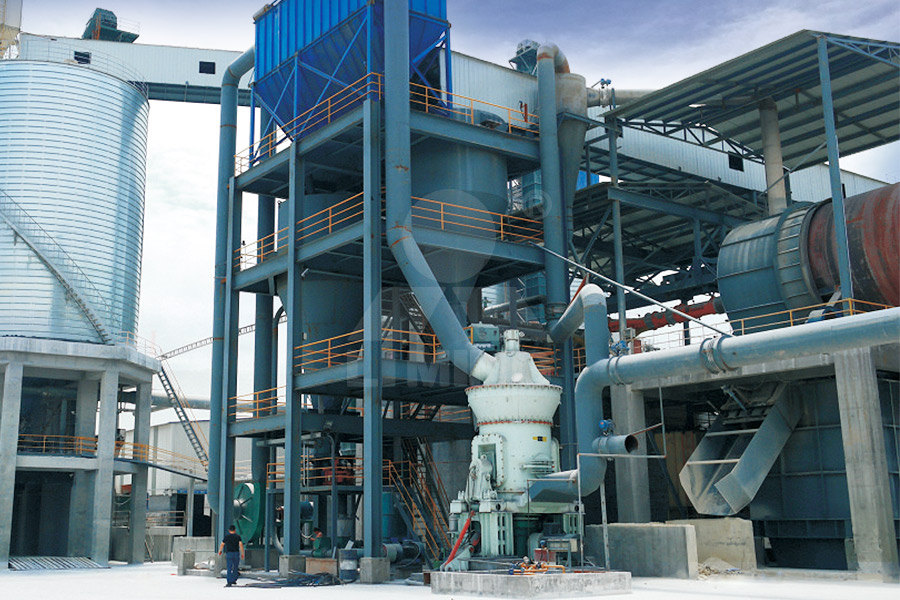
Cement Manufacturing Process: 6 StepsTo Make
2020年1月27日 6 steps of the cement manufacturing process When we talked about the manufacturing of cement, anyone who knows the cement manufacturing process slightly will mention “two grinding and one calcination”, Portland cement clinker is a dark grey nodular material made by heating ground limestone and clay at a temperature of about 1400 °C 1500 °C However, reading an article or two is perhaps not the best way to get a clear picture of a complex process like cement productionPortland cement clinker overview Understanding CementThe production of portland cement clinker from heterogeneous mixtures of raw materials is a complex process in which one must begin with an “Mineralizers and Fluxes in Clinkering Process,” Cement Research Progress, American Ceramic Society, Columbus, Ohio, pages 259280, 1976 Kuehl, H, “Addition of fluorspar to CementMix Everything you need to know about Fluxes and Mineralizers inThe cement clinker manufacturing process traditionally involves intimate mixing and the subsequent heat treatment of a blend of calcareous rock, such as chalk or limestone, and argillaceous rock, such as clay or shale A series of chemical reactions of calcium, silicon, Cement Clinker Production an overview ScienceDirect Topics
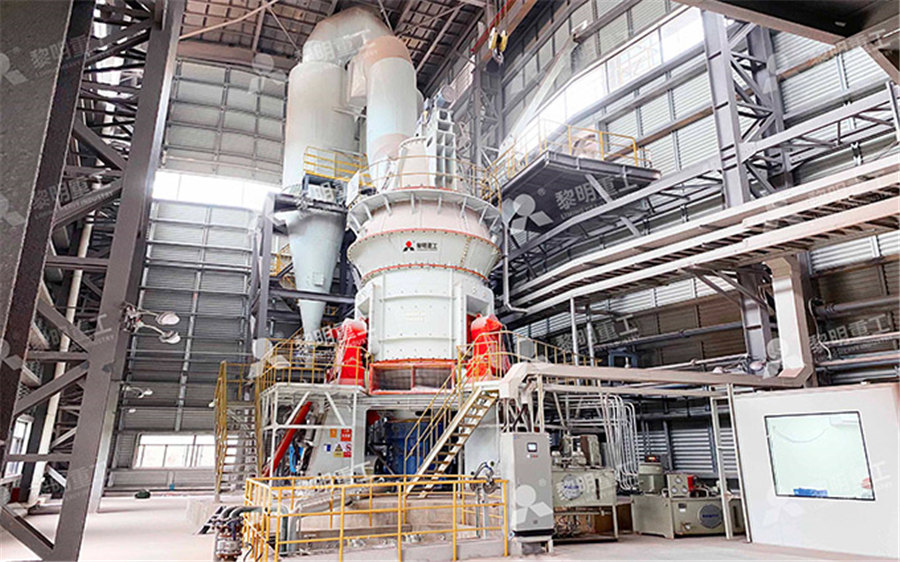
Cement kiln Wikipedia
In this process, the steps of raw material processing, fuel preparation, clinker burning and cement grinding constitute major emission sources for particulate components While particulate emissions of up to 3,000 mg/m 3 were measured leaving the stack of cement rotary kiln plants as recently as in the 1960s, legal limits are typically 30 mg/m 3 today, and much lower levels are 2023年10月19日 Clinker is a critical component in the production of cement and forms the intermediate product during the cement manufacturing process It can be best described as a nodular material, usually grayish in color, which is produced by sintering limestone and aluminosilicate materials such as clay at high temperatures in a cement kilnClinker Grinding Techniques in Cement Manufacturing JM 2020年8月25日 A full cement production process includes the cement crushing process, raw mill process, clinker process, and cement grinding process, cement packing process, and related process Find more! Skip to content +86 s about blog contact EN ES Menu Menu Home;Cement Production Process Cement Manufacturing Process AGICO CEMENT2013年1月1日 Studies on cement production optimisation have been carried out on clinker simulation using AspenTech [36], cement raw materials blending using a general nonlinear timevarying model [37], cement Modelling the cement process and cement clinker quality
.jpg)
The Cement Plant Operations Handbook International Cement
refractories – 9 Clinker cooling – 10 Kiln mechanical – 11 Emergency power – 12 Plant control systems 6 Cement milling process summary data – 8 Typical equipment downtime 110 1 Storage of clinker and other components – 2 Cement milling – 3 Separators (classifiers) – 4 Ball mill circuit control – 5 Cement storage – 6Global cement production has reached 39 billion tons However, the clinkerization process, which is the basis of cement production, is responsible for an approximate annual global CO2 emission of 2 billion tons As part of Cement and Clinker Production by Indirect Clinker is a nodular material produced in the kilning stage during the production of cement and is used as the binder in many cement products The lumps or nodules of clinker are usually of diameter 325 mm and dark grey in color It is produced by heating limestone and clay to the point of liquefaction at about 1400°C1500°C in the rotary kiln What is Cement Clinker? Composition, Types UsesThe cyclone preheating system Phase IV: Calcination The calcination is the core phase of the cement making dry process The calcination of the preheated raw meal takes place in the rotary kiln of the cement plant The rotary kiln is a huge rotating furnace in which the raw meal is heated up to 1450 ⁰C and turned to clinkerHow Is Cement Produced in Cement Plants Cement Making Process
.jpg)
Alternative Clinker Technologies for Reducing Carbon Emissions
Reduction of the cementtoclinker ratio, by replacing clinker with supplementary cementitious materials (SCM’s); The use of alternative fuels in the production of clinker together with the increase of energy efficiency of the kiln process; Development of alternative clinker technologies (ACTs), that lead to lower CO 2 emissions2015年5月5日 A simplified illustration of oxygenenriched air combustion is shown in Figure 1The idea is to add highly concentrated oxygen to the process, with the aim of increasing the production of cement clinker for sustainability purposes such as enhancing the combustion of lowgrade fuels or improving energy efficiency (Damtoft et al, 2008) Modelling the cement process and cement clinker qualityClinker Grinding The cement clinker is ground as finished cement, in a vertical roller mill for cement or in ball mills similar to those normally used for grinding hard raw materials in dry and semidry processes However, the cement clinker is more difficult to grind than raw materials and must also be finer groundAn Introduction to Clinker Grinding and Cement Storage2014年6月10日 It begins with an overview of what cement is and how it is used to make concrete It then describes the industrial process for manufacturing cement, involving grinding raw materials like limestone and clay at high temperatures in a kiln to form clinker, which is then pulverized with gypsum to become Portland cement powderCement manufacturing process PPT Free Download SlideShare
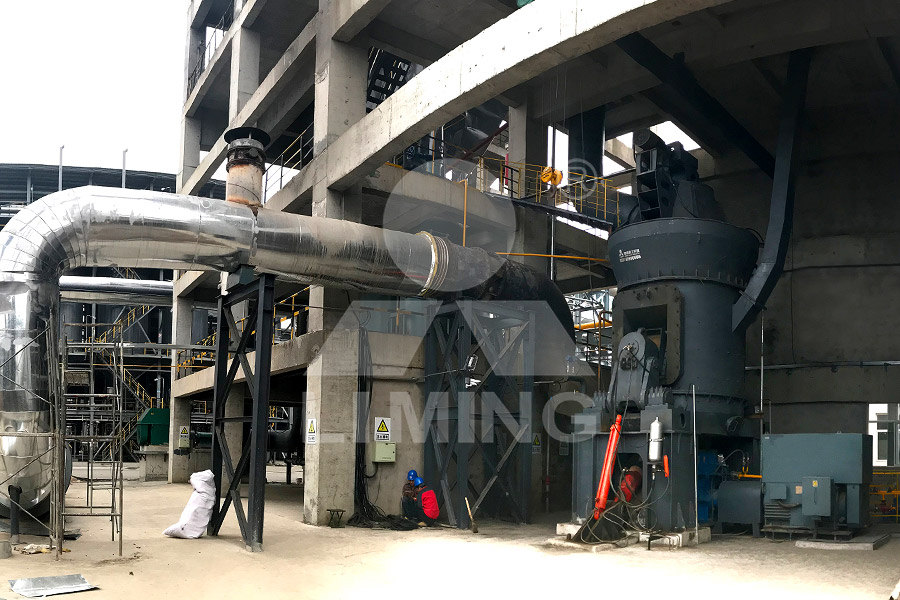
The clinker manufacturing process Al badia cement
The clinker manufacturing process The clinker manufacturing process starts with the extraction of the raw meal from the homogenization silo to insure that the raw meal is stable and homogenized in order to produce consistent clinker qualitylowering the clinkertocement ratio; and deploying carbon capture to tackle process emissions It is important to stress that each of these decarbonisation levers have their own challenges: carbon capture requires a strong value chain and significant investments together with a CLINKER SUBSTITUTION IN THE CEMENT INDUSTRY CEMBUREAUCement comprises ca 90% clinker, with the remainder being gypsum and other mineral additions (eg limestone) The The production of clinker comprises several process equipment: a preheating tower (with a set of cyclones), a calciner, a rotary kiln, and a cooler, see Fig 1A Dynamical Simulation Model of a Cement Clinker Rotary KilnPortland clinker is the main constituent of most cements In Portland cement, a little calcium sulfate (typically 310%) is added in order to retard the hydration of tricalcium aluminateThe calcium sulfate may consist of natural gypsum, anhydrite, or synthetic wastes such as fluegas desulfurization gypsum In addition, up to 5% calcium carbonate and up to 1% of other Cement mill Wikipedia
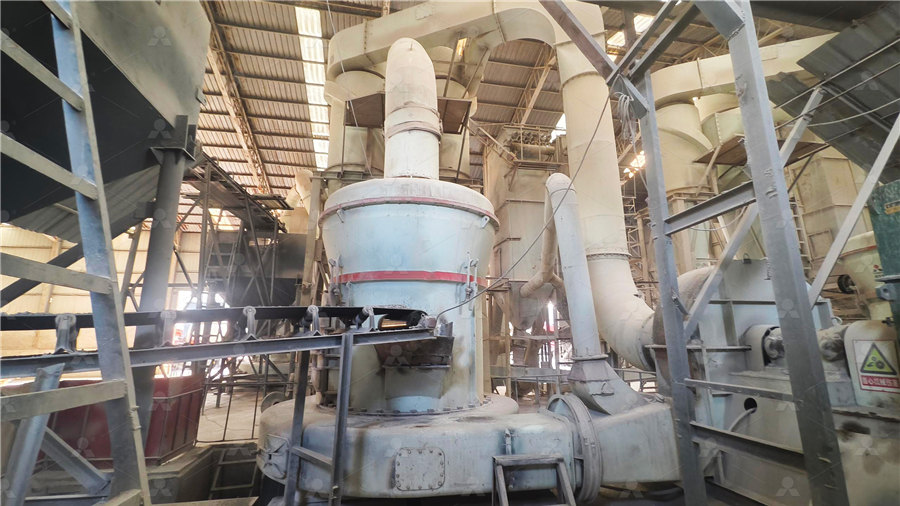
Manufacture of Cement Materials and Manufacturing
Manufacture Process of Cement The manufacture procedures of Portland cement is described below Mixing of raw material; Burning; Grinding; The size of the clinker is varies from 510mm The lower part ie clinkering zone has the Fuel costs are greater in the wet process than in the dry process because the water that is added to the raw materials to form slurry must be evaporated during the clinker manufacturing process The clinker is then cooled down, mixed with gypsum and fed in specified proportions into a cement grinding mill where they are ground into an extremely Production Process CEMEX PhilippinesCyclone preheater, cement kiln, and clinker cooler are three main cement manufacturing machines in this process Skip to content Blog Contact About Cases Factory CONTACT US info@cementplantequipment CALL US +86 REQUEST A QUOTE Just ask! Menu Cement Plant SolutionsClinker Production Clinker Manufacturing Cement 5 天之前 The manufacture of Portland cement is a complex process and done in the following steps: grinding the raw materials, mixing them in certain proportions depending upon their purity and composition, and burning them to sintering in a kiln at a temperature of about 1350 to 1500 ⁰C During this process, these materials partially fuse to form nodular shaped clinker by Manufacturing of Portland Cement – Process and Materials
.jpg)
Solving Cement's Massive Carbon Problem Scientific American
2023年2月1日 4 Convert Lime into Clinker How it works: Lime is burned at up to 1,450 degrees C in a kiln rotating three to five times per minute This process sinters (fuses) the lime into Portland cement Clinker, on the other hand, is the intermediate product formed during the manufacturing process of cement It is produced by heating limestone, clay, and other materials at high temperatures in a kilnCement vs Clinker What's the Difference? This vs Thatthe demand for cement will continue to double in the near future A core element of cement production is the clinker process in a rotary kiln This process is both energyintensive and difficult to control Due to harsh environmental conditions and high temperatures, there are few meaningful measurements within the process InAI Kiln Solution For Optimized Control How To Reduce Energycements, such as super sulfatecement, very lowheat cement and calcium aluminate cement Cement manufacture The cementmaking process can be divided into two basic steps: • Clinker (the main constituent of cement) is first made in a kiln with gas up to 2000°C, whichTHE STORY OF CEMENT MANUFACTURE CEMBUREAU