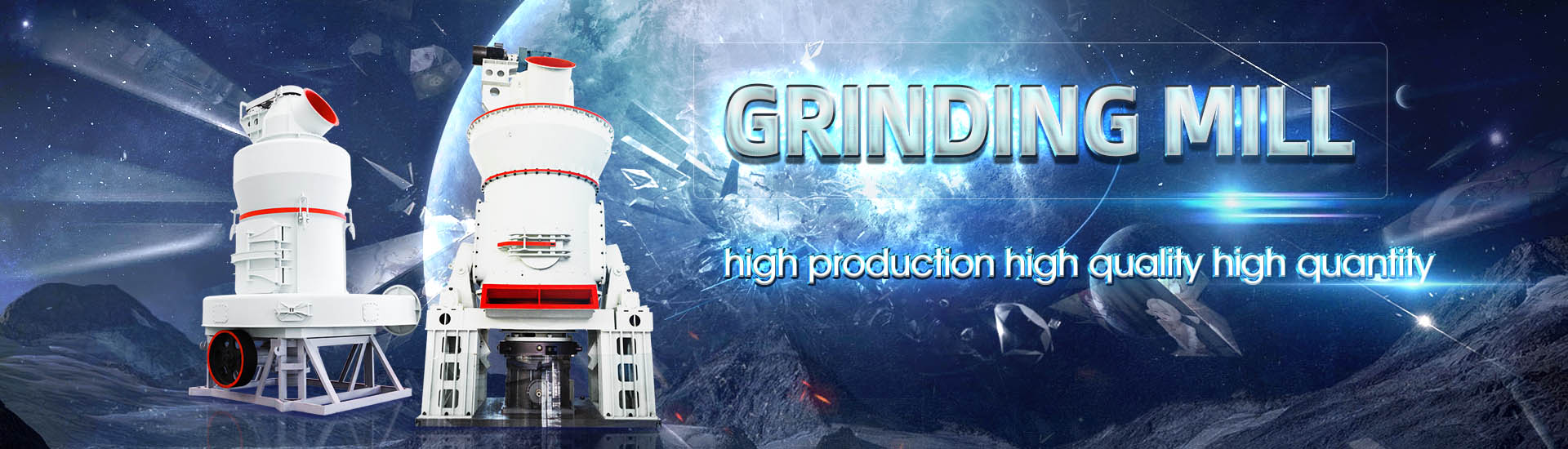
Processing process and selection of limestone for alkali and electricity production
.jpg)
Limestone Quarrying and Processing: A LifeCycle Inventory
Process flow diagram for limestone processing operations Processing commences with transportation of the (raw) stone from the quarry to the processing facility, as depicted by 2019年11月1日 In this research, the effect of limestone characteristics and calcination parameters on quicklime quality was investigated Limestone ore which is provided by Red Characterization and Optimization of Lime Production ProcessProvided in the following text are the results of the first phase of a threeyear project launched by the NSC to benchmark and improve the environmental profile of the natural stone industry A LifeCycle Inventory of Limestone Dimension Stone Quarrying Taken together, the ZeroCAL process ultimately offers >98% processCO 2 emissions reductions while requiring ∼2 times the total energy demand of conventional lime manufacturing, or ZeroCAL: Eliminating Carbon Dioxide Emissions from Limestone’s
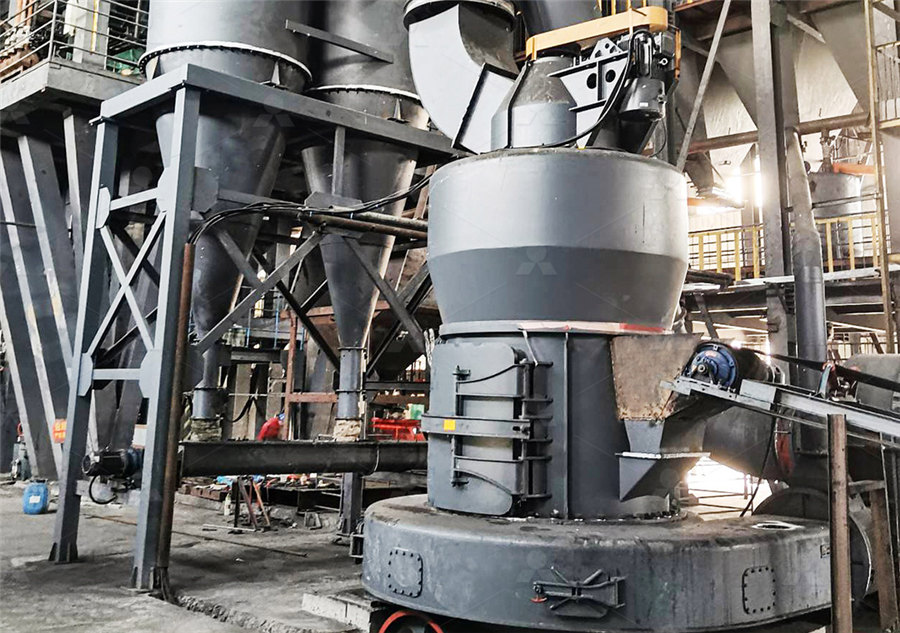
Lime Production an overview ScienceDirect Topics
The lime production process is energy intensive and results in CO 2 emissions from both mineralogical transformation process and energy used The production of one tonne of lime 2022年5月22日 Therefore, the first aim of this research work was the examination of main grinding parameters of the limestone particles to determine an empiric energymodel Dry and EnergyModel and Life CycleModel for Grinding Processes of Limestone and dolomite, after being pretreated thermally at high temperatures (1000 or 1100 °C), showed a substantial increase in calcium utilization over many calcination/carbonation cycles LongTerm Calcination/Carbonation Cycling and Thermal 2023年11月2日 This study presents an energysaving calcination strategy using low temperatures and a controlled heating process for preparing partially calcined limestone The New Insight into EnergySaving Calcination of Limestone:
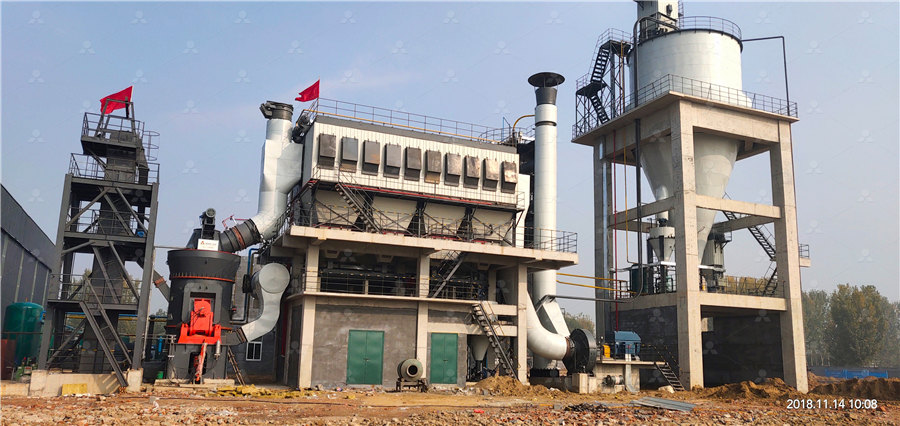
Limestone supplier selection for coal thermal power plant by
2022年5月15日 Therefore, limestone supplier selection is an important process in environmental improvement and cost reduction This paper presents a novel MCDM approach to evaluate 2021年3月3日 After a first heading devoted to the complex group of term definitions related to the lime sector, the raw materials for production of lime are reviewed, including fuels Lime SpringerLink2024年9月7日 To know the sustainable performance of calciumbased adsorbents is one of the important aspects to realize efficient and economical carbon capture, and to systematically study the properties of natural adsorbents is conducive to their industrialization The cyclic calcination and carbonation characteristics of a typical natural limestone were investigated using a Effects of OverSintering on Cyclic Calcination and MDPI2007年12月21日 When the choice of the raw material falls on marly limestone composed of 6520 wt% clays, the production process is obviously characterized by different temperatures and times and the finished Lime and Limestone: Chemistry and Technology, Production and
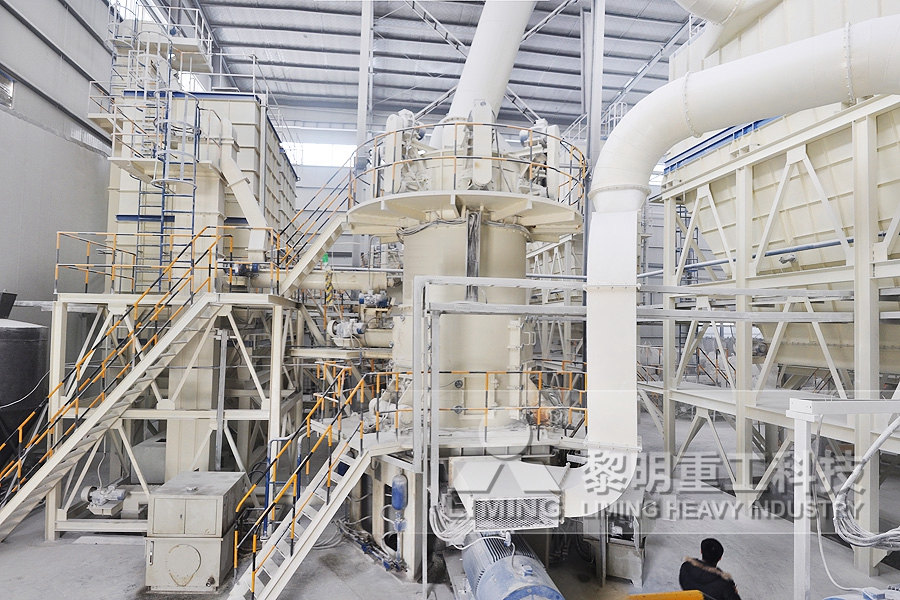
Limestone calcined clay cements (LC3): raw material processing,
2020年6月5日 Limestone calcined clay cements (LC3) are blended cements that combine clinker, limestone, calcined clay and gypsum The availability of the materials required to produce LC3 and the good 2020年9月27日 In this study, a foamed alkaliactivated glass (FAAG) via the use of milled waste glass was synthesized in lowtemperature (ie, 80°C) The influence of foaming agent (ie, aluminum powder) content on the foaming process of samples was investigated and optimized in view of their performanceWaste Glass Reuse in Foamed AlkaliActivated Binders Production 2021年3月17日 The performance of a wet FGD system is greatly influenced by gas–liquidphase mass transfer, ieof Ca 2+ ions in the liquid phase and of SO 2 from the gas phase to the aqueous phase (Hrdlička and Dlouhý 2019)This is further influenced by the rate of dissolution of limestone in the system, directly affecting the concentration of dissolved ions in the slurry Spray drying absorption for desulphurization: a review of This white paper will distill the complicated art of chloralkali membrane selection—and subsequent system optimization—into key best practices and considerations to help manufacturers achieve a oneofakind operation The ChlorAlkali Processing Landscape processing: mercury or diaphragm cell Today,ChlorAlkali Process Efficiency: A Balancing Act Chemours
.jpg)
Synthesis of waste limestone powder–based alkaliactivated
2022年12月29日 More than half of the CO2 emissions during the manufacturing of ordinary Portland cement (OPC) occur due to the calcination of calcium carbonate in addition to burning of fossil fuel to power the process Consequently, there is a concerted effort to decrease the carbon footprint associated with this process, by minimizing the use of OPC In line with this trend, an 2016年1月1日 On August 3, 1888 German Patent No 43977 entitled “A Process for the Production of Aluminum Hydroxide” was issued** The discovery which led to the patent was made by the Austrian chemist A Hundred Years of the Bayer Process for Alumina ProductionM Seko, IonExchange Membrane for the ChlorAlkali process, ACS Polymer Division Workshop on Perfluorinated Ionomer Membranes, American Chemical Society, Lake Buena Vista, Florida, Feb 1982 Google Scholar H Ukihashi and M Yamabe, Chemistry and Electrochemistry of the ChlorAlkali Process2018年7月3日 Request PDF Industrial Production of Limestone Calcined Clay Cement (LC 3 ) – Experience and Insights The reduction of the clinker factor in cement has emerged as the most promising solution Industrial Production of Limestone Calcined Clay Cement (LC 3
.jpg)
(PDF) Usage of Recycled Alkali Waste for Delamination
2023年7月6日 Usage of Recycled Alkali Waste for Delamination of Cathode Electrodes: Systematic Selection and Optimization of Hydrometallurgical Approachii table of contents 1 introduction 1 2 limestone quarrying and processing operations 2 21 limestone 2 22 limestone quarrying operations 2 23 limestone processing operations 3 3 lci methodology 5 31 lci data collection 5 32 quality of lci data set 5 331 limestone quarry operations 5 332 limestone processing operations 6 4 lci results 7Limestone Quarrying and Processing: A LifeCycle Inventory2017年5月1日 This new chloralkali process consists of three independent steps: a NaOHproduction step in a Na044MnO2/oxygendepolarizing cathode (ODC) cell (step I), a Na+ and CI extraction step in an Ag Life Cycle Assessment model for the chloralkali process: A In general, dimension stone production comprises three phases: exploration, quarrying and processing Following the exploration phase, which includes volume estimation, stone characterization and Quarrying and processing of dimension stones ResearchGate
.jpg)
EnergyModel and Life CycleModel for Grinding Processes of Limestone
2022年5月22日 Normalized and weighted values in the wet grinding process in nanograms (Functional unit: 1 kg of limestone product Impact assessment method: CML 2001/Aug 2016Random screened limestone is still used for traditional dry stone walling builders The highest grade is monumental stone This is a very uniform limestone with few surface imperfections These properties make it ideal for carving and limestone of this class can hold very fine detail when used in sculpture, headstones, plaques, or ornamental The Processing and Major Uses of Limestone Academia2005年11月1日 Download Citation Review—calcination and carbonation of limestone during thermal cycling for CO2 capture Some aspects of using lime from limestone to sequester CO2 from combustion systems Review—calcination and carbonation of limestone during 2024年8月15日 Despite the majority of EU countries with competitive cement and lime sectors reported 44% of electricity production from renewable and nuclear sources in 2020, the adoption of the Microwave Continuous Processing Technology with ≈ 50 % of global efficiency in processing limestone does not significantly aid in reducing kg CO 2 eq / kg CaCO 3 for these Modelling and energy efficiency analysis of the microwave
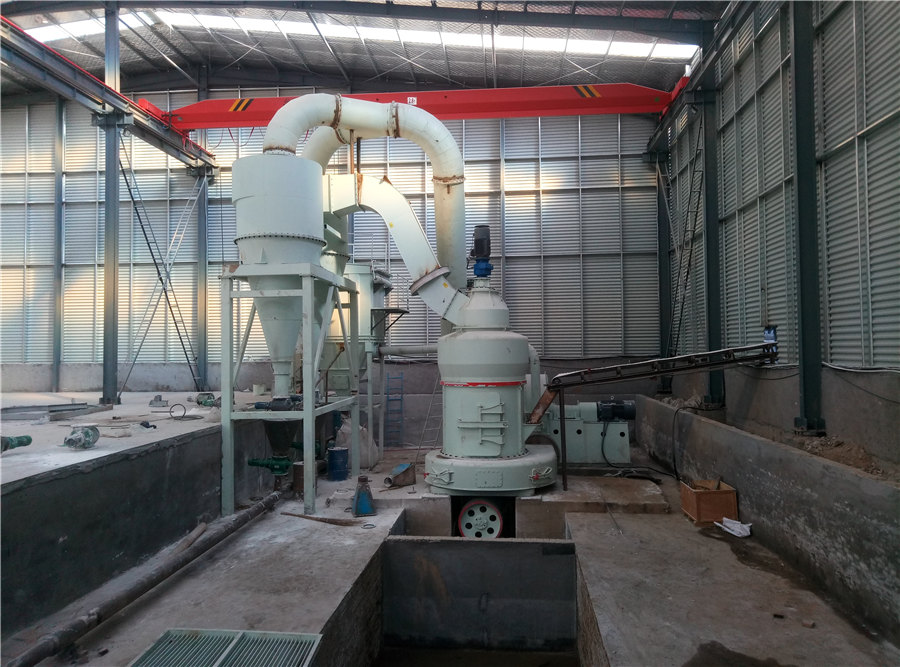
Limestone Mining, Industry, and Society SpringerLink
2021年7月15日 Three keywords (ie, industry, society, and limestone mining) are important to describe this chapter in continuation of the preceding chapter, which explained the mining or excavation process If we analyse the above three aspects, the relationships that exist2022年9月27日 The extensive usage of concrete and ordinary Portland cement has generated 5~8% of annual global CO2 emissions, causing serious environmental problems To reduce such environmental impact, researchers have made significant efforts to develop alternative materials that may partially or entirely replace the ordinary Portland cement, such as limestone calcined A Review on Hydration Process and Setting Time of Limestone2024年6月1日 The cement industry plays a critical role in global carbon emissions, primarily due to the release of CO 2 during the production of cement The process of cement production involves the transformation of raw materials, such as limestone and clay, into clinker, which is a powdered form of cementDecarbonising cement and concrete production: Strategies, 2020年8月9日 This review will show that lowCO2 cements can be produced to give superior durability, based on a sound understanding of their microstructure and how it impacts macroengineering properties For example, it is essential that aluminium is available in calciumrich alkaliactivated systems to offset the depolymerisation effect of alkali cations on C(N)ASH A Roadmap for Production of Cement and Concrete with LowCO
.jpg)
Utilization of hydrogen as clean energy resource in
2019年3月31日 The production of Cl 2 is calculated based on the stoichiometric equation (5) and found to be 62,125 kg/day based on 70,000 kg/day production of NaOH in the selected chloralkali industrial process Moreover, 1750 kg/day of 2011年1月1日 PDF Local production of ashderived alkali was assessed in this review Detailed information on local production of ashderived alkali is rare in Find, read and cite all the research you (PDF) The Ancient Alkali Production Technology and the 2021年11月1日 This article reviews the production and development of China's FGD gypsum in the past 20 years, and determines its production process, composition, and environmental impact The current beneficial utilization and latest research of FGD gypsum are summarized, and its utilization methods, principles, feasibility, environmental impact, and application prospects are Production and resource utilization of flue gas desulfurized 2017年2月15日 The function of the chloralkali process is the combined production of chlorine, caustic soda and hydrogen The process manufactures in a fixed ratio 1 ton of chlorine, 113 ton of caustic soda (sodium hydroxide) and 003 ton of hydrogenEnvironmental challenges of the chloralkali production:
.jpg)
(PDF) Nickel Laterite Smelting Processes and Some ResearchGate
2019年9月3日 production process, the ESS process, the V aniukov process, and the reduction roasting–magnetic separation process are presented in T able 1 Among these, the RKEF process has the highest recovery2013年5月17日 The chloralkali process has come a long way from the days of the diaphragm and mercury cell process to the present membrane cell process, with huge reduction in power consumption and hence its carbon footprint Although there is reduction in the release of highly toxic mercury to the environment, there is increased release of less harmful substances such The chloralkali process: Work in Progress SpringerUsually, limestone (CaCO 3) and lime (CaO) are used as Ca(OH) 2 sources thanks to their abundance and low cost Due to its low solubility, limestone needs to be pulverized in order to be used in the FGD process, adding cost and energy expenditure to the process Kikkawa et al (2002) tried to scrub SO 2 from FGD without limestone size reductionRecent advances in flue gas desulfurization gypsum processes and 2016年7月2日 The chloralkali process of sodium hydroxide production emits SO 2 and halogenated compounds from electricity consumption during the electrolytic phase [82]The chloralkali process: A review of history and pollution
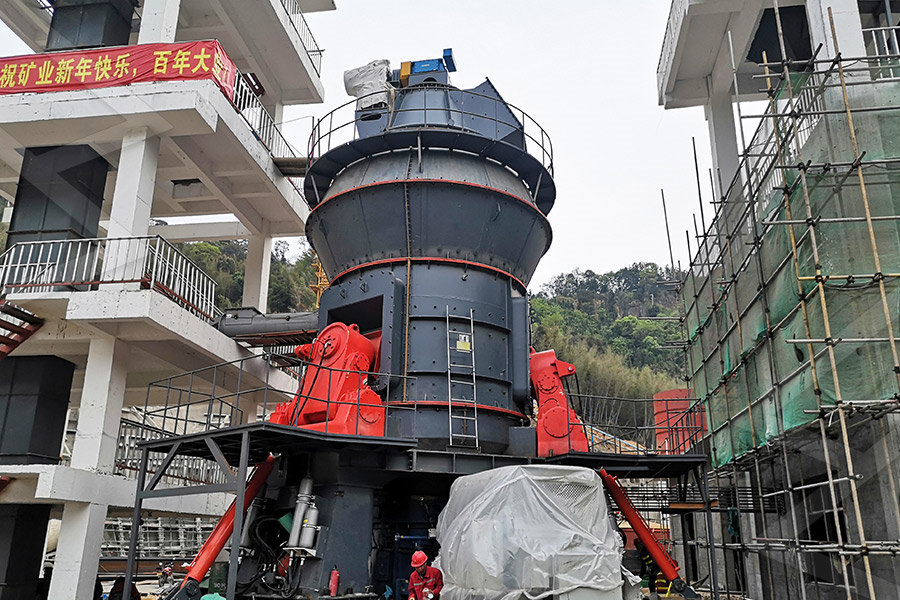
Effects of OverSintering on Cyclic Calcination and MDPI
2024年9月7日 To know the sustainable performance of calciumbased adsorbents is one of the important aspects to realize efficient and economical carbon capture, and to systematically study the properties of natural adsorbents is conducive to their industrialization The cyclic calcination and carbonation characteristics of a typical natural limestone were investigated using a 2007年12月21日 When the choice of the raw material falls on marly limestone composed of 6520 wt% clays, the production process is obviously characterized by different temperatures and times and the finished Lime and Limestone: Chemistry and Technology, Production and 2020年6月5日 Limestone calcined clay cements (LC3) are blended cements that combine clinker, limestone, calcined clay and gypsum The availability of the materials required to produce LC3 and the good Limestone calcined clay cements (LC3): raw material processing, 2020年9月27日 In this study, a foamed alkaliactivated glass (FAAG) via the use of milled waste glass was synthesized in lowtemperature (ie, 80°C) The influence of foaming agent (ie, aluminum powder) content on the foaming process of samples was investigated and optimized in view of their performanceWaste Glass Reuse in Foamed AlkaliActivated Binders Production
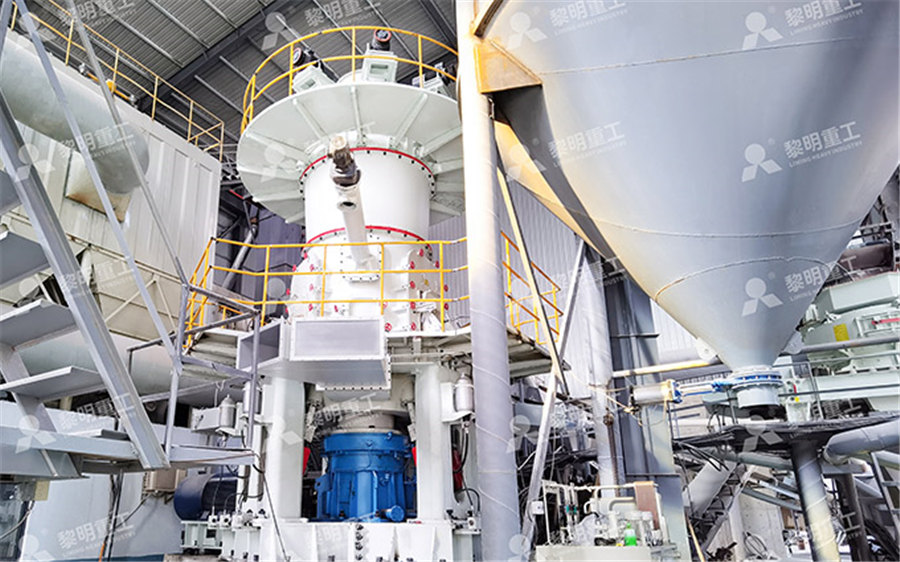
Spray drying absorption for desulphurization: a review of
2021年3月17日 The performance of a wet FGD system is greatly influenced by gas–liquidphase mass transfer, ieof Ca 2+ ions in the liquid phase and of SO 2 from the gas phase to the aqueous phase (Hrdlička and Dlouhý 2019)This is further influenced by the rate of dissolution of limestone in the system, directly affecting the concentration of dissolved ions in the slurry This white paper will distill the complicated art of chloralkali membrane selection—and subsequent system optimization—into key best practices and considerations to help manufacturers achieve a oneofakind operation The ChlorAlkali Processing Landscape processing: mercury or diaphragm cell Today,ChlorAlkali Process Efficiency: A Balancing Act Chemours2022年12月29日 More than half of the CO2 emissions during the manufacturing of ordinary Portland cement (OPC) occur due to the calcination of calcium carbonate in addition to burning of fossil fuel to power the process Consequently, there is a concerted effort to decrease the carbon footprint associated with this process, by minimizing the use of OPC In line with this trend, an Synthesis of waste limestone powder–based alkaliactivated 2016年1月1日 On August 3, 1888 German Patent No 43977 entitled “A Process for the Production of Aluminum Hydroxide” was issued** The discovery which led to the patent was made by the Austrian chemist A Hundred Years of the Bayer Process for Alumina Production

Chemistry and Electrochemistry of the ChlorAlkali Process
M Seko, IonExchange Membrane for the ChlorAlkali process, ACS Polymer Division Workshop on Perfluorinated Ionomer Membranes, American Chemical Society, Lake Buena Vista, Florida, Feb 1982 Google Scholar H Ukihashi and M Yamabe, 2018年7月3日 Request PDF Industrial Production of Limestone Calcined Clay Cement (LC 3 ) – Experience and Insights The reduction of the clinker factor in cement has emerged as the most promising solution Industrial Production of Limestone Calcined Clay Cement (LC 3