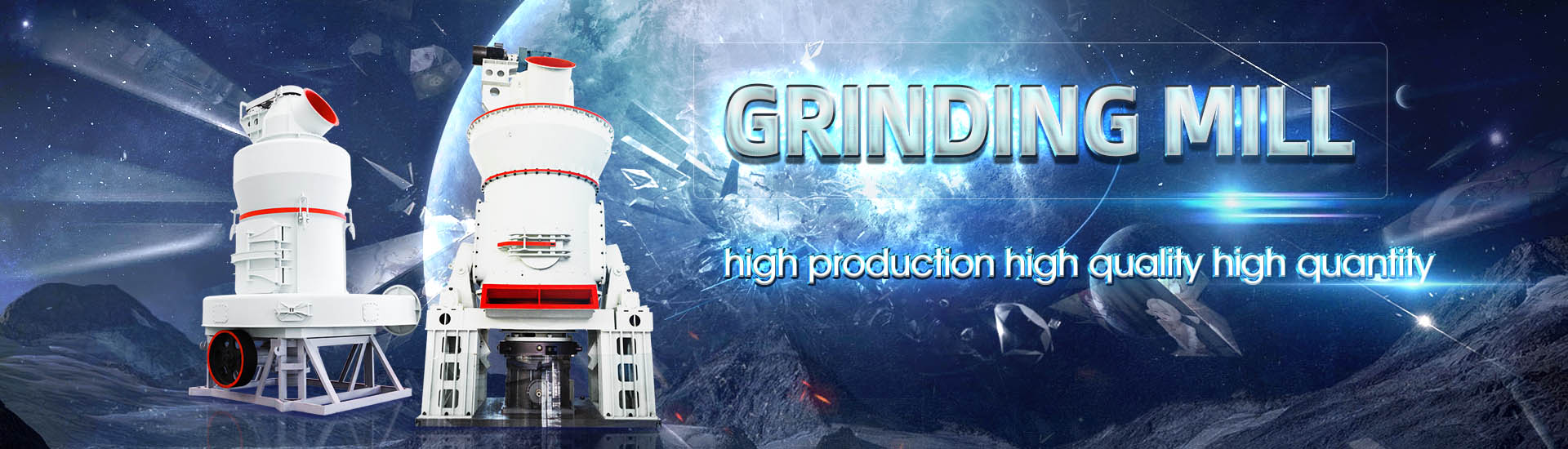
Blast furnace coal powder making process
.jpg)
Blast Furnace Process an overview ScienceDirect Topics
In addition, some steel producers use powder injection coal (PCI) or other sources of hydrocarbon (such as used motor oil) at the tuyeres with the preheated air The purpose of PCI and hydrocarbon additions is to decrease the coke rate which is defined as the amount of coke 2024年6月15日 Coke plays an irreplaceable role in blast furnaces (BFs), acting as both the skeleton of the stock column and the permeable layer of the gas flow Thus, examining the Physical and chemical properties of metallurgical coke and its In the basic process, the input materials a combination of sinter, iron pellets, limestone and cokes enter a blast furnace (BF) to be converted into molten pig iron The pig iron is then © IEA ETSAP Technology Brief I02 May 2010 etsap 2017年10月10日 Blast furnacing, smelting and direct iron reduction are the current ironmaking processes Iron is made by reacting iron ore (iron oxide and impurities), coke (a reductant) and limestone (CaCO 3) in a blast furnace Iron Ironmaking 101 – From Ore to Iron with Blast Furnaces
.jpg)
NPTEL :: Metallurgy and Material Science NOC:Ironmaking and
Lecture 11: Aerodynamics in Blast FurnacePart 1: Download: 12: Lecture 12: Aerodynamics in Blast FurnacePart 2: Channeling: Download: 13: Lecture 13: Aerodynamics in Blast Furnace 2018年6月21日 In the blast furnace, the iron ore reacts with the carbon contained in the coke to form grey or white pig iron Combustion process The iron in the processed ores must be dissolved out by chemical processes This Blast furnace process tecscienceinnovations to blast furnaces: recycled materials, such as waste plastics and biomass, as well as recycled ores can be injected with pulverized coal into the furnaces via tuyeres3A2 Pulverized Coal Injection for Blast Furnaces (PCI)2024年1月1日 Pulverized coal injection of blast furnace ironmaking is a smelting technology where pulverized coal is directly blown into the blast furnace hearth from the tuyere to replace Pulverized Coal Injection of Blast Furnace Ironmaking
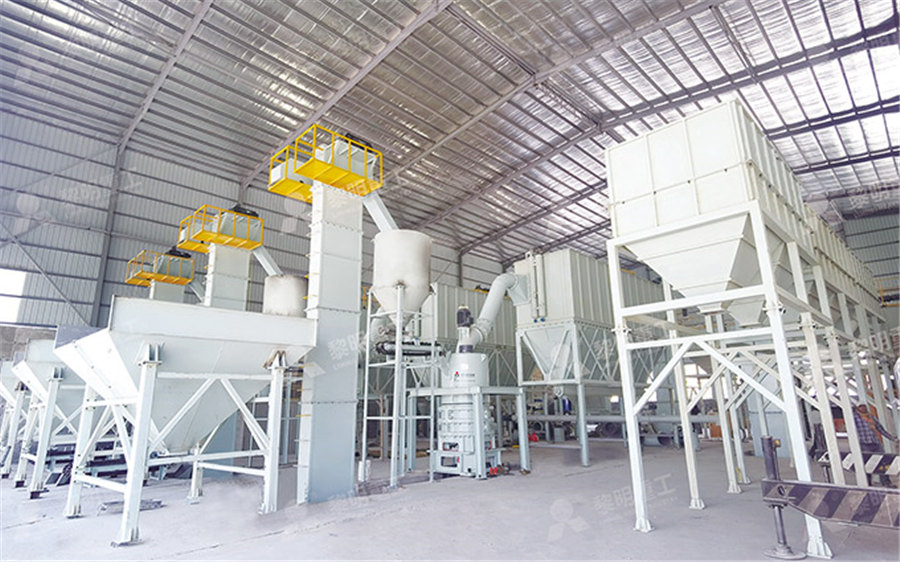
Blast Furnace Process SpringerLink
2020年3月3日 In the blast furnace process, ironbearing materials (eg lumps iron ore, sinter/pellets, mill scale and steelmaking slag), coke (fuel as well as reducer) and flux 2023年10月6日 Blast furnace ironmaking is a continuous metallurgical process in which iron ore is reduced to liquid pig iron in a blast furnace It is developed and improved from the ancient Blast Furnace Ironmaking SpringerLink2013年5月10日 Fig 1 Typical flow sheet of pulverized coal injection in blast furnace The process of coal injection The PCI process is based on the simple concept of carrying the finely ground (pulverized) dried coal by a conveying Pulverized Coal Injection in a Blast Furnace – On the completion of sintering process, finished sinter cake is crushed and cooled The cooled sinter is screened and + 6 mm fraction is despatched to blast furnace and 6 mm is recirculated as return sinter BLAST FURNACE The Blast furnace iron making process basically consists of the conversion of iron oxide to iron in liquid form Coke OvensSinterBFBOF Route SAIL
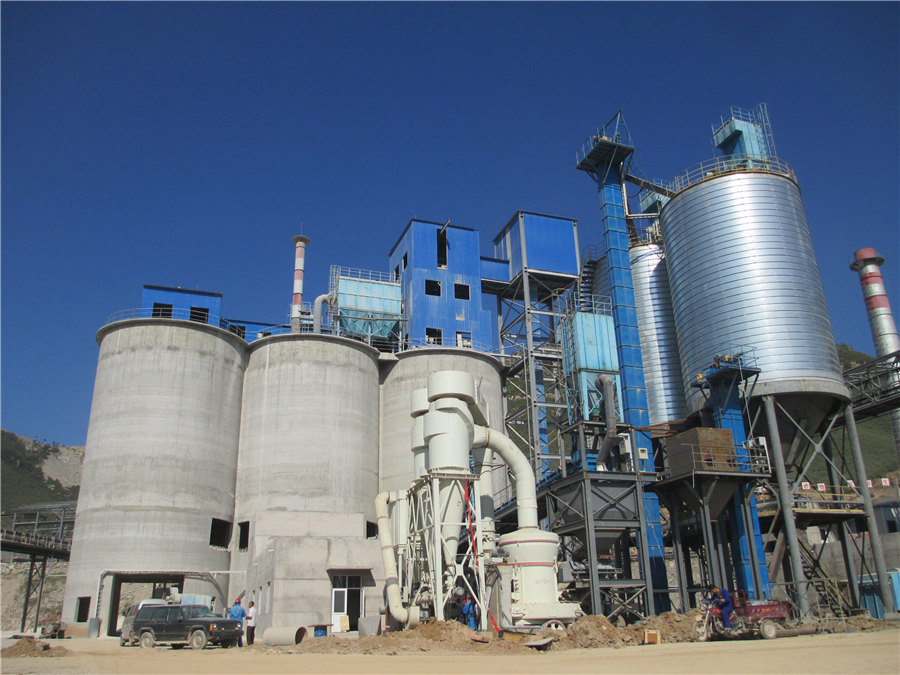
Iron processing Smelting, Refining, Alloying Britannica
Iron processing Smelting, Refining, Alloying: The primary objective of iron making is to release iron from chemical combination with oxygen, and, since the blast furnace is much the most efficient process, it receives the most attention Former AHM blast furnace in Port of Sagunt, Valencia, Spain A blast furnace is a type of metallurgical furnace used for smelting to produce industrial metals, generally pig iron, but also others such as lead or copper Blast refers to the combustion air being supplied above atmospheric pressure [1]In a blast furnace, fuel (), ores, and flux are continuously supplied Blast furnace Wikipedia2017年10月10日 Natural or direct shipping iron ores contain between 5070% iron and can be fed directly into the blast furnace Fe 3 O 4 decomposes when heated to ferrous oxide (FeO) and ferric oxide (Fe 2 O 3) via Fe 3 O 4 → FeO + Fe 2 O 3 A specialized type of coal, called hard coal, is used to make coke, a porous form of carbonIronmaking 101 – From Ore to Iron with Blast Furnaces2021年4月21日 Blast furnacebasic oxygen furnace (BFBOF): This is the dominant steel production route in the iron and steel industry, involving the reduction of iron ore to pig iron in the blast furnace BFBOF operation relies almost entirely on coal products, emitting ∼70% of CO 2 in the integrated plant (BF iron making)Lowcarbon production of iron and steel: Technology options, economic
.jpg)
Iron and SteelMaking Process SpringerLink
2020年6月10日 Blast furnace iron making is the most popular process for extraction of iron from its ores Other wellknown processes are EAF and Direct Reduction Iron (DRI) processes However, blast furnace will continue to be the most efficient route to produce pig iron for its high productivity and cost optimization, for many years to come [1, 2]Although the Romans built furnaces with a pit into which slag could be run off, little change in ironmaking methods occurred until medieval times By the 15th century, many bloomeries used low shaft furnaces with water power to drive the bellows, and the bloom, which might weigh over 100 kilograms, was extracted through the top of the shaft The final version of this kind of bloomery Iron processing Definition, History, Steps, Uses, Facts2 blast furnace and the Kobe No 3 blast furnace in 1983, as the "Kobelco system" Following that, ARMCO systems were introduced into Nippon Steel’s Nagoya No 1 blast furnace and Nisshin Steel Kure No 2 blast furnace, which entered commercial operation in 1984 In 1986, pulverized coal injection equipment3A2 Pulverized Coal Injection for Blast Furnaces (PCI)2021年7月15日 The blast furnace is an ultrahigh efficiency reactor, so it is a regret that the ironmaking process completely abandons the blast furnace route Consequently, China will start from the principles of reduction and slagging reactions in blast furnaces, seek technical routes to significantly reduce carbon consumption, and continue to explore lowcarbon routes for blast A review on low carbon emissions projects of steel industry in the
.jpg)
Blast Furnace Process Steel Museum
Molten iron is produced in a blast furnace by the following steps: 1 Charge (solid iron ore, coke, and limestone) is constantly dumped into the top of the furnace 2 A blast of hot air is blown into the furnace from the bottom 3 Coke is the fuel 2021年3月8日 Blast Furnace – Basic Oxygen Furnace (BFBOF): This is the dominant steel production route in the iron and steel industry, involving the reduction of iron ore to pig iron in the blast furnace BFBOF operation relies LowCarbon Production of Iron Steel: Technology 2017年3月22日 In this process, iron ore is reduced mainly by coke in the blast furnace (BF) This coke also produces the required heat by reacting with the available oxygen (from the hot blast and the FeO) The liquid hot metal (HM) Sulphur removal in ironmaking and oxygen 2013年11月22日 Chemistry of the Ironmaking by Blast Furnace Process satyendra; November 22 or coal in either pulverized or granular form In such cases, the carbon in the fuel burns to CO, but because of the large carbon deposition can cause ore pellets or sinter to crumble into powder and this can cause irregular gas flow and uneven Chemistry of the Ironmaking by Blast Furnace Process
.jpg)
Blast Furnace Tip: Gold Ore + Coal Bag Method : r/ironscape
When making gold bars at blast furnace, you can keep the coal bag in your inventory and use it to also deposit coal to the furnace at the same time Once you have deposited around 250 coal, switch to making the bars of your choice (mithril, adamant, rune typically) until most of the coal is used Then go back to making gold bars and depositing 2021年7月25日 Industrial and process furnaces: Principles, design and operation Elsevier Google Scholar Ryman, C (2007) On the use of process integration methods: evaluation of energy and CO 2 emission strategies in blast furnace iron making and oxygen steelmaking, Doctoral dissertation, Luleå tekniska universitetDataDriven Optimization of Blast Furnace Iron Making Process 2017年8月10日 The top gas recycling oxygen blast furnace (TGROBF) is a new ironmaking process which can significantly reduce the coke ratio and emissions of carbon dioxide To better understand the coal combustion characteristics in the TGROBF, a three dimensional model was developed to simulate the lance–blowpipe–tuyere–raceway of a TGROBF The combustion Coal Combustion Behavior in New Ironmaking Process of Top A coke oven at a smokeless fuel plant, Abercwmboi, South Wales, 1976 The industrial production of coke from coal is called coking The coal is baked in an airless kiln, a "coke furnace" or "coking oven", at temperatures as high as 2,000 °C (3,600 °F) but usually around 1,000–1,100 °C (1,800–2,000 °F) [2] This process vaporises or decomposes organic substances in the coal, Coke (fuel) Wikipedia

Modelling of blast furnace ironmaking process based on digital
Blast furnace ironmaking is the process of directly or indirectly reducing iron ore to produce pig iron by using carbon‐based fuels such as coke and coal powder and generating carbon oxides and hydrogen Ore and coke are added from the top of blast furnace, while air and coal injection are introduced from the lower tuyere of blast furnace2020年3月3日 Metal composition is not a critical feature of the blast furnace process because (ie orecokestoneorecokecoke) Hot blast is blown from the tuyeres, along with hydrocarbon gas, and oil or powder coal is YB (2020) Blast Furnace Process In: Basic Concepts of Iron and Steel Making Springer , Singapore https Blast Furnace Process SpringerLinkPulverized coal injection (PCI) is employed in blast furnace tuyeres attempting to maximize the injection rate without increasing the amt of unburned char inside the stack of the blast furnace When coal is injected with air through the injection lance, the resolidified char will burn in an atm with a progressively lower oxygen content and higher CO2 bustion Characteristics of Coal for Pulverized Coal 2023年10月6日 The smelting process of blast furnace is carried out in the shaft furnace of a closed countercurrent reactor and heat exchanger The complex physical changes and chemical reactions are completed in the process of the countercurrent movement of the charge and gas in which the raw materials containing iron oxide (sinter, pellets, etc), coke, slag flux (limestone) Blast Furnace Ironmaking SpringerLink
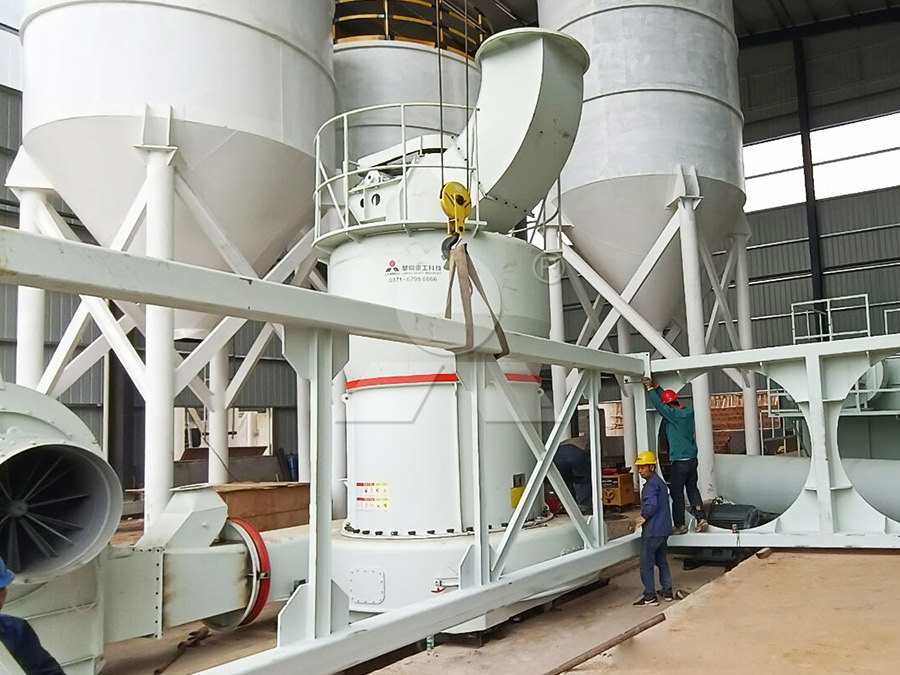
233: Metallurgy of Iron and Steel Chemistry
Coke is a form of carbon formed by heating coal in the absence of air to remove impurities The overall reaction for the production of iron in a blast furnace is as follows: \[\mathrm{Fe2O3(s) +3C(s)\xrightarrow{\Delta}2Fe(l) +3CO This 2012年8月2日 Global steel production is based on the refining of liquid pig iron in basic oxygen converters No technologies that do not use liquid pig iron are expected to replace this method in the coming decades, and ore and coal will remain the main raw materials used to make pig iron Existing technologies that produce liquid pig iron outside the blast furnace are considerably The blastfurnace process – is there any alternative?2023年9月8日 A stable and efficient operation of the ironmaking blast furnace is prerequisite to reduce the greenhouse gas emission JSW Steel, Salem have been proposed many projects to reduce greenhouse gas Blast Furnace process optimization for sustainable Iron making2024年10月11日 Blast furnaces produce pig iron from iron ore by the reducing action of carbon (supplied as coke) at a high temperature in the presence of a fluxing agent such as limestoneIronmaking blast furnaces consist of several zones: a crucibleshaped hearth at the bottom of the furnace; an intermediate zone called a bosh between the hearth and the stack; a Blast furnace Definition, Temperature, Diagrams, Facts
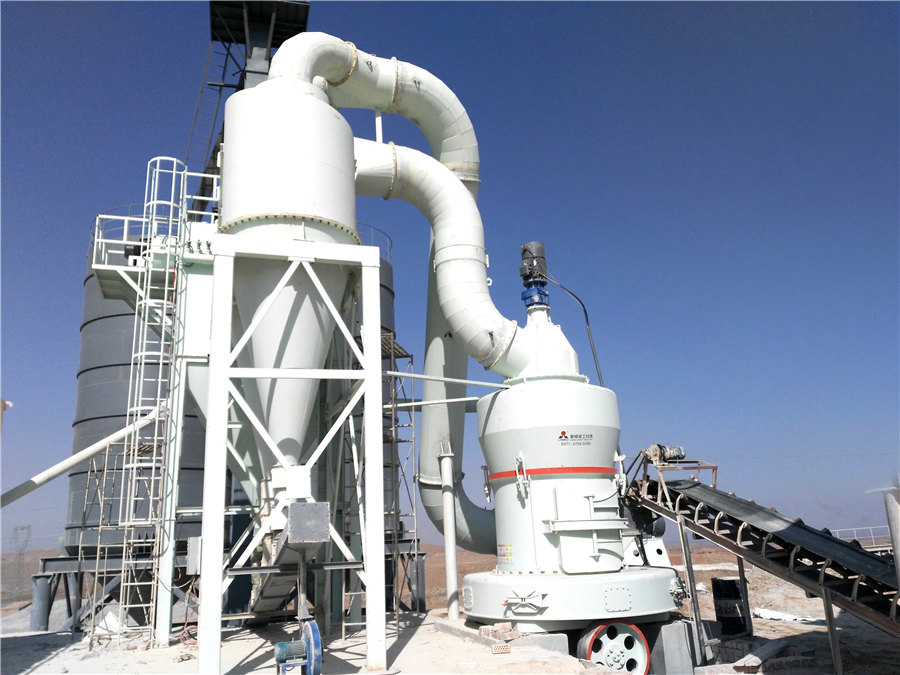
Thermal reactivity and flowability of pulverized coal blending with
2023年1月1日 Pulverized coal (PC) blending with ironbearing dust (IBD) injection technology in blast furnace (BF) ironmaking process was proposed to valorize the IBD Three aspects containing the coflow property of PC and IBD, The Carrflowability index (F) of single powder (Coal A, Coal B, Coal C and IBD) is shown in Fig 3 a, 2024年3月4日 Blast furnace dust (BFD) is the solid powder and particulate matter produced by dust removal process in ironmaking industry The element composition of BFD is complex, and a direct return to sintering will lead to heavy metal enrichment and blast furnace lining corrosion In recent years, the application of BFD in wastewater treatment has attracted widespread Review in application of blast furnace dust in wastewater 2019年9月8日 The blast furnace iron making process (BFIMP) is the key of the integrated steel enterprise for energy saving due to its largest energy consumption proportionAn AllFactors Analysis Approach on Energy Consumption for the Blast Once a blast furnace is started it will continuously run for four to ten years with only short stops to perform planned maintenance The Process Iron oxides can come to the blast furnace plant in the form of raw ore, pellets or The coal is crushed HOW A BLAST FURNACE WORKS Foundry Gate
.jpg)
Pulverized Coal Injection of Blast Furnace Ironmaking
2024年1月1日 The blast furnace injection process system is mainly composed of raw coal storage and transportation system, dry gas preparation system, pulverized coal preparation system, pulverized coal conveying system, pulverized coal injection system, and gas supply system (Fig 1)There is also a computer control center to control the entire pulverized coal 2024年10月1日 Using FLUENT software, a EulerLagrange threedimensional numerical model was constructed to analyze the influence of different positions of blast furnace tuyere coal powder injection lance (coaxial and crossaxis) on key parameters such as temperature distribution, gas flow, and combustion efficiencyNumerical simulation of the effect of coaxial and crossaxis 2016年4月8日 Blast furnaces are countercurrent chemical reactors, widely utilized in the ironmaking industry Hot reduction gases injected from lower regions of the furnace ascend, reacting with the descending burden Through Comprehensive Numerical Modeling of the Blast 2023年8月1日 At present, the blast furnace ironmaking process mainly includes sintering process, coking process, pelletizing process and pulverized coal injection process To study the environmental impact of biomass hydrochar injection on the blast furnace ironmaking process, the environmental impact before and after the application of biomass hydrochar was evaluatedLife cycle assessment of blast furnace ironmaking processes: A
.jpg)
CO2 Emission Reduction in Blast Furnaces SpringerLink
2016年9月3日 Blast furnace (BF) represents the dominant hot metalmaking process all over the world and one of the main energyconsuming processes Modern research in the field focuses on the increase in plant productivity through energy saving and on the greenhouse emission reduction compatible with legal limits2024年3月19日 The Blast Furnace (BF) is a furnace used in the ironmaking process It uses iron ore and limestone as input, metallurgical coal (converted to coke) as a reducing agent, and creates pig iron (also known as crude iron or hot metal) as output This pig iron can then be used in other furnaces, like the Basic Oxygen Furnace (BOF) or Electric Arc Furnace (EAF), to Blast furnace Global Energy Monitorblast furnace construction Modernisation 06 07 stockhouse charging systems 08 09 blast furnace top charging technology – the original 10 11 blast furnace Design: the blast furnace Proper, lining cooling 12 13 hot blast generation supply 14 15 Puvlesried c oal nIej ction 16 17 gas cleaning and energy recovery 18 19BLAST FURNACE TECHNOLOGY Paul WurthCoal Carbonization John C Crelling, in Applied Coal Petrology, 2008 71 Introduction Metallurgical coke, along with iron ore (iron oxides) and limestone, is layered into a blast furnace to convert the iron ore to metallic ironThe coke, which is mostly carbon, reacts with the blast air to produce carbon monoxide, which in turn reacts with the iron oxide to produce carbon dioxide Metallurgical Coke an overview ScienceDirect Topics
.jpg)
Iron Ore Pelletizing Process: An Overview IntechOpen
The iron ore production has significantly expanded in recent years, owing to increasing steel demands in developing countries However, the content of iron in ore deposits has deteriorated and lowgrade iron ore has been processed The fines resulting from the concentration process must be agglomerated for use in iron and steelmaking This chapter shows the status of the 2011年5月1日 The work reported in this paper studies the potential of injecting biomass to partially replace fossil reductants in the blast furnace process The ironmaking blast furnace process is described Substitution of Biomass for Coal and Coke in Ironmaking Process