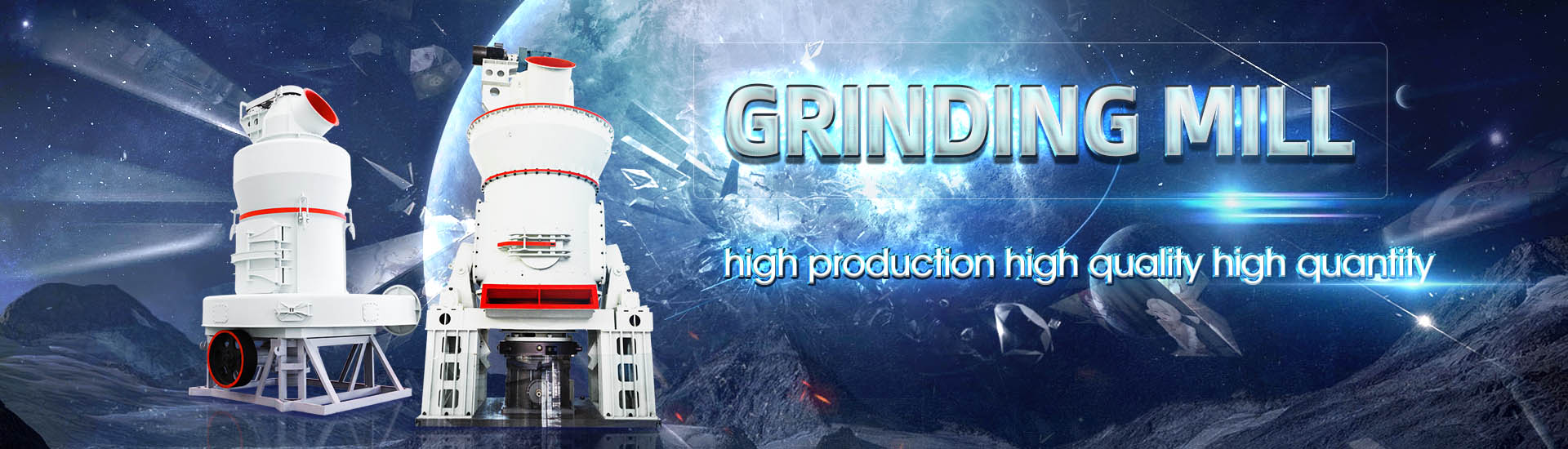
Slag mill to increase production
.jpg)
Carbon mineralization of steel and ironmaking slag: Paving the
2024年4月1日 With an increase in the operating temperature, pressure, and CO 2 gas concentration, the driving force for CO 2 diffusion to the surface of unreacted slag is 2022年10月13日 Considering a production range of 150–180 kg of electric arc furnace slag (EAF) per tonne of steel produced, slag amounted to around 325 million tonnes in 2019 (to Exploring the Potential for Steel Slags Valorisation in an Industrial 2021年10月5日 Slags are a coproduct produced by the steel manufacturing industry and have mainly been utilised for aggregates in concreting and road construction The increased Production, characterisation, utilisation, and beneficial soil 2019年10月29日 The large volume production of slag from iron and steelmaking process and the tightened regulation on the slag disposal urge engineers and researchers to explore the way which can massively use the The potential utilization of slag generated from iron
.jpg)
(PDF) Industrial uses of slag The use and reuse of iron
2005年2月1日 Steelmakers have made attempts to reduce slag volumes in the individual unit processes and to strive towards slagless steelmaking by recycling slags internally A much improved understanding of2012年2月8日 This article presents a review of the slag energy potential on a global scale, and a proposal for a recovery plant in the factories of ArcelorMittal in Asturias (Spain), based on a Steel mill slags energy potential: the case of the steel factory of Basic oxygen steelmaking (BOS) slag, a product of hot metal element (eg, Si, Mn, Fe, P) oxidation and flux (eg lime, dolomite) dissolution, plays a critical role in the production of highquality crude steel, although its behavior inside the Basic Oxygen Steelmaking Slag: Formation, Reaction, 2017年3月5日 In this chapter, the types of iron and steel industries are first illustrated The physicochemical properties of four different types of iron and steel slags, including blast furnace slag, basic(PDF) Iron and Steel Slags ResearchGate
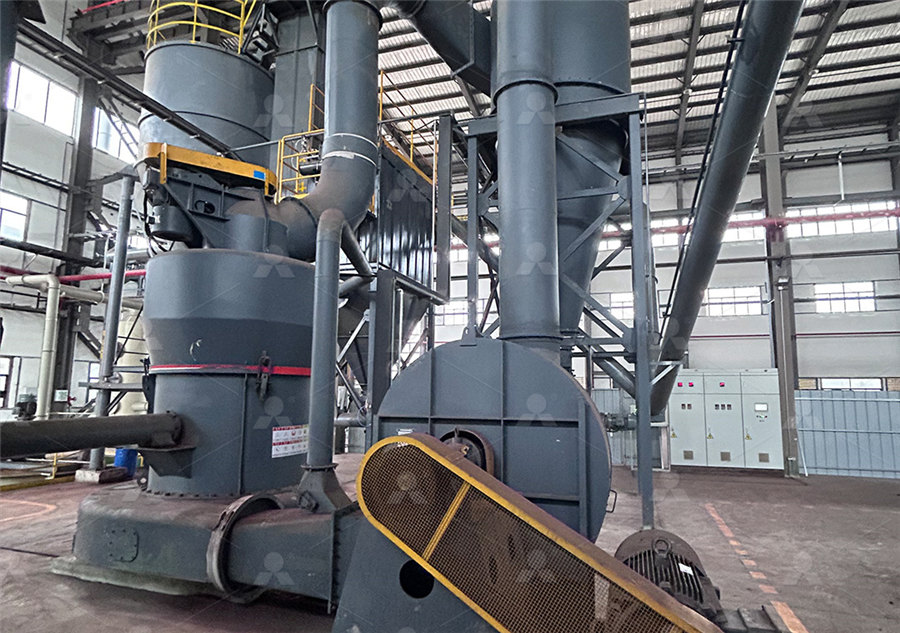
Utilization of steelmaking slag in cement clinker production: A
2024年6月1日 Steelmaking slag has promising potential for cement clinker production, boasting high levels of CaO Pretreatment methods enhance slag quality for cement production Slag 2015年9月20日 PDF The new practice of applying full precrushing of SAG mill feed to substantially increase throughput is challenged as retrogressive and Find, read and cite all the research you need on (PDF) FULL PRECRUSH TO SAG MILLS ResearchGate2015年9月7日 It is also crucial that the user has knowledge about the process, and potential changes in the plant that can cause process drift For example, liner wear can greatly affect SAG mill performance Understanding the effects of liner wear on SAG mill The simulation of the digital model captures an increase in production of 442% as a function of mineral fragmentation, while there is potential to increase production by decreasing the mill Schematic diagram of AG/SAG mill process
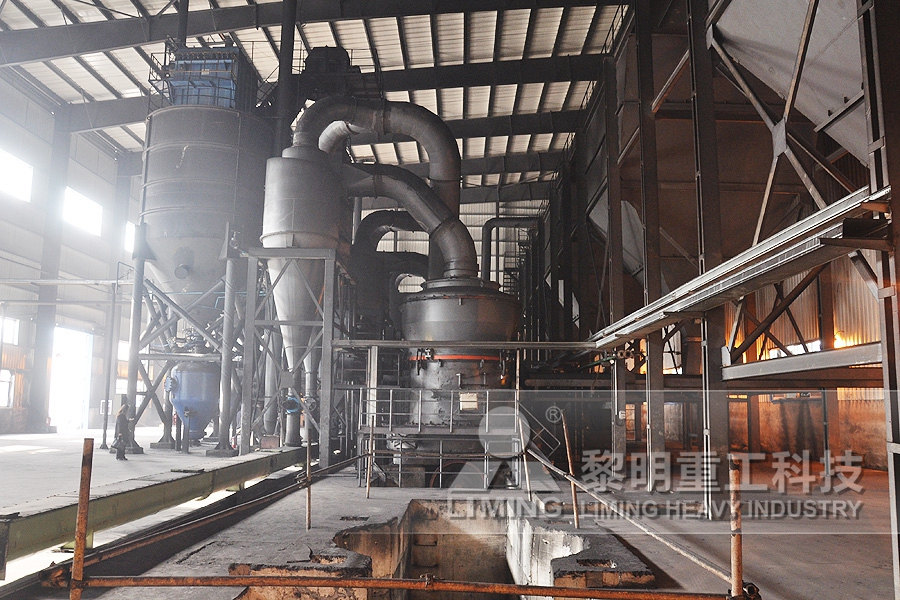
SAG mill compared to crusher and ball mill product size
Download scientific diagram SAG mill compared to crusher and ball mill product size distributions (Powell et al 2014) from publication: FULL PRECRUSH TO SAG MILLS – THE CASE FOR CHANGING THIS 2024年6月1日 mill speed, and the slurry density, allowing us to accurately model the performance and wear of our mill liners This includes predicting the liners’ wear life to avoid unscheduled downtime and to extend the time between replacements” Emphasizing that no two mill liner applications are identical,THE FUTURE OF SAG MILLS Ausenco2001年1月1日 Increasing the powder factor by 150% from the 029kg/t {058lb/st] being used to 072kg/t { 144lb/st}, the maximum feasible with mine equipment, could provide a signant net benefit of $3OWyr due to the increased concentrate productionAdjusting Blasting to Increase SAG Mill Throughput at the Red 2021年1月9日 In 1998, AgnicoEagle decided to expand production capability from 750,000 short tons per year to 1,300,000 TPY, initially by adding a SAG mill to the existing twoball mill grinding circuit As exploration results showed increasing ore reserve potential, concentrator throughput increase to 1,800,000 TPY was being studiedPage 1 INTRODUCTION SAGDesign
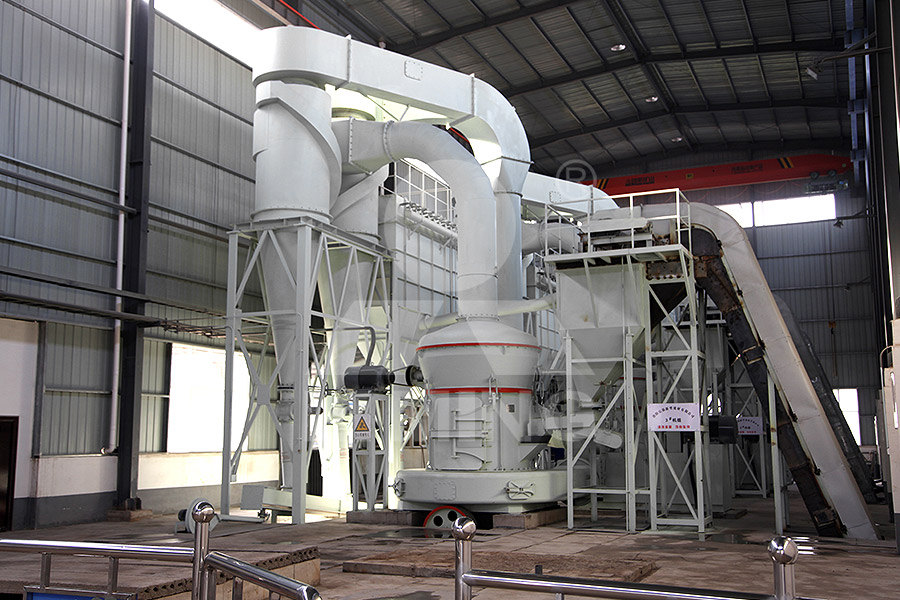
BrainWave SAG mill Andritz
The solution for increasing production in the SAG mill With improved SAG mill control stability, the mill load can be optimized to increase crushing performance and production capacity Contact us ANDRITZ Inc United States of America +1 (770) 640 2500 automationsales@andritz• Maximise power drawn by increasing mill speed while minimising direct shell impacts • Increase SAG mill availability by increasing liner life • Reduce onset of slurry pooling at increased feed rates As part of the liner evaluation, six vendor designs were compared, and their performances benchmarked against the base case liner systemMill Operators’ Conference 年6月6日 As mill sizes increases, the required volumetric capacity of the pulp lifters grows proportionally to mill volume Since AG/SAG mill volume is roughly proportional to the mill radius cubed (at typical mill lengths) while the available crosssectional area grows only as the radius squared, pulp lifters must become more efficient at transferring slurry in larger millsSAG Mill Liner Design 911MetallurgistAccordingly, the mill power consumption decreased from 84 to 516 kWh/t (a nearly 40% reduction), and the fresh feed flow rate increased from 515 to 615 t/h (a nearly 20% increase in the mill Correlation Between F80 and Mill Performance for
.jpg)
Optimal Speed Control for a SemiAutogenous Mill
2020年2月18日 The rotation speed of a mill is an important factor related to its operation and grinding efficiency Analysis and regulation of the optimal speed under different working conditions can effectively reduce energy loss, improve exhibits many of these aspects Maintaining the SAG mill weight at the optimum value is critical for achieving maximum grind rate efficiency and mill production (Powell, MS, van der Westhuizen, AP, Mainza, AN 2009) However, SAG mill weight is difficult to control as the dynamic response changes as the mill approaches maximum capacitySAG Mill Optimization using Model Predictive Control Andritz2How to Increase the Output of a Steel Slag Ball Mill? Increasing the rotational speed of the mill cylinder can enhance the centrifugal force acting improving its performance As a byproduct of steel production, steel slag can be ground into fine powder and reused in steel production Additionally, steel slag powder can serve as an Steel slag Ball Mill CEMENTL1993年11月1日 SAG mill throughput is often a bottleneck to increasing plant productivity Improved size distribution control in the mill feed can be used to increase mill production This can be accomplished by controlling blast fragmentation as a function of energy input and rock characteristics Such an approach requires the integration of rock fragmentation and Blasting design for increased SAG mill productivity
.jpg)
Slag grinding mill micro powder production line SBM Ultrafine
2022年5月12日 In industrial production, slag plays an important role ball mills, powder separators, dust collectors and fans The dried slag is sent to the mill through the metering feeding equipment, and it is ground into fine powder in the mill which meets the requirements of environmentally friendly production 2 Increase greeneryOne of the main equipment in the slag powder production line is the slag mill There are so many types of cement mills that can be selected for slag grinding plants increase revenue The slag grinding plant uses the slag for the second time to increase the extra income of the enterpriseSlag Grinding Plant GGBS Plant Slag Mill, Slag Grinding MillAG/SAG mill is inefficient in grinding particles of a certain size, typically in the range of 2555 mm, ie, pebbles Therefore, cone crushers are often used as pebble crushers and integrated into AG/SAG mill circuits to break the critical size particles that accumulate in the mill and to increase the performance of the primary grinding circuitsDynamic Modeling and Simulation of SAG Mill Circuits withThe Autogenous Mill, also known as AG Mill, is a type of grinding mill used in the mining industry This machine uses ore and rock itself as grinding media to perform its job Unlike other types of mills that use steel balls or rods for grinding materials, the Autogenous Mill relies on the material being ground to break itself into smaller piecesUnderstanding the SAG Mill in Copper Ore Mining Process
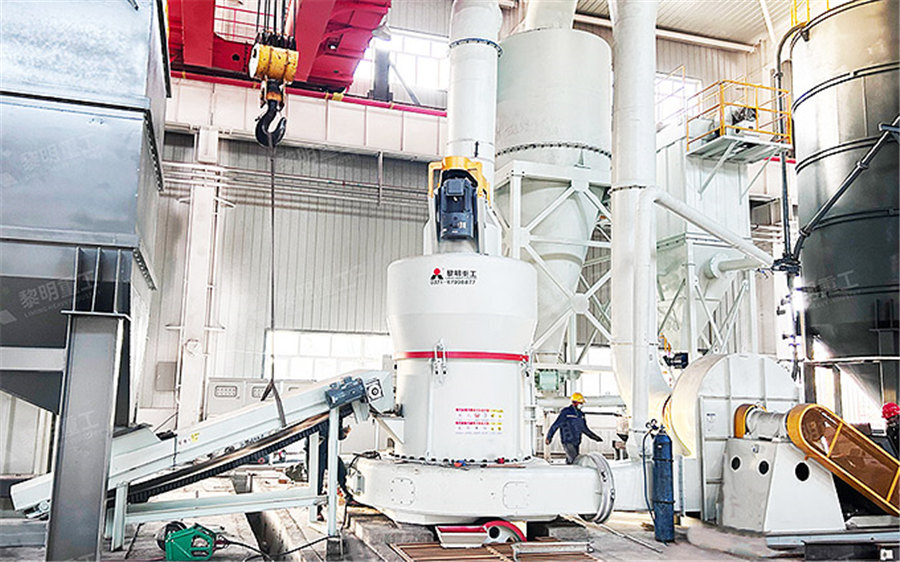
(PDF) Multicomponent AG/SAG mill model ResearchGate
2013年4月1日 The simulation of the digital model captures an increase in production of 442% as a function of mineral fragmentation, while there is potential to increase production by decreasing the mill Accordingly, the mill power consumption decreased from 84 to 516 kWh/t (a nearly 40% reduction), and the fresh feed flow rate increased from 515 to 615 t/h (a nearly 20% increase in the mill SAG Mill Response to Changes in Feed Size as 2023年4月19日 The simulation of the digital model captures an increase in production of 442% as a function of mineral fragmentation, while there is potential to increase production by decreasing the mill (PDF) Optimization of the SAG Grinding Process Using Statistical I39 OPTIMISATION OF THE SOSSEGO SAG MILL Homero Delboni1, Marco A Nankran Rosa2, Maurício G Bergerman3, and Rinaldo P Nardi4 1Consultant – HDA Serviços Ltda, Lecturer – University of OPTIMISATION OF THE SOSSEGO SAG MILL ResearchGate
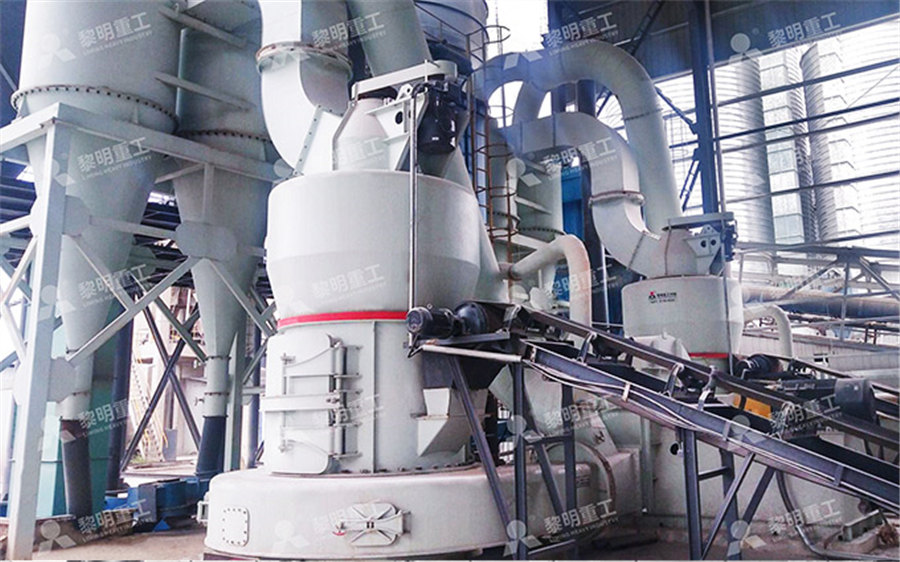
Operation Analysis of a SAG Mill under Different Conditions Based on
2020年10月9日 As one of the machines widely used in mining, a semiautogenous grinding (SAG) mill can significantly improve the roughing efficiency of rock But the SAG mill still faces the obstacles of significant energy consumption and empirical operation parameters In order to obtain the optimal operation parameters of a SAG mill, in this paper, the discrete element 2024年9月23日 SS production has increased from 3535 million tons (out of 1014 million tons of steel production) in 2017–2018 to 53 million tons (out of 150 million tons of steel production) in 2019–2020, which tends to strengthen the effective and economically viable utilization of Enhancing concrete properties with steel waste: a comprehensive mine and mill site variables determine SAG mill performance, ie capacity and grindsize In many operations these variables affect production capacity seemingly at random Methods to increase capacity , decrease energy consumption and prolong lifter and liner life are needed The variable interaction involved in slurryITP Mining: Improving Energy Efficiency in SAG Mills2023年4月19日 It shows an increase in production in TpH as a result of an M2M strategy (H 1) that produces a greater fragmentation of the mineral fed (which also impacts to a lesser degree on the energy consumption of the SAG mill), together with increases in production and decreases in energy consumption derived from optimum handling of mill control parameters, such as Optimization of the SAG Grinding Process Using Statistical
.jpg)
Analysis of sag mill machine performance using overall equipment
2022年12月30日 However, the SAG Mill machines are often broken, even suddenly not working, with an average loss time of 9730 hours which impacts a decrease in efficiency and production quality of up to 40%2022年3月8日 Photo: The existing grates within the SAG Mill were pegging Critical size grinding media were blocking apertures, reducing throughput A gold and copper mine in South East Asia was experiencing a range of challenges with its SAG mill that were hitting productivity Facing a significant increase in ore hardness that would have exacerbated the problems, the mine Customised liner solution boosts SAG mill throughput and mine 2005年12月1日 In an attempt to identify the effect of aggregate stemming on mill throughput, production data from January 1–8, May 2002 were Paley, N, Kojovic, T, 2001 Adjusting blasting to increase SAG mill throughput at the Red Dog mine In: Proc 27th ISEE Annual Conference, Orlando, January, pp 65–80 Google Scholar Sarma, 1994Influence of aggregate stemming in blasting on the SAG mill 2015年9月20日 PDF The new practice of applying full precrushing of SAG mill feed to substantially increase throughput is challenged as retrogressive and Find, read and cite all the research you need on (PDF) FULL PRECRUSH TO SAG MILLS ResearchGate
.jpg)
Understanding the effects of liner wear on SAG mill
2015年9月7日 It is also crucial that the user has knowledge about the process, and potential changes in the plant that can cause process drift For example, liner wear can greatly affect SAG mill performance The simulation of the digital model captures an increase in production of 442% as a function of mineral fragmentation, while there is potential to increase production by decreasing the mill Schematic diagram of AG/SAG mill process Download scientific diagram SAG mill compared to crusher and ball mill product size distributions (Powell et al 2014) from publication: FULL PRECRUSH TO SAG MILLS – THE CASE FOR CHANGING THIS SAG mill compared to crusher and ball mill product size 2024年6月1日 mill speed, and the slurry density, allowing us to accurately model the performance and wear of our mill liners This includes predicting the liners’ wear life to avoid unscheduled downtime and to extend the time between replacements” Emphasizing that no two mill liner applications are identical,THE FUTURE OF SAG MILLS Ausenco
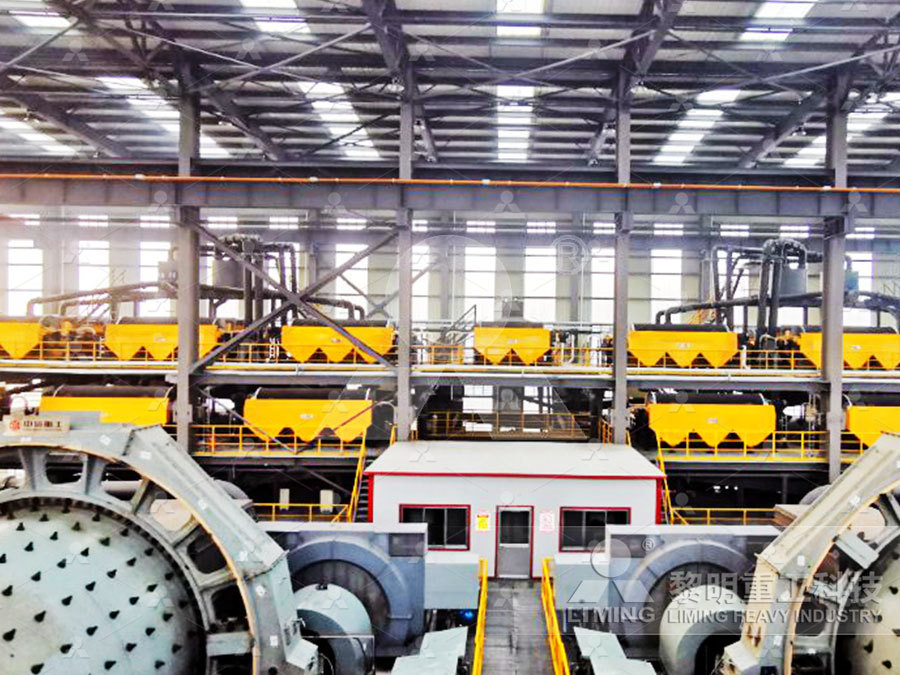
Adjusting Blasting to Increase SAG Mill Throughput at the Red
2001年1月1日 Increasing the powder factor by 150% from the 029kg/t {058lb/st] being used to 072kg/t { 144lb/st}, the maximum feasible with mine equipment, could provide a signant net benefit of $3OWyr due to the increased concentrate production2021年1月9日 In 1998, AgnicoEagle decided to expand production capability from 750,000 short tons per year to 1,300,000 TPY, initially by adding a SAG mill to the existing twoball mill grinding circuit As exploration results showed increasing ore reserve potential, concentrator throughput increase to 1,800,000 TPY was being studiedPage 1 INTRODUCTION SAGDesignThe solution for increasing production in the SAG mill With improved SAG mill control stability, the mill load can be optimized to increase crushing performance and production capacity Contact us ANDRITZ Inc United States of America +1 (770) 640 2500 automationsales@andritzBrainWave SAG mill Andritz• Maximise power drawn by increasing mill speed while minimising direct shell impacts • Increase SAG mill availability by increasing liner life • Reduce onset of slurry pooling at increased feed rates As part of the liner evaluation, six vendor designs were compared, and their performances benchmarked against the base case liner systemMill Operators’ Conference 2018
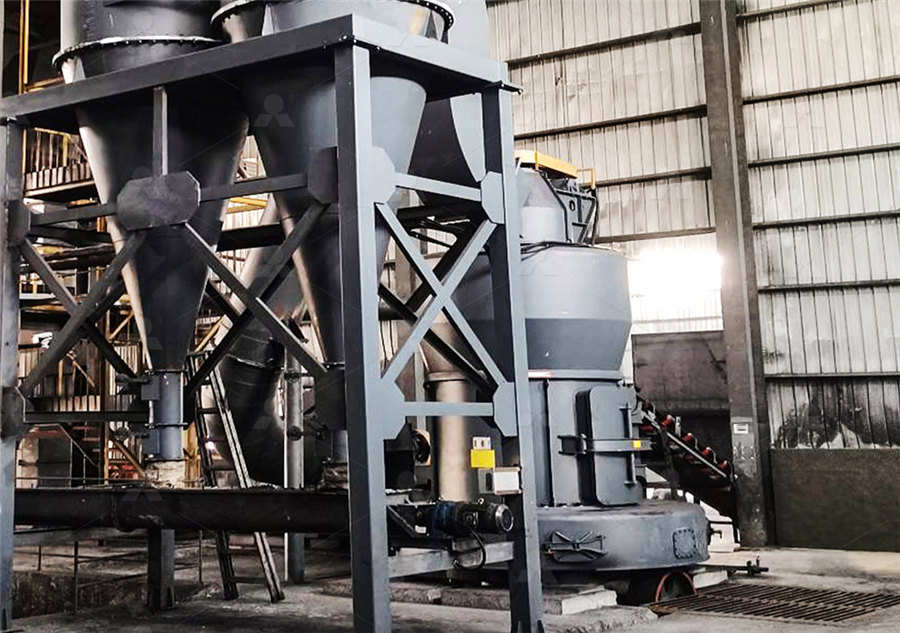
SAG Mill Liner Design 911Metallurgist
2016年6月6日 As mill sizes increases, the required volumetric capacity of the pulp lifters grows proportionally to mill volume Since AG/SAG mill volume is roughly proportional to the mill radius cubed (at typical mill lengths) while the available crosssectional area grows only as the radius squared, pulp lifters must become more efficient at transferring slurry in larger mills