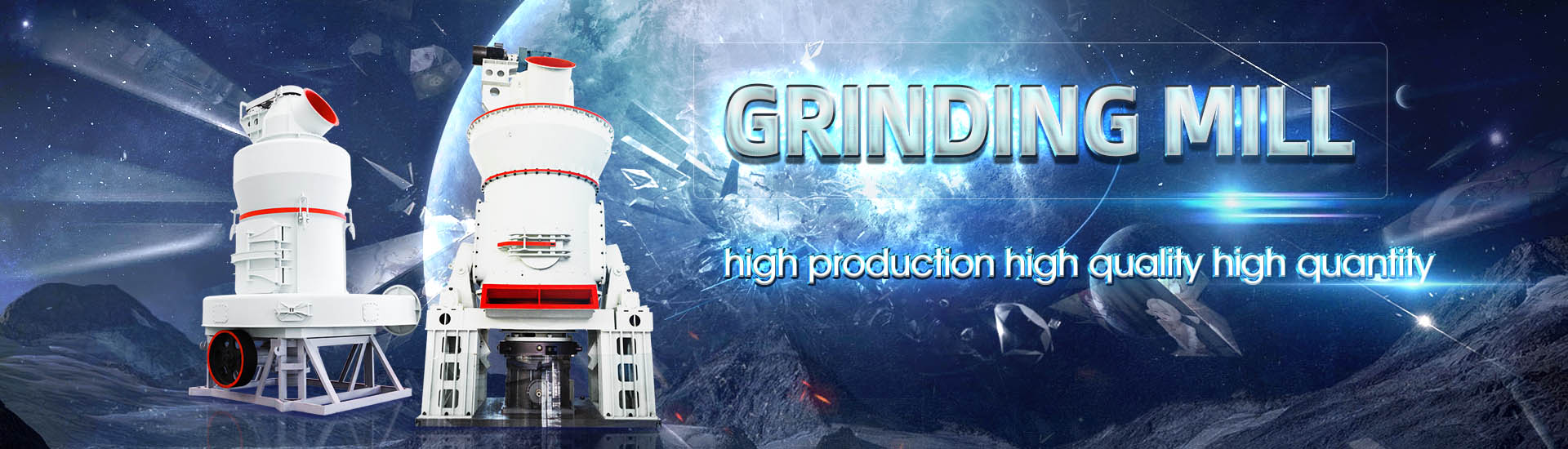
What is the reason for the heat of the grinding roller of the crusher
.jpg)
Roll Crushers ScienceDirect
2016年1月1日 Radical changes to the design of roll crushers were introduced by Schonert [1], [2], as a result of fundamental work on breakage mechanisms These roll crushers have large forces of compression and are called high pressure grinding rolls (HPGR) The present trend In the second type, known as high pressure grinding roll (HPGR), the mineral sizes Roll CrushersIn the process of Rolling the most significant aspect is the generation of heat through friction and deformation in the roll bite and in a typical Cold Tandem Mill, work roll temperatures normally Fundamentals of Roll Cooling and Control of Flatness at LechlerHeat is carried by the rolling stock (by virtue of its temperature) and some is lost to the air and to the washoff coolant before reaching the roll bite In the roll bite the strip gains heat from GENERAL ASPECTS OF ROLL COOLING FOR HOT COLD
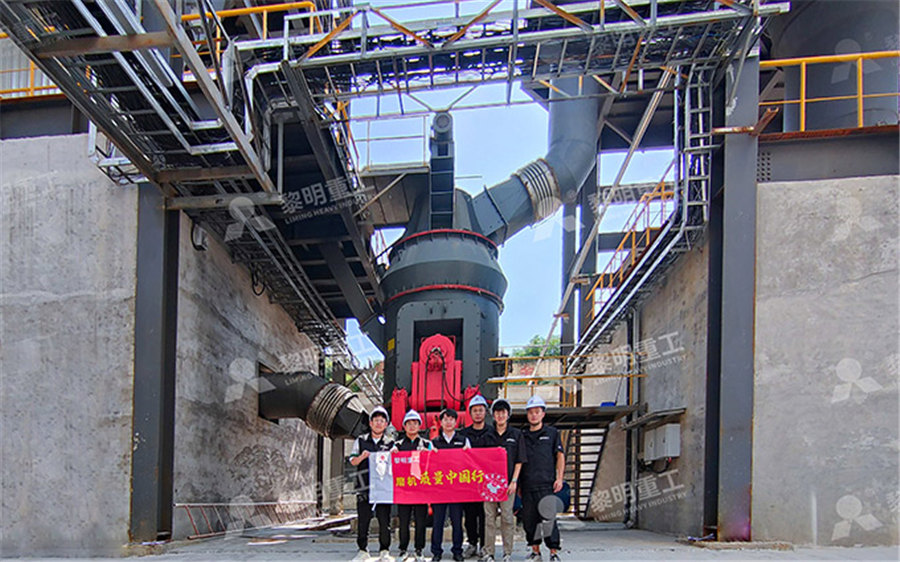
Energy and temperature analysis in grinding WIT Press
Energy consumption and dissipation are discussed, leading into a thermal model for grinding The analysis developed over many years applies to shallowcut conventional grinding processes Some of the results achieved in this article are to point out the main reason why the cutting heat when grinding is higher than other mechanical machining methods and the factors that mainly Some discussions on grinding heat in mechanical processing2023年6月22日 Roll speed differential is the difference in rotational speed between the two rolls in a pair and is one of the biggest reasons roll crushers produce a grind with a lower standard Hammermill and roll crusher maintenance and operation2022年6月24日 The excessive heat generated at the grinding contact zone might result in thermal damage such as surface oxidation, surface fractures, surface tempering and (PDF) A comprehensive review on the grinding process:
.jpg)
Residual stress generation in grinding: Mechanism and modeling
2024年3月1日 The measurement of grinding force, temperature and workpiece could be analysis basis for residual stress For example, grinding heat constitutes one of the primary influential 2007年1月1日 This chapter describes how the flour milling process interacts with the wheat kernel structure to separate it into its functional components The chapter traces the historical Chapter 7 Roller Milling of Wheat ScienceDirect2017年7月12日 In the grinding process, high temperature in grinding area is generated by the frictional resistance between workpiece and abrasive grains on the grinding wheel cylindrical (PDF) A Heat Transfer Model of Grinding Process Based on Energy 2021年7月3日 The grinding wheels tend to range in diameter from half an inch to three inches This small size introduces rapid wear, making CBN and diamond wheels in crush dressable and vitrified form popular for these applications Machining 101: What is Grinding? Modern Machine
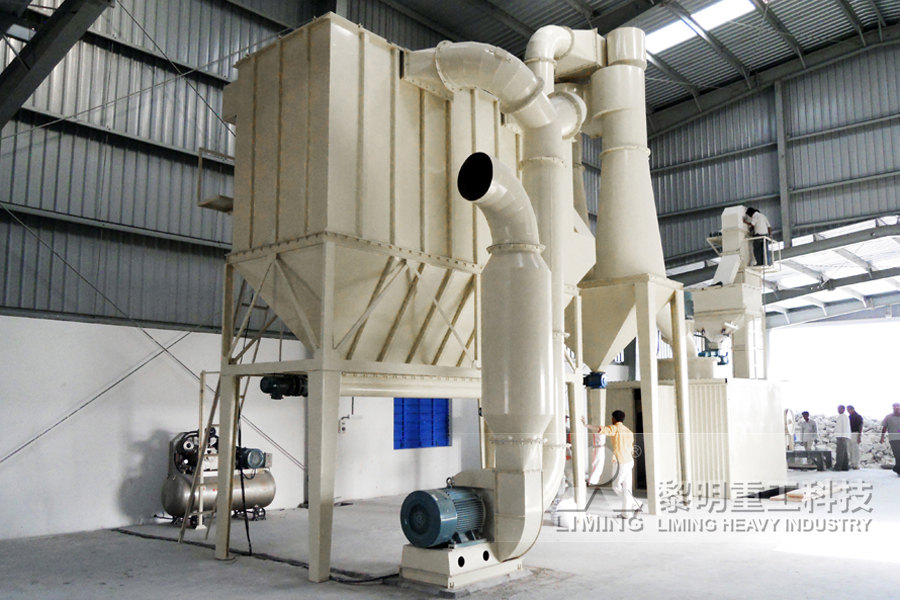
Residual stress generation in grinding: Mechanism and modeling
2024年3月1日 Furthermore, Li and Axinte (2017) performed a comprehensive review of various heat source models, including the trapezoidal heat flow model, parabolic heat flow model, elliptical heat flow model, and triangular heat flow model and analyzed the intricate relationship between grinding heat and resultant residual stresses across these different models (as shown in Fig Download scientific diagram Variation of the specific grinding energy and grinding heat flux with the grinding speed from publication: Profile grinding of DZ125 nickelbased superalloy Variation of the specific grinding energy and grinding heat” is lost to air with further losses to such things as coolant washover, however, heat absorbed by the rotating roll is subject to a more complex thermal mechanism Heat will continuously migrate to cooler zones in and out of the roll body due to the localized elevated temperatureFundamentals of Roll Cooling and Control of Flatness at LechlerGrinding is the common collective name for machining processes that utilize hard, abrasive particles as the cutting medium The grinding process of shaping materials is probably the oldest in existence, dating from the time prehistoric humans found that they could sharpen their tools by rubbing them against gritty rocksGrinding Processes SpringerLink
.jpg)
Understanding the causes of grinding burn helps alleviate the
grinding Often, the grinding engineer simply looks for workpiece discoloration to determine whether or not there is a problem There are several different types of thermal damage Some are strictly cos metic, some inhibit grinding performance and some lead to immediate fracturing of the workpiece A workpiece’s ability to tolerate the2024年1月23日 Basic Grinding Machines: Entrylevel grinding machines, suitable for smallscale operations or less complex tasks, typically range from $5,000 to $20,000 MidRange Grinding Machines: These machines, offering more features and greater precision, are generally priced between $20,000 and $60,000What is Grinding: Definition, Process, Types Specifications2020年8月12日 This study shows the performance of a currently running vertical roller coal mill (VRM) in an existing coalfired power plant In a power plant, the coal mill is the critical equipment, whose An investigation of performance characteristics and energetic 2018年11月21日 A grinding wheel is a precision tool with thousands of cutting points on its surface abrasive grains that are held in place by a bond matrix (hence these are known as bonded abrasives) and separated by pores These pores are hollow spaces between abrasive grains and the bond , which help with the clearance of discarded metal chips in the grinding Which Grinding Wheel Should I Choose? Norton Abrasives UK
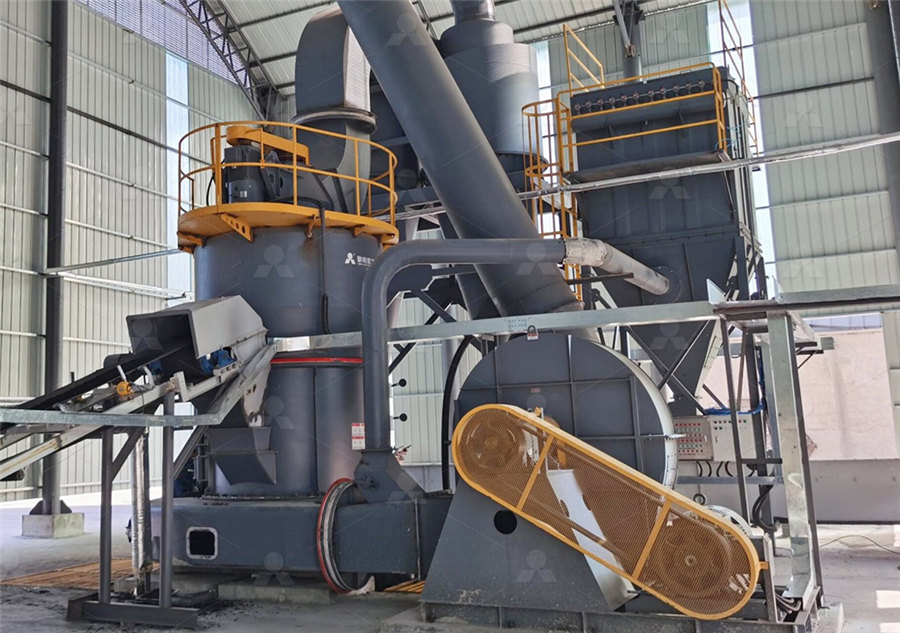
Vertical roller mill for raw Application p rocess materials
coarse and fine grinding on the same mill by ball size selection etc Therefore, a new system was proposed and developed by installing a pregrinder, which is roller mill or roller press, as coarse grinding before the existing tube mill, which is exclusively used for fine grinding This system greatly reduced the specific2023年11月10日 In combination with Eqs ()–(), the trajectory of abrasive grain under different process parameters is uniquely determined, which can be further used in the derivation of the epitrochoid heat flux distribution22 Heat flux distribution model Once the motion of the adjacent abrasive grains is determined, the thickness of the grinding chip can be calculatedEpitrochoid heat flux distribution model for cylindrical grinding 2024年1月14日 The roller at the top will rotate a bit faster than the roller at the bottom so that when wheat passes through it will create the action of shearing, Less heat generation: Like with coffee, minimizing heat generation during What’s the process of milling wheat: Stepbystep guide2024年6月21日 Grinding is an ultraprecision machining technology The grinding force and grinding heat emerge as pivotal physical parameters Excessive grinding temperature can engender unwarranted thermal damage to the processed material In cup grinding wheel face grinding, employing a singular abrasive grain discrete heat source method enables a more Grinding heat theory based on trochoid scratch model:
.jpg)
7 Causes of Quench Cracking in Steel Production Machining
2017年7月13日 However, when steel parts fail, the consequences are dire Here are seven ways that steel can fail as a result of quench cracking from heat treatment Overheating during the austenitizing portion of the heat treatment cycle can coarsen normally finegrained steels2021年8月16日 The rotor of the hammer crusher is composed of the main shaft, hammer frame, hammer head and other parts The rotor is the core component of the hammer crusher and is easy to wear If the crusher vibrates greatly during operation, you can check whether it is due to the serious wear of the components of the rotorWhat Are The Reasons for The Large Vibration Eastman Rock CrusherRubber Roller Grinding This process smoothens the surface of the rubber cover by removing protruding parts and leveling overlapping strips Grinding is done by rolling the rubber roller against an abrasive wheel, typically in some kind of turning lathe Roller Core Balancing A roller core can experience imbalance in two ways: static and dynamicRubber Roller: What Is It? How Is It Made? Types, Uses IQS Roller mills are essential equipment used extensively in the industrial processing sector, particularly for drying, grinding, and classifying a variety of materials Roller mills use the centrifugal force of cylindrical grinding rolls to crush material into a uniform particle size and grind, dry, and classifyIndustrial Roller Mills Williams Crusher
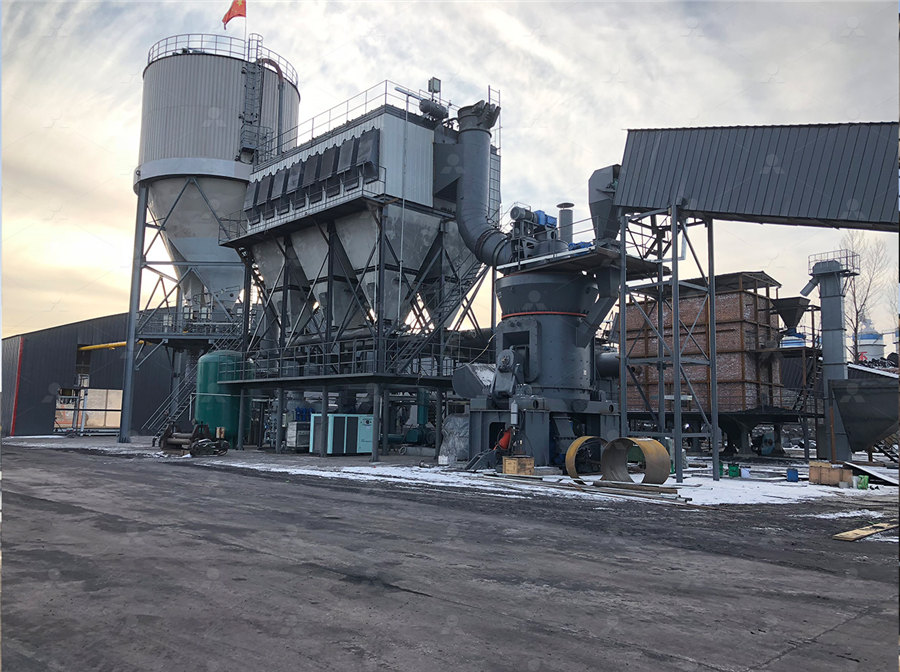
Surface Grinding EngineeringTechnology
Surface grinding is a precision machining process used to produce smooth and flat surfaces on a variety of materials, including metals, plastics, and ceramics The process involves using a grinding wheel, which is made up of abrasive particles, to remove material from the surface of a workpiece until it is smooth and flatGrinding lowalloy tool steels seldom presents any difficulties When grinding highalloy tool and highspeed steels with high carbide content, however, problems can easily occur For this reason, the grinding parameters must be selected carefully The higher the wear resistance of a steel, the more difficult it is to grindGRINDING FOR TOOLMAKING voestalpine BÖHLER US2019年10月1日 The reason for the abrasive failure is that local high temperature Grinding heat is the primary contributor to the quick wear of resinbased rail grinding wheels [38, 39]Probing the effect of grindingheat on material removal 2024年4月19日 Attrition Crushing: Abrasion crushing is the consequence of material being subjected to the grinding action, often between two rotating surfaces or media This is the reason why there is a decrease in particle size Types of Crushers Explained: Everything You Need to
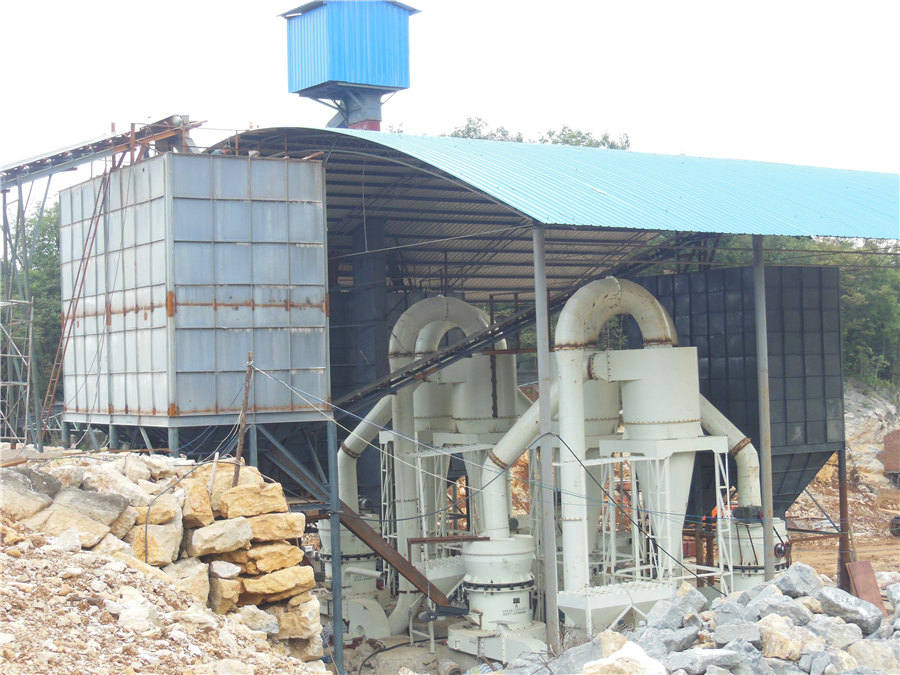
Gear Grinding Cracks: Causes and Prevention Measures
2023年9月25日 The factors that directly affect the grinding tensile stress are: (1) Heat treatment: Grinding cracks in hard tooth surface gears mostly occur in parts that have undergone carburizing, quenching, and lowtemperature tempering 2019年7月31日 The necessary press force is created by a hydraulic—pneumatic system which works like a spring The movable roller is actuated towards the static roller with the help of a hydraulic cylinder to grind the clinkers fed from the vertical chute/hopper over the rollers The roller comprises of a steel shaft and a mounted tire made of “bainite”Fault Diagnosis and Root Cause Failure Analysis of Press Roller 2016年1月1日 In some flow sheets, HPGR is placed before the roll crusher in order to induce cracks and fissures in the ore particles In such cases ball mill grinding is facilitated Several alternate circuits were suggested by Baum, Patzelt and Kneecht [17] and Patzelt et al [11], [15] A typical flow sheet for coarse grinding is illustrated in Figure 66Roll Crushers ScienceDirect2020年9月7日 There are many stone crusher types, for instance, jaw crusher, cone crusher, impact crusher, hammer crusher, roller crusher, diesel engine crusher, mobile crushing plant etc Those crushers can meet all kinds of produce requirements: large or small capacity, even large or small output size The progress of processing powder size is called grindingWhat is the difference between crushing and grinding?
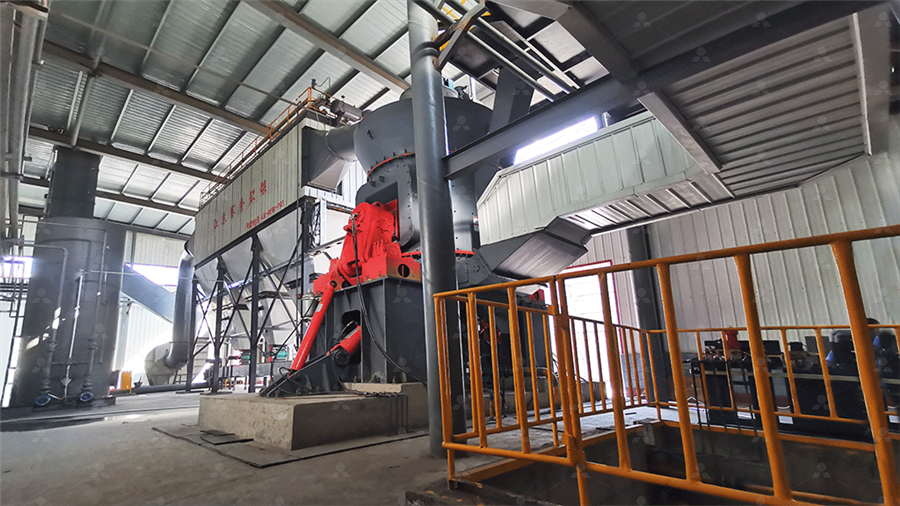
Overview of the soybean process in the crushing industry
2020年1月1日 A minimal residual oil content in the meal coming out of the hexane extractor is a clear benefit for a crushing plant; the more oil yield the better revenue for the crusher2021年3月1日 The abrasive belt grinding process is a highly nonlinear dynamic change process The coupling action mechanism between mechanical field and thermal field during grinding is complex and variable In this paper, firstly, the abrasive belt grinding experiment of titanium alloy was carried out to measure the change of temperature and force during the grinding process, Analysis of thermalmechanical causes of abrasive belt grinding 2021年5月6日 A sectional view of the singletoggle type of jaw crusher is shown below In one respect, the working principle and application of this machine are similar: the movable jaw has its maximum movement at the top of the crushing chamber, and minimum movement at the discharge point The motion is, however, a more complex one than the Dodge motion, being Jaw Crusher Working Principle 911MetallurgistHowever, it is impossible to avoid some of the heat entering the part As long as the heat input into the part is not too great, this poses no problems to the production process However, if the infeed is too high during grinding and there is insufficient cooling, such a great amount of heat enters the part that grinding burn occursFrequent problems during grinding – grindaix GmbH
.jpg)
Metallurgical Reasons for Grinding Cracks and Their Detection
2017年5月26日 Table 1: Comparison of different methods to evaluate grinding burns [10] Conclusions Grinding is used in many applications during final finishing of heattreated parts It is a highenergy process with much of the energy converted to heat This heat can cause detrimental residual stress and microstructural changes that can reduce product life2021年7月3日 The grinding wheels tend to range in diameter from half an inch to three inches This small size introduces rapid wear, making CBN and diamond wheels in crush dressable and vitrified form popular for these applications Machining 101: What is Grinding? Modern Machine 2024年3月1日 Furthermore, Li and Axinte (2017) performed a comprehensive review of various heat source models, including the trapezoidal heat flow model, parabolic heat flow model, elliptical heat flow model, and triangular heat flow model and analyzed the intricate relationship between grinding heat and resultant residual stresses across these different models (as shown in Fig Residual stress generation in grinding: Mechanism and modelingDownload scientific diagram Variation of the specific grinding energy and grinding heat flux with the grinding speed from publication: Profile grinding of DZ125 nickelbased superalloy Variation of the specific grinding energy and grinding
.jpg)
Fundamentals of Roll Cooling and Control of Flatness at Lechler
heat” is lost to air with further losses to such things as coolant washover, however, heat absorbed by the rotating roll is subject to a more complex thermal mechanism Heat will continuously migrate to cooler zones in and out of the roll body due to the localized elevated temperatureGrinding is the common collective name for machining processes that utilize hard, abrasive particles as the cutting medium The grinding process of shaping materials is probably the oldest in existence, dating from the time prehistoric humans found that they could sharpen their tools by rubbing them against gritty rocksGrinding Processes SpringerLinkgrinding Often, the grinding engineer simply looks for workpiece discoloration to determine whether or not there is a problem There are several different types of thermal damage Some are strictly cos metic, some inhibit grinding performance and some lead to immediate fracturing of the workpiece A workpiece’s ability to tolerate theUnderstanding the causes of grinding burn helps alleviate the 2024年1月23日 Basic Grinding Machines: Entrylevel grinding machines, suitable for smallscale operations or less complex tasks, typically range from $5,000 to $20,000 MidRange Grinding Machines: These machines, offering more features and greater precision, are generally priced between $20,000 and $60,000What is Grinding: Definition, Process, Types Specifications
.jpg)
An investigation of performance characteristics and energetic
2020年8月12日 This study shows the performance of a currently running vertical roller coal mill (VRM) in an existing coalfired power plant In a power plant, the coal mill is the critical equipment, whose 2018年11月21日 A grinding wheel is a precision tool with thousands of cutting points on its surface abrasive grains that are held in place by a bond matrix (hence these are known as bonded abrasives) and separated by pores These pores are hollow spaces between abrasive grains and the bond , which help with the clearance of discarded metal chips in the grinding Which Grinding Wheel Should I Choose? Norton Abrasives UKcoarse and fine grinding on the same mill by ball size selection etc Therefore, a new system was proposed and developed by installing a pregrinder, which is roller mill or roller press, as coarse grinding before the existing tube mill, which is exclusively used for fine grinding This system greatly reduced the specificVertical roller mill for raw Application p rocess materials