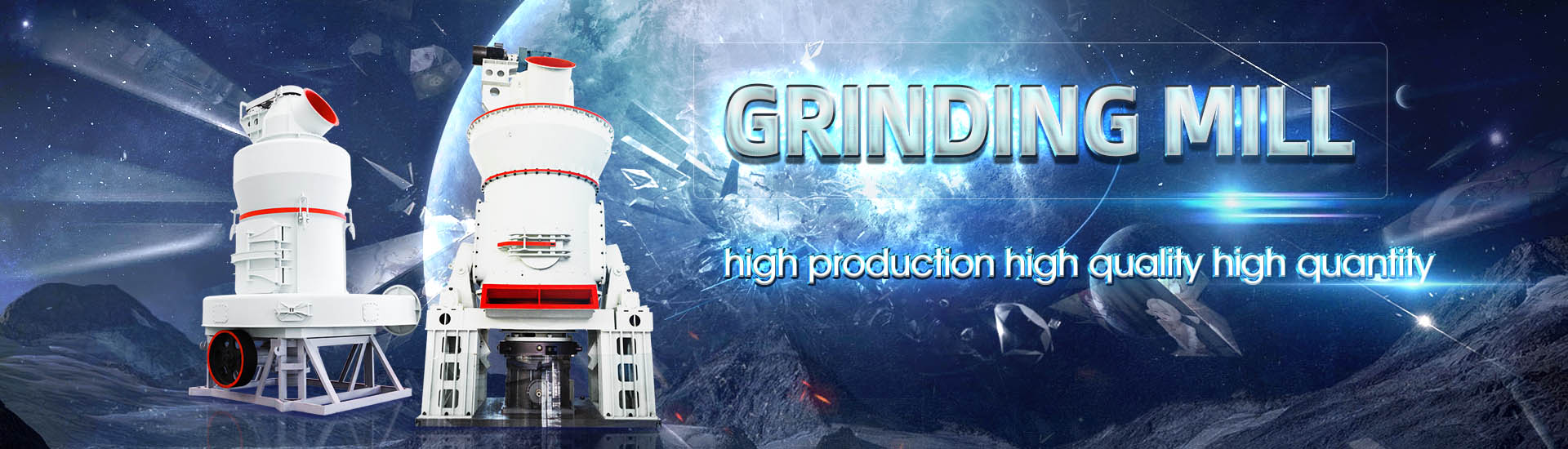
slag treatment magnetic separation
.jpg)
Application of magnetic separation to steelmaking slags for
2006年1月1日 In this study, a basic oxygen furnace (BOF) steelwork slag obtained from the Kardemir integrated iron and steel works, Karabuk, Turkey is used2024年3月1日 In order to address the issue of magnetic agglomeration leading to poor magnetic separation efficiency and low activity enhancement, resulting in limited utilization of steel slag fine powder material, this study proposes a An airfluidized magnetic separator and its separation 2023年11月7日 The magnetic properties of the ewaste slag are classified via a pretreatment with a Frantz isodynamic magnetic separator, followed by direct magnetic susceptibility measurements using the magnetic susceptibility Characterization of Magnetic and Mineralogical 2014年1月10日 The first one deals with treatment of ground LD slag at different particle size fractions of 1 mm, 400 μm, 200 μm and 200 μm by dry magnetic separation This technique Recovery of high grade iron compounds from LD slag by
.jpg)
(PDF) An airfluidized magnetic separator and its separation
2024年3月1日 In order to address the issue of magnetic agglomeration leading to poor magnetic separation efficiency and low activity enhancement, resulting in limited utilization of steel slag 2024年7月29日 Steel slag can separate inert minerals by the mineral separation method and prevent the hydration of active minerals caused by wet magnetic separationMagnetic separation characteristics of steel slag powder in a 2017年2月1日 To improve the efficiency of iron recovery from steel slag and reduce the wearandtear on facilities, a new method was proposed by adding a secondary screen sizer to the Optimization of magnetic separation process for iron recovery magnetic separation has proved to be an op ti mal method to separate and recover iron from steel slag After magnetic separation, the recovered magnetic iron (MFe) particles can be fed back Optimization of magnetic separation process for iron Springer
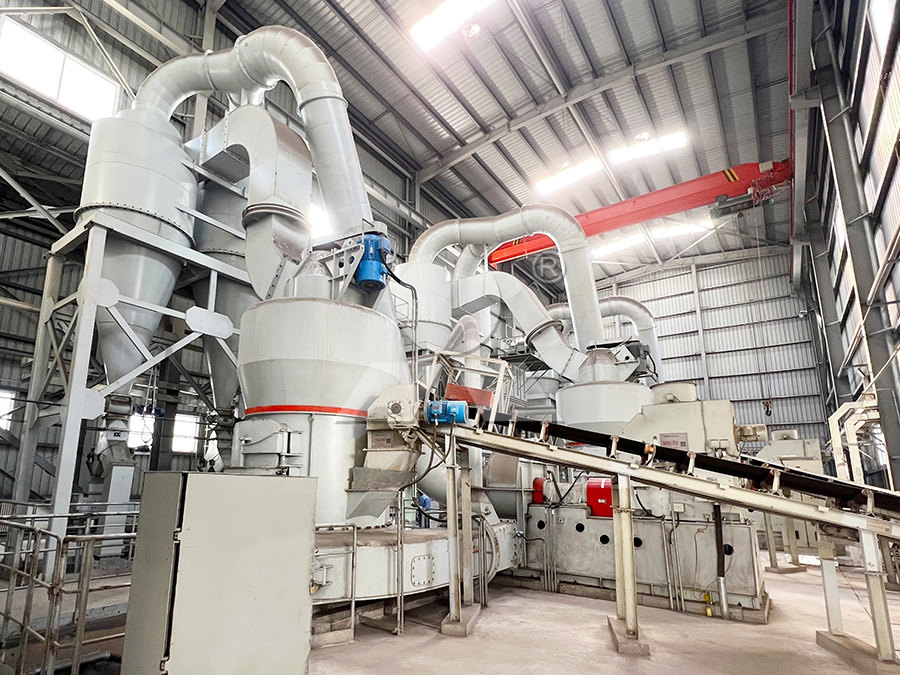
Optimization of magnetic separation process for iron recovery
2017年2月1日 Recovering iron and aluminum efficiently is the key route to utilize lowgrade highiron bauxite Aiming to optimize the iron separating process and elevate both Fe and Al 2023年11月7日 Magnetic separation has wideranging applications in both mineral processing and recycling industries Nevertheless, its conventional utilization often overlooks the interplay between mineral and particle Characterization of Magnetic and Mineralogical PreReduction and Melting/Magnetic Separation Treatment Shaoyan Hu 1, Deyong Wang 1, along with the alloy and tail slag after separation, were comprehensively analyzedEnrichment Characteristics of Cr in Chromium Slag after Pre 2021年8月30日 More importantly, a relatively low prereduction temperature and selection of magnetic separation process were found to be more beneficial for chromium enrichment in slag; the highest chromium (PDF) Enrichment Characteristics of Cr in Chromium
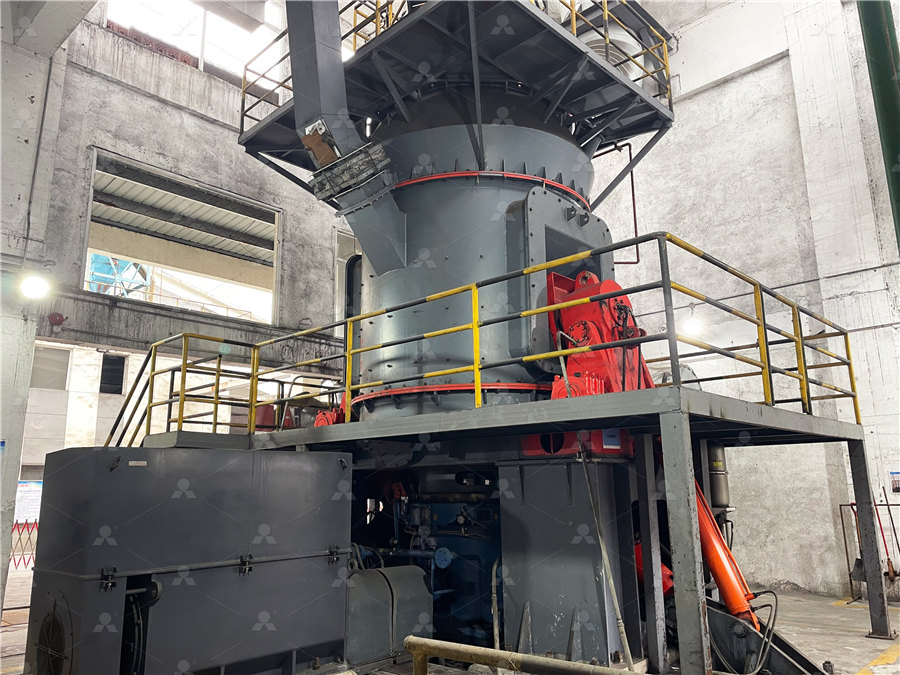
Nickel recovery from electric arc furnace slag by magnetic separation
2017年1月1日 During the pyrometallurgical treatment of the nickelbearing laterite in the plant of GMM SA LARCO, slag is produced after treatment in electricarc furnace (EAF) that contains 010 to 020 % Ni2014年1月10日 Two variants of magnetic separation were performed on LD slag The first one deals with treatment of ground LD slag at different particle size fractions of 1 mm, 400 μm, 200 μm and 200 μm by dry magnetic separation This technique may be applied on the coarse fraction of LD slag to recover only iron scrapsRecovery of high grade iron compounds from LD slag by enhanced magnetic 2024年10月1日 The main components of EAF slag are Fe x O, Fe, CaO, SiO 2, MgO, and MnOThe EAF slag contains more iron, but it is mainly dominated by RO phase, which is difficult to be recovered by magnetic separation, resulting in low utilization of iron in slag (Liu et al, 2023, Zhang et al, 2019)The traditional view that EAF slag and converter slag are similar in nature, Separation and extraction of iron resources from hazardous 2022年4月27日 In this paper, we reviewed steel slag treatment, When the mixed slag was modified at 1200℃, the grade of magnetic slag by magnetic separation was 3114% and the recovery was 6404%, Optimization of Iron Recovery from BOF Slag by Oxidation and Magnetic
.jpg)
(PDF) Recovery of iron from waste slag of pyrite ResearchGate
2013年4月1日 magnetic treatment; whereas Fe recovery is the ratio of (Fe 2 SiO 4 ) are investigated for the recovery of iron from ironrich nickel slag by oxidationmagnetic separationDOI: 101016/jjmrt202301186 Corpus ID: ; Efficient separation of iron elements from steel slag based on magnetic separation process @article{Liu2023EfficientSO, title={Efficient separation of iron elements from steel slag based on magnetic separation process}, author={Xin Liu and Dazhi Wang and Zhiwei Li and Wei Ouyang and Yanping Bao and Chao Gu}, Efficient separation of iron elements from steel slag based on magnetic 2024年3月1日 Primary magnetic separation tests on a steel slag fine powder material demonstrate that the air fluidized dry magnetic 4 J L Guo, Y P Bao, and M Wang, “Steel slag in China: Treatment (PDF) An airfluidized magnetic separator and its separation 2024年4月24日 Magnetic separation technology is a physical separation method that uses the differences in magnetism between matter to separate them from each other by different motion behaviors in a nonuniform magnetic field It is Application of Magnetic Separation Technology in

Recycling of steelmaking slag fines by weak magnetic separation
DOI: 101016/JJCLEPRO201406092 Corpus ID: ; Recycling of steelmaking slag fines by weak magnetic separation coupled with selective particle size screening @article{Ma2014RecyclingOS, title={Recycling of steelmaking slag fines by weak magnetic separation coupled with selective particle size screening}, author={Naiyang Ma and Joseph 2006年1月1日 The magnetic separation method is used for separating metallic iron and iron minerals from steel slag Slag treatment at Kardemir integrated iron and steel works International Journal of Minernal Processing, 74 (2004), pp Application of magnetic separation to steelmaking slags for 2021年8月30日 Enrichment Characteristics of Cr in Chromium Slag after PreReduction and Melting/Magnetic Separation Treatment Shaoyan Hu, 1 Deyong Wang, 1 Xianglong Li, 1, * Wei Zhao, 1 the reaction products need to be separated into the metallic alloy and nonmetallic slag Melting separation and magnetic separation are the most widely Enrichment Characteristics of Cr in Chromium Slag after Pre 2021年12月29日 Characterization of a ChromiumBearing Carbon Steel Electric Arc Furnace Slag after Magnetic Separation to Determine the The thermal treatment of steel slag up to 900 °C indicated that this Characterization of a ChromiumBearing Carbon Steel Electric Arc
.jpg)
Nickel recovery from electric arc furnace slag by magnetic separation
The results of magnetic separation are shown in Table 6 The results show that the increase of water content adversely affects magnetic separation, as the grade of the magnetic product drops from 098 % to 072 % Ni; the corresponding yield reduces from 2582 % to 2476 %, and the recovery reduces significantly from 81 % to 665 % Table 62013年1月1日 Slag treatment at Kardemir integrated iron and steel Similarly, several studies [12][13][14] [15] have also shown the potential of magnetic separation for slag recyclingRecovery of high grade iron compounds from LD slag by enhanced magnetic Available online at sciencedirect Journal of Hazardous Materials 152 (2008) 211–215 Phosphate removal from solution using steel slag through magnetic separation Jibing Xiong a , Zhenli He a,b , Qaisar Mahmood a , Dan Liu c , Xiaoe Yang a,∗ , Ejazul Islam a a MOE Key Laboratory of Environmental Remediation and Ecological Health Phosphate removal from solution using steel slag through magnetic 2019年2月20日 The recovery methods reported in the literature include the superconducting magnetic separation method, using the magnetic difference of Si and SiC (Nishijima et al, 2003), the separation technology of SiC by CuSi alloy after sedimentation and enrichment (Olsen et al, 2010), the potential regulationcentrifugation separated by the Zeta potential of the particles Separation and purification of silicon from cutting kerfloss slurry
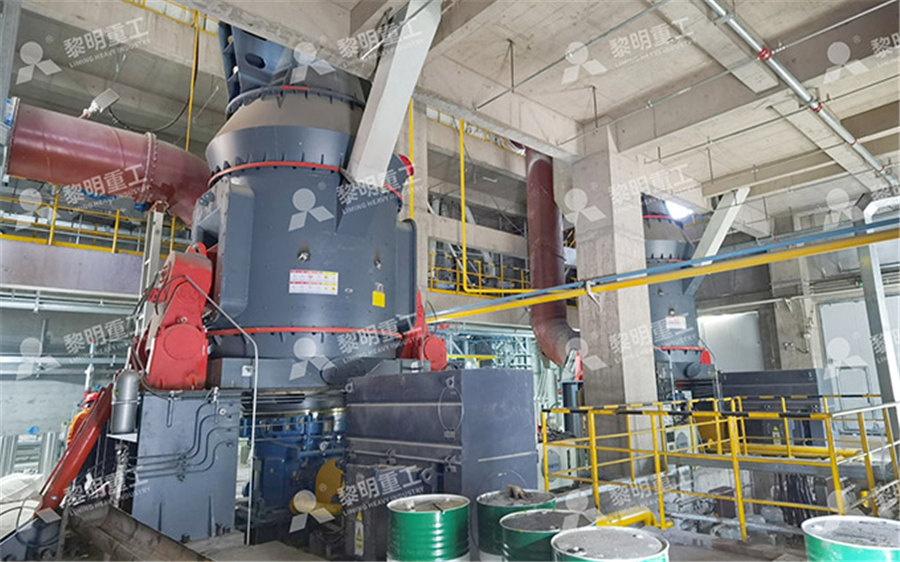
Phosphate removal from solution using steel slag through magnetic
2008年3月21日 Present study indicates that steel slag may be an effective adsorbent for phosphate removal from secondary effluents as well as solution after magnetic separation The steel slag showed good performance for phosphorus removal The maximum adsorption capacity of steel slag was 53 mg P/gAvailable online at sciencedirect Journal of Hazardous Materials 152 (2008) 211–215 Phosphate removal from solution using steel slag through magnetic separation Jibing Xiong a , Zhenli He a,b , Qaisar Mahmood a , Dan Phosphate removal from solution using steel slag 2006年2月1日 Magnetic separation is used for separating metallic iron and iron minerals from the slag using magnetic machines (crossbelt magnetic separator, drum magnetic separator and magneticpulley Application of Magnetic Separation to Steelmaking Slags for Steel slag is a byproduct generated during the steelmaking process As the largest steel producer in the world, China produces over 100 million tons of steel slag annually, accounting for approximately 15–20% of crude steel production (Rui et al 2022, Shi et al 2022)After steelmaking, the slag is placed in a slag heap and subjected to magnetic separation to recover Activation technology of steel slag for concrete exposed to
.jpg)
Resource Utilization of Copper Slag with a Focus on Springer
2024年2月7日 Reduction The reduction process for copper slag is typically followed by magnetic separation []Depending on the temperature and intensity of reduction, it can be classified as direct reduction, deep reduction, and smelting reduction []Commonly used reducing agents include coke, biomass carbon, and natural gas [31, 32]The reduction process converts 2019年5月23日 The Hefei Designing Institute of Cement Research used an HRM2800 vertical mill in a certain company in Tongling with steel slag that was not treated using magnetic separation and that treatment via magnetic separation as the raw material for a steel slag grinding test The requirement for deironing was strictly prehensive Utilization Technology of Steel Slag2020年10月12日 Slags coming from stainless steel (SS) and ferrochromium (FeCr) production generally contain between 1 and 10% Cr, mostly present in entrapped metallic particles (Fe–Cr alloys) and in spinel structures To recover Cr from these slags, magnetic and gravity separation techniques were tested for upconcentrating Cr in a fraction for further processing In case of UpConcentration of Chromium in Stainless Steel Slag and MDPIDOI: 101016/S1006706X(17)300237 Corpus ID: ; Optimization of magnetic separation process for iron recovery from steel slag @article{Lan2017OptimizationOM, title={Optimization of magnetic separation process for iron recovery from steel slag}, author={Yuanpei Lan and Qingcai Liu and Fei Meng and Deliang Niu and Heng Zhao}, Optimization of magnetic separation process for iron recovery
.jpg)
Recycling of steelmaking slag fines by weak magnetic separation
2014年11月1日 To differentiate this development from conventional lowintensity magnetic separation (1000–3000 G), our method reported here is referred to as weak magnetic separation due to the use of extremely low surface magnetic field strengths for effective separation of steelmaking slag fines Weak magnetic separation is quite effective in treating During the pyrometallurgical treatment of the nickelbearing laterite in the plant of GMM SA LARCO, slag is produced after treatment in electricarc furnace (EAF) that contains 010 to 020 % Ni Taking into account the great quantity of slag produced per year, the recovery of nickel from the EAF slag will add benefits to the entire process The target of the current work is to Nickel recovery from electric arc furnace slag by magnetic separation2022年9月25日 Fire treatment, magnetic separation treatment, alkali leaching treatment of CSS and oxygen pressurization in the acid leaching process can effectively improve the leaching efficiency of acid leaching (Zhang et al, 2021) Oxidants such as liquid chlorine or hydrogen peroxide are often added to accelerate the dissolution of copperExtraction and separation of copper and iron from copper smelting slag 2023年11月7日 Magnetic separation has wideranging applications in both mineral processing and recycling industries Nevertheless, its conventional utilization often overlooks the interplay between mineral and particle Characterization of Magnetic and Mineralogical
.jpg)
Enrichment Characteristics of Cr in Chromium Slag after Pre
PreReduction and Melting/Magnetic Separation Treatment Shaoyan Hu 1, Deyong Wang 1, along with the alloy and tail slag after separation, were comprehensively analyzed2021年8月30日 More importantly, a relatively low prereduction temperature and selection of magnetic separation process were found to be more beneficial for chromium enrichment in slag; the highest chromium (PDF) Enrichment Characteristics of Cr in Chromium 2017年1月1日 During the pyrometallurgical treatment of the nickelbearing laterite in the plant of GMM SA LARCO, slag is produced after treatment in electricarc furnace (EAF) that contains 010 to 020 % NiNickel recovery from electric arc furnace slag by magnetic separation2014年1月10日 Two variants of magnetic separation were performed on LD slag The first one deals with treatment of ground LD slag at different particle size fractions of 1 mm, 400 μm, 200 μm and 200 μm by dry magnetic separation This technique may be applied on the coarse fraction of LD slag to recover only iron scrapsRecovery of high grade iron compounds from LD slag by enhanced magnetic
.jpg)
Separation and extraction of iron resources from hazardous
2024年10月1日 The main components of EAF slag are Fe x O, Fe, CaO, SiO 2, MgO, and MnOThe EAF slag contains more iron, but it is mainly dominated by RO phase, which is difficult to be recovered by magnetic separation, resulting in low utilization of iron in slag (Liu et al, 2023, Zhang et al, 2019)The traditional view that EAF slag and converter slag are similar in nature, 2022年4月27日 In this paper, we reviewed steel slag treatment, When the mixed slag was modified at 1200℃, the grade of magnetic slag by magnetic separation was 3114% and the recovery was 6404%, Optimization of Iron Recovery from BOF Slag by Oxidation and Magnetic 2013年4月1日 magnetic treatment; whereas Fe recovery is the ratio of (Fe 2 SiO 4 ) are investigated for the recovery of iron from ironrich nickel slag by oxidationmagnetic separation(PDF) Recovery of iron from waste slag of pyrite ResearchGateDOI: 101016/jjmrt202301186 Corpus ID: ; Efficient separation of iron elements from steel slag based on magnetic separation process @article{Liu2023EfficientSO, title={Efficient separation of iron elements from steel slag based on magnetic separation process}, author={Xin Liu and Dazhi Wang and Zhiwei Li and Wei Ouyang and Yanping Bao and Chao Gu}, Efficient separation of iron elements from steel slag based on magnetic
.jpg)
(PDF) An airfluidized magnetic separator and its separation
2024年3月1日 Primary magnetic separation tests on a steel slag fine powder material demonstrate that the air fluidized dry magnetic 4 J L Guo, Y P Bao, and M Wang, “Steel slag in China: Treatment