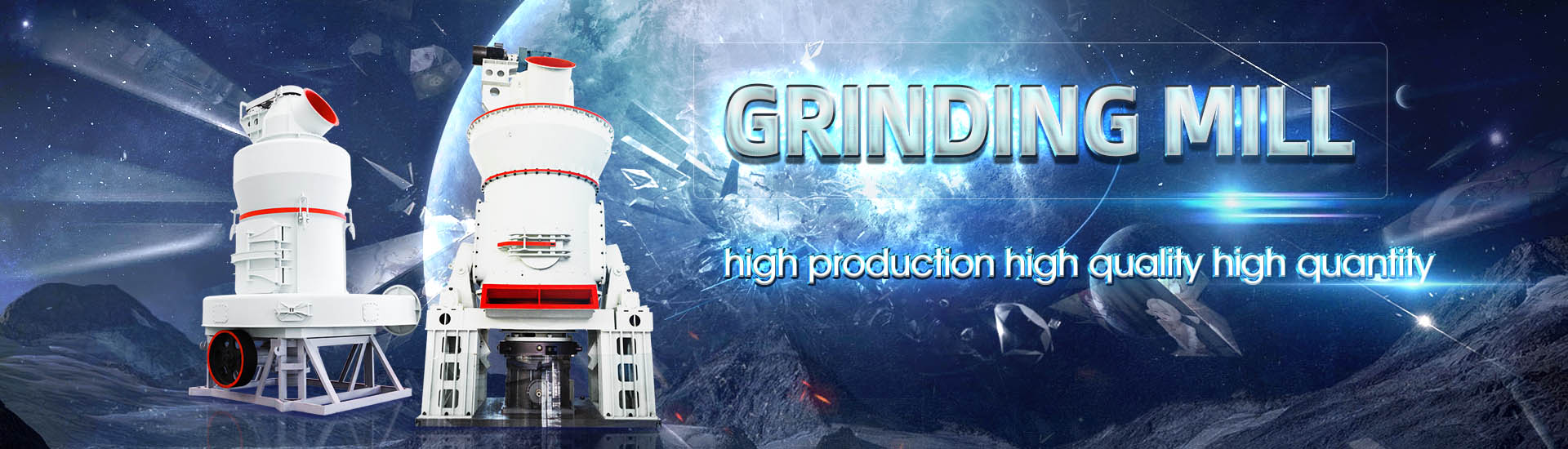
What can be done by crushing waste spodumene ore powder grinding slag
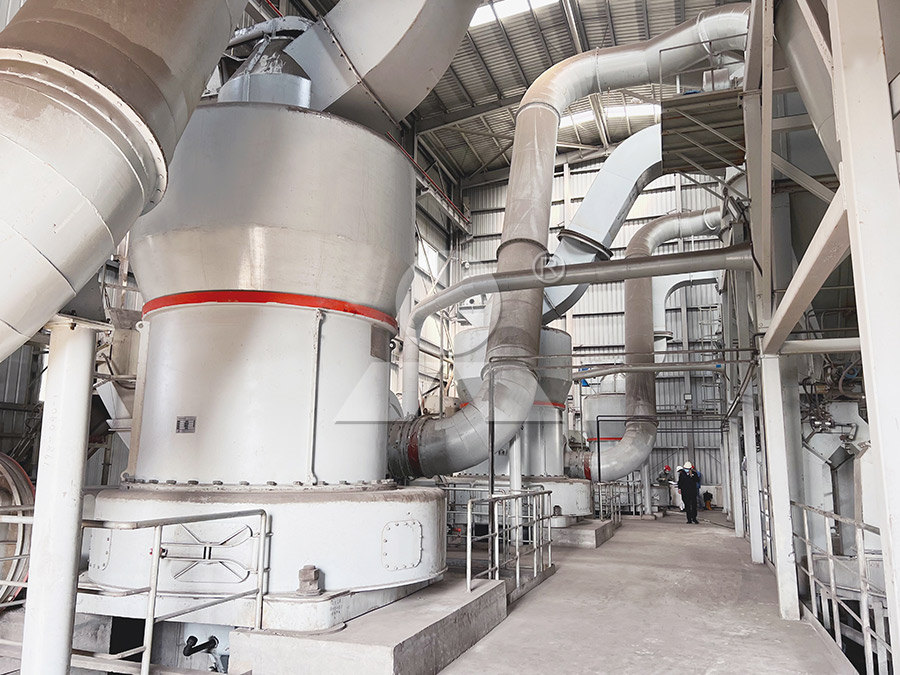
Hard Rock Spodumene Lithium Processing Saltworks
2023年12月27日 In step 1, to convert spodumene into lithium sulfate (Li 2 SO 4), the raw ore is crushed and separated both mechanically and via floatation Next, the concentrate undergoes energy and chemically intensive hot acid Spodumene ores are typically consolidated from ore comprising 1–15% Li20 to a concentrate of about 6–65% Li20 To achieve this, the ore passes through a typical concentratortype plant, Lithium processing technology Complete solutions that FLSmidthThe extraction process of lithium from spodumene (LiAlSi 2 O 6) begins with comminution such as crushing and grinding to liberate the lithium minerals from the ore matrix followed by METS Engineering Group Pty Ltd Level 3, 44 Parliament Place, Lithium can be extracted from spodumene concentrates after roasting and acid roasting operations A concentrate with at least 6% Li2O (approximately 75% spodumene) is suitable Hard Rock Lithium Processing SGS
.jpg)
Mechanical enrichment of converted spodumene by selective sieving
2016年11月1日 Particle size separation was effective for the enrichment of spodumene concentrate Almost pure spodumene concentrates were obtained by selective sieving Waste 2021年8月15日 In this work, the comprehensive utilization of spodumene waste residue lithium slag is achieved An experimental scheme of hydrothermal preparation of nanokaolinite and Comprehensive utilization of waste residue from lithium extraction 2022年10月31日 Simulations and scaleup of grinding circuits can be done based on the specific energy to reduce the particle size of the product ie the Bond method which could be Lithium deportment by size of a calcined spodumene ore2019年5月29日 This process starts with the crushing of spodumene ore The cause behind the grinding of the spodumene is an acceleration of the heat transfer between the surrounding atmosphere and the mineral The crushed Spodumene: The Lithium Market, Resources and
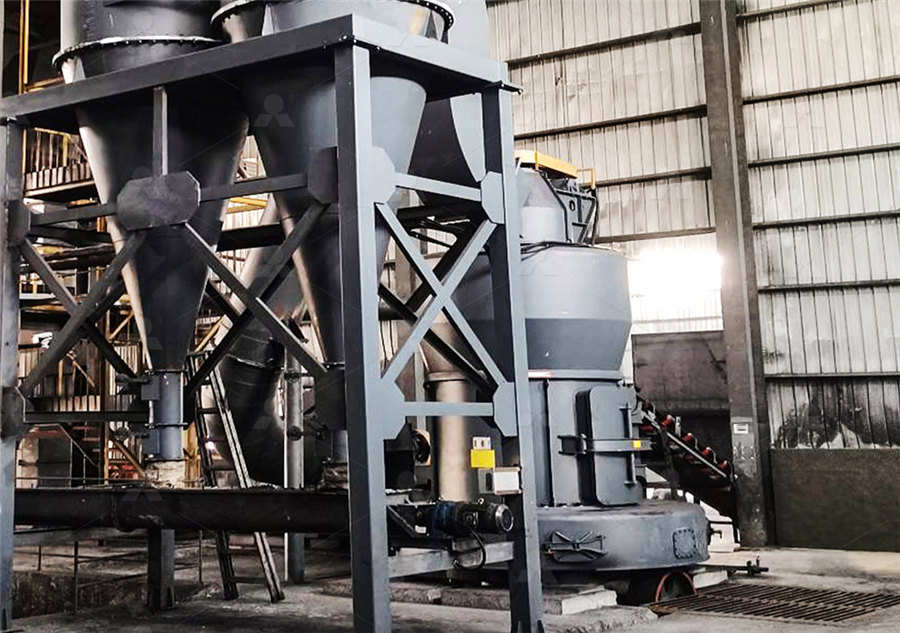
Lithium Extraction from Spodumene by the Traditional Sulfuric
2020年8月12日 The sulfuric acid process is the dominant technology for lithium extraction from spodumene However, this process generates huge quantities of waste residue and needs mineral processing, art of treating crude ores and mineral products in order to separate the valuable minerals from the waste rock, or gangue It is the first process that most ores undergo after mining in order to provide a more Mineral processing Metallurgy, Crushing2016年5月10日 In the handling of wet, sticky ores such as encountered in tropical areas having distinct dry and rainy seasons, the crushing plant is a section of the mill which must be planned very carefully Unless this is done, crushing becomes a constant source of trouble resulting in lost production and high milling cost In some areas rainfall is high for prolonged periodsCrushing and Grinding Wet Sticky Ore 911Metallurgist2023年9月8日 Step 2 Crushing and grinding production line First, the raw lithium ore undergoes a crushing and grinding process in sequence to produce a uniform fine particle size When crushing, the jaw crusher is used for coarse (primary) The Most Effective Lithium Ore Processing Method You
.jpg)
The Recovery and Concentration of Spodumene Using Dense
2021年6月18日 In coming years, global lithium production is expected to increase as the result of widespread electric vehicle adoption To meet the expected increase in demand, lithium must be sourced from both brine and hardrock deposits Heavy liquid separation (HLS) and dense media separation (DMS) tests were conducted on the pegmatites from Hidden Lake, NWT, 2019年1月15日 Run of mine spodumene ore is crushed −16 mm by primary and secondary jaw crushing and tertiary cone crushing which is then fed to a ball mill The undersize (−250 μm) fraction from the ball mill discharge is feed to cyclones to remove the slimes (−20 μm) as tailings, and the cyclone underflow is fed to the flotation circuit ( Bale and May, 1989 )The beneficiation of lithium minerals from hard rock ores: A 2015年8月3日 The ores that are mined from deposits contain the valuable minerals attached to and enclosed in lumps of waste rock The processing like crushing will disintegrate and unlock the values from the (PDF) Overview of Mineral Processing Methods ResearchGate2011年10月27日 A flux, such a fluorspar (calcium fluoride) can be added to accelerate slag formation but increases the cost of the process Volume stability The final slag can have a lime/silica ratio of about 3 or 4, although this can vary substantially from one heat to the nextBasics of slag production Article on the slag industry from Global Slag
.jpg)
Difference between Crushing and Grinding 911Metallurgist
2017年2月17日 When making comparisons of the efficiencies of different grinding and crushing machines it is desirable to be able to estimate the work actually done in crushing the ore from a given size of feed to a given size of product, the screen analysis of both feed and product being determined Messrs Klug and Taylor, in a paper on this subject, published in the monthly 2012年1月1日 "Spodumene mineral is a source of lithium for lithium ion batteries Thus, the production of a spodumene concentrate with an approximate grade of 6% Li2O is targeted Traditionally, spodumene is concentrated by froth flotation using fatty acid as the collector Amine collector can also be used to float mica ahead of spodumene as required or feldspar from the An Overview of Spodumene Beneficiation OneMine2018年1月15日 Request PDF Assessment of a spodumene ore by advanced analytical and mass spectrometry techniques to determine its amenability to processing for the extraction of lithium A combination of Assessment of a spodumene ore by advanced analytical and mass 2024年8月5日 Extraction of lithium from spodumene involves a series of expensive and energyintensive steps that emit unwanted greenhouse gases and result in hazardous waste streams The twostep process involves heating the mineral ore twice First, spodumene is roasted at 1,050 °C (1,976 °F) to convert it into a state suitable for chemical processingMechanochemistry Releases Lithium from Ore by Crushing It
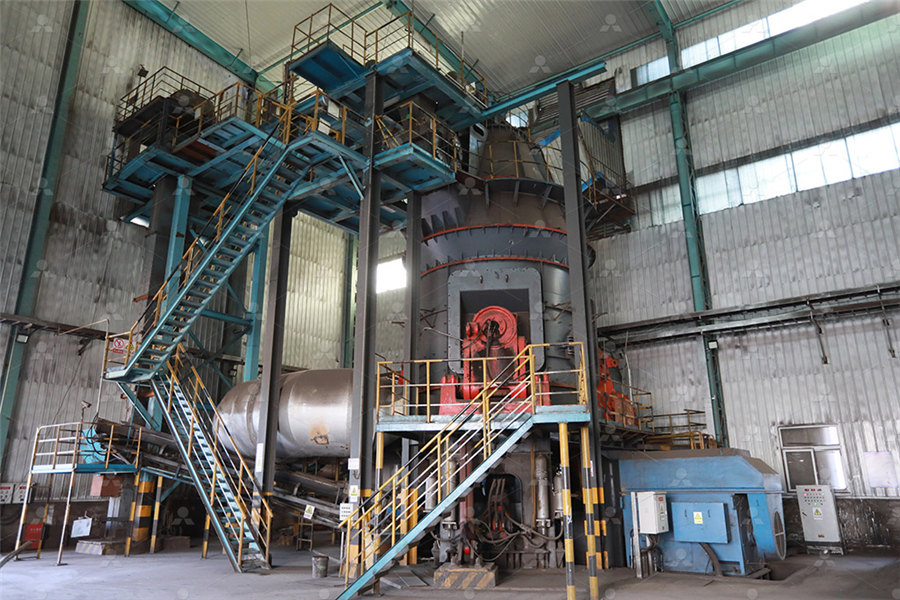
Lithium deportment by size of a calcined spodumene ore
2022年4月21日 Lithium is a key component in green energy storage technologies and is rapidly becoming a metal of crucial importance to the European Union The different industrial uses of lithium are discussed 2020年8月12日 The sulfuric acid method initially requires subjecting natural spodumene to hightemperature calcination, transforming it from αspodumene to βspodumene [59,60] Following crushing and grinding Lithium Extraction from Spodumene by the Traditional Sulfuric 2023年7月3日 (1) Crushing and Grinding of the Ore The ores occur in nature as huge lumps They are broken to small pieces with the help of crushers or grinders These pieces are then reduced to fine powder with the help of a ball mill or stamp mill This process is called pulverisation (2) Concentration of Ore or Ore BenefactionCrushing, Grinding and Concentration of the Ore2022年2月26日 Blast furnace slag can be processed into the following materials by various processes In China, blast furnace slag is usually processed into water slag, slag gravel, expanded slag and slag beadsWater slag is the process of putting the hotmelt blast furnace slag into water for rapid cooling, which mainly includes slag pool water quenching or furnace front What is Blast Furnace Slag and How to Process It?
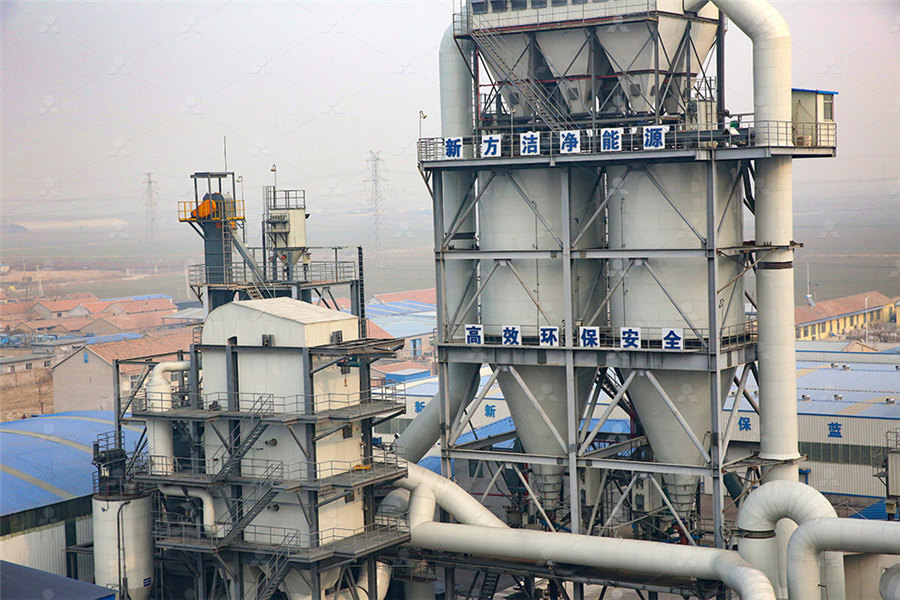
SIZE REDUCTION BY CRUSHING METHODS By ResearchGate
Crushing is normally carried out on "runofmine" ore, while grinding (normally carried out after crushing) may be conducted on dry or slurried material In comminution, the size reduction ofCarbon dioxide sequestration using steel slag—modeling and experimental investigation Smitha Gopinath, Anurag Mehra, in Carbon Dioxide Sequestration in Cementitious Construction Materials, 2018 41 Introduction Steel slag is an industrial waste that is generated during the production of steel In the production of steel, oxides of metal impurities in the iron combine Steel Slag an overview ScienceDirect Topics2023年5月15日 Steel slag is the main solid waste generated in the steelmaking process, accounting for 15 to 20% of crude steel output [1]China's crude steel output in 2021 was 1035 billion tons [2], more than half of the global crude steel output (19505 billion tons) [3], and the steel slag output exceeded 120 million tonsIn contrast, the comprehensive utilization rate of Comprehensive utilization of steel slag: A review ScienceDirect2023年11月20日 Figure 4 shows the total waste generation from the steel manufacturing process and how much industry and academic research got attention in various applications Their chemical composition, along with BOF, EAF, and LF slag, is shown in Table 2It is apparent that the BOF and EAF slags have almost identical chemical components, but a higher amount A Review on Environmental Concerns and Technological
.jpg)
Progress of Five Spodumene Beneficiation Methods
2024年11月21日 When the temperature is too high, the mica present in the ore will sinter; when the temperature is too low, the transformation of spodumene from α to β is incomplete ②The ore cannot contain a large amount of Lithium occurs naturally in over 145 minerals, but is commercially extracted from just five The most important mineral source is spodumene Extracting lithium from spodumene involves initial crushing, roasting at 2012°F (1100°C), further Lithium handling Carmeuse SystemsWhilst laboratory testwork indicates that lithium can be recovered and impurities removed, spodumene flotation at plant scale can be challenging due to reagent optimisation, grind size, water quality and the presence of slimes In addition, the activation of quartz and feldspar by iron salts introduced during grinding can be experiencedMETS Engineering Group Pty Ltd Level 3, 44 Parliament Place, 2023年12月27日 In step 1, to convert spodumene into lithium sulfate (Li 2 SO 4), the raw ore is crushed and separated both mechanically and via floatationNext, the concentrate undergoes energy and chemically intensive hot acidroasting This process (as shown in Figure 1 below) sees concentrated spodumene powder roasted at 1050°C, cooled, mixed with sulfuric acid, Hard Rock Spodumene Lithium Processing Saltworks Technologies

The Recovery and Concentration of Spodumene Using Dense
2021年6月18日 Summary of mineral abundance in the composite head sample; specific gravity; and concentration criterion (CC) in water and heavy liquid Lithium brine ponds: concentrating and precipitating impurities from geological lithium brines via evaporation pondsA highly concentrated lithium solution is subsequently refined and converted into lithium carbonate or hydroxide These lowcost operations are ideal for the convergence of rich lithium brines and arid climates, such as South America’s ‘lithium triangle’Lithium Extraction and Refining Saltworks Technologies2018年4月1日 The samples represent the spodumene zone lithologies within LCTComplex spodumenetype pegmatites (Cerny and Ercit, 2005) that are part of the mineral resource that will be mined by Pilbara Minerals Ltd Lithium Australia NL has a strategic alliance with Pilbara Minerals Ltd to assist the development of the halogenbased Sileach™ process, which can Assessment of a spodumene ore by advanced analytical and mass 2024年9月30日 Lithium (Li), a leading cathode material in rechargeable Liion batteries, is vital to modern energy storage technology, establishing it as one of the most impactful and strategical elements Given the surge in the electric car market, it is crucial to improve lithium recovery from its rich mineral deposits using the most effective extraction technique In recent years, both Aspects of Spodumene Lithium Extraction Techniques MDPI
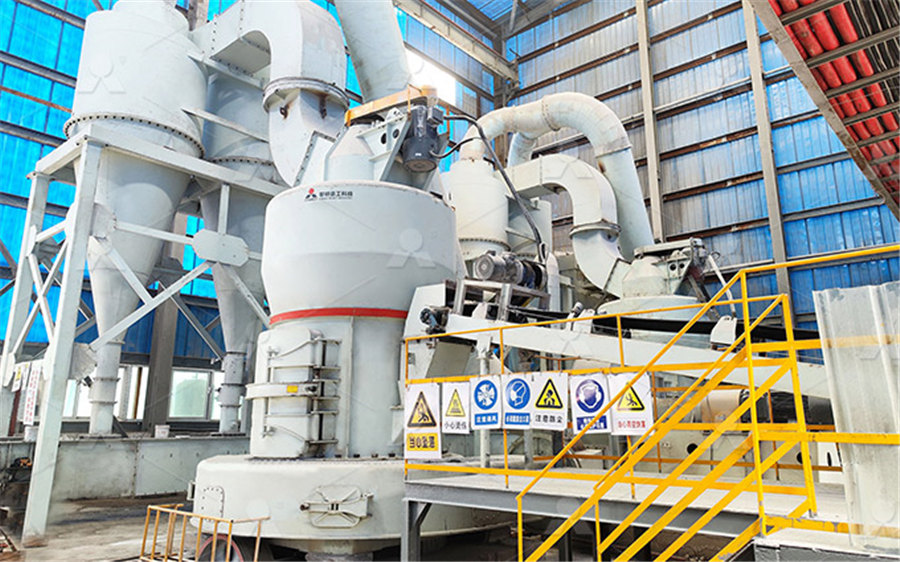
An effective method for directly extracting lithium from αspodumene
2023年6月25日 In addition, most investigations have focused on βspodumene instead of αspodumene, whereas the extra energy consumption is caused inevitably by hightemperature crystal transformation (αphase to βphase)Thus, some researchers directly choose αspodumene as the object of studyXing et al [33] successfully achieved the extraction of 2013年12月18日 Fine grinding, to P80 sizes as low as 7 μm, is becoming increasingly important as mines treat ores with smaller liberation sizes This grinding is typically done using stirred mills such as the Isamill or Stirred Media Detritor While fine grinding consumes less energy than primary grinding, it can still account for a substantial part of a mill’s energy budget Overall Energy Use of Fine Grinding in Mineral Processingmineral processing, art of treating crude ores and mineral products in order to separate the valuable minerals from the waste rock, or gangue It is the first process that most ores undergo after mining in order to provide a more Mineral processing Metallurgy, Crushing2016年5月10日 In the handling of wet, sticky ores such as encountered in tropical areas having distinct dry and rainy seasons, the crushing plant is a section of the mill which must be planned very carefully Unless this is done, crushing becomes a constant source of trouble resulting in lost production and high milling cost In some areas rainfall is high for prolonged periodsCrushing and Grinding Wet Sticky Ore 911Metallurgist
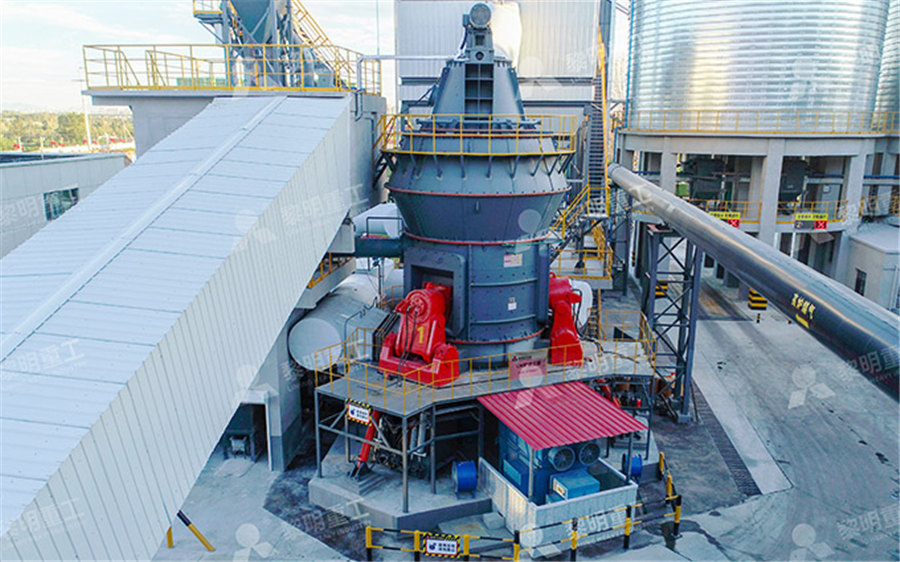
The Most Effective Lithium Ore Processing Method You
2023年9月8日 Step 2 Crushing and grinding production line First, the raw lithium ore undergoes a crushing and grinding process in sequence to produce a uniform fine particle size When crushing, the jaw crusher is used for coarse (primary) 2021年6月18日 In coming years, global lithium production is expected to increase as the result of widespread electric vehicle adoption To meet the expected increase in demand, lithium must be sourced from both brine and hardrock deposits Heavy liquid separation (HLS) and dense media separation (DMS) tests were conducted on the pegmatites from Hidden Lake, NWT, The Recovery and Concentration of Spodumene Using Dense 2019年1月15日 Run of mine spodumene ore is crushed −16 mm by primary and secondary jaw crushing and tertiary cone crushing which is then fed to a ball mill The undersize (−250 μm) fraction from the ball mill discharge is feed to cyclones to remove the slimes (−20 μm) as tailings, and the cyclone underflow is fed to the flotation circuit ( Bale and May, 1989 )The beneficiation of lithium minerals from hard rock ores: A 2015年8月3日 The ores that are mined from deposits contain the valuable minerals attached to and enclosed in lumps of waste rock The processing like crushing will disintegrate and unlock the values from the (PDF) Overview of Mineral Processing Methods ResearchGate
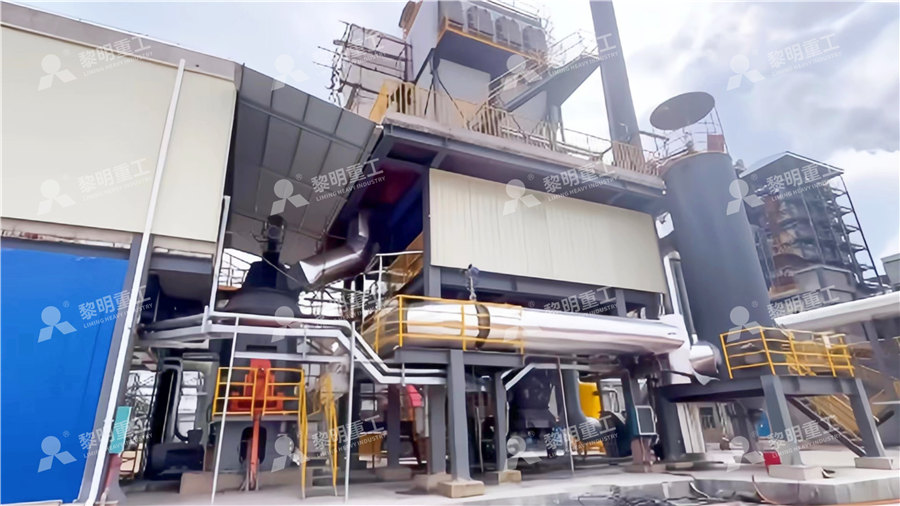
Basics of slag production Article on the slag industry from Global Slag
2011年10月27日 A flux, such a fluorspar (calcium fluoride) can be added to accelerate slag formation but increases the cost of the process Volume stability The final slag can have a lime/silica ratio of about 3 or 4, although this can vary substantially from one heat to the next2017年2月17日 When making comparisons of the efficiencies of different grinding and crushing machines it is desirable to be able to estimate the work actually done in crushing the ore from a given size of feed to a given size of product, the screen analysis of both feed and product being determined Messrs Klug and Taylor, in a paper on this subject, published in the monthly Difference between Crushing and Grinding 911Metallurgist2012年1月1日 "Spodumene mineral is a source of lithium for lithium ion batteries Thus, the production of a spodumene concentrate with an approximate grade of 6% Li2O is targeted Traditionally, spodumene is concentrated by froth flotation using fatty acid as the collector Amine collector can also be used to float mica ahead of spodumene as required or feldspar from the An Overview of Spodumene Beneficiation OneMine