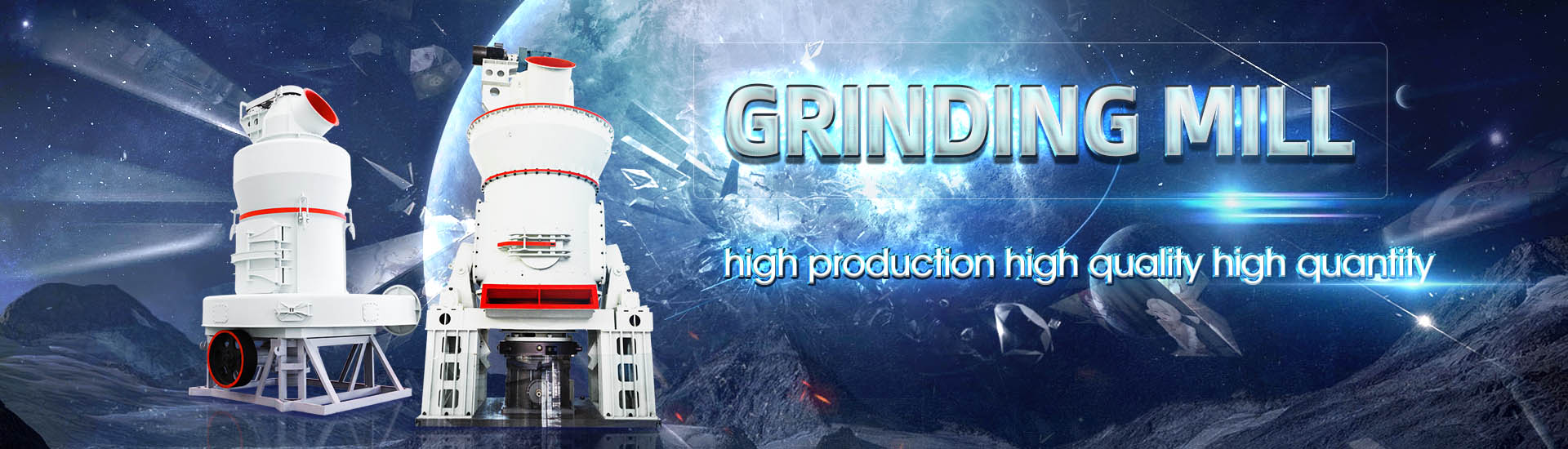
Coal mine electrolytic aluminum waste slag grinding mill crushing station
.jpg)
Recovery of Carbon and Cryolite from Spent Carbon Anode Slag
2023年3月12日 For carbon anode slag of electrolytic aluminum, Ni et al investigated the selective comminution and grinding mechanisms of rod and ball mills and proposed that a Feature papers represent the most advanced research with significant Versions Notes2024年5月23日 Here, we review carbonrich solid wastes with focus on sources and hazards, detoxification, separation, recovery, recycling and disposal Treatment techniques include The recycling of carbonrich solid wastes from aluminum 2022年10月10日 In this work, electrolytic aluminum carbon anode slag was separated by flotation Using the selectivity index ( SI) as an indicator, the influencing factors of the carbon Recovery of carbon and cryolite from spent carbon anode slag of
.jpg)
Selective comminution and grinding mechanisms of spent carbon
2022年1月10日 In this study, grinding characteristics of spent carbon anode from aluminum electrolysis in both ball mill and rod mill were analyzed, and compared based on the utilization 2023年4月25日 This article analyzes and summarizes the composition and hazards of the overhaul slag and the current development status of domestic and international electrolytic Research Progress of Electrolytic Aluminum Overhaul Slag Disposal2023年8月1日 The aluminum and silicon dissolved from the overhaul slag could be electrolytically reduced to Al–Si intermediate alloy In this scene, the craft could realize Dissolution behavior of overhaul slag from aluminum reduction anode slag under different factors (grinding time, flotation feed solid concentration, collector dosage, frother dosage, and pH of slurry) was investigated using selectivity indexRecovery of carbon and cryolite from spent carbon anode slag of
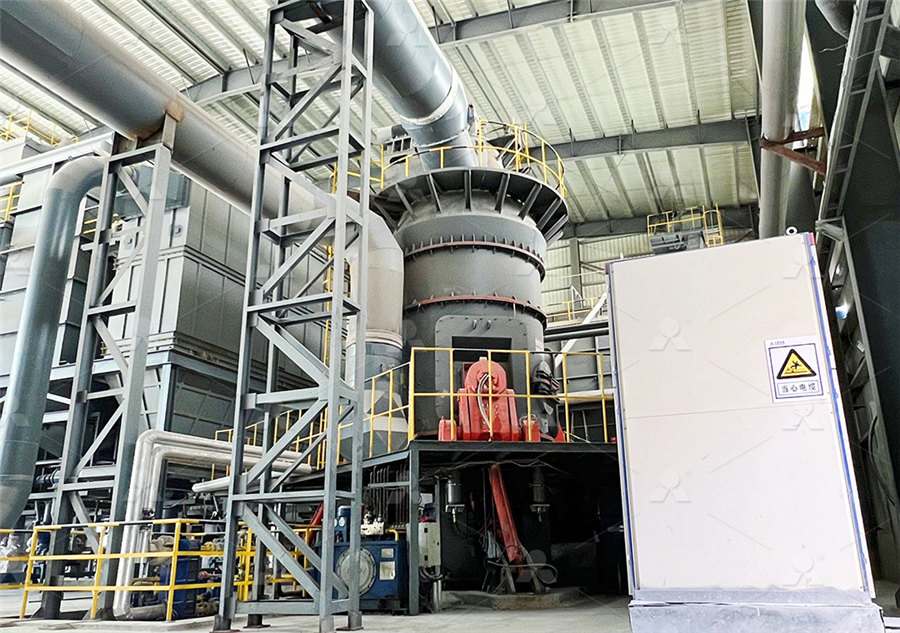
Efficient lithium recovery from electrolytic aluminum slag via an
2024年2月1日 The electrolytic aluminum industry generates a large amount lithium (Li)containing electrolytic aluminum slag (EAS) annually, and this can result in severe 2024年1月1日 Problems and challenges faced by the application of underground backfilling with multisource solid waste in coal mine are here analysed This research can provide new ideas Feasibility and challenges of multisource coalbased solid waste 2024年2月21日 Grind the aluminum electrolysis waste residue through a Cryolite Raymond Roller Mill to below 75250 microns After removing the carbon and iron in the waste residue, Aluminum slag recycled cryolite powder production line2022年1月10日 The recovery of spent carbon anode (SCA) materials plays important roles in environment protection and resources recycling, while this cannot be efficiently achieved without liberationSelective comminution and grinding mechanisms of
.jpg)
Recovery of carbon and cryolite from spent carbon
2022年10月9日 1 Department of Mining Engineering, Shanxi Institute of Technology, Yangquan, China; 2 Department of Mining Engineering, Balochistan University of Information Technology, Engineering and Management Sciences and then to the power station site The purpose of the coal stockyard is to ensure that there is sufficient coal reserves available to keep the power station in operation should the mine experience production problems Inside the power station, the coal is pulverised to a fine powder in giant grinding mills This is because pulverised coal HOW ELECTRICITY IS PRODUCED AT A COALFIRED POWER STATION Coal waste in Pennsylvania Coal refuse (also described as coal waste, rock, slag, coal tailings, waste material, rock bank, culm, boney, or gob [1]) is the material left over from coal mining, usually as tailings piles or spoil tips For every tonne of hard coal generated by mining, 400 kg (880 lb) of waste material remains, which includes some lost coal that is partially economically Coal refuse Wikipedia2023年3月12日 The aluminum electrolysis industry continually and unavoidably produces hazardous solid waste in the form of carbon anode slag Carbon anode slag poses a serious environmental pollution risk, and (PDF) Recovery of Carbon and Cryolite from Spent Carbon Anode Slag
.jpg)
Efficient lithium recovery from electrolytic aluminum slag via an
2024年2月1日 Aluminum metal was produced using the cryolitealumina molten salt electrolysis method (Ishak et al, 2017)A large amount electrolytic aluminum slag (EAS) is generated during the electrolysis process, as the falling of carbon particles on the anode into the electrolysis cells and the accumulation of lithium fluorine result in energy consumption and electrolyte scrapping 2023年1月1日 Washery wastes result from the coal separation process They account for about 80% of the total waste mass on average, which are subdivided into the following groups: (1) tailings or slurries generated from flotation processes, and their sizes are finer than 1 mm in diameter, (2) finegrained waste produced from sedimentation procedures where the sizes Coal wastes: handling, pollution, impacts, and utilization2024年2月3日 Fine slag (FS) is an unavoidable byproduct of coal gasification FS, which is a simple heap of solid waste left in the open air, easily causes environmental pollution and has a low resource utilization rate, thereby restricting the development of energysaving coal gasification technologies The multiscale analysis of FS performed in this study indicates typical grain size Multiscale analysis of fine slag from pulverized coal gasification in 2023年3月12日 The aluminum electrolysis industry continually and unavoidably produces hazardous solid waste in the form of carbon anode slag Carbon anode slag poses a serious environmental pollution risk, and it must be disposed of in a harmless manner On the other hand, it contains a few valuable resources, as well In order for the aluminum electrolysis industry to Recovery of Carbon and Cryolite from Spent Carbon Anode Slag
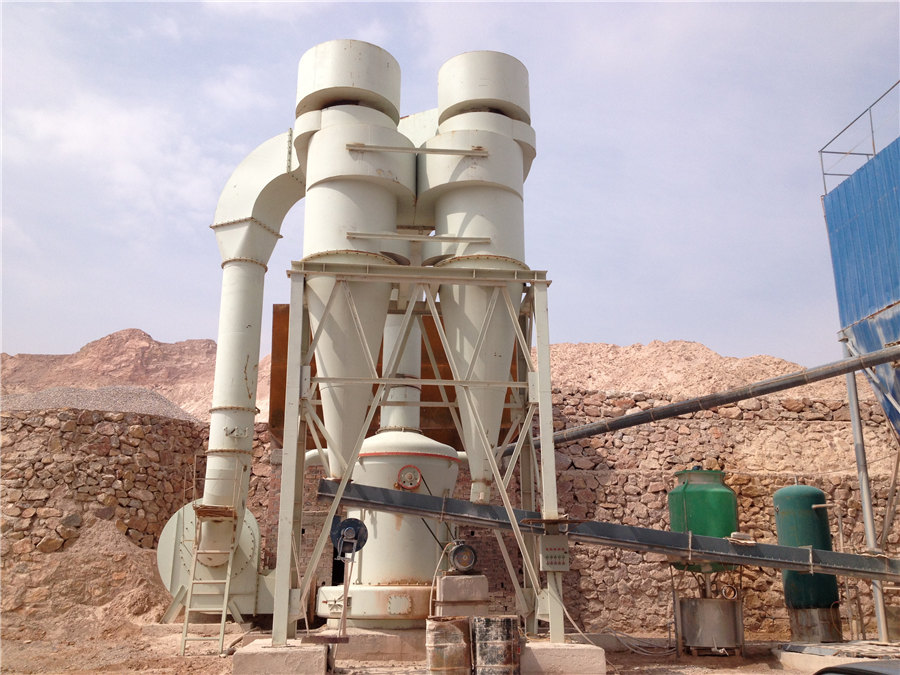
Research on the Coprocessing of Mixed Electrolytic Aluminum Waste
for electrolytic aluminum waste is proposed This mode is to pulverize the electrolytic aluminum waste, and then mix the crushed electrolytic aluminum waste with the raw coal of the circulating fluidized bed boiler [6], then send it to the circulating fluidized bed boiler for combustion In this study, a mixed combustion experiment of2022年5月12日 Commonly used crushing equipment are impact crusher, roller crusher, cone crusher and slag mobile crushing station Milling equipment As a new type of admixture for highperformance concrete, slag micro powder has Slag grinding mill micro powder production lineProcess introduction Vertical coal mill, also known as vertical roller coal mill or vertical coal grinding mill, is a mechanical equipment for crushing and grinding coal into coal powerMainly used for grinding raw coal, bituminous coal, and other fuels into coal powder, which is supplied to rotary kiln and other kilns in the cement plant and thermal power plantcoal grinding machine CHAENG2022年6月17日 At present, the equipment can be used in more markets such as solid waste residue, coal mine, cement raw meal, clinker, manganese ore, etc The micro slag powder does not need to go through the crushing process in production, because the raw material size is small, but because the slag is a byproduct in the process of blast furnace ironmaking and the Slag Powder Vertical Roller Grinding Mill
.jpg)
Slag Crusher Plant Manufacturer Exporters India Jaikar Jaw
ABOUT JAIKAR "Jaikar" has been one of the Largest Crusher Manufacturers in India For crushing industry plays an important role in our rapiddevelop world, we will never stop our footsteps in pursuing better quality and better service to 2021年4月19日 It is an excellent equipment for grinding water slag, steel slag and other solid wasteWe have been deeply engaged in the grinding market for nearly 50 years, with sufficient experience, many cases, more mature team and high evaluation from customersWhat is the grinding mill for grinding slag? – gkmillWhen a jaw crusher is equipped with the ASC system, the crushing forces are carried by massive hydraulic cylinders mounted into the rear header casting If an uncrushable object enters the crusher cavity and crushing forces reach the preset maximum level, oil starts to escape out of the cylinders and the setting releasesSlag crushing MetsoMaximize material recovery with GK’s VIBRADRUM® technology for grinding, crushing, and leaching! General Kinematics VIBRADRUM® Grinding Mills are proven in dozens of milling applications in the mining and mineral industries Because of this flexibility, they are the perfect solution for your needs, no matter the grinding processes you useGrinding Crushing Mill VIBRADRUM® General Kinematics
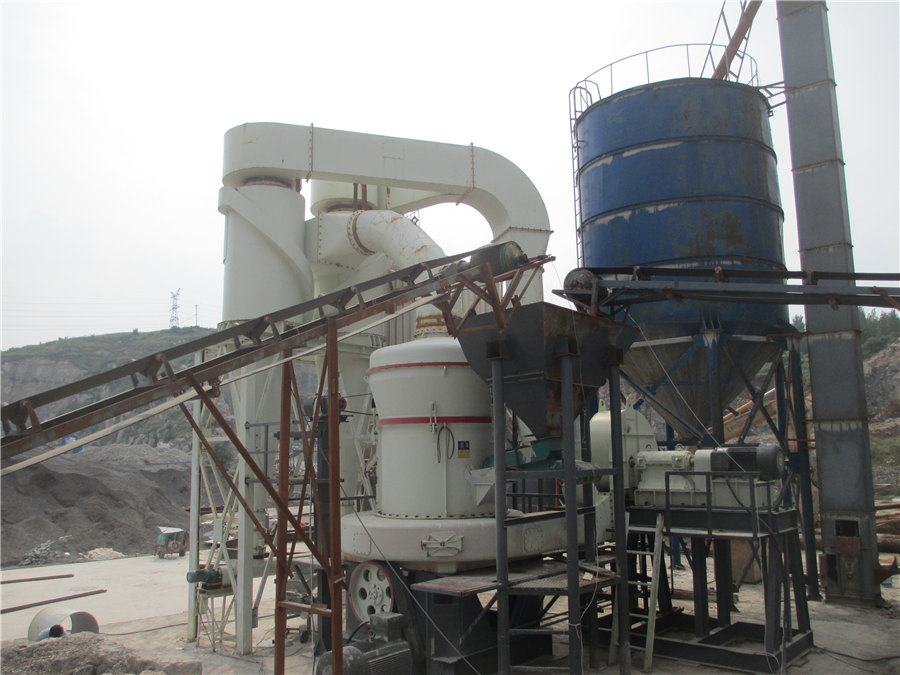
Research on Using Carbide Slag to Mineralize the Carbon Dioxide
2024年2月2日 Calcium carbide slag is a difficult industrial waste to treat Millions of tons of calcium carbide slag are piled up in China yearly, occupying a large amount of land and easily causing secondary pollution []The main component of calcium carbide slag is Ca(OH) 2, with 71–95% content []Therefore, the current recycling methods of calcium carbide slag mainly 2023年10月1日 The main components of waste aluminum cryolite electrolyte are cryolite (Na 3 AlF 6), potassium cryolite (K 2 NaAlF 6), lithium cryolite (Na 2 LiAlF 6), fluorite (CaF 2), and approximately 2% carbon black (Wang et al, 2019)The main treatment methods of waste aluminum cryolite electrolyte can be divided into two categories: combined thermalwet Efficient extraction and recovery of lithium from waste aluminum 2024年7月17日 Crushing is a multistage process that includes primary crushing, secondary crushing, and tertiary crushing Different types of crushing equipment are used at each stage to meet various crushing requirements Primary crushing breaks down large raw materials into mediumsized pieces for easier handling in subsequent processesTypes of Crushers: Choosing the Right One for Each Stage2022年1月23日 The crushing area may also include equipment for separation by particle size such as vibrating screens or rollerscreens; both having openings of a known size for proper size separation Preparing the RunofMine (ROM) bauxite for the grinding mill circuit must be completed in order to efficiently size the grinding mill circuitPhysical Bauxite Processing: Crushing and Grinding of Bauxite
.jpg)
Crusher; Grinding Mill; Rotary Dryer Manufacturer, Cone Crusher,
STM is a hightech company integrating RD, production and distribution, and provides crusher, sand making, grinding equipment, mobile crushing station, etc Mature products and solutions used in aggregate, mining and waste recycling At present, we have established cooperative relations with customers in more than 30 2014年1月1日 The emission factors of kiln end, kiln head, coal mill, crushing and cement mill was 0156 clinker g/t, 3914 clinker g/t, 1538 coal g/t, 0016 stone g/t and 0056 cement g/t respectively, the (PDF) MPS mills for coal grinding ResearchGate2022年10月1日 Thus, it is necessary to study the interaction between the electrolytic aluminum waste and coal during the cocombustion process After grinding, sieving and airdrying (at 105 °C), Combustion process of Efficient lithium recovery from electrolytic aluminum slag via an environmentally friendly process: Leaching behavior Cocombustion characteristics of electrolytic aluminum waste and coal Grinding media are essential components of coal grinding mills, as they are responsible for crushing and grinding the coal material into small particles Grinding media can be made of various materials, including steel balls, ceramic balls, and cylpebs, depending on the specific application and grinding requirementsWhat is a Coal Grinding Mill
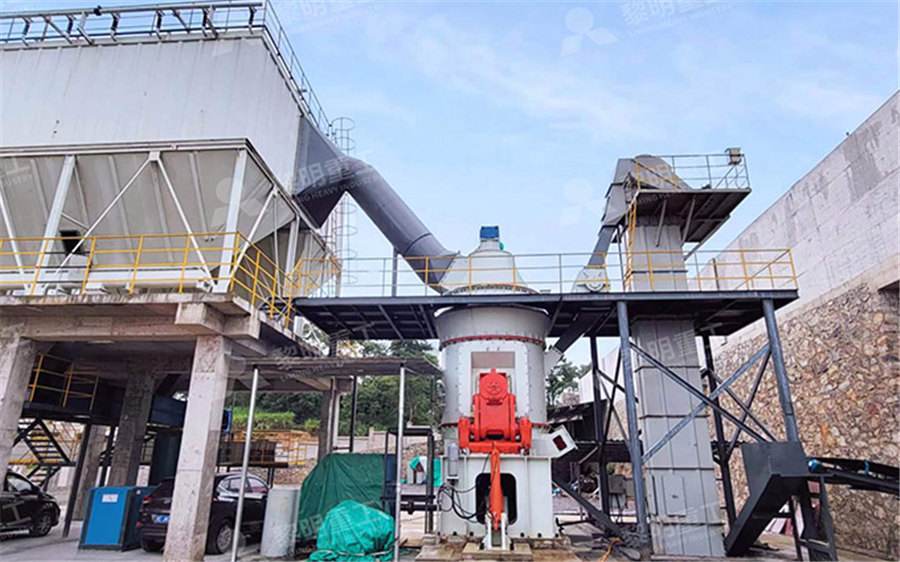
Methods for Beneficiation of Ash and Slag Waste from Coal
2019年4月17日 Abstract— Ash and slag waste (ASW) from coalfired thermal power plants (TPPs), the amounts of which make several tens or even hundreds of millions of tons per annum, require allocation of large land areas for storing them This waste is a source of pollution emitted into the atmosphere and it poisons the aqueous medium and soil Ash and slag waste consists 2020年10月22日 crushing station in openpit mine based on twostage fusion particle swarm algorithm, Engineering Optimization, DOI: 101080/X2020 To link to this article: https://doior g/101080 Layout optimization of crushing station in openpit mine based 2023年12月27日 Ball mill; Steel slag belongs to a type of industrial waste If not properly utilized, it will inevitably cause environmental pollution The most suitable equipment for processing this mine is the ball mill Steel slag through grinding can save energy and equipment costs, and the ball mill has good grinding ability and low overall energy Steel Slag Processing Plant Equipment Selection2020年8月12日 Vertical Coal Mill (VCM) is equipment for grinding and pulverizing coal into micron size Rotary kilns then use the powders as fuel burners The VCM has a housing section equipped with a lining An investigation of performance characteristics and energetic
.jpg)
How to Process Coal into Pulverized Coal in 5 Steps?
2024年1月11日 With a vertical roller mill (VRM) VRMs consist of a rotating table or bowl and rollers 1 To grind the coal, feed raw or initially crushed coal into the mill which is then ground between the rotating components; 2 Finally, hot air removes moisture, carries the pulverized coal out, and a classifier segregates the particles; Here is all you need to know about the VRM:2022年1月10日 The recovery of spent carbon anode (SCA) materials plays important roles in environment protection and resources recycling, while this cannot be efficiently achieved without liberationSelective comminution and grinding mechanisms of 2022年10月9日 1 Department of Mining Engineering, Shanxi Institute of Technology, Yangquan, China; 2 Department of Mining Engineering, Balochistan University of Information Technology, Engineering and Management Sciences Recovery of carbon and cryolite from spent carbon and then to the power station site The purpose of the coal stockyard is to ensure that there is sufficient coal reserves available to keep the power station in operation should the mine experience production problems Inside the power station, the coal is pulverised to a fine powder in giant grinding mills This is because pulverised coal HOW ELECTRICITY IS PRODUCED AT A COALFIRED POWER STATION
.jpg)
Coal refuse Wikipedia
Coal waste in Pennsylvania Coal refuse (also described as coal waste, rock, slag, coal tailings, waste material, rock bank, culm, boney, or gob [1]) is the material left over from coal mining, usually as tailings piles or spoil tips For every tonne of hard coal generated by mining, 400 kg (880 lb) of waste material remains, which includes some lost coal that is partially economically 2023年3月12日 The aluminum electrolysis industry continually and unavoidably produces hazardous solid waste in the form of carbon anode slag Carbon anode slag poses a serious environmental pollution risk, and (PDF) Recovery of Carbon and Cryolite from Spent Carbon Anode Slag 2024年2月1日 Aluminum metal was produced using the cryolitealumina molten salt electrolysis method (Ishak et al, 2017)A large amount electrolytic aluminum slag (EAS) is generated during the electrolysis process, as the falling of carbon particles on the anode into the electrolysis cells and the accumulation of lithium fluorine result in energy consumption and electrolyte scrapping Efficient lithium recovery from electrolytic aluminum slag via an 2023年1月1日 Washery wastes result from the coal separation process They account for about 80% of the total waste mass on average, which are subdivided into the following groups: (1) tailings or slurries generated from flotation processes, and their sizes are finer than 1 mm in diameter, (2) finegrained waste produced from sedimentation procedures where the sizes Coal wastes: handling, pollution, impacts, and utilization
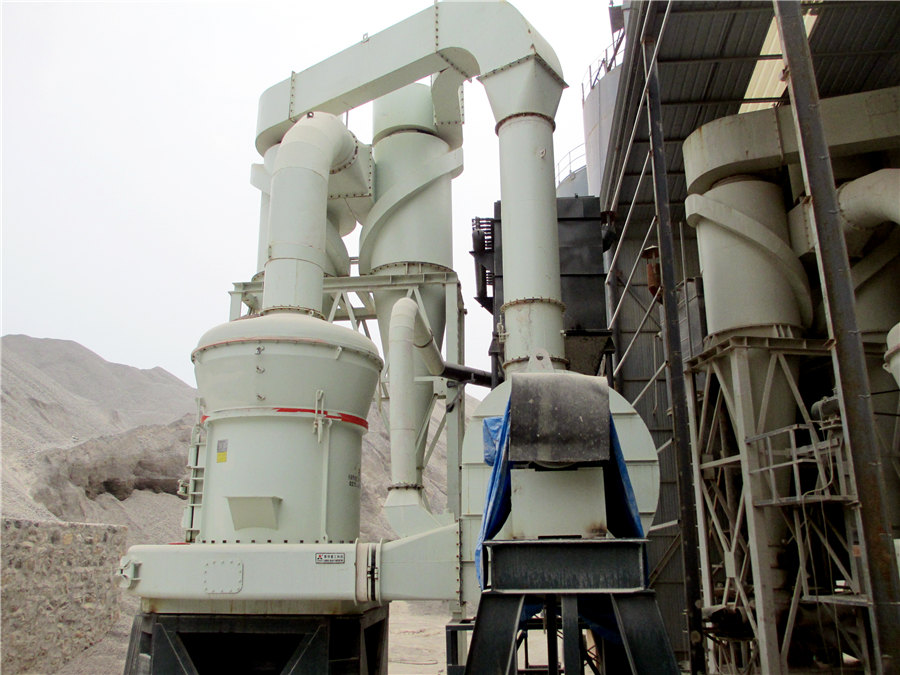
Multiscale analysis of fine slag from pulverized coal gasification in
2024年2月3日 Fine slag (FS) is an unavoidable byproduct of coal gasification FS, which is a simple heap of solid waste left in the open air, easily causes environmental pollution and has a low resource utilization rate, thereby restricting the development of energysaving coal gasification technologies The multiscale analysis of FS performed in this study indicates typical grain size 2023年3月12日 The aluminum electrolysis industry continually and unavoidably produces hazardous solid waste in the form of carbon anode slag Carbon anode slag poses a serious environmental pollution risk, and it must be disposed of in a harmless manner On the other hand, it contains a few valuable resources, as well In order for the aluminum electrolysis industry to Recovery of Carbon and Cryolite from Spent Carbon Anode Slagfor electrolytic aluminum waste is proposed This mode is to pulverize the electrolytic aluminum waste, and then mix the crushed electrolytic aluminum waste with the raw coal of the circulating fluidized bed boiler [6], then send it to the circulating fluidized bed boiler for combustion In this study, a mixed combustion experiment ofResearch on the Coprocessing of Mixed Electrolytic Aluminum Waste