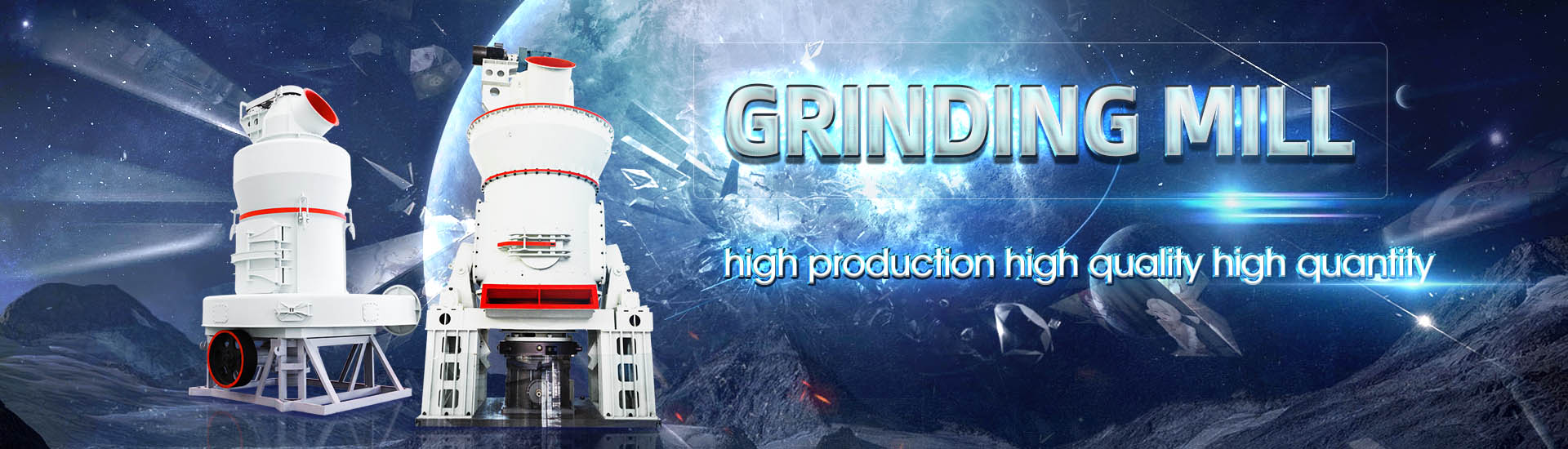
How to improve the ratio of open circuit ball mill Surface area
.jpg)
Digital Solutions to Evaluate Ball Mill Circuit Recirculating Load
Clearly recirculating load is an important consideration in overall ball mill circuit production This paper will present a digital tool and methodology to capture the tradeoff between improved throughput in close circuit overflow ball milling, considering deteriorating classificationincrease the proportion of 90mm • Check filling level of the first chamber: if mill axis in the second chamber We can then measure the material fineness evolution of nominated grain BALL MILLS Ball mill optimisation Holzinger Consulting2013年7月15日 The possibility of improving the capacity of ball mill circuits by improving classification efficiency is discussed, considering the current practical limitations of classification equipment(PDF) Energy Efficient Ball Mill Circuit – Equipment 2017年10月25日 Ball Mill Breakage Efficiency Consider a ball mill circuit processing material of a given feed size and at a given throughput rate to a target product size, the latter which once How to Improve Ball Mill Performance 911Metallurgist
.jpg)
Optimization of an industrial scale open circuit threecompartment
2016年9月10日 An industrial scale FLSmidth® threecompartment cement grinding ball mill operating in open circuit was sampled at the steady state conditions The threecompartment This paper focuses on three key areas relating to closedcircuit ball mill classification circuits: • Understanding a circuit’s maximum operating constraints for the installed equipment • DeBottlenecking the Ball mill Circuit with Hydrocyclone ControlThis paper discusses the differences between ball mill circuits closed with cyclones and with screens A methodology is described for equipment sizing and selection for a circuit closed Energy efficient ball mill circuit – equipment sizing considerationsThrough optimisation, grinding also has the potential to unlock great improvements in recovery and throughput, but how can the complex interactions between mills, classifiers, tonnage, ore Functional Performance of Ball Milling Circuits A Plant AusIMM
.jpg)
BENCHMARKING COMMINUTION CIRCUIT PERFORMANCE FOR
Bond developed three standardised characterisation tests (crushing, rod milling, and ball milling) that were compared to results from a pilot plant containing closedcircuit crushing, open circuit Next, a guide for improving CSE through manipulation of design and operating variables in the classification system will be provided Examples and case studies will illustrate the gains in A guide to maximising ball mill circuit classification system 2012年6月1日 process control in industrial ball mills remains an open problem motivating future research activities and comprehensive studies [2, 19, 26, 27, 48] We shall conclude this section by mentioning Grinding in Ball Mills: Modeling and Process ControlIt is well known in the industry that good classification system performance is vital to efficient ball mill circuit performance But what is meant by good classification system performance, and how is it achieved? Unfortunately, the perceived complexity of classification systems, and the daytoday time demands placed on the practicing metallurgist, all too often put the lowhanging fruit of A guide to maximising ball mill circuit classification system
.jpg)
Ball Mill Design/Power Calculation 911Metallurgist
2015年6月19日 The basic parameters used in ball mill design (power calculations), rod mill or any tumbling mill sizing are; material to be ground, characteristics, Bond Work Index, bulk density, specific density, desired mill The ball mill in closed circuit with hydrocyclones is an industry standard, and well known methodologies exist for equipment sizing, selection and design However, the potential to improve the capacity of ball mill circuits by replacing cyclones with screens has been recognised for many years and recently has been successfully realised, thanks to developments in fine screening Energy Efficient Ball Mill Circuit Equipment Sizing AusIMMIf a ball mill uses little or no water during grinding, it is a ‘dry’ mill If a ball mill uses water during grinding, it is a ‘wet’ mill A typical ball mill will have a drum length that is 1 or 15 times the drum diameter Ball mills with a drum length to diameter ratio greater than Ball Mill (Ball Mills Explained) saVRee saVRee2016年6月6日 A variant of this method is to direct pebblecrushing circuit product to the ballmill sump for secondary milling: while convenient, this has the disadvantage of not controlling the top size of feed to the ballmill circuit There have also been pioneer installations that have installed HPGRs as a second stage of pebble crushingSAG Mill Grinding Circuit Design 911Metallurgist
.jpg)
Addition of pebbles to a ballmill to improve grinding efficiency
2016年9月1日 This paper compares the performance of a 25/75 pebble/ball (volume ratio) composite charge to ballmilling, under conditions typical for a ballmill in SABC circuits, ie a large ball top size 2020年1月11日 Working site of ball mill grinding media refilling In addition to the grinding media proportion and frequency, other factors such as the grinding media material, the shape and so on can improve the ball mill efficiency Consult a professional engineer for details The optimized grinding media can improve the ball mill efficiency by about 30%5 Ways to Improve the Ball Mill Efficiency FTM2013年1月1日 Shortly after the first applications of closed circuit ball mill grinding it was realised that classification increases mill capacity Therefore, over the years closed ball mill – cyclone THE BENEFITS OF HIGH CLASSIFICATION EFFICIENCY IN CLOSED BALL MILL Keywords: Ball mills, grinding circuit, process control I Introduction Grinding in ball mills is an important technological process applied to reduce the size of particles which may have different nature and a wide diversity of physical, mechanical and chemical characteristics Typical examples are the various ores, minerals, limestone, etcGrinding in Ball Mills: Modeling and Process Control Sciendo
.jpg)
Autogenous and SemiAutogenous Mills ScienceDirect
2016年1月1日 If the buildup of critical sized pebbles is too great 50–90 mm slots are cut into the grate (pebble ports) to allow the scats to discharge from the mill These scats are crushed before returning to the SAG mill or passing onto a ball mill in an autogenous/ball mill/crusher (ABC) circuit (Figure 93, Figure 96)2023年8月15日 The ball mill used in Nanshan Mine is MQY2736 ball mill, the diameter (R) of the ball mill is 27 m and the length (L) is 36 m The internal liner of th e ball m ill is calculated as 01 m, then (PDF) Supplementary Relationship between Circulating 2019年10月19日 Ball mills are extensively used in the size reduction process of different ores and minerals The fill level inside a ball mill is a crucial parameter which needs to be monitored regularly for optimal operation of the ball mill In this paper, a vibration monitoringbased method is proposed and tested for estimating the fill level inside a laboratoryscale ball mill A vibration Monitoring the fill level of a ball mill using vibration sensing and 2023年2月15日 What should we do to solve those problems? 1 First of all, it is necessary to do analyses including changes of nature of the ore, whether the amount of ore, water, sand and overflow size are normal Then do the measures to deal with them 2 Reduce the amount of feed to the mill until the working state of the ball mill returns to normal; 3 Appropriately reduce the 17 Signs of Problems with Ball Mills: Quickly Remove Hidden Troubles
.jpg)
Digital Solutions to Evaluate Ball Mill Circuit Recirculating Load
range of machines, from crushers to ball mills This 75 µm material is a proxy for surface area, as typically 7080% of the surface area of grinding mill product lies below this size Size Specific Energy (SSE) is the inverse of the gradient of the curve produced when cumulativeSince balls have a greater surface area per unit weight than rods, they are better suited for fine grinding The term ball mill is restricted to those having a length to diameter ratio of 2 to 1 and less Ball mills in which the length to diameter ratio is between 3 and 5 are designated tube millsBall Mill an overview ScienceDirect Topics2016年6月6日 To a more significant degree than in other comminution devices, SAG Mill Liner Design and Configuration can have a substantial effect mill performance In general terms, lifter spacing and angle, grate open area and aperture size, and SAG Mill Liner Design 911MetallurgistFigure 2 A typical ball mill classification circuit 3 Control strategies for optimizing the hydrocyclone and closed ball milling circuit The dynamic and multivariable behavior of hydrocyclone operation requires specific operating strategies to manage the various ball mill circuit operational constraints TheDeBottlenecking the Ball mill Circuit with Hydrocyclone Control
.jpg)
HPGR 911Metallurgist
2016年7月14日 HPGR test results published by Grier (1992) on gold ores from the Mt Todd project showed significant energy savings for a HPGR/Ball Mill circuit as compared to a SAG/Ball Mill plant By adding a Polycom highpressure grinding roll, the throughput of existing plants can be increased by as much as 150% while simultaneously reducing the power consumption by Mill Type Overview Three types of mill design are common The Overflow Discharge mill is best suited for fine grinding to 75 – 106 microns; The Diaphram or Grate Discharge mill keeps coarse particles within the mill for additional grinding and typically used for grinds to 150 – 250 microns; The CenterPeriphery Discharge mill has feed reporting from both ends and the product AMIT 135: Lesson 7 Ball Mills Circuits – Mining Mill Operator How to determine whether the ratio of loaded ball is reasonable? Ball mill is one of the commonly used equipment in mineral processing equipment For ball mill, reasonable ball loading not only affects the improvement of grinding efficiency How to choose the ball loading and loading ratio of 2017年10月26日 The following are factors that have been investigated and applied in conventional ball milling in order to maximize grinding efficiency: a) Mill Geometry and Speed – Bond (1954) observed grinding efficiency to be a Factors Affecting Ball Mill Grinding Efficiency
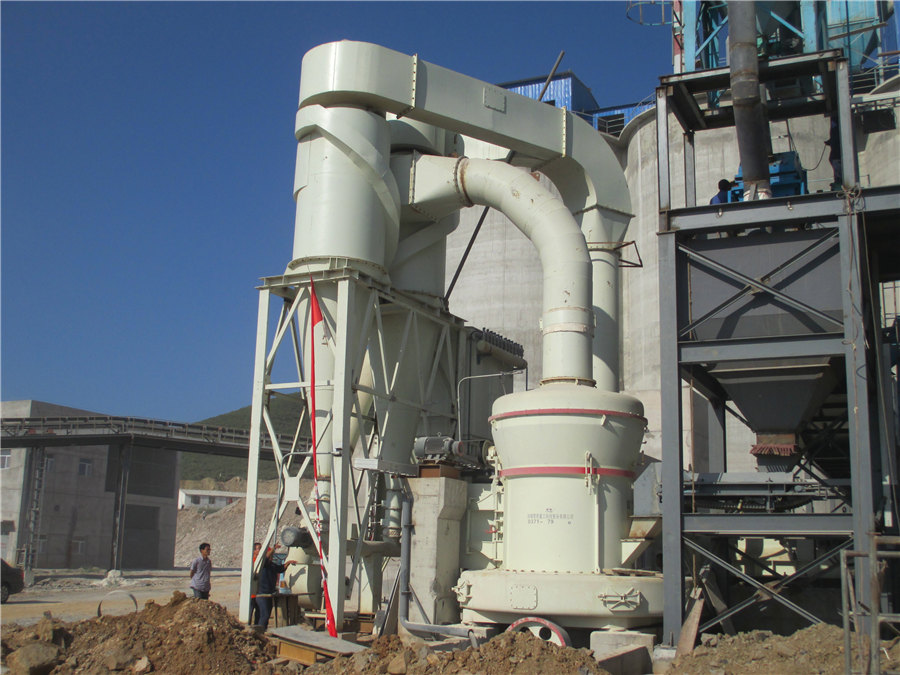
Top 10 tips to improve the grinding efficiency of ball
2020年3月21日 Ball mill’s low grinding efficiency, low processing capacity, high production energy consumption, unstable product fineness, etc are problems that many customers will encounter How to effectively improve the grinding 2015年10月9日 Calculating a grinding circuit’s circulating loads based on Screen Analysis of its slurries Compared to %Solids or Density based Circulating load equations, a more precise method of determining grinding circuit tonnages uses the screen size distributions of the pulps instead of the dilution ratiosPulp samples collected around the ball mill or rod mill and Ball Mill Circulating Load Formula 911MetallurgistBall mill mill internals o Ball mill (L/D, speed, drives reducers, etc) o Ventilation o Liners o Diaphragms o Media composition fill ratio Ball mill typically accounts for 85% of the total energy consumed in the grinding plant should be the focus of improvementsImprovements in New Existing Cement Grinding Mills by Tim 2020年7月1日 The conjecture is that by altering the profile of material transport through a ball mill, it may be possible to improve its efficiency The scope of the work is limited to the residence time distribution of the ball mill descriptive of material transport This is because flow regime and slurry rheology also affect millingAn attainable region perspective on the role of residence time
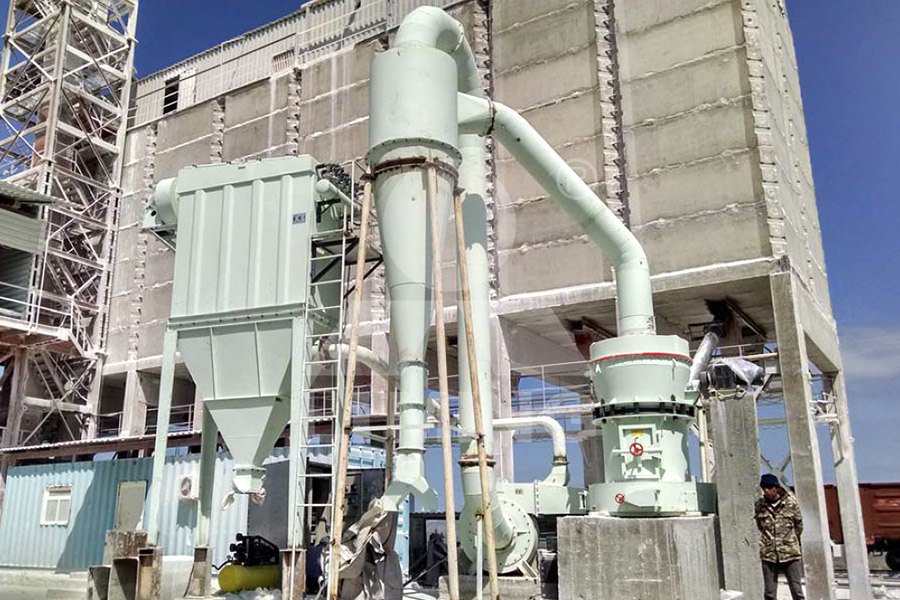
OPTIMIZATION OF CEMENT GRINDING OPERATION IN BALL MILLS
capital expenditure with a high benefit to cost ratio Optimization is especially important when multiple products are being produced Operation and Elements of a ClosedCircuit Ball Mill System Cement ball mills typically have two grinding chambers The first chamber is filled with larger diameter grinding media andlined with lifting liners 2017年9月17日 “Coarse” versus “fine” or product particle cutoff size is first selected, usually equal to some benchmark passing size of the circuit product (eg, 80%) The function of the grinding circuit is to generate new product size material (or “fines”) from “coarse” particles in the circuit feed as efficiently as possibleHow to Improve Ball Mill Grinding 911Metallurgist2017年2月13日 The apparent difference in capacities between grinding mills (listed as being the same size) is due to the fact that there is no uniform method of designating the size of a mill, for example: a 5′ x 5′ Ball Mill has a working diameter of 5′ inside the liners and has 20 per cent more capacity than all other ball mills designated as 5′ x 5′ where the shell is 5′ inside diameter and Ball Mills 911Metallurgist2021年6月29日 Nowadays, ball mills are widely used in cement plants to grind clinker and gypsum to produce cement The research focuses on the mill speed as well as air classifier speed effect on the two Effects of Mill Speed and Air Classifier Speed on Performance of
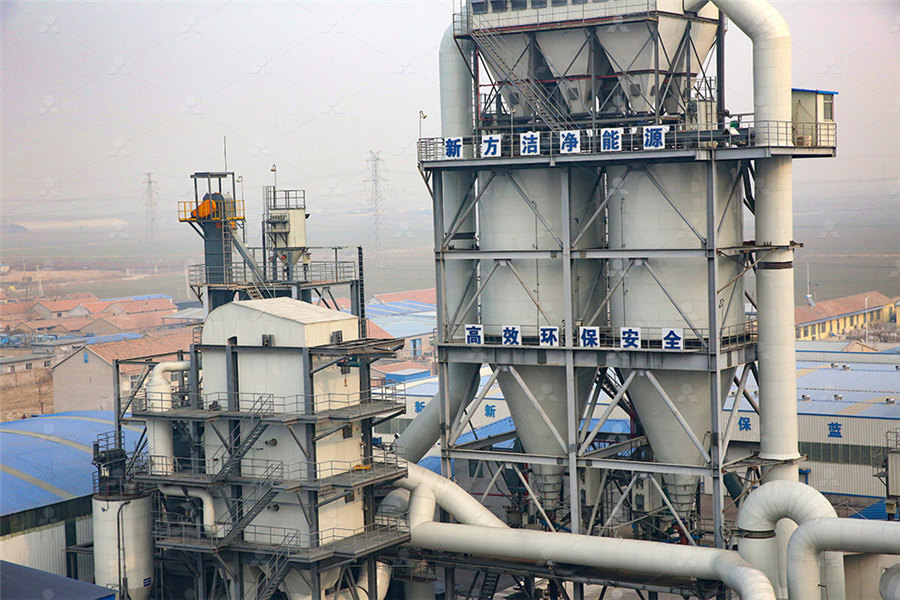
Grinding in Ball Mills: Modeling and Process Control
2012年6月1日 process control in industrial ball mills remains an open problem motivating future research activities and comprehensive studies [2, 19, 26, 27, 48] We shall conclude this section by mentioning It is well known in the industry that good classification system performance is vital to efficient ball mill circuit performance But what is meant by good classification system performance, and how is it achieved? Unfortunately, the perceived complexity of classification systems, and the daytoday time demands placed on the practicing metallurgist, all too often put the lowhanging fruit of A guide to maximising ball mill circuit classification system 2015年6月19日 The basic parameters used in ball mill design (power calculations), rod mill or any tumbling mill sizing are; material to be ground, characteristics, Bond Work Index, bulk density, specific density, desired mill Ball Mill Design/Power Calculation 911MetallurgistThe ball mill in closed circuit with hydrocyclones is an industry standard, and well known methodologies exist for equipment sizing, selection and design However, the potential to improve the capacity of ball mill circuits by replacing cyclones with screens has been recognised for many years and recently has been successfully realised, thanks to developments in fine screening Energy Efficient Ball Mill Circuit Equipment Sizing AusIMM
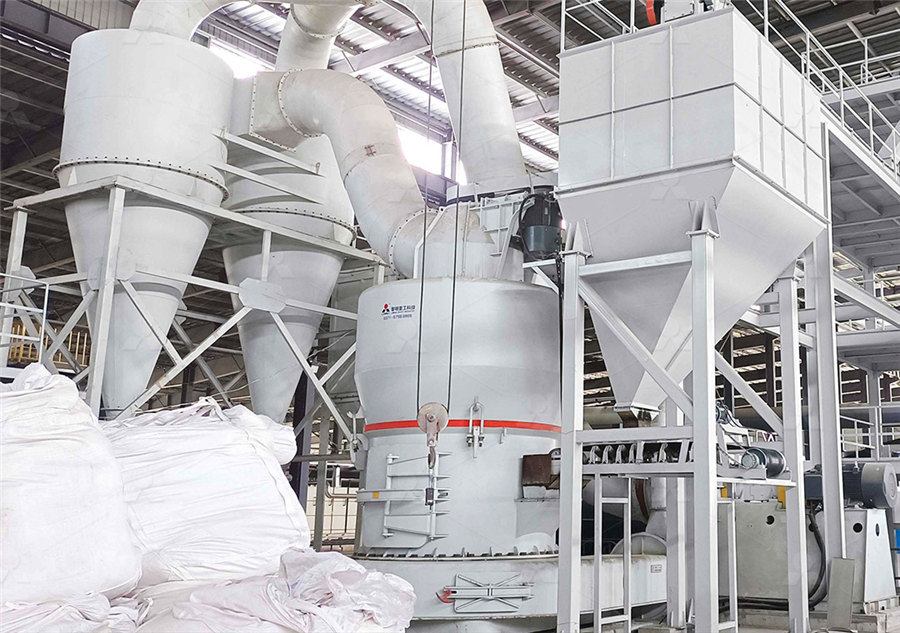
Ball Mill (Ball Mills Explained) saVRee saVRee
If a ball mill uses little or no water during grinding, it is a ‘dry’ mill If a ball mill uses water during grinding, it is a ‘wet’ mill A typical ball mill will have a drum length that is 1 or 15 times the drum diameter Ball mills with a drum length to diameter ratio greater than 2016年6月6日 A variant of this method is to direct pebblecrushing circuit product to the ballmill sump for secondary milling: while convenient, this has the disadvantage of not controlling the top size of feed to the ballmill circuit There have also been pioneer installations that have installed HPGRs as a second stage of pebble crushingSAG Mill Grinding Circuit Design 911Metallurgist2016年9月1日 This paper compares the performance of a 25/75 pebble/ball (volume ratio) composite charge to ballmilling, under conditions typical for a ballmill in SABC circuits, ie a large ball top size Addition of pebbles to a ballmill to improve grinding efficiency2020年1月11日 Working site of ball mill grinding media refilling In addition to the grinding media proportion and frequency, other factors such as the grinding media material, the shape and so on can improve the ball mill efficiency Consult a professional engineer for details The optimized grinding media can improve the ball mill efficiency by about 30%5 Ways to Improve the Ball Mill Efficiency FTM
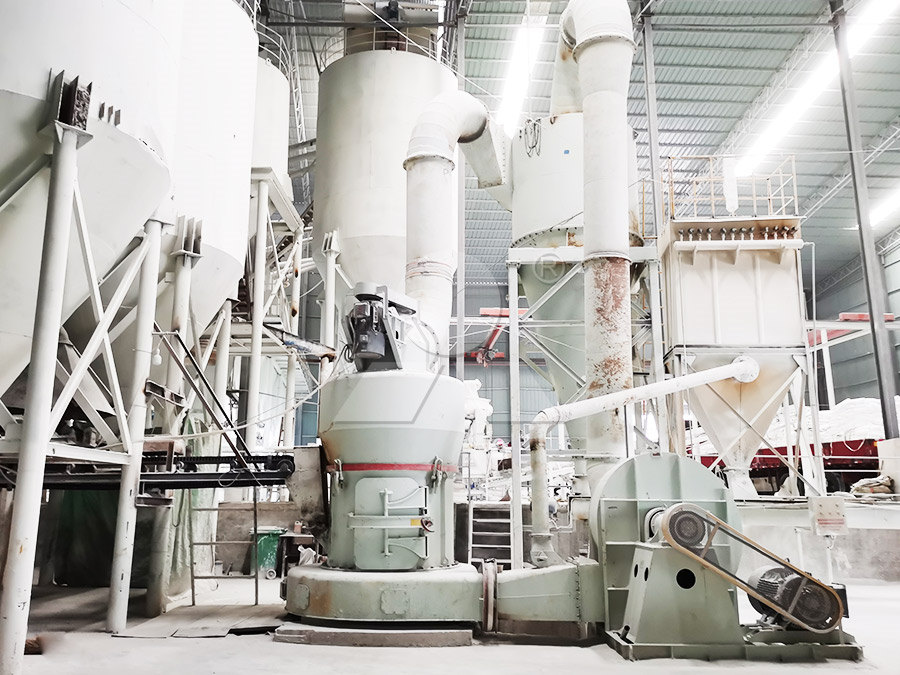
THE BENEFITS OF HIGH CLASSIFICATION EFFICIENCY IN CLOSED BALL MILL
2013年1月1日 Shortly after the first applications of closed circuit ball mill grinding it was realised that classification increases mill capacity Therefore, over the years closed ball mill – cyclone Keywords: Ball mills, grinding circuit, process control I Introduction Grinding in ball mills is an important technological process applied to reduce the size of particles which may have different nature and a wide diversity of physical, mechanical and chemical characteristics Typical examples are the various ores, minerals, limestone, etcGrinding in Ball Mills: Modeling and Process Control Sciendo