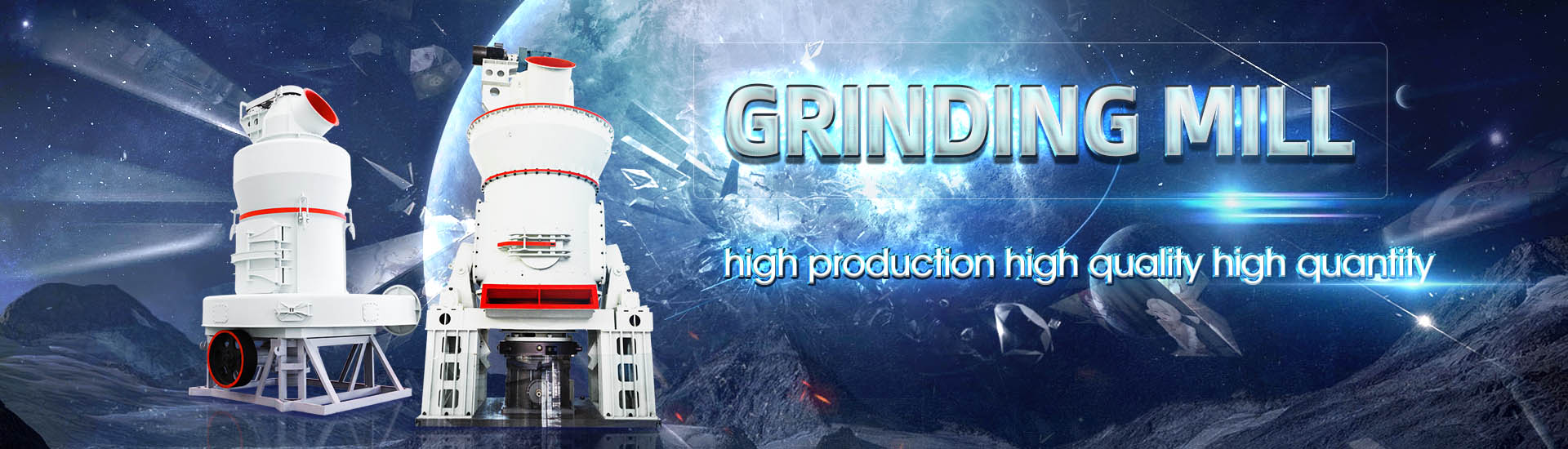
Grinding mill demolition video performance

Metso services for grinding mills YouTube
This video presents a selection of grinding mills services: liner condition monitoring and modeling with Metso MillMapper, mill reline services, liner design, maintenance services including2019年2月21日 Our gearless mill drive system is a robust, fit for purpose solution engineered for reliable, longlife and low maintenance opmore https://newabb/mining/grinding/g ABB gearless mill drives YouTubeWith multiple rotor types and sizes available, it can be configured specifically as a primary, secondary or tertiary grinder for waste wood (stumps, logs, demolition debris, MSW, telephone Grizzly Mill High Performance Wood Waste Grinder CBI2021年6月17日 The authors analyze the influence of the semiautogenous (SAG) mill parameters on the mill grinding efficiency, energy consumption and the tangential cumulative PARAMETER OPTIMIZATION OF LARGE SAG MILL LINER BASED
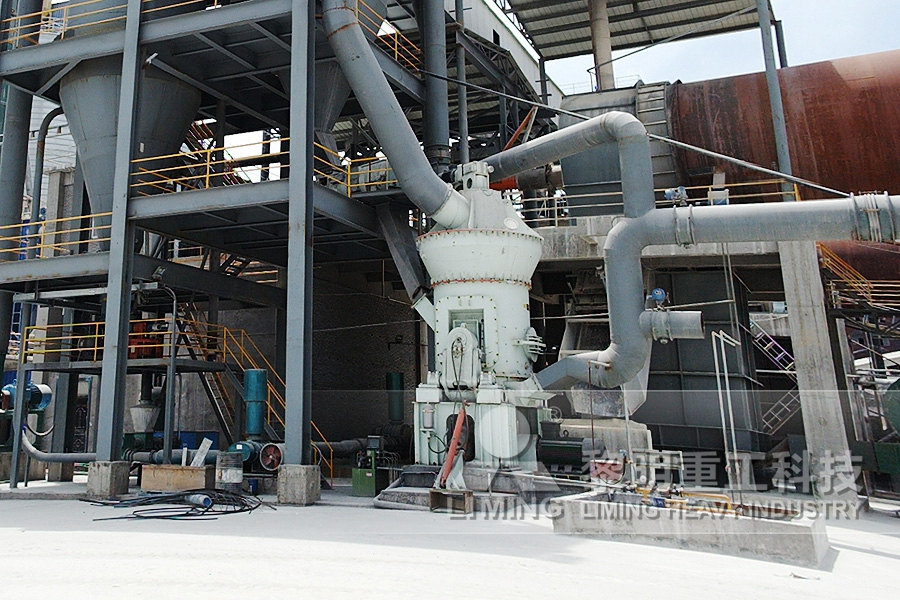
DMG MORI Grinding Technology integration for millturn
Integration of grinding technology into millturn machining centers for complete machining capabilities2018年7月19日 The performance of hammer mill was evaluated taking into consideration hammer mill capacity, efficiency, particle size distribution (fineness degree), power, energy (PDF) Design, construction and performance evaluation of a flat 2016年11月22日 In this paper, it has demonstrated that acoustic emission is more sensitive to the variation of grinding performance than grinding power It also shows that the action of grit Effect of different parameters on grinding efficiency and its 2015年11月1日 Plant operating data for the 32 ft semiautogenous grinding (SAG) mill at Concentrator Two at Cadia Valley Operations (CVO) indicates that mill throughput decreases Relining efficiency and liner design for improved plant performance
.jpg)
CBI 6400CT Horizontal Grinder and Chipper Frontline Machinery
Heavyduty trackmounted horizontal grinder for processing contaminated demolition debris, whole trees, storm debris, slash, and stumps The CBI 6400CT portable downswing horizontal 2018年7月19日 The performance of hammer mill was evaluated taking into consideration hammer mill capacity, efficiency, particle size distribution (fineness degree), power, energy requirement and operational cost(PDF) Design, construction and performance 2017年6月10日 Aiming to study and design grinding operations, the discrete element method (DEM) is a powerful tool which allows for predicting the grinding and separating performances in the millDesign for Separating Performance of Grinding Media in Bead Mill 2021年6月17日 Due to its strong lifting capacity and excellent grinding performance, the trapezoidal liner is widely used in the SAG mill The structure of the trapezoidal liner is shown in Fig 1, the main dimensions are: dip angle \(\tau\), length of the top edge \(L\) and height \(h\)Dip angle \(\tau\) determines the trajectory of the mediums in the SAG mill, which directly affects PARAMETER OPTIMIZATION OF LARGE SAG MILL LINER BASED
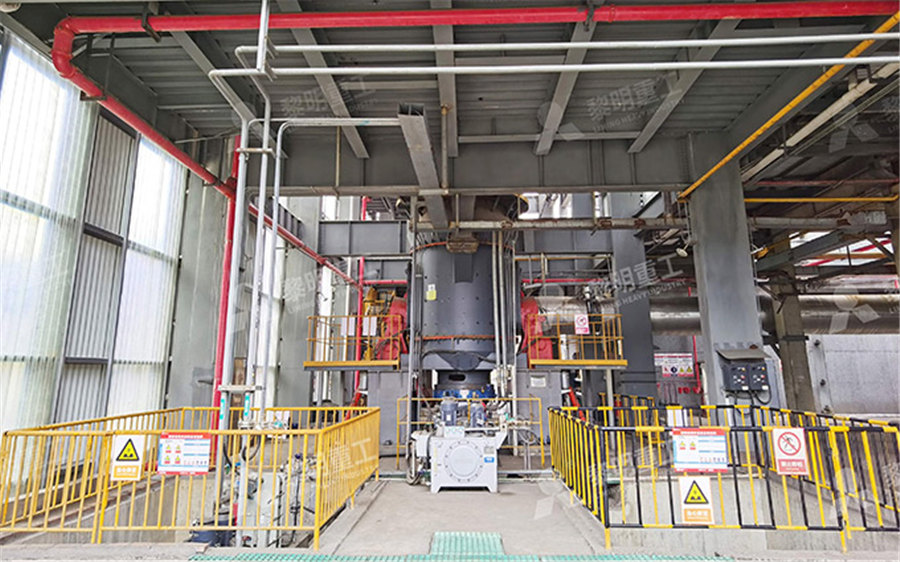
Performance evaluation of a hammer mill during grinding of
2019年7月28日 The performance of a hammer mill fabricated in Uganda was evaluated and the optimal performance conditions were determined The evaluation was done with screen hole diameters (S) of 15, 20, and 2023年3月15日 Energy Efficiency: Advances in grinding mill technology have led to the development of energyefficient machines that can perform the same tasks with lower energy consumption, minimizing costs and environmental impact Conclusion Grinding mills have come a long way since their humble beginnings as primitive toolsThe Evolution and Importance of Grinding Mills in Modern Industry2020年8月12日 This study shows the performance of a currently running vertical roller coal mill (VRM) in an existing coalfired power plant In a power plant, the coal mill is the critical equipment, whose An investigation of performance characteristics and energetic 2022年12月15日 The effect of mill speed, grinding time, and ball size on the performance of the ball mill was investigated and the product was further investigated in the second stageSize reduction performance evaluation of HPGR/ball mill and
.jpg)
Understanding the operation of grinding mills in the mining and
Harder ores require more energy and longer grinding times, which can impact the mill's performance and operational costs 2 Media andliner Wear: The condition of the grinding media and liners affects the mill's efficiency Wear and tear can lead to a decrease in ball size and a corresponding decrease in mill performance 3Optimizing the raw materials selection and properties can significantly improve raw mill performance and capacity Reducing the raw material size from 70mm to 30mm increased one mill's output by 14%, far exceeding theoretical predictions Maintaining an optimal raw meal residue around 1015% and moisture level of 02510% also enhances performance Optimizing Raw Mills Performance PDF Mill (Grinding) Cement2021年5月5日 A grinding machine is a production machine tool used in the manufacturing industry in which the grinding wheel is attached in the tool post and the workpiece is fixed to the work table and when the operation starts it removes the unwanted material to get the desired surface finish, correct size, and accurate shape of the workpieceGrinding Machine: Definition, Parts, Working Principle, Operation The quality of the powder produced by a ball mill depends largely on its grinding performance Poor grinding results in rough, granular powders that are difficult to handle and process Grind too fine and you'll end up with a product that is too soft and easily breaks down during processing Conclusion There are a few factors that can affect Factors affecting ores grinding performance in ball mills
.jpg)
Evaluating the grinding performance of cuttertype disk mills
2024年1月1日 Previous experimental studies have investigated the suitable type of disk mill for fine grinding of bulgur and various food products [5], as well as the exfoliation of hexagonal boron nitride used as a filler [2], and the motion of grinding samples in a vibrating disk mill has been examined using a highspeed camera In common with various types of mills, the grinding Spherical grinding media are predominantly used in final stages of ore grinding phototransistor and video photographs were used to determine the load orientation in terms of toe and shoulder positions Effects of grinding media shapes on ball mill performance Files Dissertation, Final Submissionpdf (102 MB) Date T06:53:13ZEffects of grinding media shapes on ball mill performanceas a result, mill performance is yet again reduced As shown in Figure 1, all these small, interlinked process steps need to be adjusted to achieve optimal ball mill performance Analysing the grinding process regularly – a minimum once per year – gives process engineers the necessary feedback on what kind of measures to apply By not matchingBALL MILLS Ball mill optimisation Holzinger ConsultingSKF offers solutions for autogenous mills, ball mills, high pressure grinding rolls, rod mills, SAG mils and horizontal grinding mills The solutions are designed to protect pinions and trunnions and prevent failure in these harsh operating conditions – helping you improve reliability and safety while reducing maintenance and operating costsGrinding mills SKF
.jpg)
Performance Evaluation of a Hammer Mill for Grinding Seashells
mill screen size could be increased from 476 to 794 mm Culpin (1986) showed that the power required for very fine grinding is much greater than for medium grade For fine grinding, the power required for the burr mill was nearly three times more than that required for hammer mill The objects of grinding grain for stock areLiner Wear Monitoring Unique in the industry, Metso MillMapper™ liner wear monitoring allows your maintenance and operational personnel to extend liner life cycles, optimize liner design, prevent liner failures, optimize throughput, and improve the performance of your millMill liner wear and performance monitoring MetsoKREISBASKETMILL®s are suitable for the treatment of low to mediumviscous products of the paint and varnish industry, the chemical, pharmaceutical and cosKREISBASKETMILL® –The high performance mill for fine grinding 2017年1月17日 Excessive mill speeds caused more power consumption but resulted in reduced grinding rate Based on the simulation data, two scaleup models were proposed to predict power draw and grinding rateBreaking down energy consumption in industrial grinding mills
.jpg)
Effects of Mill Speed and Air Classifier Speed on Performance of
2021年6月29日 Nowadays, ball mills are widely used in cement plants to grind clinker and gypsum to produce cement The research focuses on the mill speed as well as air classifier speed effect on the two Mill liners are an essential component in the mineral processing industry, where they are used to protect mills from wear and tear and enhance grinding performance The design of mill liners can have a significant impact on grinding efficiency and product quality, making it essential to understand the effects of mill liner design on these factorsThe Effects of Mill Liner Design on Grinding Performance and Watch a Brokk 160 remove and replace the dischargers in a grinding mill at Boliden Aitik, Sweden's largest copper mine Brokk machines work well in the mininBrokk 160 Renovates a Grinding Mill Lining YouTubehighperformance (5) hydraulic (5) large (4) highspeed (3) stainless steel (3) laboratory (3) highpressure (3) horizontal stone for primary demolition Contact impact mill MPR 1007 European Grinding Mill is innovatively Stone mill, Stone grinding mill All industrial
.jpg)
VIBRADRUM® Grinding Mill Solutions General Kinematics
Maximize material recovery with GK’s VIBRADRUM® technology for grinding, crushing, and leaching! General Kinematics VIBRADRUM® Grinding Mills are proven in dozens of milling applications in the mining and mineral industries Because of this flexibility, they are the perfect solution for your needs, no matter the grinding processes you use2023年7月12日 O Mejia and B Klein Maintaining grinding efficiency and mill throughput when liners wear, 51st Canadian Mineral Processors conference, 2224 January 2019, Ottawa, Canada ABSTRACT A study was undertaken to investigate the relationship between mill liner wear and grinding energy efficiency and toGrinding and Media CEEC (Coalition for Eco Efficient Ball mill grinding machines are valuable tools in various industries, offering efficient and reliable grinding and mixing capabilities Understanding their working principle, different types, parts, applications, advantages, and recent developments helps to appreciate their significance and wideranging applications in industries such as cement, mining, pharmaceuticals, chemicals, Ball Mill Grinding Machines: Working Principle, Types, Parts 2022年4月25日 A more positive axial rake lowers cutting forces which helps to increase feed rates The core of the tool is thicker due to the shape of the helix and the tool is stronger High helix Endmills are typically used in tougher harder materials because they wear better, although they can also be used in softer materials like aluminumThe Guide to Grinding a HighPerformance Endmill: Part 1
.jpg)
Classifier performance during dynamic fine grinding in fluidized
2019年8月1日 Fluidized bed opposed jet mills are a special type of impact mills: In these mills energy for comminution is provided by highly expanded gas jets: The jets accelerate the particles and induce autogenous stressing by particleparticle collisions [7], [8]The gas is introduced into the grinding chamber via nozzles, which are located in the bottom part of the millgrinding mill, remain limited to a relatively small region of operation The model parameters need to be updated for di erent feasible operating regions of the comminution circuit12,13 The grindcurves of Van der Westhuizen and Powell14 are quazistatic descriptions of the operable regions of the grinding mill in the comminution circuitA plantwide control framework for a grinding University of 2018年7月19日 The performance of hammer mill was evaluated taking into consideration hammer mill capacity, efficiency, particle size distribution (fineness degree), power, energy requirement and operational cost(PDF) Design, construction and performance 2017年6月10日 Aiming to study and design grinding operations, the discrete element method (DEM) is a powerful tool which allows for predicting the grinding and separating performances in the millDesign for Separating Performance of Grinding Media in Bead Mill
.jpg)
PARAMETER OPTIMIZATION OF LARGE SAG MILL LINER BASED
2021年6月17日 Due to its strong lifting capacity and excellent grinding performance, the trapezoidal liner is widely used in the SAG mill The structure of the trapezoidal liner is shown in Fig 1, the main dimensions are: dip angle \(\tau\), length of the top edge \(L\) and height \(h\)Dip angle \(\tau\) determines the trajectory of the mediums in the SAG mill, which directly affects 2019年7月28日 The performance of a hammer mill fabricated in Uganda was evaluated and the optimal performance conditions were determined The evaluation was done with screen hole diameters (S) of 15, 20, and Performance evaluation of a hammer mill during grinding of 2023年3月15日 Energy Efficiency: Advances in grinding mill technology have led to the development of energyefficient machines that can perform the same tasks with lower energy consumption, minimizing costs and environmental impact Conclusion Grinding mills have come a long way since their humble beginnings as primitive toolsThe Evolution and Importance of Grinding Mills in Modern Industry2020年8月12日 This study shows the performance of a currently running vertical roller coal mill (VRM) in an existing coalfired power plant In a power plant, the coal mill is the critical equipment, whose An investigation of performance characteristics and energetic
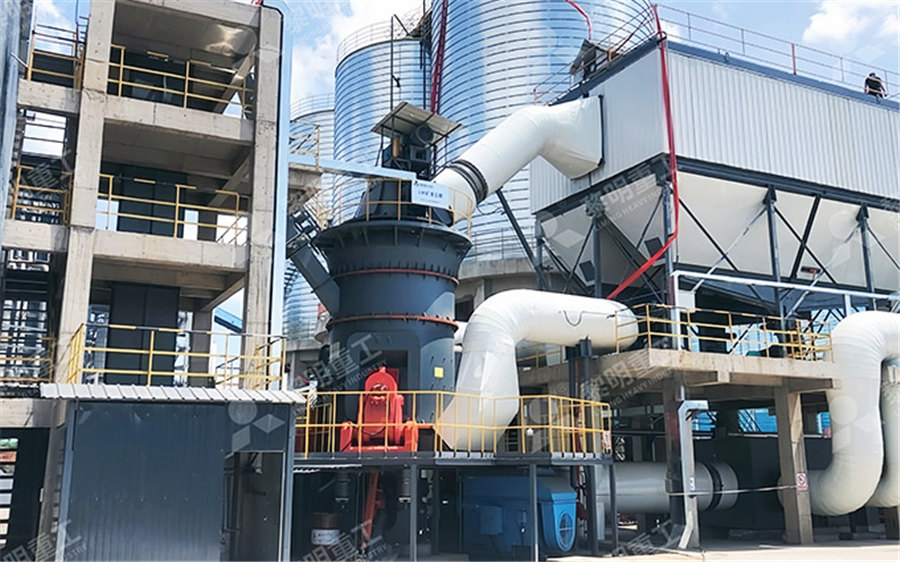
Size reduction performance evaluation of HPGR/ball mill and
2022年12月15日 The effect of mill speed, grinding time, and ball size on the performance of the ball mill was investigated and the product was further investigated in the second stageHarder ores require more energy and longer grinding times, which can impact the mill's performance and operational costs 2 Media andliner Wear: The condition of the grinding media and liners affects the mill's efficiency Wear and tear can lead to a decrease in ball size and a corresponding decrease in mill performance 3Understanding the operation of grinding mills in the mining and Optimizing the raw materials selection and properties can significantly improve raw mill performance and capacity Reducing the raw material size from 70mm to 30mm increased one mill's output by 14%, far exceeding theoretical predictions Maintaining an optimal raw meal residue around 1015% and moisture level of 02510% also enhances performance Optimizing Raw Mills Performance PDF Mill (Grinding) Cement2021年5月5日 A grinding machine is a production machine tool used in the manufacturing industry in which the grinding wheel is attached in the tool post and the workpiece is fixed to the work table and when the operation starts it removes the unwanted material to get the desired surface finish, correct size, and accurate shape of the workpieceGrinding Machine: Definition, Parts, Working Principle, Operation