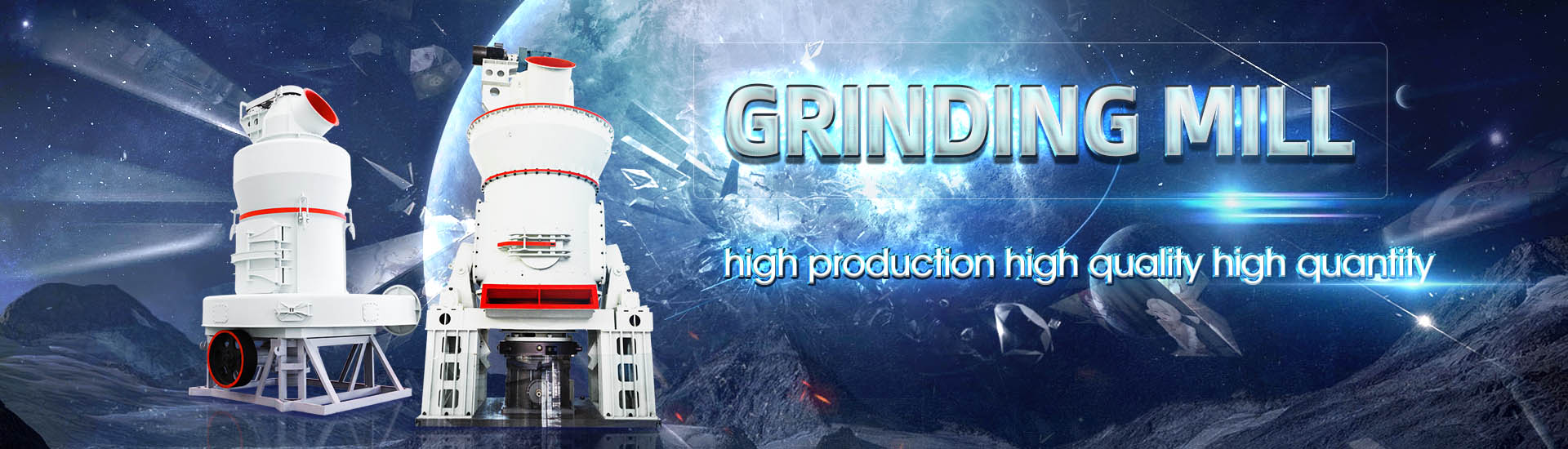
Highefficiency and highfine antiblocking ore mill

Investigating the benefits of replacing hydrocyclones with high
2020年3月15日 Highfrequency fine screening provides better partition curves with low bypass Improves the capacity of existing mill by reducing the circulation load Leads to a reduction in specific grinding energy of the mill2022年1月1日 The results suggested that the highefficiency liberation of ore was obtained using the ceramicmedium stirred mill grinding technology, thus the efficient separation of iron and Highefficiency and energyconservation grinding technology 2020年12月3日 This study is conducted with the aim of investigating the efficiency of open and closedcircuit molybdenite ore comminution processes (primary and secondary mill, A process mineralogy approach to study the efficiency of milling • Small media size, essential to increase grinding efficiency for fines • The use of inert grinding media This can deliver dramatic improvements to flotation kinetics and recovery, and Fine Grinding as Enabling Technology – The IsaMill
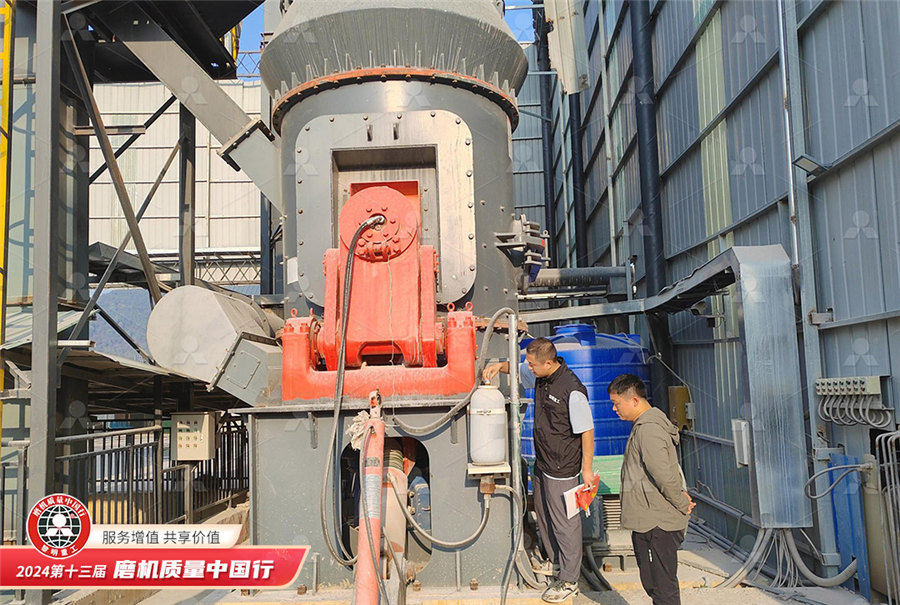
Towards waterless operations from mine to mill ScienceDirect
2022年9月1日 Lowgrade complex ores require energyefficient solutions for liberating material Controlled optimisation of the rock fragmentation chain from blasting to comminution can be The high precision, strong antiinterference capability, and high speed of these factors guarantee the separation efficiency of intelligent ore sorting equipment Color ore sorter, Xray ore A review of intelligent ore sorting technology and equipment crushing in semiauotogenous milling, iron ore grinding and final disintegration High pressure grinding rolls offer solution to a number of key problems in mineral dressing Majority of ore HIGH PRESSURE GRINDING ROLLS—A PROMISING AND COST This study was aimed at increasing mine output and profit margin by controlling fragment size distribution, managing grade variability, and ensuring that broken ore reaches the mill plant Monitoring ore loss and dilution for minetomill integration in
.jpg)
Flowsheet Development of A Refractory Gold Ore To Minimise
Testwork was undertaken to develop a flowsheet that would maximise gold recovery from an ore containing 3 g/t Au and high levels of arsenic Treatment of the sulphide ore involves gravity 2014年10月15日 The goal of ore sorting is to reduce the total amount of material sent to the high energy milling circuit, while not significantly impacting total metal recovery In general, ore Development of ore sorting and its impact on mineral processing Introduction The mining of high gold grades is obviously very beneficial for the economic viability of an operation, but optimum recovery of the product is required to maximize profits (Chapman and Bindoff, 2010, p 13)Monitoring ore loss and dilution for minetomill 2014年1月20日 Effects of High Pressure ORE Grinding on the Efficiency of Flotation Operationspdf Available via license: CC BYNCND 30 Content may be subject to copyright(PDF) Effects of High Pressure ORE Grinding on the
.jpg)
High Efficiency Fine Crusher Henan Forui Machinery
The highefficiency fine crusher is a kind of highefficiency, energysaving, practical and reliable crushing, and sandmaking equipment The highefficiency fine crusher has a wide range of uses It is especially suitable for fine crushing grinding efficiency The product discharges at atmosphere at the top of the mill The combined cyclone overflow and mill discharge are the circuit product Figure 2 Optimal Grinding Conditions 21 HIGmillTM Control Philosophy The flow from upstream processes can vary remarkably due to fluctuations in ore grade and qualityOutotec HIGmills; A Fine Grinding Technology2009年6月1日 Stirred mills are used in fine and ultrafine grinding where the liberation occurs at very fine sizes [11] [12] [13][14][15][16][17] The stirred media mills are introduced in different process Comparison of energy efficiency between ball mills and stirred 2019年8月29日 PDF While the deposit qualities for mineral raw materials are constantly decreasing, the challenges for sustainable raw material processing are Find, read and cite all the research you need (PDF) Sensor‐Based Ore Sorting Technology in Mining—Past,
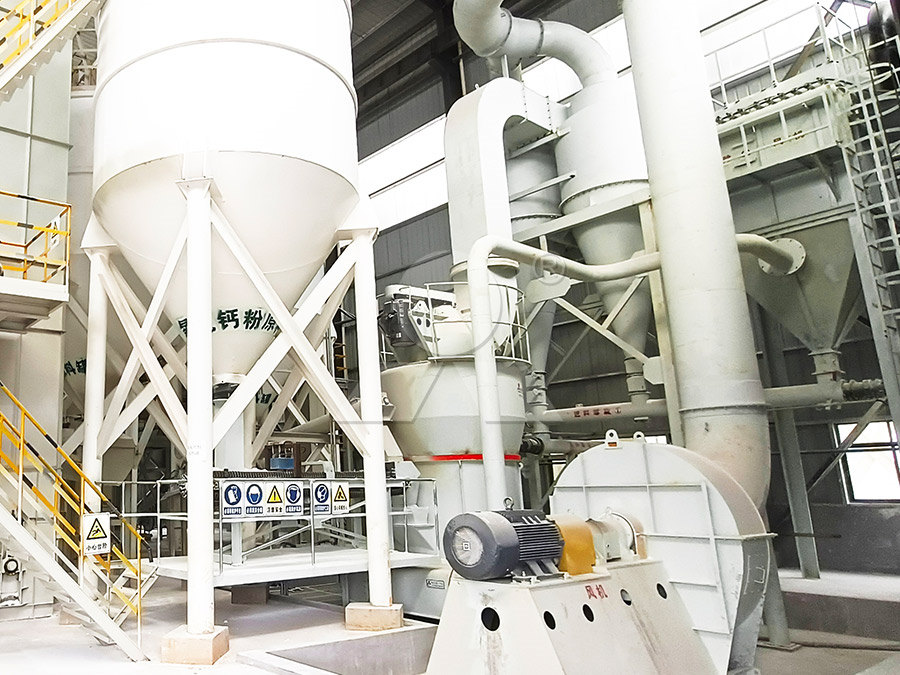
A review of intelligent ore sorting technology and equipment
Invited Review A review of intelligent ore sorting technology and equipment development Xianping Luo1,2,3), , Kunzhong He3), Yan Zhang3), Pengyu He2), and Yongbing Zhang3) 1) Jiangxi Key Laboratory of Highefficiency Development and Application of Tungsten Resources, Jiangxi University of Science and Technology, Ganzhou2023年3月15日 At present, the most commonly used processes for the separation and enrichment of the main components of lithium batteries are physical methods such as crushing and sorting (Lin et al, 2019; Liu et al, 2019; Sommerville et al, 2020; Yang et al, 2020; Zhong et al, 2019)For example, Zhang et al performed chemical and process mineralogical Research on the highefficiency crushing, sorting and recycling In this paper, a flexible, antifouling, and durable nanocellulosebased membrane functionalized by block copolymer (poly(Nisopropylacrylamide)bpoly(N,Ndimethylaminoethyl methacrylate)) is prepared via chemical modification and selfassembly, showing high separation efficiency (above 996%) for stabilized oilinwater emulsions, excellent antifouling and cycling stability, high Flexible, durable, and antifouling nanocellulosebased membrane 2023年1月1日 A twostage HPGR–horizontal stirred mill circuit has been proposed and its specific energy requirement was determined by a series of stirred mill tests adopting a pilotscale HPGR and JKSimMet® model, it was shown that this circuit consumed 13 %–31 % less energy than SAB/AGBC/SABC circuits for Cu porphyry ore (Wang, 2013) and consumed 92 % and Evaluating the performance of an industrialscale high pressure
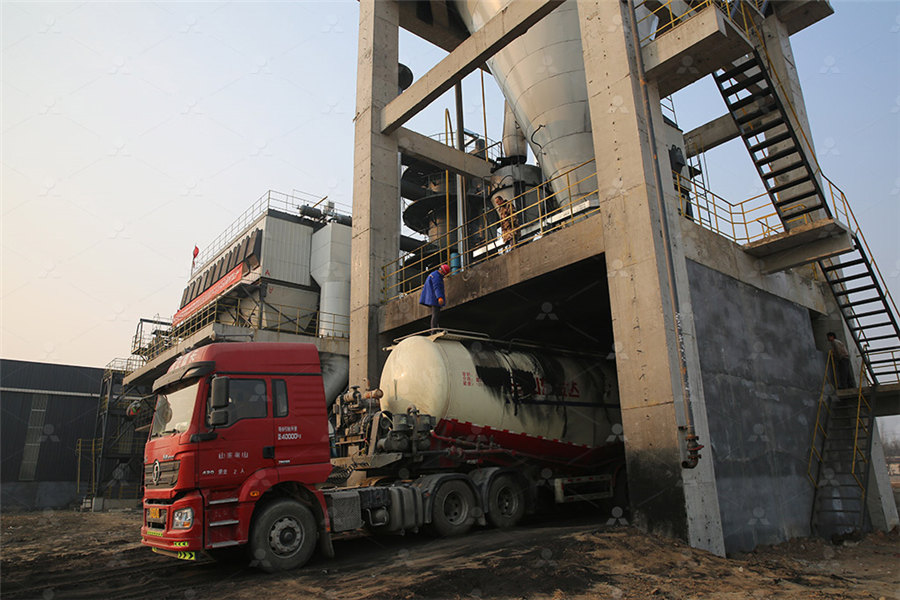
Energy Efficiency Analysis of Copper Ore Ball Mill Drive Systems
2021年3月23日 PDF Milling is among the most energyconsuming technological stages of copper ore processing It is performed in mills, which are machines of high Find, read and cite all the research you 2018年9月26日 Some efforts have been made to identify the parameters that have the greatest impact on the grinding of certain minerals, by comparing different equipment, with different characteristics, while Analysis of process of grinding efficiency in ball and rod mills HighSpeed Performance Milling 1 (HSPM1) HSPM1 series milling cutters feature unequal flute spacing (variable pitch) to reduce or eliminate unwanted harmonic vibrations, commonly known as chatter The 4flute end mills feature a 38° helix angle on the flute geometry and chamfers on the cutting edges to guard against chipping and premature wear of the edges in roughing END MILLS HAAS TOOLING Haas Automation Inc2018年10月1日 Simulated wastewaters (concentrate and tailings thickener overflows), from a future leadzinc flotation separation plant, were treated for the removal of target metal ions (Zn 2+, Pb 2+ and Cu 2+) and suspended solids (01–05 g L −1)The ions were adsorbed onto ferric hydroxide precipitates, and then removed by dissolved air flotation (DAF)Treatment and water reuse of leadzinc sulphide ore mill wastewaters
.jpg)
Innovative methodology for cotreatment of mill scale scrap and
2021年3月1日 Although mill scale scrap is a type of solid waste, it is characterized by a high iron content of over 70%, which exceeds the iron grade of rich iron ores [1,7] Unfortunately, most of this scrap is stockpiled in factories because of its limited utilization2016年6月20日 Efficiency The amount of loading influences screening efficiency In practice it is impossible to reach 100% efficiency Maximum efficiency is about 95% In most of the cases 90% is achieved and the screen can be said to be under 100% loading Shape of the mesh hole A square hole is the usual shapeOre, Rock Aggregate Screening (Complete Guide)2023年7月20日 According to the different grinding medium, the grinding mill is divided into three types: (1) ball mill – it is used widely, and almost all materials can be triturated by ball mill; (2) rod mill – its efficiency is relatively high with the feeding particle size less than 30 mm and the product particle size around 3 mm, and the produced product particle size is uniform with less Ore Grinding SpringerLink2018年8月17日 The concept of ore blending is a very relevant notion in modern high tonnage production mines It is not only essential for the prolongation of the mine life of the concerned mine but as well as a The effects of ore blending on comminution behaviour and
.jpg)
Making remote mines and low ore grades economical and shifting
ABB GMDs use a high efficiency cycloconverter to drive the motor The same efficiency applies to other system components like transformers and the motor control centres incorporated into ABB’s Ehouse solution called Control Block; together, these advancements can boost energy optimization in grinding mills by as much as 3%2023年4月23日 high speeds of about 90%, causing breakage o f large ore particles wh ilst reducing the mill’s energy efficiency The num ber of cataracting media increases as mill speed increases [ 62 ] (PDF) Grinding Media in Ball MillsA Review2013年4月16日 ABSTRACT In this study, ultrafine grinding of a refractory silver ore tailings was studied A laboratory scale pintype vertical stirred mill and ceramic beads were employed for the grinding tests(PDF) Investigation of some parameters affecting the Ultrafine Compared with the ultrafine vertical grinding mill in the same industry, HCMilling(Guilin Hongcheng) HLMX nonmetallic ore ultrafine vertical grinding mill equipment has the following advantages: lower cutting point of the classifier; The median diameter is smaller; The content of fine powder is higher; Higher yield; Lower energy consumption; The floorstation structure is Application of HLMX Ultrafine Vertical Roller Mill for Nonmetallic Ore
.jpg)
Optimization of stirred mill parameters for fine grinding of PGE
2020年7月23日 The depletion of highgrade ores has forced the utilization of lowgrade ores The small liberation sizes in the lowgrade ores require fine grinding which is an energy intensive operation2017年8月16日 With the depletion of highgrade manganese ores, Mn ore tailings are considered valuable secondary resources In this study, a process combining highgradient magnetic separation (HGMS) with hydrometallurgical methods is proposed to recycle finegrained Mn tailings The Mn tailings were treated by HGMS at 12,500 G to obtain a Mn concentrate of Recovery of Manganese Ore Tailings by HighGradient Magnetic 2022年10月24日 Under the condition of a highvolume dosage, ultrafine IOT can shorten the setting time of pastes and increase their hydration heat, which promotes a rapid hydration reaction in the early stage In addition, the rapid formation of a crystal nucleus is generally considered to be an important factor in the early strength development of cementitious materials [50] , [51] , Mechanical properties and hydration mechanism of highvolume ultrafine 2022年3月16日 Abstract HPGR has been found to be efficient size reduction equipment compared to conventional size reduction equipments due to its potential processing benefits in terms of energy savings, improved exposure or liberation and particle weakening The objective of the current work is to study the optimization of different process parameters during grinding Potential of HighPressure Grinding Roll (HPGR) for Size
.jpg)
An Improved HighPressure Roll Crusher Model for Tungsten and Tantalum Ores
2018年10月25日 An improved approach is presented to model the product particle size distribution resulting from grinding in highpressure roll crusher with the aim to be used in standard highpressure grinding rolls (HPGR) This approach uses different breakage distribution function parameter values for a single particle compression condition and a bed compression 2017年10月1日 The technology of high frequency vibration is widely used at mining and metallurgical industries to separate fine and ultrafine particles from the flow of dry material or pulpCurrent status and application of fine screening technology in ChinaIntroduction The mining of high gold grades is obviously very beneficial for the economic viability of an operation, but optimum recovery of the product is required to maximize profits (Chapman and Bindoff, 2010, p 13)Monitoring ore loss and dilution for minetomill 2014年1月20日 Effects of High Pressure ORE Grinding on the Efficiency of Flotation Operationspdf Available via license: CC BYNCND 30 Content may be subject to copyright(PDF) Effects of High Pressure ORE Grinding on the
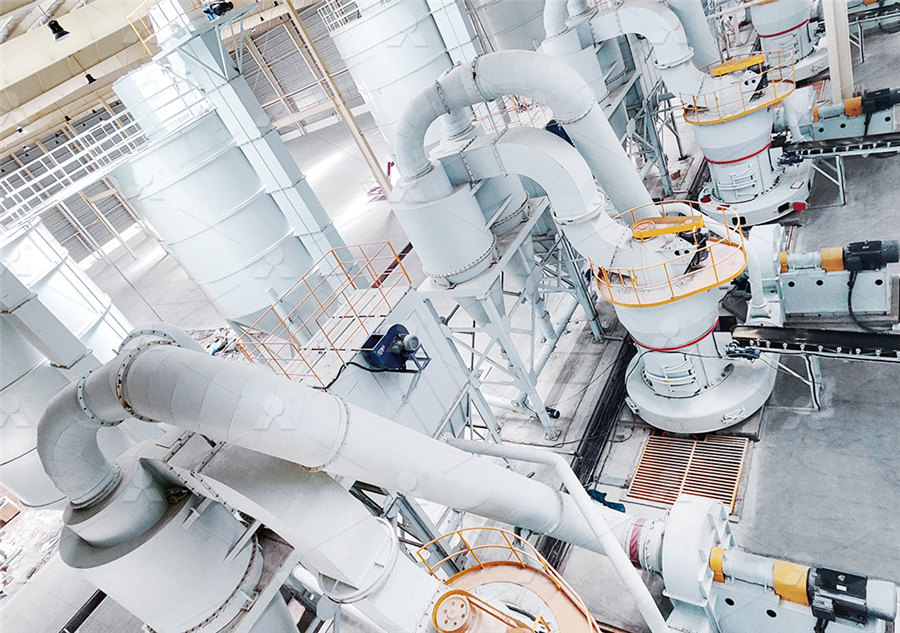
High Efficiency Fine Crusher Henan Forui Machinery
The highefficiency fine crusher is a kind of highefficiency, energysaving, practical and reliable crushing, and sandmaking equipment The highefficiency fine crusher has a wide range of uses It is especially suitable for fine crushing grinding efficiency The product discharges at atmosphere at the top of the mill The combined cyclone overflow and mill discharge are the circuit product Figure 2 Optimal Grinding Conditions 21 HIGmillTM Control Philosophy The flow from upstream processes can vary remarkably due to fluctuations in ore grade and qualityOutotec HIGmills; A Fine Grinding Technology2009年6月1日 Stirred mills are used in fine and ultrafine grinding where the liberation occurs at very fine sizes [11] [12] [13][14][15][16][17] The stirred media mills are introduced in different process Comparison of energy efficiency between ball mills and stirred 2019年8月29日 PDF While the deposit qualities for mineral raw materials are constantly decreasing, the challenges for sustainable raw material processing are Find, read and cite all the research you need (PDF) Sensor‐Based Ore Sorting Technology in Mining—Past,
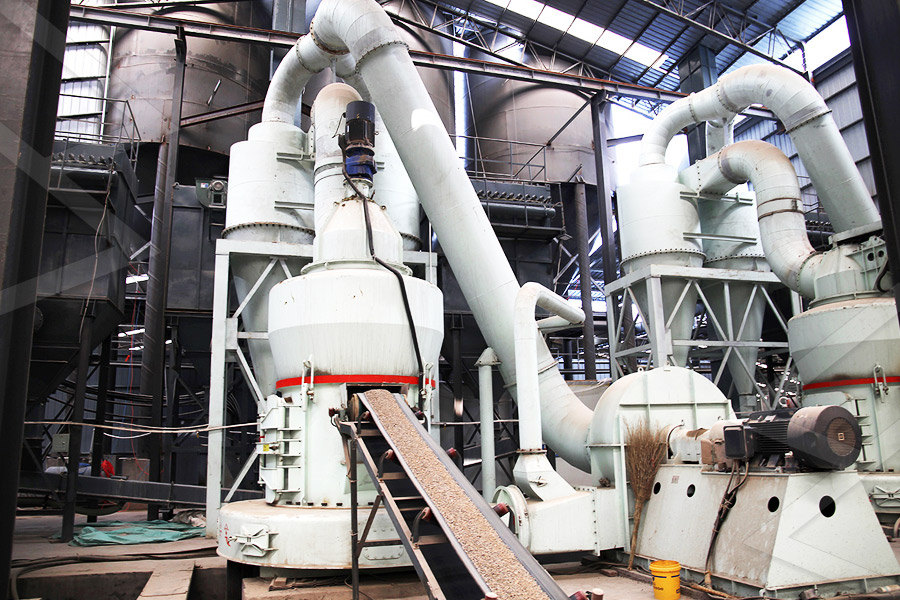
A review of intelligent ore sorting technology and equipment
Invited Review A review of intelligent ore sorting technology and equipment development Xianping Luo1,2,3), , Kunzhong He3), Yan Zhang3), Pengyu He2), and Yongbing Zhang3) 1) Jiangxi Key Laboratory of Highefficiency Development and Application of Tungsten Resources, Jiangxi University of Science and Technology, Ganzhou2023年3月15日 At present, the most commonly used processes for the separation and enrichment of the main components of lithium batteries are physical methods such as crushing and sorting (Lin et al, 2019; Liu et al, 2019; Sommerville et al, 2020; Yang et al, 2020; Zhong et al, 2019)For example, Zhang et al performed chemical and process mineralogical Research on the highefficiency crushing, sorting and recycling In this paper, a flexible, antifouling, and durable nanocellulosebased membrane functionalized by block copolymer (poly(Nisopropylacrylamide)bpoly(N,Ndimethylaminoethyl methacrylate)) is prepared via chemical modification and selfassembly, showing high separation efficiency (above 996%) for stabilized oilinwater emulsions, excellent antifouling and cycling stability, high Flexible, durable, and antifouling nanocellulosebased membrane