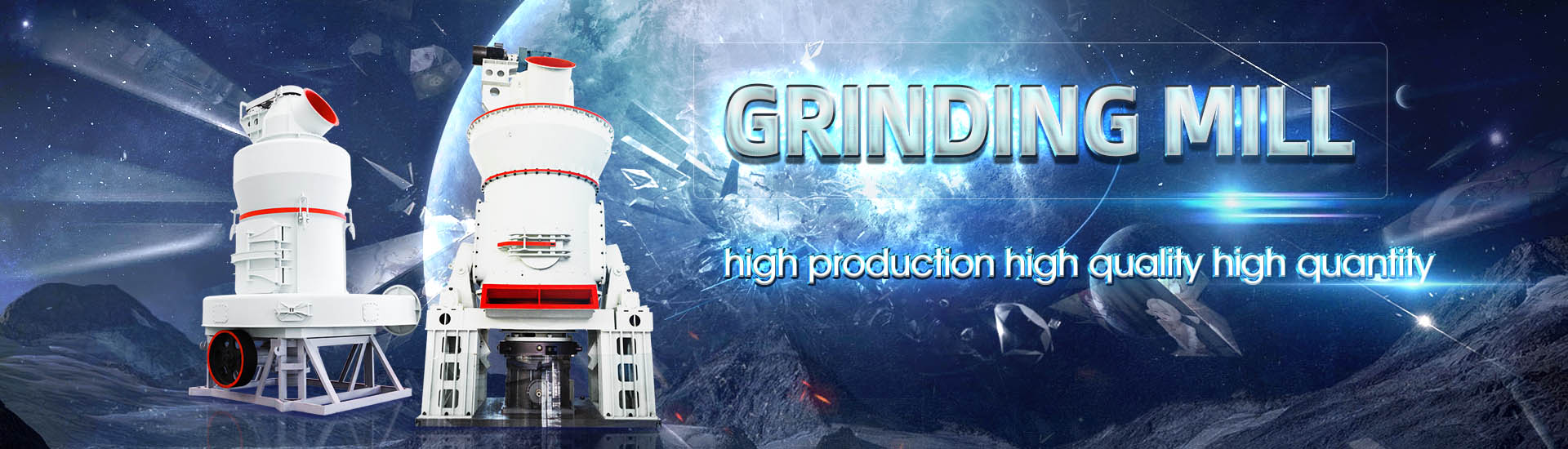
Cement plant ton consumption table
.jpg)
Electricity use per tonne of cement in selected countries and
Electricity use per tonne of cement in selected countries and regions, 2018 Chart and data by the International Energy AgencyThe following table below shows the total annual energy consumption of the whole sector in 2012, 2030 and 2050 according to the four scenarios Furthermore, the table shows the annual and Benchmarking Report for the Cement Sector UNIDOThe full cement and concrete lifecycle, from production to final disposal, accounts for nearly 10% of global energyrelated CO2 emissions with the majority of these emissions produced fromtop Cement Consuming Countries Download Table2011年5月1日 Specific energy consumption in cement production varies from technology to technology The dry process uses more electrical but much less thermal energy than the wet A critical review on energy use and savings in the cement industries
.jpg)
2021 in figures CemBR
New supply in 2021 grew by around 28% reaching just over 32 billion tonnes This capacity is distributed among 1,960 plants 32% of which are grinding, whereas the rest are integrated or Key energy and emissions parameters, including thermal and electrical energy intensity, recovered energy and CO2 intensity, are computed per tonne of cement produced along with Benchmarking of Energy Consumption and CO2 Emissions in use and now account for over 90 percent of cement consumption worldwide (41 billion tons in 2016) Cement accounts for at least 5 percent of anthropogenic emissions of greenhouse IMPROVING THERMAL AND ELECTRIC ENERGY EFFICIENCY AT consumption and raw material calcination dropped 24%, from 610 lb C/ton of cement (031 tC/tonne) to 469 lb C/ton cement (023 tC/tonne) Despite the historic progress, there is ample Energy Efficiency Improvement and Cost Saving Opportunities for
.jpg)
Energy Consumption Benchmark Guide: Cement Clinker Production
1 Determine your plant’s energy use per tonne of clinker, by fuel type (See the table on page 10 for the calculation method if these data are not readily available) 2 Compare your plant’s per 2024年2月2日 The benchmarking analysis quantified the plant’s energy intensity and CO 2 emissions per tonne of cement produced across key process stages including raw material Benchmarking of Energy Consumption and CO2 Emissions in Study on Intelligent Power Consumption Strategy of Cement Plant Based on Virtual Power Plant Yu Gong1, Liqiang Shi1, Yao Xu1, Xiaoyin Chen1, Baohua Wang2, Naiyun Sang2 1Yancheng Power Supply Branch, Jiangsu Electric Power Co, Ltd, Yancheng Jiangsu 2Institute of Automation, Nanjing University of Science and Technology, Nanjing JiangsuStudy on Intelligent Power Consumption Strategy of Cement Plant Index Terms— Cement plant, energy consumption distribution, energy cost distribution, energy management system, ISO 50001, PDCA, plandocheckact, profitabilityAnalysis of energy consumption and cost distribution on a South
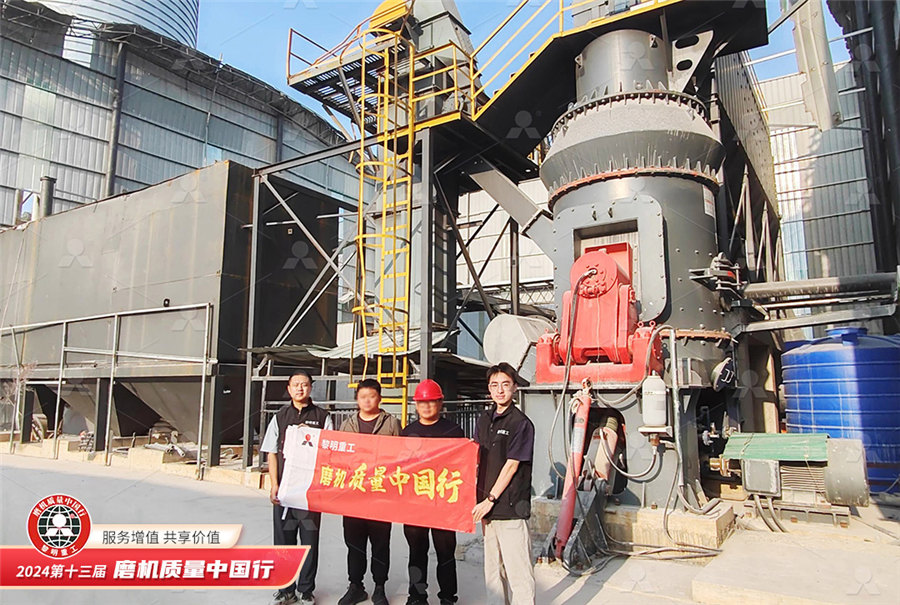
ENERGY STAR INDUSTRIALINSIGHTS
In 2012, cement plants spent over $680 million on fuels and over $570 million on electricity2 Electric Costs The Plant Energy Use table was complied to show plantlevel consumption for representative small (10th percentile), medium (median), and large year from 73 MBtu/short ton to 45 MBtu/short ton Carbon dioxide intensity due to fuel consumption and raw material calcination dropped 24%, from 610 lb C/ton of cement (031 tC/tonne) to 469 lb C/ton cement (023 tC/tonne) Despite the historic progress, there is ample room for energy efficiency improvement TheEnergy Efficiency Improvement and Cost Saving Opportunities for Cement (eg 50 years or longer) There were 110 operating cement plants in the US in 2010, spread across 37 states and Puerto Rico Portland and blended cement was produced at 110 plants in 2010, while masonry cement was produced at 71 plants Clinker was produced at 100 plants (102 including Puerto Rico) in the US in 2010 Total cementEnergy Efficiency Improvement and Cost Saving Opportunities for Cement The specific heat consumption of modern plant ranges 690 to 800 Kcal/kg clinkers The objective of firing in kiln is to convert the latent heat in the fuel to free heat and to transfer this heat to the charge in the kiln In the cement industry, coal, fuel oil and natural gas are the fuels used for combustion commonlyCement Manufacturing Process INFINITY FOR CEMENT EQUIPMENT
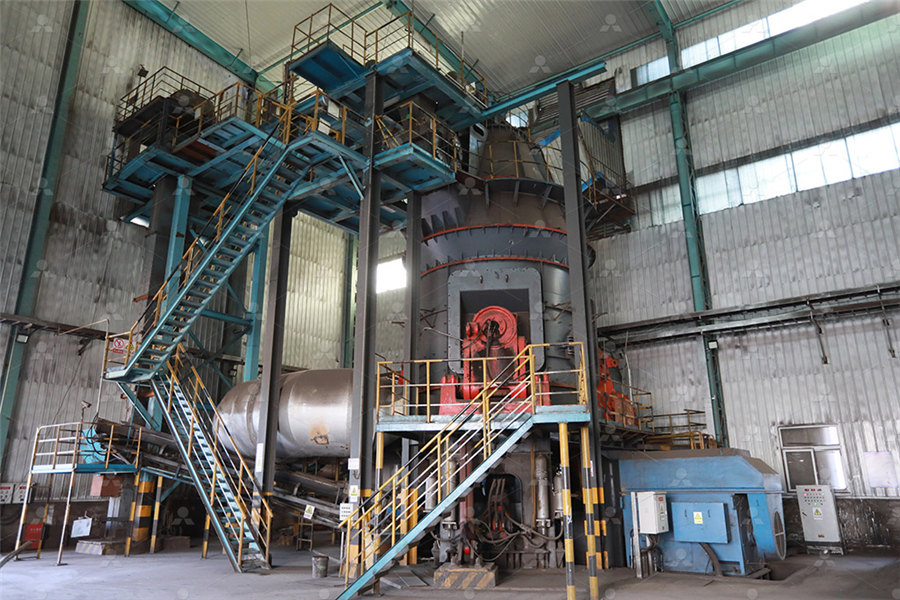
Cement Plant an overview ScienceDirect Topics
Blended cements release less GHG as compared to OPC per ton of cement 13 The impact of introducing features that make a cement plant green These have already been discussed Consumption and production of cement are cyclical, concurrent with business cyclesDownload Table Energy consumption in cement production [10] from publication: Use of Wastes in Construction Industries as an Energy Saving Approach In the modern society, demands and Energy consumption in cement production [10] ResearchGate2016年4月25日 In this study, certain measures are implemented in an existing raw mill in a cement factory and the specific energy consumption of the unit is calculated to be 2552 kWh/ton farineDetermination of correlation between specific energy consumption Construction works involving cement as one of the material requires cement consumption coefficients for estimation of quantities and cost of such works Coefficients of cement consumption works for various construction activities involving cement mortar, concrete etc are presented in tableCement Consumption Coefficients for Various Construction

IMPROVING THERMAL AND ELECTRIC ENERGY
2019年3月8日 IMPROVING THERMAL AND ELECTRIC ENERGY EFFICIENCY AT CEMENT PLANTS: INTERNATIONAL BEST PRACTICE March 2019; Table 1: Specific Thermal reduced the energy consumption by tonne per day capacity dry process cement plantKey energy and emissions parameters, including thermal and electrical energy intensity, recovered energy and CO 2 intensity, are computed per tonne of cement produced along with capacity utilisation across major process stages including raw material grinding, clinkerisation and cement grindingBenchmarking of Energy Consumption and CO2 Emissions in Cement 2020年6月24日 The method of the cement production and the thermal energy losses across the preheater tower, kiln and clinker cooler etc has been studied for the reference cement plant (Emami cement) The total thermal energy losses were found as 45% through radiation and convection, whereas 41% from the surface of the kiln, 35% from the preheater, 15% from the Thermal energy consumption and its conservation for a cement 2015年6月1日 In this paper, implementation of proper energy saving actions in an Iranian cement production plant was studied and several useful methods were suggested to improve energy consumption, since cement industry is considered to be one of the most energy intensive industries [7], [8]Establishment of proper saving actions is necessary to facilitate energy Energy consumption assessment in a cement production plant
.jpg)
ENERGY CONSUMPTION AND ENERGY AUDITS The Cement
This figure can help cement plants compare their own energy use with other plants in the industry The table classifies individual plants from the most efficient (1) to the least efficient (15) To position your plant among the others in the industry, complete the table on the next page with your most recent information to calculate the energy use per unit of your plantThis document is a daily production report for Bhavya Cements Limited that provides data on opening and closing stock quantities, receipts, production, consumption, and despatches of raw materials like limestone, laterite, gypsum, and coal as well as cement products from May 10, 2019 It also includes data on bag receipts and consumption for poly bags and paper bags Daily Production Report Format and Example PDF CementPDF On Aug 1, 2017, Wiehan A Pelser and others published Analysis of energy consumption and cost distribution on a South African cement plant Find, read and cite all the research you need on (PDF) Analysis of energy consumption and cost ResearchGateWorldwide, the production of Portland cement (PC) ranks third in energy consumption by industries (Costa and Ribeiro, 2020), emitting 5%7% of the total anthropogenic carbon dioxide (CO 2 ) into Mass balance of the cement mill system Download Table
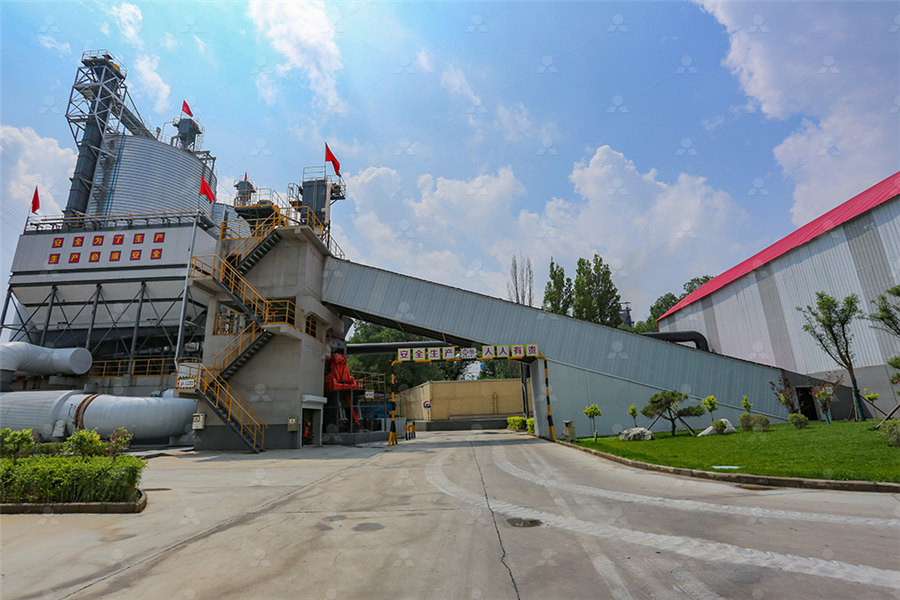
Cement Sector Bureau of Energy Efficiency
51 Grouping of Cement plants 7 52 Energy Consumption Range 8 53 Example: Normalised Baseline parameters and Target for PPC 8 Table 7: Own generation through Captive Power Plants 96 Table 8: Solid Fuel Consumption 100 Table 9: Table 1 Training data details After obtaining production data from the cement plant and removing null values and outliers, the correlation coefficients between the feature variables and coal consumption, as well as power consumption, are calculated using Eq(1) The heatmap generated from these coefficients is shown in Fig2ENERGY CONSUMPTION PREDICTION OF CEMENT Finally, in many corporate sustainability reports and research articles, water consumption rates reported for cement manufacturing plants range from 014 to 128 L / kg cement (Table 3)Water consumption rates in cement production 2018年1月20日 The distance of the case cement plant to the nearest center of population is about 15 km The annual capacity of the plant is 17 million ton cement and the annual direct water consumption of the plant is 300,000 m 3 One percent of the direct water is wasted, based on the cement plant experts’ opinion Having thisWater footprint and virtual water assessment in cement industry:
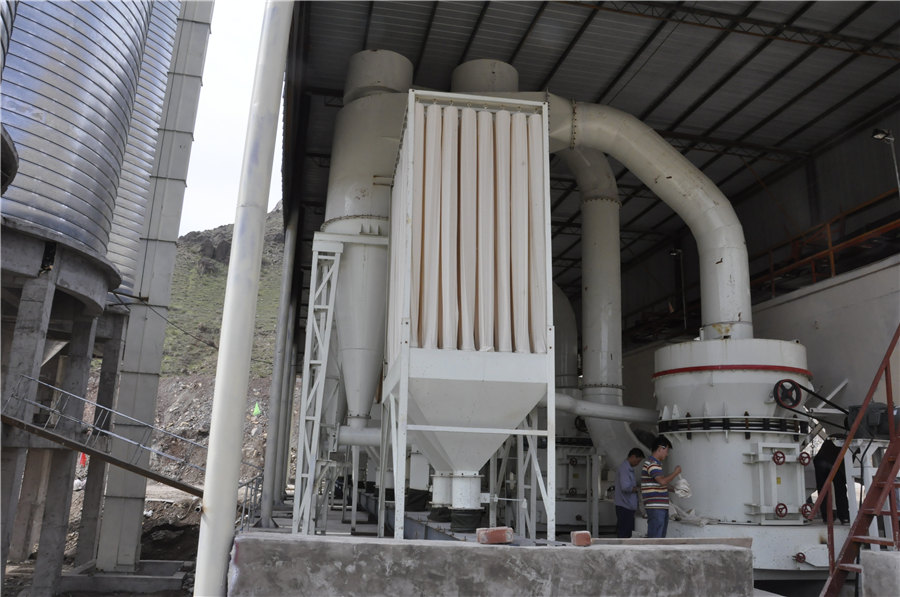
Unveiling Cement Manufacturing Plant Costs Osum
2024年4月4日 Smallscale plants can produce a few hundred tons of cement per day, while largescale plants have the capacity to produce thousands of tons per day The choice of plant size depends on various factors, including market 2022年5月9日 Cement production is one of the most energyintensive manufacturing industries, and the milling circuit of cement plants consumes around 4% of a year's global electrical energy production It is Modeling of energy consumption factors for an industrial cement 2020年6月24日 The method of the cement production and the thermal energy losses across the preheater tower, kiln and clinker cooler etc has been studied for the reference cement plant (Emami cement) The total thermal energy losses were found as 45% through radiation and convection, whereas 41% from the surface of the kiln, 35% from the preheater, 15% from the Thermal energy consumption and its conservation for a cement table 10: section wise specific energy consumption trend19 17 table 11: list of key technologies in the sector 20 table 12: comparison with har without har 23 table 13: improvement in parameters with har 23 table 14: benefit achieved by implementation of project 24 table 15: plant contact details 24 table 16: plant details 25 table 17 Cement Kerala Energy
.jpg)
2017 Fact Sheet Cement copy
ton of cement CMAN 2013/14 * MT Cement ** MT Clinker Table 1: Speci˜c energy consumption in Nepalese Cement Sector) Types of Cement Plant Speci˚c Energy Consumption Baseline 20121 2015 Scenario2 Potential Target Limestone based Electrical 149 kWh/t* 80 – 2021年7月28日 Energy efficiency in a cement plant is measured as a combination of two factors, viz, Thermal Energy Consumption and (2) Electrical Energy Consumption The former specifically measures the kiln performance while the latter measures the overall performance of the plant Thermal Energy Consumption (measured as MJ/t clinker)Indian Cement Sector CMAthe US cement industry’s consumption of nonfuel raw materials increased in 2018 compared with that in 2017 for the production of clinker, to 129 mt from 128 mt, and cement, to 106 mt from 938 mt (table 6) A variety of raw materials can be substituted to make clinker at 2018 Minerals Yearbook USGS Publications Warehouse2015年2月16日 Typical cement plant power costs can range from EUR39 to EUR170/MWh Mill designs The most important first step in controlling energy consumption is to be aware of the relative importance of the process areas where most energy is consumed Figure 2 shows a typical breakdown of electrical energy consumption at a cement plantBest energy consumption International Cement Review
.jpg)
Study on Intelligent Power Consumption Strategy of Cement Plant
Study on Intelligent Power Consumption Strategy of Cement Plant Based on Virtual Power Plant Yu Gong1, Liqiang Shi1, Yao Xu1, Xiaoyin Chen1, Baohua Wang2, Naiyun Sang2 1Yancheng Power Supply Branch, Jiangsu Electric Power Co, Ltd, Yancheng Jiangsu 2Institute of Automation, Nanjing University of Science and Technology, Nanjing JiangsuIndex Terms— Cement plant, energy consumption distribution, energy cost distribution, energy management system, ISO 50001, PDCA, plandocheckact, profitabilityAnalysis of energy consumption and cost distribution on a South In 2012, cement plants spent over $680 million on fuels and over $570 million on electricity2 Electric Costs The Plant Energy Use table was complied to show plantlevel consumption for representative small (10th percentile), medium (median), and large ENERGY STAR INDUSTRIALINSIGHTSyear from 73 MBtu/short ton to 45 MBtu/short ton Carbon dioxide intensity due to fuel consumption and raw material calcination dropped 24%, from 610 lb C/ton of cement (031 tC/tonne) to 469 lb C/ton cement (023 tC/tonne) Despite the historic progress, there is ample room for energy efficiency improvement TheEnergy Efficiency Improvement and Cost Saving Opportunities for Cement
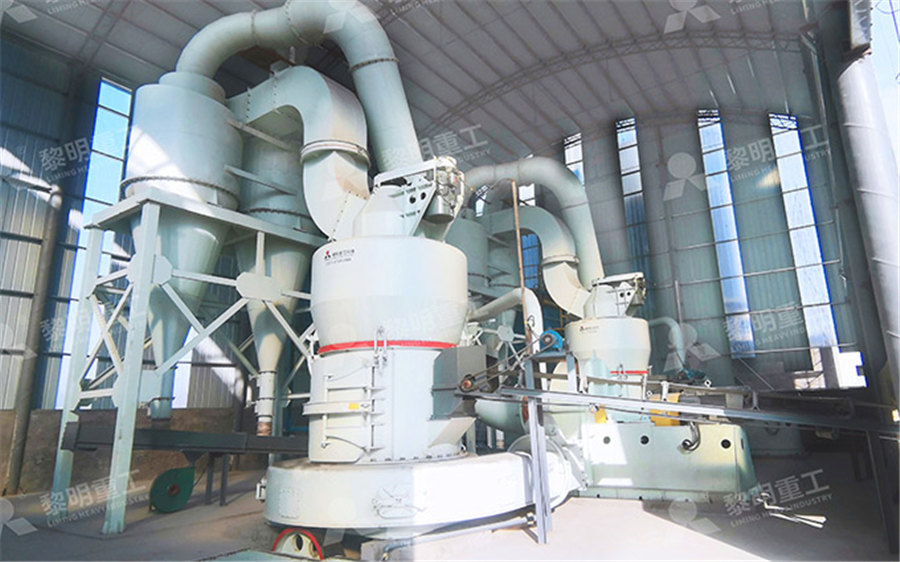
Energy Efficiency Improvement and Cost Saving Opportunities for Cement
(eg 50 years or longer) There were 110 operating cement plants in the US in 2010, spread across 37 states and Puerto Rico Portland and blended cement was produced at 110 plants in 2010, while masonry cement was produced at 71 plants Clinker was produced at 100 plants (102 including Puerto Rico) in the US in 2010 Total cementThe specific heat consumption of modern plant ranges 690 to 800 Kcal/kg clinkers The objective of firing in kiln is to convert the latent heat in the fuel to free heat and to transfer this heat to the charge in the kiln In the cement industry, coal, fuel oil and natural gas are the fuels used for combustion commonlyCement Manufacturing Process INFINITY FOR CEMENT EQUIPMENTBlended cements release less GHG as compared to OPC per ton of cement 13 The impact of introducing features that make a cement plant green These have already been discussed Consumption and production of cement are cyclical, concurrent with business cyclesCement Plant an overview ScienceDirect TopicsDownload Table Energy consumption in cement production [10] from publication: Use of Wastes in Construction Industries as an Energy Saving Approach In the modern society, demands and Energy consumption in cement production [10] ResearchGate
FYEFEPS2HDZ49G5Z0[B.jpg)
Determination of correlation between specific energy consumption
2016年4月25日 In this study, certain measures are implemented in an existing raw mill in a cement factory and the specific energy consumption of the unit is calculated to be 2552 kWh/ton farineConstruction works involving cement as one of the material requires cement consumption coefficients for estimation of quantities and cost of such works Coefficients of cement consumption works for various construction activities involving cement mortar, concrete etc are presented in tableCement Consumption Coefficients for Various Construction