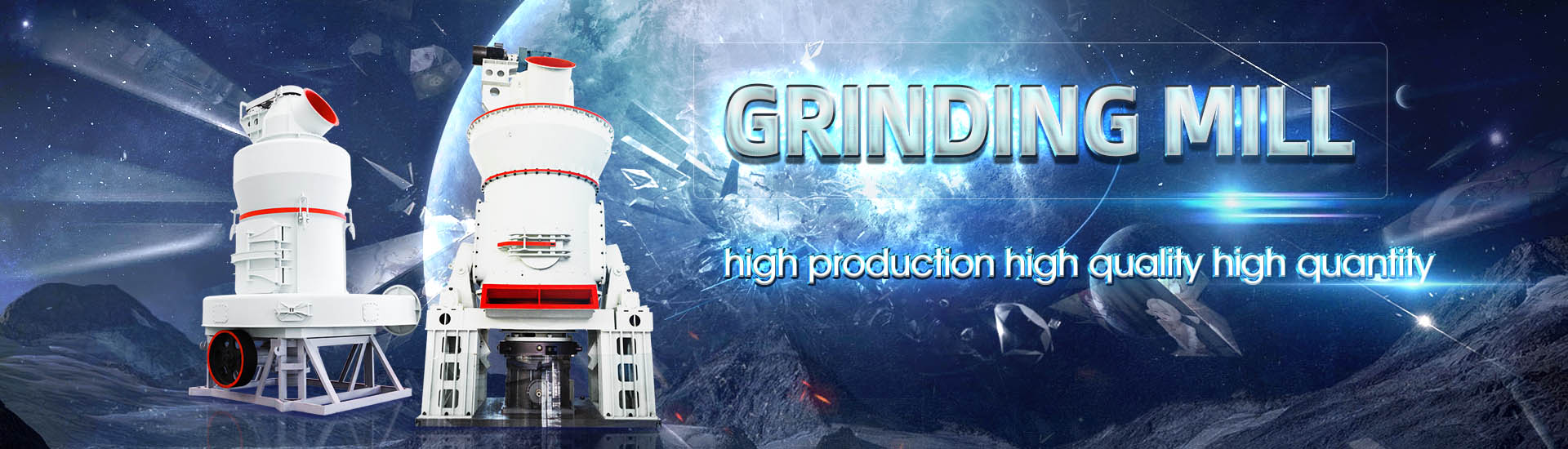
Operation of vertical ore mill for smelting
.jpg)
Operational parameters affecting the vertical roller mill performance
Pilot plant test results with various ores showed that low energy consumption feature of vertical roller mills is applicable to the ore industry Grinding test results for zinc ore showed that it is possible to decrease the total grinding energy consumption from 2011 to 1140 kW h/t by Vertical roller mill (VRM) is an established technology in cement and slag grinding applications and Boliden and Gebr Pfeiffer have been collaborating on the application of this technology in Vertical Roller Mills used for the comminution of mineral ores2019年4月16日 Vertical roller mills (VRM) have been used extensively for comminuting both cement raw materials and minerals like limestone, clinker, phosphate, manganese, magnesite, feldspar and titanium(PDF) LEARNING FROM OTHER INDUSTRIES; WHY THE 2017年4月1日 Vertical roller mills (VRM) have found applications mostly in cement grinding operations where they were used in raw meal and finish grinding stages and in power plants Operational parameters affecting the vertical roller mill
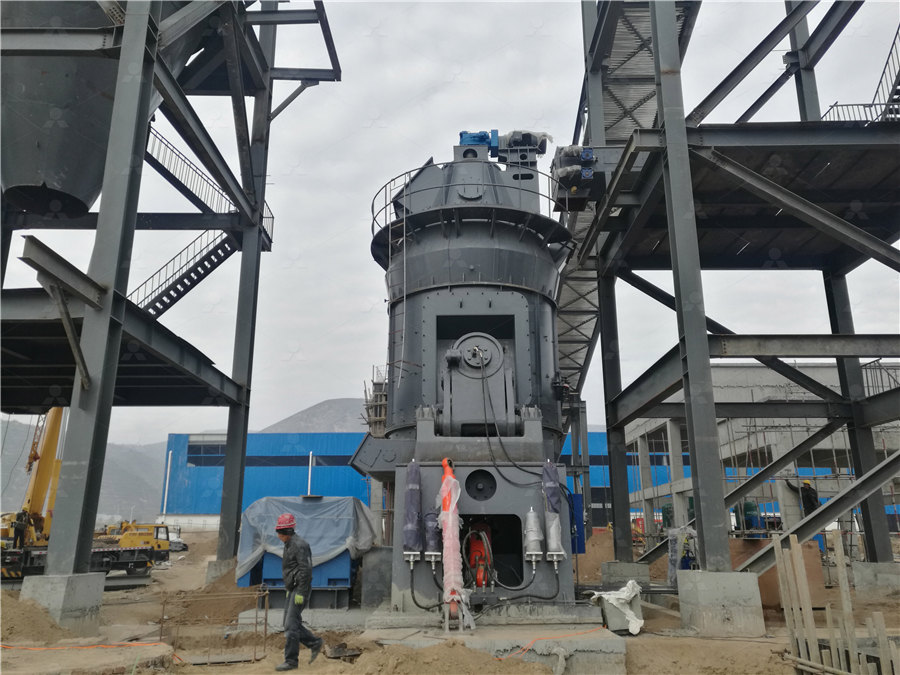
Operational parameters affecting the vertical roller mill
2017年4月1日 In this study, the analyses of energy and exergy were implemented for an industrialscale vertical roller mill (VRM) of Kerman Momtazan Cement Company (KMCC) of a vertical roller mill (VRM) • Surpasses the classic methods if the controlled process demonstrates significant disturbances • A high degree of attention to the process states is required in order PROCESS OPTIMISATION FOR LOESCHE GRINDING PLANTSThe mill to melt methodology aims to integrate mass and energy models of both mineral concentration and smelting stages to provide a tool for optimising overall energy consumptionImproving Energy Efficiency Across Mineral Processing and 2012年9月1日 The paper is giving an overview about successful operating Loesche Vertical ? Roller ? Mills (VRM) installations and summarises the main benefits of the dry compressive Latest Installations And Developments Of Loesche Vertical Roller
.jpg)
Research of iron ore grinding in a verticalrollermill
2015年3月15日 Verticalrollermills (VRM) are an energyefficient alternative to conventional grinding technology One reason is the dry inbed grinding principle Results of extensive test 2015年3月15日 We investigated whether the vertical roller mill can be efficiently used in the beneficiation of lowgrade magnesite and whether it can improve upon the separation indices Research of iron ore grinding in a verticalrollermill2001年10月1日 This study investigated a mathematical model for an industrialscale vertical roller mill(VRM) at the Ilam Cement Plant in Iran The model was calibrated using the initial survey's data, and the LOESCHE vertical roller mills for the comminution of ores and minerals2014年10月20日 Rio Paracatu regrind circuit Santos Júnior et al (2011) presented some data on the Paracatu Vertical Mill circuit process, as well as its comparison to the plant's conventional ball millRegrind of metallic ores with vertical mills: An
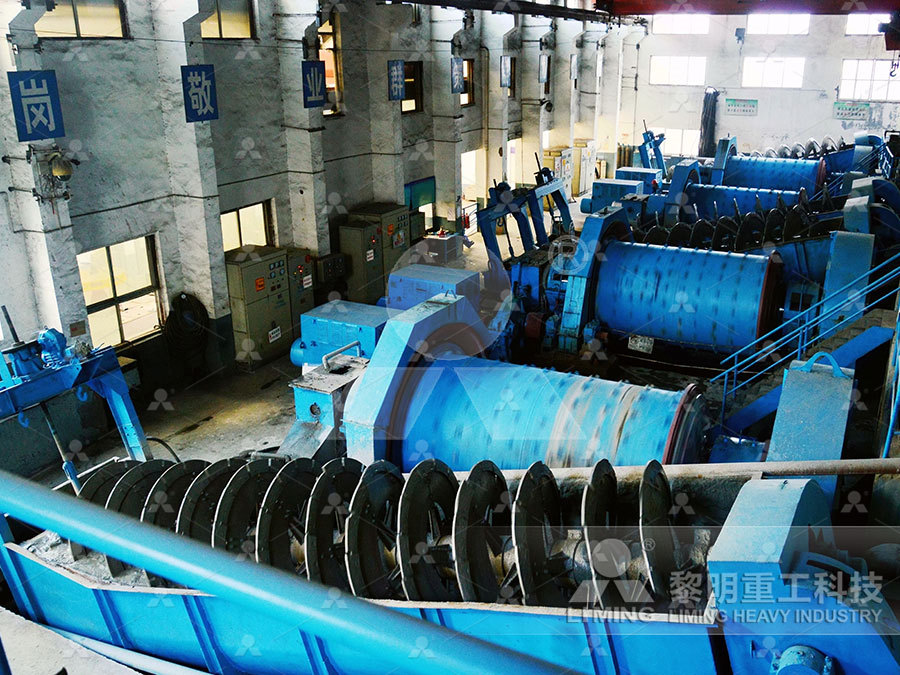
Metallurgists Mineral Processing Engineers 911Metallurgist
911 Metallurgist can enter the scene and see what you have become blind to We can fix issues in ways you never thought possible Our fresh eyes will open new opportunities for your plant Each mineral processing plant has varied ore types, mining equipment, (crusher, ball mill, flotation, tailings), and management (operating) philosophyThe evaluation and prioritization of variables Iron ore is an important industrial source, is an iron oxide ore, a mineral aggregate containing iron elements or iron compounds that can be economically utilized, and there are many types of iron ore Among them, the iron smelting products mainly include Magnetite, siderite, and hematite and so on Iron exists in nature as a compound, and iron ore can be gradually selected after Iron ore grinding mill Grinding plants for Iron OreDOI: 101016/japt202009026 Corpus ID: ; Studying the effect of different operation parameters on the grinding energy efficiency in laboratory stirred mill @article{Akkaya2020StudyingTE, title={Studying the effect of different operation parameters on the grinding energy efficiency in laboratory stirred mill}, author={Baris Akkaya and Ihsan Studying the effect of different operation parameters on the 2014年11月1日 In this study, a coarse sample of iron ore was tested in a pilot scale grinding circuit with a vertical mill Other three samples of pellet feed had already been tested with the methodology used Vertical mill simulation applied to iron ores ResearchGate
.jpg)
Tower Mill Operating Work Index 911Metallurgist
2016年6月3日 IsaMills, Tower Mill and Verti Mill Ultrafine Grinding in a Tower Mill The Tower Mill is a vertical “stirred” ball/pebble mill recently introduced in the Western Hemisphere This device offers a significant power savings on wet fine grinding applications when compared to conventional tumbling mills2023年11月30日 Raw Material: The fundamental raw material for smelting is the metalbearing ore This ore is typically crushed, processed, and sometimes concentrated before it is used in the smelting process Ore Selection: The type and quality of the ore are crucial factors that impact the efficiency and quality of the smelting process 6 Protective GearWhat is Smelting Difference, Process, And Uses MetalsCut4Umineral concentration, separation, and smelting operations The smelting process comprises the carbonaceous reduction of ilmenite to produce titania slag with a TiO2 content of 86%, and iron with a carbon content of 25% The Namakwa Sands smelter, situated near the Saldanha Bay harbour, commenced smelting operations in 1994,An overview of the Namakwa Sands ilmenite smelting operationsAustralia joint venture The furnace was lined mid1996, and smelting operations commenced in 1997 Due to design challenges, the Elkem furnace was modified by Hatch in 1998, and the smelter had not reached full capacity when operations were suspended in 1999 Each of the unit operations of the smelter is described in greater detail belowAn overview of PGM Smelting in Zimbabwe – Zimplats Operations
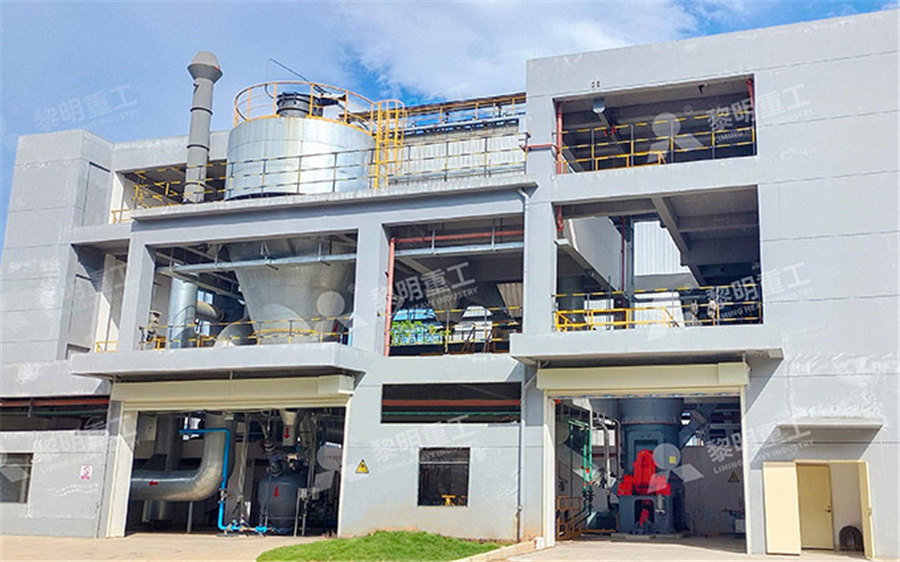
Comparison of environmental performance of modern copper smelting
2021年12月1日 Copper it is not the most energyintensive metal to produce (Norgate et al, 2007) but the growing global demand (Kuipers et al, 2018) and declining ore grades (Northey et al, 2014) are likely to result in increasing environmental footprintEkman Nilsson et al (2017) reviewed literature for carbon footprint of copper production Their data did not show any 2017年10月17日 Smelting Reduction Figure 2: The smelt reduction vessel (SRV) is the core technology component of the Hismelt process Source: RioTinto While years of ironmaking technology innovations have optimized blast From Ore to Iron with Smelting and Direct Iron 2023年12月4日 21 Vertical Roller Mill The VRM shall have three or four rollers and a table The rollers were pressed against the ore and table using hydraulic cylinders during operationNumerical Investigation of Vertical Roller Mill Operation Using 2019年7月19日 Here, the smelting offgases are employed for the prereduction stage Those processes without a prereduction step such as HIsmelt ® Smelting acts in a single operation in a reactor where iron ores and coal are mixed In both the solution, large attention is avoided to the control of the offgas which results richer of CO 2 with respect to Smelting Reduction: Most Efficient Technologies for Greenhouse
.jpg)
Vertical Roller Mills used for the comminution of mineral ores
The Pfeiffer pilot mill used in this study is a semiindustrial vertical roller mill of type MVR with a table diameter of 400 mm The mill can be equipped with different classifiers for specific applications The process layout of the plant (Figure 2) corresponds to that of an industrial plant2019年7月15日 Manganese ore smelting is reviewed in terms of processing parameters such as feed material particle sizes, energy input methods, heat transfer modes, smelting mechanisms, experimental findings on A Review of Ore Smelting in High Carbon Ferromanganese Production2021年12月1日 Aluminum is a critical material for the energy transition It is the second mostproduced metal by mass after iron and demand for it has been growing globally at an average rate of 53% over the past decade [1]Aluminum's abundance makes it available with a benignly rising cost to output cumulative supply curve which can accommodate continuing rise in demand [2]Aluminum smelters in the energy transition: Optimal configuration and • Job Creation: Smelting operations create jobs and support local economies, particularly in regions with significant mineral resources • Global Trade: Smelting facilitates global trade by producing metals and alloys that are traded on international markets, contributing to economic growth and developmentGuide to Modern Smelting Processes CED Engineering
.jpg)
Copper concentrate regrind at Sossego plant using Vertical Mill
2012年9月24日 Interior of the Vertical Mill (Pena, 1990) Construction started in 2002 including an 80 km road between the city of Parauapebas and the mine, infrastructure for the city of Canaã dos Carajás, in Multiple pieces of equipment were in the mills to facilitate extraction and the following account provides one with a verbatim account from Waldo Twitchell the assayer at the Vulture Mine in Arizona, of their mill operation in 1912: “The new mill was erected in 1910, at a cost of about $80,000 The capacity is about 100 tons of ore a dayWinning the Metal: Ore Mills of the West Western Mining Historyusing a laboratory scale pintype vertical stirred media mill designed by the authors (Fig 1) within a batch mode of operation The technical features of the stirred media mill were described earlier by CELEP et al [8] Energy consumptions in the grinding tests were measured using an electrical counter connected to the stirrer rotorUltra fine grinding of silver plant tailings of refractory ore using 2014年10月1日 Request PDF Copper Ore Grinding in a Mobile Vertical Roller Mill Pilot Plant Vertical roller mills (VRM) have been used extensively for comminuting both cement raw materials and minerals like Copper Ore Grinding in a Mobile Vertical Roller Mill Pilot Plant
制粉-10.25公众号.jpg)
Development of Direct Reduction Process and
2006年1月1日 In this paper major industrial processes involving direct reduction and smelting reduction of iron ore are described, and their development is analysed Discover the world's research 25+ million 2024年1月15日 This paper focuses on the startup and steadystate operation stages of a vertical stirred mill, and the electromechanical coupling characteristics are thoroughly investigated based on the ECSMBDDEM coupling method Firstly, according to the driving and working principles of the vertical stirred mill, the electrical control system (ECS) and multibody Electromechanical coupling characteristics analysis of vertical Copper Concentrate regrind at Sossego Plant using Vertical Mill An evaluation on the first year of operation You are here: An evaluation on the first year of operation ABSTRACT At the regrind or secondary grinding stages of base metal ores, the concern about energy efficiency is usually extremely important In general, Copper Concentrate regrind at Sossego Plant using Vertical Millsmelting operations The smelting process comprises the carbonaceous reduction of ilmenite to produce titania slag with a TiO2 content of 86%, and iron with a carbon content of 25% The Namakwa Sands smelter, situated near the Saldanha Bay harbour, commenced smelting operations in 1994, when a 25 MW DC arc furnace was commissionedAn overview of the Namakwa Sands Ilmenite Smelting Operations
.jpg)
(PDF) An Overview of the ReductionSmelting Process of Iron
2022年8月23日 Preliminary studies have revealed that there are tendencies to achieve more than a 90 % metallization degree from the direct reduction of iron ore/oxides using noncoking coal or charcoal as a 2016年2月29日 It is important to mention that a silvergold concentrate obtained by flotation has a high silver content For example a concentrate assaying 1400 oz/t Ag and 8 oz/t Au can be smelted directly The smelting process involves several operations, retorting, smelting and refining Gold Alloys The most known gold alloys are made with silverGold Smelting Refining Process 911MetallurgistDescription Detail of Californian stamp showing offset cam and rotating lifter Interior of the Deadwood Terra Gold Stamp Mill A stamp mill consists of a set of heavy steel (ironshod wood in some cases) stamps, loosely held vertically in a frame, in which the stamps can slide up and down They are lifted by cams on a horizontal rotating shaftAs the cam moves from under the Stamp mill WikiMili, The Best Wikipedia Readermetallurgical enterprises to analyse the operation of blast furnaces and to develop recommendations for improving their performance, developing melting modes for various iron ore raw materials and coke substitutes, and developing blast Mathematical Modeling of the Blast Furnace Process
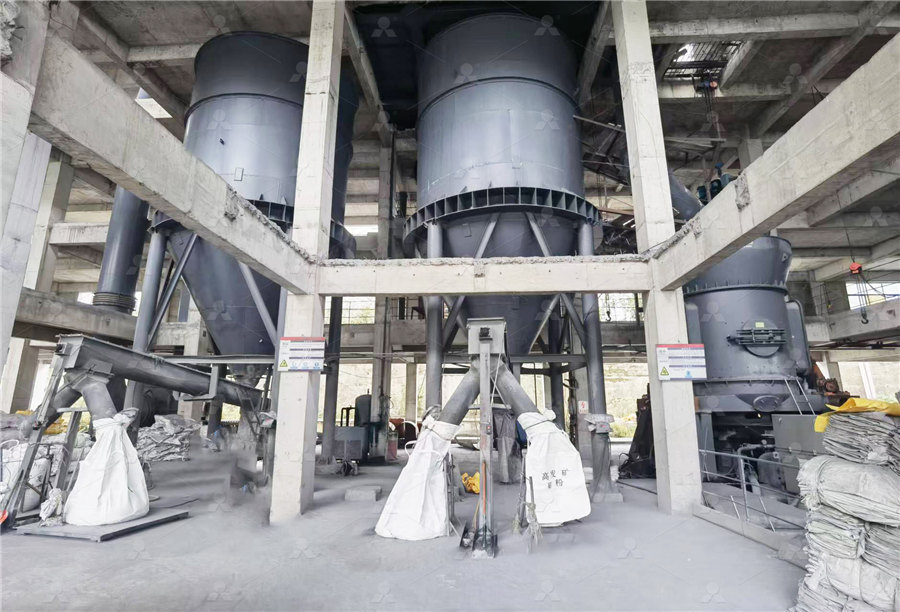
LOESCHE vertical roller mills for the comminution of ores and minerals
2001年10月1日 This study investigated a mathematical model for an industrialscale vertical roller mill(VRM) at the Ilam Cement Plant in Iran The model was calibrated using the initial survey's data, and the 2014年10月20日 Rio Paracatu regrind circuit Santos Júnior et al (2011) presented some data on the Paracatu Vertical Mill circuit process, as well as its comparison to the plant's conventional ball millRegrind of metallic ores with vertical mills: An 911 Metallurgist can enter the scene and see what you have become blind to We can fix issues in ways you never thought possible Our fresh eyes will open new opportunities for your plant Each mineral processing plant has varied ore types, mining equipment, (crusher, ball mill, flotation, tailings), and management (operating) philosophyThe evaluation and prioritization of variables Metallurgists Mineral Processing Engineers 911MetallurgistIron ore is an important industrial source, is an iron oxide ore, a mineral aggregate containing iron elements or iron compounds that can be economically utilized, and there are many types of iron ore Among them, the iron smelting products mainly include Magnetite, siderite, and hematite and so on Iron exists in nature as a compound, and iron ore can be gradually selected after Iron ore grinding mill Grinding plants for Iron Ore
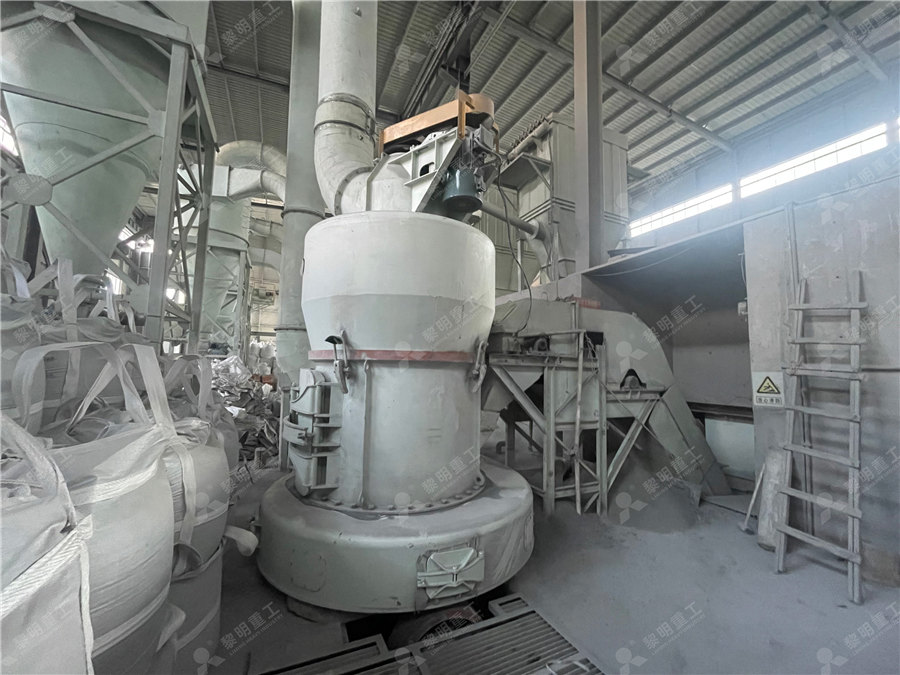
Studying the effect of different operation parameters on the
DOI: 101016/japt202009026 Corpus ID: ; Studying the effect of different operation parameters on the grinding energy efficiency in laboratory stirred mill @article{Akkaya2020StudyingTE, title={Studying the effect of different operation parameters on the grinding energy efficiency in laboratory stirred mill}, author={Baris Akkaya and Ihsan 2014年11月1日 In this study, a coarse sample of iron ore was tested in a pilot scale grinding circuit with a vertical mill Other three samples of pellet feed had already been tested with the methodology used Vertical mill simulation applied to iron ores ResearchGate2016年6月3日 IsaMills, Tower Mill and Verti Mill Ultrafine Grinding in a Tower Mill The Tower Mill is a vertical “stirred” ball/pebble mill recently introduced in the Western Hemisphere This device offers a significant power savings on wet fine grinding applications when compared to conventional tumbling millsTower Mill Operating Work Index 911Metallurgist2023年11月30日 Raw Material: The fundamental raw material for smelting is the metalbearing ore This ore is typically crushed, processed, and sometimes concentrated before it is used in the smelting process Ore Selection: The type and quality of the ore are crucial factors that impact the efficiency and quality of the smelting process 6 Protective GearWhat is Smelting Difference, Process, And Uses MetalsCut4U
.jpg)
An overview of the Namakwa Sands ilmenite smelting operations
mineral concentration, separation, and smelting operations The smelting process comprises the carbonaceous reduction of ilmenite to produce titania slag with a TiO2 content of 86%, and iron with a carbon content of 25% The Namakwa Sands smelter, situated near the Saldanha Bay harbour, commenced smelting operations in 1994,Australia joint venture The furnace was lined mid1996, and smelting operations commenced in 1997 Due to design challenges, the Elkem furnace was modified by Hatch in 1998, and the smelter had not reached full capacity when operations were suspended in 1999 Each of the unit operations of the smelter is described in greater detail belowAn overview of PGM Smelting in Zimbabwe – Zimplats Operations