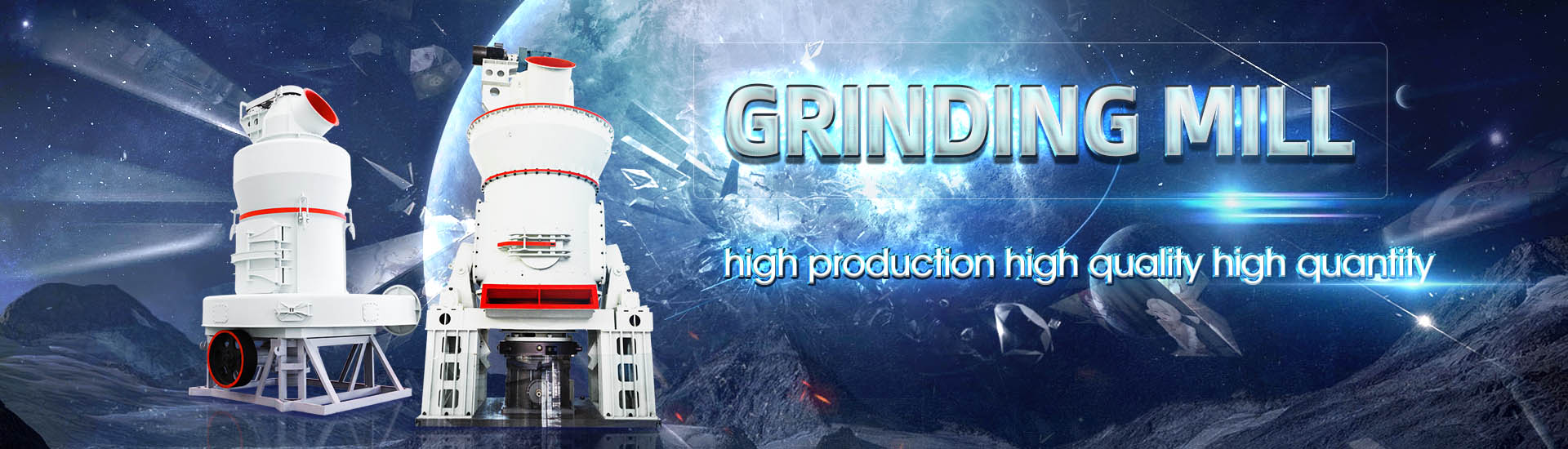
What is the name of the job of cement plant burning and crushing
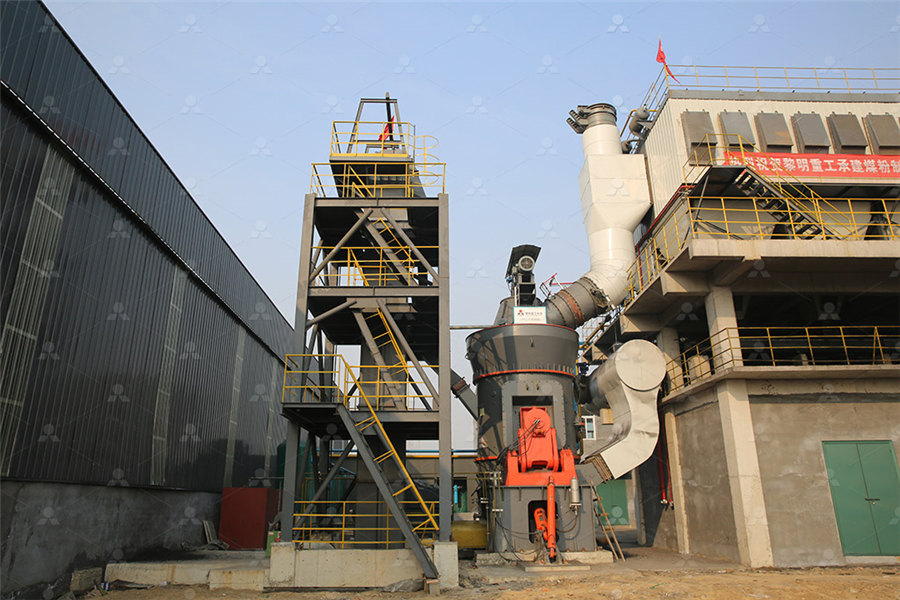
The Cement Plant Operations Handbook International Cement
raw materials, burning, grinding and quality control are supported by a range of chapters addressing critial topics such as maintenance and plant reporting, alongside a detailed 2020年8月25日 Cement grinding: The clinker is taken from the clinker silo and sent to the feed bin where it is mixed with gypsum and additives before entering the cement grinding plant In the cement grinding process, the clinker is Cement Production Process Cement Manufacturing The both calcareous and argillaceous raw materials are firstly crushed in the gyratory crushers to get 25cm size pieces separately The crushed materials are again grinded to get fine particles into ball or tube mill Each finely grinded Manufacture of Cement Materials and Manufacturing The desired raw mix of crushed raw material and the additional components required for the type of cement, eg silica sand and iron ore, is prepared using metering devicesFrom raw materials to cement
.jpg)
The Cement Production Process
Clinker is ground to produce cement The three broad processes of cement manufacturing are: Raw milling — the preparation of the kiln feed Calcining and burning or clinkering — the Cement is typically made from limestone and clay or shale These raw materials are extracted from the quarry crushed to a very fine powder and then blended in the correct proportions This blended raw material is called the 'raw feed' or Cement manufacturing: components of a cement plant The crushed limestone and aggregates such as sand, clay and ironstone are blended together in a raw mill to a particle size of 90 micrometres, producing “kiln feed” Cement Plant: The Cement Plant: The Manufacturing Process 4 5 World Cement Concrete is made by mixing cement with aggregate (sand, gravel, and water), which forms a paste that hardens over time Cement is necessary to give the concrete its binding properties, How Cement is Made Cement Manufacturing Process
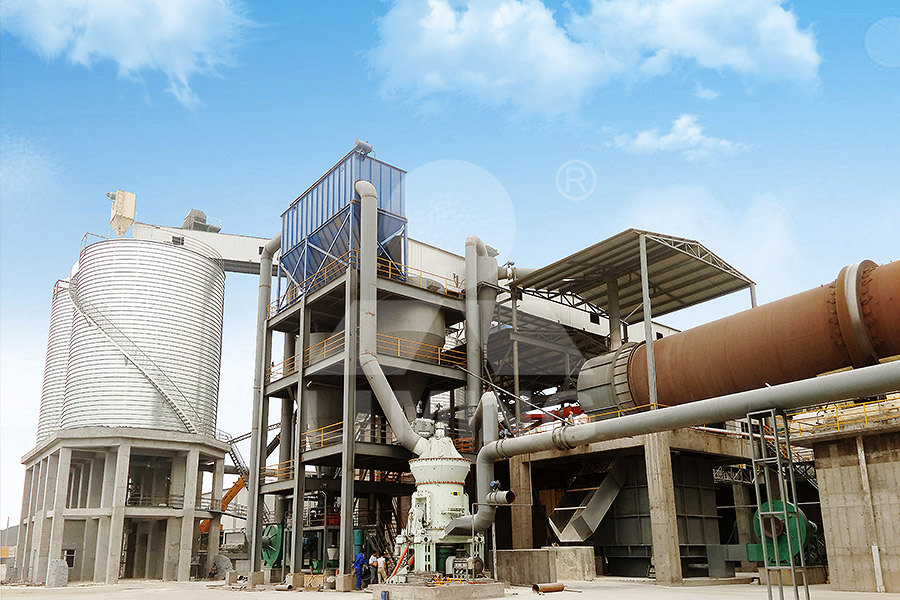
StepbyStep Guide to the Manufacturing of Cement
How can I start a cement manufacturing plant? Starting a cement factory involves several crucial steps: Determine the scale of production and type of cement to be produced Choose an optimal location for the cement plant Design the layout 2024年9月5日 Tricalcium silicate (C₃S): this compound gives strength to the cement and hardening properties Dicalcium silicate (C₂S): Strengthens cement hardening over time (C₃A) Tricalcium aluminate: regulates cement setting A Comprehensive Guide to the Cement Manufacturing 2024年1月30日 The following steps describe how a concrete plant works: The cement, sand, gravel, and water are loaded into the plant The ingredients are mixed together in the mixer The concrete is discharged from the mixer and transported to the desired location The concrete plant is a vital piece of equipment for the construction industryWhat is a Concrete Plant? (The Ultimate Guide) Plant4HarvestIn short, if you need highvolume crushing capabilities and are looking to expand your business into more complex areas of crushing materials, then setting up a crusher plant is your best choice! All in all, setting up a full crushing plant offers greater flexibility, better efficiency and improved productivity rather than relying on a single crusher aloneCrushing plants what are they and how do I set one up?
.jpg)
Cement Manufacturing Process and Its Environmental Impact
2023年7月10日 Cement manufacturing is a significant industrial activity that plays a vital role in the construction sector However, the process of cement production is associated with various environmental to cement Extracting raw materials Crushing and transportation Raw material preparation I: Storage and homogenisation Raw material preparation II: Drying and raw grinding Burning The burning of the raw meal at approx 1,450°C is carried out in Lepol or preheater kilns that work by varying methods, theFrom raw materials to cement2021年1月10日 Primary crushing is the first stage of material reduction and can sometimes be the only stage needed to generate the desired product for a job Depending on the setup, primary crushing will take the larger material that has been blasted, excavated, or reclaimed and process it through an impactor, jaw, or gyratory crusher to generate a range of product sizesWhat Is Primary, Secondary, and Tertiary Crushing?3Stationary Concrete Batching Plant: Stable concrete batching plants are steady and situated in a long way from the construction site Concrete is transported to the construction site using a truck; steady concrete batching plants are simple to set up, they are bigger in dimension than cellular concrete batching plantsBatching Plant: Types, Advantages Disadvantages
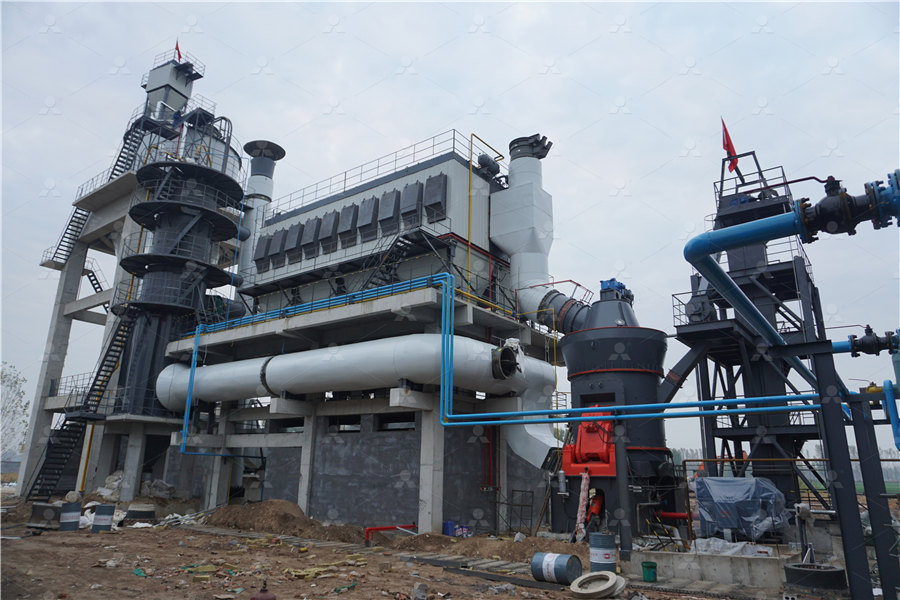
Overview of Concrete Batch Plants: types, parts applications JEL
The cost of a concrete plant depends on several factors, such as the type of plant (stationary or mobile), production capacity, level of automation and additional features Generally, a small to mediumsized stationary concrete plant can cost anywhere from $200,000 to $1 million2020年9月14日 Step #4 The burning of the raw meal at approx 1,450°C is carried out in Lepol or preheater kilns that work by varying methods, the main difference being in the preparation and preheating of the kiln feed By chemical conversion, a process known as sintering, a new product is formed: clinker Step #5The essentials of electrical systems in cement plants EEPPrimary crushing equipment As the name suggests, this kind of crushing is the first in the process Run of Mine (ROM) materials are brought directly from blasting projects and crushed a primary crusher for the first round of crushing Types of Crushers: What You Need to KnowCyclone Preheater Introduction: The cyclone preheater is the core equipment of the new dry process cement production technologyIt uses the suspension preheating method to preheat and partially decompose the raw material to Cyclone Preheater Provided for Cement Plant
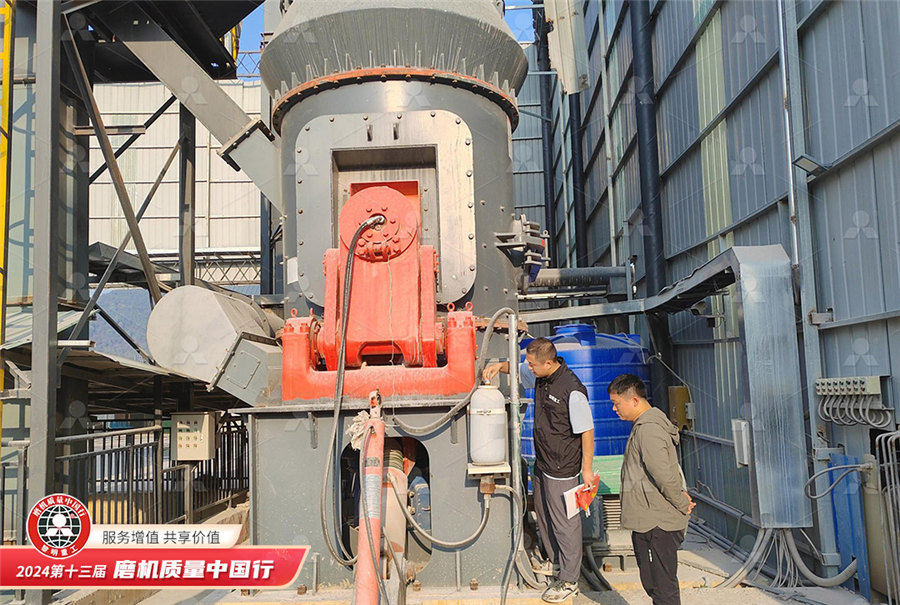
Reactions in the cement kiln clinkering
Alite formation and other reactions at 1300 °C 1450 °C in the burning zone In the burning zone, above about 1300 °C, reactions take place quickly The clinker is in the burning zone for perhaps 1020 minutes but in this time a lot 2024年6月21日 Blended Hydraulic Cement Types Most blended hydraulic cements mix Type I portland cement with other materials: Type IL: Portlandlimestone cement has 515% limestone added Type IS: Blast furnace slag cement contains up to 60% blast furnace slag, a byproduct of iron smelting Type IP: Portlandpozzolana cement contains silica or aluminumbased clinker Different Cement Types and How They're Made Substrata2022年12月23日 PDF Even if cement is a wellconsolidated material, the chemistry of cement (and the chemistry inside cement) ergy involved in a standard cement plant (high cost)(PDF) An Insight into the Chemistry of Cement—A Review2024年10月14日 A stone crushing plant needs essential primary crushers like jaw and gyratory crushers as well as finecrushing equipment like impact crushers and ball mills Other critical heavyduty machines for the effective operation of a stone mill include the belt conveyors, vibration feeder, vibrating screens, and a central control system for all these machinesWhat Machines Do Stone Crushing Plants Need? Fote Machinery
.jpg)
Manufacture of Cement Materials and Manufacturing Process of
The name Portland was given by the inventor as it resembles a stone quarried on the Isle of Portland The first use of modern day Portland cement was in the tunnel construction in the Thames River in 1828 Manufacture Process of Cement The manufacture procedures of Portland cement is described below Mixing of raw material; Burning; Grinding2020年8月25日 A full cement production process includes the cement crushing process, raw mill process, clinker process, and Cement equipment refers to all equipment in the cement plant, such as cement mill, cement crusher, cement kiln this process is generally known as wet grinding dry burning It has advantages of easy to Cement Production Process Cement Manufacturing Process AGICO CEMENT2019年9月12日 Various types of cement are currently available in the market Cement can be characterized as hydraulic and nonhydraulic Nonhydraulic cement doesn’t set in wet conditions or underwater Instead, it sets because it dries and reacts with Carbon dioxide in the airWhat is Cement Definition, Properties and Types Civil GyanWilliam Aspdin made what could be called ‘mesoPortland cement‘ (a mix of Portland cement and hydraulic lime)Isaac Charles Johnson further refined the production of ‘mesoPortland cement’ (middle stage of development), and claimed to be the real father of Portland cement In 1859, John Grant of the Metropolitan Board of Works, set out requirements for cement to be used in What is the manufacturing process of Portland Cement?
.jpg)
Cement Grinding Plant Overview Cement Grinding
Cement grinding process The whole workflow of the cement grinding plant is as follows: the cement clinker, gypsum, and mixture in the cement silo are mixed by the belt conveyor in a certain proportion and transported to the cement roller Maintenance in the cement industry is one of the contributors to the production cost and represent typical 15 of two main divisions, labor and material By achieving maximum availability (minimum downtime) and efficiency of the MAINTENANCE IN THE CEMENT INDUSTRYPortland cement was invented in 1824 by Englishman Joseph Aspdin and patented in 1825 The name comes from its similarity to the stone quarried on the Isle of Portland, Dorset, England Portland cement is one of the most widely Everything You Need to Know About Portland CementThe Cement Plant Operations Handbook SEVENTH EDITION The Cement Plant Operations Handbook is a concise, practical guide to cement manufacturing and is the standard reference used by plant operations personnel worldwide Providing a comprehensive guide to the entire cement production process from raw materialThe Cement Plant Operations Handbook International Cement
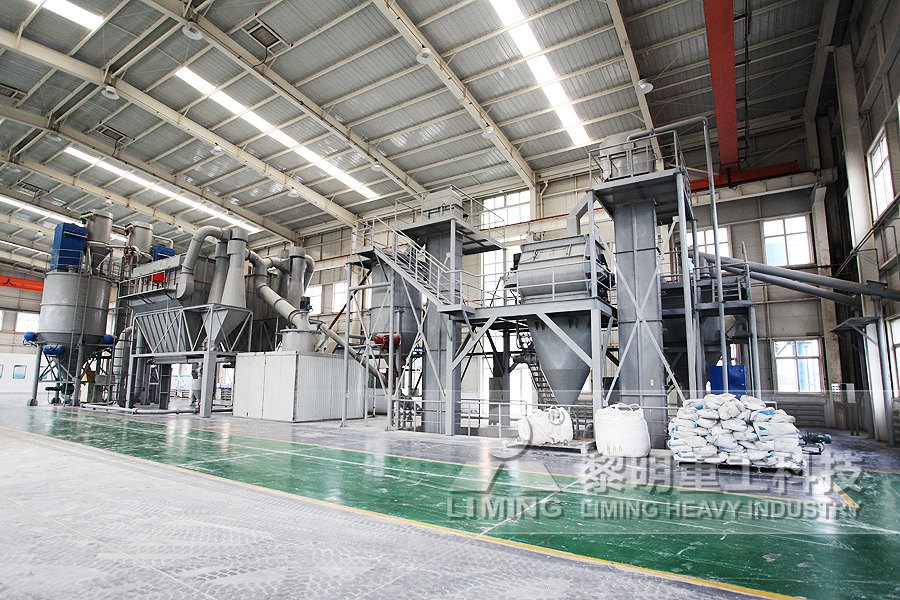
Cement Types of Cement Classification, Uses Dream Civil
2023年9月20日 Cement may be prescribed as a material with adhesive and cohesive properties which make it capable of bonding mineral fragments into a compact whole For constructional uses, the definition of the word cement is restricted to the bonding materials utilized with stones, sand, bricks, building blocks, etc The principal components of this type []2022年6月30日 How is Cement Made? The cement manufacturing process is a sequence of complicated steps that occur in cement manufacturing plants, also known as cement mills There are four main steps in the manufacturing process of Portland cement These steps include 1) Crushing and Grinding the Raw Materials 2) Blending the Materials in Correct ProportionsThe Manufacturing Process of Cement in Factory2022年2月1日 Perumal Jagatheesan, Safety Head, HeidelbergCement India and Zuari Cement, discusses the safety norms and standards at a cement plant, while underscoring the importance of training, safety protocols and practices and the use of technology at a cement plant How would you define a safe cement plant? What are the major areas of concern for safety []Safety is at the centre of everything that we do Indian Cement Wonder Cement is part of the RK Marble group which is one of the leading names in the marble industry Its cement plant produces cement in line with international quality standards The entire design of the plant is based on the latest environment norms, keeping emissions clearly below maximum permissible values ABOUT THE AUMUND GROUPCement handling storage the right equipment for the job
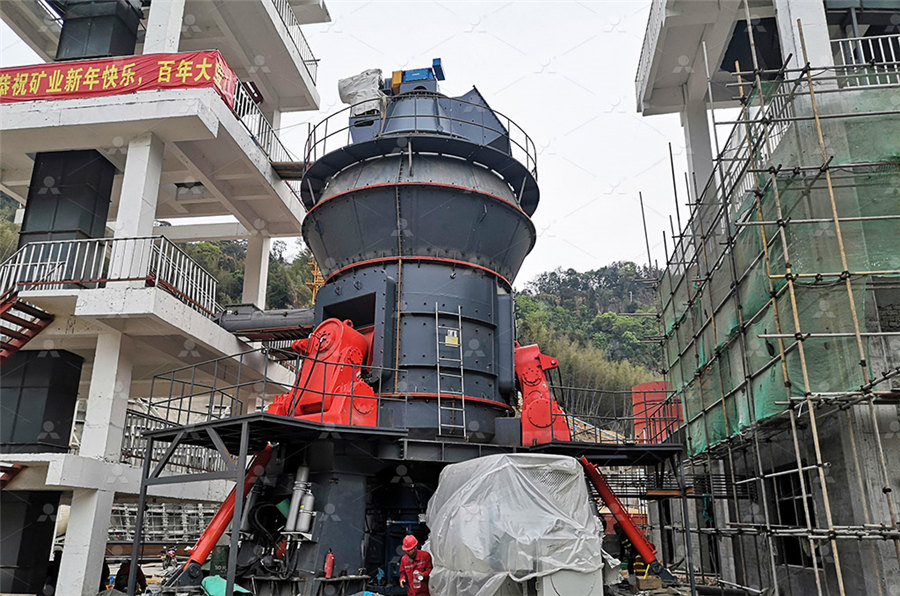
Primary and Secondary Crushing: Understanding the Basics A
2023年2月28日 Granite Crushing Plant; Projects Menu Toggle 500t/h Coal Gangue Mobile As the name implies, crushing is the process of reducing large materials into By understanding the basics of primary and secondary crushing, and by choosing the right crusher for the job, you can ensure a successful and profitable operation Share thisAs the meal passes through the burning zone, it reaches clinkering temperatures of about 1400 C 1500 C Nodules form as the burning zone is approached When the clinker has passed the burning zone, it starts to cool, slowly at first, then much more quickly as it passes over the 'nose ring' at the end of the kiln and drops out into the coolerManufacturing the cement kiln Understanding CementHow can I start a cement manufacturing plant? Starting a cement factory involves several crucial steps: Determine the scale of production and type of cement to be produced Choose an optimal location for the cement plant Design the layout StepbyStep Guide to the Manufacturing of Cement2024年9月5日 Tricalcium silicate (C₃S): this compound gives strength to the cement and hardening properties Dicalcium silicate (C₂S): Strengthens cement hardening over time (C₃A) Tricalcium aluminate: regulates cement setting A Comprehensive Guide to the Cement Manufacturing
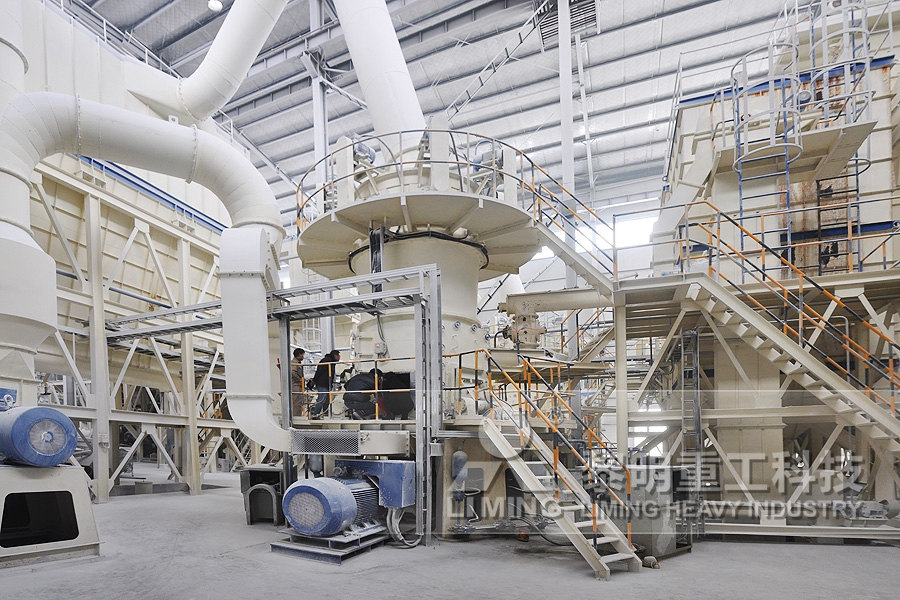
What is a Concrete Plant? (The Ultimate Guide) Plant4Harvest
2024年1月30日 The following steps describe how a concrete plant works: The cement, sand, gravel, and water are loaded into the plant The ingredients are mixed together in the mixer The concrete is discharged from the mixer and transported to the desired location The concrete plant is a vital piece of equipment for the construction industryIn short, if you need highvolume crushing capabilities and are looking to expand your business into more complex areas of crushing materials, then setting up a crusher plant is your best choice! All in all, setting up a full crushing plant offers greater flexibility, better efficiency and improved productivity rather than relying on a single crusher aloneCrushing plants what are they and how do I set one up?2023年7月10日 Cement manufacturing is a significant industrial activity that plays a vital role in the construction sector However, the process of cement production is associated with various environmental Cement Manufacturing Process and Its Environmental Impactto cement Extracting raw materials Crushing and transportation Raw material preparation I: Storage and homogenisation Raw material preparation II: Drying and raw grinding Burning The burning of the raw meal at approx 1,450°C is carried out in Lepol or preheater kilns that work by varying methods, theFrom raw materials to cement
.jpg)
What Is Primary, Secondary, and Tertiary Crushing?
2021年1月10日 Primary crushing is the first stage of material reduction and can sometimes be the only stage needed to generate the desired product for a job Depending on the setup, primary crushing will take the larger material that has been blasted, excavated, or reclaimed and process it through an impactor, jaw, or gyratory crusher to generate a range of product sizes3Stationary Concrete Batching Plant: Stable concrete batching plants are steady and situated in a long way from the construction site Concrete is transported to the construction site using a truck; steady concrete batching plants are simple to set up, they are bigger in dimension than cellular concrete batching plantsBatching Plant: Types, Advantages DisadvantagesThe cost of a concrete plant depends on several factors, such as the type of plant (stationary or mobile), production capacity, level of automation and additional features Generally, a small to mediumsized stationary concrete plant can cost anywhere from $200,000 to $1 millionOverview of Concrete Batch Plants: types, parts applications JEL 2020年9月14日 Step #4 The burning of the raw meal at approx 1,450°C is carried out in Lepol or preheater kilns that work by varying methods, the main difference being in the preparation and preheating of the kiln feed By chemical conversion, a process known as sintering, a new product is formed: clinker Step #5The essentials of electrical systems in cement plants EEP