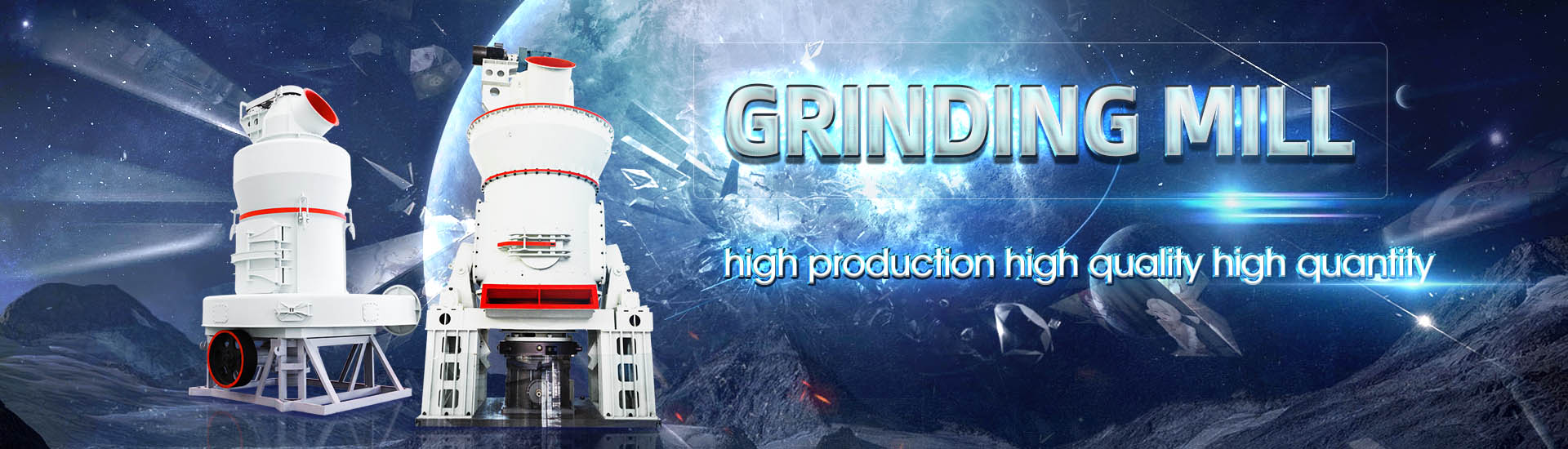
Process flow chart of cement vertical mill
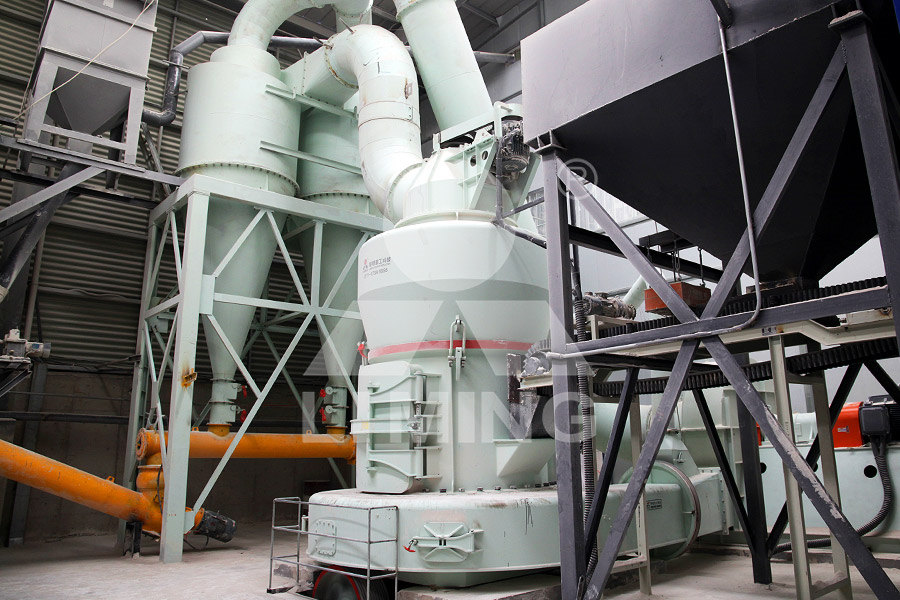
Vertical roller mill for raw Application p rocess materials
Fig Flow chart of roller mill adopting the external circulating system It depends on scale of facilities For example, about 820,000 US$ per unit At the beginning stage when vertical roller The core elements of these plants are the Loesche vertical mills for drygrinding the abovementioned grinding stock Loesche has developed and built the largest and most efficient PROCESS OPTIMISATION FOR LOESCHE GRINDING PLANTSFig2 Schematic process flow of vertical roller mill for grinding of raw materialsVertical roller mill for raw materialsAs can be seen in Fig 1 (Process and Quality flow diagram) above, there are around 8 quality check points where by different samples are taken at some time interval (every hour most of CEMENT PRODUCTION AND QUALITY CONTROL A Cement
.jpg)
(PDF) Performance Evaluation of Vertical Roller Mill in
2017年9月11日 In this study, an extensive sampling study was carried out at vertical roller mill of ESCH Cement Plant in Luxemburg Samples were collected from mill inside and around the circuit toThe different grinding processes of vertical mills compared to tubular ball mills have led to the development of a new generation of Cement Grinding Additives These products have been Technical Notebook CEMENT ADDITIVES FOR VERTICAL MILLSThe Cement Plant Operations Handbook is a concise, practical guide to cement manufacturing and is the standard reference used by plant operations personnel worldwide Providing a The Cement Plant Operations Handbook International Cement The cement production process 1 The Quarry: The cement production process begins with the extraction of limestone and clay from the quarry 2 Crusher and PreBlending: The material is A practical guide to improving cement manufacturing processes
.jpg)
SikaGrind® for vertical roller mills
The common intergrinding of limestone and clinker in classical ball mills is therefore producing a cement of very high surface The higher the limestone content, the higher the negative impact The following is a cement manufacturing process flow chart, The cooled clinker is ground into a fine powder, known as cement, in a cement mill Addition of Gypsum: Gypsum is added to control the setting time of the cement, and the Wet Process Of Cement Manufacturing With Flow Stage of Cement Manufacture There are six main stages of the cement manufacturing process Stage 1: Raw Material Extraction/Quarry The raw cement ingredients needed for cement production are limestone (calcium), sand and clay (silicon, aluminum, iron), shale, fly ash, mill scale, and bauxite The ore rocks are quarried and crushed into smaller pieces of about 6 inchesHow Cement is Made Cement Manufacturing ProcessCement and Concrete Testing Laboratory (VCCTL) 7 Calorimetry – 8 Burnability – 9 Grindability – 10 Physical testing – 11 Process control analysis – 12 Chromate passivation – 13 Cement quality – 14 Setting time – 15 ASTM cement types and specifications – 16 European EN 197 cement specification – 17 Composite cementsThe Cement Plant Operations Handbook International Cement
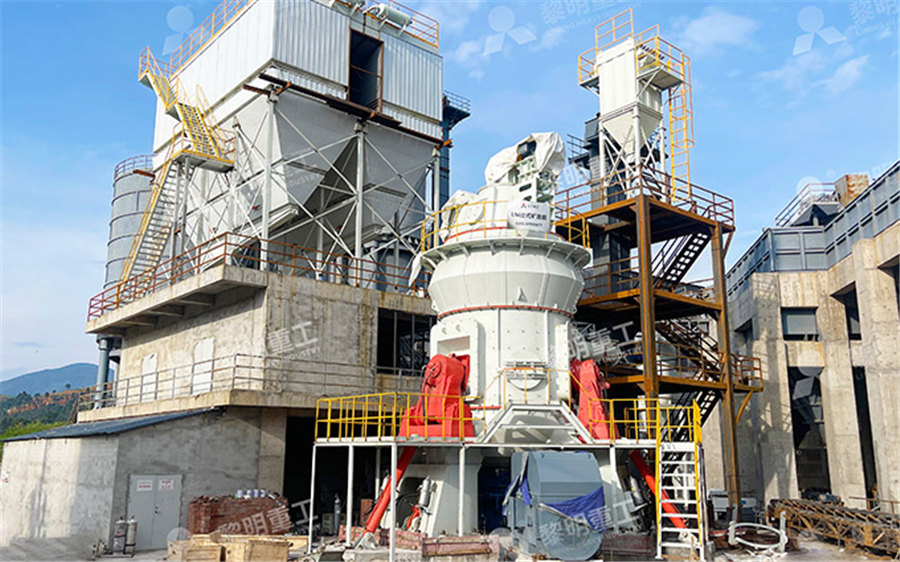
Manufacturing of Portland Cement – Process and Materials
5 天之前 Dry process, wet process, how ,cement production, cement plant Skip to content November 28, 2024 Facebook; Twitter; Wet process of cement manufacturing (Flow chart) sixstage preheater, and vertical roller mill The latest Technology with a modern control system includes stacker and reclaimer, online Xray analyzer, Cement making process – Raw materials, clinker, cement Steelmill scale 25 11 899 40 TYPICAL COMPOSITION OF RAW MATERIALS Kiln Process Thermochemical Reactions Process Reactions Temperature ºC free water evaporates 20 100 Drying/ PreheatCement Manufacturing2016年1月20日 The purpose of this study is to examine the material flow in a typical cement production process, The raw coal from the stockyard is crushed in a hammer crusher and fed to the coal mill The coal mill is a vertical roller mill, (13393 t/h) flow into the cement mill for grinding, and then elevated to the vortex classifierAnalysis of material flow and consumption in cement production process Burning: In this operation, the slurry is directly fed into a long inclined steel cylinder called a Rotary kilnIn this kiln there are 3 different zones shown in fig below Cement Manufacturing Process Flow Chart (i) Drying Zones: In the wet process, the drying zone is comparatively larger than the dry process It is because the raw material in slurry form is directly fed into the kiln Manufacturing of Cement By Dry and Wet Process Expert Civil
.jpg)
Modeling of energy consumption factors for an industrial cement
2022年5月9日 Modeling of energy consumption factors for an industrial cement vertical roller mill by SHAPXGBoost: a "conscious lab" approachThe vertical roller mill (VRM) is a type of grinding machine for raw material processing and cement grinding in the cement manufacturing processIn recent years, the VRM cement mill has been equipped in more and more cement plants around the world because of its features like high energy efficiency, low pollutant generation, small floor area, etc The VRM cement mill has a Vertical Roller Mill Operation in Cement PlantWhat Is Cement Vertical Mill The cement vertical mill is a type of grinding equipment that merges fine crushing, drying, grinding, and powder separating into a single, which simplifies the production process and has many irreplaceable advantages, such as high grinding efficiency, large feeding size, low power consumption (2030% less power than a cement ball mill), large Cement Vertical Mill Vertical Grinding Mill Vertical Mill2019年11月30日 Manufacture Of Portland Cement Process Flow chart – civil learners July 23, 2021 November 30, 2019 by Maruthi Baddi When the mill is rotated about its horizontal axis, the steel balls strike against the perforated Manufacture Of Portland Cement Process Flow
.jpg)
OPTIMIZATION OF CEMENT GRINDING OPERATION IN BALL MILLS
The consumption of energy by the cement grinding operation amounts to one third of the total electrical energy used for the production of cement The optimization of this process would yield substantial benefits in terms of energy savings and capacity increase Optimization of the Cement Ball Mill OperationThe cement production process 1 The Quarry: The cement production process begins with the extraction of limestone and clay from the quarry 2 Crusher and PreBlending: The material is then crushed to reduce particle sizes and blended to reduce variability in composition 3 Raw Mill and Kiln: Raw materials and additives areA practical guide to improving cement manufacturing processes In a rotary kiln system producing cement clinker, gas flows are countercurrent to material flows Gases enter the kiln as secondary air at about 600°C – 1100°C and rise abruptly to over 1750°C as heat from fuel combustion, and the exothermic heat of clinker formation are releasedCement Manufacturing Process INFINITY FOR CEMENT EQUIPMENT2023年6月1日 Scholars have studied the flow field characteristics of vertical mills Bhasker [5] described the meshing process of vertical mill fluid simulation and used the gas–solid twophase flow method to simulate the vertical mill and obtain the complete trajectory of the gas–solid twophase flow from the inlet to the outlet of the vertical millOperation parameters multiobjective optimization method of
.jpg)
Cement manufacturing process PPT Free Download SlideShare
2014年6月10日 Evolution of the cement Process • Wet process easiest to control chemistry better for moist raw materials • Wet process high fuel requirements fuel needed to evaporate 30+% slurry water • Dry process kilns less fuel requirements • Preheater/Precalciner further enhance fuel efficiency allow for high production ratesFinally, during the cement grinding and distribution process, firstly the cooled clinker is ground with around 5% of gypsum and other 17 JRTE2020 cementitious materials to form the final cement Typical cement manufacturing process flow diagram [4]2020年8月25日 A full cement production process includes the cement crushing process, raw mill process, clinker process, and cement grinding process, cement packing process, and related process Find more! Skip to content +86 s about cement ball mill and cement vertical mill are generally used in the raw meal Cement Production Process Cement Manufacturing Process AGICO CEMENTPROCESS DIAGNOSTIC STUDIES FOR CEMENT MILL OPTIMISATION CASE STUDY VK Batra*, • Tube mill with precrushing unit ie vertical shaft impactor (VSI) or horizontal impact crusher Mill vent flow : 972 m 3/min Separation air at separator outlet : PROCESS DIAGNOSTIC STUDIES FOR CEMENT MILL
.jpg)
Process flow diagram for the cement manufacturing process,
Download scientific diagram Process flow diagram for the cement manufacturing process, showing electricity and heat consumption or inputs [39] from publication: Energy Savings Associated with Cement temperature Outlet gas flow determined from mill inlet and outlet drafts or flow meters installed Vertical Roller Mills In Vertical Roller mill 2 4 Examples of these separators are OSepa (FLSmidth), Sepol (ThyssenKrupp) A simplified process flow these separators is as follows Material is fed onto a rotating dispersion Cement Grinding Cement Plant Optimization2015年9月17日 Cooler 01 Limestone Stockpile 10 Deep Bucket Conveyor 02 Additives Hopper 11/12 Clinker/Gypsum Storage 03 Additives Storage 13 Coal Mill Building 04 Raw Mill Building 14 Cement Mill and Bag House 05 Cement Production Process PPT SlideShareDownload scientific diagram CEMENT MANUFACTURING PROCESS FLOW CHART from publication: Industrial Geology ResearchGate, the professional network for scientistsCEMENT MANUFACTURING PROCESS FLOW CHART
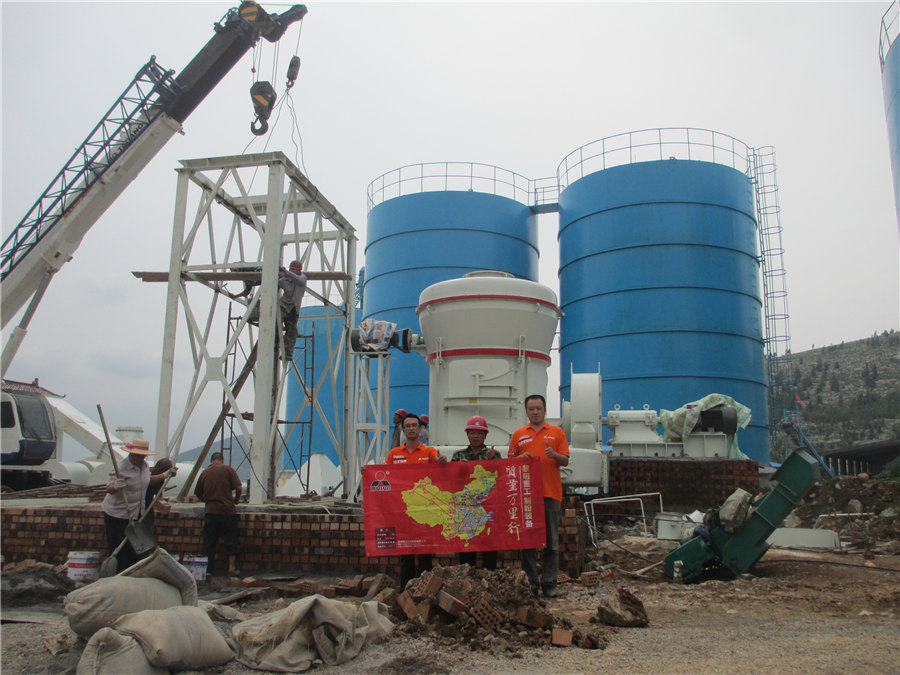
Process Flow Diagram of the Cement Plant ResearchGate
Download scientific diagram Process Flow Diagram of the Cement Plant from publication: Energy audit of thermal utilities in a cement plant Energy Audit and Thermal ResearchGate, the The use of fossil fuels such as coal, natural gas, and oil is common in cement production, both as a fuel for the kiln and as a source of heat for other parts of the process which leads to CO2 emitted by combustionHowever chemical reactions happening in the kiln (calcination) are also responsible for up to 60% of the total of emissions of the cement production process [PCA]Cement Production Demystified: StepbyStep Process and Vertical roller mills and ball mills represent two clearly distinct technologies However, with proper adjustments to the operational parameters of the vertical roller mill almost identical cement properties can be achieved by the two mills that satisfy the cement user’s demandsNevertheless, the two types of mills have their distinctive meritsCement grinding Vertical roller mills VS ball mills2020年11月5日 We compare 3 cement milling and cement mill processes, including cement ball mill, vertical roller mill, and rod mill Find your answer here! Skip to content +86 s about blog compared with the cement ball mill, there are also some defects such as long process flow, many links, large plant 3 Necessary Cement Milling Comparison Ball Mill, Vertical Roller Mill
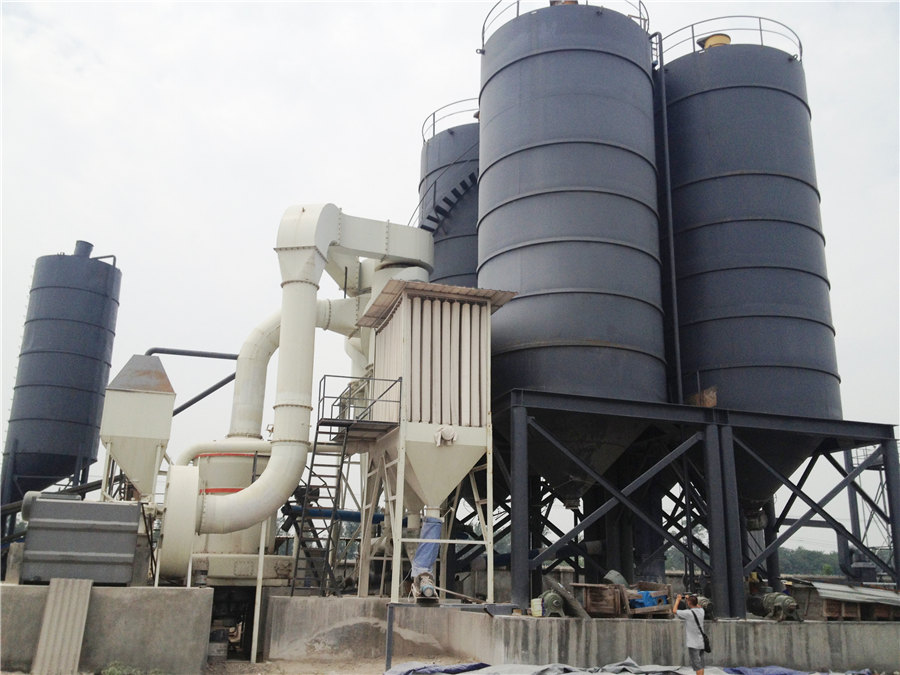
Vertical Cement Mill
The vertical cement mill is largescale cement grinding machine With advantages of energyefficient and stable quality, vertical roller mill is widely applied to many industries, such as cement, power, metallurgy, chemical and nonmetallic mining industry and etc As a typical type of Cement Mill, vertical cement mill set crushing, drying, grinding, grading transportation in one, it grind In recent years, Zimbabwe has experienced an increase in high energy demand and this brings the use of coal in generating electricity Coal fired power plants produces waste products during the coal burning process which are known as coal combustion residuals which includes 3% boiler slag, 24% flue gas desulphurization material, 57% fly ash and 16% pulverized coal ashFLOWCHART OF PROCESS USED IN MANUFACTURING OF CEMENT 2017年9月11日 In this study, an extensive sampling study was carried out at vertical roller mill of ESCH Cement Plant in Luxemburg Samples were collected from mill inside and around the circuit to evaluate the (PDF) Performance Evaluation of Vertical Roller Mill in Cement The following is a cement manufacturing process flow chart, The cooled clinker is ground into a fine powder, known as cement, in a cement mill Addition of Gypsum: Gypsum is added to control the setting time of the cement, and the Wet Process Of Cement Manufacturing With Flow
.jpg)
How Cement is Made Cement Manufacturing Process
Stage of Cement Manufacture There are six main stages of the cement manufacturing process Stage 1: Raw Material Extraction/Quarry The raw cement ingredients needed for cement production are limestone (calcium), sand and clay (silicon, aluminum, iron), shale, fly ash, mill scale, and bauxite The ore rocks are quarried and crushed into smaller pieces of about 6 inchesCement and Concrete Testing Laboratory (VCCTL) 7 Calorimetry – 8 Burnability – 9 Grindability – 10 Physical testing – 11 Process control analysis – 12 Chromate passivation – 13 Cement quality – 14 Setting time – 15 ASTM cement types and specifications – 16 European EN 197 cement specification – 17 Composite cementsThe Cement Plant Operations Handbook International Cement 5 天之前 Dry process, wet process, how ,cement production, cement plant Skip to content November 28, 2024 Facebook; Twitter; Wet process of cement manufacturing (Flow chart) sixstage preheater, and vertical roller mill The latest Technology with a modern control system includes stacker and reclaimer, online Xray analyzer, Manufacturing of Portland Cement – Process and MaterialsCement making process – Raw materials, clinker, cement Steelmill scale 25 11 899 40 TYPICAL COMPOSITION OF RAW MATERIALS Kiln Process Thermochemical Reactions Process Reactions Temperature ºC free water evaporates 20 100 Drying/ PreheatCement Manufacturing
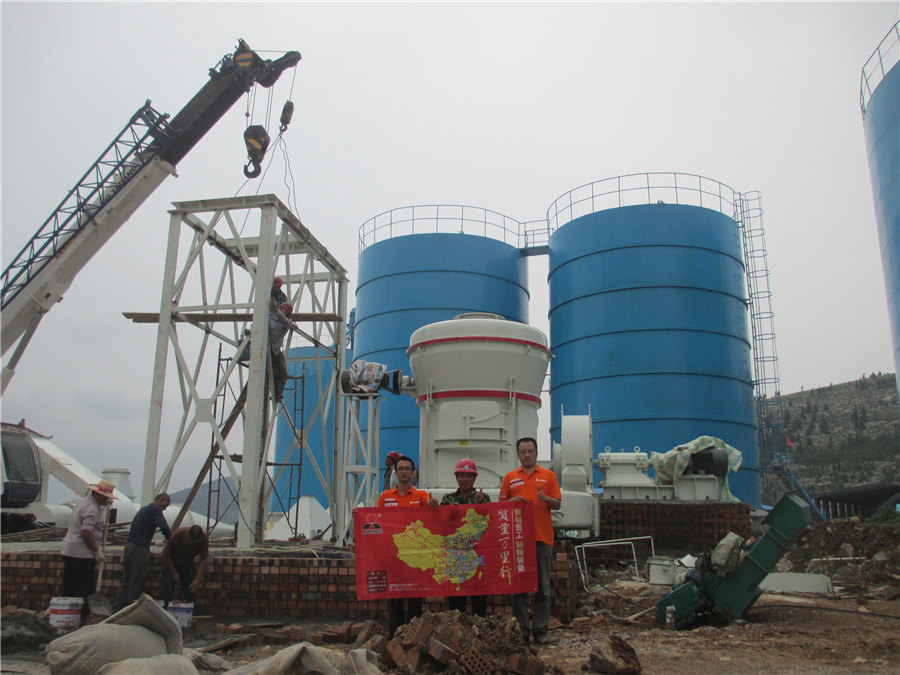
Analysis of material flow and consumption in cement production process
2016年1月20日 The purpose of this study is to examine the material flow in a typical cement production process, The raw coal from the stockyard is crushed in a hammer crusher and fed to the coal mill The coal mill is a vertical roller mill, (13393 t/h) flow into the cement mill for grinding, and then elevated to the vortex classifierBurning: In this operation, the slurry is directly fed into a long inclined steel cylinder called a Rotary kilnIn this kiln there are 3 different zones shown in fig below Cement Manufacturing Process Flow Chart (i) Drying Zones: In the wet process, the drying zone is comparatively larger than the dry process It is because the raw material in slurry form is directly fed into the kiln Manufacturing of Cement By Dry and Wet Process Expert Civil2022年5月9日 Modeling of energy consumption factors for an industrial cement vertical roller mill by SHAPXGBoost: a "conscious lab" approachModeling of energy consumption factors for an industrial cement The vertical roller mill (VRM) is a type of grinding machine for raw material processing and cement grinding in the cement manufacturing processIn recent years, the VRM cement mill has been equipped in more and more cement plants around the world because of its features like high energy efficiency, low pollutant generation, small floor area, etc The VRM cement mill has a Vertical Roller Mill Operation in Cement Plant
.jpg)
Cement Vertical Mill Vertical Grinding Mill Vertical Mill
What Is Cement Vertical Mill The cement vertical mill is a type of grinding equipment that merges fine crushing, drying, grinding, and powder separating into a single, which simplifies the production process and has many irreplaceable advantages, such as high grinding efficiency, large feeding size, low power consumption (2030% less power than a cement ball mill), large