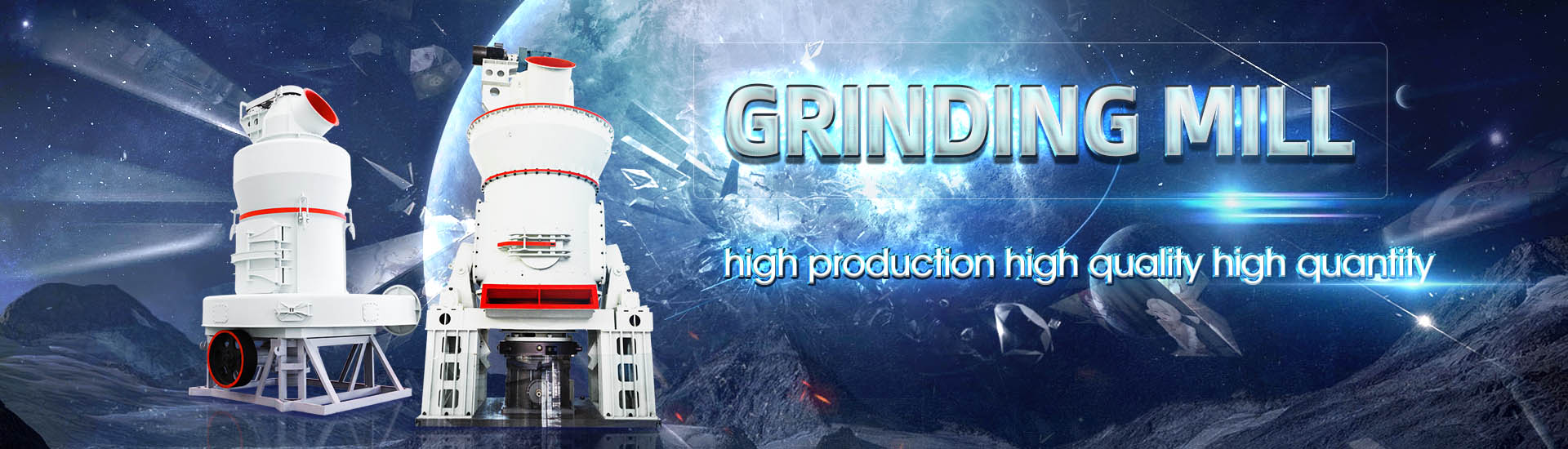
Raw Material Vertical Mill Installed
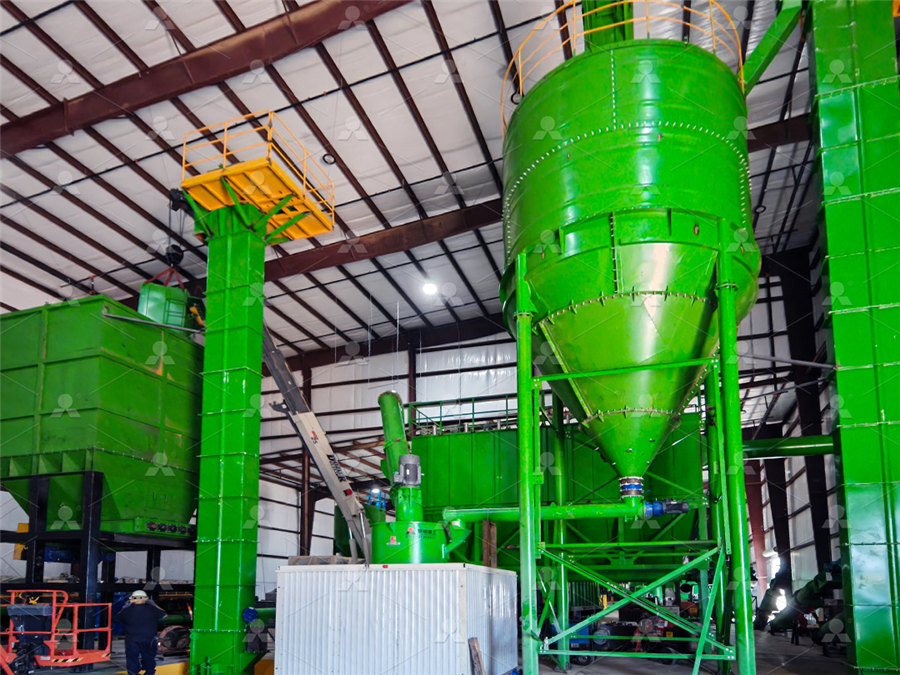
Vertical roller mill for raw Application p rocess materials
Vertical roller mills are adopted in 20 cement plants (44 mills) in Japan In the vertical roller mill which is widely used in the raw material grinding process, raw materials input grinding table Our bestinclass OK™ Mill is a globally successful vertical roller mill solution for grinding raw material, cement and slag Its cuttingedge design features consistently deliver the highest quality products with the greatest efficiency It Vertical roller mills FLSmidth CementUBE Vertical Mill is used for grinding of cement raw materials, coal, cement clinker, blast furnace slag and other materialUBE Vertical Mill UBE Machinery Corporation, Ltd1 A 5000t/d cement production line EPC turnkey project in South Africa adopts GRMR5341 raw material vertical mill of CHAENG 2 A 5000t/d cement production line in Henan, China adopts GRMR5341 raw material vertical mill of CHAENG 5000t/d cement production line of Henan Meng Electric Group adopts GRMR5341 raw material vertical mill of CHAENGVertical Raw Mill CHAENG
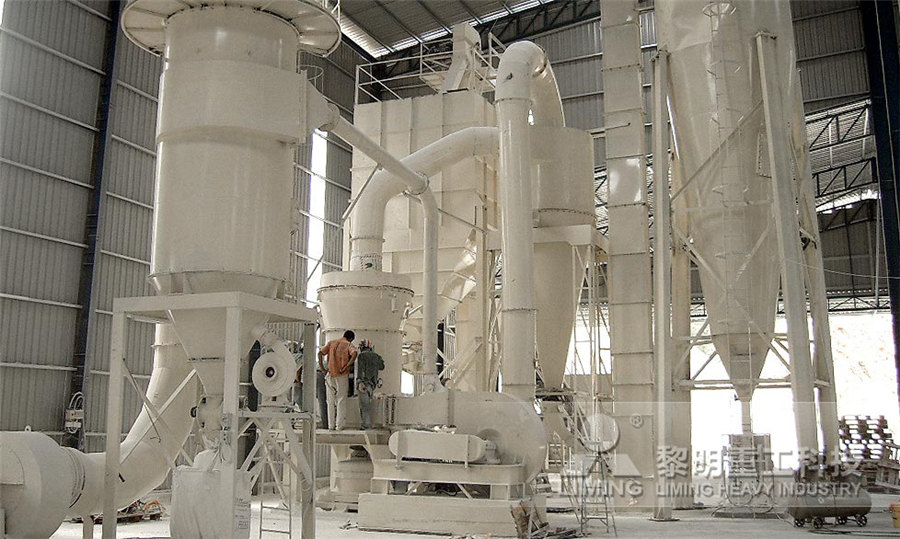
Vertical raw mill Cement Plant
Vertical raw mill is one kind of raw mill, generally used to grind bulk, granular, and powder raw materials into required cement raw meal in the cement manufacturing plantVertical raw mill is an ideal grinding mill that crushing, drying, grinding, THE CUSTOMER PROFILE M/s Chettinad Cement Corporation Limited (CCCL), An Indian Rs 85 Billion business group is into Manufacturing (Cement, Silica, Quartz, Grits) Services (Construction, Transports, Ship Management, Raw Mill – Kiln Application in Cement Industryvertical planetary gear reducer At the same time, raw material is dried by hot gas induced through the louver ring installed at outer side of the table Construction This Machine is a vertical type roller mill which performs drying grinding classification and pneumatic transportation simultaneously Material is fed at aVERTICAL ROLLER MILLS AMCL2021年1月22日 In the whole process of cement production, the electricity consumption of a raw material mill accounts for about 24% of the total Based on the statistics of the electricity consumption of the raw A Survey and Analysis on Electricity Consumption of Raw Material Mill
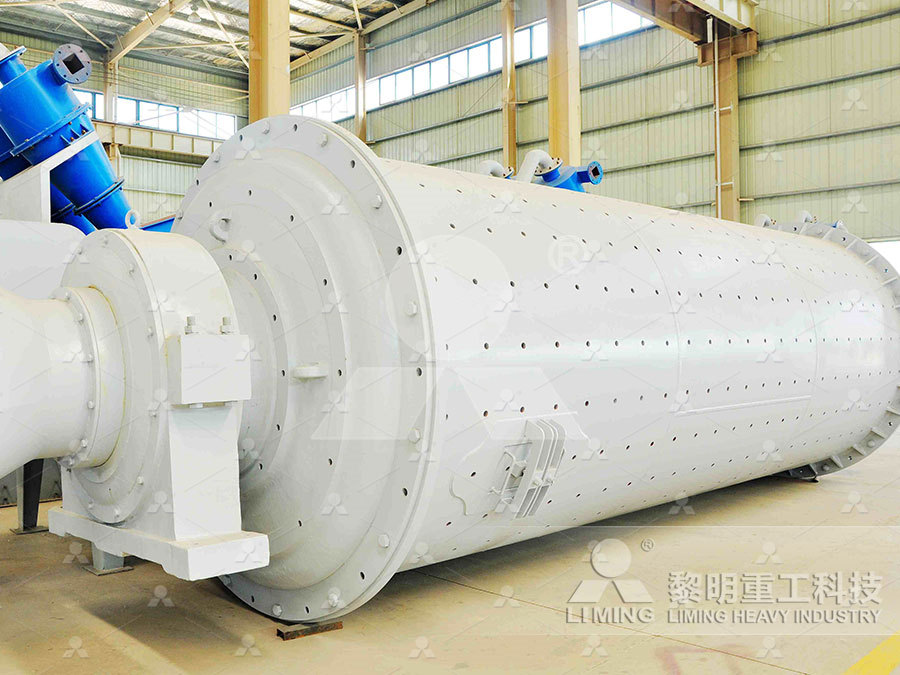
Raw Material DryingGrinding Cement Plant Optimization
Dry Grinding: Open circuit Ball mill, closed circuit Ball mill, vertical roller mill, Roll Press or Roll press in circuit with ball mill However, it would be seen that the most significant process and types used for raw material grinding operations in modern cement industry are: Process: Dry Closed circuit drygrinding Type of mill: Ball and 2021年1月1日 Stacking Reclaiming of Raw material: Swing type stacker Reclaimer: Limestone other raw material are stored in open area into a longitudinal storage unit called stockpile through Stacker These are then extracted transversely from the stockpile through reclaimer: 3: Raw Meal Grinding Homogenization: Grinding Mill Vertical Roller Mill Review on vertical roller mill in cement industry its 7Feed sluice ensures air flow and steady feed flow for minimum power consumption and optimum mill production 8The raw mill is easily adaptable to grind wet materials Specifications Note: mill spectral pattern benchmark 1Material medium friction (MF)=09~10; 2Material moisture max 7%; 3Refined powder granularity 80μmR 12~15%;Raw Material Vertical Roller MillThis mill, designated the LM 606 has a grinding table with a diameter of 600 m and an installed drive rating of 4 650 kW Even with poor grindability of the raw material this mill is expected to produce an output of 640 t/h at a raw meal fineness corresponding to a residue of about 15 % on a 009 mm sieve The first Loesche mill equipped with sixRedundancy and interchangeability – large vertical roller mills
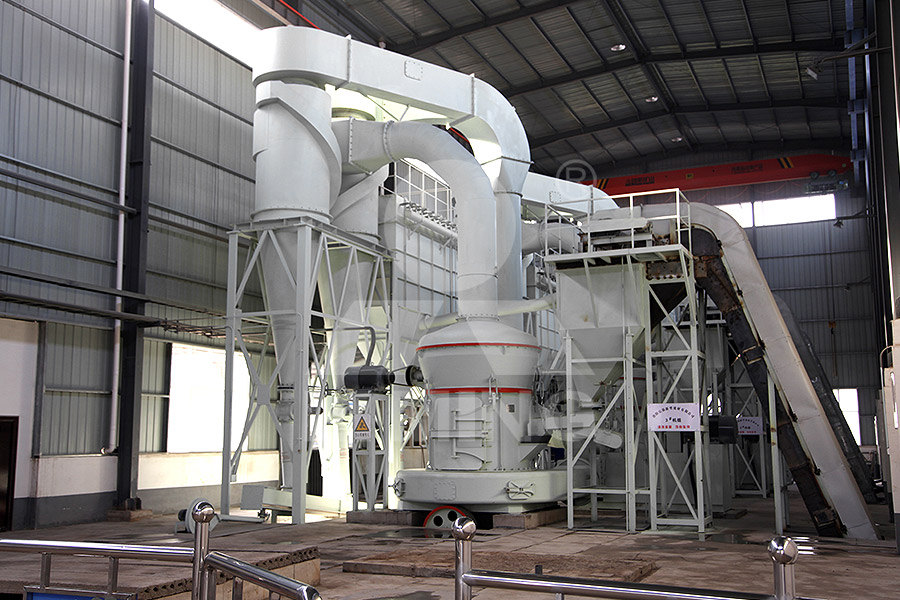
OK RAW AND CEMENT MILL
available for raw grinding, ensure the ability to meet all possible capacity requirements in a single mill even for the hardest materials The wellknown reputation of the OK mill as a reliable machine that is easy to operate and maintain continues with the OK raw mill In addition to the roller design features, the OK mill retains the abilityVertical Roller SINOMALY produces cement raw material grinding mills in various specifications These machines are suitable for grinding mill production lines with an output of 2500t/d, 3200t/d, 4000t/d, 5000t/d, 6000t/d and 8000t/d Vertical Roller Mill for Cement Raw MaterialThe Horomill used as a raw mill is claimed to combine the effectiveness of the vertical roller mill and the roller press with a very low pressure drop in the circuit It is also expected to offer some advantage in handling raw materials Everything you need to know about cement Materials raw material grinding, a modular vertical roller mill with 5 m table diameter and 4 rollers was added The existing kiln systems were partly modernized, one kiln system was replaced by new system Grinding Process Optimization Featuring Case Studies and
.jpg)
Vertical Cement Mill
With the incensement of moisture of the raw material, the powder consumption will decrease obviously The vertical mill saves 30%40% of energy consumption compared to the ball mill Vertical mill has less noise than ball mill, about 2025dB Besides, vertical mill adopt enclosed system, and works under negative pressure, no dust, clean 2022年10月3日 Vertical Raw Mill is a main equipment that is used in grinding or refining raw materials at PT Semen Baturaja (Persero) Tbk using a tire roller that can produce raw meal with the standard (PDF) ANALISA KINERJA ALAT VERTICAL RAW MILL PABRIK II PT 2014年4月1日 For decades vertical roller mills have been in use in the cement industry for the grinding of cement raw material and coal Since the 1980's this mill type has also been used for combined or (PDF) The latest innovative technology for vertical roller mills A raw material vertical mill external circulation system, comprising a proportioning belt conveyor (29), a feed elevator (30), a feed conveying mechanism (31), a feed tee coupling (32), a Vshaped powder concentrator (33), an external circulation vertical roller mill (37), a cyclone (38), a circulation draught fan (39), and a bag type dust remover (40)Raw material vertical mill external circulation system and process
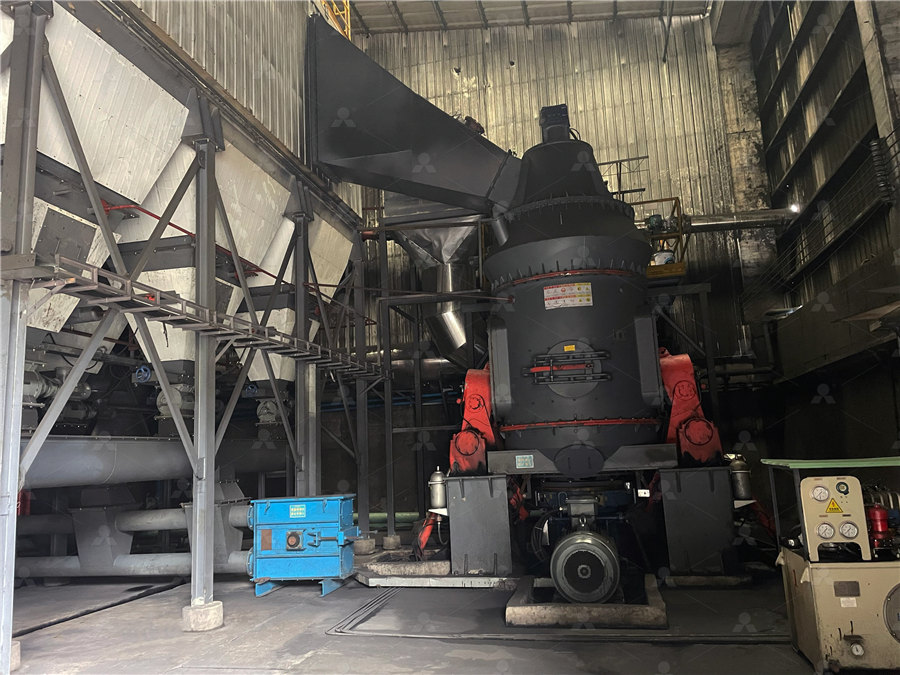
Best HLM Vertical Roller Mill Manufacturer and Factory
As the vertical roller mill works, the motor drives the reducer to rotate the dial, the raw material are delivered to the center of the dial from the air lock rotary feeder The material moves to the edge of the dial due to the effect of centrifugal force and than be ground by the force of the ro2010年11月1日 The new MVR vertical roller mill for grinding cement raw material, cement and granulated blast furnace slag has a modular design, which enables operation to be continued even if one roller module The new pfeiffer MVRR vertical roller mill for producing raw PROCESS TRAINING for operators of Vertical RAW Mills Heating of mill and grinding plant For drying the wet raw material it is necessary that prior to the mill start up the grinding plant isheated for some timeOtherwise the cold grinding plant would take away too much heat from the drying process and the finish product would not be dry PROCESS TRAINING for operators of Vertical RAW Mills1) Raw material batching and feeding: Limestone, raw coal and gravel coal are fed into the pulverized coal vertical mill through a quantitative feeder respectively: limestone, raw coal and gravel coal are placed in the auxiliary material News What is the process flow of vertical mill to
.jpg)
Vertical Raw Mill PENGFEI Group
It offers simplified processing flow, so the structure is compact Our PFRM range of vertical mill combines material crushing, drying, grinding and 5060% of that of ball mills, respectively Our vertical raw mill features low noise and low dust OK mill – the name says it all A complete size range, including the largest VRM available for raw grinding, ensure the ability to meet all possible capacity requirements in a single mill even for the hardest materials The wellknown reputation of the OK mill as a reliable machine that is easy to operate and maintain continues with the OK raw OK™ RAW MILLPart Three: Raw Mill Process of Raw Mill The proportioned raw material is feed first to a grinding mill In the mill, particles ground in to very fine sizes In the grinding unit, drying, grinding and mixing takes place simultaneously Hot gas from clinker burning unit is passed into the grinding unit to assist the drying and grinding processCement Manufacturing Process INFINITY FOR CEMENT EQUIPMENTThe advantages of the vertical roller mill include high grinding efficiency and low energy consumption For raw materials and cement clinker, the vertical roller mill is an excellent grinding solution due to its relatively low installation cost, ease of operation and maintenance, energy savings, and good product qualityVertical roller mill DARKO
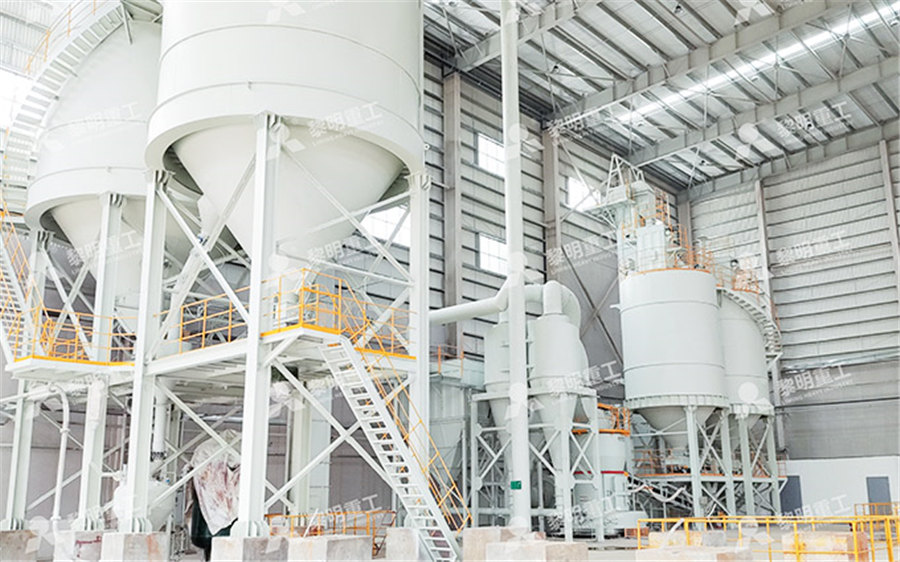
Review on vertical roller mill in cement industry its
2021年1月1日 For the past three decades the vertical roller mill has emerged to be the preferred choice for grinding raw materials With the grinding capacity of a vertical roller mill and the ability to dry, grind and sort in a single unit, the vertical roller mill offers a definite advantage over the ball mill system [10]As the vertical roller mill works, the motor drives the reducer to rotate the dial, the raw material are delivered to the center of the dial from the air lock rotary feeder The material moves to the edge of the dial due to the effect of centrifugal force and than be ground by the force of the roBest HLM Vertical Roller Mill Manufacturer and Factoryamount of raw material supplied, plus the system operates smoothly even with a low load 'As the raw material easily catches fire, the system is structured so that no coal is left in the system and an N2 purging unit is attached to the storage lank 'As the raw material has a low moisture content, the method of one川重商事株式会社2017年1月1日 7 CEM 6000 kW drive for a raw material mill FLSmidth on reference lists of the leading vendors in vertical mill sector, including to allow all drives to be installed (PDF) Drives for large vertical roller mills ResearchGate
.jpg)
A Survey and Analysis on Electricity Consumption of Raw Material Mill
2021年1月22日 In the whole process of cement production, the electricity consumption of a raw material mill accounts for about 24% of the total Based on the statistics of the electricity consumption of the raw material mill system of 1005 production lines in China between 2014 and 2019, it is found that the average electricity consumption of the raw material preparation Raw mill is generally called cement raw mill, raw mill in cement plant, it refers to a common type of cement equipment in the cement plantIn the cement manufacturing process, raw mill in cement plant grind cement raw materials Raw mill Cement PlantAGICO Cement Vertical Mill AGICO Cement Ball Mill Cement Vertical Mill Grinding System Cement vertical mill, also called roller mill, is another raw mill commonly used in cement pared with the cement ball mill, it has a Raw Mill – Raw Mill In Cement Plant AGICO Cement 2023年10月3日 Unveiling the Vertical Roller Mill In the everevolving world of industrial machinery, vertical roller mills (VRMs) have gained immense popularity for their efficiency and versatility This powerful milling machine is used across various industries, including cement, mining, and chemicals, to grind raw materials and achieve finely ground productsWhat is a vertical roller mill (VRM)? A Comprehensive Guide to
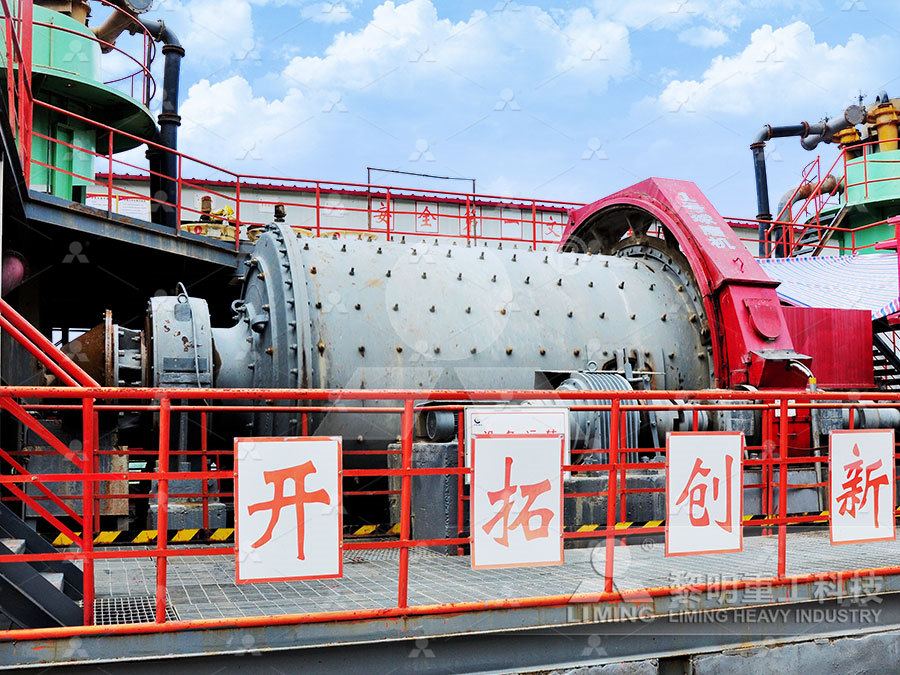
Raw mills for all requirements Gebr Pfeiffer
The cement raw material mixtures are ground, dried, and classified in the Pfeiffer vertical roller mill For drying the material, hot gases are directed into the mill Product fineness can be adjusted within a wide range (0063 to 02 mm)OptimizationofVerticalRawMillOperationpdf Free download as PDF File (pdf), Text File (txt) or view presentation slides online The document discusses optimization and operation of vertical roller mills (VRMs) Key points include: 1) Continuously monitor and adjust process parameters to find the optimum operating conditions of highest capacity and lowest power consumptionOptimization of Vertical Raw Mill Operation PDFFirst vertical mill for cement grinding Gebr // In 1864, company founder Jacob Pfeiffer had a vision of grinding mineral raw materials on a large scale This idea became reality Today the company looks back on a longtime success story of developing the most modern mill technologies vertical mills installed worldwide 26PASSION FOR GRINDINGClassroom Training General Installation for LOESCHE Raw Material Mill BENI SUEF CEMENT CO LM 464 Presented by David Salt – Senior Installation Supervisor trainingcenter@loesche loesche ©Classroom Training Installation LOESCHE vertical mill
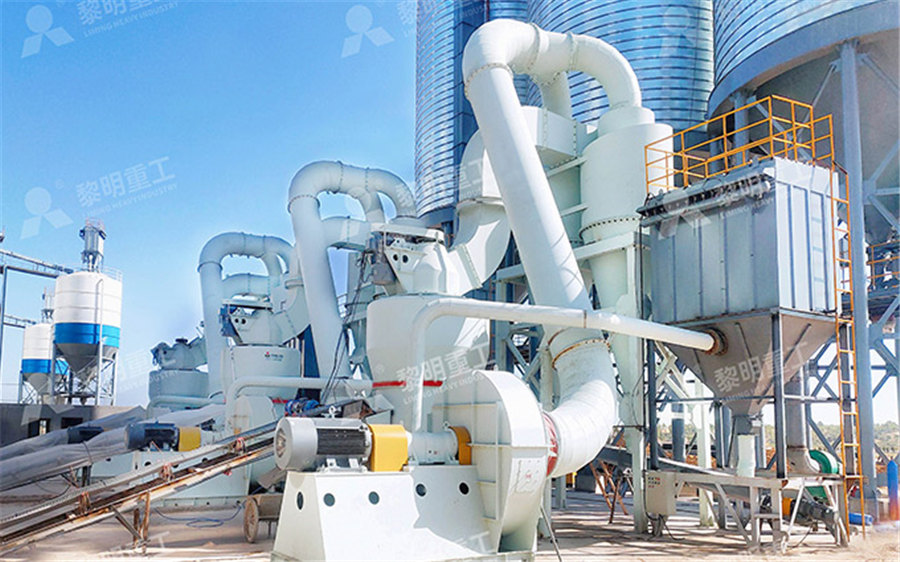
quadropol® thyssenkrupp Polysius Grinding Technologies
In addition, the raw material grinding process will be supported by a QMR² 48/24 For the 4,000 tons per day kiln line Shiva Cement Ltd contracted a quadropol® vertical roller mill for grinding pet coke with a QMK² 32/16 The same mill size QMK² 32/16 is running in Indonesia for years now, grinding and drying lignite// When grinding raw material, cement and granulated blastfurnace slag, what’s the point? Maximum throughput and utmost technical availability! This is ensured by the Pfeiffer MVR vertical mill with its revolutionary MultiDrive® With a drive power of up to 18,000 kW, throughput rates of more than 1,400 t/h can be reached on a single millPFEIFFER VERTICAL MILL WITH MULTIDRIVE MORE POWER2017年1月1日 The MVR vertical roller mill with an installed power of up to 18000 kW offered by the Operational results of the MVR 6000 R6 mill for raw material grinding THE MOST COMPETITIVE WAY Of (PDF) Case studies and operational results of modern MVR vertical