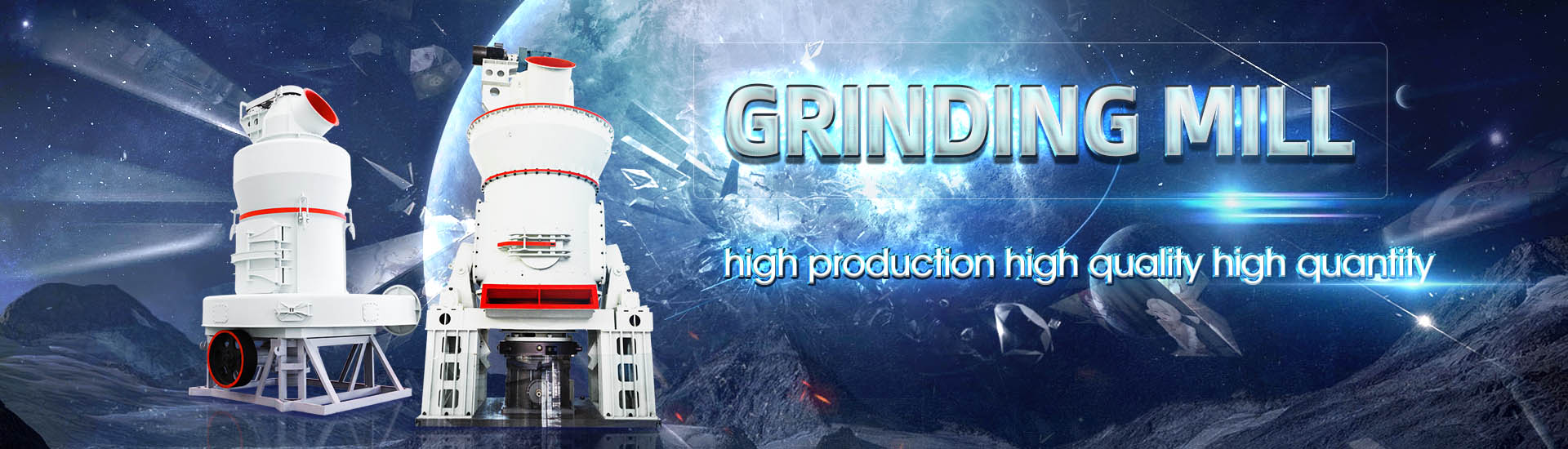
Laterite nickel powder making process
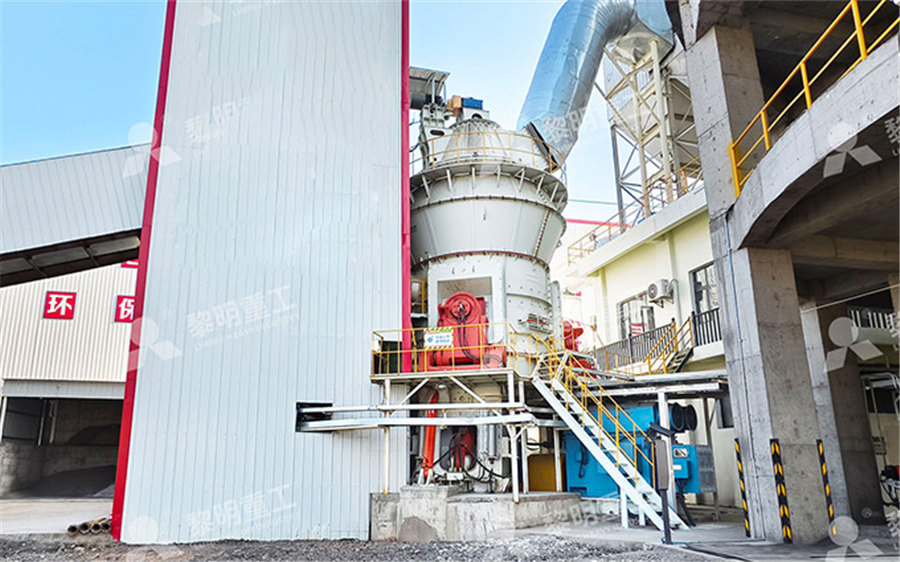
Nickel industry Part 2 Processing nickel laterites and smelting
2024年8月7日 The two main processing methods for laterite ores are smelting and HighPressure Acid Leaching (HPAL) Smelting is used primarily on saprolite ores to obtain an ironnickel alloy (ferronickel – FeNi, Nickel Pig Iron – NPI) while HPAL is used primarily to process Ore is often processed near the mine site, but there is substantial regional and Nickel industry Part 1 Proc2024年5月3日 Ore is often processed near the mine site, but there is substantial regional and global trade in nickel laterite ores, and some trade in nickel sulfide concentrates Laterite ores occur as surface deposits and are traditionally Nickel industry Part 1 Processing nickel laterites and 2019年9月3日 Industrially, the pyrometallurgical treatment of laterites is mostly accomplished with a wellestablished method, namely, the rotary kiln–electric arc furnace (RKEF) process, (PDF) Nickel Laterite Smelting Processes and Some ResearchGate
.jpg)
Review on hydrometallurgical processing technology of lateritic
Current technological schemes for the production of nickel and cobalt using combined manufacturing processes are presented, as well as the results of scientific research on 2002年8月1日 A greenfield laterite processing operation to produce nickel cathodes via electrowinning, and recover electrowon copper and cobalt sulphide as byproducts was Nickel laterite processing and electrowinning practice2019年9月3日 Industrially, the pyrometallurgical treatment of laterites is mostly accomplished with a wellestablished method, namely, the rotary kiln–electric arc furnace (RKEF) process, which includes three main operations—calcination, Nickel Laterite Smelting Processes and Some Examples Primary world nickel production in 2020 was 24307 kt Ni; 69% (16777 kt) of them came from oxidized nickel ores (laterites) and 31% from sulfides Productionwise, 877% of the 16777 kt came from pyrometallurgical and The Nickel Production Methods from Laterites and the
.jpg)
Advances and Innovations in FerronickelMaking
2023年1月19日 Based on a detailed overview of nickel utilization from laterite ores, it provides the advances of four main methods for laterite ore processing, including the solidsate reductionmagnetic separation process, the rotary kiln The CESL Nickel process for sulphide concentrates has been adapted to treat pressure leach solution from laterite ores and offers an alternative to the existing flowsheetsTHE APPLICATION OF THE CESL NICKEL PROCESS TO LATERITES2020年7月30日 Nickel laterites as sources of nickel, cobalt and scandium: Increasing resource efficiency through new geochemical and biological insightsNickel Laterites: From Exploration to Processing ScienceDirectThere is no essential difference between the traditional blast furnace iron making process and producing low nickel pig iron from laterite ore The main process is crush and screening of nickel also be reduced into the nickel powder[8] Laterite Nickel Ore Mining Raw Ore Drying CaO Coke Powder CaCO 3 Coke Sintering Blast Furnace Smelting LCA EVALUATION FOR DIFFERENT TREATMENT PROCESSES OF NICKEL LATERITE
.jpg)
Nickel Laterite Smelting Processes and Some
2019年9月3日 The treatment of laterites has been a research hotspot in extractive metallurgy over the past decades Industrially, the pyrometallurgical treatment of laterites is mostly accomplished with a wellestablished method, 2022年8月22日 Laterite ore contributes to about 70% of the world’s landbased nickel resources Hydrometallurgical techniques such as heap leaching (HL), atmospheric leaching (AL), highpressure sulfuric acid leaching (HPAL), Caron process, and direct nickel process (DNi) are the most common processes to treat lateritic ore Recent Progress in Hydrometallurgical Processing of Nickel 2023年1月19日 Dong J, Wei Y, Zhou S et al (2018) The effect of additives on extraction of Ni, Fe and Co from nickel laterite ores JOM 70:2365–2377 Article Google Scholar Guo X, Li D, Park KH et al (2009) Leaching behavior of metals from a limonitic nickel laterite using a sulfation–roasting–leaching processAn Overview of Nickel Utilization from Laterite Ore2021年12月2日 A new process of extracting silica from laterite nickel ore by hydrothermal treatment with sodium hydroxide as reaction auxiliary agent was proposed The mineralogical transformation and silicon extraction kinetics of laterite nickel ore in alkaline hydrothermal treatment were studied The effects of reaction temperature (175 ~ 250℃), molar ratios of Alkaline Hydrothermal Treatment and Leaching Kinetics of Silicon
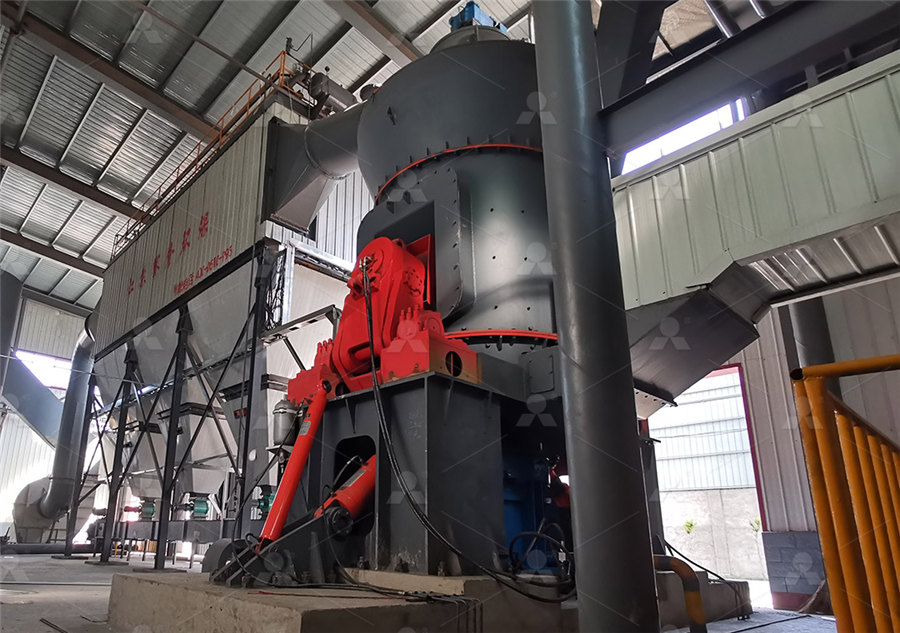
Nickel laterite processing and electrowinning practice
2002年8月1日 The 2001 Inco Limited production amounted to 457 and 256 million pounds of nickel and copper respectively The main production facilities in the Sudbury Region accounted for an output of 210 M lbs during the year 2001The balance of 2001 nickel production included 136 M lbs from PT Inco and 111 M lbs from ThompsonInco's Manitoba Division electrolytically PDF On Mar 11, 2019, Sait Kursunoglu and others published Hydrometallurgical Processing of Nickel Laterites—A Brief Overview On The Use of Solvent Extraction and Nickel/Cobalt Project For The (PDF) Hydrometallurgical Processing of Nickel Laterites—A 2023年1月19日 Based on a detailed overview of nickel utilization from laterite ores, it provides the advances of four main methods for laterite ore processing, including the solidsate reductionmagnetic separation process, the rotary kiln reductionelectric arc furnace smelting process, the KruppRenn process, and the sinteringblast furnace smelting processAdvances and Innovations in FerronickelMaking SpringerLinkUsing the direct nickel process (DNP), nickel ores are leached with nitric acid at 110 °C under atmospheric pressure in agitation tanks The Direct Nickel Group of Australia, which processes Indonesian laterite ores, created the process The duration of leaching is 2–4 h and the recovery of nickel and cobalt is more than 95%Bioleaching of Lateritic Nickel Ores SpringerLink
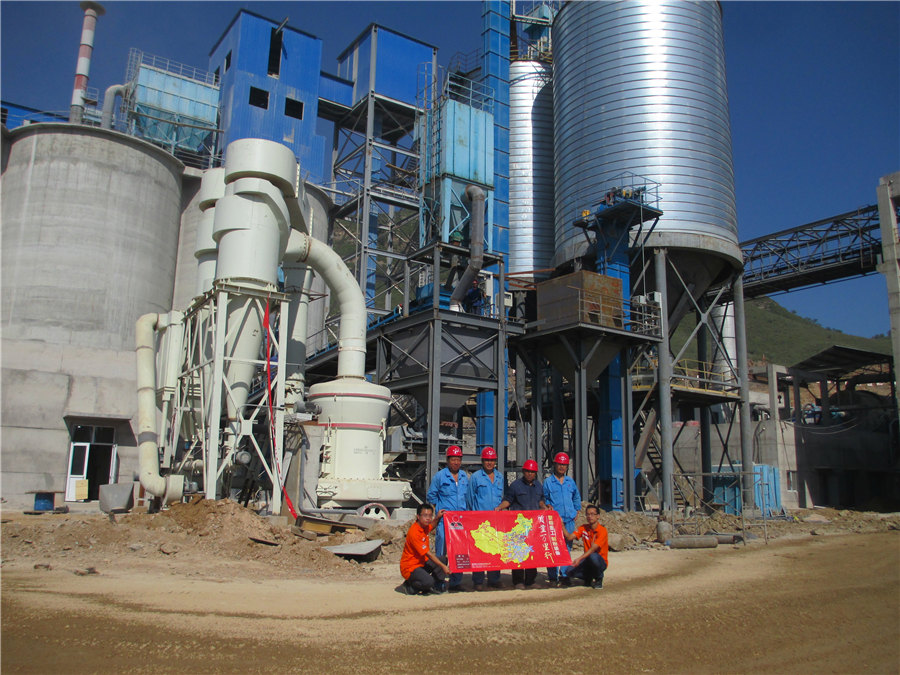
Processing of Nickel Laterite Ores on the Rise FEECO
While sulfide nickel ores are processed via upgrading to concentrates and then smelting, this approach is not applicable to laterite ores A variety of approaches are available to process nickel laterite ores, with the most prevalent approaches explained below The method(s) chosen is dependent on the composition of the unique ore source2024年9月1日 Nickel resources in Australia are laterite nickel (69%) and nickel sulfide (31%), mainly in Western Australia (90%), Queensland (5%) and New South Wales (4%) [46] Scandiumrich laterite deposits have been found in New South Wales and Queensland in eastern Australia, and scandium reaches concentration values up to 800 gt −1 in the Sunrise project [ 47 , 48 ]Hydrometallurgical process and recovery of valuable elements for 2021年8月23日 Lowgrade saprolite nickel laterite, characterized by complicated minerals composition and finegrained and complex dissemination, was commonly treated with a low recovery efficiency of Ni and Fe by conventional methods Hence, an improved direct reduction and magnetic separation process was proposed Meanwhile, the mechanisms on the Upgrade of nickel and iron from lowgrade nickel laterite by 2022年4月29日 In order to improve the recovery ratio of valuable metals in stainless steel dust, reduce environmental pollution, and promote solid waste resource recovery and sustainable development of industry, the synergistic reduction process for preparing Fe–CrNiC alloy was studied in detail by changing the addition of laterite nickel ore and reduction process A novel process for preparing Fe–CrNiC alloy: synergetic

The Great Laterite Challenge: Why Scaling Class 1 Nickel
2021年1月18日 New sulfide deposits will continue to be discovered in the years ahead, but not nearly at the pace necessary to keep up with batterydriven demand For better or for worse, the future of Class 1 nickel supply is very much dependent on these known yet undeveloped limonitic laterite deposits being successfully commercialized Nickel Laterite Overview2024年1月1日 The nickel laterite in upper layer of the ore deposit, with higher content of iron (Fe) and lower content of silica (SiO 2) and magnesium (Mg) in general, belongs to the limonite type, and usually contains lower nickel of about 1%, but a certain amount of cobalt (Co), while the nickel laterite in lower layer of the ore deposit, with higher content of silica (SiO 2) and Nickel Laterite Metallurgy SpringerLink2010年1月1日 A ferronickel powder with 65% to 80% nickel content, and 80% to 86% total iron grade was obtained from a sample of laterite ore with 158% nickel and 2207% iron; the recovery of nickel and iron A novel process for preparing ferronickel powder from laterite 2022年11月4日 Strict environmental regulations have made on many industrial sectors to try and reduce CO2 gas production, including the nickel and ferronickel manufacturing industries One of the promising technologies in reducing CO2 emissions is carbothermic reduction using a lower operating temperature than smelting process This study aims to study the effects of adding Effect of Inner Reductant Addition and Laying on Carbothermic
.jpg)
Nickel Laterites—Mineralogical Monitoring for Grade Definition
2021年10月24日 Dendrogram after cluster analysis based on the correlation matrix from 40 nickel laterite samples (cluster 1 = orange, cluster 2 = yellow, cluster 3 = light green, cluster 4 = dark green), Xaxis 2011年5月1日 Therefore, research in hydrometallurgical processing of laterite nickel ores has been vibrant, at least in the last three decades, resulting in many new technological development such as Recent Developments in the Chloride Processing of Nickel Laterites2020年11月5日 Nickel slags can be produced through ferronickel preparation by the pyrometallurgical processing of laterite nickel ores; however, such techniques are underutilized at present, and serious environmental problems arise from the stockpiling of such nickel ores In this study, a modification to the process of ferronickel preparation by the direct reduction of carbon Coupled Preparation of Ferronickel and Cementitious Material from various nickel laterite However, the high amount of water and gangue in laterite always need huge transport cost and energy consumption especially for the lower grade laterite ores4,5) In addition, more and more investments from Chinese enterprises have been attracted to the Southeast Asia to exploit the laterite mine, where is normally lack ofNovel Process of Ferronickel Nugget Production from Nickel Laterite
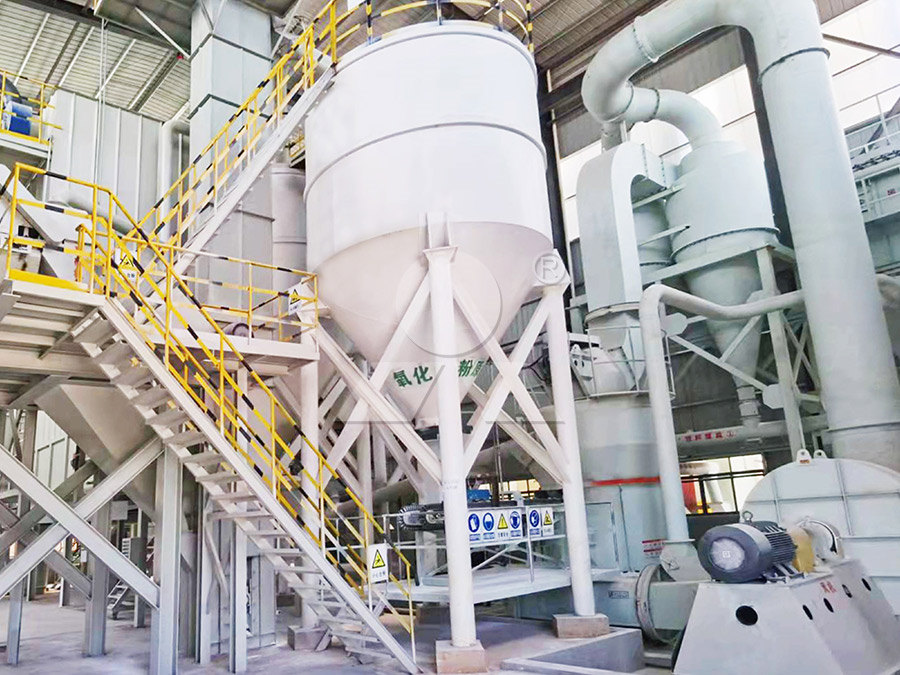
Selective Reduction of Laterite Nickel Ore JSTAGE
The examples of hydrometallurgical route for limonitic nickel laterite ore processing is High Pressure Acid Leaching (HPAL) 15 – 17) A number of hydrometallurgy processes have been applied in industrial scale, but this application cannot meet the need of production level and its operational cost was too high 16 – 19) In addition to the hydrometallurgical process, a Part 1 – Geology of nickel laterite deposits Geology of laterite profiles on ultramafic rocks The process referred to as “lateritisation” is essentially chemical weathering taking place inNickel laterite deposits – geological overview, resources and 2024年2月3日 Efficient extraction of nickel and cobalt from laterite ores is essential for the rapid development of new energy vehicles (EVs) In this work, Ni–Co–Fe powder with nickel, cobalt, and iron grades of 1198%, 118%, and 7013%, respectively, was obtained from a limonitic laterite ore via rotary kiln reductive roasting followed by magnetic separationPhosphoric Acid Leaching of Ni–Co–Fe Powder Derived from 2023年2月14日 This study provided a novel process of resource utilization of alloy powder on largescale and strengthened the limonitic laterite sintering process References Kim MS, Lee JC, Park HS, Jun MJ, Kim B (2018) A multistep leaching of nickelbased superalloy scrap for selective dissolution of its constituent metals in hydrochloric acid solutionsEfficient Utilization of Alloy Powder During Limonitic Laterite
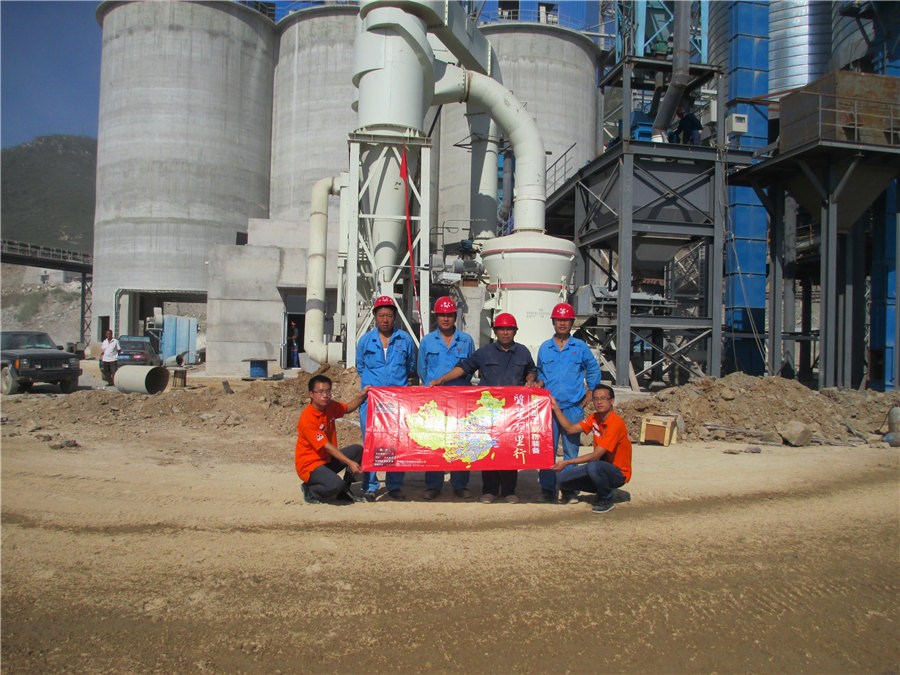
Making Ferronickel from Laterite Nickel Ore by CoalBased Self
2016年1月1日 Based on the process of coalbased selfreduction and melting separation at high temperature, it was investigated that the effect of process factors on the reduction of iron and nickel oxide, the 2017年8月16日 Nickel, a valued metal, mainly exists as nickel oxide in laterite nickel ore Furthermore, a large part of the laterite nickel ore is lowgrade saprolitic ore In this paper, a research on preparing ferronickel alloy from lowgrade saprolitic laterite nickel ore using metallized reductionmagnetic separation was studied In the research, the carbothermic Preparing FerroNickel Alloy from LowGrade Laterite Nickel Ore 2023年11月27日 How to reduce the energy consumption of the rotary kilnelectric furnace (RKEF) process has become an important issue for the stainless steel industry The aim of this study is to reduce the energy consumption of ferronickel production from saprolite nickel laterite in the RKEF process The effects of the slag binary basicity, FeO content, and Cr2O3 content on Enhancing Rotary KilnElectric Furnace Process of Saprolitic Laterite 2023年8月31日 The hydrometallurgical process of nickel laterite leaves a residue that still contains valuable elements Its utilization can improve overall process efficiency and reduce environmental damage(PDF) Valorization of Solid Residue from the Lateritic Nickel Ore
.jpg)
Effect of Inner Reductant Addition and Laying on Carbothermic
Table2 Chemical constituents of laterite nickel ore ElemNi Fe O Mg Al Si PSCa Cr Co wt% 125 5537 3149 042 504 194 020 067 046 154 162 Fig2 Xray graph showing compounds in laterite nickel ore of nickel sulfate powder both for nickelbased battery applications, chemicals, coating, and other applications 2 MaterialsandMethod 21 There is no essential difference between the traditional blast furnace iron making process and producing low nickel pig iron from laterite ore The main process is crush and screening of nickel also be reduced into the nickel powder[8] Laterite Nickel Ore Mining Raw Ore Drying CaO Coke Powder CaCO 3 Coke Sintering Blast Furnace Smelting LCA EVALUATION FOR DIFFERENT TREATMENT PROCESSES OF NICKEL LATERITE 2019年9月3日 The treatment of laterites has been a research hotspot in extractive metallurgy over the past decades Industrially, the pyrometallurgical treatment of laterites is mostly accomplished with a wellestablished method, Nickel Laterite Smelting Processes and Some 2022年8月22日 Laterite ore contributes to about 70% of the world’s landbased nickel resources Hydrometallurgical techniques such as heap leaching (HL), atmospheric leaching (AL), highpressure sulfuric acid leaching (HPAL), Caron process, and direct nickel process (DNi) are the most common processes to treat lateritic ore Recent Progress in Hydrometallurgical Processing of Nickel
.jpg)
An Overview of Nickel Utilization from Laterite Ore
2023年1月19日 Dong J, Wei Y, Zhou S et al (2018) The effect of additives on extraction of Ni, Fe and Co from nickel laterite ores JOM 70:2365–2377 Article Google Scholar Guo X, Li D, Park KH et al (2009) Leaching behavior of metals from a limonitic nickel laterite using a sulfation–roasting–leaching process2021年12月2日 A new process of extracting silica from laterite nickel ore by hydrothermal treatment with sodium hydroxide as reaction auxiliary agent was proposed The mineralogical transformation and silicon extraction kinetics of laterite nickel ore in alkaline hydrothermal treatment were studied The effects of reaction temperature (175 ~ 250℃), molar ratios of Alkaline Hydrothermal Treatment and Leaching Kinetics of Silicon 2002年8月1日 The 2001 Inco Limited production amounted to 457 and 256 million pounds of nickel and copper respectively The main production facilities in the Sudbury Region accounted for an output of 210 M lbs during the year 2001The balance of 2001 nickel production included 136 M lbs from PT Inco and 111 M lbs from ThompsonInco's Manitoba Division electrolytically Nickel laterite processing and electrowinning practicePDF On Mar 11, 2019, Sait Kursunoglu and others published Hydrometallurgical Processing of Nickel Laterites—A Brief Overview On The Use of Solvent Extraction and Nickel/Cobalt Project For The (PDF) Hydrometallurgical Processing of Nickel Laterites—A
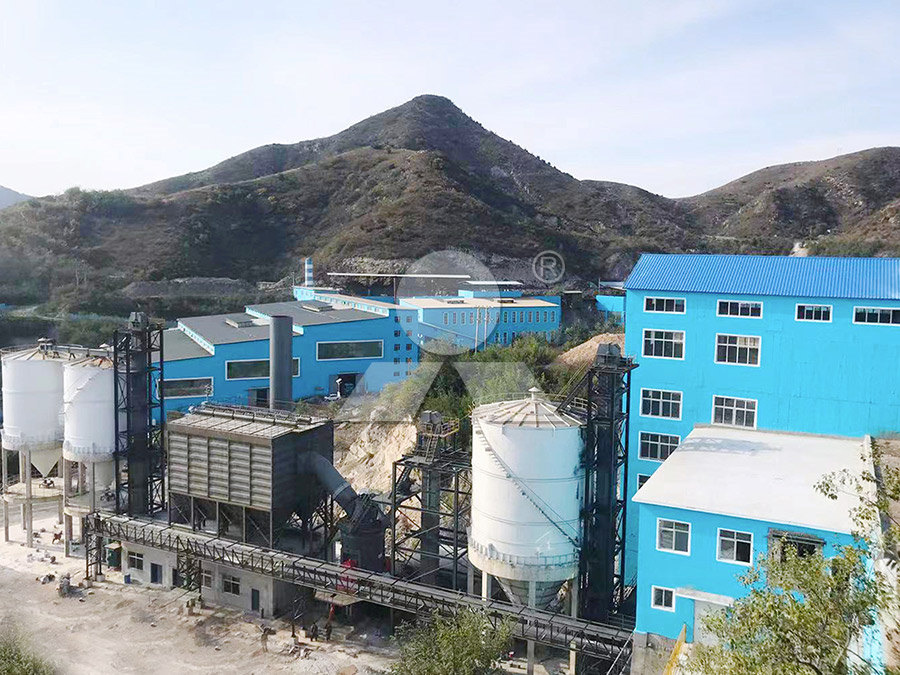
Advances and Innovations in FerronickelMaking SpringerLink
2023年1月19日 Based on a detailed overview of nickel utilization from laterite ores, it provides the advances of four main methods for laterite ore processing, including the solidsate reductionmagnetic separation process, the rotary kiln reductionelectric arc furnace smelting process, the KruppRenn process, and the sinteringblast furnace smelting processUsing the direct nickel process (DNP), nickel ores are leached with nitric acid at 110 °C under atmospheric pressure in agitation tanks The Direct Nickel Group of Australia, which processes Indonesian laterite ores, created the process The duration of leaching is 2–4 h and the recovery of nickel and cobalt is more than 95%Bioleaching of Lateritic Nickel Ores SpringerLinkWhile sulfide nickel ores are processed via upgrading to concentrates and then smelting, this approach is not applicable to laterite ores A variety of approaches are available to process nickel laterite ores, with the most prevalent approaches explained below The method(s) chosen is dependent on the composition of the unique ore sourceProcessing of Nickel Laterite Ores on the Rise FEECO