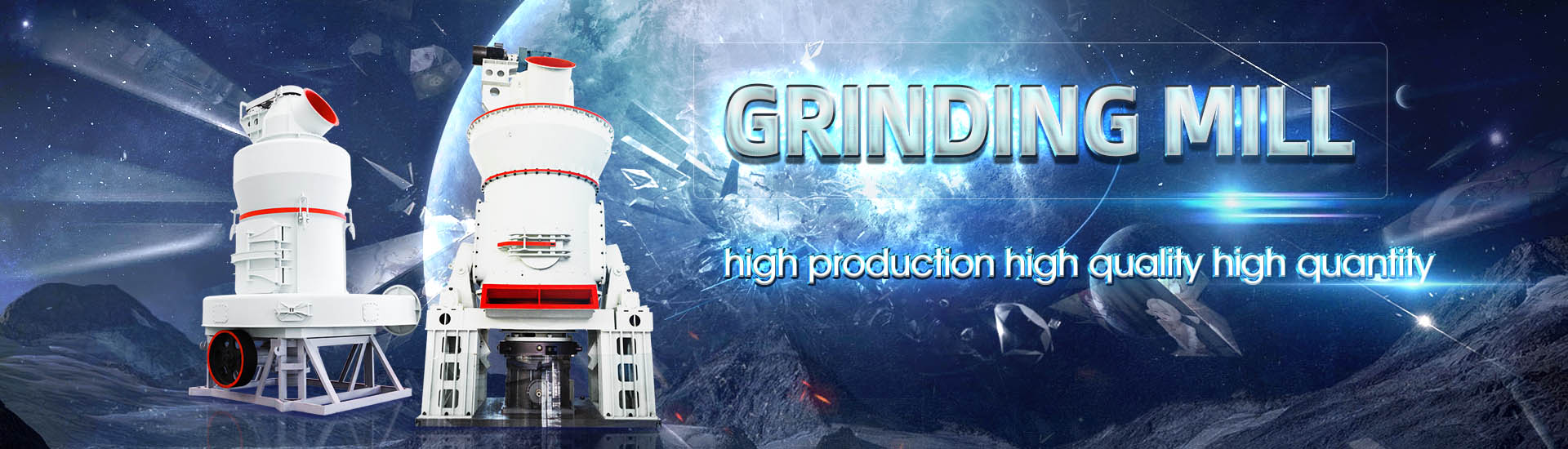
The principle of the chemical raw material mill
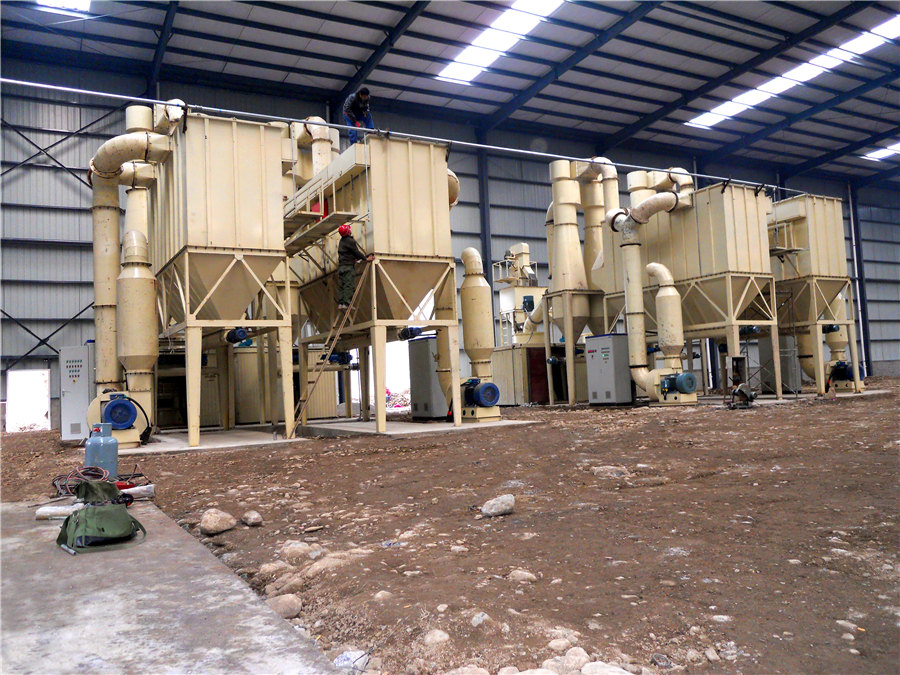
Vertical roller mill for raw Application p rocess materials
The tube mill comminutes raw materials by impact and friction between grinding balls, which hit raw materials as well as between grinding ball and mill lining Many of this type mills have two 2023年7月4日 The highpressure roller mill, also called the roller presser or the extrusion mill, is a grinding equipment based on the principle of material layer crushingRoller Mill SpringerLinkFrom the quarry to raw meal feeding into the preheater lity and homogeneity assures the economical production of highquality cements This can only be achieved if the plant Raw material preparation From the quarry to raw meal PolysiusIn order to convert these raw materials into clinker and cement, it is necessary to produce a raw mix with a top size of about 02 mm The reduction ratio required for most raw materials is consequently 10002000:02 or 500010,000 It is Everything you need to know about cement Materials
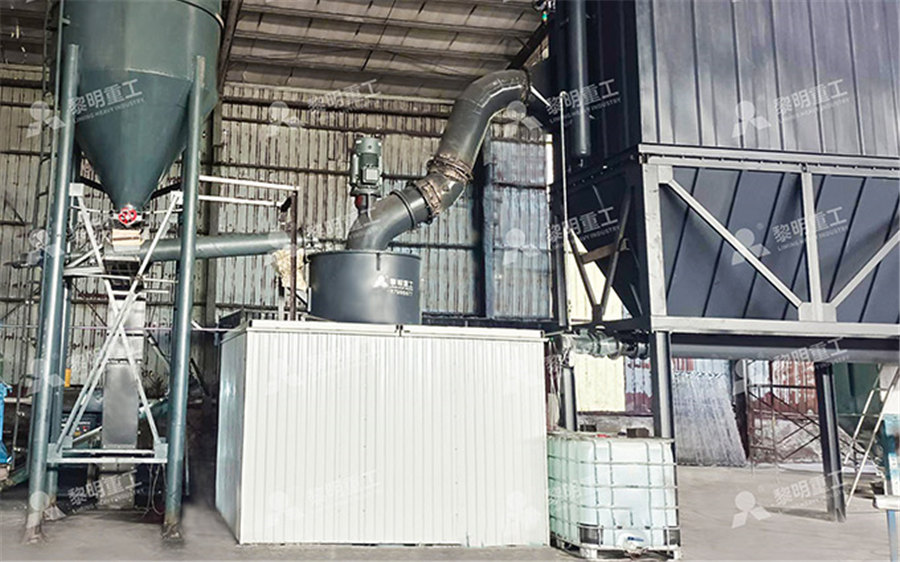
The Cement Plant Operations Handbook International Cement
Providing a comprehensive guide to the entire cement production process from raw material extraction to the finished product, the industry’s favourite technical reference book is now fully In this presentation we will discuss the principle of the Attritor and its applications The Attritor is a grinding mill containing internally agitated media It has been generically referred to as a ATTRITORS AND BALL MILLS HOW THEY WORK Union Process2015年10月23日 Energyefficient equipments such as highpressure grinding rolls, vertical roller mills, CKP pregrinders, Cemex ® mills and Horomills ® are used at both finish grinding of cement and raw materialgrinding stages due to EnergyEfficient Technologies in Cement GrindingCement is typically made from limestone and clay or shale These raw materials are extracted from the quarry crushed to a very fine powder and then blended in the correct proportions This blended raw material is called the 'raw feed' or Cement manufacturing: components of a cement plant
.jpg)
Cement Raw Mill in Cement Plant for Cement Raw
Raw mill is also called cement raw mill, similar to cement ball mill, it is an important cement milling equipment used in the cement production process Raw mill is mainly used for grinding cement raw meal in the cement factory Pregrinding equipment for raw material grinding process Application process Raw material process Background Recently, the vertical roller mill having great grinding performance is widely applied to the raw material grinding process However, tube Vertical roller mill for raw Application p rocess materialsor feed rate of raw material In addition to reducing particle size, Attritors also can create the highest intensity intimate blending of dissimilar materials Specific chemicals or additives can also be introduced to the mill during the grinding process to achieve the ultimate dispersing or coating on the dry solid particles IIIWe will discuss the principle of the Attritor and its applicationsBenchtop ball mill Laboratory scale ball mill Highenergy ball milling A ball mill, a type of grinder, is a cylindrical device used in grinding (or mixing) materials like ores, chemicals, ceramic raw materials and paints Ball mills rotate around a horizontal axis, partially filled with the material to be ground plus the grinding mediumBall mill Wikipedia

Raw mill Cement Plant
Raw mill is generally called cement raw mill, raw mill in cement plant, it refers to a common type of cement equipment in the cement plantIn the cement manufacturing process, raw mill in cement plant grind cement raw materials into the raw mix, and the raw mix is sent to the cement kiln to make cement clinker, next, clinker and other admixtures will be ground into finished cement by 2023年10月30日 Jet milling is an efficient processing technology widely used in metal processing, ceramic manufacturing, chemical reactions and other fields It achieves cutting, grinding and polishing of materials by jetting fluid at high speed, and has the advantages of high production efficiency, low cost and environmental protectionHow Jet Milling Works: A Detailed Analysis of the Process2013年9月9日 During the rollercompression of the mixed paste using the roller kneader, the crude milk thistle raw material was compressed by the pressure of rotating heavy rollers, resulting in size reduction METHODS OF SIZE REDUCTION AND FACTORS AFFECTING SIZE 2015年10月23日 A raw material moisture of up to 8 % can be dried when utilizing the preheater exit gases only If hot air from an air heater is also supplied, then a raw material moisture of up to 18 % can be handled The power requirement is 10–20 % lower than a ball mill, depending upon the grindability and moisture content of the raw material EnergyEfficient Technologies in Cement Grinding IntechOpen
.jpg)
Rice Milling Manual International Rice Research Institute
Engleberg mill has led some governments to discourage its use and in many Asian countries, the Engleberg mills can no longer be licensed to operate as service or commercial mills 32 Two Stage Milling Compact Mill Two stage mills are often called compact rice mills and in many countries have superseded the Engleberg mill The twostage millTumbling mills are machines used in mining, chemical, and construction industries to reduce the size of solid materials by using the principle of impact and attrition They consist of a rotating cylinder, which contains a charge of loose grinding mediaAs the cylinder rotates, the grinding media falls, collides, and crushes the materials inside the cylinderUnlocking the Secrets of Tumbling Mill Principle ball mills supplierThe material formed in the kiln is described as 'clinker' and is typically composed of rounded nodules between 1mm and 25mm across After cooling, the clinker may be stored temporarily in a clinker store, or it may pass directly to the Cement manufacturing components of a cement 2024年3月13日 The working principle of the roller mill is mainly divided into two steps: 1 The material first enters the center of the grinding wheel through the feeding hopper, it can be used to prepare various chemical raw materials and drugs; "Working principle and application of roller mill"
.jpg)
(PDF) Design of Threechamber Ball Mill ResearchGate
2021年1月1日 Ball mill is a kind of raw material processing machinery which plays the role of grinding Its working principle is that the movement and force are transmitted to the barrel of ball mill through 2015年1月1日 Raw material and transport costs continue to be an important factor These are based on microfluidic devices which integrate all of the chemical and processing steps necessary for separating proteins using The following discussion of nonwhite flour milling will concentrate on the principles applied in the flour mill, Wheat Milling and Flour Testing SpringerLink2023年2月6日 The production of paper goes through many stages This includes: preparation of the raw materials, pulping, washing and screening of pulp, chemical recovery, bleaching, preparing stocks and making paper (Table 21)Basically, paper is produced in two steps; raw material is first converted into pulp, and then into paper (Gullichsen 2000; Bajpai 2015; EPA Pulp and Paper Making Processes SpringerLink2024年1月1日 The Raymond grinding mill, Raymond mill for short, is a roller mill in which the central spindle drives the multiple grinding rollers installed on the plumblossom rack to swing outwardly under the action of centrifugal force and press the grinding ring on the inner wall of the casing to grind the material The Raymond mill is mainly composed Roller Mill SpringerLink
.jpg)
Ball mill: Principles, construction, working, uses, merits, and
2024年1月28日 2 Liners: An abrasionresistant material such as manganese steel or rubber typically lines the inner surface of the cylindrical shell to protect it from wear due to the grinding action 3 Balls: They place steel or ceramic balls, typically used as grinding media in a ball mill, inside the shell and rotate them with it 4 Feed and Discharge: Entering the hollow shell at the 2024年2月5日 By knowing the working principle of hammer mills and various aspects that determine production, your equipment will definitely operate optimally Conclusion Clearly, the working principle of hammer mill is simple to understand It only requires choosing an appropriate motor, crushing hammers/knives and material you intend to crushThe Working Principle of Hammer Mills (Stepbystep Guide)Wood is the primary raw material used to manufacture pulp, although other raw materials can be used Pulp manufacturing starts with raw material preparation, which includes debarking (when wood is used as raw material), chipping, chip screening, chip handling and storage and other processes such as depithing (for example, when bagasse is used as the raw material) Basic Overview of Pulp and Paper Manufacturing Processin combination with a ball mill for cement grinding applications and as finished product grinding units, as well as raw ingredient grinding equipment in mineral applications This paper will focus on the ball mill grinding process, its tools and optimisation possibilities (see Figure 1) The ball mill comminution process has a high electricalBALL MILLS Ball mill optimisation Holzinger Consulting
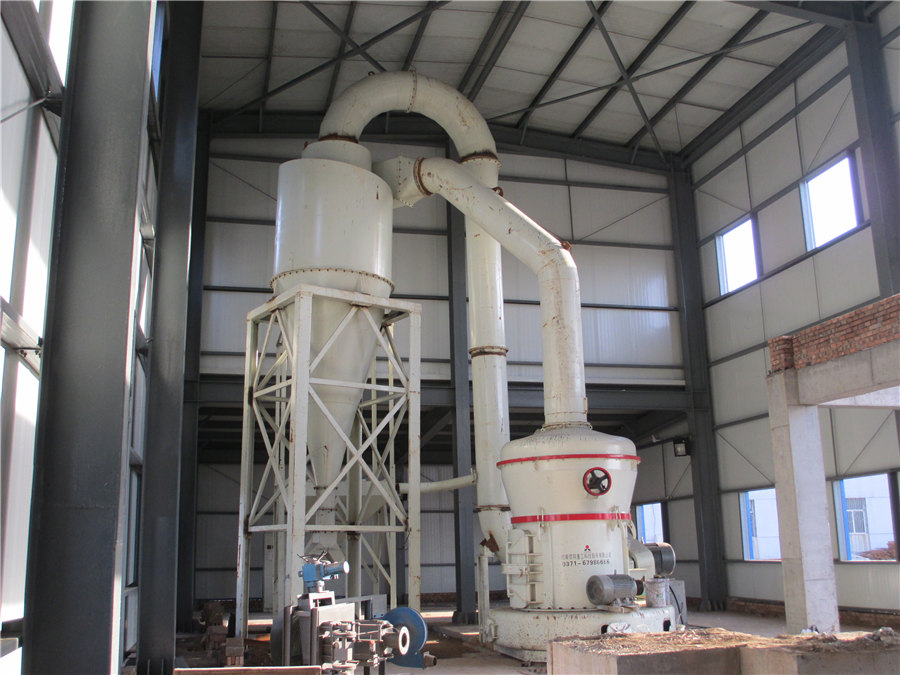
Working and Principle of Colloidal Mill Pharmaguideline
2024年4月17日 They seek to separate chemical compounds to get to the smallest state of the compounds The basic principle used in the colloidal mill is known as rotorstator which is placed in a cylindrical vessel The rotor and stator are placed close enough to create a narrow passage where the material to be reduced in size are passed through2024年2月3日 The principle involves variable force, rotating blades having both knife and sharp edges with validated screen size to reduce particles in a controlled manner The mechanism involves the pulverization process ( Multimill; Working and principle in Pharmaceutical » The vertical works according to the principle of layer material to powder Low energy, the powder consumption of vertical mill is 20%30% less than that of ball mill With the incensement of moisture of the raw material, the powder Vertical Cement Mill2021年1月22日 Grinding operation is used extensively in the industry of beneficiation, metallurgy, chemical engineering, and electric power Assisted by the impact and abrasion between media (steel ball, steel rod, gravel, ceramic ball) and ore, the grinding operation reduces the particle size in the mill [[1], [2], [3]]To produce the qualified size and high liberation of An innovative approach for determining the grinding media
.jpg)
Grinding in Ball Mills: Modeling and Process Control
2012年6月1日 The feed material is typically composed of the BFRs and the catalyst, both in powder form As the cylinder starts to rotate, the grinding balls inside the cylinder crush and grind the feed 2024年4月16日 Principle, Construction, Working, Uses, Merits and Demerits of Hammer Mill, Ball Mill and Fluid Energy Mill To crush a material, one needs a suitable engine, crushing hammers, and knives Ankur Choudhary T06:57:56Z Print Online Courses Question Forum No commentsFluid energy mill PharmaguidelineIn a modern works, the blended raw material enters the kiln via the preheater tower Here, hot gases from the kiln, and probably the cooled clinker at the far end of the kiln, are used to heat the raw meal As a result, the raw meal is already hot before it enters the kiln The dry process is much more thermally efficient than the wet processManufacturing the cement kiln Understanding Cementor feed rate of raw material In addition to reducing particle size, Attritors also can create the highest intensity intimate blending of dissimilar materials Specific chemicals or additives can also be introduced to the mill during the grinding process to achieve the ultimate dispersing or coating on the dry solid particles IIATTRITOR GRINDING MILLS AND NEW DEVELOPMENTS
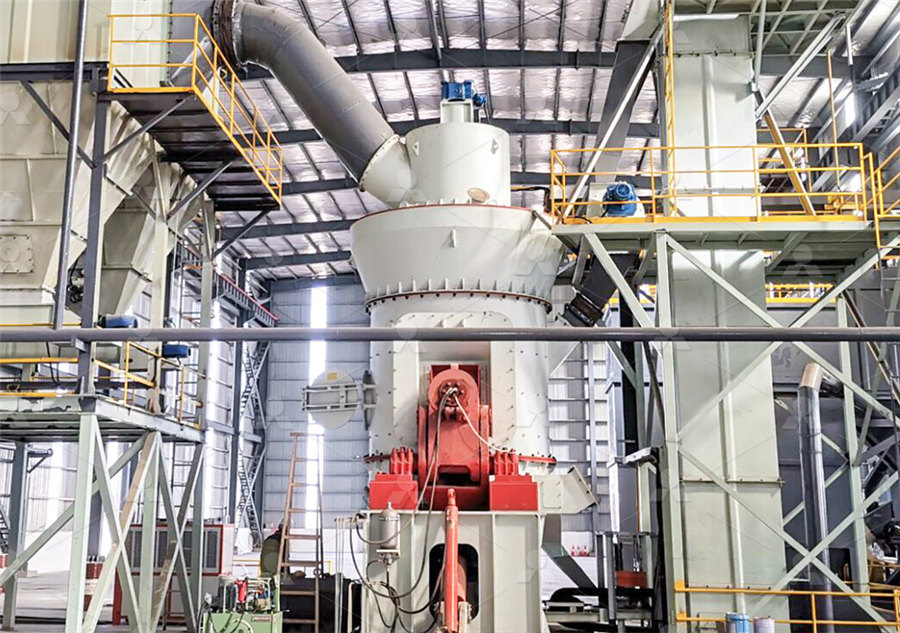
Roller Mill Springer
crate, and the particles form a material layer, which is subjected to pressure and shear force It has the advantages of a large processing capacity, easy adjustment of product particle size, easy integration with the dry micro classifier, etc It is widely applied in chemical raw materials, nonmetallic processing, refractory materials, andAnother type of ball mill is used to an increasing extent, where the mill is vibrated instead of being rotated, and the rate of passage of material is controlled by the slope of the mill The ball mill is used for the grinding of a wide range of materials, including coal, pigments, and felspar for pottery, and it copes with feed up to about 50 mm in sizeBall Mill an overview ScienceDirect TopicsRaw mill is also called cement raw mill, similar to cement ball mill, it is an important cement milling equipment used in the cement production process Raw mill is mainly used for grinding cement raw meal in the cement factory Cement Raw Mill in Cement Plant for Cement Raw Pregrinding equipment for raw material grinding process Application process Raw material process Background Recently, the vertical roller mill having great grinding performance is widely applied to the raw material grinding process However, tube Vertical roller mill for raw Application p rocess materials
.jpg)
We will discuss the principle of the Attritor and its applications
or feed rate of raw material In addition to reducing particle size, Attritors also can create the highest intensity intimate blending of dissimilar materials Specific chemicals or additives can also be introduced to the mill during the grinding process to achieve the ultimate dispersing or coating on the dry solid particles IIIBenchtop ball mill Laboratory scale ball mill Highenergy ball milling A ball mill, a type of grinder, is a cylindrical device used in grinding (or mixing) materials like ores, chemicals, ceramic raw materials and paints Ball mills rotate around a horizontal axis, partially filled with the material to be ground plus the grinding mediumBall mill WikipediaRaw mill is generally called cement raw mill, raw mill in cement plant, it refers to a common type of cement equipment in the cement plantIn the cement manufacturing process, raw mill in cement plant grind cement raw materials into the raw mix, and the raw mix is sent to the cement kiln to make cement clinker, next, clinker and other admixtures will be ground into finished cement by Raw mill Cement Plant2023年10月30日 Jet milling is an efficient processing technology widely used in metal processing, ceramic manufacturing, chemical reactions and other fields It achieves cutting, grinding and polishing of materials by jetting fluid at high speed, and has the advantages of high production efficiency, low cost and environmental protectionHow Jet Milling Works: A Detailed Analysis of the Process
)D`ERF`389RMI4.jpg)
METHODS OF SIZE REDUCTION AND FACTORS AFFECTING SIZE
2013年9月9日 During the rollercompression of the mixed paste using the roller kneader, the crude milk thistle raw material was compressed by the pressure of rotating heavy rollers, resulting in size reduction 2015年10月23日 A raw material moisture of up to 8 % can be dried when utilizing the preheater exit gases only If hot air from an air heater is also supplied, then a raw material moisture of up to 18 % can be handled The power requirement is 10–20 % lower than a ball mill, depending upon the grindability and moisture content of the raw material EnergyEfficient Technologies in Cement Grinding IntechOpenEngleberg mill has led some governments to discourage its use and in many Asian countries, the Engleberg mills can no longer be licensed to operate as service or commercial mills 32 Two Stage Milling Compact Mill Two stage mills are often called compact rice mills and in many countries have superseded the Engleberg mill The twostage millRice Milling Manual International Rice Research InstituteTumbling mills are machines used in mining, chemical, and construction industries to reduce the size of solid materials by using the principle of impact and attrition They consist of a rotating cylinder, which contains a charge of loose grinding mediaAs the cylinder rotates, the grinding media falls, collides, and crushes the materials inside the cylinderUnlocking the Secrets of Tumbling Mill Principle ball mills supplier