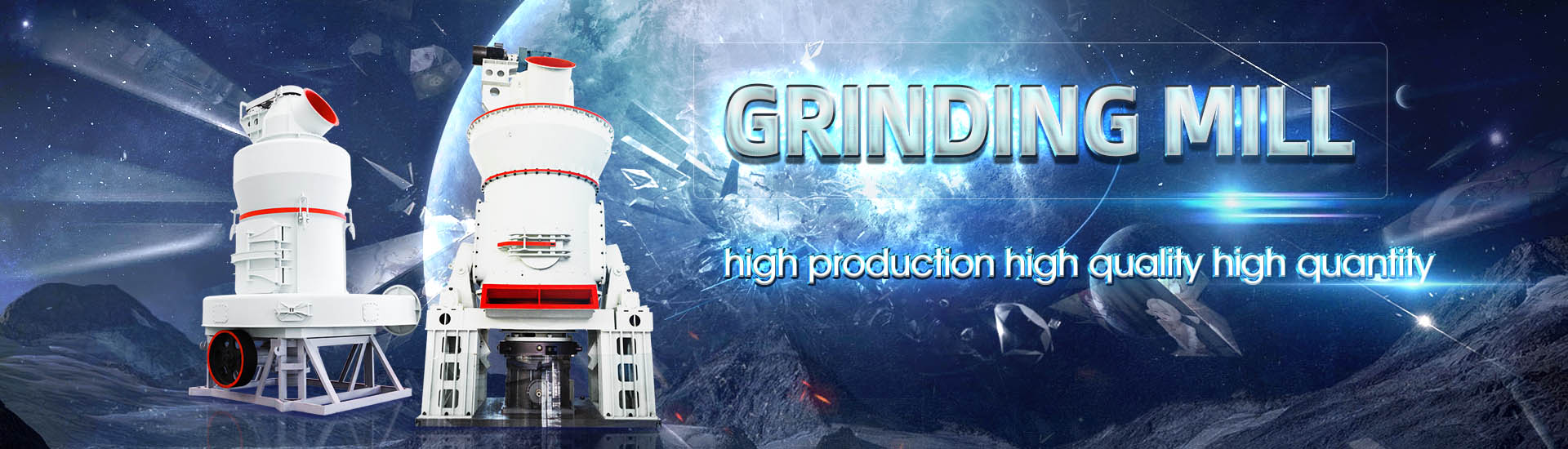
Highspeed cement raw materials Ball mill
.jpg)
BALL MILLS Ball mill optimisation Holzinger Consulting
common solution to grind raw materials and cement Roller presses are used mainly in combination with a ball mill for cement grinding applications and as finished product grinding Efficient ball mill for grinding cement, mineral ores, and raw materials Highperformance design ensures fine output and energy savings Learn more nowBall mill CEMENTLRoller press with Ball mill Ball Mill Ball mills with high efficiency separators have been used for raw material and cement grinding in cement plants all these years Ball mill is a cylinder Raw Material DryingGrinding Cement Plant Optimizationensuring economical grinding of cement raw material, cement clinker, granulated blastfurnace slag, pozzolana, other additives, and coal Highest plant availability, appropriate wear PFEIFFER MILLS FOR THE CEMENT INDUSTRY
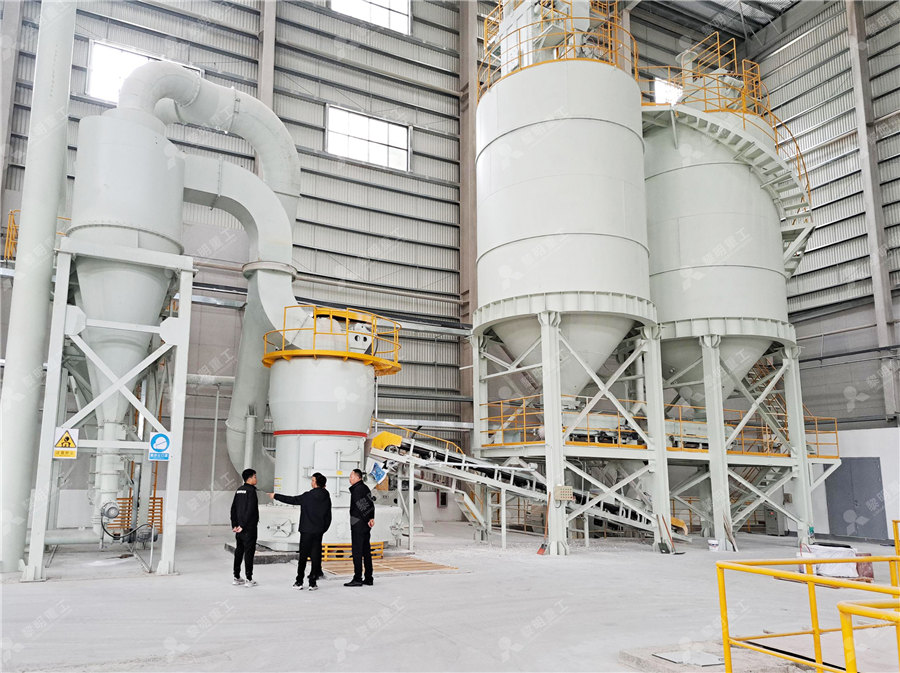
polycom® high pressure grinding roll thyssenkrupp
One of the principal reasons for the outstanding success of the high pressure grinding roll in the cement industry is its low power requirement Today, this mill is employed all around the world for the grinding of cement raw material, cement optimization of cement grinding operation in ball mills Several energy efficient options for cement grinding are available today such as vertical roller mills, roller presses (typically in combination OPTIMIZATION OF CEMENT GRINDING OPERATION IN BALL MILLS2015年10月23日 Energyefficient equipments such as highpressure grinding rolls, vertical roller mills, CKP pregrinders, Cemex ® mills and Horomills ® are used at both finish grinding of cement and raw materialgrinding stages due to EnergyEfficient Technologies in Cement GrindingFor raw material grinding four QMR² 48/24 are contracted, while for cement grinding four polycom® high pressure grinding rolls as a combi grinding system are considered due to material properties The four mills are operating very quadropol® thyssenkrupp Polysius Grinding
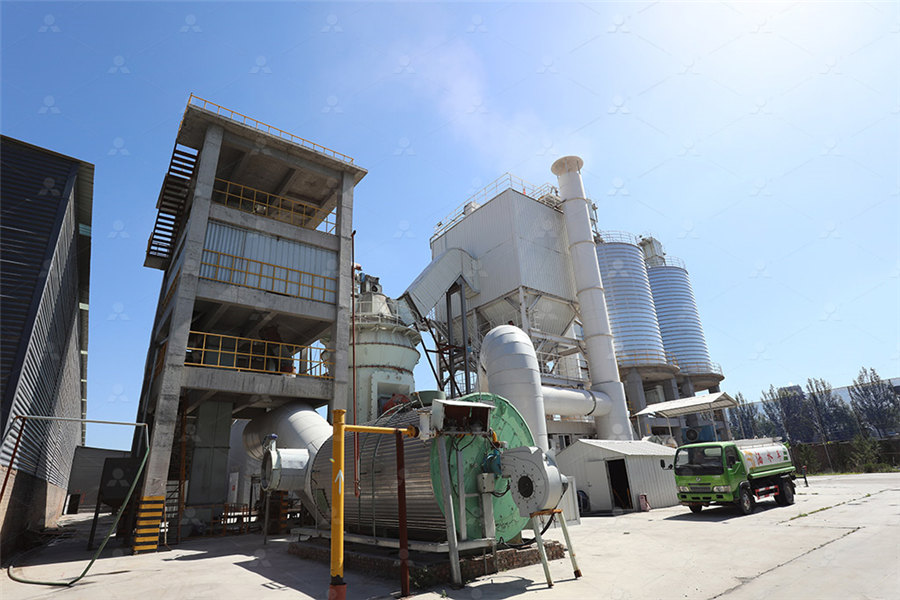
Review on vertical roller mill in cement industry its performance
2021年1月1日 Raw mix, high grade limestone, sand and iron ore are transported from their bins to raw mills for drying and further fine grinding The raw mill is either a Ball mill with two 2015年4月1日 Production capacity of a fully airswept industrial scale twocompartment KHD Humboldt Wedag® cement ball mill was optimized with the aid of simulation It was proposed Optimization of a fully airswept dry grinding cement raw meal Tongli ball mill has following categories: according to the product mate rial can be divided into cement ball mill, mineral ball mill, limestone ball mill, gypsum ball mill, slag ball mill, ore ball mill, raw material ball mill, coal mill; according to the size of the crushed material can be divided into: coarse ball mill, highfine powder ball mill, ultrafine powder ball mill; according to Cement Ball Mill Manufacturers Tongli Machinery2019年6月22日 Introduction: Raw milling is one of the most important and integral component of cement production process; it is the stage which produces the most important intermediate product ieOptimizing Raw Mills Performance ; the Materials
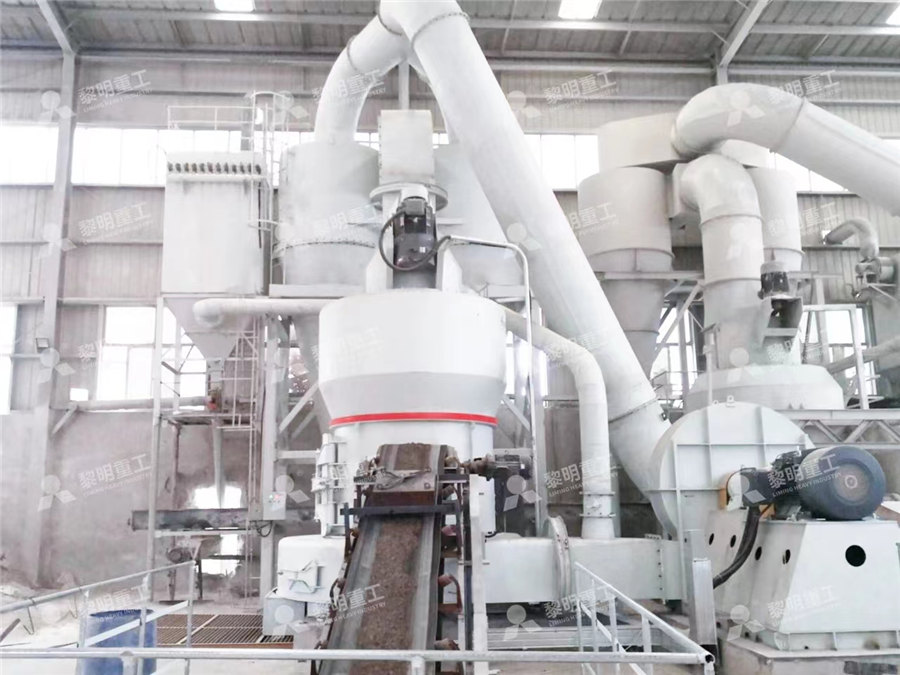
Raw milling and blending INFINITY FOR CEMENT
The main difference to cement mill operation is the need to dry rawfeed and assure transport of stightly moist materialwithin a mill Also, many raw materials are softer than clinker, and operations must avoid coarse residues in kiln feed Benchtop ball mill Laboratory scale ball mill Highenergy ball milling A ball mill, a type of grinder, is a cylindrical device used in grinding (or mixing) materials like ores, chemicals, ceramic raw materials and paints Ball mills rotate around a horizontal axis, partially filled with the material to be ground plus the grinding mediumBall mill Wikipedia2021年6月10日 The results demonstrated that the VRM unit consumes around 81% (975 kWh/t of raw materials), and 36% (58 kWh/t of raw materials) more energy to grind raw material than the IBAT unit and domestic Ventilation Prediction for an Industrial Cement Raw Ball Mill by 2024年1月26日 Grinding media is mostly prepared from high chrome steel Ball mills are efficiently utilized for final grinding of clinker It grounds the raw mix (clinker) into fine powder Ball mills are available of different sizes and capacities Ball mill may be of two compartment or three compartments The schematic view of cement ball mill is shown in Computation of charging media for a double compartment cement ball mill
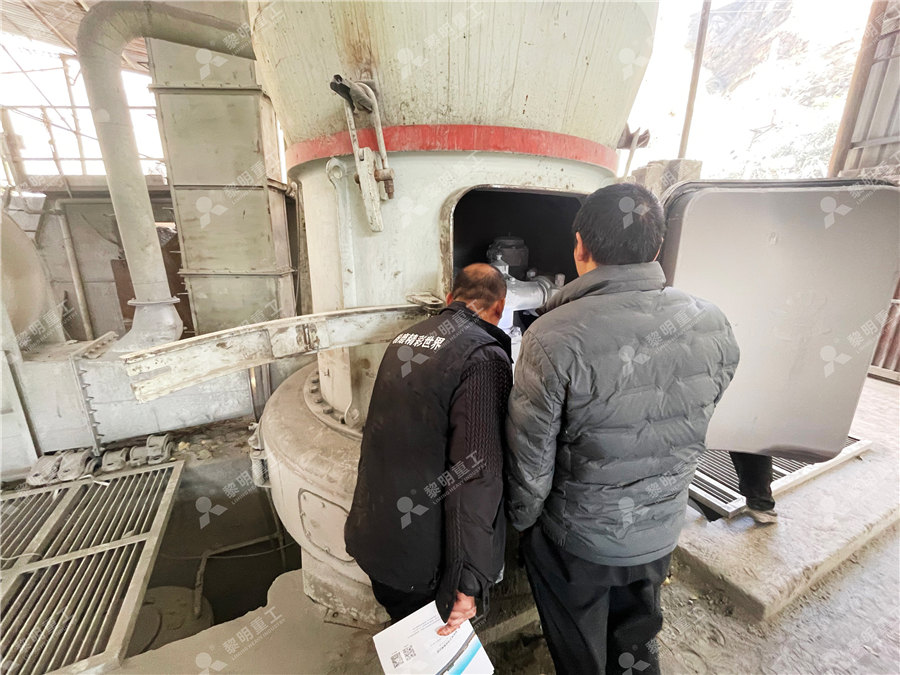
Review on vertical roller mill in cement industry its performance
2021年1月1日 Raw mix, high grade limestone, sand and iron ore are transported from their bins to raw mills for drying and further fine grinding The raw mill is either a Ball mill with two chambers or Vertical roller mill with inbuilt classifier The hot gases from the pre heater enter the mill and are used for drying material in the mills首页 > Products > Ball Mill > Raw Material Ball Mill Raw Material Ball Mill Overview; Ball Motor Power: 4753550 kW: Fineness: 3300~3800 cm²/g: Overview This ball mill is mainly used for grinding raw materials and final products in cement plant It can be replaced by vertical raw mill It is also suitable High wear resistance Raw Material Ball MillBall Mill In Cement Plant is an important piece of equipment for grinding cement raw materials into proper particle size, mix raw materials and produce highquality cement to improve production efficiency and output Cement Mill The main working part of the ball mill grinding material occurs on the horizontal lowspeed rotating cylinderBall Mill In Cement Plant Selling Various Types Of Cement MillAGICO vertical roller mills can be used as cement mills, raw mills, and slag mills AGICO also supplies vertical roller mill components and parts, we can customize machines according to customers’ needs Vertical roller mills (VRM) are a type of mainstream clinker grinding equipment in the cement manufacturing process Vertical roller mills are still newish []Vertical Roller Mill for Sale AGICO Cement Plant
.jpg)
High Efficiency and Large Output Cement Ball Mill
Motor: The motor is the power source that drives the mill; Bearings: These components support the mill shell and allow it to rotate; Lining plates: The mill shell interior is often lined with replaceable plates to protect it from wear due Operation and Elements of a ClosedCircuit Ball Mill System Cement ball mills typically have two grinding chambers The first chamber is filled with larger diameter grinding media andlined with lifting liners The first chamber coarsegrinds the feed material and prepares it for the second chamber The second chamber is the fine grinding OPTIMIZATION OF CEMENT GRINDING OPERATION IN BALL MILLS7 // Almost any plant for the grinding of cement raw material is a combination of machines specially adapted to the particular physical properties of the material to be ground As a result, our plants work efficiently without any trouble » Highly efficient grinding, drying, and separating in one unit » Outstanding production capacities exceeding 1,400 t/h in one single millPFEIFFER MILLS FOR THE CEMENT INDUSTRY2024年8月8日 In the intricate dance of ball milling, where raw materials are transformed into finely milled particles, the choice of grinding media emerges as a pivotal performance lever This seemingly minor selection can dramatically influence the efficiency of the milling process, the quality of the output, and, ultimately, the bottom lineBall Mill Success: A StepbyStep Guide to Choosing the Right
.jpg)
Steel slag Ball Mill CEMENTL
2How to Increase the Output of a Steel Slag Ball Mill? Increasing the rotational speed of the mill cylinder can enhance the centrifugal force acting on the grinding balls, Suitable for cement grinding, with high production capacity The main raw material for gold refining, ball mill can improve its extraction efficiency GarnetVertical raw mill is one kind of raw mill, generally used to grind bulk, granular, and powder raw materials into required cement raw meal in the cement manufacturing plantVertical raw mill is an ideal grinding mill that crushing, drying, grinding, grading transfer set in one It can be widely used in cement, electric power, metallurgy, chemical industry, nonmetallic ore, and other industriesVertical raw mill Cement Plant2023年8月23日 The production process of a cement ball mill involves raw material preparation, grinding, linearization, clinker grinding, and the eventual storage and distribution of the finished cement product This process is integral to the production of cement, a vital building material that plays a central role in construction and infrastructure development around the worldWhat Are the Parts of a Cement Mills? Cement Ball Mill 2023年4月23日 ment of grinding media which results in collisions is affected by mill design, mill speed, mill filling and grinding media properties[14] The collision impact cause pa rticle breakage due to the (PDF) Grinding Media in Ball MillsA Review ResearchGate
.jpg)
Effects of Mill Speed and Air Classifier Speed on Performance of
A ball mill is a type of grinder used to grind, blend and sometimes for mixing of materials for use in mineral dressing processes, paints, pyrotechnics, ceramics and selective laser sintering Ball mill in the cement industry is used to reduce the size of clinker into fine particles also called as cement Mill speed and air classifier speed The EThammer mill is provided with an enclosed base and with a separation compartment This design results in a longer residence time of the raw material in the mill, thus ensuring a high degree of drying; a size reduction ratio of 1 : 100 and more, can be attainedDrying of raw materials INFINITY FOR CEMENT EQUIPMENTSINOMALY produces cement raw material grinding mills in various specifications These machines are suitable for grinding mill production lines with an output of 2500t/d, 3200t/d, 4000t/d, 5000t/d, 6000t/d and 8000t/d The vertical grinding Vertical Roller Mill for Cement Raw MaterialThe raw material fed to the ball mill is cement clinker Mill drum is filled with steel balls that grind the cement clinker upon impact When the For a step change of 1 for mill fan speed and a step Modeling And Simulation Of A Closed Loop Ball Mill Grinding Circuit April 2014, MODELING AND SIMULATION OF A CLOSED LOOP BALL MILL
.jpg)
OK™ Raw and Cement Mill
Our bestinclass OK™ Mill is a globally successful vertical roller mill solution for grinding raw material, cement and slag Our OK Mill offers a high run factor of typically 90 to 95 percent availability uses five to ten percent less power The grinding plate is powered by an electric motor that rotates the plate at a speed of around 2030 RPM The raw materials used in a raw mill in a cement plant include limestone, clay, shale, and iron ore 85tph Cement Ball Mill Put Into Operation In Indian Cement Plant Read MoreWhat does a Raw Mill do in Cement Plant? ball mills supplierAfter monitoring and controlling the quality of incoming raw material, the area of high activity for quality department to ensure quality mix for smooth production of high quality of cement is “mill feeding system” The system consists of material hoppers/bins, weighing, conveying, venting and mill feeding gate Mill Feeding HoppersRaw Mill Feeding Cement Plant OptimizationEffect may arise, not only on the raw materials but also due to the burning cooling methods Mill L / D ratio: The ratio, however varies with the circuit used, material type, feed Size and grinding requirements Generally there is no fixed rule; however tube mills have the ratio of 3 to 6: 1 and ball mills are of 2: 1Notes on Tube mills INFINITY FOR CEMENT EQUIPMENT
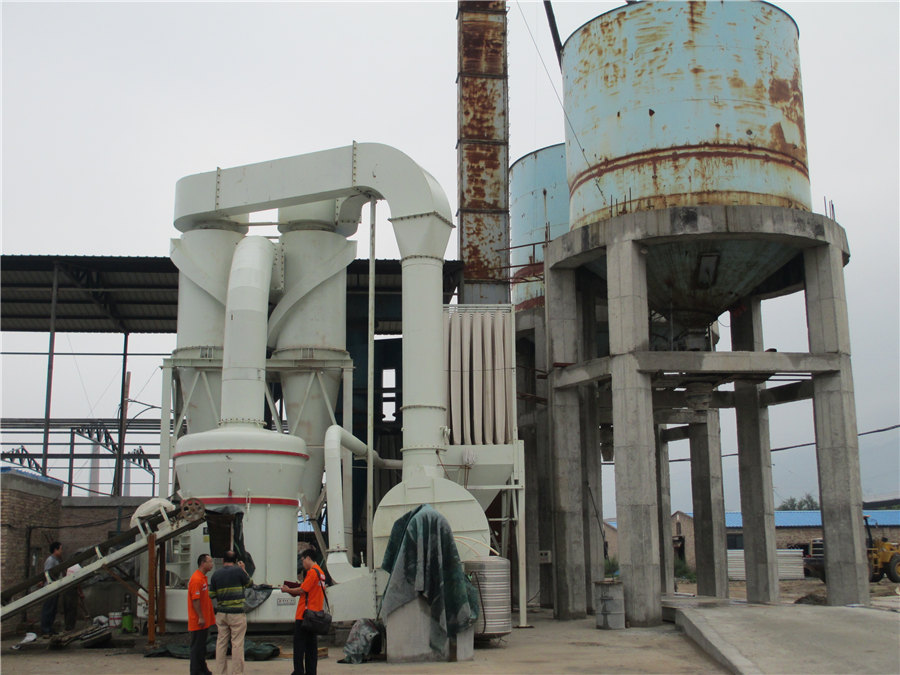
A Survey and Analysis on Electricity Consumption of Raw Material Mill
2021年1月22日 In the whole process of cement production, the electricity consumption of a raw material mill accounts for about 24% of the total Based on the statistics of the electricity consumption of the raw material mill system of 1005 production lines in China between 2014 and 2019, it is found that the average electricity consumption of the raw material preparation A highefficiency cement separator is essential for costeffectiveness as improving product quality and reduces energy Applications Closed circuit ball mill grinding plant Closed circuit system mainly composed of the cement vertical mill Roller press and ball mill pregrinding in combined cement grinding systems, raw mill finish Cement Mill Separator High Efficiency Cement Separator2019年8月14日 After rising to a certain height, it will hit the raw material under the action of gravity, and then rises with the wall of the cylinder again and again to grind the raw material Working principle of ball mill back to top The ball mill is usually composed of a horizontal cylinder, a hollow shaft and a grinding headThe Ultimate Guide to Ball Mills MiningpediaThe cement raw material mixtures are ground, dried, and classified in the Pfeiffer vertical roller mill For drying the material, hot gases are directed into the mill Product fineness can be adjusted within a wide range (0063 to 02 mm)Raw mills for all requirements Gebr Pfeiffer
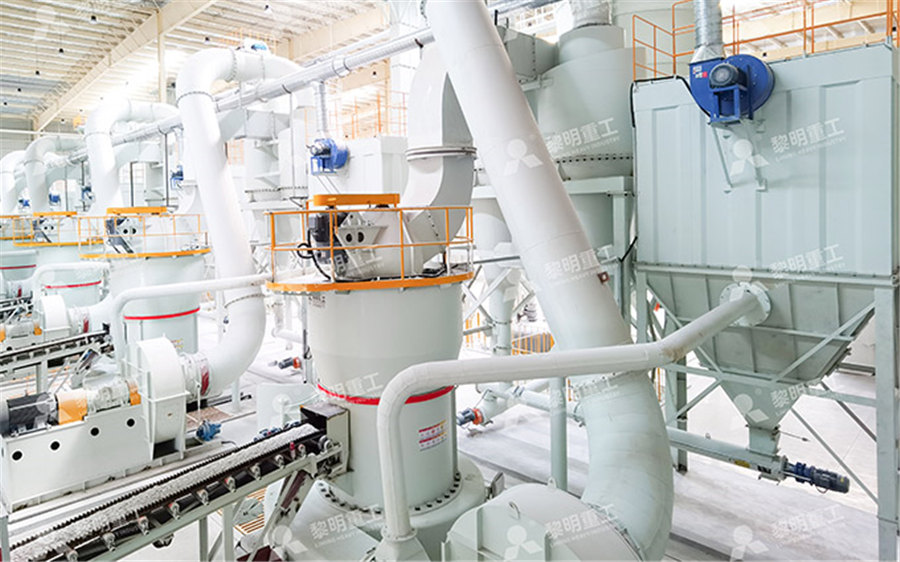
Cement Ball Mill Manufacturers Tongli Machinery
Tongli ball mill has following categories: according to the product mate rial can be divided into cement ball mill, mineral ball mill, limestone ball mill, gypsum ball mill, slag ball mill, ore ball mill, raw material ball mill, coal mill; according to the size of the crushed material can be divided into: coarse ball mill, highfine powder ball mill, ultrafine powder ball mill; according to 2019年6月22日 Introduction: Raw milling is one of the most important and integral component of cement production process; it is the stage which produces the most important intermediate product ieOptimizing Raw Mills Performance ; the Materials The main difference to cement mill operation is the need to dry rawfeed and assure transport of stightly moist materialwithin a mill Also, many raw materials are softer than clinker, and operations must avoid coarse residues in kiln feed Raw milling and blending INFINITY FOR CEMENT Benchtop ball mill Laboratory scale ball mill Highenergy ball milling A ball mill, a type of grinder, is a cylindrical device used in grinding (or mixing) materials like ores, chemicals, ceramic raw materials and paints Ball mills rotate around a horizontal axis, partially filled with the material to be ground plus the grinding mediumBall mill Wikipedia
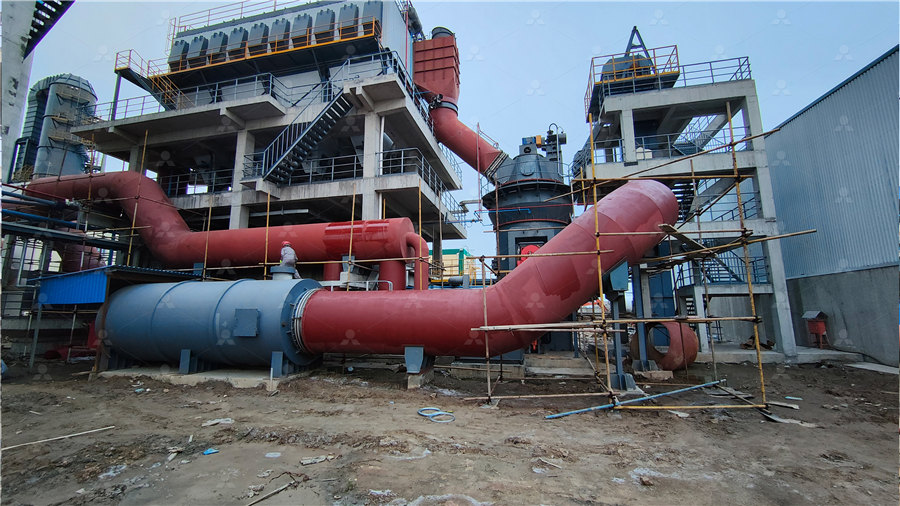
Ventilation Prediction for an Industrial Cement Raw Ball Mill by
2021年6月10日 The results demonstrated that the VRM unit consumes around 81% (975 kWh/t of raw materials), and 36% (58 kWh/t of raw materials) more energy to grind raw material than the IBAT unit and domestic 2024年1月26日 Grinding media is mostly prepared from high chrome steel Ball mills are efficiently utilized for final grinding of clinker It grounds the raw mix (clinker) into fine powder Ball mills are available of different sizes and capacities Ball mill may be of two compartment or three compartments The schematic view of cement ball mill is shown in Computation of charging media for a double compartment cement ball mill 2021年1月1日 Raw mix, high grade limestone, sand and iron ore are transported from their bins to raw mills for drying and further fine grinding The raw mill is either a Ball mill with two chambers or Vertical roller mill with inbuilt classifier The hot gases from the pre heater enter the mill and are used for drying material in the millsReview on vertical roller mill in cement industry its performance 首页 > Products > Ball Mill > Raw Material Ball Mill Raw Material Ball Mill Overview; Ball Motor Power: 4753550 kW: Fineness: 3300~3800 cm²/g: Overview This ball mill is mainly used for grinding raw materials and final products in cement plant It can be replaced by vertical raw mill It is also suitable High wear resistance Raw Material Ball Mill
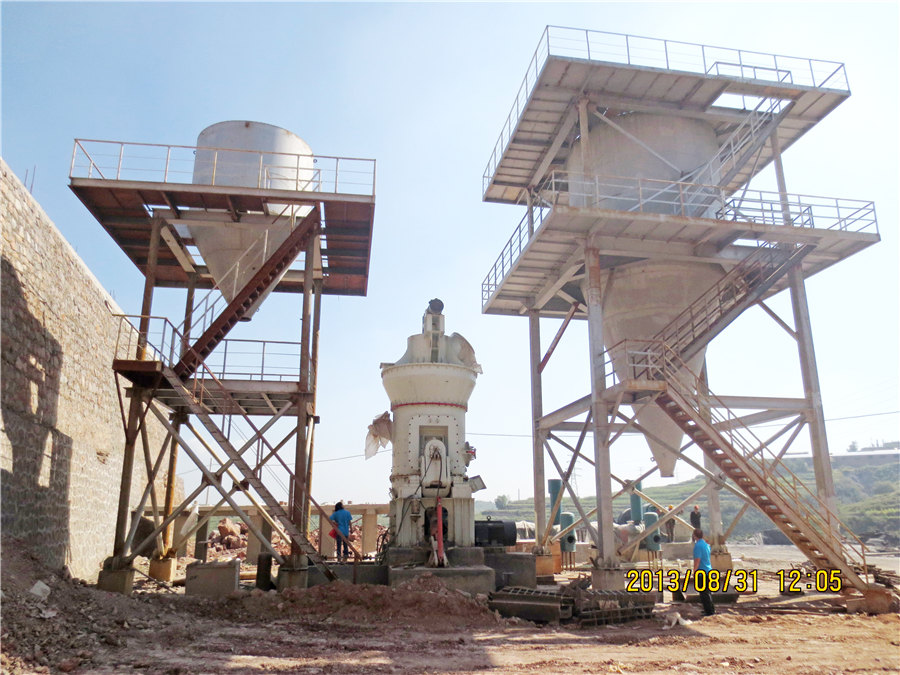
Ball Mill In Cement Plant Selling Various Types Of Cement Mill
Ball Mill In Cement Plant is an important piece of equipment for grinding cement raw materials into proper particle size, mix raw materials and produce highquality cement to improve production efficiency and output Cement Mill The main working part of the ball mill grinding material occurs on the horizontal lowspeed rotating cylinderAGICO vertical roller mills can be used as cement mills, raw mills, and slag mills AGICO also supplies vertical roller mill components and parts, we can customize machines according to customers’ needs Vertical roller mills (VRM) are a type of mainstream clinker grinding equipment in the cement manufacturing process Vertical roller mills are still newish []Vertical Roller Mill for Sale AGICO Cement Plant