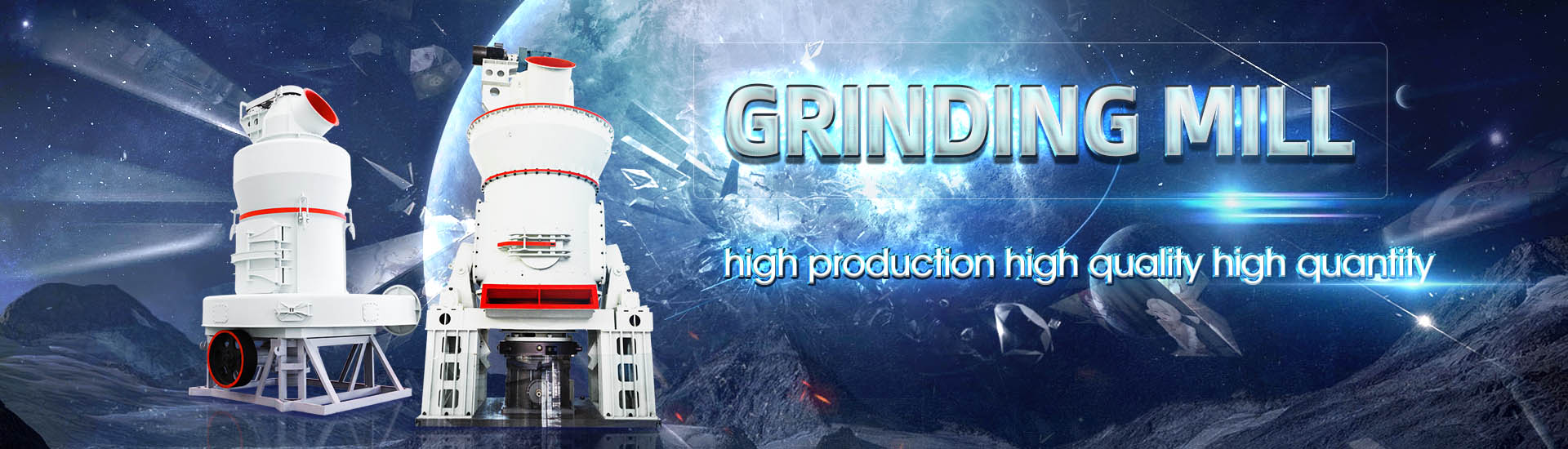
Matte iron production line process flow
.jpg)
1A Manufacturing Process for Iron and Steel
The smelting and refining process for iron and steel in the BFBOF process involves the carbon reduction of iron ore (Fe 2 O 3) in the BF to make molten iron, and decarburization of molten 2023年6月7日 Matte converting by PS Converter is the metallurgical process in which copper matte or lowgrade nickel matte is generated through matte smelting in pyrometallurgical Matte Converting by PS Converter SpringerLinkThe molten iron and slag are removed, or cast, from the furnace periodically The casting process begins with drilling a hole, called the taphole, into the clayfilled iron notch at the base of the 125 Iron And Steel Production US EPA2014年1月1日 The main steps of the process are matte production, anode casting, electrolysis, and harvesting [8] Molten matte with a typical composition of 76% Ni, 19% S, and 3% Cu is Nickel and Cobalt Production ScienceDirect
.jpg)
ISASMELT™ TSL – MAKING A SPLASH FOR NICKEL Glencore
Figure 4 also shows the possibility of using the nickel ISASMELT™ process to produce Bessemer matte with low iron content directly from concentrate feed This would obviate the need for1998年10月30日 The primary purpose of matte smelting is to melt and recombine the charge into a homogeneous matte of metallic copper, nickel, cobalt, and iron sulfides and to give an Metallurgy Matte Smelting, Refining, Alloying BritannicaThe PSC is the dominant technology for final deironisation and desulphurization of copper matte from the primary smelting The twostage processing cycle contains several blowing and Taskinen, Pekka; Akdogan, Guven; Kojo, Ilkka; Lahtinen, Markku 2022年5月19日 The extraction of nickel (Ni) from sulfide resources commences with flotation to produce a concentrate which is then smelted to produce a nickelenriched phase called matte, The Direct Leaching of Nickel Sulfide Flotation Concentrates – A
.jpg)
Material and energy flows in rotary kilnelectric furnace smelting
2016年10月25日 Among these methods, the rotary kilnelectric furnace (RKEF) process has the advantages of yielding high nickel/iron grade from crude ferronickel products, less harmful 2019年2月6日 PDF The first brochure on the topic "Production process of a lithiumion battery cell" is dedicated to the production process of the lithiumion cell Find, read and cite all the research Lithiumion Battery Cell Production Process2023年9月8日 These actions targeted blast furnace process enhancement, leading to heightened production rates, reduced fuel consumption, and diminished greenhouse gas emissionsBlast Furnace process optimization for sustainable Iron 2013年3月16日 Direct Reduced Iron and its Production Processes satyendra; March 16, 2013; 12 Comments ; ranging from 800 deg C to 1050 deg C is maintained along the length of the kiln at different zones and as the material Direct Reduced Iron and its Production Processes –
.jpg)
Flow sheet over the steelmaking processes Steel can be
Primary aluminium production is energy and GHGintensive in which electrolysis is by far the most energy and GHGintensive process This paper’s aim is to study the effects on (1) primary 2023年4月5日 The blast furnace and direct reduction processes have been the major iron production routes for various iron ores (ie goethite, hematite, magnetite, maghemite, siderite, etc) in the past few decades, but the challenges of maintaining the iron and steelmaking processes are enormous The challenges, such as cumbersome production routes, scarcity of Recent Trends in the Technologies of the Direct Reduction and As the process continue the molten iron flow down through the furnace and collects at the bottom, where it is removed through an opening in the side When it cools the impure iron is brittle and some cases soft due to the presence of the small impurities, such as sulfur and phosphorusIron Production Chemistry LibreTexts2019年6月22日 Fig 1 Schematic process flow diagram of a continuous electrotinning line The bright bath has several advantages over the matte process which include improved corrosion resistance, This flow melting process enhances the corrosion resistance of the product by formation of an inert tiniron alloy layerTinplate and Process of Tinning IspatGuru
.jpg)
Casting Production: Process Flow, Equipment, Principle and
2024年8月17日 Our guide provides an overview of the process flow, equipment involved, as well as the principles and characteristics of the casting method Close; Articles Metalworking Pig Iron Pig iron is a primary intermediate product in the iron and steel industry, typically containing a high carbon content ranging from 2% to 669% Primary world nickel production in 2020 was 24307 kt Ni; 69% (16777 kt) of them came from oxidized nickel ores (laterites) and 31% from sulfides Productionwise, 877% of the 16777 kt came from pyrometallurgical and 123% from hydrometallurgical processes For a long time, FeNi had a 20–40% Ni analysis, but in 2006 a new FeNi quality came into the scene This is the The Nickel Production Methods from Laterites and the Greek2016年3月30日 In book: Encyclopedia of Iron, Steel, and Their Alloys (pppp 10821108) Chapter: i) Direct Reduced Iron: Production; Publisher: CRC Press, Taylor and Francis Group, New York(PDF) i) Direct Reduced Iron: Production ResearchGate2019年9月3日 According to a review published by Diaz et al, oxidetype nickel ores accounted for 64% of landbased nickel ores, but more than 60% of nickel production was based on the matte smelting of sulfide ores in 1988 []This Nickel Laterite Smelting Processes and Some Examples
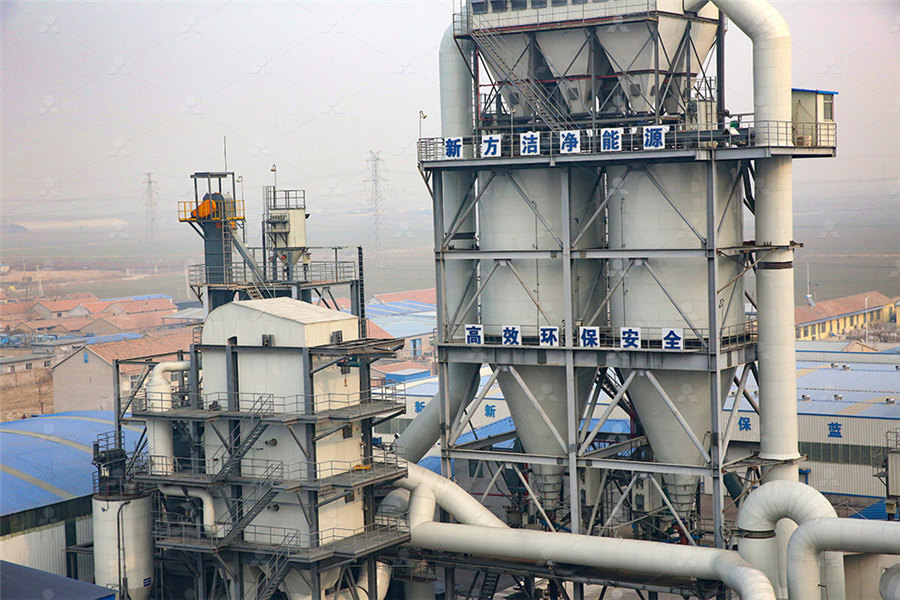
Copper Production ScienceDirect
2014年1月1日 Abstract Section 211 covers the basic thermodynamic and kinetic principles involved in producing copper by hightemperature smelting processes The section starts with the description of the stability of copper compounds relevant to the pyrometallurgical production of copper from the minerals and how it relates to the development and operation of different 2018年12月1日 oxidation of iron sulfide in the matte into iron oxides Further oxidation would rely upon mass transport of oxygen from the bulk slag phase into the reactionCopper matte slag reaction sequences and 2023年1月31日 Copper matte converting is an essential process in copper pyrometallurgy Replacing traditional batch converting in Peirce–Smith converters (PSCs), continuous converting is becoming a new trend In this work, a thermodynamic modeling of the copper matte continuous converting process was carried out under actual production conditions There were five Operation and Fundamentals of Direct Anode Copper Production From MatteNickel processing Extraction, Refining, Alloying: The extraction of nickel from ore follows much the same route as copper, and indeed, in a number of cases, similar processes and equipment are used The major differences in equipment are the use of highertemperature refractories and the increased cooling required to accommodate the higher operating temperatures in nickel Nickel processing Extraction, Refining, Alloying Britannica
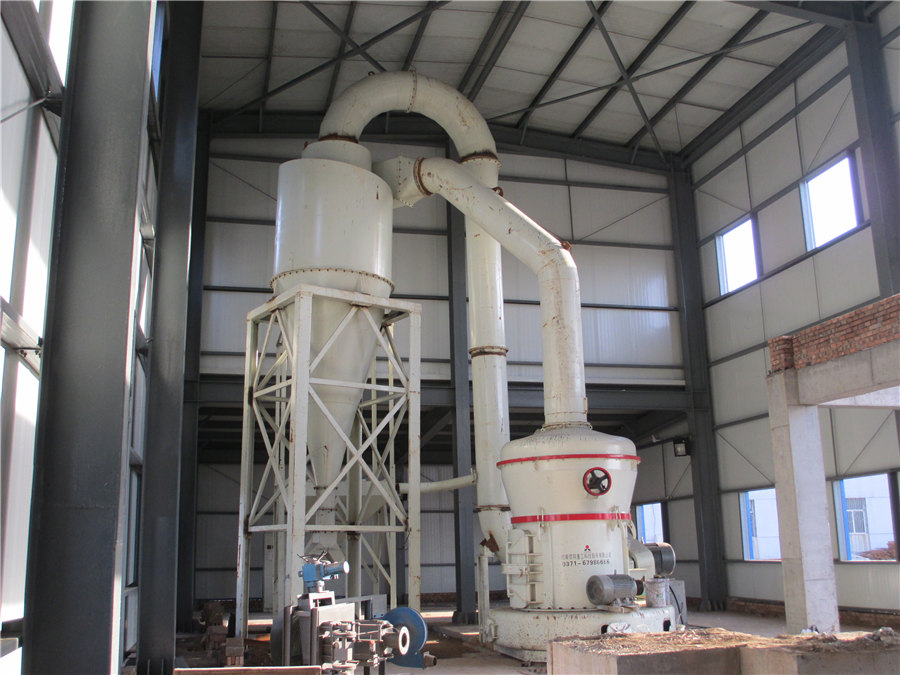
The production of modern corrugated packaging Fefco
The flexographic print process is commonly used for printing on corrugated In the recent years the digital direct print is entering the market offering new possibilities Printing can be done « inline » or « offline » Related Links Additional information 1251 Process Description13 The production of steel at an integrated iron and steel plant is accomplished using several interrelated processes The major operations are: (1) During casting, molten iron flows into runners that lead to transport ladles Slag also flows into the clayfilled iron notch at the base of the hearth During 125 Iron And Steel Production US EPAWhile there is not industry standard specification for the content of iron in lowiron glass, ASTM C1036 standard defines lowiron glass as below: 3218 lowiron glass, n – glass formulated to have transmittance in the visible spectrum higher than that of clear glass of the same thicknessManufacturing Process for Float GlassDownload scientific diagram Simplified Smelter Process Flow Schematic at Waterval Source: (Jacobs, 2006) from publication: Inventory Assessment of the cleaning of Plant Offgas in the recovery Simplified Smelter Process Flow Schematic at Waterval
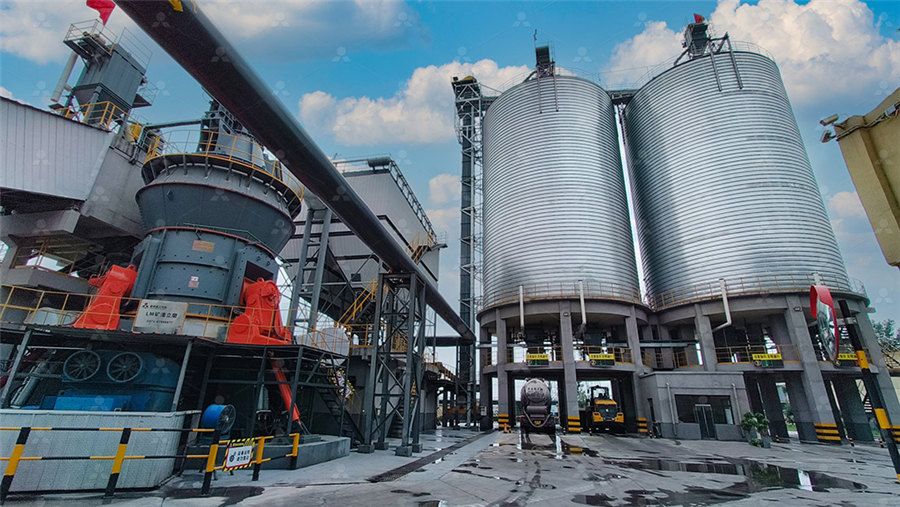
Data Analysis and Prediction Model for Copper Matte Smelting Process
2024年5月13日 During copper matte smelting, a lag exists in the analysis of the smelting results, leading to the production parameters not being effectively adjusted in time As the first smelting process in copper pyrometallurgy, the optimization of the amount of raw material, as well as the prediction and adjustment of slag and matte phases, has become an extremely important step 2020年3月9日 The blast furnace and direct reduction processes have been the major iron production routes for various iron ores (ie goethite, hematite, magnetite, maghemite, siderite, etc) in the past few Experimental Approach to MatteSlag Reactions in 2018年2月21日 About 80% of the worlds’ reserves for platinum group metals (PGMs) are in South Africa’s Bushveld Igneous Complex Processing of PGM involves comminution, flotation, smelting, converting, base metals refinery and Extraction of Platinum Group Metals IntechOpen2019年2月1日 Thus, In this study, we established two thermodynamic process models of iron production process based on the commercial simulator gPROMS, and then we constructed two iron and steel production processes by using the simulation results of the 4220 Jiayuan Song et al / Energy Procedia 158 (2019) 4218–4223 Author name / Energy Procedia 00 (2018) Analysis and Evaluation of Material Flow in Different Steel Production
.jpg)
Comprehensive Review on Metallurgical Upgradation Processes
2022年2月11日 With the vigorously growing demand of the steel industry, corrosion resistance alloys, clean energy industries, and a variety of engineered infrastructure or technology, highgrade nickel ores are being exhausted gradually in the world This review outlines metallurgical processes for nickel production from various nickel sulfide ores resources, particularly focusing 2011年4月11日 This paper first presents some basic criteria for process selection in the copper production chain from mine to metal, and then gives some examples of how the other trends are seen to affect (PDF) Sustainable copper production processes from mine to Copper processing is a complicated process that begins with mining of the ore (less than 1% copper) and ends with sheets of 9999% pure copper called cathodes, which will ultimately be made into products for everyday useThe most common types of ore, copper oxide and copper sulfide, undergo two different processes, hydrometallurgy and pyrometallurgy, respectively, Copper Mining and Processing: Processing Copper OresThis flexibility is impossible in flow production, as the production line is designed to produce a specific product continuously Costeffectiveness: Batch production is often more costeffective than flow production Maintaining Equipment and Processes: Since flow production is geared towards continuous production, From Batch to Flow: Different Approaches to Manufacturing Production
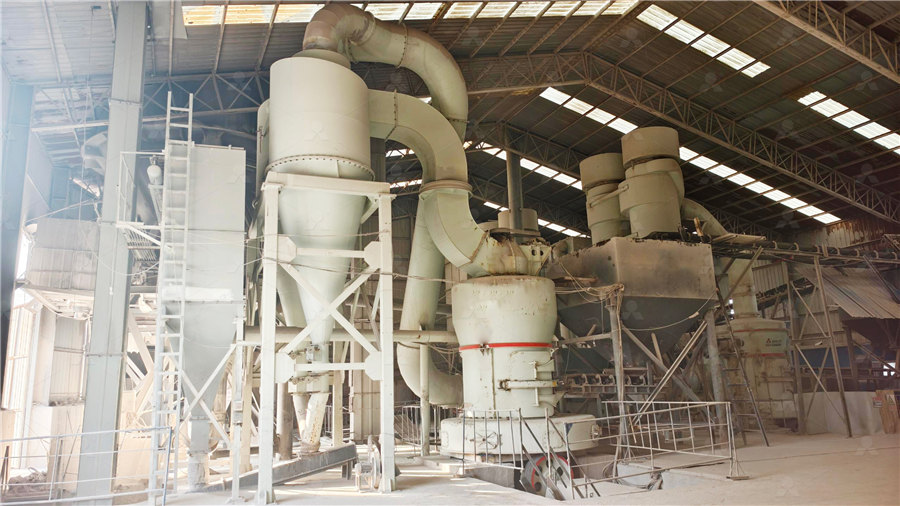
1A Manufacturing Process for Iron and Steel
In addition to the BFBOF process, there is another process which utilizes mainly scrap as an iron source, with some direct reduced iron whenever necessary The direct reduced iron is produced by reducing iron ore with reformed natural gas, whose principal components are hydrogen, carbon monoxide, and methaneCorporation in 1964), which works on direct reduction of ore This process is adopted by worldwide conventional sponge iron industries The production of sponge iron in the plant undertaken is Process flow diagram of the sponge iron plant2024年3月20日 Electrochemical production of iron metal can support a decarbonized process for steelmaking Here, we report a lowtemperature, electrochemical cell that consumes lowcost and abundant iron oxide, salt, and water, while producing both iron and the alkaline electrolyte needed for efficient operation of the cell Coproduction of iron, lye, and chlorine leads to a process Electrochemical chloriron process for iron production from iron 2019年2月6日 PDF The first brochure on the topic "Production process of a lithiumion battery cell" is dedicated to the production process of the lithiumion cell Find, read and cite all the research Lithiumion Battery Cell Production Process
.jpg)
Blast Furnace process optimization for sustainable Iron
2023年9月8日 These actions targeted blast furnace process enhancement, leading to heightened production rates, reduced fuel consumption, and diminished greenhouse gas emissions2013年3月16日 Direct Reduced Iron and its Production Processes satyendra; March 16, 2013; 12 Comments ; ranging from 800 deg C to 1050 deg C is maintained along the length of the kiln at different zones and as the material Direct Reduced Iron and its Production Processes – Primary aluminium production is energy and GHGintensive in which electrolysis is by far the most energy and GHGintensive process This paper’s aim is to study the effects on (1) primary Flow sheet over the steelmaking processes Steel can be 2023年4月5日 The blast furnace and direct reduction processes have been the major iron production routes for various iron ores (ie goethite, hematite, magnetite, maghemite, siderite, etc) in the past few decades, but the challenges of maintaining the iron and steelmaking processes are enormous The challenges, such as cumbersome production routes, scarcity of Recent Trends in the Technologies of the Direct Reduction and
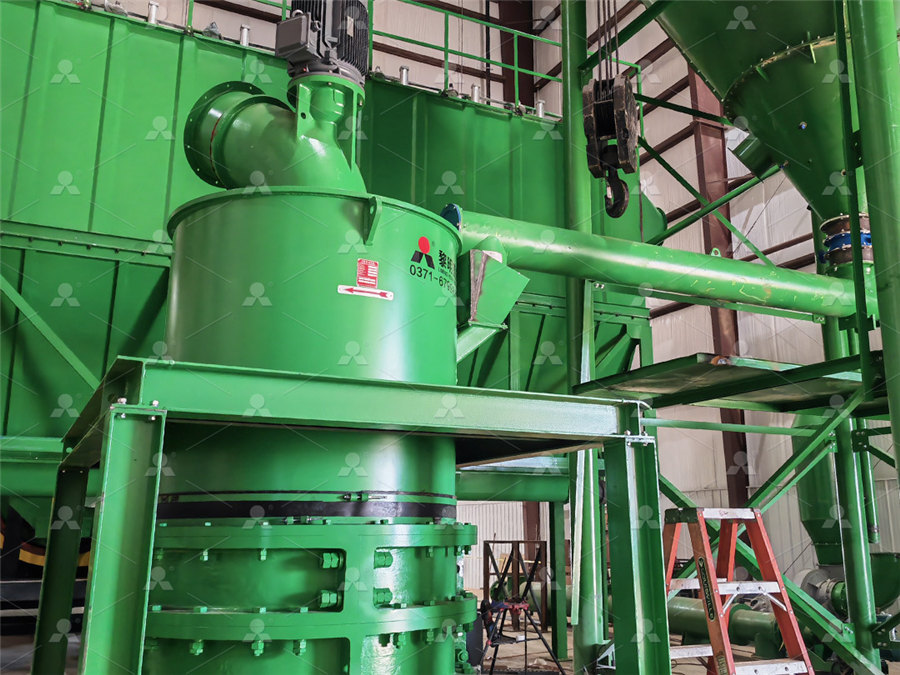
Iron Production Chemistry LibreTexts
As the process continue the molten iron flow down through the furnace and collects at the bottom, where it is removed through an opening in the side When it cools the impure iron is brittle and some cases soft due to the presence of the small impurities, such as sulfur and phosphorus2019年6月22日 Fig 1 Schematic process flow diagram of a continuous electrotinning line The bright bath has several advantages over the matte process which include improved corrosion resistance, This flow melting process enhances the corrosion resistance of the product by formation of an inert tiniron alloy layerTinplate and Process of Tinning IspatGuru2024年8月17日 Our guide provides an overview of the process flow, equipment involved, as well as the principles and characteristics of the casting method Close; Articles Metalworking Pig Iron Pig iron is a primary intermediate product in the iron and steel industry, typically containing a high carbon content ranging from 2% to 669% Casting Production: Process Flow, Equipment, Principle and Primary world nickel production in 2020 was 24307 kt Ni; 69% (16777 kt) of them came from oxidized nickel ores (laterites) and 31% from sulfides Productionwise, 877% of the 16777 kt came from pyrometallurgical and 123% from hydrometallurgical processes For a long time, FeNi had a 20–40% Ni analysis, but in 2006 a new FeNi quality came into the scene This is the The Nickel Production Methods from Laterites and the Greek
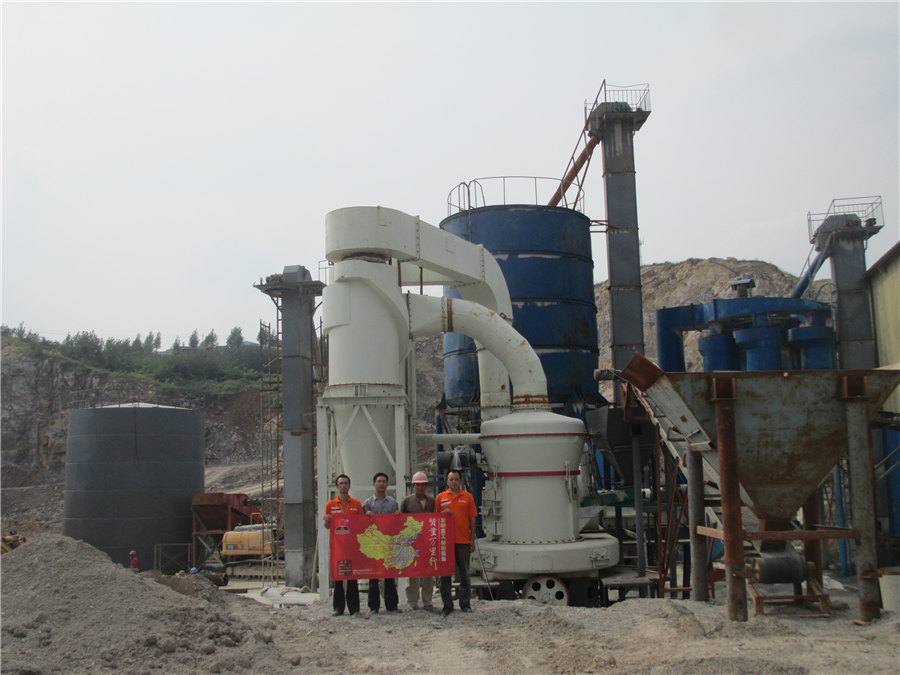
(PDF) i) Direct Reduced Iron: Production ResearchGate
2016年3月30日 In book: Encyclopedia of Iron, Steel, and Their Alloys (pppp 10821108) Chapter: i) Direct Reduced Iron: Production; Publisher: CRC Press, Taylor and Francis Group, New York