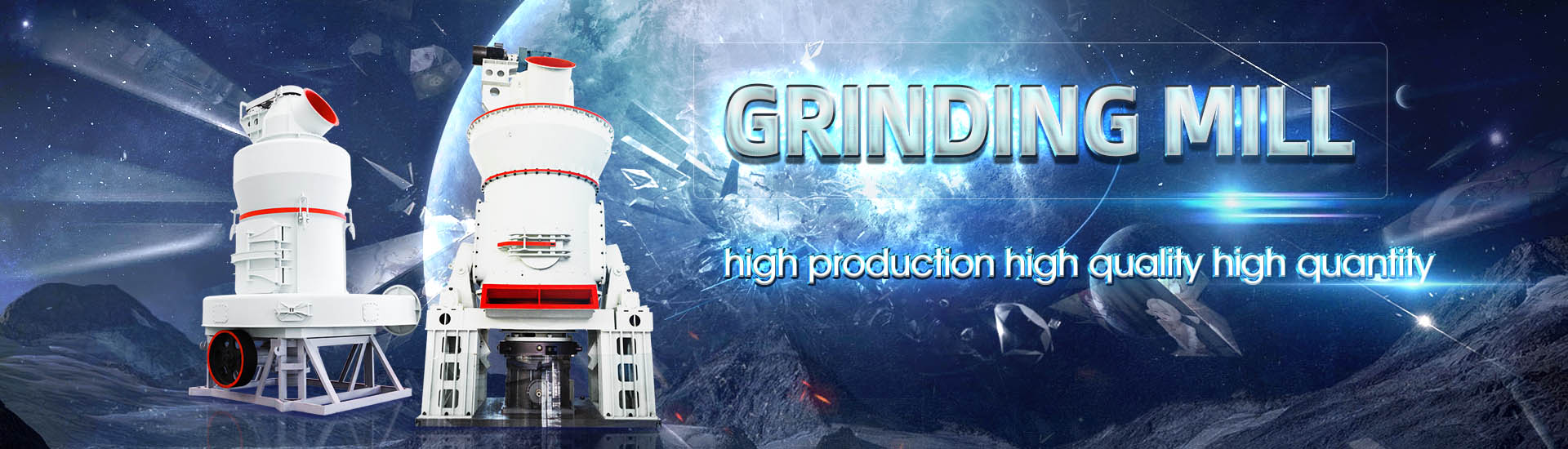
Why add gypsum in the production process of silicate cement
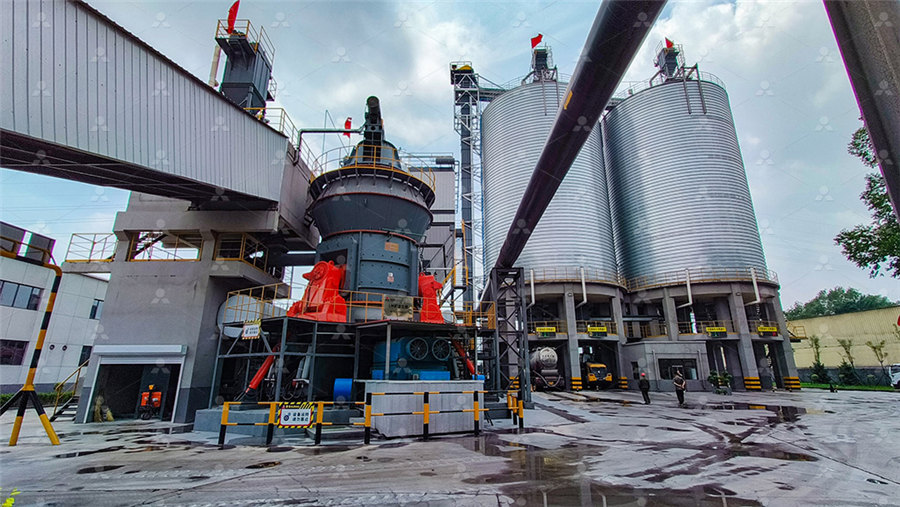
Role of Gypsum in Cement and its Effects –
The main purpose of adding gypsum in the cement is to slow down the hydration process of cement once it is mixed with water The process involved in hydration of cement is that, when the water is added into cement, it starts reacting with 2023年2月20日 Gypsum is an important additive in cement production, used to improve the workability and properties of cement By slowing down the setting time of cement and improving its workability, gypsum makes it easier to The Role of Gypsum in Cement: Why it is Added and Gypsum plays a very important role in controlling the rate of hardening of the cement During the cement manufacturing process, upon the cooling of clinker, a small amount of gypsum is What is the purpose of adding gypsum in cement?1983年1月1日 Gypsum affects the silicate reaction, particularly that of C3S, from a very early stage of hydration Ménétrier et al, [14] measuring changes in the Ca 2 + concentration of the Gypsum in Cement ScienceDirect
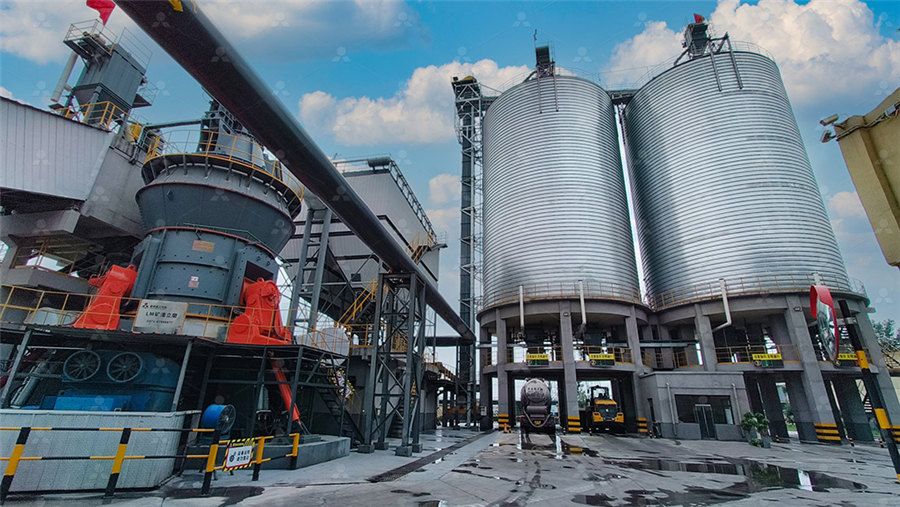
Role of Gypsum in Cement and its Effects Civil Engineering Portal
Gypsum averts the occurrence of flash setting during cement manufacturing It serves to delay the setting time of cement, extending the duration available for mixing, transporting, and placing 2022年3月26日 Gypsum makes up only about 3% or less of cement, but it plays an important role in cement The application of gypsum in cement is mainly to delay the setting time of cement, which isWhat are the Roles of Gypsum in Cement ProductionGypsum (composed of crystallized calcium sulfate ( CaSO4) is added to Portland cement to regulate the extreme setting reaction which occurs in the presence of water The gypsum content ofThe role of gypsum in the production of cement?2004年3月1日 Gypsum renders workability to mortar or concrete by keeping the cement in plastic state at early age of hydration This is achieved by changing the course of hydration of calcium aluminateDual role of gypsum: Set retarder and strength
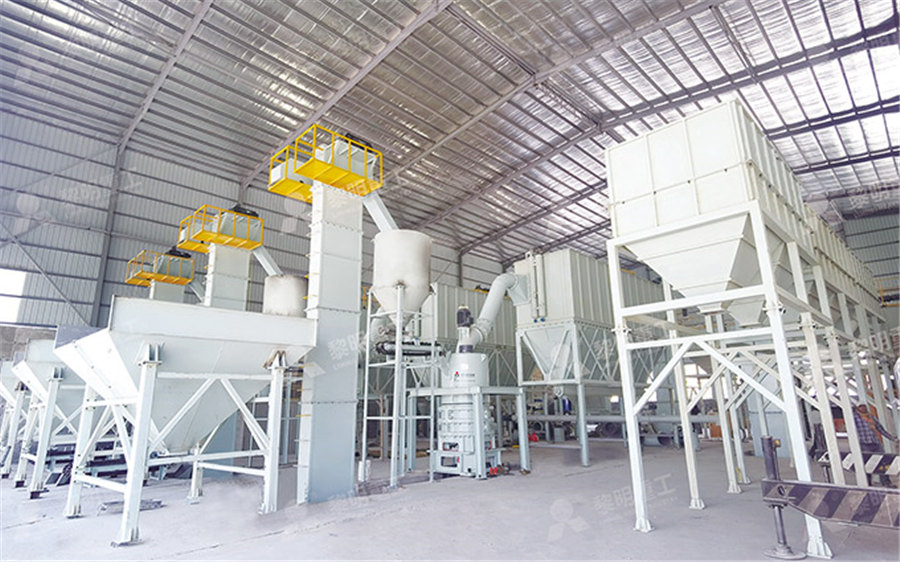
Understanding Gypsum’s Crucial Role in Cement and Its Impact on
Gypsum acts as a guardian, preventing the premature flash setting of cement during the manufacturing process Gypsum puts the brakes on the setting time of cement, extending the 2022年10月27日 Gypsum aids in lengthening the time required for tasks like mixing, laying, and transporting concrete during the concreting process Comparing gypsum cement to nongypsum cement reveals that gypsum What is Gypsum Why Gypsum Added to Cement2021年3月3日 Cement is produced by a hightemperature (about 1500 °C) reaction in a rotary kiln of carefully proportioned and blended ratios of lime (CaO), silica (SiO 2), alumina (Al 2 O 3), and iron oxide (Fe 2 O 3)The production of cement is a chemical process requiring an accurate blend of the previously cited four key organic oxides and the limitation of several undesirable Cement SpringerLinkColored silicate cement, shortened as colored cement, is a kind of hydraulic cementing material made in these two ways: mix white silicate cement clinker, super white gypsum, mineral pigment and additives (water proofing agent, water retaining agent and plasticizer etc) together and grind them to tiny powder as end product; or directly add metallic oxide coloring material to white Silicate Cement an overview ScienceDirect Topics
.jpg)
What are the Roles of Gypsum in Cement Production Medium
2022年3月26日 Gypsum can be used as a raw material, mineralizer, retarder and activator in cement plants Among the components, SO2 is used to balance the sulfuralkali ratio in the calcining of clinker and2019年1月11日 India’s cement production capacity stood at around 502 million tonnes per year (mtpa) in 2018 and is expected to reach 550 mtpa by 2025 Typically, manufacturing cement uses 2 to 4 per cent gypsum per tonne of cement Thus the country requires importing substantial gypsum to cater to the requirements of cement industryThe role of gypsum in cement Indian Cement ReviewIt is worth mentioning that tricalcium silicate is the only compound that provide high early strength to concrete Compounds in Cement and Their Influence on Concrete Strength Tricalcium silicate and Dicalcium silicate The chemical formula for Tricalcium silicate (C 3 S) and Tricalcium silicate (C 3 S) are 3CaOSiO 2 and 2CaOSiO 2, pounds in Cement and Their Influence on Concrete StrengthManufacture Process of Cement Cost of production: High: Low: Overall cost: Costly: Cheaper: Physical state: Raw mix (solid) the cement becomes stiff and the gypsum retards the dissolution of tricalcium aluminates by forming tricalcium sulfoaluminate which is insoluble and prevents too early further reactions of setting and hardeningManufacture of Cement Materials and Manufacturing Process of
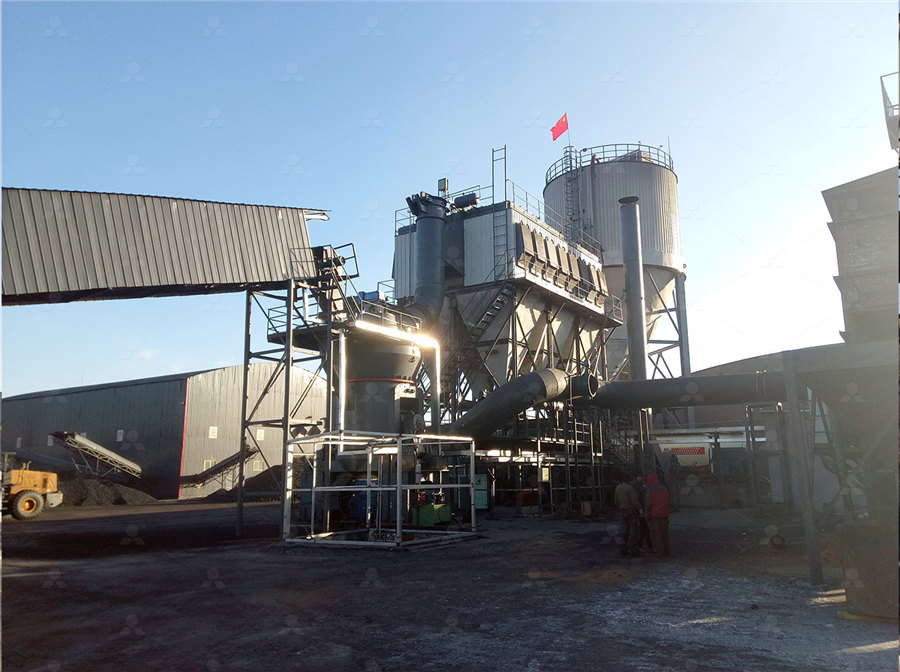
Why Gypsum is Added to Cement? GKToday
2015年10月31日 This early period in the hardening of cement is known as `Setting of Cement’ Why Gypsum is added to Cement? When cement reacts with water, the silicates and aluminates of calcium gets converted to the hydrated colloidal gels and following reactions take place: So it slows the process of fastening 3CaO Al 2 O 3 + 3CaSO 4 2019年10月1日 This paper reviews our understanding of the kinetics and mechanisms of cement hydration It follows closely from papers written for the two previous Chemistry of Cement Conferences [1, 2]The main focus is on the hydration of the tricalcium silicate phase, which dominates the hydration process, especially at early agesAdvances in understanding cement hydration mechanismsHydration products The products of the reaction between cement and water are termed "hydration products" In concrete (or mortar or other cementitious materials) there are typically four main types: Calcium silicate hydrate: this is the main reaction product and is the main source of concrete strength It is often abbreviated, using cement chemists' notation, to "CSH," the Cement hydrationHydration of Portland Cement Introduction Portland cement is a hydraulic cement, hence it derives its strength from chemical reactions between the cement and water The process is known as hydration Cement consists of the following major compounds (see composition of cement): Tricalcium silicate, C 3 S; Dicalcium silicate, C 2 S; Tricalcium Hydration of Portland Cement Pennsylvania State University
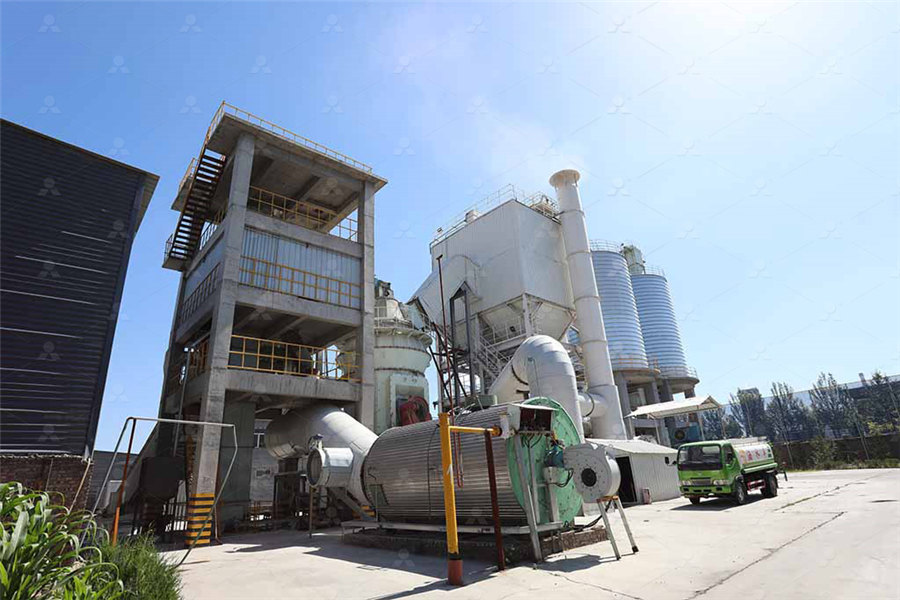
(PDF) An Insight into the Chemistry of Cement—A
2022年12月23日 This review provides an indepth analysis of the complex chemistry of cement, offering valuable insights for researchersCement paste was prepared at a w/c ratio of 029 containing the superplasticizer dosages (SCS 035% bwoc, PCs 02% bwoc) Figure 79 depicts the hydration heat–time curves, showing the effect of SCS and PCs on the cement hydration process The results indicated that SCS can obviously delay the occurrence of hydration heat and make the rate of the production of Cement Hydration Reaction an overview ScienceDirect TopicsDuring the cement hydration process, several products are formed These products are important because they have bonding or bonding value The quality, quantity, continuity, stability, and formation rate of the hydrated product are important Products of the cement hydration process are discussed below Calcium Silicate Hydrates ProductsWhat are the 5 Stages of Cement Hydration ProcessStage of Cement Manufacture There are six main stages of the cement manufacturing process Stage 1: Raw Material Extraction/Quarry The raw cement ingredients needed for cement production are limestone (calcium), sand and clay (silicon, aluminum, iron), shale, fly ash, mill scale, and bauxite The ore rocks are quarried and crushed into smaller pieces of about 6 inchesHow Cement is Made Cement Manufacturing Process
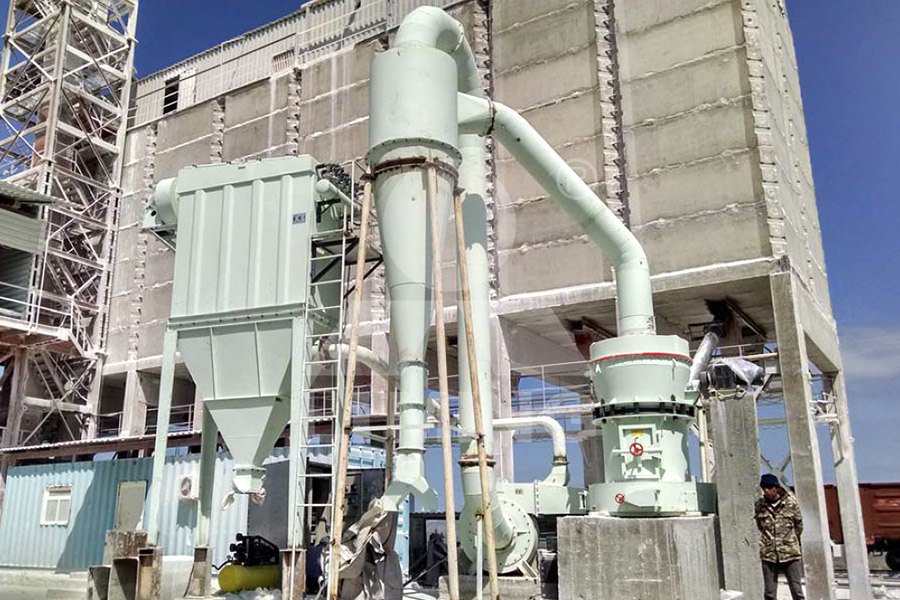
Use of recycled gypsum in the cementbased stabilization of very
2022年6月1日 In particular, as one of the constituents in Portland cement, gypsum plays a nonnegligible role in the CBSC Generally, gypsum itself does not have any cementitious properties However, with the participation of clinker and metakaolin, it can react with calcium aluminate to form the acicular ettringite crystals (see Eq2023年5月1日 Calcium silicate cement (CSC) can be a promising cementitious binder for its reduced CO 2 footprint in comparison with ordinary Portland cement, while its detailed chemical information remains undisclosed Herein, we present thermodynamic calculation results that illustrate the effect of reaction and carbonation degrees on the reaction products of CSC that Exploring reaction and carbonation products of calcium silicate cement However, reading an article or two is perhaps not the best way to get a clear picture of a complex process like cement production To get a more complete and integrated understanding of how cement is made, do have a look at the Understanding Cement book or ebook Reactions in the cement kiln clinkering Understanding CementGypsumbased cement requires less water in the hydration process, contributing to a more efficient and sustainable construction process In conclusion, the unassuming mineral, gypsum, emerges as a silent hero in the realm of cement, regulating its behavior and enhancing its properties, ultimately shaping the structures that stand tall in our built environmentUnderstanding Gypsum’s Crucial Role in Cement and Its Impact
.jpg)
Preparation and properties of calcium aluminate cement with
2023年4月10日 Red mud is a solid waste discharged by the aluminum industry in the production of alumina [1] Red mud can be divided into sintering red mud, Bayer red mud, and Bayer sintering combined red mud based on the different production processes of alumina At present, the Bayer process is the main production process of alumina productionThe ordinary Portland cement is also known as silicate cement we usually add gypsum, fly ash and other raw materials into the cement to realize the different usage of cement An Indepth Guide To Cathode Active Material Production Portland Cement Manufacturing Process In Cement In conclusion, gypsum emerges as a crucial player in the cement production process, exerting control over the setting time and enhancing the overall performance of cementbased materials Its multifaceted impact on the manufacturing and properties of cement positions gypsum as an indispensable element in the construction industryRole of Gypsum in Cement and its Effects Civil Engineering Portal2022年6月1日 Although CF is not as effective as calcium chloride at accelerating the hydration of pastes, it can boost early strength satisfactorily without causing any harm to reinforcement [21]In addition, CF can also effectively promote the early strength development of mortar at low temperatures [22, 23]The degree of solubility of Ca 2+ or OH − ions determines the hydration Effect of calcium formate on the compressive strength, and
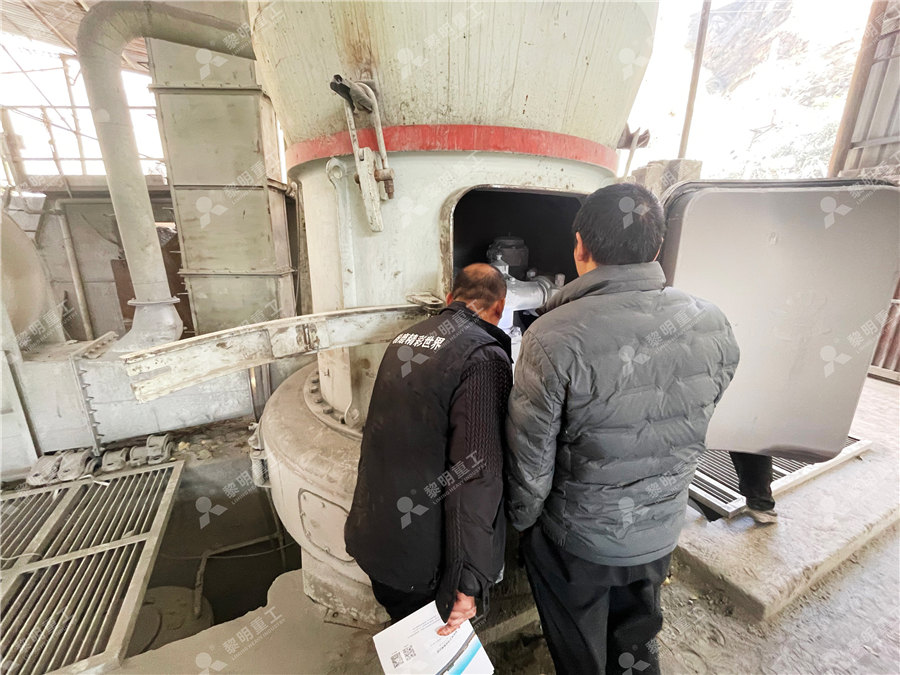
8 Main Cement Ingredients Their Functions Civil Engineering
Silica: Silicon dioxide is known as silica, chemical formula SiO 2 A sufficient quantity of silica should be present in cement to dicalcium and tricalcium silicate Silica imparts strength to cement Silica usually presents to the extent of about 30 percent cement Alumina: Alumina is Aluminium oxideThe chemical formula is Al 2 O 3 Alumina imparts quick setting property to the cement2021年11月1日 Due to the global urbanization, economic development, and increasing rate of the world’s population, the construction of new buildings and infrastructure is increasingAn Overview of EcoFriendly Alternatives as the Replacement of Cement The mixture is then sent to the final grinding process The main purpose of adding gypsum in the cement is to slow down the hydration process of cement once it is mixed with water During the cement manufacturing process, upon the cooling of the clinker, a small amount of gypsum is introduced during the final grinding process Gypsum is added Gypsum is added to cement clinker to: VedantuThus, the reaction of C3A with water is very rapid and is regulated by adding gypsum during production Gypsum (composed of crystallized calcium sulfate (CaSO4) is added to Portland cement to The role of gypsum in the production of cement? ResearchGate
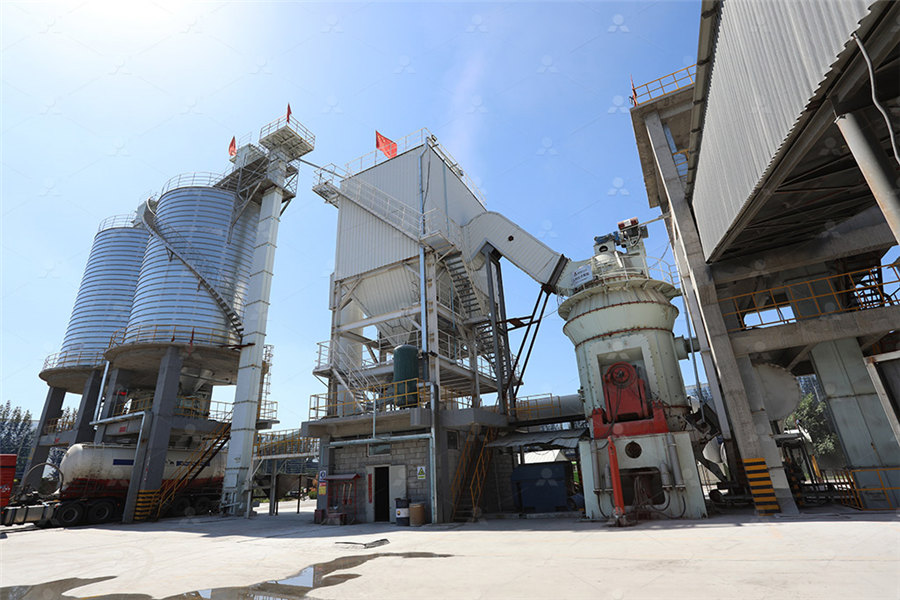
(PDF) Optimization of Gypsum Composition Against Setting Time
2021年2月1日 Gypsum is one of the additive raw materials added to the clinker grinding process that regulate the binding time of cement or commonly known as a retarder2004年3月1日 Gypsum plays a crucial role in cement Though it is used in a small quantity, in the range of 2530 percent in terms of SO3, gypsum's role in cement is significant, more predominantly at early agesDual role of gypsum: Set retarder and strength acceleratorWilliam Aspdin made what could be called ‘mesoPortland cement‘ (a mix of Portland cement and hydraulic lime)Isaac Charles Johnson further refined the production of ‘mesoPortland cement’ (middle stage of development), and claimed to be the real father of Portland cement In 1859, John Grant of the Metropolitan Board of Works, set out requirements for cement to be used in What is the manufacturing process of Portland Cement?2Silica (SiO 2) Silica or silicon dioxide is the second largest quantity of cement ingredients which is about 17 to 25% Silica can be obtained from sand, argillaceous rock etc Sufficient quantity of silica helps for the formation of di Proportions of Cement Ingredients, Their Functions
.jpg)
A Comprehensive Guide to the Cement Manufacturing
2024年9月5日 These raw materials are blended in definite quantities to obtain a uniform and homogeneous raw mix which is very crucial in the production of good quality cement The Manufacturing Process of Cement Now, let’s explore the The production process of silicate cement (also known as Portland cement) is representative in cement production For example, we add gypsum to obtain the ordinary Portland cement and add gypsum and fly ash to obtain the All about the Wet Process of Cement Manufacturing2024年9月4日 Tricalcium Silicate (C3S) Dicalcium Silicate (C2S) Tricalcium Aluminate (C3A) Tetracalcium Aluminoferrite (C4AF) These compounds are crucial for the cement’s strength and setting properties Grinding and Mixing The clinker is then cooled and ground into a fine powder During this process, gypsum is added to control the setting timeThe Science Behind Cement: Understanding the Chemical 2024年11月23日 Cement Extraction, Processing, Manufacturing: Raw materials employed in the manufacture of cement are extracted by quarrying in the case of hard rocks such as limestones, slates, and some shales, with the aid of blasting when necessary Some deposits are mined by underground methods Softer rocks such as chalk and clay can be dug directly by Cement Extraction, Processing, Manufacturing Britannica
.jpg)
Cement Boards 101
2013年12月19日 There are three processing methods employed for the production of fibre cement board, namely the Hatscheck process, the Extrusion process and the Perlite process Hatschek process production of FCB The most common production method used is the Hatschek process, during which unbleached cellulose fibres are repulped in water and then refined Study with Quizlet and memorize flashcards containing terms like What ingredients are used for the production of portland cement?, What is the role of gypsum in the production of portland cement?, What is a typical value for the fineness of portland cement? and moreChapter 6 notes Flashcards QuizletEnvironmental Friendliness: Silicatebased cement reduces carbon footprints by requiring less energy during production and emitting fewer harmful substances Surface Hardening: Silicate densifiers strengthen and seal concrete surfaces, increasing resistance to wear and tear Silicate in Polished Concrete Silicate finds a popular application in Why is Silicate used in cement? Bisley International LLCManufacturing Process Flow Diagram for Cement Raw Materials ⇓ Grinding / Crushing ⇓ Mixing in specific proportions ⇓ Burning of materials in a large rotary kiln, reaching temperatures of up to 1600 °C ⇓ Formation of Clinkers (small balls) ⇓ Cooling Grinding ⇓ Addition of Gypsum powder ⇓ OPC Manufacturing of Cement Composition and Manufacturing of Cement in Civil Engineering

Coal utilization in the cement and concrete industries
2023年1月1日 The utilization of coal in the cement and concrete industries takes three basic forms: (1) as a fuel in the production of cement clinker; (2) ash produced by burning coal in power stations is used as a component in cement rotary kiln feeds; (3) ash produced by burning coal in power stations is used as a mineral additive in concrete mixes