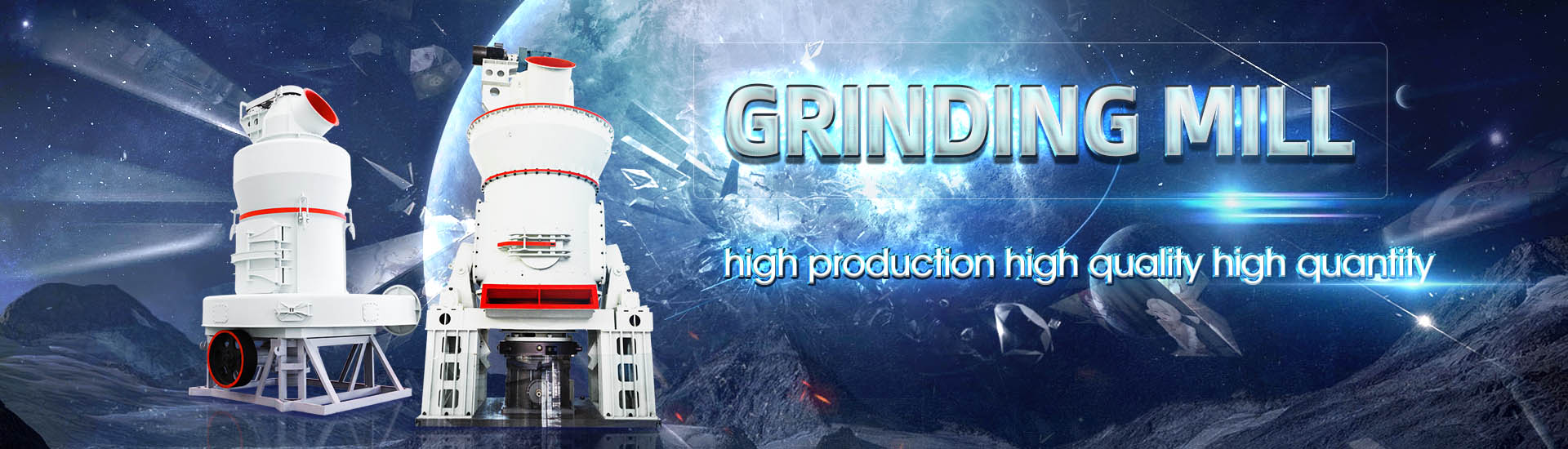
Causes and phenomena of coal mill blockage
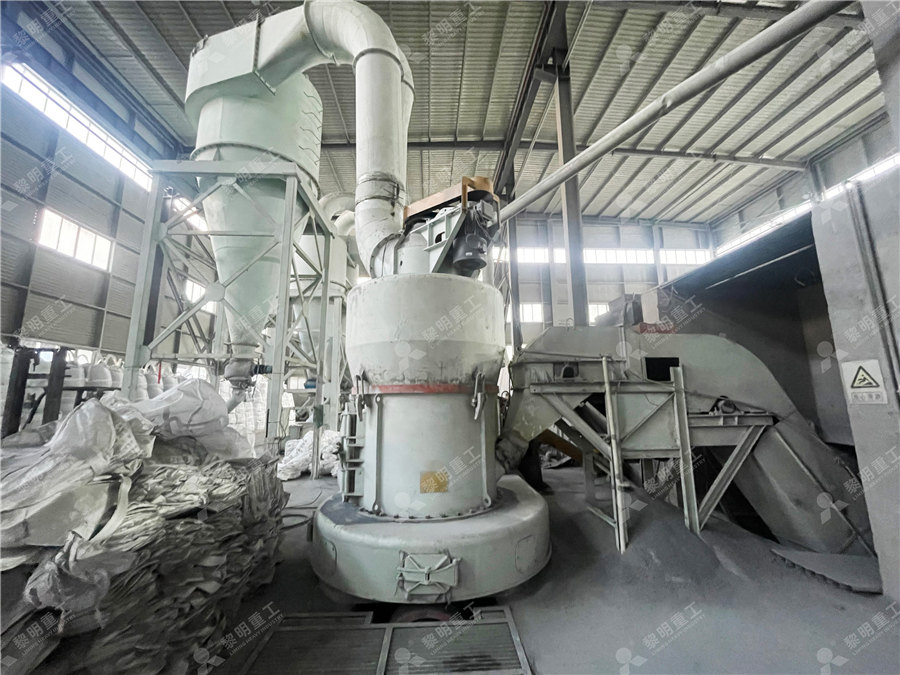
Early Warning of Critical Blockage in Coal Mills Based on Stacked
2020年9月25日 Abstract: Coal mills have a significant influence on the reliability, efficiency, and safe operation of a coalfired power plant Coal blockage is one of the main reasons for coal mill malfunction It is highly essential to accurately detect the critical blockage in coal mills to Coal mills have a significant influence on the reliability, efficiency, and safe operation of a coalfired power plant Coal blockage is one of the main reasons for coal millThe framework of early warning for coal mill ResearchGate2018年5月2日 There are three main fault causes that algorithm detects: feeder blockage, lack of coal in the mill and mill overload Inference mechanism combines the algorithm performance Detection of Malfunctions and Abnormal Working Conditions of a The results demonstrated that the proposed method can effectively detect critical blockage in a coal mill and issue a timely warning, which allows operators to detect potential faults Coal Early Warning of Critical Blockage in Coal Mills Based on Stacked
.jpg)
A Fault Early Warning Method for Coal Mills Based on Causality
2024年9月4日 This paper proposes a method to screen the inputoutput parameters for LSTM based on different feature selection methods, including expert experience, correlation and The experimental results show that it can effectively detect the coal blocking and coal breaking faults of the coal feeder and the coal mill, effectively reduce the system false alarm rate, Research and Application of Coal Blockage Early Warning Coal mills have a significant influence on the reliability, efficiency, and safe operation of a coalfired power plant Coal blockage is one of the mainEarly Warning of Critical Blockage in Coal Mills Based on Stacked 2015年8月1日 In this paper, a review of researches done on the mill control and methods employed for fault diagnosis of coal mills is provided, with the aim of improving performance Review of control and fault diagnosis methods applied to coal
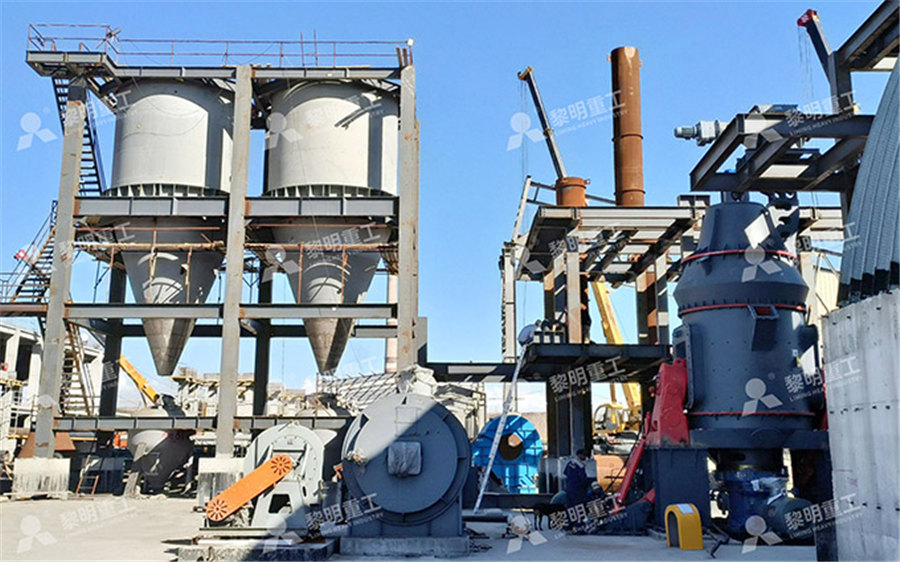
Early Warning of Critical Blockage in Coal Mills Based on Stacked
Coal blockage is one of the main reasons for coal mill malfunction It is highly essential to accurately detect the critical blockage in coal mills to ensure a safe and stable operation of the2020年6月15日 Furthermore, as can be seen from Fig 5, the air to coal ratio of mill A increases to about 30 after the pulverizing mill restarts but stays at around 20 before blockage builds up Such a phenomenon indicates that the air to coal ratio of mill A is too low to provide a sufficient air mass flow rate to suspend the PF particlesInvestigations into the blockage of pulverized fuel pipes on coal 2016年7月7日 Coal mills have a significant influence on the reliability, efficiency, and safe operation of a coalfired power plant Coal blockage is one of the main reasons for coal mill malfunctionIntelligent Decision Support System for Detection and Root Cause 2019年10月4日 ZnO–CaO catalysts were prepared and tested for the synthesis of dimethyl carbonate (DMC) from urea and methanol Meaningfully, the bifunctional catalysts ZnO–CaO exhibited noticeable DMC The Causes Analysis of the Air Preheater and
.jpg)
Optimization and transformation of 300MV units steel ball coal mill
2019年11月7日 Comprehensive treatment,we should have a test on the 300 MV unit steel ball coal mill pulverizing systemAt the same time,analyze the main operating parameters before modificationTransform the 2021年1月28日 coal mills may suffer from blockage, fire, shut down, and enters the coal mill through the inlet pipe, combustion or ignition of coal inside the mill The main causes A Novel MultiMode Bayesian Method for the Processmill can also be improved by modifying mill windbox to reduce reject coal rate and altering throat dimensions by putting inserts With the help of CFD model of mill, potential fire proneCFD Modeling of MPS Coal Mill for Improved Performance and 2020年4月7日 However, no matter what causes the coal blockage, it will lead to the increase of coal/powder storage in the mill and the increase of flow resistance The inlet primary air flo w a nd po wder carryingModeling of Coal Mill System Used for Fault Simulation
.jpg)
Technological advancements in evaluating the performance of
2020年9月11日 Schematic of pulverized coal injection in the lower part (lanceblowpipetuyereracewaycoke bed) of a BF [49] 2015年5月7日 Coal blockage is one of the main reasons for coal mill malfunction It is highly essential to accurately detect the critical blockage in coal mills to ensure a safe and stable operation of the unitReview of Control and Fault Diagnosis Methods Applied to Coal At present, thermal electric generation need be delivered coal through feederRun coal bin and feeder are important composition members, and its structure is that top is cylinder, and the bottom is circular cone, and is as shown in Figure 3; In the course of the work, the coal dust piece leans on gravity fall, causes the coal dust piece in coal spout, to flow, and in the coal dust piece Method and system for preventing coal blockage of raw coal 2024年9月23日 High or low moisture content of the material will cause the die hole to be blocked, causing the pellet machine to not discharge Especially in the case of ring dies with small apertures and large compression ratios, when the tempering moisture content is too high exceeding 1617%, machine blockage and slippage may occur 9Analysis of the causes of frequent blockage of pellet machine
.jpg)
Investigations into the blockage of pulverized fuel pipes on coal
2020年6月15日 The blockage of pulverized fuel (PF) conveying pipes on a coalfired power plant is a hazard accident An indepth understanding of the factors that cause PF pipe blockage provides operators with prior knowledge to avoid such accidents Two representative primary air pipe blockage events are observed on two commercial boilers, respectively2009年1月1日 Wider coal lines and larger power plant units necessitate measures for increasing the capacity of the mills without driving up power consumption and installation costsCFD Modeling of MPS Coal Mill for Improved Monitoring and diagnosis of coal mill systems are critical to the security operation of power plants The traditional datadriven fault diagnosis methods often result in low fault recognition rate Simulation of coal blockage Download Scientific Diagram2018年10月21日 Coal injection with Fe oxides (fine iron ore, and Fe containing waste etc), carbonates, and other O2 rich additives Use of chemical and physical phenomena, eg catalytic, polarizing and other effects Optimization of coal grinding, depending on operating conditions and coal properties Effect of coal rankUnderstanding Pulverized Coal Injection in Blast Furnace
.jpg)
Decision Support System for Coal Mill Fault Diagnosis in Coal
The coal mill under study is a vertical roller type, such as the one available at the PLTU (coalfired steam power plant) Rembang unit, which has two boilers with a steam generator capacity of 513 t/h The schematic of a coal pulverizer mill is provided in Fig 1 Details of these coal mill parameters are presented in Table 1 Coal mill modelingCause analysis:(1)Insufficient primary mixed air volume(2)Phenomenon of coal blockage in coal mill(3)Dynamic separator speed too high(5)Improper adjustment of air throttle ring SHPHGLXP VSHHGFRDOPLOO ResearchGateAdditionally, large quantity of coal supply required for the same load, which is easy to cause coal mill blockage and other faults When the coal mill is operating under normal conditions, the The monitoring indicator of coal mill under normal conditionThe results demonstrated that the proposed method can effectively detect critical blockage in a coal mill and issue a timely warning, which allows operators to detect potential faults Coal mills have a significant influence on the reliability, efficiency, and safe operation of a coalfired power plant Coal blockage is one of the main reasons for coal mill malfunctionEarly Warning of Critical Blockage in Coal Mills Based on Stacked
%3C1PGHL[2}HK_]YT.jpg)
Coal Mill an overview ScienceDirect Topics
A simple energy balance model of the coal mill is derived in (Odgaard and Mataji 2006), this model is based on a more detailed model found in (Rees and Fan 2003)In this model the coal mill is seen as one body with the mass m mThe following variables are defined: T(t) is the temperature in the coal dust flow in the mill, ṁ PA (t) is the primary air mass flow, T PA (t) is 32 Insufficient output of coal mill Cause analysis: (1) the primary air volume was insufficient(2) Cause analysis:(1)Insufficient primary mixed air volume(2)Phenomenon of coal blockage in coal mill(3)Dynamic separator speed too high(5)Improper adjustment of air throttle ring(6)Coal has high water content, SHPHGLXPVSHHGFRDOPLOO IOPscienceIOP Publishing % %% )Optimization and transformation of 300MV units steel ball coal mill 2003年12月31日 Request PDF Chapter 2 Fouling phenomena during microfiltration: Effects of pore blockage, cake filtration, and membrane morphology Membrane fouling remains a major problem in applications of Chapter 2 Fouling phenomena during microfiltration: Effects of
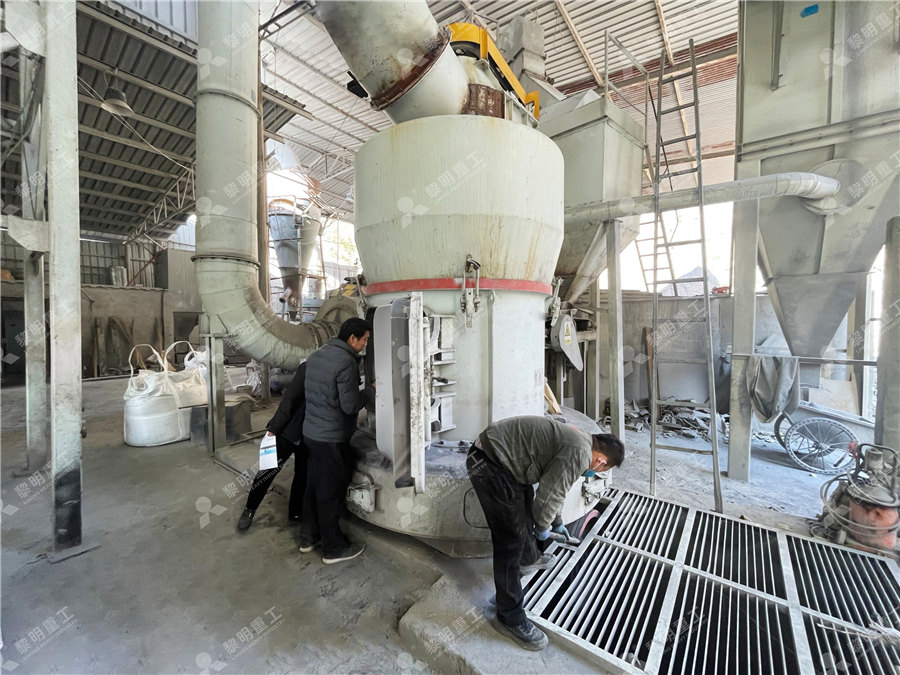
Derivation and validation of a coal mill model for control
2012年5月1日 The input mass flow of the raw coal to the mill is difficult to measure as well; typically, the conveyor belt speed is used for this purpose Additionally the varying coal quality, eg Hardgrove Grindability Index (HGI) and moisture, of coal fed to the mills varies, and general mill wear cause parameter changes (Fan, Rees, Parker, 1997)2007年3月1日 Ventilation mill for grinding coal is one of the main steam power plants in the system that makes a significant effect on the level of energy efficiency with its workCauses of pulverizedcoal leakage from a race pulverizer and its 2020年9月25日 Coal mills have a significant influence on the reliability, efficiency, and safe operation of a coalfired power plant Coal blockage is one of the main reasons for coal mill malfunction It is highly essential to accurately detect the critical blockage in coal mills to ensure a safe and stable operation of the unit Taking advantage of unsupervised learning methods and Early Warning of Critical Blockage in Coal Mills Based on Stacked Coal grinding is a critical process in various industries, particularly in power generation and cement production However, the process involves significant safety risks due to the combustible nature of coal dust and the mechanical hazards posed by the operation of the mill Ensuring safety during coal grinding is essential to prevent accidents, exAspects of Coal Mill Safety Coal Mill Safety, Explosion and Fire
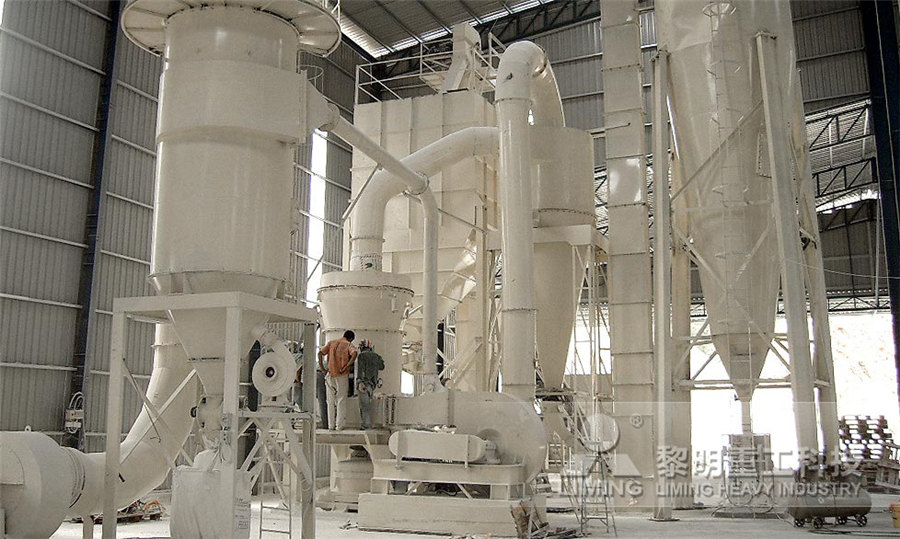
Research and Application of Coal Blockage Early Warning
the coal pulveriz ing system, the coal feeder and the coal mill run at a continuous high load for a long time will lead to various failures in the coal pulverizing system, and a large number of2013年4月1日 Observation of the bowl mill at site after failure indicated that hard lumps were present in the bull ring segment, which clearly made it evident that there was sudden jamming of it which in turn Root cause analysis of bowlmill pinion shaft failures2022年1月26日 One of the main causes of damage to the elements of coalfired boilers installations, leading to breakdowns and, consequently, a shutdown of the block, are erosive processesNumerical Study of the Erosion Process and Transport of Pulverized Coal 2020年6月15日 Furthermore, as can be seen from Fig 5, the air to coal ratio of mill A increases to about 30 after the pulverizing mill restarts but stays at around 20 before blockage builds up Such a phenomenon indicates that the air to coal ratio of mill A is too low to provide a sufficient air mass flow rate to suspend the PF particlesInvestigations into the blockage of pulverized fuel pipes on coal
.jpg)
Intelligent Decision Support System for Detection and Root Cause
2016年7月7日 Coal mills have a significant influence on the reliability, efficiency, and safe operation of a coalfired power plant Coal blockage is one of the main reasons for coal mill malfunction2019年10月4日 ZnO–CaO catalysts were prepared and tested for the synthesis of dimethyl carbonate (DMC) from urea and methanol Meaningfully, the bifunctional catalysts ZnO–CaO exhibited noticeable DMC The Causes Analysis of the Air Preheater and 2019年11月7日 Comprehensive treatment,we should have a test on the 300 MV unit steel ball coal mill pulverizing systemAt the same time,analyze the main operating parameters before modificationTransform the Optimization and transformation of 300MV units steel ball coal mill 2021年1月28日 coal mills may suffer from blockage, fire, shut down, and enters the coal mill through the inlet pipe, combustion or ignition of coal inside the mill The main causes A Novel MultiMode Bayesian Method for the Process
.jpg)
CFD Modeling of MPS Coal Mill for Improved Performance and
mill can also be improved by modifying mill windbox to reduce reject coal rate and altering throat dimensions by putting inserts With the help of CFD model of mill, potential fire prone2020年4月7日 However, no matter what causes the coal blockage, it will lead to the increase of coal/powder storage in the mill and the increase of flow resistance The inlet primary air flo w a nd po wder carryingModeling of Coal Mill System Used for Fault Simulation2020年9月11日 Schematic of pulverized coal injection in the lower part (lanceblowpipetuyereracewaycoke bed) of a BF [49] Technological advancements in evaluating the performance of 2015年5月7日 Coal blockage is one of the main reasons for coal mill malfunction It is highly essential to accurately detect the critical blockage in coal mills to ensure a safe and stable operation of the unitReview of Control and Fault Diagnosis Methods Applied to Coal
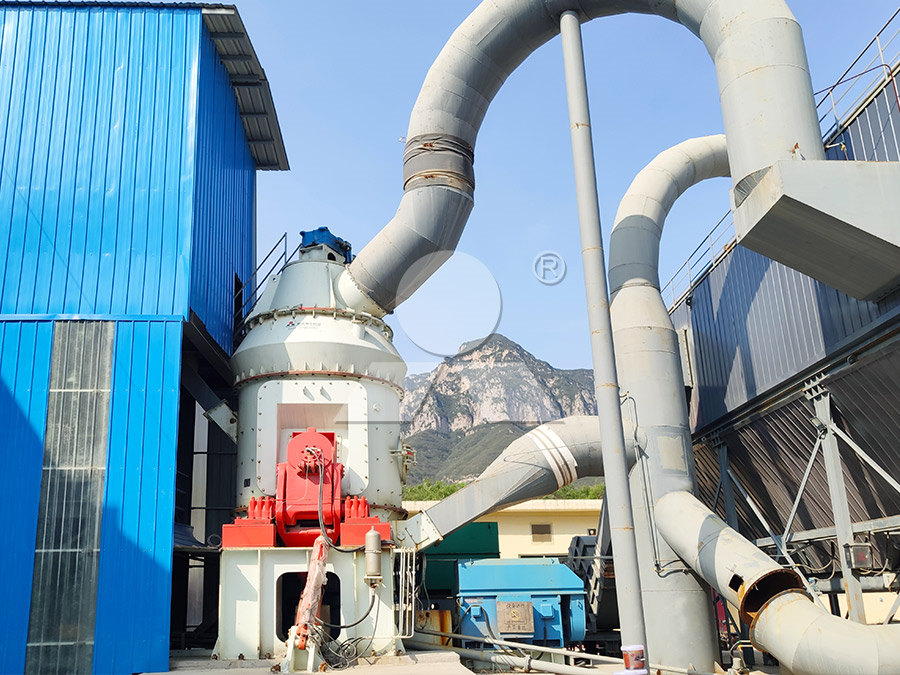
Method and system for preventing coal blockage of raw coal
At present, thermal electric generation need be delivered coal through feederRun coal bin and feeder are important composition members, and its structure is that top is cylinder, and the bottom is circular cone, and is as shown in Figure 3; In the course of the work, the coal dust piece leans on gravity fall, causes the coal dust piece in coal spout, to flow, and in the coal dust piece