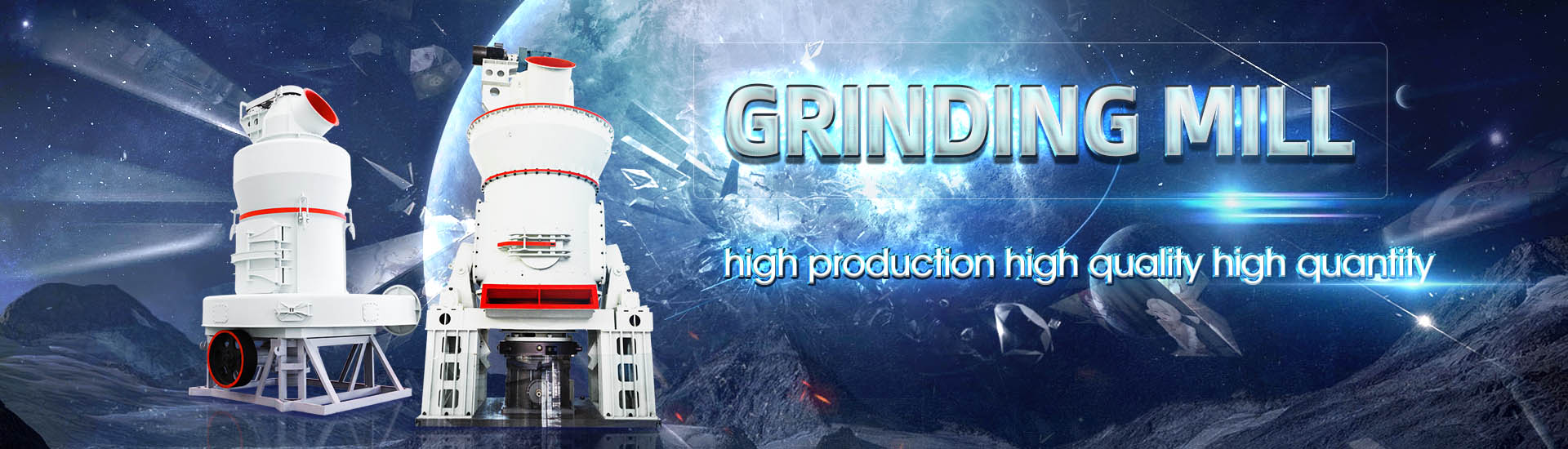
What is the method of grinding mechanical pig iron
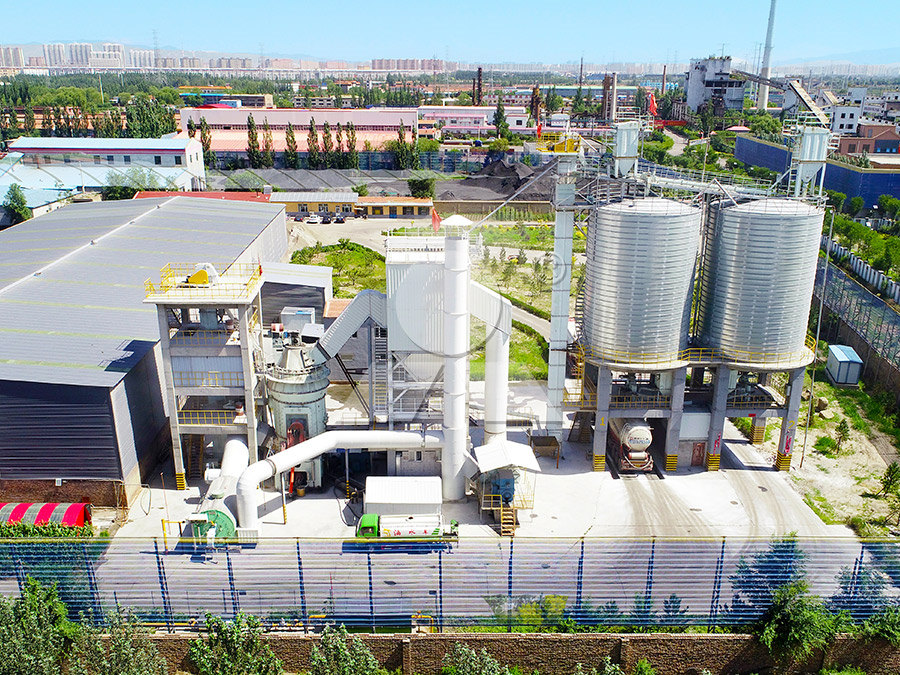
How to Manufacture Pig Iron: How Pig Iron is made?
Following three distinct operations are involved in the manufacturing process of pigiron: (1) Dressing (2) Calcination and roasting (3) Smelting (1) Dressing: The iron ores as obtained from mines are crushed into pieces of size of 25 mm diameter This is achieved in the rock crushers 2013年4月1日 It is produced when liquid iron (hot metal) is cast in the pig moulds Pig iron is basically an alloy of iron (Fe), carbon (C), silicon (Si), and manganese (Mn) It also contains Pig Iron IspatGuru2018年6月21日 After the pig iron has been tapped, it must be desulfurized and oxidized with oxygen (refining) to obtain crude steel Due to its high carbon content and relatively high From pig iron to crude steel tecscienceThis book covers the process of production of pig iron and describes topics such as raw materials for the steel production, sintering process, pelletizing process, the production of coke, the Operations and Basic Processes in Ironmaking SpringerLink

Puddling process Iron Smelting, Refining Casting Britannica
puddling process, Method of converting pig iron into wrought iron by subjecting it to heat and frequent stirring in a furnace in the presence of oxidizing substances (see oxidationreduction) 2023年4月20日 The smelting process of highmanganese pig iron is studied to determine ways to efficiently utilize the byproduct of manganeserich slag This process consists of two Study on Efficient Use of HighManganese Pig Iron Wiley Online Being manufactured from selected iron ore or ilmenite sources, Pig Iron has a consistent and predictable chemical and physical analysis which allows better control and variability of Pig Iron: a valueadding feedstock for ferrous casting Metallics2024年4月1日 Iron ore serves as an essential feedstock for steel manufacturers, with approximately 70% of the annual pig iron production from iron ore smelting relying on the integrated steelmaking process The percentage of iron ore undergoing beneficiation varies globally, dependent on ore type and qualityA critical review on metallurgical recovery of iron from iron ore
.jpg)
Principles of Modern Grinding Technology
2013年1月1日 Coverage includes abrasives and superabrasives, wheel design, dressing technology, machine accuracy and productivity, machine design, highspeed grinding technology, cost optimization, ultra high purity pig iron (also known as nodular pig iron): used in the manufacture of ductile [also known as nodular or spheroidal graphite – SG] iron castings There are also various subtypes, for example low manganese basic pig iron, semi Pig Iron International Iron Metallics AssociationThe term cast iron refers to ironcarbonsilicon alloys that contain 254 % carbon and usually 13 % silicon In grey irons, the carbon is present as graphite; in white cast iron it is present in the form of iron carbide and alloy carbides Cast iron has good castability and machinability, as well as moderate mechanical propertiesMetallography of cast iron insight StruersMechanical grinding refers to the physical mixing of presynthesized or commercially obtainable catalysts with gC 3 N 4 precursors This method is an alternative to improve the interface between the nanocrystals and gC 3 N 4 without adding any agent It also showed that the use of properties of composite material could be significantly improved in comparison to blend due to Mechanical Grinding an overview ScienceDirect Topics
.jpg)
IS 15338 (2003): Spectrometric Analysis of Cast Iron by Direct
1S 12308’ Methods for chemical analysis of cast iron and pig iron’ in parts covers the chemical analysis of various constituents in cast iron and pig iron Since instrumental techniques are now widely adopted for rapid and accurate analysis a need was felt to prepare this standard In this standard the condensed spark method is specified forGuide for manufacturing and making Pig Iron Following three distinct operations are involved in the manufacturing process of pigiron: (1) Dressing (2) Calcination and roasting (3) Smelting (1) Dressing: The iron ores as obtained from mines are crushed into pieces of size of 25 mm diameter This is achieved in the rock crushers of ordinary type The crushing of ores helps in How to Manufacture Pig Iron: How Pig Iron is made?2018年11月21日 I have got a glimpse of a method of causing a pistonrod to move up and down perpendicularly, by only fixing it to a piece of iron upon the beam, without chains, or perpendicular guides, or untowardly frictions, arch heads, or other pieces of clumsiness” 361The First Wave of Industrial Revolution: Cotton Textiles and Pig Iron Pig iron used to manufacture ductile iron Pig iron, also known as crude iron, is an intermediate good used by the iron industry in the production of steelIt is developed by smelting iron ore in a blast furnacePig iron has a high carbon content, typically 38–47 %, [1] along with silica and other dross, which makes it brittle and not useful directly as a material except for limited Pig iron Wikipedia
.jpg)
What is Grinding? Understanding the Basics and Applications
2024年7月17日 Grinding is a complex abrasive machining process that uses a grinding wheel as a cutting tool It’s known for producing very fine finishes and extremely accurate dimensions on metal parts Grinding uses a rotating grinding wheel made up of abrasive particles, which act like tiny cutting tools Now, let’s get into the details of what is 2017年3月4日 Ball mills are used for wet grinding iron ore, g old/copper ore, nickel ore and other ores, as wel l as lime/limestone for flue gas desulphurisat ion systems, coal and other raw materials Rod mill :SIZE REDUCTION BY GRINDING METHODS2024年8月18日 (4) Alloy Pig Iron: A specialized category of pig iron, alloy pig iron is intentionally produced with elevated levels of specific alloying elements such as silicon, manganese, nickel, or chromium Common examples include Pig Iron vs Wrought Iron: The Differences ExplainedIron processing, use of a smelting process to turn the ore into a form from which products can be fashioned Included in this article also is a discussion of the mining of iron and of its preparation for smelting Iron (Fe) is a relatively dense Iron processing Definition, History, Steps, Uses,
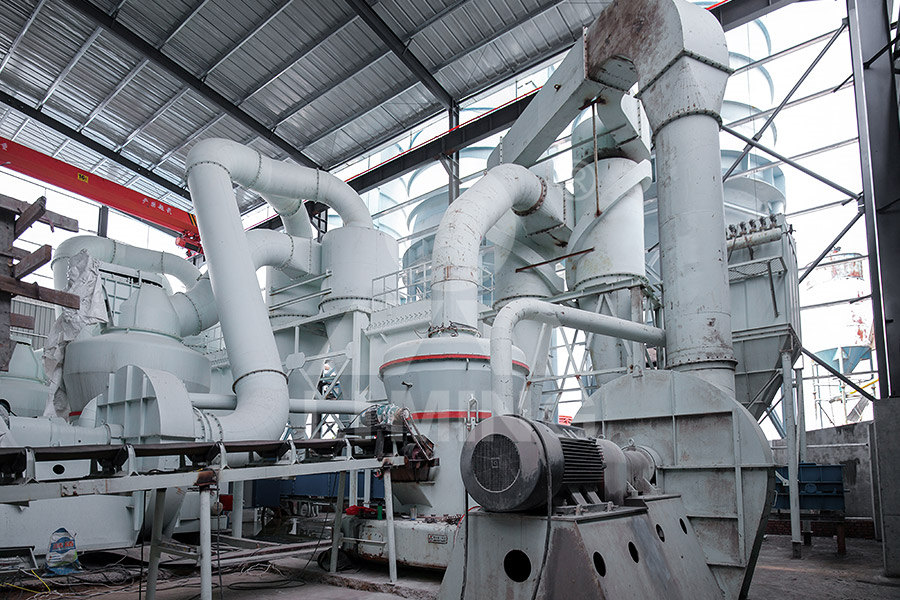
From pig iron to crude steel tecscience
2018年6月21日 Pig iron must therefore be desulphurised and decarburised! Desulfurization The refining of pig iron into steel is carried out in liquid form For this purpose, the pig iron produced in the ironworks is first collected in large mixing containers (called pig iron mixers) with a capacity of up to 1800 tonsPig iron is also very low in nitrogen content: when pig iron melts into the steel bath, it provides carbon which is blown out of the steel bath with oxygenThe generation of carbon monoxide in the steel bath helps to strip out dissolved nitrogen from the bathOperations that use large proportions of pig iron in the EAF are capable of tapping steel with nitrogen contents less than 20 ppmFrequently Asked Questions International Iron Metallics 2020年9月1日 Meanwhile, manufactured iron scrap cakes replaced pig iron were added into an intermediate frequency furnace, melted into liquid iron and cast into sound castings Effect of iron scrap cakes on microstructure and mechanical properties A novel recycling and reuse method of iron scraps from machining In general, the pig iron is an intermediate product of the iron industryPig iron, known also as crude iron, is produced by the blast furnace process and contains up to 4–5% carbon, with small amounts of other impurities like sulfur, magnesium, phosphorus, and manganesePig iron is supplied in a variety of ingot sizes and weights, ranging from 3 kg up to more than 50 kgWhat is Pig Iron – Crude Iron Definition Material Properties
.jpg)
Effects of Magnesium Variation and Heat Treatment on Mechanical
2017年9月30日 The effects of magnesium variation and austempering heat treatment on mechanical and microstructural properties of ductile iron produced using the rotary furnace were investigatedGrinding technology can be applied in a number of ways to improve manufacturing processes For example, It can be used to improve the surface finish of machined parts; To improve dimensional accuracy; Increase productivity; It can also be used to prepare surfaces for further finishing processes, such as polishing or platingWhat is Grinding? – Working Principles, Applications Use of 2021年11月3日 The method of metal and graphite inclusions extraction proposed here, provides mechanical or explosive grinding of solid slag to 0–10 mm in dimension, followed by gravitymagnetic and aeration separation of the formed fine slagmetalgraphite mechanical mixture The process is very timeconsuming, costly, and environmentally unsafe (dusty)A new technological approach to the granulation of slag melts of The haematite is widely used for the production of pig iron Since pyrite contains only 30 to 40% iron, therefore it is not used for manufacturing pig iron The pig iron is obtained from the iron ores in the following steps: 1 Concentration It is the process of removing the impurities like clay, sand etc from the iron ore by washing with Pig Iron and Its Manufacturing Mechanical Engineering
.jpg)
Why pig iron is called pig iron? QuickAnimals
2022年4月5日 Pig iron, also known as crude iron, is an intermediate product of the iron industry in the production of steel which is obtained by smelting iron ore in a blast furnace When the metal had cooled and hardened, the smaller ingots (the “pigs”) were simply broken from the runner (the “sow”), hence the name “ pig iron “2022年5月27日 The main chemical component of highsilicon iron tailings (HSITs) is SiO2; HSITs also include some oxides such as Al2O3 and CaO Mechanical activation can reduce the particle size of HSITs and enhance their pozzolanic activity such that they can be used as a type of mineral admixture for cementbased materials (CBMs) This study aims to investigate the On the grinding effects of highsilicon iron tailings2017年10月17日 Smelting Reduction Figure 2: The smelt reduction vessel (SRV) is the core technology component of the Hismelt process Source: RioTinto While years of ironmaking technology innovations have optimized blast furnace productivity, two alternative processes—smelting reduction and direct iron reduction— are growing in adoption The From Ore to Iron with Smelting and Direct Iron ReductionThe openhearth furnace is one way to create steel from pig iron The pig iron, limestone and iron ore go into an openhearth furnace It is heated to about 1,600 degrees F (871 degrees C) The limestone and ore form a slag that floats on the surface Impurities, including carbon, are oxidized and float out of the iron into the slagHow Iron and Steel Work HowStuffWorks
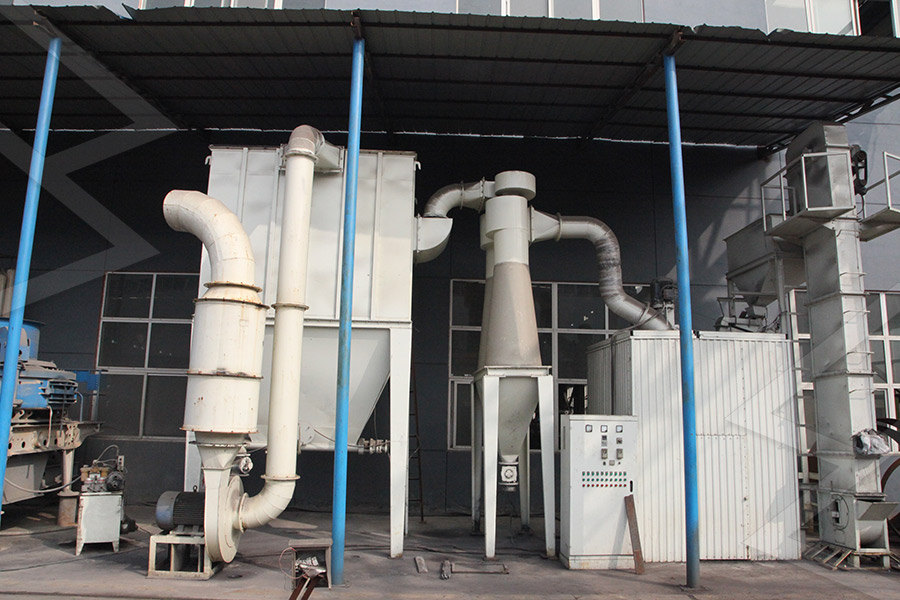
Grinding in Ball Mills: Modeling and Process Control
2012年6月1日 As the cylinder starts to rotate, the grinding balls inside the cylinder crush and grind the feed material, generating mechanical energy that aids in breaking bonds, activating the catalyst, and Purpose The article is aimed to determine effect of the chemical composition of FeCCrMnNi cast iron on the chromium content in the metallic base, carbides and the coefficient of interphase The chemical composition cast iron Download Tablemechanical properties where ductile iron offers the designer the option of choosing high ductility, with grades guaranteeing more than 18% elongation, or high strength, with tensile strengths exceeding 825 MPa [7], [8] In addition to the cost advantages offered by all castings, ductile iron, when compared to steel and malleable iron castings,Processing Techniques and Productions of Ductile Iron: A Diversity of pig iron properties Pig iron usually consists of about 92 percent iron, three to four percent carbon, and varying amounts of silicon (05 to 3%), manganese (05 to 6%), phosphorous (01 to 2%) and traces of sulfur (001 to 005 percent) Grey pigiron is produced when the pigiron is cooled slowly and the carbon settles out as Pig Iron Production – Interstahl
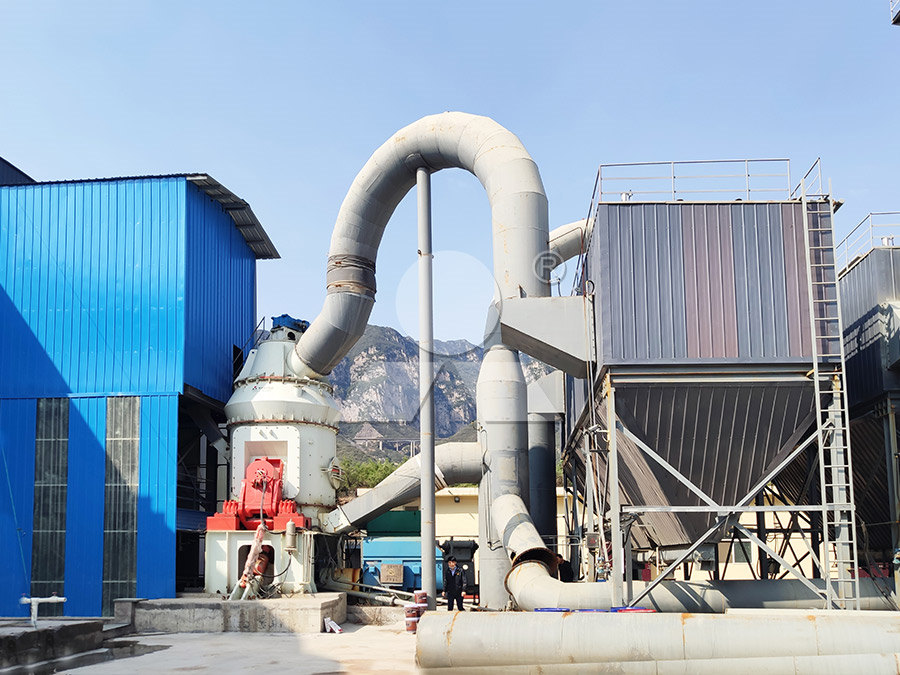
The six main steps of iron ore processing Multotec
When iron ore is extracted from a mine, it must undergo several processing stages Six steps to process iron ore 1 Screening We recommend that you begin by screening the iron ore to separate fine particles below the crusher’s CSS before the crushing stage2024年4月1日 Iron ore serves as an essential feedstock for steel manufacturers, with approximately 70% of the annual pig iron production from iron ore smelting relying on the integrated steelmaking process The percentage of iron ore undergoing beneficiation varies globally, dependent on ore type and qualityA critical review on metallurgical recovery of iron from iron ore 2013年1月1日 Coverage includes abrasives and superabrasives, wheel design, dressing technology, machine accuracy and productivity, machine design, highspeed grinding technology, cost optimization, ultra Principles of Modern Grinding Technologyhigh purity pig iron (also known as nodular pig iron): used in the manufacture of ductile [also known as nodular or spheroidal graphite – SG] iron castings There are also various subtypes, for example low manganese basic pig iron, semi Pig Iron International Iron Metallics Association
.jpg)
Metallography of cast iron insight Struers
The term cast iron refers to ironcarbonsilicon alloys that contain 254 % carbon and usually 13 % silicon In grey irons, the carbon is present as graphite; in white cast iron it is present in the form of iron carbide and alloy carbides Cast iron has good castability and machinability, as well as moderate mechanical propertiesMechanical grinding refers to the physical mixing of presynthesized or commercially obtainable catalysts with gC 3 N 4 precursors This method is an alternative to improve the interface between the nanocrystals and gC 3 N 4 without adding any agent It also showed that the use of properties of composite material could be significantly improved in comparison to blend due to Mechanical Grinding an overview ScienceDirect Topics1S 12308’ Methods for chemical analysis of cast iron and pig iron’ in parts covers the chemical analysis of various constituents in cast iron and pig iron Since instrumental techniques are now widely adopted for rapid and accurate analysis a need was felt to prepare this standard In this standard the condensed spark method is specified forIS 15338 (2003): Spectrometric Analysis of Cast Iron by Direct Guide for manufacturing and making Pig Iron Following three distinct operations are involved in the manufacturing process of pigiron: (1) Dressing (2) Calcination and roasting (3) Smelting (1) Dressing: The iron ores as obtained from mines are crushed into pieces of size of 25 mm diameter This is achieved in the rock crushers of ordinary type The crushing of ores helps in How to Manufacture Pig Iron: How Pig Iron is made?
.jpg)
The First Wave of Industrial Revolution: Cotton Textiles and Pig Iron
2018年11月21日 I have got a glimpse of a method of causing a pistonrod to move up and down perpendicularly, by only fixing it to a piece of iron upon the beam, without chains, or perpendicular guides, or untowardly frictions, arch heads, or other pieces of clumsiness” 361Pig iron used to manufacture ductile iron Pig iron, also known as crude iron, is an intermediate good used by the iron industry in the production of steelIt is developed by smelting iron ore in a blast furnacePig iron has a high carbon content, typically 38–47 %, [1] along with silica and other dross, which makes it brittle and not useful directly as a material except for limited Pig iron Wikipedia2024年7月17日 Grinding is a complex abrasive machining process that uses a grinding wheel as a cutting tool It’s known for producing very fine finishes and extremely accurate dimensions on metal parts Grinding uses a rotating grinding wheel made up of abrasive particles, which act like tiny cutting tools Now, let’s get into the details of what is What is Grinding? Understanding the Basics and Applications