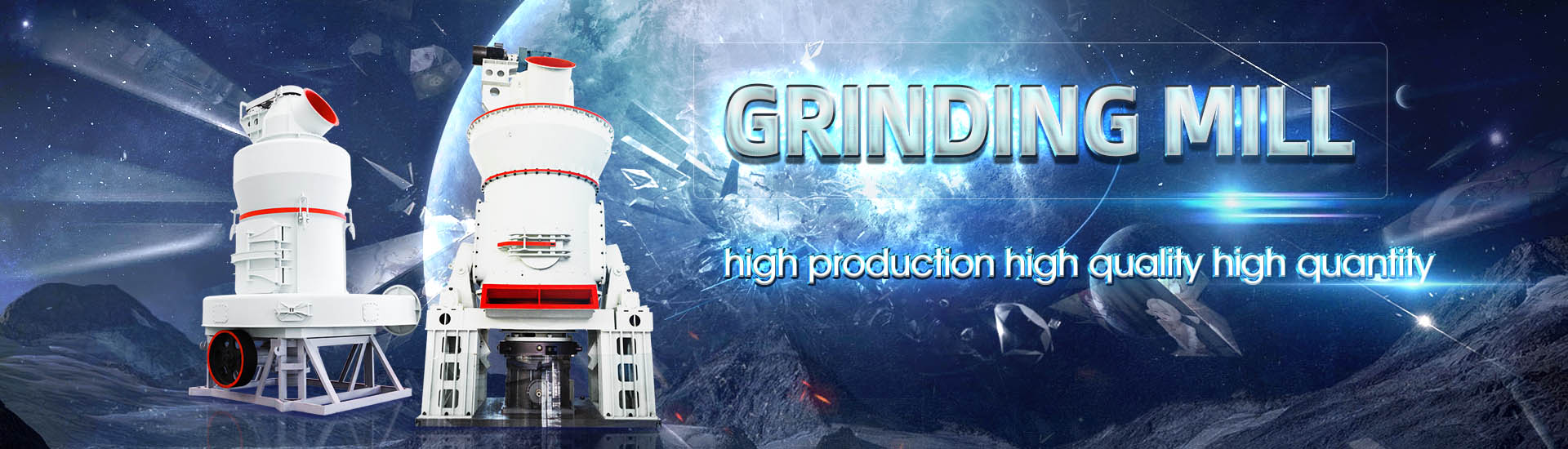
Grinding material recovery rate
.jpg)
Material removal mechanism and corresponding models in the
2023年10月6日 To understand the current status and future trends of material removal in the grinding process, this paper adopts a systematic review approach to summarize the research As the part geometry and process kinematics are easy to follow, surfaceperipheraltraverse grinding is chosen as an example for calculating the specific material removal rate for Local Simulation of the Specific Material Removal Rate for Comminution and highefficiency liberation are vital for better recovery rates of materials 25 Shredding or grinding operations can produce hazardous fine metal particles, dioxins, and BFRs in the dust and reduce the number of precious Recovery of metals and valuable chemicals from waste 2024年3月1日 Propose a multistep grinding process optimization method for hard brittle materials with variable grinding depth Prove the effectiveness of the optimization method and Optimization of grinding process for hard and brittle materials
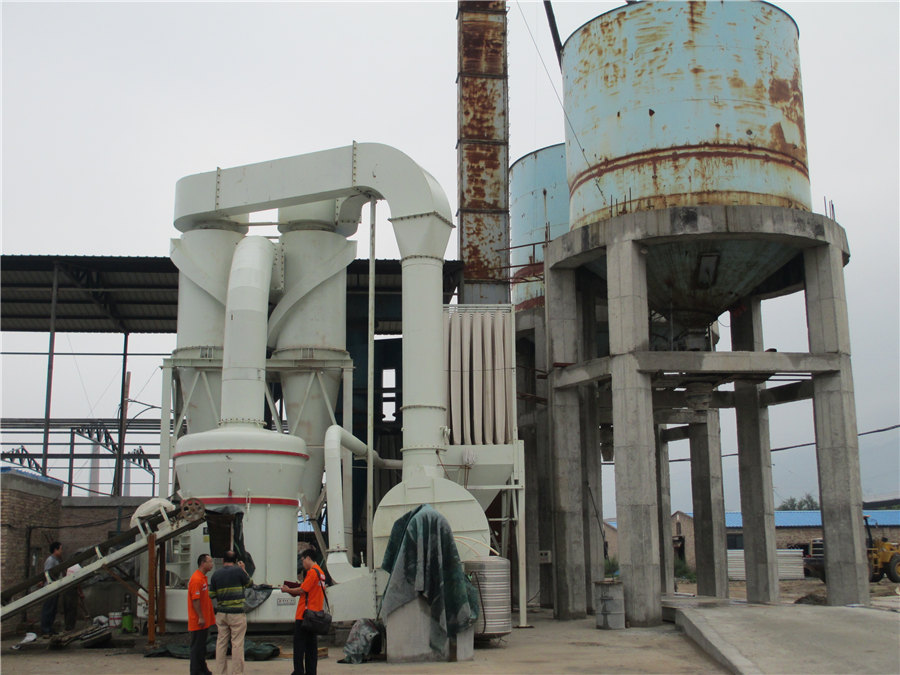
Enhanced prediction accuracy in highspeed grinding of brittle
4 天之前 Machine Learning (ML) is transforming manufacturing by adeptly managing large and complex dataset, holding immense potential to improve various machining processes 16 challenges in the accurate estimation of the material’s elastic recovery effect The 17 quantification of elastic recovery is rather complex in the grinding operation due to (i) 18 Elastic recovery of monocrystalline silicon during ultrafine 2013年1月1日 Principles of Modern Grinding Technology explains the principles that led to rapid improvements in modern grinding technology over recent decades Removal rates and quality standards havePrinciples of Modern Grinding Technology2024年3月11日 Grinding difficulttocut alloys is critical in many industrial applications, including aerospace, automotive, and medical industries However, this process has several challenges, Towards Sustainable Grinding of DifficulttoCut Alloys—A Holistic
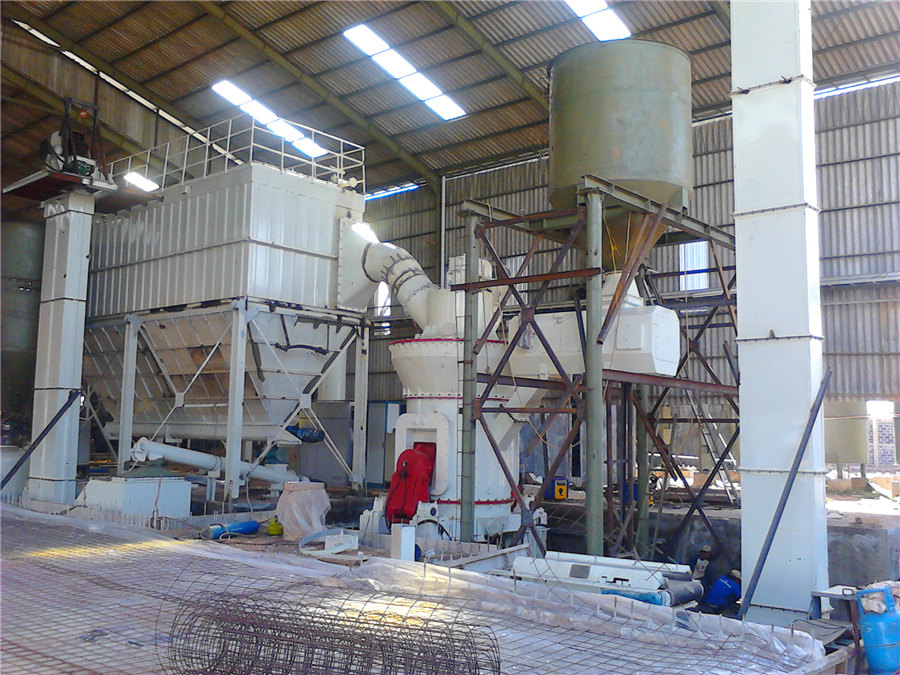
Optimization of Grinding Parameters for the
Lee et al used compressed air to minimize specific grinding forces and surface roughness while maximizing specific material removal rate (MRR), conducted a multiobjective optimization and got the optimal values of depth of cut, feed 2021年1月1日 1 Introduction It is widely agreed that recycling and other material recovery techniques are essential for a global transition from linear to circular consumption patterns (MacArthur, 2013)In order to shift consumption patterns to materials that have higher recovery yields, manufacturers and policymakers need to be able to universally estimate and compare Economic indicators for material recovery estimationWu [73] analyzed the generation of cracks in grinding of white garnet glass from the material elastic recovery rate, material nano hardness, material elastic modulus, strain rate and from constant depth of cut nano scratch experiments It was observed that the material's elastic recovery rate gradually decreased as the scratching depth increasedMaterial Removal Process an overview ScienceDirect Topics2024年4月15日 The tests showed that at a temperature of 1250 °C, 125% of coal percentage dosage, 90 min of roasting time, and 45 min of grinding time, the grade of 9361% and recovery rate of 9071% of iron ore concentrate were obtained from lead slag via “roasting–grinding–magnetic separation”Iron recovery from lead smelting waterquenching slag by
.jpg)
Surface micromorphology model involved in grinding of GaN
2024年10月1日 The elastic recovery rate of GaN crystals is approximately 45 %, and elastic recovery will lead to a distinct increase in the contact force between the workpiece and abrasives, The material involved in grinding exhibited different deformation or removal behaviours as the machining depth changes1994年6月1日 Understanding grinding technology using a diamond grinding wheel is very important to achieve the dimensional accuracy of the final product in structural application of ceramics Because Si3N4 is very difficult to grind, its grindability, which is estimated from the grinding force, is examined with regard to some of its physical properties The difficulttogrind Grinding Forces and Elastic Recovery in Ceramic Materials2021年5月6日 Dan Goad, Application Engineer III, Norton Abrasives When calculating the material removal rate (MRR) for a roll grinding process, many may read and understand some of what they are looking at, but it quickly turns into a science class with formulas typically not used in How to Accurately Calculate Material Removal Rate in Roll Grinding2023年12月8日 The vigorous development of new energy vehicles, as well as the promotion policy and market, has made China the world’s leading producer and consumer of lithiumion batteries With a large number of lithiumion batteries entering the market, the issue of recycling and reuse of used lithiumion batteries has likewise grown up to be major challenge for the The latest research on the pretreatment and recovery methods
.jpg)
Material removal mechanism and corresponding models in the grinding
2023年10月6日 Grinding technology is extensively applied in manufacturing industries, eg, composites, aerospace alloys, and wind turbine blades (as depicted in Fig 1), and its machining accuracy directly affects the working performance and surface integrity of workpieces [1]To fulfil the efficiency and accuracy requirements of the grinding surface, it is crucial to understand its Surface roughness and the material removal rate (MRR) are two important indicators during the grinding process The former determines the surface quality while the latter reflects the grinding efficiency directly In this paper, the two indicators are taken into consideration simultaneously and differently by converting them into a comprehensive goal with using weighting objective Optimization of Grinding Parameters for the Workpiece 2021年12月1日 Request PDF Grinding activation effect on the flotation recovery of unburned carbon and leachability of rare earth elements in coal fly ash Coal fly ash (CFA) as a secondary resource has Grinding activation effect on the flotation recovery of unburned 2020年3月1日 After 9 min of cryogenic grinding, the grade of LiCoO2 concentrate was up to 9175%, with a recovery rate of 8983% after flotation, but the materials that have not been cryogenic grinding, the Recovery of LiCoO2 and graphite from spent lithiumion batteries
.jpg)
A novel material removal rate model based on single grain
2021年8月1日 Modelling of grinding force and material removal rate (MRR) has been widely investigated for wheel grinding which often has a preset cutting depth, but is rather lacking for sand belt grinding2020年7月1日 The function of grinding modification in the flotation recovery of LCO electrode materials was revealed by Yu et al [185, 192] Fig 16f shows the modification mechanism of graphite and LCO Exploring the critical role of grinding modification on the cific material removal rate based on a regression model follows This approach provides an empirical formula without having to use the previous local approach, making it much easier to handle and less timeconsuming Local Approach for Calculating the Specific Material Removal Rate for Generating Gear GrindingLocal Simulation of the Specific Material Removal Rate for (strain rate = scratching speed/groove width) is positively correlated with scratching 93 speed for a given groove width To our best knowledge, few papers expounded on 94 material elastic recovery in the grinding process Also, it may be noted that much of theElastic recovery of monocrystalline silicon during ultrafine
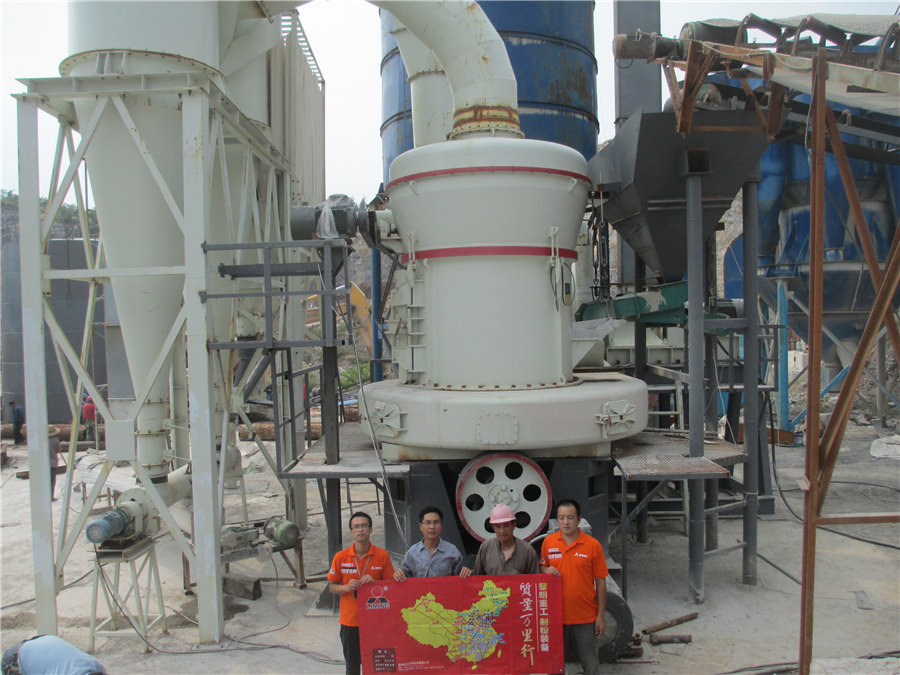
Inprocess material removal rate monitoring for abrasive belt grinding
2022年2月2日 In the abrasive belt grinding process, actual material removal is an important parameter that affects its accuracy At present, for obtaining the actual material removal, offline measurements are required to establish the mathematical prediction model To improve the accuracy and efficiency of abrasive belt machine grinding, this paper proposes a novel method Moreover, there are mainly three approaches to determine material removal rate The most popular one is defined as the product of cutting the cross section and the grinding speed [10,[16] [17] [18 Specific energy consumption and materialremoval ratebody, when the ball mill simplified turning, grinding body effect by the inertia and centrifugal force, the effect of friction make it for cylinder liner board near being carried away by cylinder, when was taken to a certain height, cast by its own gravity and whereabouts of the grinding medium like projectile body of the cylinder body material to breakgrinding material 英中 – Linguee词典2019年7月11日 Remarkable elastic recovery rate over 50% is observed in both cutting speeds Malkin et al 1) and Klocke et al 10) have reviewed and discussed the stateofart of the research on the grinding mechanism The material removal is considered as a combination of three fundamental phases, namely rubbing, plowing and cuttingElastic–plastic deformation of singlecrystal silicon in nano
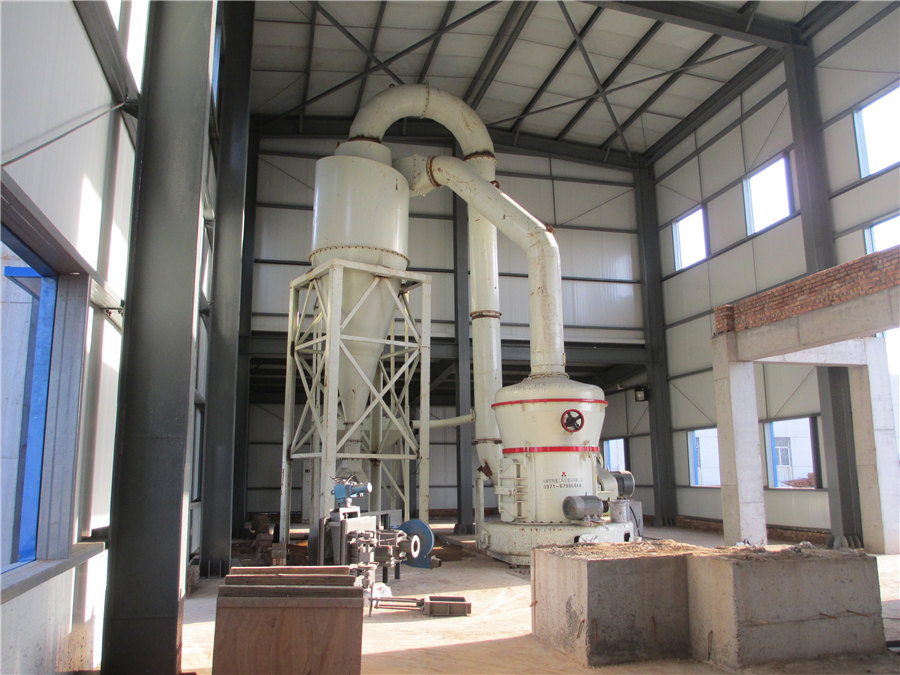
Principles of Modern Grinding Technology
2013年1月1日 PDF Principles of Modern Grinding Technology explains the principles that led to rapid improvements in modern grinding technology over recent decades Find, read and cite all the research 2018年8月13日 Material selection Grinding wheel scrap were obtained from M/s Carborundum Universal Ltd, from their rejected wheels Figure 1 shows the experimental procedure of the recovery process Scrap from brown alumina grinding wheels of 60 grit size with three variable hardness values (A60J5 V10, A60K5V10, A60L5V10) were selected as raw material for the A study on recovery of alumina grains from spent vitrified grinding Moreover, target material recovery rates of 95 % for cobalt, 95% for copper, 95% for lead, 95% for nickel, and 70% for lithium by 2030 have been defined , when the solid Na 2 CO 3 is used directly as the precipitant, the lithium recovery Recycling of Lithium‐Ion Batteries—Current State of 2021年11月1日 Effect of CO 2 flow rate on the a) selective recovery of lithium by dry grinding and CUAWL (roasting temperature = 600 °C, roasting time = 30 min, grinding time = 10 min, grinding speed =1800 rpm, ultrasound frequency= 40 kHz, leaching time = 3 h), b) acid leaching efficiency of the metals in the water leaching residue (leaching temperature 80 °C, acid Dry Grinding Carbonated UltrasoundAssisted Water Leaching
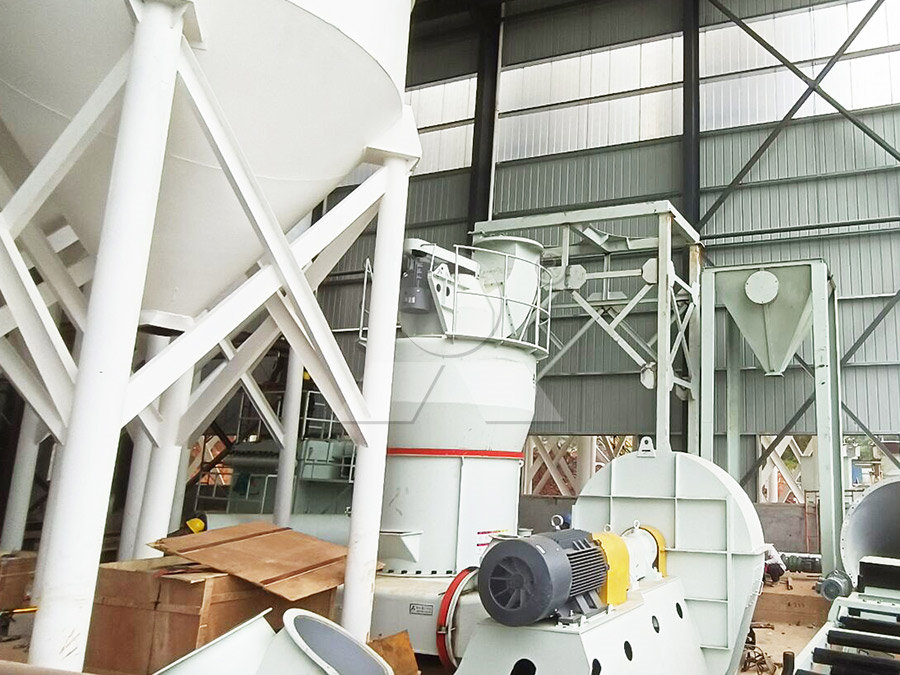
Recent Developments on Processes for Recovery of Rhodium
2022年11月11日 Rhodium (Rh) catalyst has played an indispensable role in many important industrial and technological applications due to its unique and valuable properties Currently, Rh is considered as a strategic or critical metal as the scarce highquality purity can only be supplemented by refining coarse ores with low content (2–10 ppm) and is far from meeting the This paper studies the model of ELID grinding material removal rate, proposes a new model of material removal rate and then conducts theoretical analysis and experimental verification Studies show that the theoretical calculation results of the model and the actual measurement results are in good agreement, demonstrating the regularity of material removal in ELID Model of ELID Grinding Material Removal Rate Semantic Scholar2021年7月3日 The grinding wheels tend to range in diameter from half an inch to three inches This small size introduces rapid wear, making CBN and diamond wheels in crush dressable and vitrified form popular for these applications Surface grinding involves grinding a plane surface by feeding the workpiece beneath a rotating grinding wheelMachining 101: What is Grinding? Modern Machine Shop2019年10月10日 Vitrified grinding wheels are used in various end applications They are easy to dress and have better mechanical properties In general, grinding wheels are used till the stub portion After usage, this stub portion is discarded as waste Grains in this portion are fresh Recovering and reusing the grain in the stub portion are both economically and On the use of grains recovered from spent vitrified wheels in
.jpg)
Wear of diamond grinding wheels and material removal rate of
DOI: 101016/JMATLET200604004 Corpus ID: ; Wear of diamond grinding wheels and material removal rate of silicon nitrides under different machining conditions @article{Li2007WearOD, title={Wear of diamond grinding wheels and material removal rate of silicon nitrides under different machining conditions}, author={W Li and Yu Yin Wang and 2020年9月1日 This paper provides a fresh experimental methodology to obtain the inprocess measurement of material elastic recovery during the grinding process, based on the workpiece selfrotational principle has been extensively employed to obtain a high surface accuracy and material removal rate during the wafer thinning processElastic recovery of monocrystalline silicon during ultrafine 2021年1月1日 1 Introduction It is widely agreed that recycling and other material recovery techniques are essential for a global transition from linear to circular consumption patterns (MacArthur, 2013)In order to shift consumption patterns to materials that have higher recovery yields, manufacturers and policymakers need to be able to universally estimate and compare Economic indicators for material recovery estimationWu [73] analyzed the generation of cracks in grinding of white garnet glass from the material elastic recovery rate, material nano hardness, material elastic modulus, strain rate and from constant depth of cut nano scratch experiments It was observed that the material's elastic recovery rate gradually decreased as the scratching depth increasedMaterial Removal Process an overview ScienceDirect Topics
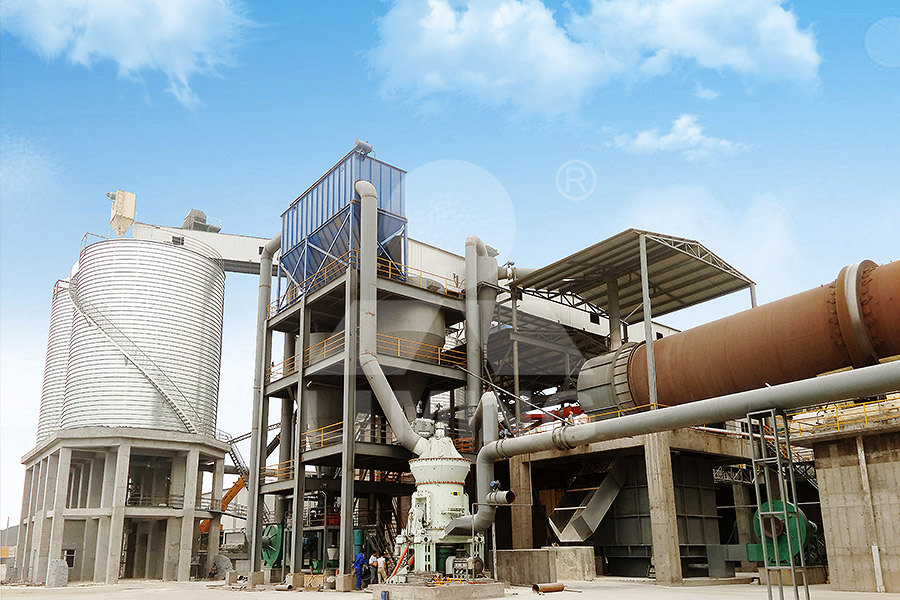
Iron recovery from lead smelting waterquenching slag by
2024年4月15日 The tests showed that at a temperature of 1250 °C, 125% of coal percentage dosage, 90 min of roasting time, and 45 min of grinding time, the grade of 9361% and recovery rate of 9071% of iron ore concentrate were obtained from lead slag via “roasting–grinding–magnetic separation”2024年10月1日 The elastic recovery rate of GaN crystals is approximately 45 %, and elastic recovery will lead to a distinct increase in the contact force between the workpiece and abrasives, The material involved in grinding exhibited different deformation or removal behaviours as the machining depth changesSurface micromorphology model involved in grinding of GaN 1994年6月1日 Understanding grinding technology using a diamond grinding wheel is very important to achieve the dimensional accuracy of the final product in structural application of ceramics Because Si3N4 is very difficult to grind, its grindability, which is estimated from the grinding force, is examined with regard to some of its physical properties The difficulttogrind Grinding Forces and Elastic Recovery in Ceramic Materials2021年5月6日 Dan Goad, Application Engineer III, Norton Abrasives When calculating the material removal rate (MRR) for a roll grinding process, many may read and understand some of what they are looking at, but it quickly turns into a science class with formulas typically not used in How to Accurately Calculate Material Removal Rate in Roll Grinding
.jpg)
The latest research on the pretreatment and recovery methods
2023年12月8日 The vigorous development of new energy vehicles, as well as the promotion policy and market, has made China the world’s leading producer and consumer of lithiumion batteries With a large number of lithiumion batteries entering the market, the issue of recycling and reuse of used lithiumion batteries has likewise grown up to be major challenge for the 2023年10月6日 Grinding technology is extensively applied in manufacturing industries, eg, composites, aerospace alloys, and wind turbine blades (as depicted in Fig 1), and its machining accuracy directly affects the working performance and surface integrity of workpieces [1]To fulfil the efficiency and accuracy requirements of the grinding surface, it is crucial to understand its Material removal mechanism and corresponding models in the grinding Surface roughness and the material removal rate (MRR) are two important indicators during the grinding process The former determines the surface quality while the latter reflects the grinding efficiency directly In this paper, the two indicators are taken into consideration simultaneously and differently by converting them into a comprehensive goal with using weighting objective Optimization of Grinding Parameters for the Workpiece