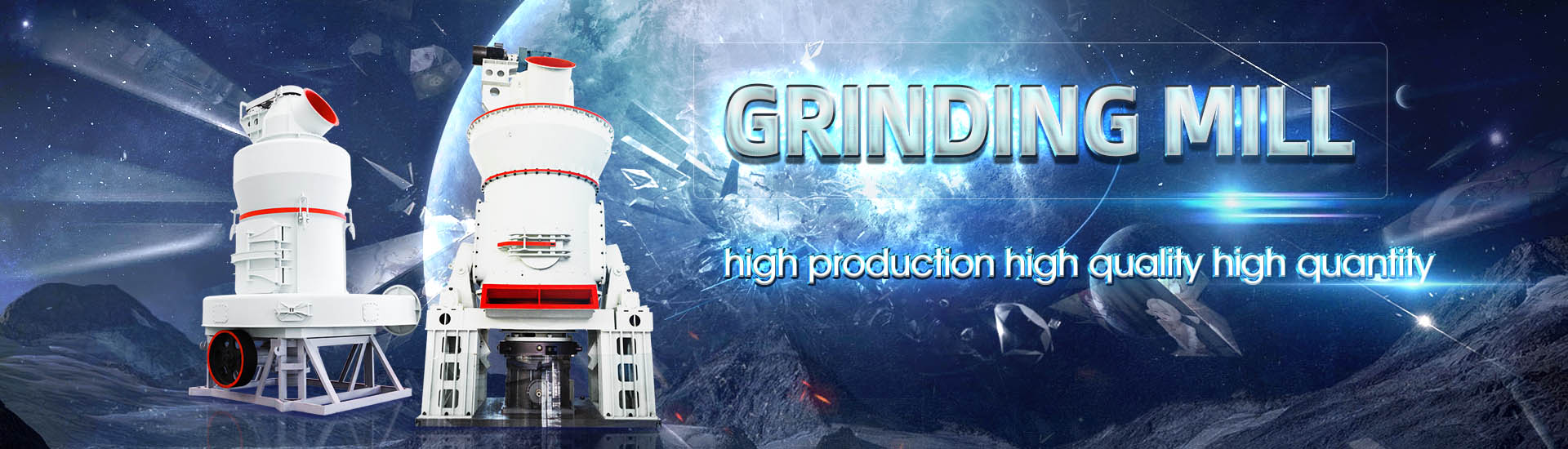
Blast furnace coal injection inspection items

Injection of coal and waste plastics in blast furnaces USEA
Pulverised coal injection (PCI) is a well established technology It is practised in most, if not all, countries with cokebased BFs, and new BFs are nearly always fitted with PCI capability Waste plastics injection (WPI) is less Injection of coal and waste plastics in blast furnaces 5 Pulverized coal injection technology has the potential to spur innovations to blast furnaces: recycled materials, such as waste plastics and biomass, as well as recycled ores can be injected3A2 Pulverized Coal Injection for Blast Furnaces (PCI)2019年3月1日 The efficiency of blast furnace operation with pulverized coal injection (PCI) by tuyeres is determined by the composition and properties of the used coals and by the quality of the ferrous(PDF) Selection of materials for blast furnace injection 2019年1月20日 Identifying coals suitable for blast furnace injection has become increasingly important due to rising injection rates This review of traditional pulverised coal reactivity Suitability of pulverised coal testing facilities for blast furnace
.jpg)
Video monitoring of pulverized coal injection in the blast furnace
coal powder injection in a blast furnace is presented and discussed Image analysis of video recordings is used as a means to estimate the instantaneous coal flow Initial experiments at 2003年1月1日 Pulverized coal injection has assisted the steel industry to lower operating costs, extend coke oven life and lower greenhouse emissions As the understanding of the impact of quality of theImpact of PCI Coal Quality on Blast Furnace Operations 2024年1月1日 Pulverized coal injection of blast furnace ironmaking is a smelting technology where pulverized coal is directly blown into the blast furnace hearth from the tuyere to replace Pulverized Coal Injection of Blast Furnace Ironmaking2022年1月10日 The injection of coal through tuyeres into a blast furnace is widely adopted throughout the industry to reduce the amount of coke used and to improve the efficiency of the iron making process Coals are selected A Comparison of Laboratory Coal Testing with the Blast
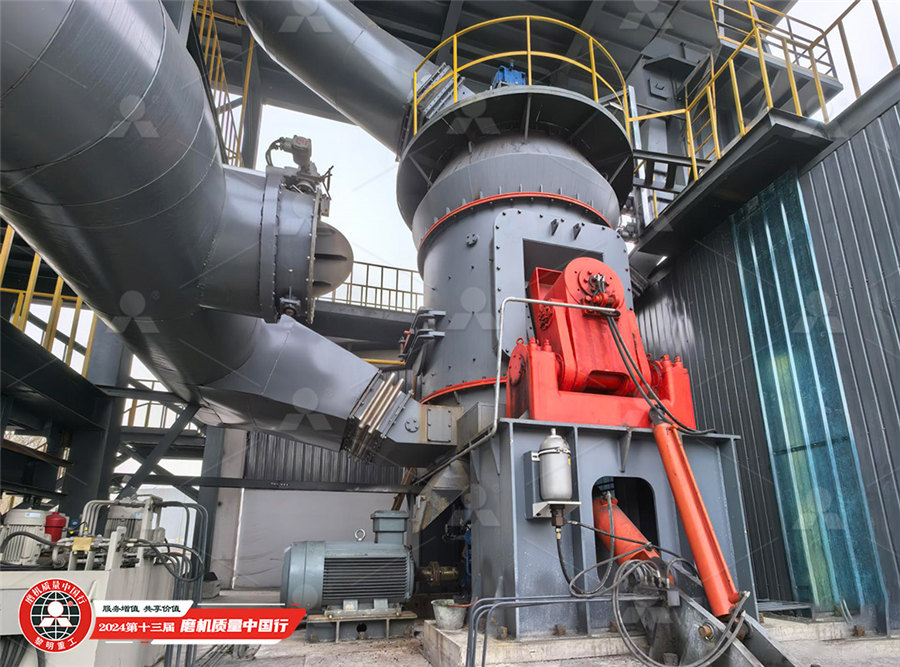
Injection of coal and waste plastics in blast furnaces,
Utilising injectants with a high burnout and optimising operating conditions, such as blast temperature and oxygen enrichment, can improve combustion efficiency Interactions between coal and wastes plastics can be exploited to improve 12 Injection of Pulverized Coal into the Blast Furnace A pulverized coal injection system with Oxycoal+ technology is presented in Fig In 6 this process the pulverized coal is conveyed pneumatically in the dense phase with nitrogen as carrier gas, out of a pressurized injection vessel, and over longerREDUCE CO2 EMISSIONS AND COSTS IN BLAST FURNACE 2012年7月31日 Due to the lack of knowledge regarding the combustion of granular coal injected into a blast furnace, injection characteristics of granular coal were first studied through proximate analysis, element analysis, and research of explosivity, ignition point, meltability of ash, grindability, calorific value, etc Using a sampling device in the raceway combined with Energy Conservation for Granular Coal Injection into a Blast FurnacePulverized coal injection was developed in the 19th century, but was not implemented industrially until the 1970s Rises in the cost of coke due to increased global demand and thus more competition for the resource have made this method attractive to the ironproducing industries and increased its value The PCI method is based on the simple concept of primary air (termed Pulverized coal injection method Wikipedia
.jpg)
Energy Conservation and CO2 Abatement Potential of a Gasinjection
The gasinjection blast furnace (BF) is a new ironmaking technology with an injecting gas instead of traditional pulverized coal injection (PCI) and recycling of the BF top gas through a gasifier In contrast to traditional allcoke and PCI BFs, the coke rate will depend mostly on the heat consumption in a gasinjection BF with abundant injected gas, which results in a large coke 2012年1月1日 Pulverized coal injection (PCI) was introduced at the Kokura No 2 Blast Furnace in 1986 The PC injection rate was started at 25kg/THM and was increased in stages to 75 kg/THM by February 1989(PDF) Coal dust injection in blast furnace ResearchGateMaximum Rates of Pulverized Coal Injection in Ironmaking Blast Furnaces Shinichiro NOMURA1) and Thomas G CALLCOTT2) 1) HiroOhshingai 21526, Kure, Hiroshima, 7370141 Japan 2) PO Box 122 in the lower part of the blast furnace Of these items, Abe et al9) demonstrated the importance of items (1) and (2) when determining the position of Maximum Rates of Pulverized Coal Injection in Ironmaking Blast Furnacesviii) Pulvarised coal Injection: In this section coal is pulvarised to fine dust in mills and injected in the furnace Some of critical Equipments/ facilities in Blast Furnace Department are as follows: Sl No Area Major equipments / facilities 1 Blast Furnace In the Blast Furnaces (BF) liquid iron (popularly termed as ‘Hot
.jpg)
Pulverized Coal Injection of Blast Furnace Ironmaking
2024年1月1日 The blast furnace injection process system is mainly composed of raw coal storage and transportation system, dry gas preparation system, pulverized coal preparation system, pulverized coal conveying system, pulverized coal injection system, and gas supply system (Fig 1)There is also a computer control center to control the entire pulverized coal Pulverised coal injection (PCI) is a well established technology It is practised in most, if not all, countries with cokebased BFs, and new BFs are nearly always fitted with PCI capability Waste plastics injection (WPI) is less Injection of coal and waste plastics in blast furnaces 5 commonly carried out, with only a few ironmaking plants inInjection of coal and waste plastics in blast furnaces USEA2021年7月1日 McCarthy F, Sahajwalla V, Hart J Metal/char interactions during pulverised coal injection in a blast furnace 61st Ironmaking Conference; Nashville, Tennessee; 2002 p 313–324 Google Scholar Teasdale SL, Hayes PC Kinetics of reduction of FeO from slag by graphite and coal chars ISIJ Int 2005;45(5):642–650Blast furnace injection for minimizing the coke rate and CO2020年9月2日 The tuyère injection is one of the key tools to exhaust the blast furnace potential and to minimize its CO2 emissions The review argues theoretical basis and operation strategies for ensuring Char Formation by Coal Injection and Its Behavior
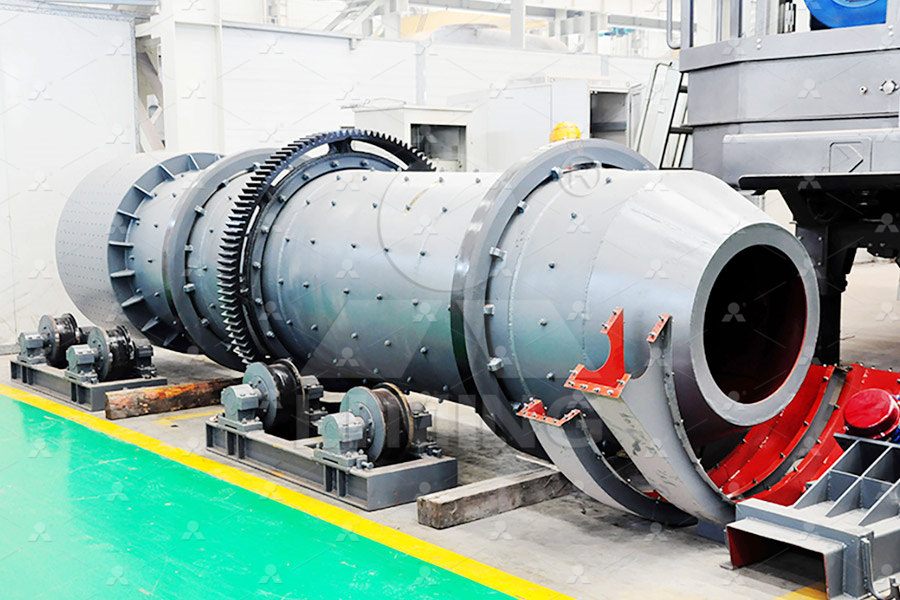
Understanding Pulverized Coal Injection in Blast Furnace
2018年10月21日 Fig 1 Pulverized coal combustion and gas composition in raceway The extent of combustion (combustion efficiency), and hence the amount of unburnt material transported out of the raceway, depends on several parameters which include (i) properties of the coal, such as the VM content, particle size and density, and (ii) operating conditions, for example, blast gas 2020年9月2日 Research and Development, Blast Furnace Development and Alternative Ironmaking, Tata Steel Nederland Technology BV, Wenckebachstraat 1, 1951 JZ VelsenNoord, The Netherlands Coal injection rate of 700 g h −1 and air Char Formation by Coal Injection and Its Behavior in the Blast Furnace 2023年6月15日 The blast furnace injection process system is mainly composed of raw coal storage and transportation system, dry gas preparation system, pulverized coal preparation system, pulverized coal conveying system, pulverized coal injection system, and gas supply system (Fig 1)There is also a computer control center to control the entire pulverized coal Pulverized Coal Injection of Blast Furnace Ironmakingmedia present inthe furnace are vital foranefficient blast furnace (BF) operation Herein, done in the scope of a European Research Fund for Coal and Steel project, two injection coals are selected and used to produce char Chemical, physical, petrographic, and microstructural properties of produced chars are characterizedChar Formation by Coal Injection and Its Behavior in the Blast Furnace
.jpg)
Blast furnace hydrogenrich metallurgyresearch on efficiency injection
2022年3月1日 Blast furnace hydrogenrich metallurgyresearch on efficiency injection of natural gas and pulverized coal Author links open overlay panel Cuiliu Zhang a b , Listopadov Vladislav c , Runsheng Xu a b , Grachev Sergey c , Kexin Jiao a b , Jianliang Zhang a b , Tao Li a b , Ternovykh Aleksei c , Chuan Wang d e , Guangwei Wang a b2021年8月18日 Medium oxygenenriched blast furnaces that utilize reducing gas injections are a feasible new ironmaking process that can significantly reduce the coke ratio and carbon dioxide emissions To better inject the reducing gas into the blast furnace, two injection methods were designed in this study, and the effects of the reducing gas on the combustion of pulverized Influence of Reducing Gas Injection Methods on Pulverized Coal 2021年6月16日 Hydrogen is a carbonfree clean energy and a potential fuel to mitigate CO2 emission in ironmaking blast furnaces (BFs) where the coinjection of hydrogen/coal is one of the most promising and feasible technologies In this article, a 3D steadystate industrialscale CFD model is improved and used for investigating the coinjection of hydrogen/coal in BFs The CFD Study of Hydrogen Injection in Blast Furnaces: Tuyere Coinjection Blast Furnace Granular Coal Injection (BFGCI) Process at Bethlehem Steel’s Burns Harbor Plant in Burns Harbor, Indiana The technology is installed on Blast Furnaces C and D, each of these units having a production capacity of 7,000 net tons of hot metal per dayBlast Furnace Granular Coal Injection System Demonstration
43.jpg)
Control Blast Furnace Pulverized Coal Injection to Increase PCI
Control Blast Furnace Pulverized Coal Injection to Increase PCI Rates Roland Weiser, Ingo Braune, Peter Matthes AMEPA GmbH Jülicher Str 320 D52070 Aachen Germany Tel: +49241168040 Fax: +492411680444 Email: info@amepa Key words: Pulverized coal injection, Coal flow meter, Controlled injection, Equal distribution, Increase of PCI INTRODUCTION PDF On Jan 1, 2021, Lingling Liu and others published Optimization of Pulverized Coal Injection (PCI) Rate in an Ironmaking Blast Furnace By an Integrated Process Model Find, read and cite all (PDF) Optimization of Pulverized Coal Injection (PCI) 2014年6月1日 The combustion efficiency of pulverized coal particles in a blast furnace depends strongly on the particle flow behaviors and the shape of the main combustion zone, ie, the raceway shapeNumerical simulation and optimization of pulverized coal injection 2022年5月1日 Maximum rates of pulverized coal injection in ironmaking blast furnaces ISIJ Int, 51 (7) (2011), pp 10331043 Crossref View in Scopus Google Scholar [61] L Jiao, S Kuang, Y Li, X Mao, H Xu, A Yu Numerical Simulation of 3D Asymmetric Inner States of an Ironmaking Blast Furnace Resulting from Tuyere ClosureOptimization of pulverized coal injection (PCI) rate in an
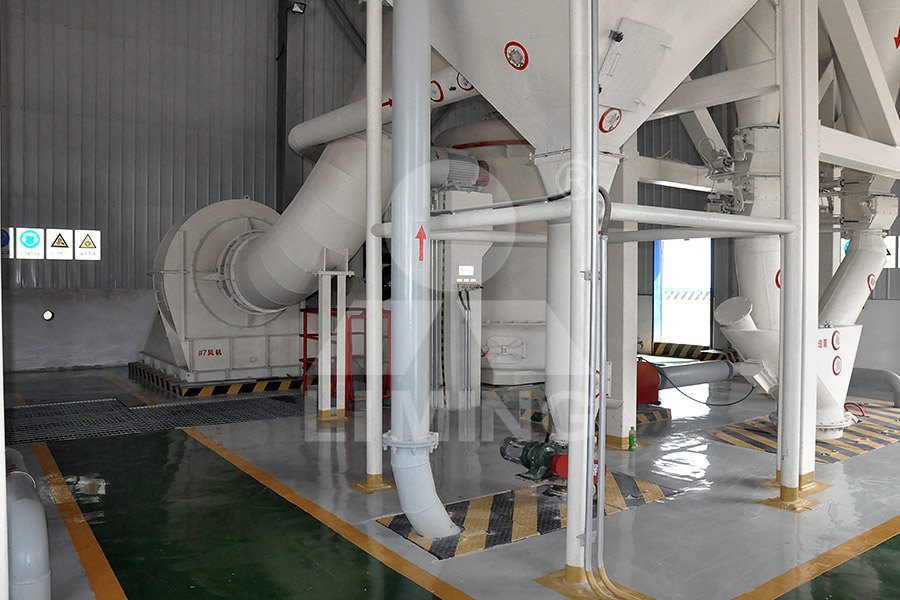
SAFETY GUIDELINES FOR IRON STEEL SECTOR BLAST FURNACE
Some of critical Equipments/ facilities in Blast Furnace Department are as follows: Sl No Area Major equipments / facilities 1 Blast Furnace auxiliary sections Blast Furnace proper with top charging system, stoves hot blast supply system, Stock House conveyor/skip charging system, Fines handling system, Dust Catcher/Cyclone, (water 2018年11月4日 The injection of the pulverized coal into the BF results into (i) increase in the productivity of the BF, ie the amount of hot metal (HM) produced per day by the BF, (ii) reduce the consumption of the more expensive coking coals by replacing coke with cheaper soft coking or thermal coals, (iii) assist in maintaining furnace stability, (iv) improve the consistency of the Understanding Blast Furnace Ironmaking with Pulverized Coal Injection 1996年3月1日 Posco Kwangyang No 4 furnace is currently operated with a PCI rate of 150 kg/tHM, at the high production level of 270 t/m3 d This performance has been achieved thanks to an optimization of the operating conditions, a control of burden distribution and an expert system guided operationHigh coal injection into the blast furnace under high productivity1 Replacement of Pulverised Coal Injection (PCI) with hydrogen and its impact on blast furnace internal conditions N Barrett1, P Zulli2, D O’Dea3, S Mitra4, T Honeyands5 1 AAusIMM, PhD Replacement of Pulverised Coal Injection (PCI) with hydrogen and
.jpg)
Replacement of Pulverised Coal Injection (PCI) with hydrogen and
a blast furnace operating with PCI as a base case, and various approaches to hydrogen injection assessed, with a particular focus on displacing PCI The maximum hydrogen injection rate of 1952021年4月25日 The tuyère injection is one of the key tools to exhaust the blast furnace potential and to minimize its CO2 emissions The review argues theoretical basis and operation strategies for ensuring the high efficiency of injection of auxiliary reducing agents (ARA) First, it provides the theoretical analysis of requirements that ensure minimum coke and carbon rates, and Blast furnace injection for minimizing the coke rate and CO2 Chapter Headings Introduction high rate PCI operation in Japan Characteristics of pulverized coal combustion Combustion behaviour of PC particle group PC combustion in blast furnace Modeling of pulverized coal combustion Advanced injection lances for high rate PCI Phenomena in blast furnace with high rate PCI Generation of fine blast furnace at high rate PCI Burden Advanced pulverized coal injection technology and blast furnace 2020年9月11日 Technological advancements in evaluating the performance of the pulverized coal injection through tuyeres in blast furnace September 2020 Metallurgical Research and Technology 117(6):611633Technological advancements in evaluating the
.jpg)
(PDF) Introduction of pulverizedcoal injection at
2017年5月1日 The introduction of pulverizedcoal injection at Yenakiieve Iron and Steel Works in 2016 is described The state of the lining of the blastfurnace shaft and hearth is analyzedSustainability 2022, 14, 10885 3 of 17 Meanwhile, Shenhua bituminous coal (BC) and anthracite (AC) used for blast furnace injection in a steel company were selected as the comparisonFeasibility Analysis of Biomass Hydrochar Blended Coal Injection 2003年1月1日 Pulverized coal injection has assisted the steel industry to lower operating costs, extend coke oven life and lower greenhouse emissions As the understanding of the impact of quality of the Impact of PCI Coal Quality on Blast Furnace Operations2021年9月17日 Box plots of the range of coal injection rates for each of the coals/coal blends used during blast furnace production (• represents outliers and * extreme outliers) Metals 2021, 11, x FOR PEER (PDF) A Comparison of Laboratory Coal Testing with the Blast Furnace
.jpg)
High Rate Coal Injection of 218kg/t at Fukuyama No 4 Blast Fukuyama
1996年6月1日 Al Fukuyama No 4 Blast Furnace, a pulverized coal injection system with a capacity of 72 t/h was installed at the end of April 1994 In October, six months later, the highest coal injection was 2022年1月17日 As an energyintensive industry, the iron and steel industry has been facing the challenges associated with reducing CO2 emissions Therefore, metallurgical workers have been examining whether the steel industry can absorb some of the CO2 emissions At high temperatures, CO2 is capable of oxidizing, which can lead to reactions with the carbon in the CO2 Emission of CO2 Injection into Blast Furnace SpringerNumerical Study on Pulverized Biochar Injection in Blast Furnace Agung Tri WIJAYANTA,1,2) Md Saiful ALAM,3,4) Koichi NAKASO,3) Jun FUKAI,3)* Kazuya KUNITOMO5) and Operation with pulver ized coal injection (PCI) into a blast furnace tuyere is used to reduce the coke feed rate The operating conditions, coal types, pulverized coal (PC) diamNumerical Study on Pulverized Biochar Injection in Blast Furnace2015年3月1日 During the operation of blast furnace, blast air heated to temperatures of 1100–1250 °C is blown into the furnace through tuyeres, and reacts with coke in raceways to generate heat and reduction gases for iron ore reductionTo diminish the consumption of expensive coke, some cheaper auxiliary fuels, such as oil, natural gas, and pulverized coal, Burning characteristics of pulverized coal within blast furnace
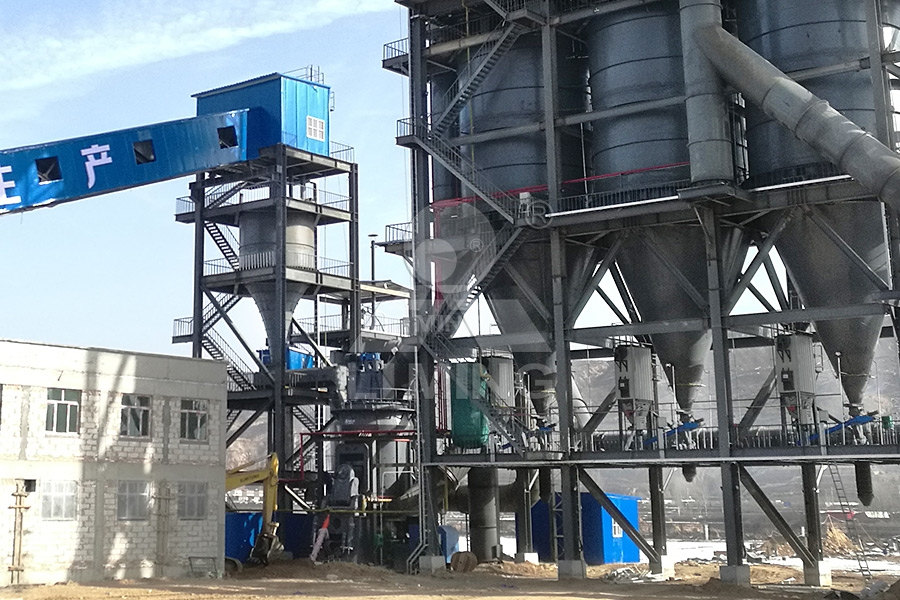
Use of PCI in blast furnaces ICSC
Today in Asia, coal injection equipment is installed on all BFs in Japan, Korea and Taiwan and nearly all of the full sized furnaces in China A goal was set for an injection rate of 150 kg/thm to be achieved in all of China’s large and medium BFs in 2005, and an average 100 kg/thm in the smaller ones (Pei, 2003) Coal injection is installed