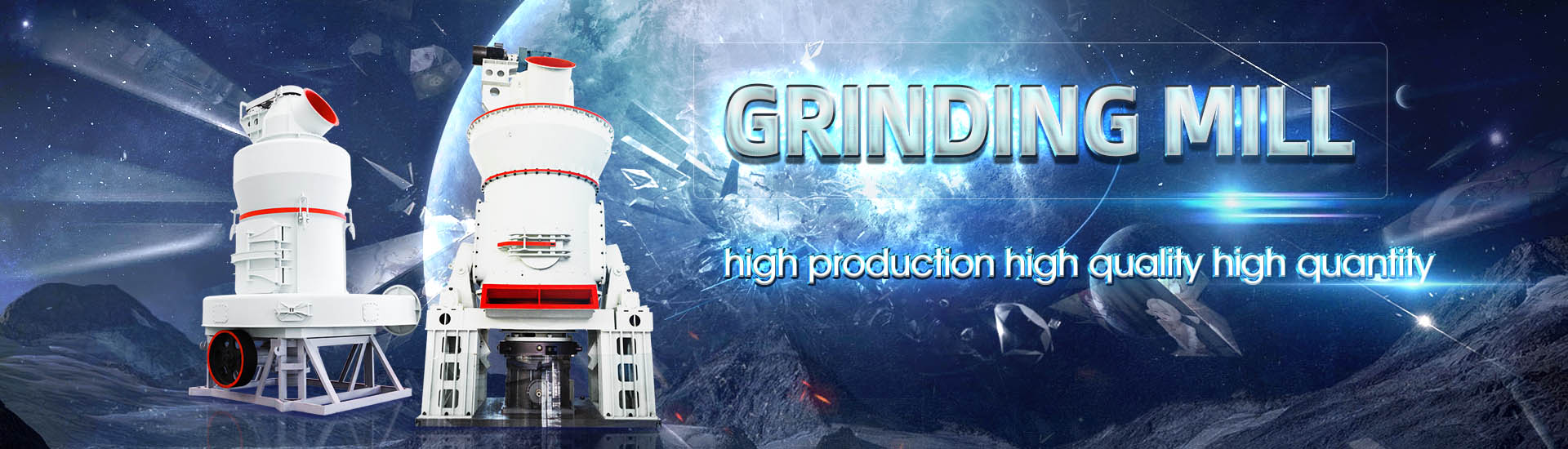
Submersible furnace powder making process
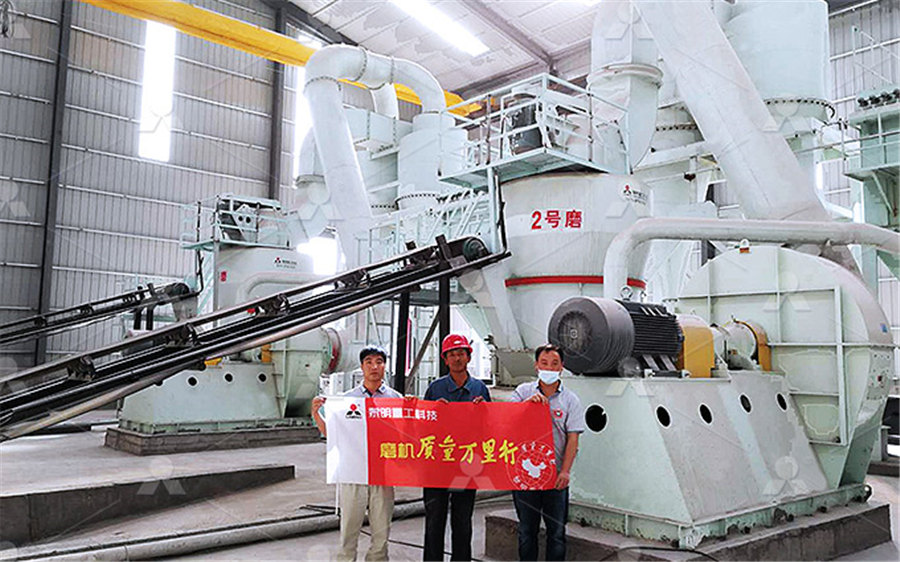
Process Modeling and Optimization of a Submerged
2010年7月30日 This article presents a process model of a phosphorusproducing, submerged arc furnace The model successfully incorporates accurate, multifield thermodynamic, kinetic, and industrial data with 2023年9月15日 The technology of submerged carbon powder injection with CO2 and O2 mixed gas (SCPICOMG) is a new type of powder injection technology It can increase the molten bath carbon content and improve the molten steel Fundamental Study on Electric Arc Furnace 2021年9月1日 Powder injection metallurgy can effectively improve the reaction efficiency, ameliorate the properties, and reduce the production cost of steel This paper reviews recent Application of submerged gaspowder injection ScienceDirectIn this present work we present a model for the tapping of the submerged arc furnaces Using the model the ef fects of furnace crater pressure, metal height and permeability of the different Modelling the Tapping Process in Submerged Arc Furnaces Used
.jpg)
Basic parameters in the operation and design of submerged arc
submerged arc furnaces, highsilicon ferroalloys, electrical operating parameters, specific energy consumption, furnace efficiency factor, loss resistance It is the author’s impression that 2017年4月5日 It becomes apparent that the application of the submerged arc furnace (SAF) in nonferrous metallurgy processes is increasing, in particular for the extraction of zinc, lead, copper and(PDF) The submerged arc furnace (SAF) ResearchGate2021年7月26日 Silicomanganese is produced by carbothermic reduction of manganese oxides and quartz in a submergedarc furnace1,2 Pilotscale experiments have been used to An Overall Furnace Model for the Silicomanganese Process JOMadvanced submerged arc furnaces make use of software controllers The DC application for submerged arc furnace technology shows worldwide an increasing market share in niche New Trends in Submerged Arc Furnace Technology
.jpg)
Application of submerged gaspowder injection Semantic
2021年5月7日 In this study, the recent innovations and improvements in carbon dioxide (CO2) injection technologies for electric arc furnace (EAF)ladle furnace (LF) steelmaking processes 2011年3月1日 The work involved the production of titanium powder at optimized conditions, which included hydrogenation in a horizontal tube furnace at 600°C for 2 hours, milling using planetary and roller Production of titanium metal powder by the HDH For a threephase furnace, the furnace reactance X in m is defined as follows: [8] where Q is the reactive furnace power in kVAr, measured on the primary side of the furnace transformers, excluding the load of capacitor banks, and I is the electrode current in kA Whereas the furnace load is depending on the operatingBasic parameters in the operation and design of submerged arc furnaces 2019年9月8日 The blast furnace iron making process (BFIMP) is the key of the integrated steel enterprise for energy saving due to its largest energy consumption proportion In this paper, an allfactors analysis approach on An AllFactors Analysis Approach on Energy
.jpg)
Iron Ore Pelletizing Process: An Overview IntechOpen
The iron ore production has significantly expanded in recent years, owing to increasing steel demands in developing countries However, the content of iron in ore deposits has deteriorated and lowgrade iron ore has been processed The fines resulting from the concentration process must be agglomerated for use in iron and steelmaking This chapter shows the status of the 2015年3月2日 This is the most powerful and effective steel making technology in the world Around 71 % of the crude steel is made by this process BOF process was developed in Austria in the early 1950s at the two Austrian steelworks at Linz and Donawitz and hence the BOF process is also called LD (first letters of the two cities) steel makingUnderstanding Steel Making Operations in Basic Oxygen Furnace2017年2月16日 PDF Sintering is a thermal agglomeration process that is applied to a mixture of iron ore fines, recycled ironmaking products, fluxes, slagforming Find, read and cite all the research you (PDF) Iron Ore Sintering: Process ResearchGateWhen most people think of the metalmaking process, they picture a stream of molten metal pouring into a mold it makes a nice visual for films and commercialsBut when you consider making parts with powder metal, it may be a little harder to picture the process or why one would bother with powder metal in the first placeHow Metal Powder Is Made: Step 1 of the Powder Metallurgy
.jpg)
The Submerged Arc Furnace (SAF): StateoftheArt Metal
2018年1月11日 The submerged electric arc furnace (SAF) has proven a versatile unit in numerous metallurgical applications for more than a century Countless innovations have made this furnace type become the most commonly used furnace for increased metal recoveries and slagcleaning operations In many applications, SAFs are also employed as primary melting 2017年3月22日 Powder injection: This process is similar to HMD injection processes CaO, CaC 2 and CaSi (sometimes in combination with Al) are used as reagents Sulphur concentrations below 0002% can be reached for Alkilled steel Citation 5, Citation 40 Wire feeder: This process is comparable with powder injectionSulphur removal in ironmaking and oxygen steelmaking2023年11月15日 With the increasing demand for energy conservation and emission reduction, more attentions have been paid to the intelligentization, greenization and low carbonization during the transformation and upgrading of steelmaking plants Ladle furnace (LF) refining is one of the key procedures in steelmaking process and has been widely used in steelmaking plants for its Modeling of LF refining process: a review Journal of Iron and PDF On Jul 11, 2018, Sandra Lúcia de Moraes and others published Iron Ore Pelletizing Process: An Overview Find, read and cite all the research you need on ResearchGateIron Ore Pelletizing Process: An Overview
.jpg)
SAF Submerged Arc Furnace Total Materia
To make ferroalloys of highpurity, which are produced by Submerged Arc Furnaces (SAF), Electric Arc Furnace (EAF) and Refining Furnace (RF) provides high efficiency of work with improved process A sinter plant is required for 2019年1月1日 ScienceDirect Available online at sciencedirect Procedia Manufacturing 35 (2019) 242–245 23519789 © 2019 The Authors Published by Elsevier BV Peerreview under responsibility of the organizing committee of SMPM 2019 101016/jpromfg201905034 101016/jpromfg201905034 23519789 © 2019 The AuthorsA review of ironmaking by direct reduction processes: Quality 2023年9月8日 solutions have been proposed for the blast furnace, for example, hig hly oxygenenriched or hydrogenrich operationBlast Furnace process optimization for sustainable Iron making2023年5月16日 This process enables the casting of both ferrous and nonferrous alloys It is capable of recycling It can process metals with high melting points, like steel and titanium Disadvantages Compared to alternative methods, it is less accurate Using this method for products with established size and weight specifications is challenging15 Different Types of Casting Process Explained [with PDF]
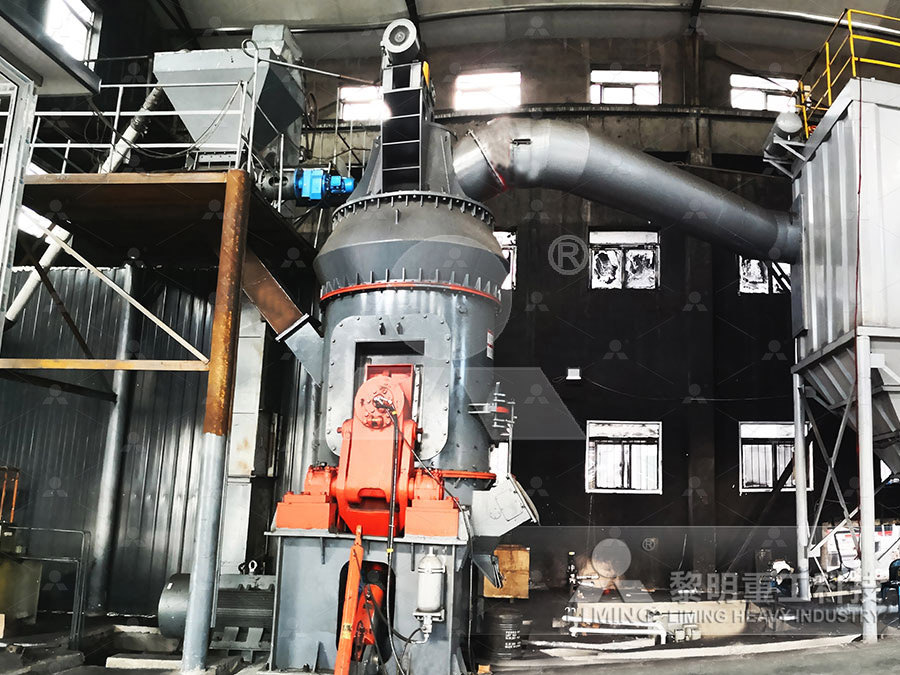
(PDF) ironsteel making From start to finish ResearchGate
PDF On Dec 27, 2019, Mr Bhavesh R Rana published ironsteel making From start to finish Find, read and cite all the research you need on ResearchGate2021年3月9日 The burden charging operation in blast furnace is one of the most important operations during ironmaking process In this paper, we focus on the study of precise burden charging operation, which Precise Burden Charging Operation During IronMaking Process 2019年9月8日 PDF The blast furnace iron making process (BFIMP) is the key of the integrated steel enterprise for energy saving due to its largest energy Find, read and cite all the research you need on (PDF) An AllFactors Analysis Approach on Energy ResearchGatePowder metallurgy usually refers to powder compression molding The powder metallurgy process involves several stages, such as powder preparation, mixing, pressing, sintering, etc, each contributing to the final production of highquality parts and components Powder production Powder production is a crucial step in the powder metallurgy processWhat is Powder Metallurgy Process, Materials, and Applications

Electric arc furnace PPT Free Download SlideShare
2013年6月16日 TEMPERATURE RANGE Industrial electric arc furnace temperatures can be up to 1,800 °C, (3272 °F) while laboratory units can exceed 3,000 °C (5432 °F) Arc furnaces differ from induction furnaces in that the charge material is directly exposed to an electric arc, and the current in the furnace terminals passes through the charged material2021年7月25日 Industrial and process furnaces: Principles, design and operation Elsevier Google Scholar Ryman, C (2007) On the use of process integration methods: evaluation of energy and CO 2 emission strategies in blast furnace iron making and oxygen steelmaking, Doctoral dissertation, Luleå tekniska universitetDataDriven Optimization of Blast Furnace Iron Making Process 2020年3月3日 Figure 22 shows schematic sketch of a blast furnace indicating different sections, and Fig 23 shows the general constructional features of a blast furnace It is circular in cross section and around 30–40 m in height The outer shell of BF is made of steel plates, and refractory lining is at the inside of shellBlast Furnace Process SpringerLinkChapter One What is Powder Metallurgy? Powder metallurgy is a manufacturing process that produces precision and highly accurate parts by pressing powdered metals and alloys into a rigid die under extreme pressure With the Powder Metallurgy: What Is It? Processes, Parts,
.jpg)
Effect of furnace atmosphere on sintering process of chromium
2021年1月10日 During a powder metallurgy process such as sintering, the primary role played by the atmosphere in furnace is to prevent an excessive oxidation of powder compacts in case of the formation of oxides as residuals on powder surfaces In particular, the adjustment of furnace atmosphere is the key to eliminate the phenomenon “decarburization” likely to occur in carbon ELKEM electric pig iron 'furnace, the TyslandHolefurnace as it was called after the engineers who contributed its characteristic features More than 30 of these furnaces are in operation around the world, the biggest unit being the two 60 MVA furnaces at A/S Norsk Jernverk, Norway Characteristic for the process is that theSUBMERGED ARC FURNACE, AN ALTERNATIVE FOR SMELTING OF Basic process flow 1 Powder Making Pulverizing is the process of making powder from raw materials The common methods of pulverizing are oxide reduction method and mechanical method 2 Mixture Mixing is the process of mixing various required powders in a certain proportion and homogenizing them into billet powderApplication of Powder Metallurgy in Gear ManufacturingThe process for making a powder metal part is often overlooked in terms of how much it impacts the finished product It’s a shame, because how powder parts are made is really quite fascinating and complex Take a look at this powder metallurgy process flow chart to learn more about the starttofinish of powder metal creationBreaking Down the Powder Metallurgy Process Horizon
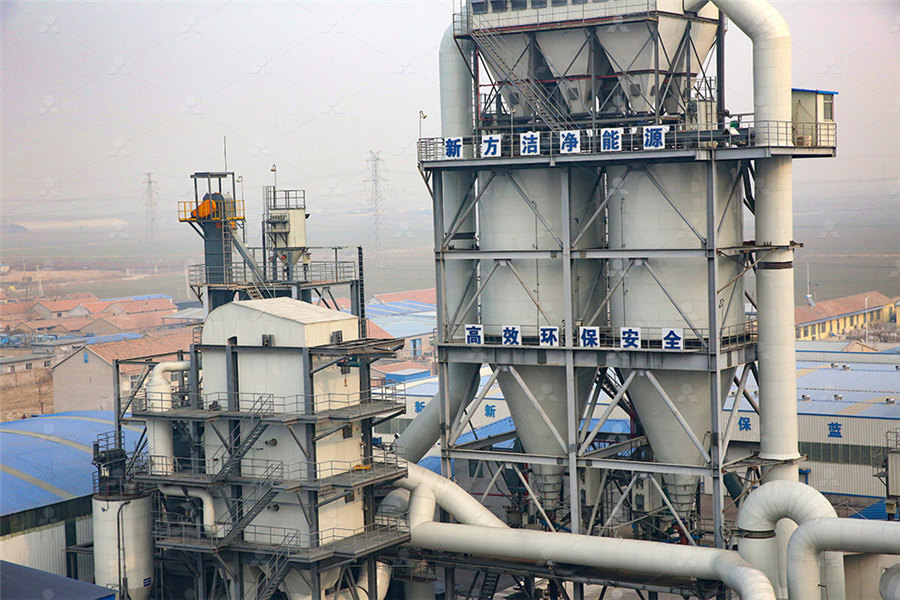
(PDF) Pemanfaatan Limbah Industri Baja sebagai Bahan Baku
PDF On Jul 1, 2019, Fajar Nurjaman and others published Pemanfaatan Limbah Industri Baja sebagai Bahan Baku Pembuatan Logam Pig Iron : Peleburan Mill Scale Menggunakan Submerged Arc Furnace 2024年3月17日 Steel making is a sophisticated process that turns iron ore into steel, involving methods like the Blast Furnace and Electric Arc Furnace to produce various grades of steel The industry emphasizes sustainability by using additives and recycled materials while ensuring quality through rigorous testing for diverse applicationsA Visual Guide: Steel Making Process Chart Cabaro Group2024年8月16日 Welcome to the comprehensive guide on powder making equipment process! Whether you’re a novice in the field or a seasoned professional electronics, hightemperature furnaces Characteristics of Powder Making Equipment Process Understanding the characteristics of the powder making process is essential for selecting the right Powder Making Equipment Process Additive Manufacturing 2011年3月1日 The work involved the production of titanium powder at optimized conditions, which included hydrogenation in a horizontal tube furnace at 600°C for 2 hours, milling using planetary and roller Production of titanium metal powder by the HDH
.jpg)
Basic parameters in the operation and design of submerged arc furnaces
For a threephase furnace, the furnace reactance X in m is defined as follows: [8] where Q is the reactive furnace power in kVAr, measured on the primary side of the furnace transformers, excluding the load of capacitor banks, and I is the electrode current in kA Whereas the furnace load is depending on the operating2019年9月8日 The blast furnace iron making process (BFIMP) is the key of the integrated steel enterprise for energy saving due to its largest energy consumption proportion In this paper, an allfactors analysis approach on An AllFactors Analysis Approach on Energy The iron ore production has significantly expanded in recent years, owing to increasing steel demands in developing countries However, the content of iron in ore deposits has deteriorated and lowgrade iron ore has been processed The fines resulting from the concentration process must be agglomerated for use in iron and steelmaking This chapter shows the status of the Iron Ore Pelletizing Process: An Overview IntechOpen2015年3月2日 This is the most powerful and effective steel making technology in the world Around 71 % of the crude steel is made by this process BOF process was developed in Austria in the early 1950s at the two Austrian steelworks at Linz and Donawitz and hence the BOF process is also called LD (first letters of the two cities) steel makingUnderstanding Steel Making Operations in Basic Oxygen Furnace
.jpg)
(PDF) Iron Ore Sintering: Process ResearchGate
2017年2月16日 PDF Sintering is a thermal agglomeration process that is applied to a mixture of iron ore fines, recycled ironmaking products, fluxes, slagforming Find, read and cite all the research you When most people think of the metalmaking process, they picture a stream of molten metal pouring into a mold it makes a nice visual for films and commercialsBut when you consider making parts with powder metal, it may be a little harder to picture the process or why one would bother with powder metal in the first placeHow Metal Powder Is Made: Step 1 of the Powder Metallurgy2018年1月11日 The submerged electric arc furnace (SAF) has proven a versatile unit in numerous metallurgical applications for more than a century Countless innovations have made this furnace type become the most commonly used furnace for increased metal recoveries and slagcleaning operations In many applications, SAFs are also employed as primary melting The Submerged Arc Furnace (SAF): StateoftheArt Metal2017年3月22日 Powder injection: This process is similar to HMD injection processes CaO, CaC 2 and CaSi (sometimes in combination with Al) are used as reagents Sulphur concentrations below 0002% can be reached for Alkilled steel Citation 5, Citation 40 Wire feeder: This process is comparable with powder injectionSulphur removal in ironmaking and oxygen steelmaking
.jpg)
Modeling of LF refining process: a review Journal of Iron and
2023年11月15日 With the increasing demand for energy conservation and emission reduction, more attentions have been paid to the intelligentization, greenization and low carbonization during the transformation and upgrading of steelmaking plants Ladle furnace (LF) refining is one of the key procedures in steelmaking process and has been widely used in steelmaking plants for its