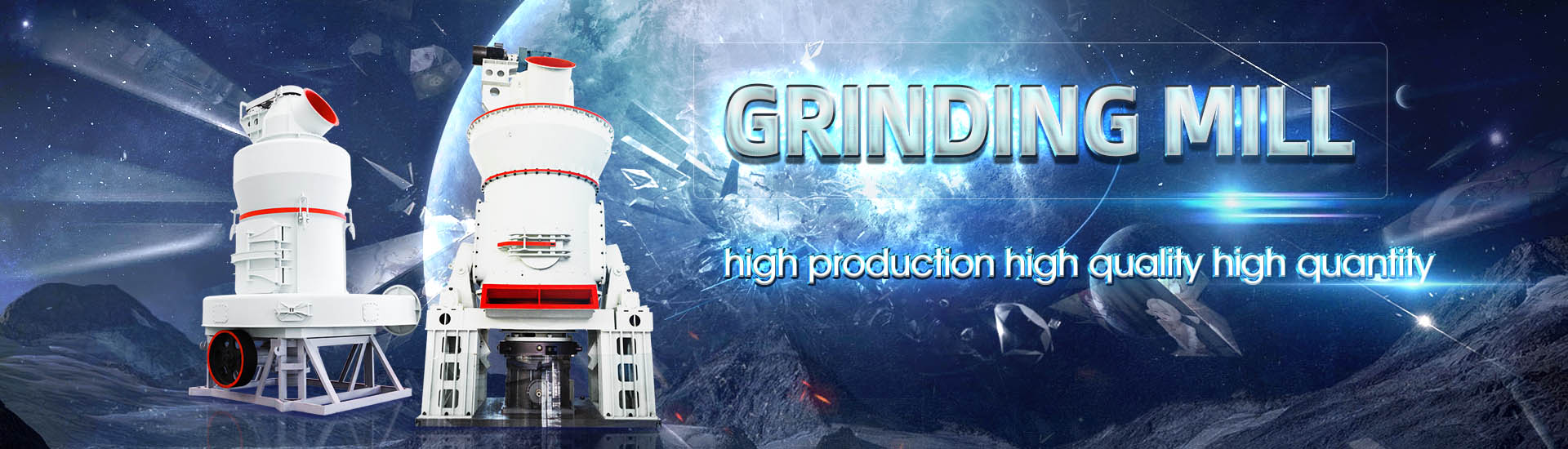
Threestage separation of mediumspeed mill
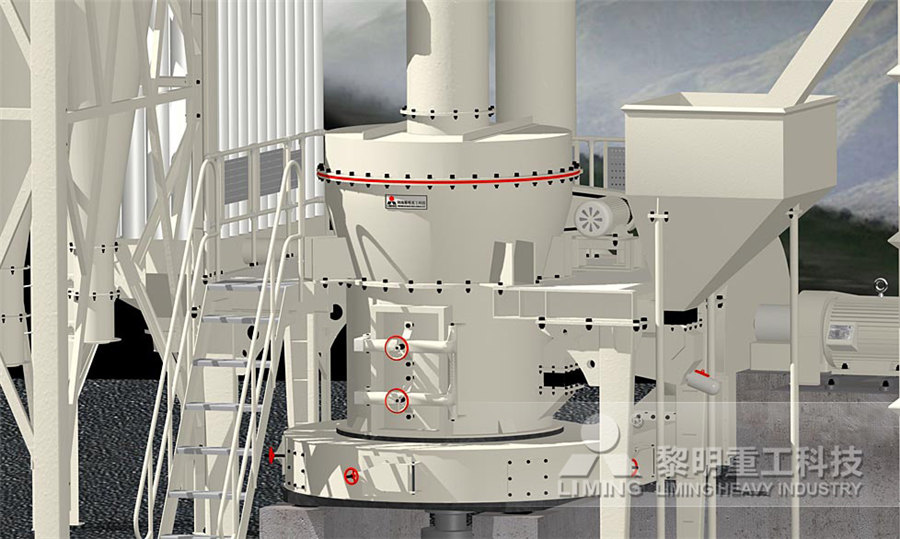
brochure sepol separator myPolysiusService
The separation process takes place by means of fresh air and filter separation, or by means of cyclone circulating air The sepol® separator has also proven an ideal solution for plant 2022年1月1日 Mineral liberation analyser (MLA) suggested that the liberation of iron from gangue was through grinding in the ceramicmedium stirred mill Four NEUM850 ceramic Highefficiency and energyconservation grinding technology It is mainly used for grinding, drying and separating raw coal into qualified fineness for steam boiler combustion in thermal power plant 12 Model meaning HP ** × 3Dyn HP bowl mill HP Bowl type millspower plant equipmentCrushers have more efficient transfer of applied power to the breakage of rock than grinding mills Typically a crushing flowsheet for a mineral processing plant will have from onetothree AMIT 135: Lesson 5 Crushing – Mining Mill Operator Training
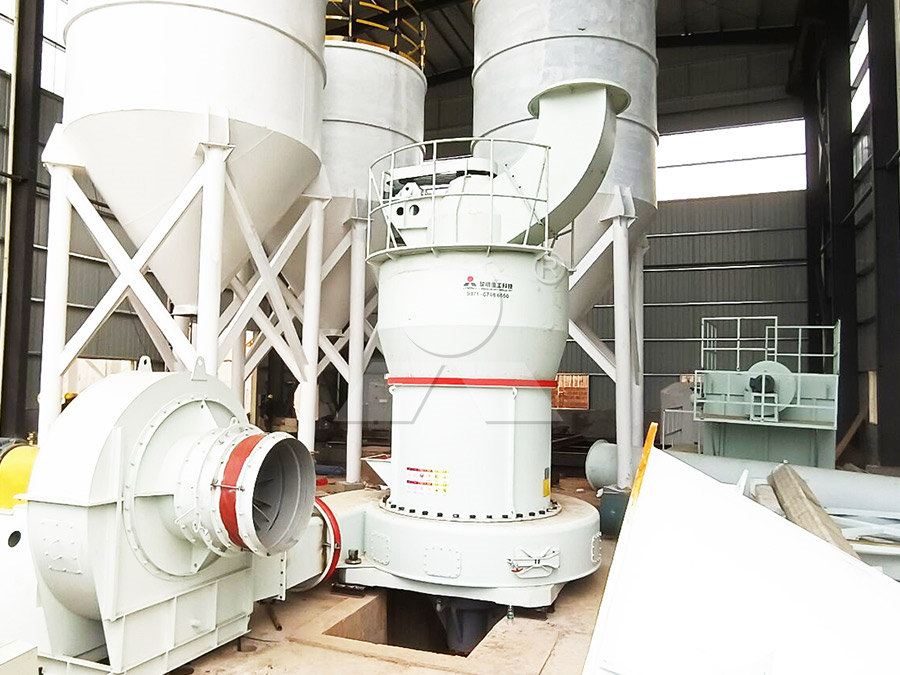
Energy conservation and consumption reduction in grinding
2023年11月1日 The successful case of ceramic medium stirring mill replacing twostage ball grinding provides a feasible solution for energy conservation and consumption reduction in 2023年8月3日 In summary, the paper proposes for the first time a new grinding analysis method that quantitatively separates and characterizes the grinding contribution of the impact and Grinding Contribution and Quantitative Separation of Impact and Dense medium separation (DMS) is a robust process that can be conducted at particle sizes as coarse as 300 mm and as fine as 500 µm with high separation efficiency, depending on Dense Medium Separation An Effective and Robust Pre 2020年6月1日 Stirred media mills are used by the mining industry for ultrafine grinding to enhance liberation, and to decrease particle sizes of industrial minerals to tailor functional Stirred media mills in the mining industry: Material grindability
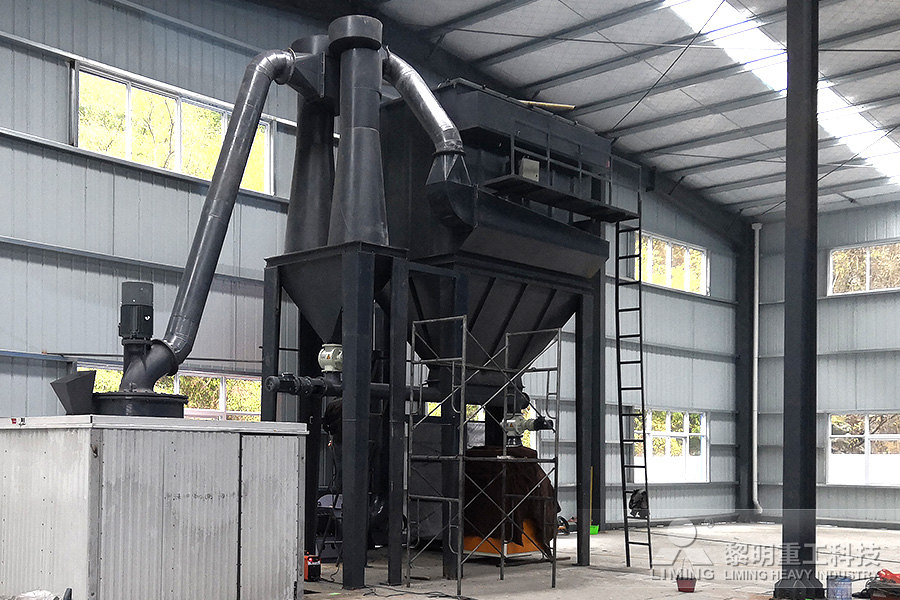
ZGM type Mediumspeed Rolling coal millpower
Structural features of ZGM medium speed mixed coal mill 1321 so as to keep the mill output basically unchanged (about 5%) in the later stage of wear 1324 The crosssection shape of grinding roller and grinding ring (lining 2024年1月31日 Ceramic ball milling has demonstrated remarkable energysaving efficiency in industrial applications However, there is a pressing need to enhance the grinding efficiency for coarse particles This paper introduces a Enhancing the Grinding Efficiency of a Magnetite Dense medium separation (DMS) is a robust process that can be conducted at particle sizes as coarse as 300 mm and as fine as 500 µm with high separation efficiency, depending on liberation characteristics of the value minerals The DMS process involves three steps: feed preparation, dense medium separation, and ferrousbased media recoveryDense Medium Separation An Effective and Robust Pre 1310 The power of motor for HP bowl mill is smaller than that of other medium speed pulverizers 1311 The ventilation resistance of HP coal mill is smaller than that of other medium speed pulverizers, and the air pressure of primary air fan is smaller, which can reduce the investment cost of fan 14 Working principleHP Bowl type millspower plant equipment
.jpg)
Strengthening the flotation recovery of silver using a special
2022年7月1日 Recently, to overcome the problems of high energy consumption, large medium consumption and iron pollution in traditional grinding operation [[5], [6], [7]], Northeastern University has innovatively developed a special ceramicmedium stirred mill (as shown in previously published article by Zhang et al [8]) with small pitch, high speed and low energy 2017年8月1日 In this study, the lumped parameter modeling method is adopted with the following assumptions: 1) the parameters of the medium in the coal mill are uniform; 2) the media in the coal mill are incompressible; 3) the parameters of the medium in the coal mill change along the axial direction only; 4) the change in the flow power in the coal mill is ignored; 5) the coal Modeling of a medium speed coal mill ScienceDirect2017年1月1日 General scheme of the initial recovery stage of the separation and purification process of biological products highlighting the differences and insoluble components present in the fermentation medium 741 These new types of packing materials allowed a high separation efficiency and a high speed of separation [71] 77 Fundamentals of Biological Separation Processes ScienceDirectImage of a “Classical” 3stage ore crushing prior to rod mill [image: Speed = 100 – 359 rpm: Frequency of Stroke = 100 – 300 cycles/minute AMIT 145: Lesson 3 Dense Medium Separation; AMIT 145: Lesson 4 Gravity Separation; AMIT 145: Lesson 5 Froth Flotation;AMIT 135: Lesson 5 Crushing – Mining Mill Operator Training
.jpg)
Energy conservation and consumption reduction in grinding
ratio of 06, 3:2:5 media ratio (10:15:20 mm) of 3:2:5, medium filling rate of 90%, as well as stirring speed of 110 rpm Under the optimum grinding parameters, an iron concentrate with an iron Stage 3 is North America's leading provider of innovative solids and liquids separation solutions We deliver customengineered waste management and fluid recycling services for construction, drilling, industrial, and municipal projects, maximizing efficiency Trusted By Stage 3 Separation2021年3月25日 The separation of the polyphenols for an inlet pressure of 3 bars is very important where the separation efficiency tends to 71% at the level of the apex (lower vortex) and 2976% for the overflow Valorization of Olive Mill Wastewater polyphenols by 2020年12月1日 In this study, computational fluid dynamics (CFD) numerical simulations were applied to comparatively evaluate the flow field of a threestage cone wateronly cyclone (TWOC) with that of a single Study on the flow field and improved separation performance of a three
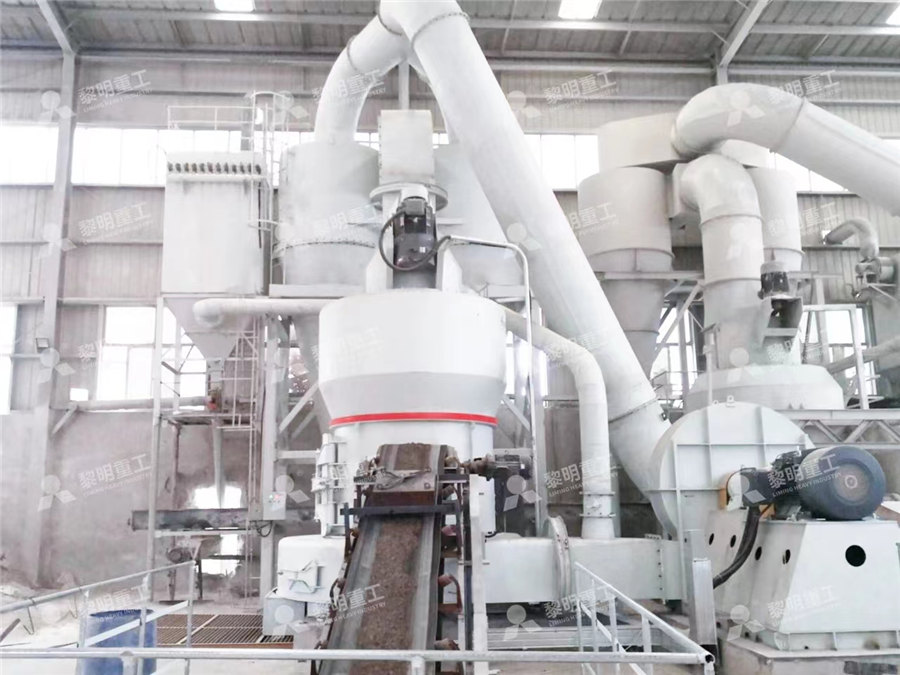
Dense Medium Separation An Effective and Robust PreConcentration
Dense medium separation (DMS) is a robust process that can be conducted at particle sizes as coarse as 300 mm and as fine as 500 µm with high separation efficiency, depending on liberation characteristics of the value minerals The DMS process involves three steps: feed preparation, dense medium separation, and ferrousbased media recovery1708 Mining, Metallurgy Exploration (2023) 40:1707–1717 1 3 of the cylindrical mill mainly includes two mechanisms: impact crushing formed by the dropping of the mediumGrinding Contribution and Quantitative Separation of Impact and Beneficiation of Coal Srdjan M Bulatovic, in Handbook of Flotation Reagents: Chemistry, Theory and Practice, Volume 3, 2015 3933 Heavy media separation Heavy media separation dates back to several centuries Initially, a fine magnetite was used as a heavy media In 1936, a plant was designed employing organic liquid as a heavy media for treating anthracite coal Heavy Media Separation an overview ScienceDirect TopicsThere are three types of separation systems or discharge methods for bead mills: It is especially suitable for those in medium and low viscosity The available types of bead mills are NTV, Pin Type Micron Bead Mill LDMC Series 3 Centrifugal Separation How To Select The Separation System In Bead Mills?
.jpg)
The structure of MPS mediumspeed coal mill system
The mediumspeed coal mill system is mainly composed of raw coal bunker, coal feeder, coal mill, primary fan, sealing fan, hot and cold air regulating valves View in fulltext Similar 2020年7月2日 A comprehensive investigation was conducted to delineate the effect of ball size distribution, mill speed, and their interactions on power draw, charge motion, and balls segregation in a (PDF) Effects of Ball Size Distribution and Mill Speed and Their 2023年8月3日 As far as the cylindrical mill is concerned, there are many factors in grinding operation, including mill speed, medium filling rate, medium maximum size and gradation, grinding concentration and so on [4,5,6,7,8,9,10,11,12,13,14] Among these factors, the grinding medium has the most significant influenceGrinding Contribution and Quantitative Separation of Impact and 2022年12月1日 The TSTO model, which consists of two threedimensional (3D) wedges as orbiter and booster, is used to investigate the interstage aerodynamic interferences and separation characteristics with Numerical Investigation of Aerodynamic Separation Schemes for TwoStage
.jpg)
Mechanism Modeling and Simulation for Coal Pulverizing System
2017年12月15日 To realize rapid and effective evaluation and control on the performance of an MPS medium speed coal mill, a mathematical model was built up for the grinding, drying, separation and circulation In the existing practice, twostage separation commonly takes place at the hotrolling mills In the first stage, mill scale is periodically reclaimed from the mill scale pits using clamshell buckets on cranes or is continuously removed from the pits using chain scrapers [6] Oil is recovered by skimmers installed by the mill scale pits TheSeparation of Mill Scale from Flume Wastewater Using a Dynamic McArthur River Mine Heavy Medium Plant – The Benefits of Applying Modern Coal Plant Design Principles to Base Metal Heavy Medium Separation Jim Wallace1, Sam Strohmayr2, Keith Cameron3 1 MAusIMM, Process Engineer, FTF Optimisation, 28 Griffith Street, Tamborine Mountain, QLD 4272, 2McArthur River Mine Heavy Medium Plant – The Benefits of 2022年2月28日 The maximum force supplied throughout this mechanism almost equals the weight of the grinding medium [111, 112] Since the revolving part is the mill body, the critical speed limits the mill rotational speed If mill rotation speed exceeds the critical speed, centrifugal force causes particles and balls to adhere to the mill’s inner wallGrinding SpringerLink
.jpg)
Paper Making Process: From Raw Materials to Finished Products
2023年7月13日 Medium Consistency Cleaning: MC cleaners are mediumsized, singlestage machines with a junk trap, operating at 2% pulp consistency They protect machinery from wear and ensure optimal functioning by removing glass and sand paper particlesto mill Wheat is poured from a bin in the upper storey of the mill into a hole (the eye) in the centre of the upper stone (Figure 31) In this way the wheat is positioned centrally between the two millstones The upperside of the lower stone and the underside 3: Milling of wheat2021年8月1日 HP type medium speed coal pulverizer produced by Shanghai heavy machinery works has been widely used in recent years, with common faults in operation, short maintenance cycle and heavy taskFault analysis and optimization technology of HP bowl type medium speed 2023年10月27日 The ball mill is a rotating cylindrical vessel with grinding media inside, which is responsible for breaking the ore particles Grinding media play an important role in the comminution of mineral A Review of the Grinding Media in Ball Mills for Mineral Processing
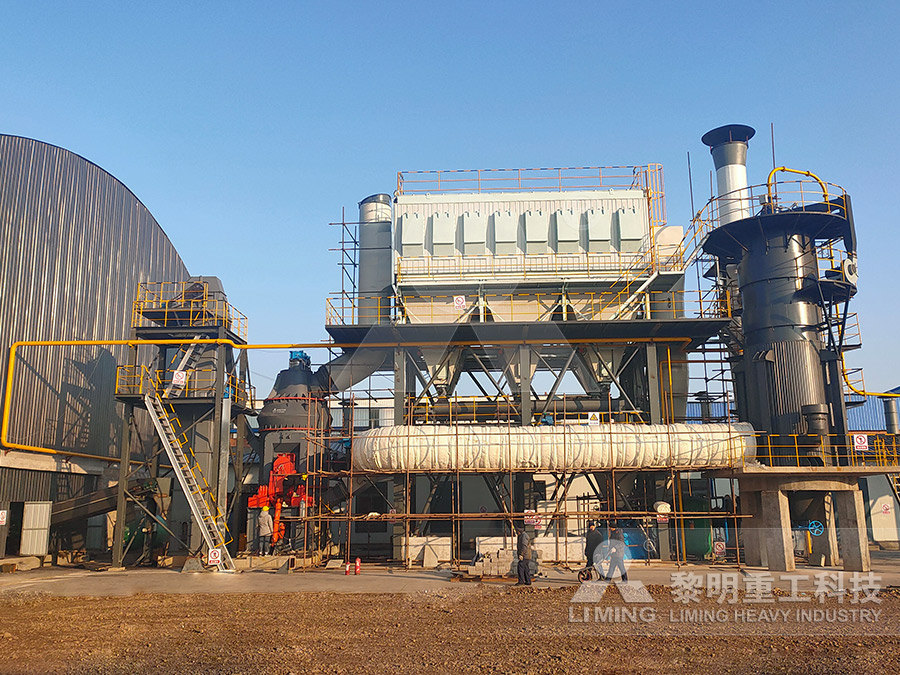
Three Stage Flow Sheet with Two Stage HPGR and Ball Mill Fine
Comparative grinding tests of twostage closed HPGR with 7 mm and 1 mm screens and a final mill grind, and twostage closed HPGR with a 7 mm screen and an air classifier cutting for final product 2021年1月22日 Four NEUM850 ceramicmedium stirred mills superseded the ball mills of second and third stage in the Aoshan concentrator, and the grinding unit consumption decreased by 4838% A potential ceramic ball grinding medium for optimizing flotation separation of chalcopyrite and pyriteAn innovative approach for determining the grinding media Structural features of ZGM medium speed mixed coal mill 1321 so as to keep the mill output basically unchanged (about 5%) in the later stage of wear 1324 The crosssection shape of grinding roller and grinding ring (lining ZGM type Mediumspeed Rolling coal millpower 2024年1月31日 Ceramic ball milling has demonstrated remarkable energysaving efficiency in industrial applications However, there is a pressing need to enhance the grinding efficiency for coarse particles This paper introduces a Enhancing the Grinding Efficiency of a Magnetite
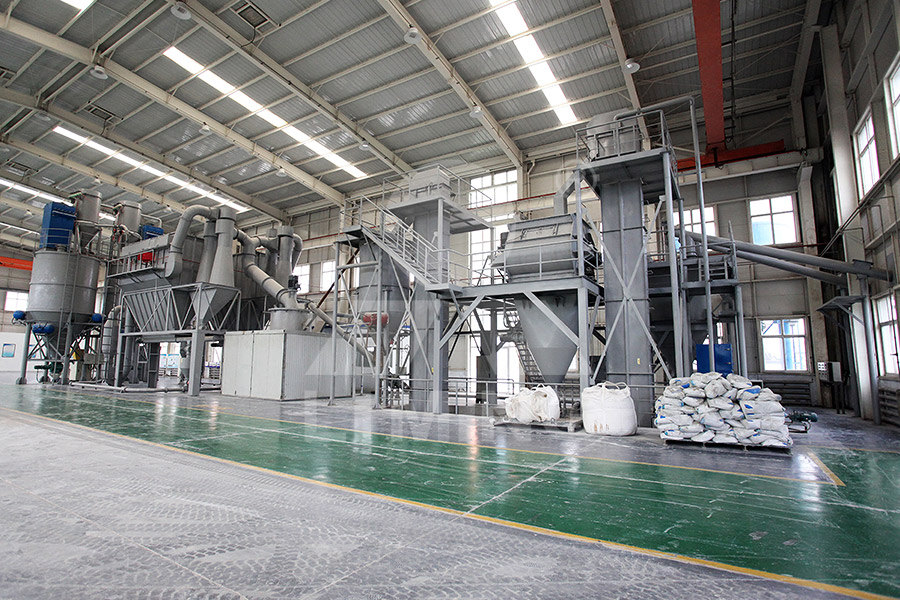
Dense Medium Separation An Effective and Robust Pre
Dense medium separation (DMS) is a robust process that can be conducted at particle sizes as coarse as 300 mm and as fine as 500 µm with high separation efficiency, depending on liberation characteristics of the value minerals The DMS process involves three steps: feed preparation, dense medium separation, and ferrousbased media recovery1310 The power of motor for HP bowl mill is smaller than that of other medium speed pulverizers 1311 The ventilation resistance of HP coal mill is smaller than that of other medium speed pulverizers, and the air pressure of primary air fan is smaller, which can reduce the investment cost of fan 14 Working principleHP Bowl type millspower plant equipment2022年7月1日 Recently, to overcome the problems of high energy consumption, large medium consumption and iron pollution in traditional grinding operation [[5], [6], [7]], Northeastern University has innovatively developed a special ceramicmedium stirred mill (as shown in previously published article by Zhang et al [8]) with small pitch, high speed and low energy Strengthening the flotation recovery of silver using a special 2017年8月1日 In this study, the lumped parameter modeling method is adopted with the following assumptions: 1) the parameters of the medium in the coal mill are uniform; 2) the media in the coal mill are incompressible; 3) the parameters of the medium in the coal mill change along the axial direction only; 4) the change in the flow power in the coal mill is ignored; 5) the coal Modeling of a medium speed coal mill ScienceDirect
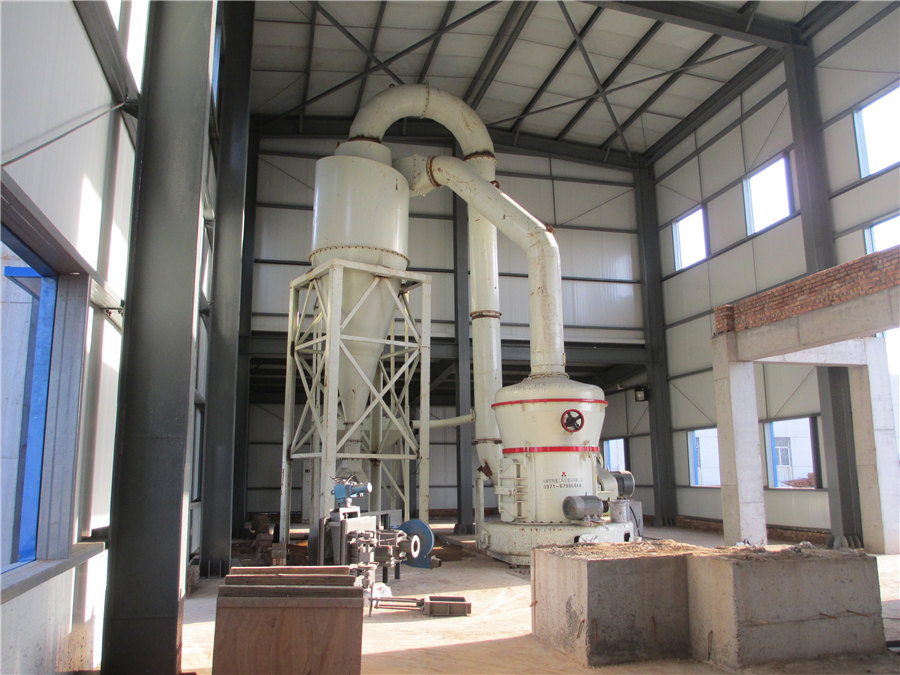
Fundamentals of Biological Separation Processes ScienceDirect
2017年1月1日 General scheme of the initial recovery stage of the separation and purification process of biological products highlighting the differences and insoluble components present in the fermentation medium 741 These new types of packing materials allowed a high separation efficiency and a high speed of separation [71] 77 Image of a “Classical” 3stage ore crushing prior to rod mill [image: Speed = 100 – 359 rpm: Frequency of Stroke = 100 – 300 cycles/minute AMIT 145: Lesson 3 Dense Medium Separation; AMIT 145: Lesson 4 Gravity Separation; AMIT 145: Lesson 5 Froth Flotation;AMIT 135: Lesson 5 Crushing – Mining Mill Operator Trainingratio of 06, 3:2:5 media ratio (10:15:20 mm) of 3:2:5, medium filling rate of 90%, as well as stirring speed of 110 rpm Under the optimum grinding parameters, an iron concentrate with an iron Energy conservation and consumption reduction in grinding Stage 3 is North America's leading provider of innovative solids and liquids separation solutions We deliver customengineered waste management and fluid recycling services for construction, drilling, industrial, and municipal projects, maximizing efficiency Trusted By Stage 3 Separation