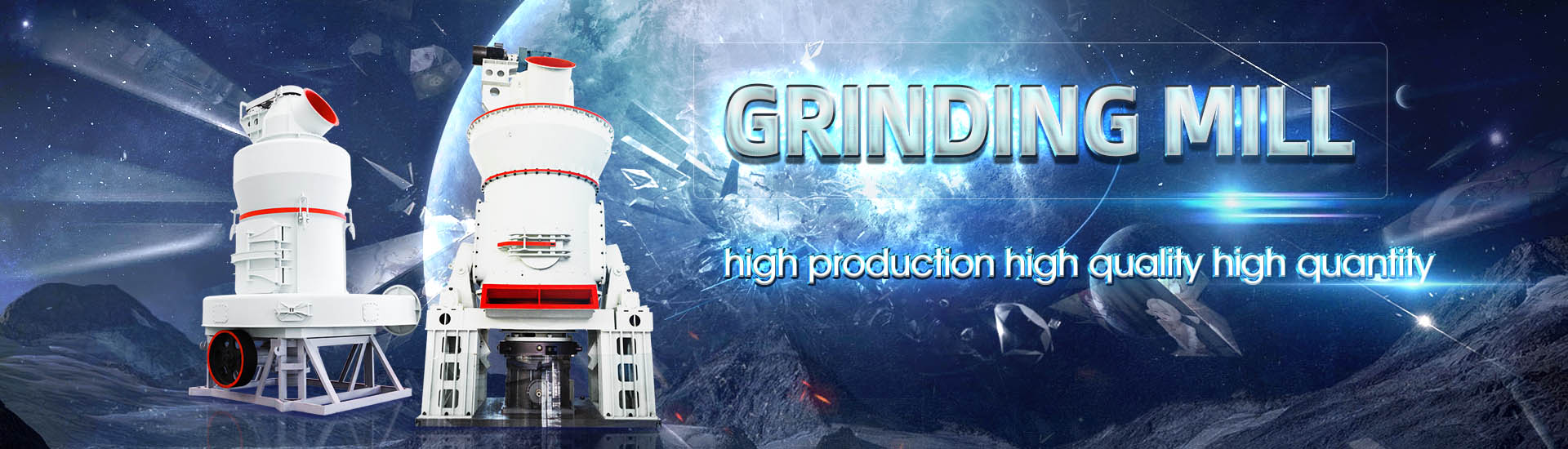
Ball mill steel ball consumption level
.jpg)
Consumption of steel grinding media in mills – A review
2013年8月1日 Improper size distribution or filling level of the ball charge can reduce the efficiency of grinding by 5–20%, amounting to losses of millions per annum for a mill with a the ball mill had an average production rate of 190tph with a specific electrical energy consumption of 355kWh/t Its operational issues included: • oversized limestone • wornout BALL MILLS Ball mill optimisation Holzinger Consulting2023年10月27日 The grinding media affect the power consumption by ball mill, breakage parameters and the product particle size distribution (PSD) They should thus have the largest A Review of the Grinding Media in Ball Mills for Mineral Processing 2023年11月24日 The grinding efficiency of a ball mill is determined by the product size distribution, energy consumption, and the grinding costs According to Hassanzadeh [6], about Grinding Media in Ball Mills for Mineral Processing
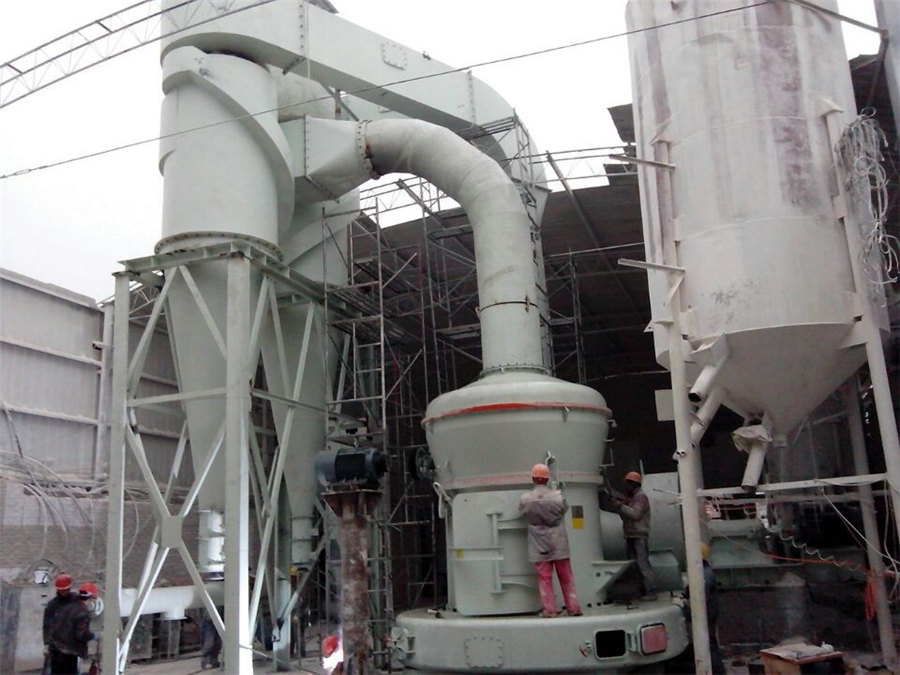
(PDF) Effects of Ball Size Distribution and Mill Speed and Their
2020年7月2日 When the mills charge comprising 60% of small balls and 40% of big balls, mill speed has the greatest influence on power consumption When the mill charge is more 2001年8月1日 Discrete element method (DEM) modelling has been used to systematically study the effects of changes in mill operating parameters and particle properties on the charge Charge behaviour and power consumption in ball mills: Sensitivity 2022年2月8日 The wear law is introduced to the model to predict and analyze the steel consumption due to the wear of the balls, the mass density function, the distribution function of Study of steel ball recharge and consumption in a wet cement The amount of comminution or fineness of minerals in a mill can be described by various parameters, the most important of which is d 80 (80% passing size) The purpose of this Power consumption management and simulation of optimized
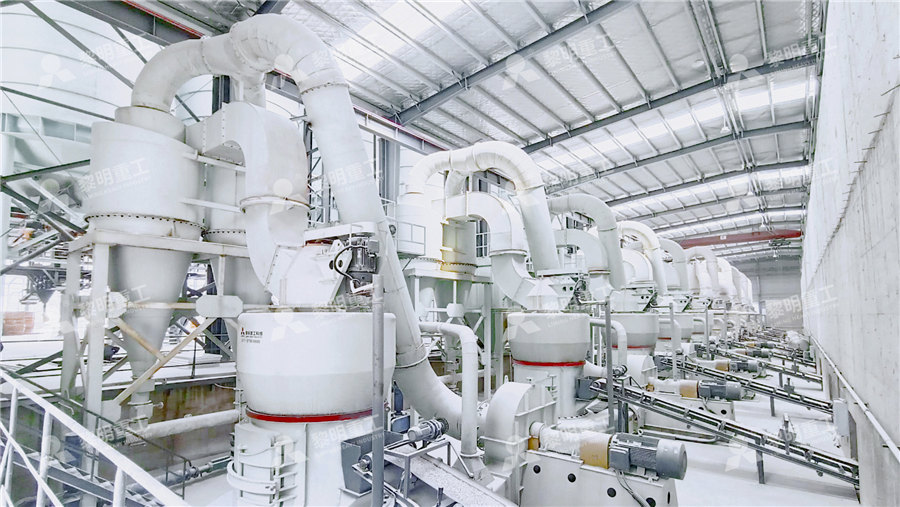
Ball Mill an overview ScienceDirect Topics
The characteristic tumbling motion of these mills has given them the name ‘tumbling mills’, which include the ball mill, tube mill and rod mill Ball mills are horizontal rotating cylindrical or conical steel chambers, approximately one third to half full of steel, alloy steel or iron balls, like that shown in Fig 410 A–C , or flint stonesInt J Miner Process 63 Ž2001 79–114 elsevierrlocaterijminpro Charge behaviour and power consumption in ball mills: sensitivity to mill operating conditions, liner geometry and charge composition Paul W Cleary ) CSIRO DiÕision of Mathematical and Information Sciences, PriÕate Bag 10, Clayton South MDC, Clayton, Victoria, 3169, Australia Received 21 January 2000; Charge behaviour and power consumption in ball mills: 2 Heating: Steel ball billets are heated to an appropriate temperature in a continuous heating furnace; 3 Forging (rolling) into balls: The redhot billets are sent to steel ball mills, then rotates forward between two rolls with spiral Choose the Best Grinding Steel Balls for Your Ball Mill 2015年4月24日 2 Ball mill consist of a hollow cylindrical shell rotating about its axis Axis of the shell horizontal or at small angle to the horizontal It is partially filled with balls made up of Steel,Stainless steel or rubber Inner surface of the shell is lined with abrasion resistant materials such as Manganese,Steel or rubber Length of the mill is approximately equal to its diameter Ball mill PPT Free Download SlideShare
.jpg)
Charge behaviour and power consumption in ball mills:
2001年8月1日 Charge behaviour and power consumption in ball mills: Fig 2 shows the variation of the average torque and power with mill speed for the ball mill described above with a fill level of 50% The effect of noncircularity on both the flow and power draw is evaluated for the case where the mill contains only noncircular steel ballsBall mill optimisation As grinding accounts for a sizeable share in a cement plant’s power consumption, optimisation of grinding equipment such as ball mills can provide significant cost and CO 2 emission benefits to the cement producer n by Thomas Holzinger, Holzinger Consulting, Switzerland BALL MILLS 1 FEBRUARY 2021 INTERNATIONAL CEMENT BALL MILLS Ball mill optimisation Holzinger Consulting2023年11月24日 The ball mill is a rotating cylindrical vessel with grinding media inside, such as highchromium cast iron and highcarbon lowalloy steel, have certain levels of both martensite and austenite C Consumption of steel grinding media in mills—A review Miner Eng 2013, Grinding Media in Ball Mills for Mineral Processing2001年8月1日 A ball mill employs steel balls to generate a It was found that increasing the ore filling level would increase energy consumption and reduce the energy efficiency and the wear of liner Charge behaviour and power consumption in ball mills:
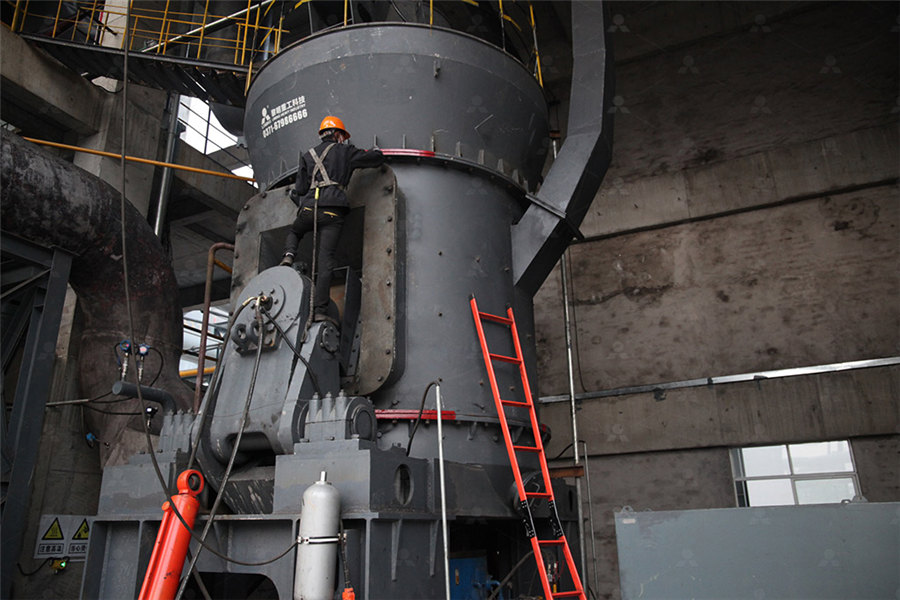
Ball Mills Suitable for every application Retsch
Ball mills are tools for reduction of hard, brittle or fibrous materials vast range variable effective world leading manufacturer Learn more Retsch GmbH FoodGrade version of 316 L steel available; To the product range; XRDMill McCrone Sample preparation for subsequent Xray diffraction (XRD)2023年2月15日 The above situations result in higher ball consumption, lower grinding efficiency, and lessideal product fineness 3 Clean the materials and steel ball in the ball mill and remove the agglomerated materials 16 1 Adjust the sinking part to make the ground level on the bottom of the machine17 Signs of Problems with Ball Mills: Quickly Remove Hidden TroublesIn ball mills, steel balls or hard pebbles to break particle based on impact and attrition Mill Power Consumption Example Ball mill = 35 m x 35 m; Rubber lining = 75 mm % Mill volume charge = 40%; Lesson 4 Level; PRT 140: AMIT 135: Lesson 7 Ball Mills Circuits – Mining 2015年6月19日 We can calculate the steel charge volume of a ball or rod mill and express it as the % of the volume within the liners that is filled with grinding media 911 Metallurgist is a trusted resource for practical insights, solutions, and support in mineral processing engineering, helping industry professionals succeed with proven expertise Mill Steel Charge Volume CalculationMill Steel Charge Volume Calculation 911Metallurgist
.jpg)
SAG Mill Ball Size Evaluator Evaluation Factors Calculate
2013年9月8日 SAG Ball consumption is “average” at 400 g/t while Ball Mill grinding media (3″ balls) usage in 550 g/t Yet, you add steel and nothing seems to happen, tonnage is not noticeably improved You need more tonnage and could actually use a larger/coarser transfer size from the SAG to Ball Mill2017年4月22日 The ball, consumption for mills delivering a coarse product, all passing 8mesh and containing 10 to 20 per cent below 200mesh, the mill being run in open circuit, is about ½ lb per ton for steel balls and 1 lb for cast composition ballsBall Milling 911Metallurgist2024年1月15日 Such as: The initial ball loading capacity of the Φ 1500mm ×3000mm ball mill was 10 tons, and it was shut down after 3 months, a total of 5000 tons of ore (rock ore, hardness level 8) were processed during maintenance, and all the steel balls in the energysaving ball mill were removed clean and screen out 95 tons of reusable balls; If a total of 6 tons of balls were The calculation formula and method for the steel ball moldGrinding is the process of achieving particle size reduction through attrition and compressive forces at the granular level The grinding media in a ball mill is typically steel or ceramic balls of varying sizes, depending on the feed size, work index of the ore and the size reduction and distribution required in the dischargeBall Mills and Ball Charging Bulk Handling Technologies
.jpg)
Assessing load in ball mill using instrumented grinding media
2021年11月1日 It should be noted that power consumption of serial number 11,14, and 15 remains relatively The signal processing also shows a satisfactory prediction of the load level in ball mill It is difficult to transmit the signal data to the computer through the steel ball shell and mill barrel due to the shielding effect of Ball MillSlicer Ball Mill Fill Level Measurement Instrumentation Milling MCAUINSRBALS11 Reduce ball consumption/ton milled Reduce liner wear by operating the mill at an optimal fill level Features • High frequency indication of the mill fill level vectors that can be used to improve mill operationBall Mill Fill Level Measurement Molycop2019年10月19日 Ball mills are extensively used in the size reduction process of different ores and minerals The fill level inside a ball mill is a crucial parameter which needs to be monitored regularly for optimal operation of the ball mill In this paper, a vibration monitoringbased method is proposed and tested for estimating the fill level inside a laboratoryscale ball mill A vibration Monitoring the fill level of a ball mill using vibration sensing and online live calculators for grinding calculations, Ball mill, tube mill, critical speed, Degree of filling balls, Arm of gravity, mill net and gross powerball mill calculations, grinding media filling degree, ball size, mill
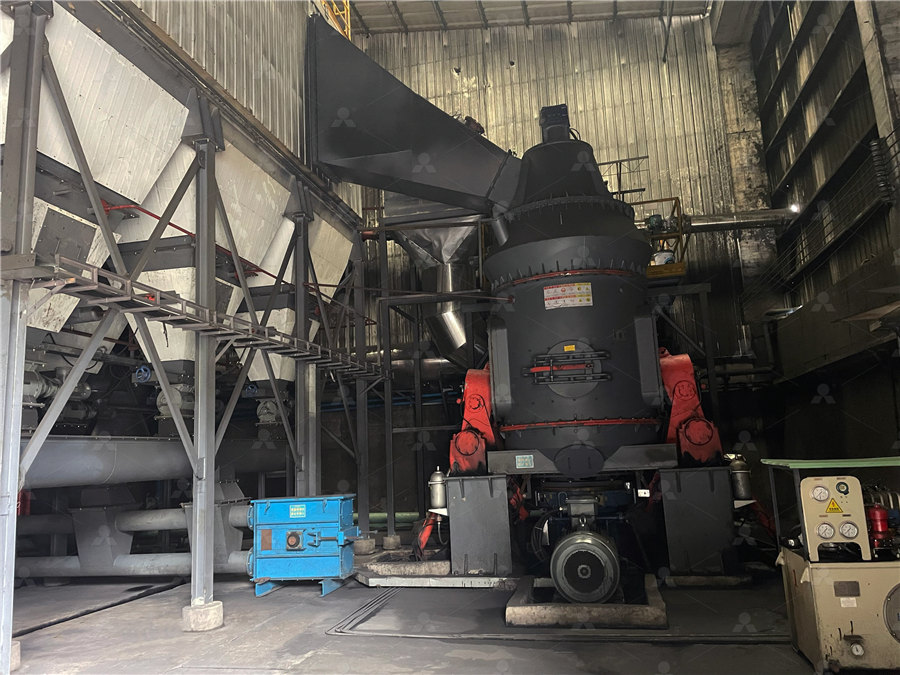
How to Reduce Steel Consumption in Grinding Mills
2017年8月26日 Depending on the hardenability and impact levels required, carbon content of steel for grinding balls vary from 05 to 11%; whereas, For example, in a sulfide concentrator, addition of lime to the pyrrhotite regrind mill 2017年10月18日 Smallscale ball mill tests are convenient but could give misleading results because they do not produce the severe ball impacts of fullsized mills During ball milling, balls are subjected to three conditions: impact, abrasion, and corrosion Much effort has been made to simulate these conditions in the laboratoryGrinding Ball Wear Breakage by Impact Abrasion Tests2017年11月6日 This phenomenon is being exploited to improve mill productivity and ball consumption in the Henderson SAG mills The opposite effect occurs in Climax 3 and 4 m (95 and 13 ft) ball mills These grind less than 95 mm (03 Grinding Ball Design 911Metallurgist2012年6月1日 is lined with mill liners protecting the steel body of the mill and incorporating mill lifters which help to raise the content of the mill to greater heights before it drops and cascades down [36]Grinding in Ball Mills: Modeling and Process Control
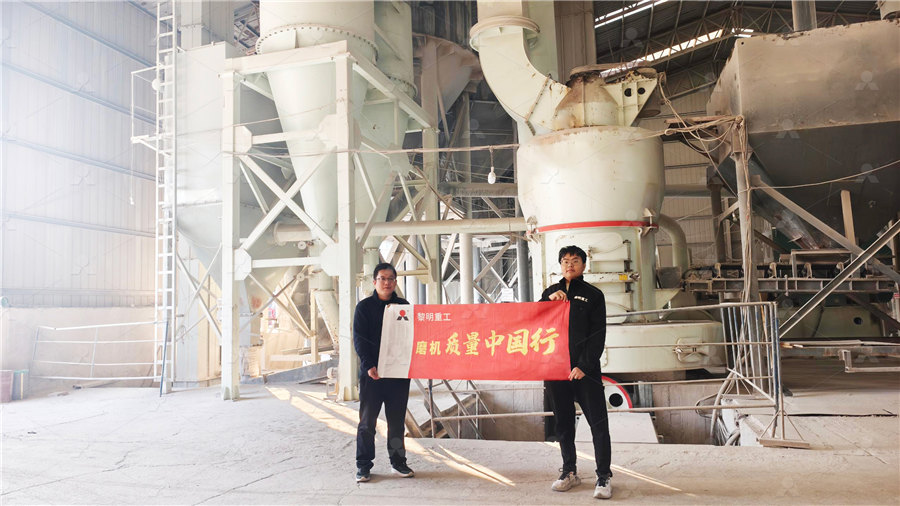
Ball Mill Success: A StepbyStep Guide to Choosing the Right
2024年8月8日 Unlock the secrets to ball mill efficiency with our comprehensive guide on choosing the right grinding media Learn how material composition, size, shape, Their lightweight nature also contributes to reduced energy consumption during milling Steel Balls: Predominantly made from carbon steel, stainless steel, 2017年8月22日 Ball consumption decreased 24% and power remained the same although power data was somewhat questionable because of power metering problems The test results of Unit 14 Ball Mill were sufficiently convincing to immediately convert the grate discharge mills in the newer mill building to mixed ballsRationed Ball Mill Charging to Improve Grinding Efficiency2020年7月2日 A comprehensive investigation was conducted to delineate the effect of ball size distribution, mill speed, and their interactions on power draw, charge motion, and balls segregation in a (PDF) Effects of Ball Size Distribution and Mill Speed and Their sion with steel balls, and is a key component of beneficiation plant production Even though it has massive benefits, such as a high reduction ratio, effective breakage impact, and a wide application (Fuerstenau and Abouzeid, 2002), it also has shortcomings, such as lower efficiency, higher steel ball consumption, and severeEffect of grinding media on the milling efficiency of a ball mill
.jpg)
(PDF) Performance optimization of an industrial ball mill for
2017年1月1日 An increase of over 10% in mill throughput was achieved by removing the ball scats from a single stage SAG mill These scats are non spherical ball fragments resulting from uneven wear of balls Ball mills are very effective for grinding smooth, aqueous, or oily dispersions by wet grinding since it gives particles of 10 microns or less Construction of Ball Mill: The basic parts of the ball mill are a shell, balls, and motor Fig2 A ball mill is also known as a pebble mill or tumbling millBall Mill Principle, Construction, Working, and More Soln PharmaThe characteristic tumbling motion of these mills has given them the name ‘tumbling mills’, which include the ball mill, tube mill and rod mill Ball mills are horizontal rotating cylindrical or conical steel chambers, approximately one third to half full of steel, alloy steel or iron balls, like that shown in Fig 410 A–C , or flint stonesBall Mill an overview ScienceDirect TopicsInt J Miner Process 63 Ž2001 79–114 elsevierrlocaterijminpro Charge behaviour and power consumption in ball mills: sensitivity to mill operating conditions, liner geometry and charge composition Paul W Cleary ) CSIRO DiÕision of Mathematical and Information Sciences, PriÕate Bag 10, Clayton South MDC, Clayton, Victoria, 3169, Australia Received 21 January 2000; Charge behaviour and power consumption in ball mills:
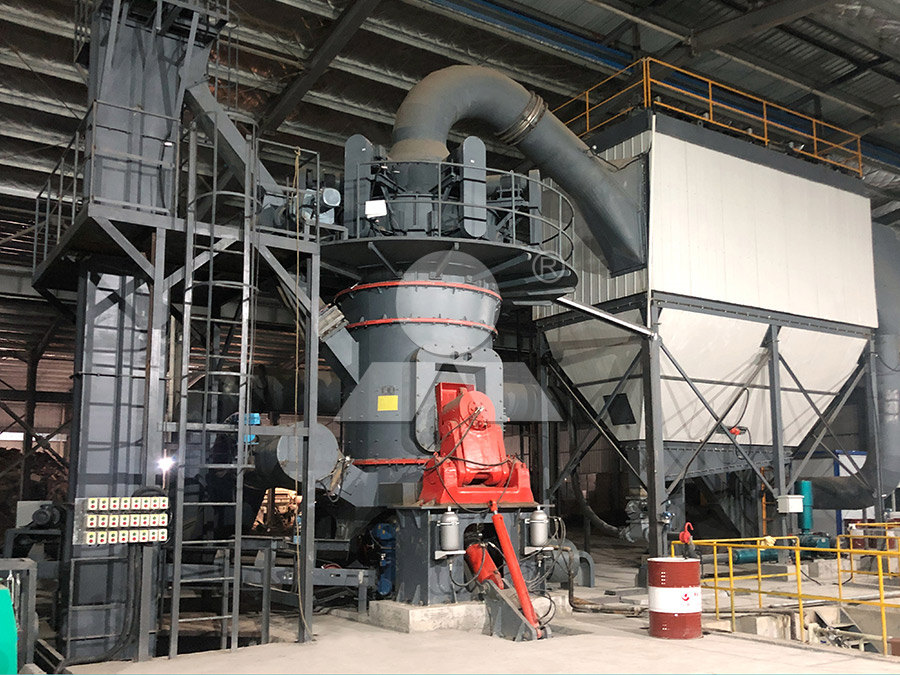
Choose the Best Grinding Steel Balls for Your Ball Mill
2 Heating: Steel ball billets are heated to an appropriate temperature in a continuous heating furnace; 3 Forging (rolling) into balls: The redhot billets are sent to steel ball mills, then rotates forward between two rolls with spiral 2015年4月24日 2 Ball mill consist of a hollow cylindrical shell rotating about its axis Axis of the shell horizontal or at small angle to the horizontal It is partially filled with balls made up of Steel,Stainless steel or rubber Inner surface of the shell is lined with abrasion resistant materials such as Manganese,Steel or rubber Length of the mill is approximately equal to its diameter Ball mill PPT Free Download SlideShare2001年8月1日 Charge behaviour and power consumption in ball mills: Fig 2 shows the variation of the average torque and power with mill speed for the ball mill described above with a fill level of 50% The effect of noncircularity on both the flow and power draw is evaluated for the case where the mill contains only noncircular steel ballsCharge behaviour and power consumption in ball mills: Ball mill optimisation As grinding accounts for a sizeable share in a cement plant’s power consumption, optimisation of grinding equipment such as ball mills can provide significant cost and CO 2 emission benefits to the cement producer n by Thomas Holzinger, Holzinger Consulting, Switzerland BALL MILLS 1 FEBRUARY 2021 INTERNATIONAL CEMENT BALL MILLS Ball mill optimisation Holzinger Consulting
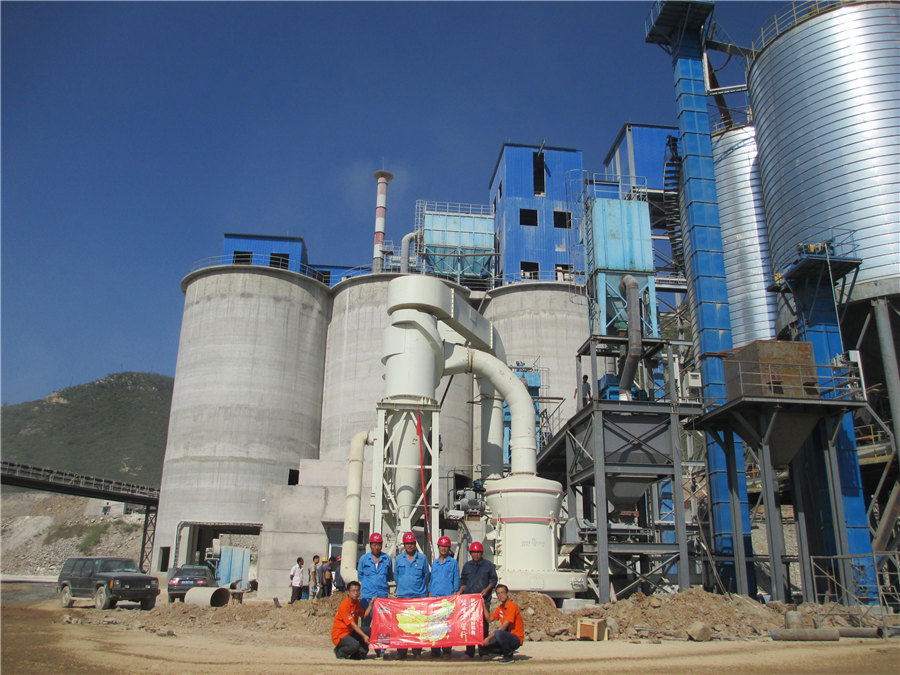
Grinding Media in Ball Mills for Mineral Processing
2023年11月24日 The ball mill is a rotating cylindrical vessel with grinding media inside, such as highchromium cast iron and highcarbon lowalloy steel, have certain levels of both martensite and austenite C Consumption of steel grinding media in mills—A review Miner Eng 2013, 2001年8月1日 A ball mill employs steel balls to generate a It was found that increasing the ore filling level would increase energy consumption and reduce the energy efficiency and the wear of liner Charge behaviour and power consumption in ball mills: Ball mills are tools for reduction of hard, brittle or fibrous materials vast range variable effective world leading manufacturer Learn more Retsch GmbH FoodGrade version of 316 L steel available; To the product range; XRDMill McCrone Sample preparation for subsequent Xray diffraction (XRD)Ball Mills Suitable for every application Retsch2023年2月15日 The above situations result in higher ball consumption, lower grinding efficiency, and lessideal product fineness 3 Clean the materials and steel ball in the ball mill and remove the agglomerated materials 16 1 Adjust the sinking part to make the ground level on the bottom of the machine17 Signs of Problems with Ball Mills: Quickly Remove Hidden Troubles