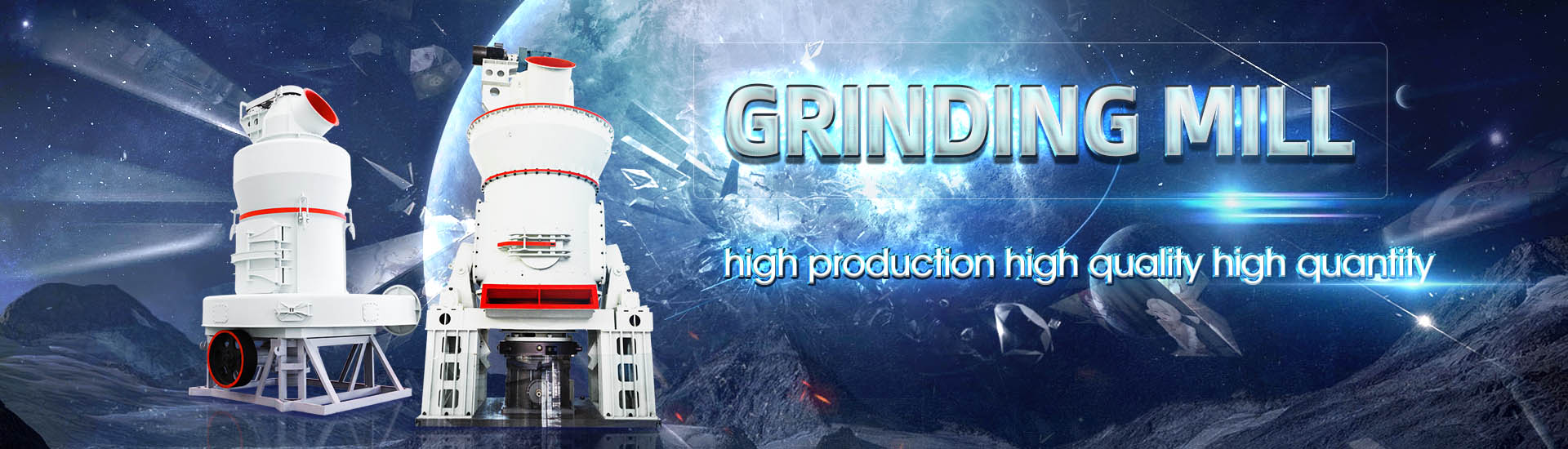
Coal mill system supply
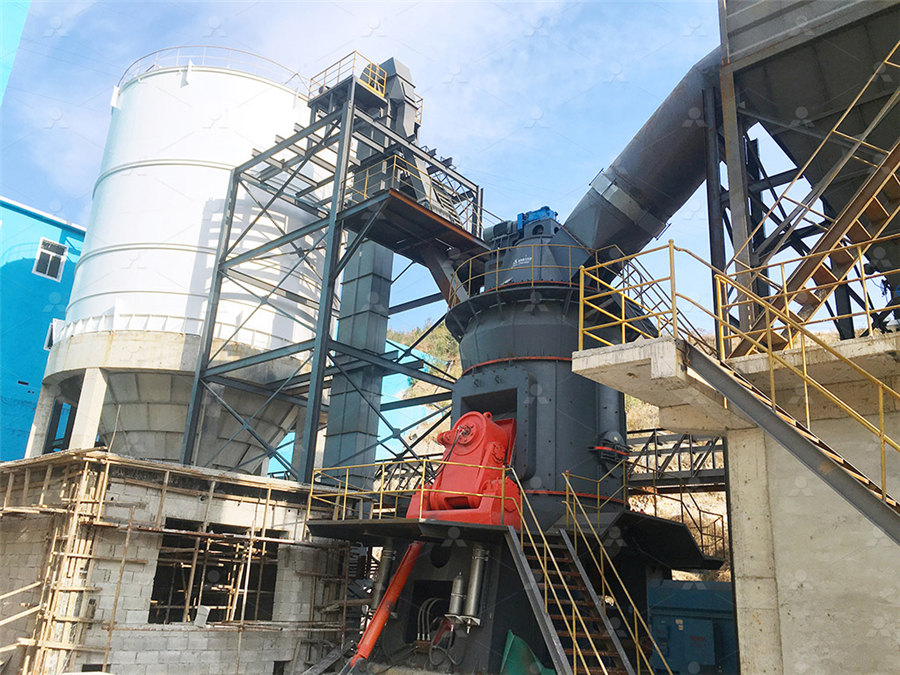
Coal Mill an overview ScienceDirect Topics
Coal mills or pulverizers play a very essential part in the coalfired power production system Coal mills grind the coal into fine powder, and the primary air entering the mill dries and drives the Production of cement also requires a supply of electrical energy, expressed as Cement PlantThe Loesche coal grinding mill range is divided into two serial types: Small twin mills constructed to individual specifications (LM 122 D to LM 202 D), with table diameters from 1,200 to 2,000 LOESCHEMILLSLoesche produces grinding mills and classifiers for all solid fuels, with throughputs ranging from 8 to 240 t/h (16,000 to 640,000 lb/h) With a long wear life and easy replacement of worn parts, Loesche Grinding Technology for the Power Industry
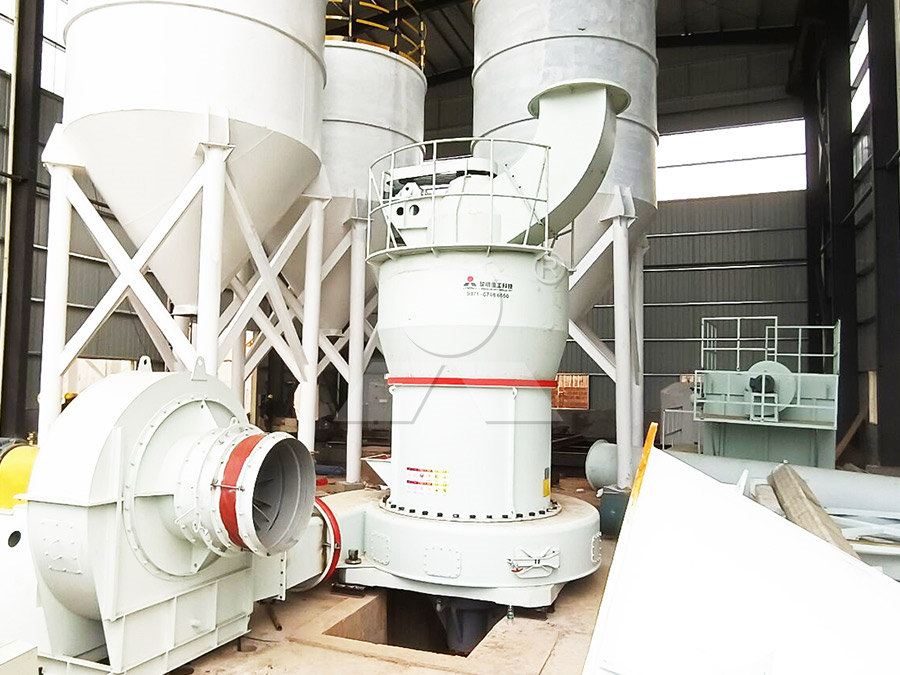
Analysis of the Coal Milling Operations to the Boiler Parameters
Abstract: Fuel and firing system purposely to deliver light fuel oil or coal as one of the primary elements of fuel in an ideal condition for combustion to take place in the boiler combustion From our original E/EL ballandrace type pulverizers for lower capacity applications, to the latest BW Roll Wheel™ pulverizer capable of grinding up to 230,000 pounds of coal per hour (104,300 kg/hr), we set the standard for high Reliable Coal Pulverizers and Mills » Babcock WilcoxCoal quality (that is the properties of coal) has an impact on many parts of a power plant including the coal handling facilities, pulverising mills, boiler, air heater, ESP, ash disposal as well as Expert systems and coal quality in power generation USEAThe original fuel system consisted of three springloaded, MB type, vertical spindle mills, each gravimetric belt feeder, seal air fan, 1800 rpm primary air fan, and four mill outlets supplying WorldProven Coal Pulverizer Technology Debuts in the US
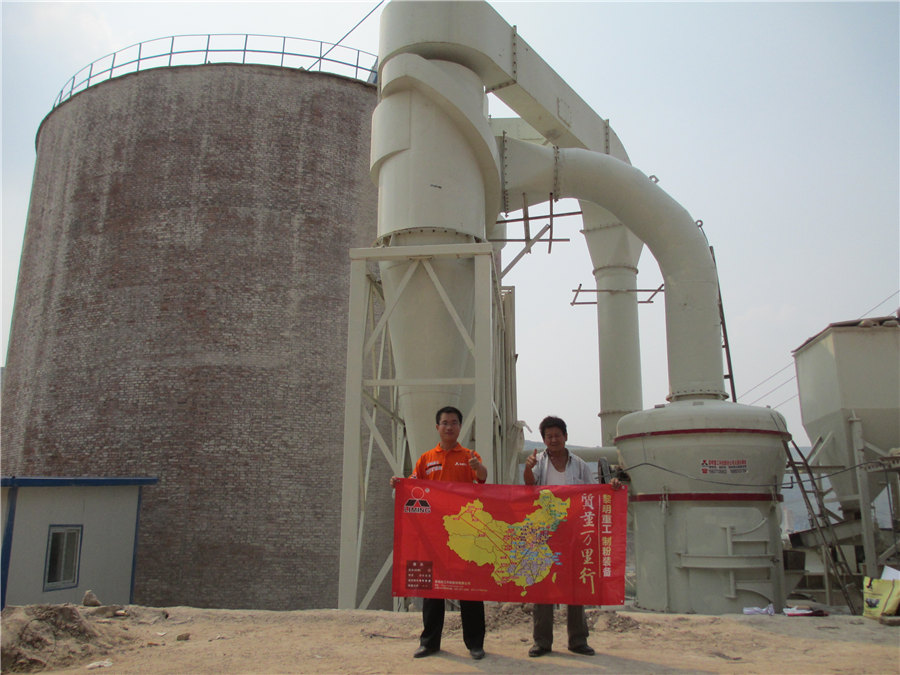
Derivation and validation of a coal mill model for control
2012年5月1日 The paper presents development and validation of a coal mill model to be used for improved mill control, which may lead to a better load following capability of power plants The BTM is a lowspeed mill that primarily grinds coal by impact and attrition The VRM is a medium speed mill that grinds coal by compression and, because of the low coal inventory in A Comparison of Three Types of Coal Pulverizers Babcock Power2020年4月2日 Milling system in coal power plant purposely to process the raw coal to become as pulverise fuel before enter to the boiler furnace Pulverise fuel enter to the boiler furnace throughAnalysis of the Coal Milling Operations to the Boiler In addition to the requirement by NFPA 85 for inerting a tripped mill system, coal mill OEMs usually recommend that a mill system be inerted during both the normal mill startup and shut down process Steam is commonly employed in the power industry for coal pulverizer system inerting, due to its ready availability and cost effectivenessMill Steam Inerting System Review and Performance Validation
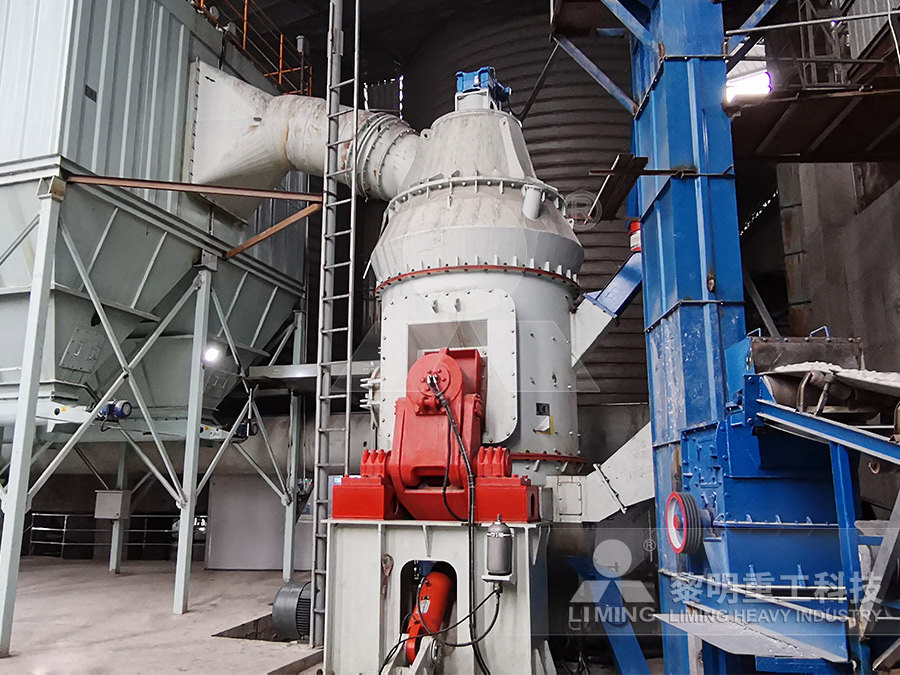
A Comparison of Three Types of Coal Pulverizers Babcock Power
Refer to Table I for a summary of the design features for each mill system Mill Comparisons—General The BTM is a lowspeed mill that primarily grinds coal by impact and attrition The VRM is a medium speed mill that grinds coal by compression and, because of the low coal inventory in the mill and flat grindingThe ATOX mill will grind and dry coal containing more than 20% moisture in one operation The possibility of customersupplied parts, along with the low civil costs that accompany compact mill installation, add to the excellent economy of the ATOX coal mill Working principles The raw coal enters the mill via a rotary sluice and feed chuteATOX COAL MILL2021年3月12日 1 Introduction Two mill systems are employed for most coal grinding applications in the cement industry These are, on the one hand, vertical roller mills (VRM) that have achieved a share of almost 90% and, on the other MPS mills for coal grinding AYS EngineeringLOESCHE Energy Systems supply LOESCHE coal mills type LM 353D to Rafako In May 2015, LOESCHE Energy Systems successfully signed a contract to supply 5 off LOESCHE coal mills type LM 353D with LSKS Classifiers to Rafako SPV for a New Power Unit in TAURON Wytwarzanie SA Jawzorno III Power Plant in PolandPower Industry Loesche
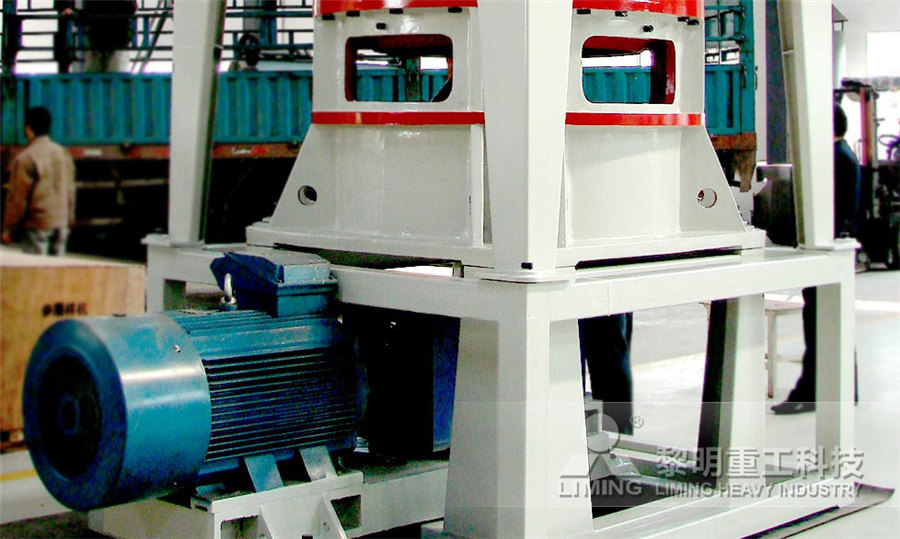
Coal pulverizer mill system modeling for failure simulation
2023年5月8日 They function to supply coal fuel in the furnace; thus, they determine the quality of perfect combustion Research on fault diagnosis of coal mill system based on the simulated typical fault samples,” Measurement 2020, vol 161, ISSN 02632241,FT Coal has the infrastructure and logistical capabilities to ensure the reliable supply of coal products to multiple sites We operate a direct account with Transnet Freight Rail, through which we have a steady and consistent feed of trains carrying our containerised coal products into the Western Cape and KwaZuluNatalFT Coal – Coal Supply Logistics2015年8月1日 Mill problems originate mainly due to poor controls or faults occurring within the milling system As discussed by GQ Fan and NW Rees [3], the control of mills remains very simple in most of the power plants due to the fact that the mill system is highly nonlinear with strong coupling among the variables and it is very difficult to measure some important Review of control and fault diagnosis methods applied to coal Decision Support System for Coal Mill Fault Diagnosis in CoalFired Steam Power Plant *Joga Dharma Setiawan Mechanical Engineering Department, Universitas Diponegoro, Jl Prof Sudarto, SH, Tembalang, Semarang, Indonesia 50275, IndonesiaDecision Support System for Coal Mill Fault Diagnosis in Coal
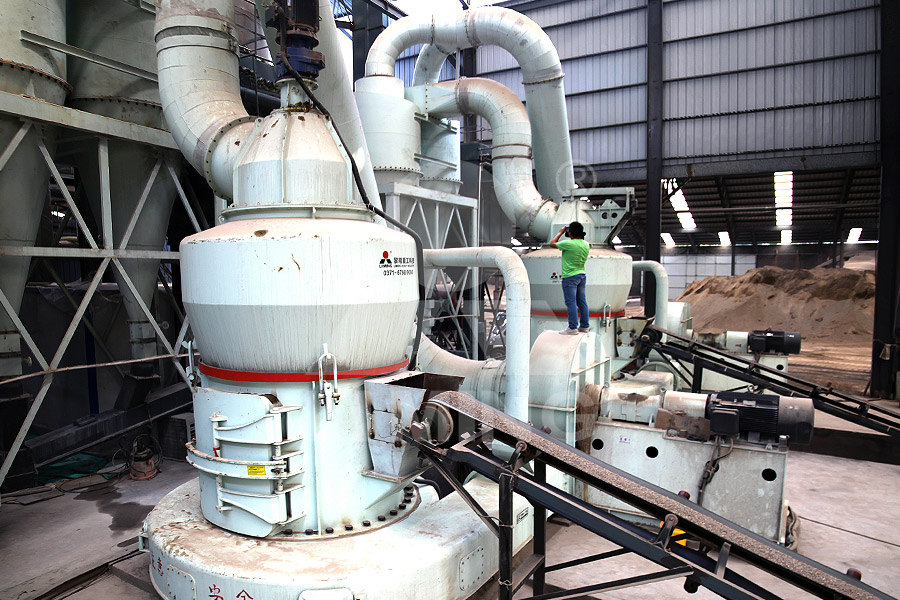
RULA BULK MATERIALS HANDLING
The code requires coal feeders to withstand explosions of 344 kPa Our indepth Finite element designs ensure that we can optimize material strength and costs Each coal feeder system is unique We design our coal mill feeders to integrate elegantly into the plant, while meeting the capacity and other technical requirements Design Features2020年8月12日 This study shows the performance of a currently running vertical roller coal mill (VRM) in an existing coalfired power plant In a power plant, the coal mill is the critical equipment, whose An investigation of performance characteristics and 2020年4月7日 The main task of a coal mill system is to prov ide qualified fuel for the pulverized coal boiler In fails, th e fuel supply of the boiler will not be guaranteed directly, Modeling of Coal Mill System Used for Fault 2012年7月10日 Alstom has secured an order close to 4 million/INR 260 million from Tata Projects Limited for the supply of a Coal Grinding System for National Mineral Development Corporation Limiteds (NMDC) Nagarnar Blast Furnace ProjectAlstom to supply Coal Grinding System for NMDCs first Blast
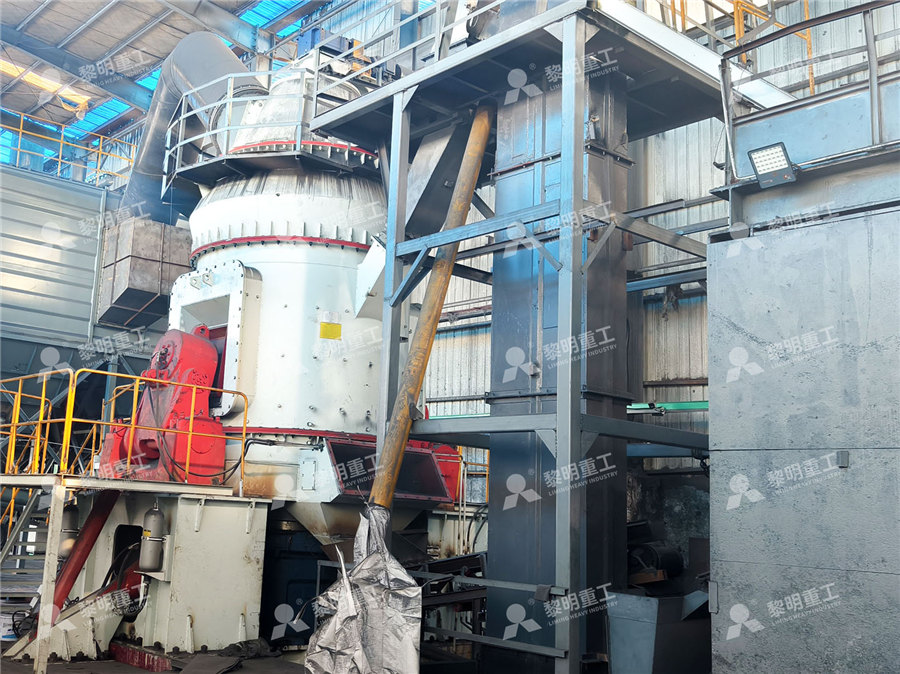
Analysis of the Coal Milling Operations to the Boiler Parameters
2020年4月2日 Milling system in coal power plant purposely to process the raw coal to become as pulverise fuel systemAuxiliary ste am supply for inerting Coal mill motor power (kW) 0 4171 4548 2012年11月17日 2Coal pulverizer/mill system One of the critical power plant components that is relied upon to convert the energy stored in coal into electricity is the coal pulverizer or mill The coal flow is controlled by the feeder, allowing coal to flow into the pulverizer mill The pulverized coal and air mixture is then transport to the boiler burner Coal mill pulverizer in thermal power plants PPT SlideShareThe supply of processed coal to the plant is critical to the uninterrupted power generation in CoalFired Power Station and like any crushing or milling process, System: Mill Drive Gearbox Oil: 600L Mobil 632 gear oil ISO Prior to CJC®: 23/22/21 ISO After CJC®: 18/16/12Coal Mills and Coal Crushers IQ Oil AustraliaCOAL FEEDING SYSTEM Free download as Powerpoint Presentation (ppt / pptx), PDF File (pdf), Text File (txt) or view presentation slides online The document summarizes the coal feeding system for a power plant, including five coal bunkers that feed coal to five mills through rotary coal feeders (RC feeders) There are three types of RC feeders volumetric, Coal Feeding System (Coal Bunkers, RC Feeders Coal Mills)
.jpg)
Model Predictive Control of Duplex Inlet and Outlet Ball Mill System
2019年3月7日 The fineness of pulverized coal is difficult to be measured online directly, but it is mainly affected by the quantity of air supply, the amount of coal and the speed of the mill, so it can be represented by these three variables indirectly 222 Model VerificationCoal Supply System equipment Stacker and Reclaimer Stacker and reclaimer parts Crusher Conveyor Feeder Composed equipment Screen Auxiliary equipment HP coal mill adopts a new type of spiral bevel gear and planetary gear twostage reduction vertical transmission at home and abroad, HP Bowl type millspower plant equipmentIn the late 1930’s, inthemill coal drying was relatively new, and Schulte (1939) the independence of the primary air supply from the demands made by the mill The systems were mOre expensive both in capital cost and to install and operate when compared with direct firing, The mill requires a hot gas supply for dryingCOAL PREPARATION AND FIRING INFINITY FOR CEMENT EQUIPMENTThey serve to supply coal fuel in the furnace to get perfect combustion In the operation of coal mills, the drying process in the coal pulverizer mill system is provided Those conditions cause frequent changes in operating patterns such as setting the flow rate of coal and primary airCoal IJSER
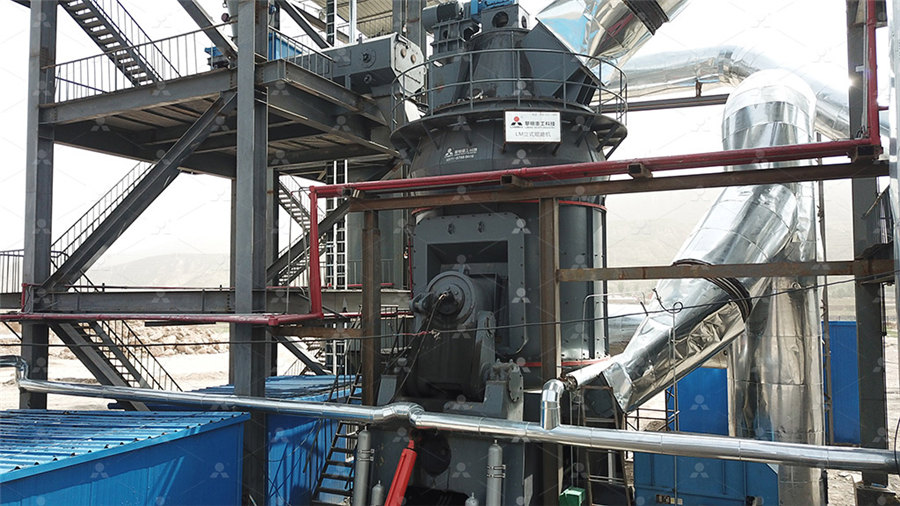
MRHS Mill Reject Handling System in Thermal
The function of Mill Reject Handling system (MRHS) is to automatically discharge the iron pyrite and other non‐grind‐able material from coal mill through an outlet connection to the reject conveying system Basic Working of Mill Reject 1927 First Loesche coal mill delivered for the Klingenberg power station in Berlin 1953 500th coal mill plant sold worldwide 1961 Introduction of hydraulic spring assembly system 1965 Construction of first pressure mill (LM 122 D) 1980 Delivery of first modular coal mill (LM 263 D) 1985 Delivery of first selfinerting coal grinding plant (LM 212 D) for the steel industry (PCI LOESCHEMILLS: pradeebhamit@gmail, npappa@rediffmail , vasanthi@annauniv Abstract: The paper presents development and validation of coal mill model (including the action of classifier) to be used for improved coal mill control The model is developed by using the mass and heat balance equations of the coal mill(PDF) Modeling and Control of Coal Mill AcademiaCoal Feed Systems For Boiler and Coal Milling Plant Gravimetric and Volumetric Systems Belt and Chain Type Feeders Q Stock Equipment Company established in 1929 Q First Gravimetric Coal Feeder (1957) designated as ASME Historic Landmark in 1995 Q More Feed System installations than all competitors combined 8,000 Feeders supplied worldwide Q Australia Q Coal Feed Systems For Boiler and Coal Milling Plant Gravimetric
.jpg)
Modeling of Coal Mill System Used for Fault Simulation MDPI
2020年4月7日 Monitoring and diagnosis of coal mill systems are critical to the security operation of power plants The traditional datadriven fault diagnosis methods often result in low fault recognition rate or even misjudgment due to the imbalance between fault data samples and normal data samples In order to obtain massive fault sample data effectively, based on the 2014年1月1日 Two mill systems are employed for most coal grinding applications in the cement industry These are, on the one hand, vertical roller mills (VRM) that have achieved a share of almost 90% and, on (PDF) MPS mills for coal grinding ResearchGate1980 Delivery of first modular coal mill (LM 263 D) 1965 Construction of first pressure mill (LM 122 D) 1961 Introduction of hydraulic spring assembly system 1953 th500 coal mill plant sold worldwide 1927 First Loesche coal mill delivered for the Klingenberg power station in Berlin We have been successfully involved in the grinding of solidLoesche Grinding Technology for the Power IndustryJapan to manufacture supply stateoftheart UBE Vertical Roller Mills for grinding applications related to Raw material, Coal, Clinker and Slag Reliable Performance performs drying grinding classification and pneumatic transportation simultaneously The mill consists of the lower casing, upper casing, tableVERTICAL ROLLER MILLS AMCL
.jpg)
Coal Mill Manual PDF Furnace Combustion
Coal Mill Manual Free download as PDF File (pdf), Text File (txt) or read online for free This document provides an overview of the operation and maintenance of a pulverized coal system used for direct coal firing in power plants It describes the key components of the system including bowl mills that pulverize coal, windboxes that inject coal into the furnace, feeders that supply In addition to the requirement by NFPA 85 for inerting a tripped mill system, coal mill OEMs usually recommend that a mill system be inerted during both the normal mill startup and shut down process Steam is commonly employed in the power industry for coal pulverizer system inerting, due to its ready availability and cost effectivenessMill Steam Inerting System Review and Performance ValidationRefer to Table I for a summary of the design features for each mill system Mill Comparisons—General The BTM is a lowspeed mill that primarily grinds coal by impact and attrition The VRM is a medium speed mill that grinds coal by compression and, because of the low coal inventory in the mill and flat grindingA Comparison of Three Types of Coal Pulverizers Babcock PowerThe ATOX mill will grind and dry coal containing more than 20% moisture in one operation The possibility of customersupplied parts, along with the low civil costs that accompany compact mill installation, add to the excellent economy of the ATOX coal mill Working principles The raw coal enters the mill via a rotary sluice and feed chuteATOX COAL MILL
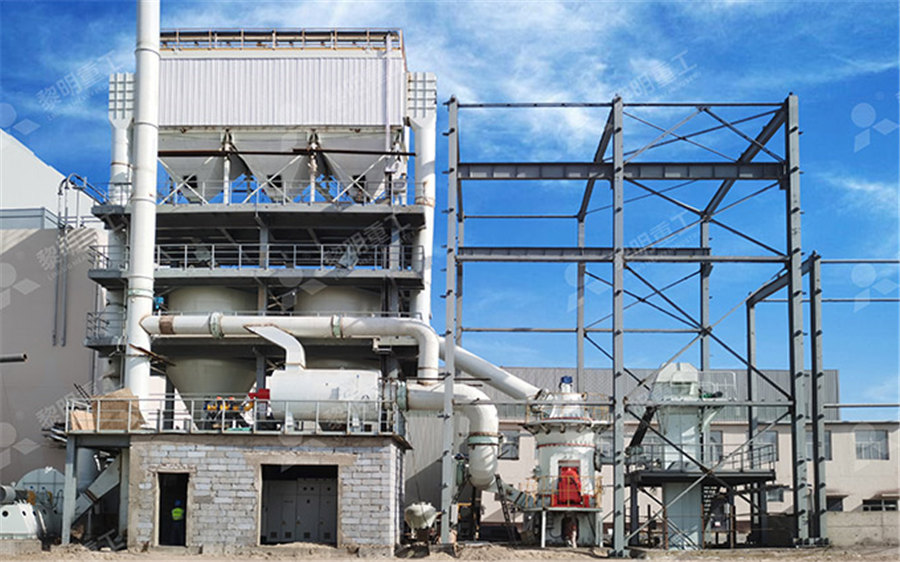
MPS mills for coal grinding AYS Engineering
2021年3月12日 1 Introduction Two mill systems are employed for most coal grinding applications in the cement industry These are, on the one hand, vertical roller mills (VRM) that have achieved a share of almost 90% and, on the other LOESCHE Energy Systems supply LOESCHE coal mills type LM 353D to Rafako In May 2015, LOESCHE Energy Systems successfully signed a contract to supply 5 off LOESCHE coal mills type LM 353D with LSKS Classifiers to Rafako SPV for a New Power Unit in TAURON Wytwarzanie SA Jawzorno III Power Plant in PolandPower Industry Loesche2023年5月8日 They function to supply coal fuel in the furnace; thus, they determine the quality of perfect combustion Research on fault diagnosis of coal mill system based on the simulated typical fault samples,” Measurement 2020, vol 161, ISSN 02632241,Coal pulverizer mill system modeling for failure simulationFT Coal has the infrastructure and logistical capabilities to ensure the reliable supply of coal products to multiple sites We operate a direct account with Transnet Freight Rail, through which we have a steady and consistent feed of trains carrying our containerised coal products into the Western Cape and KwaZuluNatalFT Coal – Coal Supply Logistics
.jpg)
Review of control and fault diagnosis methods applied to coal
2015年8月1日 Mill problems originate mainly due to poor controls or faults occurring within the milling system As discussed by GQ Fan and NW Rees [3], the control of mills remains very simple in most of the power plants due to the fact that the mill system is highly nonlinear with strong coupling among the variables and it is very difficult to measure some important Decision Support System for Coal Mill Fault Diagnosis in CoalFired Steam Power Plant *Joga Dharma Setiawan Mechanical Engineering Department, Universitas Diponegoro, Jl Prof Sudarto, SH, Tembalang, Semarang, Indonesia 50275, IndonesiaDecision Support System for Coal Mill Fault Diagnosis in Coal The code requires coal feeders to withstand explosions of 344 kPa Our indepth Finite element designs ensure that we can optimize material strength and costs Each coal feeder system is unique We design our coal mill feeders to integrate elegantly into the plant, while meeting the capacity and other technical requirements Design FeaturesRULA BULK MATERIALS HANDLING