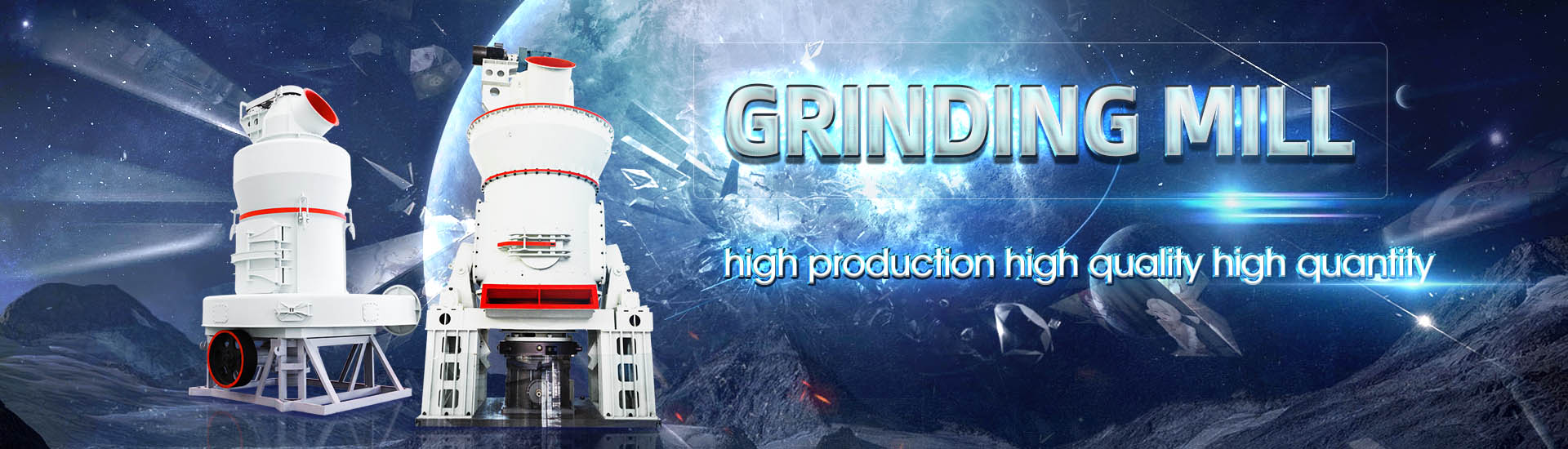
iron oxide crushing production process

Iron Ore Processing: From Extraction to Manufacturing
2024年4月26日 Iron ore processing is a complex and vital process that transforms raw iron ore into usable steel From exploration and extraction to grinding, beneficiation, and ironmaking, each stage plays a crucial role in 2017年1月1日 Effective technology for a complex wasteless processing of the iron ores has been designed and includes three main components (plats): comminution plant, briquette plant, pigment plant The(PDF) Effective Processing of the Iron Ores2020年10月26日 Steelmaking viz carbon steel and alloy steel is a multistep process where iron ore is the starting material used for iron making Blast furnace iron making is mostly adopted by industries throughout the globe [1, 2] Plasma Processing of Iron Ore IntechOpen2018年7月15日 In this paper, the morphology and microstructure evolution of iron oxide in CLC were studied, and the essential cause of its deactivation was obtained, which provided Redox reaction induced morphology and microstructure evolution
.jpg)
Iron Ore Pelletizing Process: An Overview IntechOpen
Iron ore and iron ore pellets are important sources of iron for manufacturing steel The iron ore production has significantly expanded in recent years, owing to increasing steel demands in The primary objective of iron making is to release iron from chemical combination with oxygen, and, since the blast furnace is much the most efficient process, it receives the most attention here Alternative methods known as direct Iron processing Smelting, Refining, Alloying Britannica2022年10月20日 Making iron and steel from iron ore requires a long process of mining, crushing, separating, concentrating, mixing, agglomeration (sintering and pelletizing), and Iron Ore Processing, General SpringerLink2018年7月11日 Iron ore and iron ore pellets are important sources of iron for manufacturing steel The iron ore production has significantly expanded in recent years, owing to increasing steel demandsIron Ore Pelletizing Process: An Overview ResearchGate
.jpg)
(PDF) i) Direct Reduced Iron: Production
2016年3月30日 In book: Encyclopedia of Iron, Steel, and Their Alloys (pppp 10821108) Chapter: i) Direct Reduced Iron: Production; Publisher: CRC Press, Taylor and Francis Group, New York2013年2月23日 Recrystallization of iron oxides is essentially a physical process in which smaller particles consolidate into larger ones with the loss of surface energy During the recrystallization of iron oxides, continued growth of iron Introduction to Iron ore Pellets and Pelletizing 2017年2月16日 PDF Sintering is a thermal agglomeration process that is applied to a mixture of iron ore fines, recycled ironmaking products, fluxes, slagforming Find, read and cite all the research you (PDF) Iron Ore Sintering: Process ResearchGate2024年2月5日 Electrochemical chloriron process for iron production from iron oxide and salt water Berkley B Noble, 1,2Anastasiia Konovalova, Louka J Moutarlier, 1,2 Valerie Brogden, 3 and Paul A Kempler1 ,2 4 * SUMMARY The iron and steel industry accounts for 8% of global greenhouse gas emissions Electrochemical reduction of iron ore to metal forElectrochemical chloriron process for iron production from iron oxide
.jpg)
Cement Clinker Manufacturing Process with Reactions
Alumina and iron oxide react: Calcium carbonate continues to react with other oxides and no free lime is yet formed Though tricalcium aluminate is stable here, poorly crystallized mayenite (Ca 12 Al 14 O 33) seems to be formed The reactions at this stage are: 12 CaCO 3 + 7 Al 2 O 3 → Ca 12 Al 14 O 33 + 12 CO 2 4 CaCO 3 + Al 2 O 3 + Fe 2 O 3 Iron processing Ores, Smelting, Refining: Iron ores occur in igneous, metamorphic (transformed), or sedimentary rocks in a variety of geologic environments Most are sedimentary, but many have been changed by weathering, and so their precise origin is difficult to determine The most widely distributed ironbearing minerals are oxides, and iron ores consist mainly of Iron processing Ores, Smelting, Refining Britannica2018年7月15日 The most important aspect is that iron oxides experience repeated reduction and oxidation whereas inert oxides remain as initial For the different phases of iron oxides, the melting temperature of Fe 3 O 4 is higher than that of Fe 2 O 3 According to the XRD results in Fig 3, the main phase was Fe 3 O 4 after reduction with 10 minRedox reaction induced morphology and microstructure evolution of iron Table 181 shows the most common titanium minerals along with their chemical compositions (Lakshmanan et al 2014)Titanium dioxide is produced from the following ores: Ilmenite (FeTiO 3), rutile, anatase, and leucoxene (TiO 2 xFeO yH 2 O) Other sources of raw material for the production of titanium dioxide are slag produced during iron smelting and synthetic rutile Innovative Process for the Production of Titanium Dioxide
.jpg)
Iron ore crushing and screening process SBM Ultrafine Powder
2022年8月3日 The iron ore processing and production process mainly includes three processes: crushing, grinding and beneficiation In the crushing process, the threestage closedcircuit crushing is more modern and suitable for highhardness iron ore crushing and can complete the work of ore crushing and partial dissociation, thereby improving the subsequent grinding 2024年3月20日 Ironmaking processes that do not generate greenhouse gas (GHG) emissions are needed for netzeroemissions energy systems 1 Most emissions associated with iron and steel production result from stochiometric quantities of CO 2 (∼15 kg CO 2 per kg Fe) produced during reduction of iron oxide ores in blast furnaces 2, 3 Demand for steel is unlikely to Electrochemical chloriron process for iron production from iron oxide Iron very rarely occurs in the earth's surface as a metal It is widely distributed, combined with oxygen as iron oxides In fact it is believed that iron makes up about 5% by weight of the earth's crust Geologists recognise various types of iron ore, classified chiefly according to iron (Fe) content (see Table 1 below)The Making of Iron Steel SEAISI2017年1月1日 World production of iron oxide pigments is about 600 paint grade ore, crushing containting more than 48% of Fe on the process of iron reduction under various Development of technology for the production of natural red iron oxide
.jpg)
Iron ore sintering Part 1 Theory and practice of the
2013年8月1日 Sintering is a process by which a mixture of iron ores, fl uxes and coke is agglomerated in a sinter plant to manufacture a sinter product of a suitable composition, quality and granulometry to be 2018年10月23日 The ore is Hematite, chemical name is iron III oxide, the chemical formula is Fe 3 O 4, It has a blood red colour, it is more easily reduced, Iron is from 5060 %, place of deposits is Oasis area (western desert) and western part of Aswan The ore is Limonite, chemical name is Hydrated iron III oxide, the chemical formula is 2Fe 2 O 33H 2 O, It has a yellow hydrated Extraction of Iron from its ores, Iron dressing, Reduction production 2023年2月22日 Process parameters and sensitivities of the batch chloriron cell (A) Relationship between ηFe and J for Fe plated in a batch cell divided by Nafion 115 ηFe >85 % was sustained for current Electrochemical ChlorIron Process for Iron Production from Iron Oxide 2018年7月11日 Iron Ores and Iron Oxide Materials 50 Bentonite, an inorganic binder, has been the main binder used in the iron ore pelletizing process since the beginning of pellet production in the 1950sIron Ore Pelletizing Process: An Overview ResearchGate
.jpg)
Clinker Production an overview ScienceDirect Topics
Calcination is the main process of clinker production, calcining calcium carbonate (CaCO 3) at about 900 °C to form calcium oxide, CaO, lime, and the release of carbon dioxide gas (CO 2) In the next step of the socalled clinker treatment, calcium oxide (CaO) is exposed to temperatures of 1400 °C to 1500 °C together with silica (SiO 2 ), aluminum oxide (Al 2 O 3 ), and ferrous 2017年2月14日 The process has the advantage of low capital expenditure and no requirement of coking coal The metallic iron in this process is produced by the reduction of iron oxide below the fusion temperature of iron ore (1535 deg C) by utilizing carbonaceous material present in the noncoking coalCoal based Direct Reduction Rotary Kiln Process – IspatGuru2024年5月27日 Steel industry is one of the significant pillar industries to ensure national security and drive economic and social development According to the National Bureau of Statistics of China, the Chinese crude steel and blast furnace pig iron production in 2023 reached approximately 1019 billion tons and 871 million tons, accounting for 5397% of global crude Mechanism of thermal compressive strength evolution of carbon 2024年6月4日 The iron oxide (FeO) content had a significant impact on both the metallurgical properties of sintered ores and the economic indicators of the sintering process Precisely predicting FeO content possessed substantial potential for enhancing the quality of sintered ore and optimizing the sintering process A multimodel integrated prediction framework for FeO Identification of working conditions and prediction of FeO content
.jpg)
Highly efficient visible light active iron oxidebased Nature
2024年8月7日 The hydrogen recovery efficiency of iron oxidebased photocatalysts from Sulphide ion acts as the sacrificial agent in the hydrogen production process Different doses of iron oxidebased 2022年1月1日 Iron ore operations commonly employ one or more stages of crushing with screening stages incorporated to remove material meeting product size specifications as soon as possible Lump product (typically between 63 mm and 315 mm) attracts a premium price compared to fines product (typically less than 63 mm)Comminution and classification technologies of iron ore2020年11月1日 Coprecipitation synthesis of stable iron oxide nanoparticles with NaOH: New insights and continuous production via flow chemistry Author links open overlay panel Maximilian O Besenhard a , Alec P LaGrow b c , Aden Hodzic e , Manfred Kriechbaum d , Luca Panariello a , Giorgio Bais f , Katerina Loizou a , Spyridon Damilos a , M Margarida Cruz g , Nguyen Thi Coprecipitation synthesis of stable iron oxide nanoparticles with Electrochemical ChlorIron Process for Iron Production from Iron Oxide and Seawater Berkley B Noble,12 Louka J Moutarlier,12 Paul A Kempler12* 1Department of Chemistry and Biochemistry, University of Oregon, Eugene, OR 97403 2Oregon Center for Electrochemistry, University of Oregon, Eugene, OR 97403 *Correspondence: pkempler@uoregonElectrochemical ChlorIron Process for Iron Production from Iron Oxide
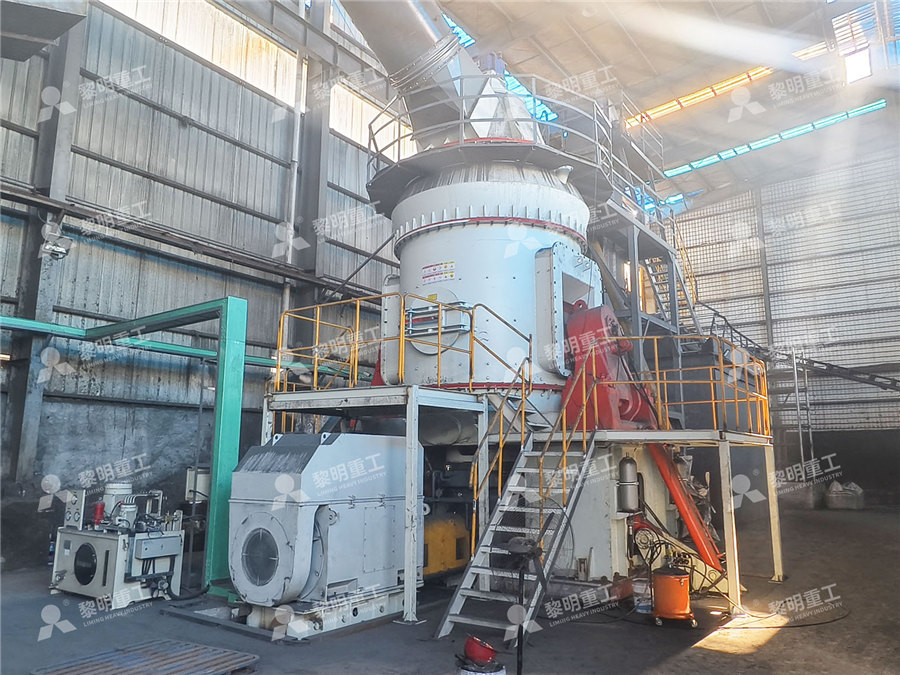
Iron Separation from Bauxite Through SmeltingReduction Process
2017年2月12日 Pedersen Process Alternative process for alumina production is the Pedersen process , which has no red mud production problem This process was patented in Norway in the 1920s by Harald Pedersen, and was used for over 40 years before it was closed down due to economic reasons []It was developed to process ferruginous bauxites with high TiO 2 and SiO Steps in Bayer process : (1) Ore Preparation : It is important to do ore preparation to reduce total precentage of silica in boxite Using crushing and grinding, the silica content reduced from 10% to 15% as bauxite tends to get concentrated in the finer fractions (ie, 100 mesh)Bayer Process Extraction of Aluminium Extractive Metallurgy2024年9月10日 Longer Production Time: The wet process generally takes longer for Cement production compared to the dry process, as it involves additional steps such as slurry formation and drying Conclusion This marks an end to the discussion on the wet and dry processes of Cement manufacture and has also enumerated on the major points of difference between dry Cement Manufacturing Process: Know Extraction, Processing 2023年4月1日 The process yielded calcium aluminate slag as the main product and pig iron as a byproduct which could be reused in the steel industry The calcium aluminate slag was reduced in size by crushing and leaching by using a Na 2 CO 3 solution to extract aluminaToward sustainable green alumina production: A critical review on
.jpg)
Study of reduction kinetics and properties of iron oxides for COREX process
to assess the raw materials for the COREX plant with the selected iron oxides Five kinds of commercial iron oxides (3 pellets and 2 lump ores) were compared by various experiments The chemical and physical properties including bulk density, porosity, surface area and crushing strength of unreduced samples were investigated2019年3月21日 Although the understanding of the hightemperature reduction of iron oxide particles is still not comprehensive, a brief review of the academic reports is helpful for the future work on this topic The hightemperature reduction of iron oxide suspension is characterized by having: rapid reaction, obvious thermal decomposition and melting processReview and data evaluation for hightemperature reduction of iron oxide 2016年3月30日 In book: Encyclopedia of Iron, Steel, and Their Alloys (pppp 10821108) Chapter: i) Direct Reduced Iron: Production; Publisher: CRC Press, Taylor and Francis Group, New York(PDF) i) Direct Reduced Iron: Production2013年2月23日 Recrystallization of iron oxides is essentially a physical process in which smaller particles consolidate into larger ones with the loss of surface energy During the recrystallization of iron oxides, continued growth of iron Introduction to Iron ore Pellets and Pelletizing

(PDF) Iron Ore Sintering: Process ResearchGate
2017年2月16日 PDF Sintering is a thermal agglomeration process that is applied to a mixture of iron ore fines, recycled ironmaking products, fluxes, slagforming Find, read and cite all the research you 2024年2月5日 Electrochemical chloriron process for iron production from iron oxide and salt water Berkley B Noble, 1,2Anastasiia Konovalova, Louka J Moutarlier, 1,2 Valerie Brogden, 3 and Paul A Kempler1 ,2 4 * SUMMARY The iron and steel industry accounts for 8% of global greenhouse gas emissions Electrochemical reduction of iron ore to metal forElectrochemical chloriron process for iron production from iron oxide Alumina and iron oxide react: Calcium carbonate continues to react with other oxides and no free lime is yet formed Though tricalcium aluminate is stable here, poorly crystallized mayenite (Ca 12 Al 14 O 33) seems to be formed The reactions at this stage are: 12 CaCO 3 + 7 Al 2 O 3 → Ca 12 Al 14 O 33 + 12 CO 2 4 CaCO 3 + Al 2 O 3 + Fe 2 O 3 Cement Clinker Manufacturing Process with ReactionsIron processing Ores, Smelting, Refining: Iron ores occur in igneous, metamorphic (transformed), or sedimentary rocks in a variety of geologic environments Most are sedimentary, but many have been changed by weathering, and so their precise origin is difficult to determine The most widely distributed ironbearing minerals are oxides, and iron ores consist mainly of Iron processing Ores, Smelting, Refining Britannica
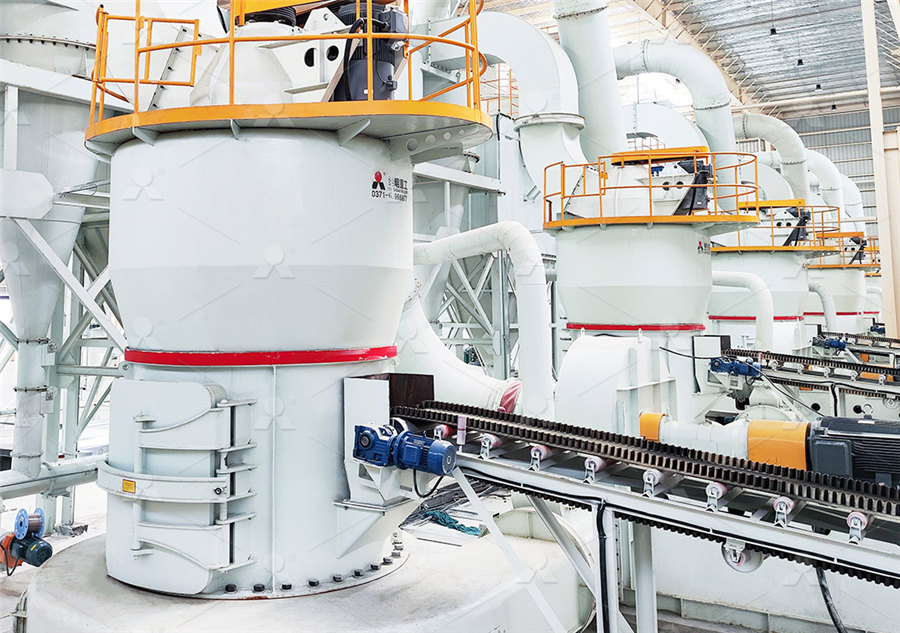
Redox reaction induced morphology and microstructure evolution of iron
2018年7月15日 The most important aspect is that iron oxides experience repeated reduction and oxidation whereas inert oxides remain as initial For the different phases of iron oxides, the melting temperature of Fe 3 O 4 is higher than that of Fe 2 O 3 According to the XRD results in Fig 3, the main phase was Fe 3 O 4 after reduction with 10 minTable 181 shows the most common titanium minerals along with their chemical compositions (Lakshmanan et al 2014)Titanium dioxide is produced from the following ores: Ilmenite (FeTiO 3), rutile, anatase, and leucoxene (TiO 2 xFeO yH 2 O) Other sources of raw material for the production of titanium dioxide are slag produced during iron smelting and synthetic rutile Innovative Process for the Production of Titanium Dioxide2022年8月3日 The iron ore processing and production process mainly includes three processes: crushing, grinding and beneficiation In the crushing process, the threestage closedcircuit crushing is more modern and suitable for highhardness iron ore crushing and can complete the work of ore crushing and partial dissociation, thereby improving the subsequent grinding Iron ore crushing and screening process SBM Ultrafine Powder 2024年3月20日 Ironmaking processes that do not generate greenhouse gas (GHG) emissions are needed for netzeroemissions energy systems 1 Most emissions associated with iron and steel production result from stochiometric quantities of CO 2 (∼15 kg CO 2 per kg Fe) produced during reduction of iron oxide ores in blast furnaces 2, 3 Demand for steel is unlikely to Electrochemical chloriron process for iron production from iron oxide