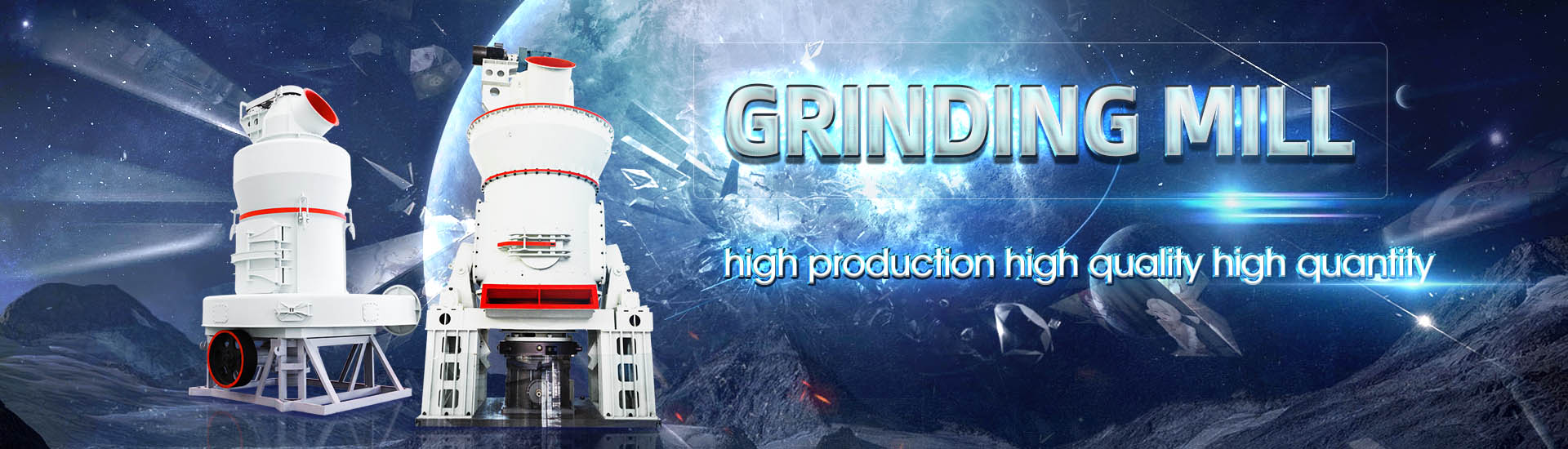
Working principle of gypsum powder making process
.jpg)
Gypsum Plaster Manufacturing Process Gongyi
Working Principle of Gypsum Plaster Manufacturing Process The gypsum and FGD gypsum are fed from the inlet, effective contacting the surface of the heat exchange tube in the shell, and be burnt by the fume as a medium from the 2024年11月5日 Gypsum powder manufacturing is a comprehensive process that harmonizes mining, processing, and quality assurance By understanding each stage of production and Essential Guide to Gypsum Powder Manufacturing ProcessGypsum powdermaking process According to the process requirements, the construction gypsum production line is usually divided into five parts, including crushing system, storage conveying system, grinding system, calcining Gypsum Powder Manufacturing Gypsum Powder 2024年9月28日 The production of gypsum powder using an HGM micro powder grinding mill involves a series of welldefined steps, ensuring highquality results suitable for various Gypsum Powder Manufacturing Process Using HGM Micro Powder
.jpg)
Making Gypsum Board Gypsum Association
To produce gypsum board, crushed natural gypsum or synthetic gypsum is heated or calcined to dehydrate the feedstock Next the calcined gypsum is mixed with water and additives to form a In this process, the gypsum is dried and ground to the required fineness of the plaster in the mill Thanks to the relatively high temperature level in the gypsum calcining mill, the gypsum is Grinding and calcining of gypsum with Pfeiffer grinding plantsGypsum products are used in dentistry, medicine, homes, and industry In homes, gypsum plaster is used to make walls; in industry, it is used to make molds Three types of gypsum products Handbook on Gypsum and Gypsum Based Products NIIR Project Gypsum plaster manufacturing process as well as the main properties of gypsum and gypsum products (fire, acoustic, thermal, and other properties) are described Gypsum products and Gypsum Products Springer
.jpg)
Gypsum Board production flow
Let's see the manufacturing process "Gypsum" is baked in a furnace and made into "calcined plaster" which will solidify when it reacts with water Calcined “gypsum” is mixed with water to make a slurry (muddy state) Then, the slurry Gypsum board making machines The gypsum board manufacturing machines in the world has been takes placed in different ways according to the economic development level and the users of the gypsum panel for construction around Design and Fabrication of Gypsum Board Making The process of manufacturing of shaped components or semifinished products such as bar and sheet from metal powder is called as Powder metallurgy The technique of powder metallurgy combines unique technical features with cost Introduction To Powder Metallurgy Principles of A flow diagram for a typical gypsum process producing both crude and finished gypsum products is shown in Figure 11161 In this process gypsum is crushed, dried, ground, and calcined Not all of the operations shown in Figure 11161 are performed at all gypsum plants Some plants produce only wallboard, and many plants do not produce soil 1116 Gypsum Manufacturing US EPA

How does a briquette machine work types and making process
What is a briquette machine A briquette machine is used to turn the waste fine/powder into a regular shape block, which can help to improve the physical or chemical conditions for those powder, make it easy for transportation, storage, reduce the generated dust and be more useful for further applications The briquette system is able to deal with all kinds of materials under 2017年2月13日 In this paper, waste gypsum from wet flue gas desulfurization (WFGD) mixed with NH3H2O was applied for CO2 absorption in the solidliquidgas phase system The effects of operation temperature, CO2 flow rates, and ammoniatogypsum ratio on carbonation process were discussed Meanwhile, a model for CO2 absorption in the suspension of WFGD gypsum Carbonation of gypsum from wet flue gas desulfurization process Stage 2: Grinding, Proportioning, and Blending The crushed raw ingredients are made ready for the cementmaking process in the kiln by combining them with additives and grinding them to ensure a fine homogenous mixture The composition of cement is proportioned here depending on the desired properties of the cement Generally, limestone is 80%, and the remaining 20% How Cement is Made Cement Manufacturing ProcessStone powder making machine is an ultrafine industrial grinding mill, dolomite, calcite, limestone, kaolin, bentonite, marble, gypsum, quartz, feldspar, clay, talc, fluorite, white mud, mica, refractory material, glass, total about 1000 Working Principle of Stone Powder Making Machine Stone powder making machine is mainly formed by Stone Powder Making Machine
.jpg)
Powder Bed Fusion: The Working Process, Current Applications and
2018年8月7日 Powder bed fusion (PBF) is an umbrella term for three separate threedimensional (3D) printing technologies; selective laser sintering (SLS), direct metal laser sintering (DMLS) and selective Mineralogically identical to natural gypsum, FGD gypsum, or synthetic gypsum, is produced from gas captured within emission control systems at coal fired electric utilities An emission that would compromise air quality, sulfur dioxide (SO2) gas, is the primary contribution coal makes to FGD gypsum Utilities that produce panelgrade synthetic gypsum beneficially reuse FGD sludge FGD Gypsum Production ProcessCooling and addition of gypsum; Milling of gypsum and clinker that will together make the cement; The block diagram of the production process of cement is given below : Figure 1 : Cement production process block diagram 2 Cement production step by Cement Production Demystified: StepbyStep Process and Food powder mixing Explore this informative page to gain insights into the world of food powder mixing Whether you're a smallscale business owner looking for practical mixing solutions or part of a largescale production facility aiming to maintain highquality standards, this resource offers valuable guidancePowder Mixing: The Ultimate Engineering Guide for Bulk Solids
.jpg)
Gypsum Powder Ball Mill Gypsum Grinding
Gypsum powder ball mill is the key equipment for grinding after the crushing process, which is widely used in the manufacture industries, such as cement, dolomite and other minerals which can be used in cement powder making Fig8 Cost Ball mills for wet grinding • To get the price of the ball mill for 2007: 7 13 Summary The Ball Mill is designed to grind materials by turning the cylindrical shell with grinding medium (eg steel balls) put in the shell, and has a simple structure and ease of handlingworking principle of gypsum wet ball mill CapabuildGypsum is normally only screened to remove ‘fines’ (mainly mudstones), then crushed and finely ground Gypsum/Anhydrite for cement manufacture is supplied in crushed form for further fine grinding with cement clinker C Processing Natural Gypsum When Gypsum ( CaSO 4,2H 2O) is ground to a powder and heated at 150° to 165° C, threeFactsheet on: What is Gypsum?2019年5月21日 The boiling furnace for gypsum industry, gypsum powder production line gypsum powder production line • 0 likes • 594 views G Gery Zhang Follow Shanghai Clirik Machinery devoted into the filed of gypsum powder making machines RD and manufacturing more than 4 The Boiling Furnace Working Principle ShanghaiClirik M The boiling furnace for gypsum industry, gypsum powder
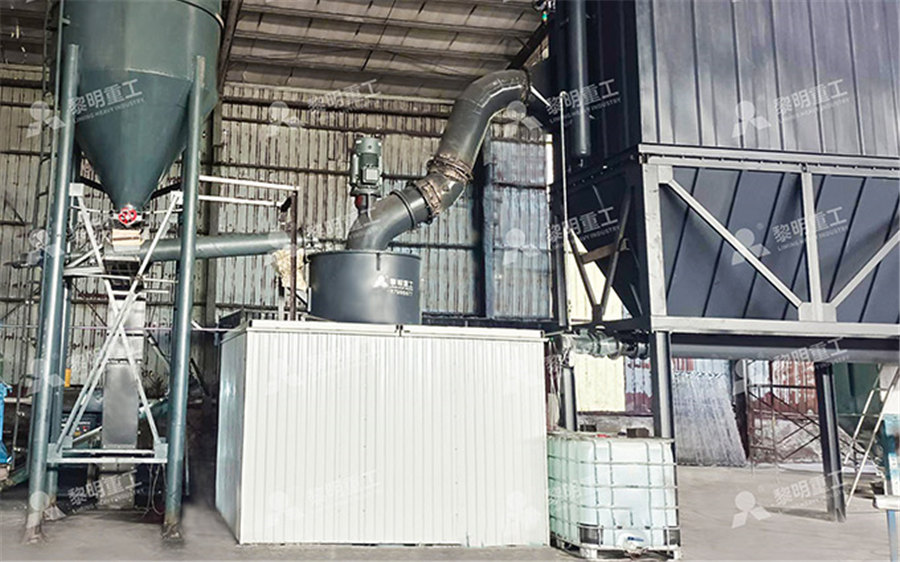
Cement Extraction, Processing, Manufacturing Britannica
2024年11月23日 Cement Extraction, Processing, Manufacturing: Raw materials employed in the manufacture of cement are extracted by quarrying in the case of hard rocks such as limestones, slates, and some shales, with the aid of blasting when necessary Some deposits are mined by underground methods Softer rocks such as chalk and clay can be dug directly by Indeed, products like instant milk or instant coffee are produced thanks to this process The possibility to avoid degradation during drying makes it also a process of choice for pharma Examples of applications for spray drying are given below : Instant milk; Whey powder; Instant coffee; Non dairy creamer; CaseinSpray drying process : overview, fundamentals of spray dryingThe first step in the overall powder metallurgy process is making metal powders There are four main processes used in powder production: solidstate reduction, atomization, electrolysis, In principle, the technique is applicable to all metals that can be melted and is used commercially for the production of iron; copper; alloy steels Making Metal Powder MPIFIntroduction Cyclonic separation is a means of separating different liquid phases (different liquid densities), or, separating particles from a gas streamCyclone separators often form part of a precleaning stage prior to a gas or liquid being discharged This article focuses on the gas cyclone separator Cyclone Separators What’s in a Name? A cyclone separator has several colloquial Cyclone Separator Working Principle (Dust Separator) saVRee
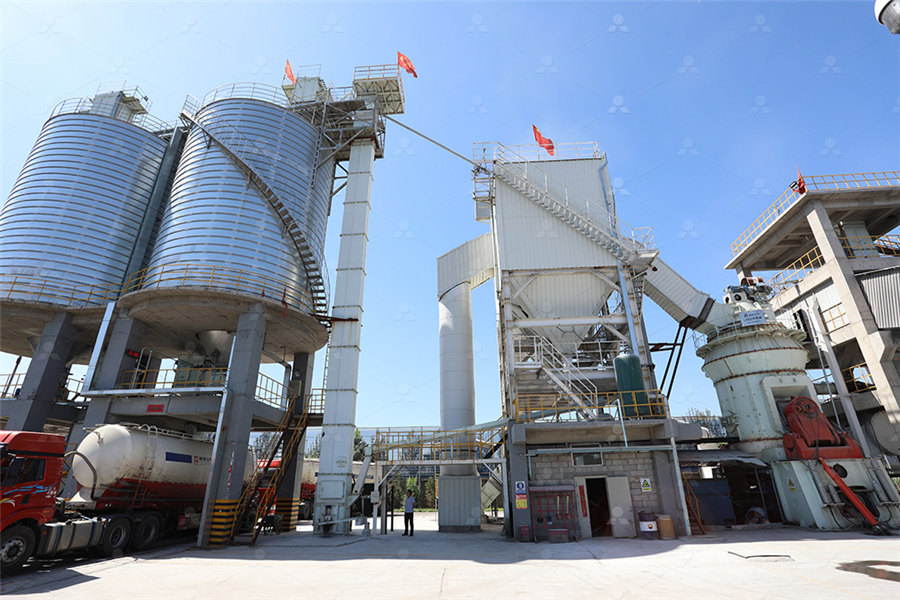
(PDF) Revealing the working principle of sodium
Via this approach, it was ultimately possible to reveal the working principle of STMP as a highly effective anticreep agent and deduce a general understanding for anticreep agents These insights could help to find and The main raw materials are limestone, basalt, sand stone, pumice, gypsum Site Exploration of suitable deposits, for the raw material has three main aims:Verifying the quality of the raw materials Establishing the range of variation in Cement Manufacturing Process INFINITY FOR 2021年6月21日 Powder detergent is a broad term encompassing all kinds of soap manufactured in powder form However, it’s commonly used as a synonym for laundry detergent While most formulas are suitable for both machine and Powder Detergent: Ingredients Manufacturing 5 CEMENT –HISTORY In India, Portland cement was first manufactured in 1904 near Madras, by the South India Industrial LtdBut this venture failed Between 1912 and 1913, the Indian Cement Co Ltd, was established at Porbander (Gujarat) and by 1914 this Company was able to deliver about1000 tons of Portland cement By 1918 three factories were established1 Manufacturing Process of Cement Indus University
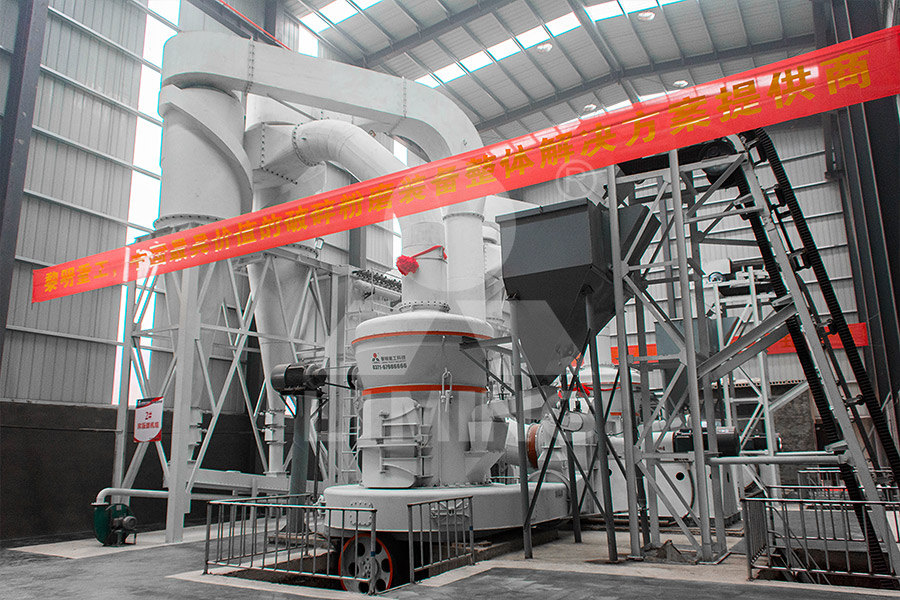
How To Set Up a Gypsum Powder Production Line From Scratch
2023年11月2日 Setting up a gypsum powder production line requires careful planning and a good understanding of the overall process Gypsum powder is widely used in the construction industry for making drywall, plaster, and other building materials +29 Principle of Thus, there is a need to provide an improved method of making a gypsum board so as to improve the control and delivery of the dry additives DETAILED DESCRIPTION [0004] Generally speaking, the present publication is directed to a method of making a gypsum slurry and a gypsum board using a particular dry additive delivery systemMETHOD OF PROVIDING DRY ADDITIVES FOR A GYPSUM BOARD MANUFACTURING PROCESSClick here to see the principle on how gypsum solidifies Chemical reaction of “gypsum” Molding process Calcined “gypsum” is mixed with water to make a slurry (muddy state) Then, the slurry is poured into a line (belt) where board liners are flowing down, thus sandwiched with board linersGypsum Board production flow2024年5月16日 Gypsum Manufacturing Process The gypsum manufacturing process involves several steps, from sourcing raw materials to ensuring the quality of the final product This section will provide an overview of the key aspects of the gypsum manufacturing process, including raw materials, production techniques, and quality control measures Raw MaterialsThe Gypsum Board Manufacturing Process Unveiled Osum
.jpg)
How Cement is Made Portland Cement Association
Chunks are then ground into a fine powder Site A Sustainable Future Roadmap This happens throughout the manufacturing process, making it more sustainable Manufacturers are implementing innovations The clinker keeps cooling and a ball mill grinds it with gypsum or other ingredients into fine cement—about 150 billion 64 Gypsum Powder The Gypsum powder (chemical name: Hydrous calcium sulfate) is a white smooth powder, which is created by heating the gypsum stone The gypsum that is mined is heated, dried, crushed and processed to become the gypsum powder shown in figure 5 It is a nontoxic powder it is mainly used for the purpose of molding, sculpturing, etcDESIGN AND FABRICATION OF BINDER JETTING 3D PRINTERGypsum board making machines The gypsum board manufacturing machines in the world has been takes placed in different ways according to the economic development level and the users of the gypsum panel for construction around Design and Fabrication of Gypsum Board Making The process of manufacturing of shaped components or semifinished products such as bar and sheet from metal powder is called as Powder metallurgy The technique of powder metallurgy combines unique technical features with cost Introduction To Powder Metallurgy Principles of
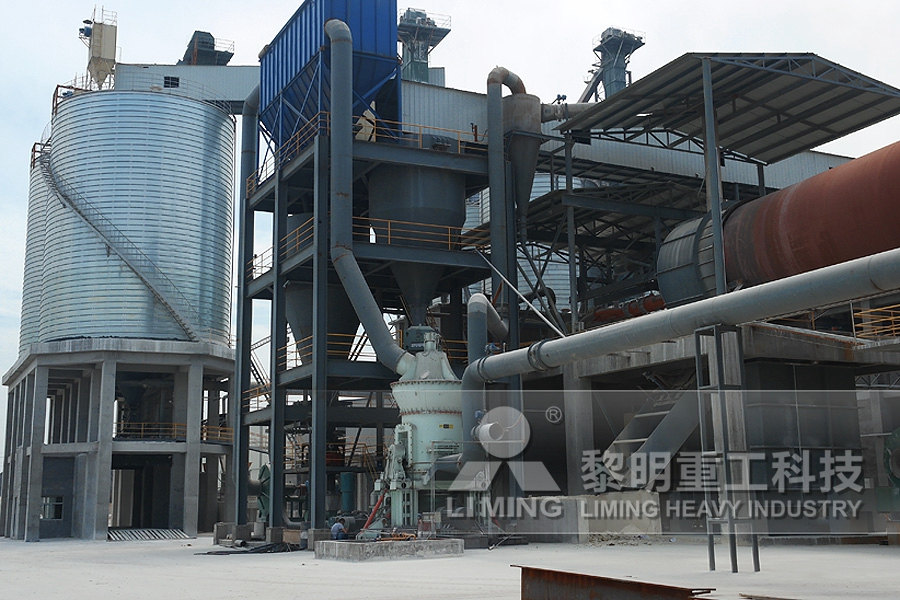
1116 Gypsum Manufacturing US EPA
A flow diagram for a typical gypsum process producing both crude and finished gypsum products is shown in Figure 11161 In this process gypsum is crushed, dried, ground, and calcined Not all of the operations shown in Figure 11161 are performed at all gypsum plants Some plants produce only wallboard, and many plants do not produce soil What is a briquette machine A briquette machine is used to turn the waste fine/powder into a regular shape block, which can help to improve the physical or chemical conditions for those powder, make it easy for transportation, storage, reduce the generated dust and be more useful for further applications The briquette system is able to deal with all kinds of materials under How does a briquette machine work types and making process2017年2月13日 In this paper, waste gypsum from wet flue gas desulfurization (WFGD) mixed with NH3H2O was applied for CO2 absorption in the solidliquidgas phase system The effects of operation temperature, CO2 flow rates, and ammoniatogypsum ratio on carbonation process were discussed Meanwhile, a model for CO2 absorption in the suspension of WFGD gypsum Carbonation of gypsum from wet flue gas desulfurization process Stage 2: Grinding, Proportioning, and Blending The crushed raw ingredients are made ready for the cementmaking process in the kiln by combining them with additives and grinding them to ensure a fine homogenous mixture The composition of cement is proportioned here depending on the desired properties of the cement Generally, limestone is 80%, and the remaining 20% How Cement is Made Cement Manufacturing Process
.jpg)
Stone Powder Making Machine
Stone powder making machine is an ultrafine industrial grinding mill, dolomite, calcite, limestone, kaolin, bentonite, marble, gypsum, quartz, feldspar, clay, talc, fluorite, white mud, mica, refractory material, glass, total about 1000 Working Principle of Stone Powder Making Machine Stone powder making machine is mainly formed by 2018年8月7日 Powder bed fusion (PBF) is an umbrella term for three separate threedimensional (3D) printing technologies; selective laser sintering (SLS), direct metal laser sintering (DMLS) and selective Powder Bed Fusion: The Working Process, Current Applications and Mineralogically identical to natural gypsum, FGD gypsum, or synthetic gypsum, is produced from gas captured within emission control systems at coal fired electric utilities An emission that would compromise air quality, sulfur dioxide (SO2) gas, is the primary contribution coal makes to FGD gypsum Utilities that produce panelgrade synthetic gypsum beneficially reuse FGD sludge FGD Gypsum Production ProcessCooling and addition of gypsum; Milling of gypsum and clinker that will together make the cement; The block diagram of the production process of cement is given below : Figure 1 : Cement production process block diagram 2 Cement production step by Cement Production Demystified: StepbyStep Process and