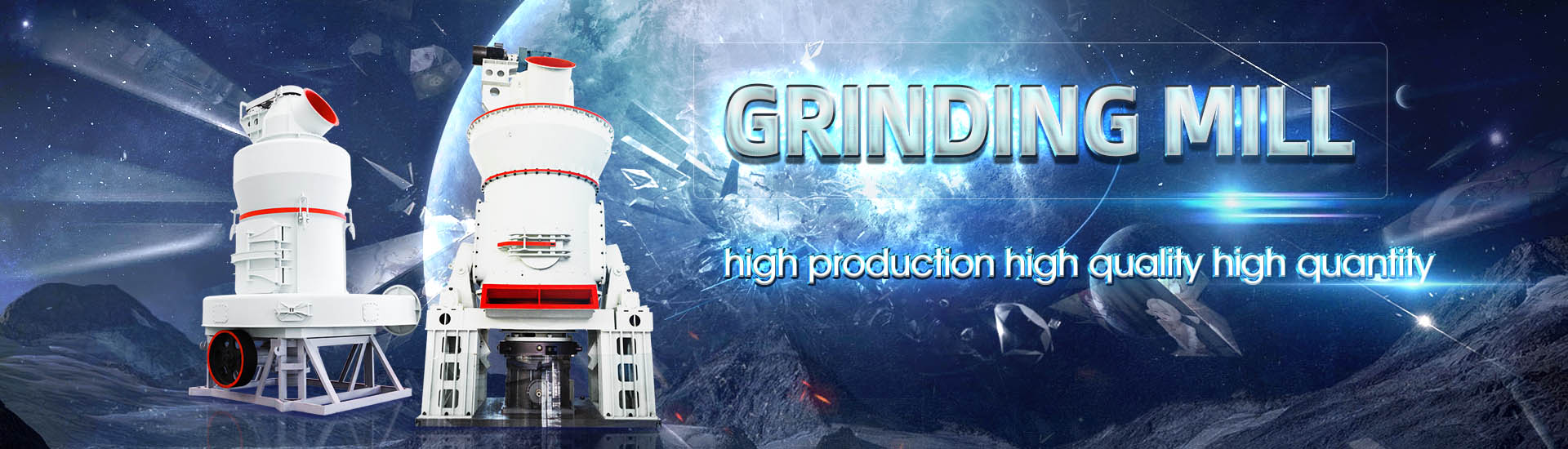
Ore grinding machine electrolytic aluminum waste residue grinding mill chassis
.jpg)
The recycling of carbonrich solid wastes from aluminum
2024年5月23日 Here, we review carbonrich solid wastes with focus on sources and hazards, detoxification, separation, recovery, recycling and disposal Treatment techniques include 2023年9月6日 When electrolytic aluminum enterprises clean and polish aluminum electrolysis, a large number of electrolytic blocks are cleaned from the surface of residual electrodes Electrolytic Grinders for Recycling Smelted Aluminum2023年3月12日 The aluminum electrolysis industry continually and unavoidably produces hazardous solid waste in the form of carbon anode slag Carbon anode slag poses a serious (PDF) Recovery of Carbon and Cryolite from Spent Carbon Anode 2022年4月13日 Here we propose a solidstate electrolysis (SSE) process using molten salts for upcycling aluminium scrap The SSE produces aluminium with a purity comparable to that of A solidstate electrolysis process for upcycling aluminium scrap
.jpg)
Recovery of aluminum from waste aluminum alloy by low
2020年8月1日 Here, we discuss the influence of different processing parameters on electrolytic refining of aluminum alloy and investigate the mechanism of extracting Al from coarse AlSi In this study, grinding characteristics of spent carbon anode from aluminum electrolysis in both ball mill and rod mill were analyzed, and compared based on the utilization of theSelective comminution and grinding mechanisms of spent carbon 2022年8月15日 The developed setup of Electrochemical Surface Grinding performs the hybrid actions of electrochemical machining and surface grinding, simultaneously The MRR Evaluation of Machining Performance for Electrochemical Surface 2024年2月21日 Grind the aluminum electrolysis waste residue through a Cryolite Raymond Roller Mill to below 75250 microns After removing the carbon and iron in the waste residue, Aluminum slag recycled cryolite powder production line
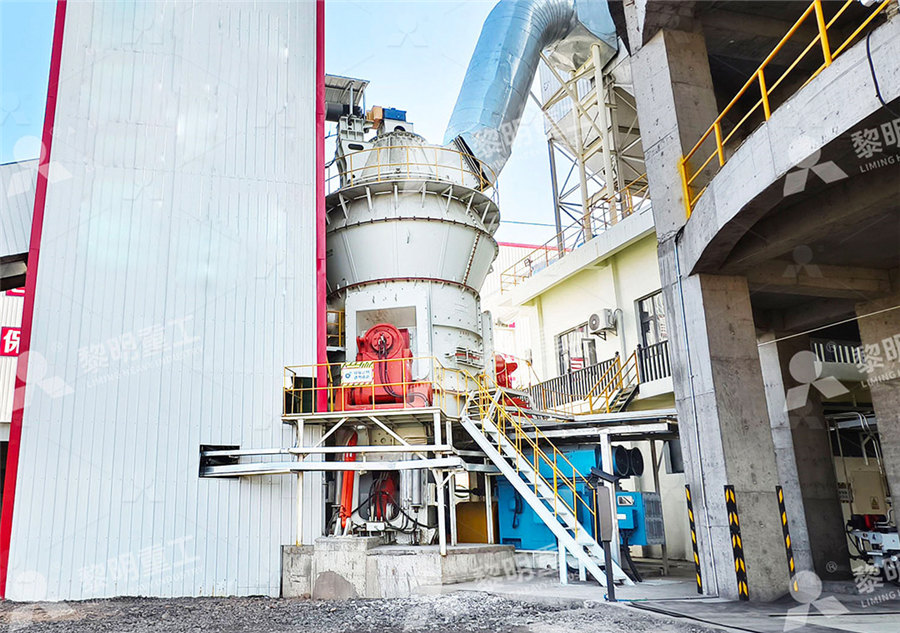
Ultimate Guide – Aluminum Fabrication, Grinding,
2021年6月16日 Aluminum and aluminum alloys are among the most used metals in fabrication,construction, and in the creation of good all around you It is such a useful and versatile metal, but there are some special 2022年10月10日 One of the main electrolytic aluminum production costs is the consumption of carbon anodes, and carbon anode slag is a common hazardous waste in the aluminum industryRecovery of carbon and cryolite from spent carbon 2022年11月1日 Roasting mechanism of lightweight lowaluminum–silicon ceramisite derived from municipal solid waste incineration fly ash and electrolytic manganese residue(PDF) Roasting mechanism of lightweight low 2020年3月31日 This laboratory study investigates selective grinding and beneficiation options for a Greek bauxite ore First, a series of batch grinding tests were carried out in order to investigate the Grinding Behavior and Potential Beneficiation Options of Bauxite Ores
.jpg)
Processing Materials SBM Ultrafine Powder Technology
SBM has been focusing on the field of mining ore crushing and grinding machinery for many years Our grinding equipment can grind 100+ kinds of nonmetallic +17Request PDF On Mar 15, 2015, Mathis Reichert and others published Research of iron ore grinding in a verticalrollermill Find, read and cite all the research you need on ResearchGateResearch of iron ore grinding in a verticalrollermillTo achieve this objective an attempt is made to stabilize the operation by principally controlling the process variables The main disturbances in a grinding circuit are: 1 change in ore characteristics (ore feed rate, grindability, feed particle size distribution, mineral composition and mineral characteristics like abrasiveness, hardness), 2Grinding Mill an overview ScienceDirect Topics2017年6月9日 The unit was converted to a grinder simply by using a charge composed of the material to be ground, water, and a spherical sand grinding medium The details of this machine are shown in figures 13 Summarized in figure 4 are the results of the comparative kaolin grinding tests made in the various grinding machinesAttrition Grinding Mill Design 911Metallurgist
.jpg)
SBM Ultrafine Powder Technology Industrial Grinding Mill,
SBM ultrafine powder technology co,ltd Is China's excellent ore mill supplier Our main products include ultrafine vertical roller mill, ultrafine grinding mill, stone powder production HGM series ring roller mill is a type of advanced grinding machine designed to produce fine to ultrafine powders for various industrial applications2018年8月10日 Based on its chemical composition, mainly of SiO 2 and small amounts of Al 2 O 3 and Fe 2 O 3, EMR is considered to be a type of silicate mining and metallurgy wasteSeveral researchers attempted to recycle manganese and ammonium from EMR by electrolytic processes (Shu et al, 2016a, Shu et al, 2016b), wet processes, and biological methods (Xin et al, 2011)Activation of silicon in the electrolytic manganese residue by 2021年8月1日 Anode carbon residue is produced in the production of electrolytic aluminum Its properties need to be studied for secondary utilization In this paper, mineralogy of anode carbon residue from an Occurrence State of Carbon and Electrolyte in Anode 2019年5月23日 The solid waste mainly includes manganese residues generated from acid immersion, chrome residues from wastewater treatment, and anode sludge from electrolytic processes In this chapter, the physical and chemical properties of manganese metal, manganese ore, manganese metal production, and electrolytic manganese residue (EMR) treatment were Resource Utilization of Electrolytic Manganese Residues
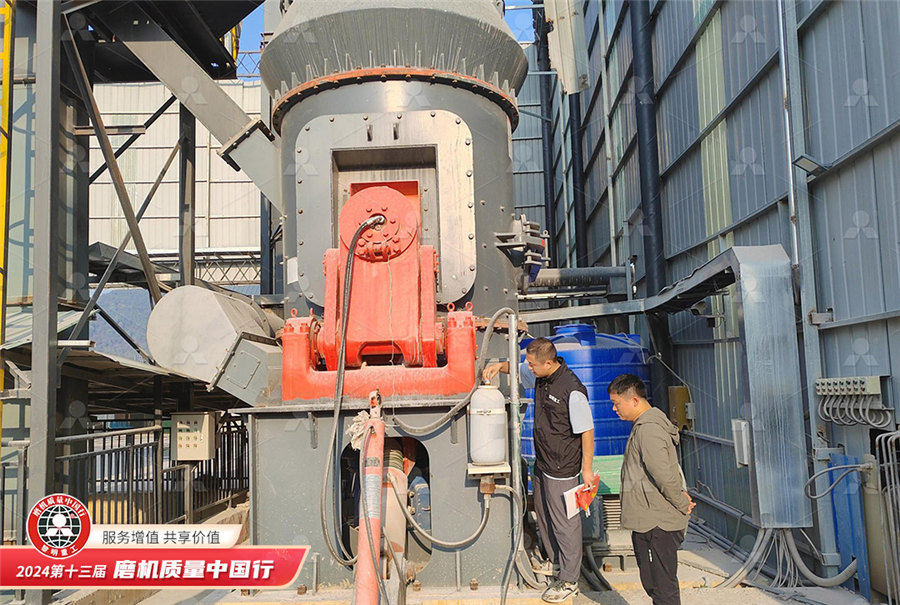
Activation of Silicon in the Electrolytic Manganese Residue by
2018年4月1日 Electrolytic manganese residue (EMR) is a solid waste produced in the process of electrolytic manganese metal (EMM) production In recent years, the accumulation of EMR has caused increasingly 2018年8月17日 Extreme temperatures, impact velocity, mill load, grinding media, ore types, and applications are some of the factors to be considered while installing new linersGrinding Mills — Types, Working Principle Applications2024年5月23日 16 Million metric tons of spent carbon electrodes modify carbonrich solid wastes from aluminum electrolysis are produced annually, threatening ecosystems by cyanide and fluoride pollution Here, we review carbonrich solid wastes with focus on sources and hazards, detoxification, separation, recovery, recycling and disposal Treatment techniques The recycling of carbonrich solid wastes from aluminum electrolytic Grinding Mills: Ball Mill Rod Mill Design PartsCommon types of grinding mills include Ball Mills and Rod Mills This includes all rotating mills with heavy grinding media loads This article focuses on ball and rod mills excluding SAG and AG mills Although their concepts are very similar, they are not discussed herePhotographs of a glass ended laboratory ball mill show Grinding Mills 911Metallurgist
.jpg)
Activation of silicon in the electrolytic manganese residue by
2018年8月10日 Electrolytic manganese residue (EMR) is a solid waste containing several potentially harmful substances, which could pose severe environmental problems The EMR also contains a large amount of silicon in the form of quartz that cannot be really absorbed by plants Plants can only absorb effective silicon, hence, an increase in the content of the effective 2023年7月20日 Therefore, the rod mill is mostly used for coarse grinding of the previous period of ball mill, or grinding of brittle materials and materials against overcrushing, such as tungsten and tin ore before gravity separation; and (3) autogenous mill – it refers to the materials which themselves are collided and ground mutually to be crushed when the grinding mill rotates, and Ore Grinding SpringerLinkRecovery of carbon and cryolite from spent carbon anode slag of electrolytic aluminum by flotation based on the evaluation of selectivity index Yemin Wang1, Xuexia Wang1* and Muhammad Bilal2 Recovery of carbon and cryolite from spent carbon anode slag of2023年3月8日 Electrolytic manganese residue (EMR) is a solid waste produced in the process of electrolytic manganese metal (EMM) production In recent years, the accumulation of EMR has caused increasingly serious environmental problems To better understand the state of EMR recycling in recent years, this paper used a comprehensive literature database to conduct a Progress in comprehensive utilization of electrolytic manganese residue
.jpg)
An easier upgrading process of aluminum dross residue by screening
2014年7月8日 Metallic aluminum in aluminum dross is recovered in Japan generally by physical separation, using the socalled Metal Reclamate Machine (MRM) A large amount of the residue containing oxides, metallic aluminum, nitrides and salts is unavoidably generated as a byproduct of the MRM process Since the metallic aluminum is much more viscous than the relatively 2024年1月10日 Chromite ore processing tailings and lowgrade manganese ores are typically considered waste due to their limited or negligible utility, leading to environmental and storage concerns Researchers globally have explored various methods to utilize or upgrade these wastes, particularly because dumping chromite ore has been linked to severe health issues Valorization From Waste: Combined Reduction of Chromite OreRotational speed: 120 rpm 240 rpm Output: 400 kg/h 30,000 kg/h Machine length: 13,900, 14,700 mm inhales air within the grinding mill and, in turn, the airflow with crushed materials are brought to the classifier whose highspeed impeller will screen the airflow: the unqualified particle size will fall and return Ultrafine mill, Ultrafine grinding mill All industrial manufacturers2024年3月20日 Sulfur resource recovery based on electrolytic manganese residue calcination and manganese oxide ore desulfurization for the clean production of electrolytic manganese Chin J Chem Eng , 28 ( 2020 ) , pp 864 870 , 101016/jcjche201911013Efficient leaching of manganese from electrolytic manganese residue
.jpg)
(PDF) Recovery of Carbon and Cryolite from Spent Carbon Anode
2023年3月12日 Recovery of Carbon and Cryolite from Spent Carbon Anode Slag Using a Grinding Flotation Process Based on Mineralogical CharacteristicsPDF On Jan 1, 2014, Tanveer Saleh published Electrolytic InProcess Dressing (ELID) Grinding for NanoSurface Generation Find, read and cite all the research you need on ResearchGateElectrolytic InProcess Dressing (ELID) Grinding for Nano 200 mm Diameter X 240 mm Long Grinding Mill which can be used as Ball Mill or Rod Mill; Mill Motor Power of 103kW; Feed Ore is precrushed to 15 mm; This ultra small scale grinding mill can function as a primary ball mill or rod mill for or mini flotation plant or as a regrind mill if your pilot plant is built using our larger primary mill SMALL GRINDING / REGRINDING MILL 3 TO 10 KILO/HR2024年2月1日 Aluminum metal was produced using the cryolitealumina molten salt electrolysis method (Ishak et al, 2017)A large amount electrolytic aluminum slag (EAS) is generated during the electrolysis process, as the falling of carbon particles on the anode into the electrolysis cells and the accumulation of lithium fluorine result in energy consumption and electrolyte scrapping Efficient lithium recovery from electrolytic aluminum slag via an
.jpg)
Bauxite Grinding Mill: Unveiling the Role in Aluminum Production
Bauxite grinding mills operate through a combination of impact, compression, and attrition forces In a typical setup, bauxite ore is fed into the mill, where steel balls or other grinding media crush and grind the ore particles As the mill rotates, the grinding media cascade and collide with the bauxite, gradually reducing its size2021年6月16日 Aluminum and aluminum alloys are among the most used metals in fabrication,construction, and in the creation of good all around you It is such a useful and versatile metal, but there are some special Ultimate Guide – Aluminum Fabrication, Grinding, 2022年10月10日 One of the main electrolytic aluminum production costs is the consumption of carbon anodes, and carbon anode slag is a common hazardous waste in the aluminum industryRecovery of carbon and cryolite from spent carbon 2022年11月1日 Roasting mechanism of lightweight lowaluminum–silicon ceramisite derived from municipal solid waste incineration fly ash and electrolytic manganese residue(PDF) Roasting mechanism of lightweight low
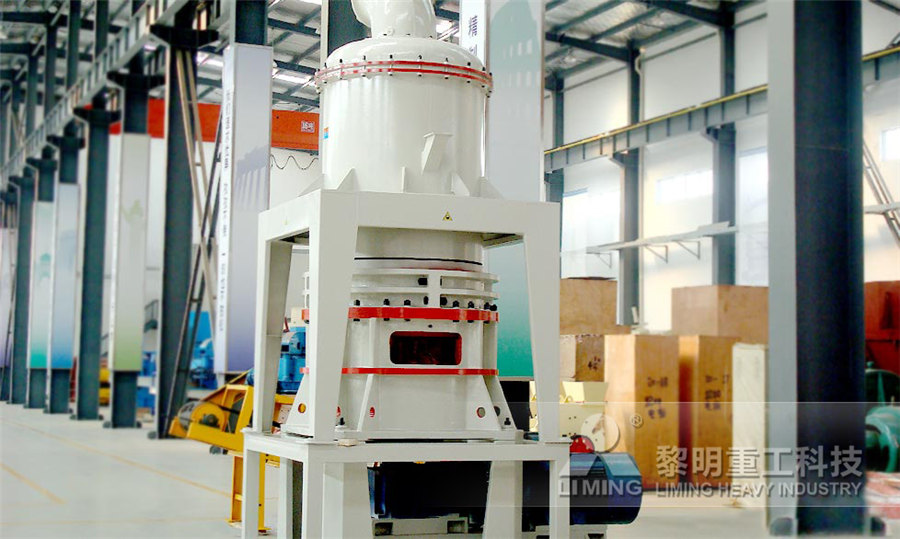
Grinding Behavior and Potential Beneficiation Options of Bauxite Ores
2020年3月31日 This laboratory study investigates selective grinding and beneficiation options for a Greek bauxite ore First, a series of batch grinding tests were carried out in order to investigate the SBM has been focusing on the field of mining ore crushing and grinding machinery for many years Our grinding equipment can grind 100+ kinds of nonmetallic +17Processing Materials SBM Ultrafine Powder TechnologyRequest PDF On Mar 15, 2015, Mathis Reichert and others published Research of iron ore grinding in a verticalrollermill Find, read and cite all the research you need on ResearchGateResearch of iron ore grinding in a verticalrollermillTo achieve this objective an attempt is made to stabilize the operation by principally controlling the process variables The main disturbances in a grinding circuit are: 1 change in ore characteristics (ore feed rate, grindability, feed particle size distribution, mineral composition and mineral characteristics like abrasiveness, hardness), 2Grinding Mill an overview ScienceDirect Topics
.jpg)
Attrition Grinding Mill Design 911Metallurgist
2017年6月9日 The unit was converted to a grinder simply by using a charge composed of the material to be ground, water, and a spherical sand grinding medium The details of this machine are shown in figures 13 Summarized in figure 4 are the results of the comparative kaolin grinding tests made in the various grinding machinesSBM ultrafine powder technology co,ltd Is China's excellent ore mill supplier Our main products include ultrafine vertical roller mill, ultrafine grinding mill, stone powder production HGM series ring roller mill is a type of advanced grinding machine designed to produce fine to ultrafine powders for various industrial applicationsSBM Ultrafine Powder Technology Industrial Grinding Mill, 2018年8月10日 Based on its chemical composition, mainly of SiO 2 and small amounts of Al 2 O 3 and Fe 2 O 3, EMR is considered to be a type of silicate mining and metallurgy wasteSeveral researchers attempted to recycle manganese and ammonium from EMR by electrolytic processes (Shu et al, 2016a, Shu et al, 2016b), wet processes, and biological methods (Xin et al, 2011)Activation of silicon in the electrolytic manganese residue by