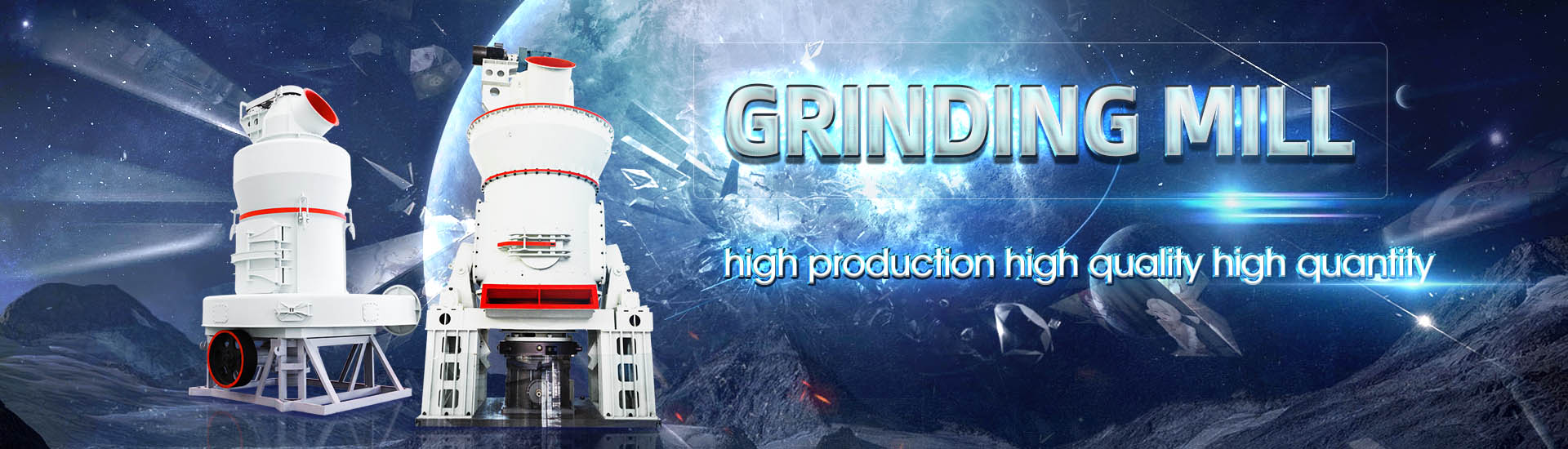
Suspended roller coal raw coal mill
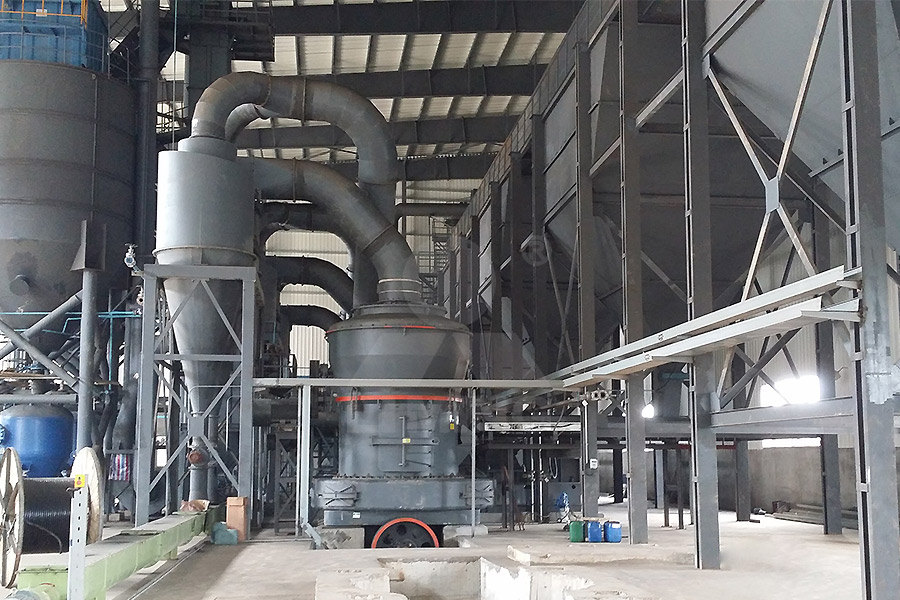
A unified thermomechanical model for coal mill operation
2015年11月1日 Coal mills are bottleneck in coal–fired power generation process due to difficulty in developing efficient controls and faults occurring inside the mills In this paper, a dynamic Raw coal is transported on a conveyor belt and dropped into the mill through the chute The coal falls into the grinding table rotating at a constant speed The coal then moves under centrifugal Modeling and Control of Coal MillMills are mechanical devices used to break different types of solid materials in small pieces by grinding, crushing or cutting In pulverised coalfired power plants, a pulveriser coal mill grinds Coal Mill an overview ScienceDirect Topics2021年8月1日 The working process of coal mill is as follows: raw coal is transported by the coal feeder and dropped into the grinding plate; three grinding rollers crush the raw coal from the Coal mill model considering heat transfer effect on mass

COAL GRINDING IMPS: more than meets the eye Gebr Pfeiffer
Vertical roller mills are not only used for grinding cement raw materials but also find an application in grinding a wide variety of coal types in cement and power plants Gebr Pfeiffer SE (GPSE) Find out all of the information about the Xinxiang Great Wall Machinery Co, Ltd product: roller mill GMRC Series coal mill Contact a supplier or the parent company directly to get a quote or to find out a price or your closest point of saleRoller mill GMRC Series coal mill DirectIndustryCoal mills are used to pulverize the raw coal and conveyor the fine coal particles to primary zone of boiler for an eficient combustion Performance of the pulverizing system hasAn investigation of performance characteristics and energetic A coal mill is an important component of a steam power plant which grinds precrushed raw coal particles of size 1020 mm to fine particles of size less than 150 µm using heated primary air Mathematical validation and comparison of ball tube and bowl
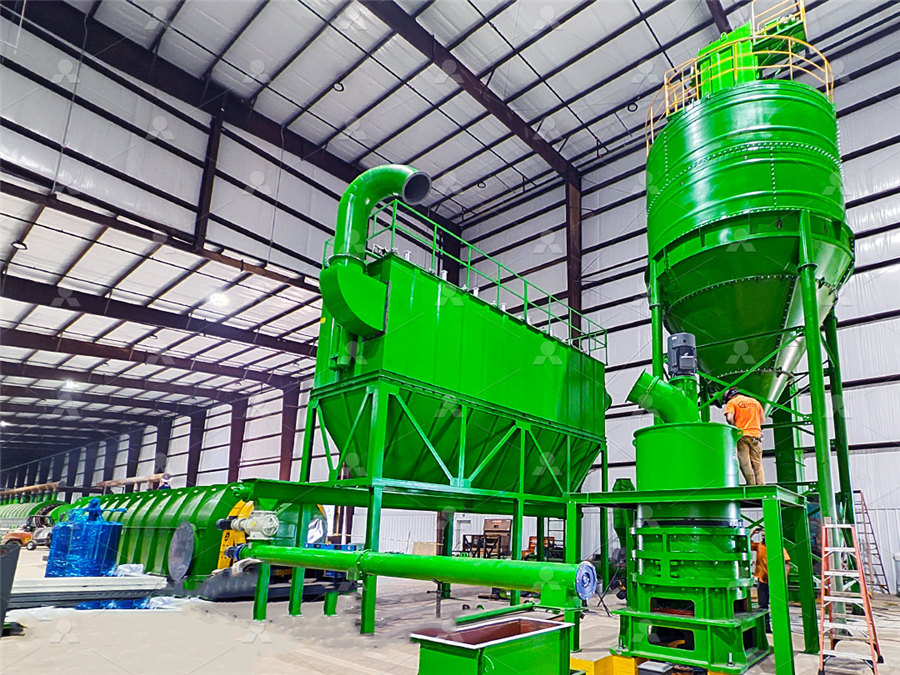
An investigation of performance characteristics and energetic
2020年8月12日 This study shows the performance of a currently running vertical roller coal mill (VRM) in an existing coalfired power plant In a power plant, the coal mill is the critical The Loesche coal grinding mill range is divided into two serial types: Small twin mills constructed to individual specifications (LM 122 D to LM 202 D), with table diameters from 1,200 to 2,000 LOESCHEMILLSDownload Citation On Nov 1, 2024, Hailiang Hu and others published Numerical Study of Flow Field and Particle Motion Characteristics on Raw Coal Vertical Roller Mill Circuits Find, read and Numerical Study of Flow Field and Particle Motion Characteristics Coal vertical mills also called coal mills, which are specialized in superfine grinding of raw coal and bituminous coal materials in cement plant, power plants, steel mills and other fields Capacity :570 t/h fineness :80 mu;mR 3% Power Roller mill GMRC Series coal mill Xinxiang Great
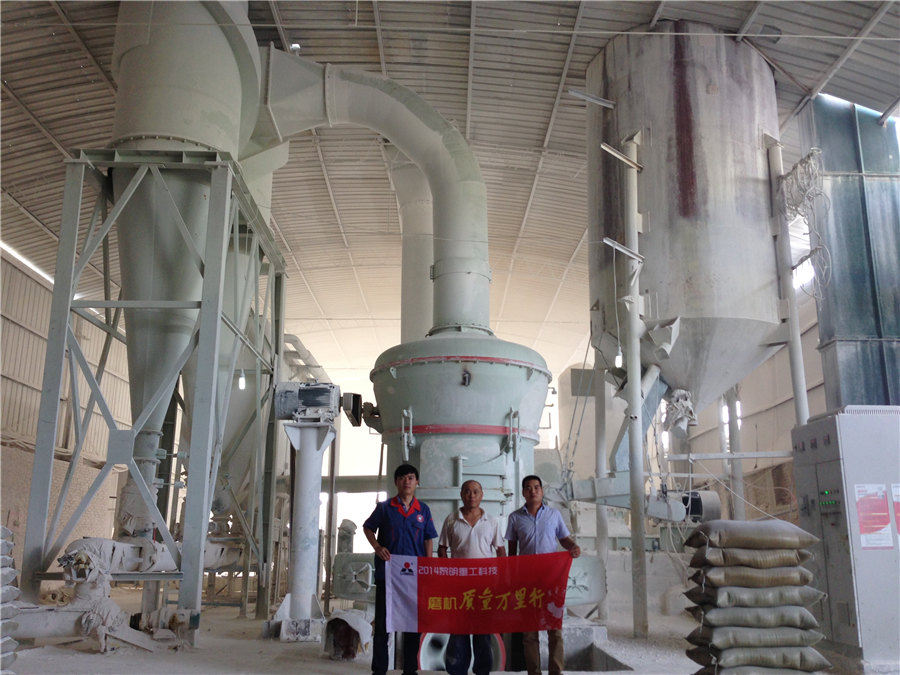
Optimization of the pulverized system of the coalfired power
effectively represent the midhigh process of coal mill dynamics and estimate the key parameters in coal mills Grudziak et al [ 7] monitored the temperature of a dust–air mixture at the outlet of a coal mill an using additive regression model and data mining techniques, thereby improving the usability of the statistical modeling Hu et al 2014年1月1日 Two mill systems are employed for most coal grinding applications in the cement industry These are, on the one hand, vertical roller mills (VRM) that have achieved a share of almost 90% and, on (PDF) MPS mills for coal grinding ResearchGateet al 2017) In a coalfired power plant, one of the main equipment is the coal mill, whose effectiveness influences mainly the whole power plant performance (Shah, Vuthaluru, andAn investigation of performance characteristics and energetic Whether grinding raw coal, clinker, cement and/or slag, we have a VRM solution to suit your grinding needs What’s more, our online condition monitoring services enable you to adopt a proactive maintenance strategy for your OK™ and ATOX® mills that eliminates unexpected downtime and ensures continuous high performanceVertical roller mills FLSmidth Cement
.jpg)
An investigation of performance characteristics and energetic
2020年8月12日 To understand the performance of a vertical roller coal mill, the real operational tests have been performed considering three different coal sources Obtained results indicate that grinding pressure, primary air (PA) temperature and mill motor current have a tendency to rise by increasing coal feeding mass flow rates for all used coalA compact coal mill solution for grinding virtually any type of raw coal Our ATOX® Coal Mill is a compact vertical roller mill that can grind almost any type of raw coal The coal mill utilises compression and shear force generated between the large rollers and the rotating table to crush and grind raw coal, removing the need for a separate Roller mill ATOX® COAL FLSmidth DorrOliver EimcoThe dried coal powder is then transported to the combustion chamber where it is burned to generate heat The process of generating heat from raw coal is similar to that of pulverizer coal mills How Does a Raw Coal Mill Work? Raw coal is fed into the mill through the raw coal feeder The raw coal is then crushed between the roller and the ringHow does a Coal Mill Work? ball mills supplierCoal Inlet coal is fed to the centre of the grinding table Coal fed to the mill may be raw or pretreated Pulverized Coal Outlet/Discharge pulverized coal flows out of an outlet duct How Vertical Grinding Mills Work The below video is an extract from our Mechanical and Electrical Engineering Explained Online Video CourseVertical Grinding Mill (Coal Pulverizer) Explained saVRee
.jpg)
Coal mill pulverizer in thermal power plants PPT
2012年11月17日 20 131Fineness Fineness is an indicator of the quality of the pulverizer action Specifically, fineness is a measurement of the percentage of a coal sample that passes through a set of test sieves usually designated at 50, Process introduction Vertical coal mill, also known as vertical roller coal mill or vertical coal grinding mill, is a mechanical equipment for crushing and grinding coal into coal powerMainly used for grinding raw coal, bituminous coal, and other fuels into coal powder, which is supplied to rotary kiln and other kilns in the cement plant and thermal power plantcoal grinding machine CHAENGA vertical roller mill is an energysaving mill that meets market demand It has a low operating cost and highcost performance Home; Equipment All Equipment; The raw coal moisture Pulverized coal moisture Main motor power(kW) Energysaving and Efficient Vertical Roller Mill Fote 2009年9月20日 A control oriented model was then developed by Fan (1994) and Fan and Rees (1994) In 2009, coal flow and outlet temperature of mill were modelled using mass and heat balance equations for startup Modeling and Parameter Identification of Coal Mill

A Comparison of Three Types of Coal Pulverizers Babcock Power
Vertical Roller Mill The vertical roller mill (VRM) shown in Figure 4 is an air swept, mediumspeed, vertical pulverizer with integral classifier It pulverizes coal by applying hydraulicallyloaded grinding pressure through three grin ding rollers onto a rotating bed of coal Grinding pressure can be adjusted to account for variations in coalDownload scientific diagram The layout of the coal mill with a rotary classifier from publication: An investigation of performance characteristics and energetic efficiency of vertical roller The layout of the coal mill with a rotary classifierVertical roller mills are not only used for grinding cement raw materials but also find an application in grinding a wide variety of coal types in cement and power plants Gebr Pfeiffer SE (GPSE) describes its vertical roller mills for coal grinding and provides a case study of an MPS225BK installed at CBR’s Lixhe cement works in BelgiumCOAL GRINDING IMPS: more than meets the eye Gebr PfeifferVertical coal grinding mill integrates crushing, drying, grinding, powder selection and conveying; It has simple system and compact structure Vertical coal mill covers an floor area about 50% of the coal ball mill with the same specification; Coal vertical mills can work in openair environments, greatly reducing the cost of investment The design of the vertical coal mill system is simple Vertical Coal Mill ball mills supplier
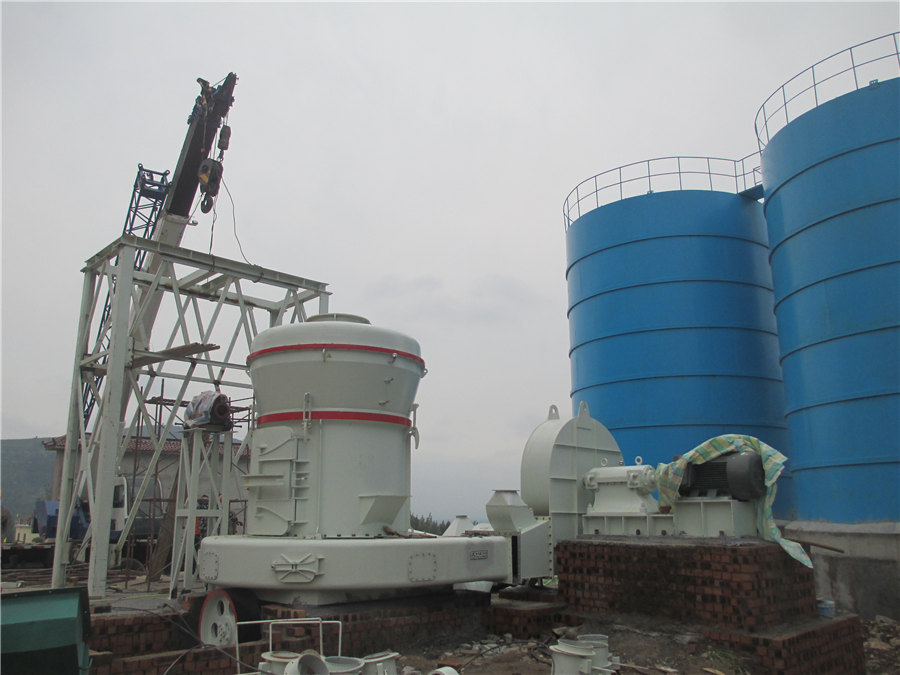
Modeling of Coal Mill System Used for Fault Simulation
2020年4月7日 Because the amount of raw coal and coal powder stored in the mill c annot be measured, there is no a ctual reference data in the model identification process So, t he dynamic characteristic of rawOur grinding roller coal mill has a simple process, compact equipment, low dust emission, and efficient combustion of coal powder Working Principle During operation, the main motor drives the grinding disc through a reducer Hot air enters the vertical mill through the inlet, while the raw coal is fed evenly into the center of the grinding HighEfficiency Vertical Coal Mill Enhancing Coal Pulverizationvertical roller grinding mills for grinding: • Coal • Cement raw material • Clinker / granulated slag • Industrial minerals, and • Ores The core elements of these plants are the Loesche vertical mills for drygrinding the abovementioned grinding stock Loesche has PROCESS OPTIMISATION FOR LOESCHE GRINDING PLANTSDownload scientific diagram Technical specifications of vertical roller coal mill from publication: An investigation of performance characteristics and energetic efficiency of vertical roller Technical specifications of vertical roller coal mill
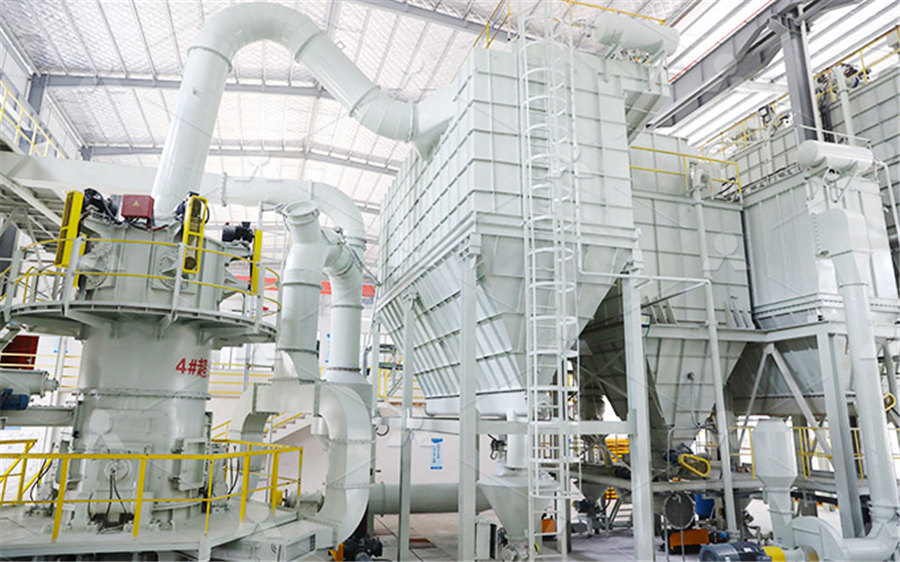
Accept the probability that the fire and explosion safety of your coal
51) the mill, vertical roller mill (VRM) or horizontal ball mill (HBM) where it goes wrong (210) Coal mills have to have explosion pressure shock resistance (EPSR) The USAmerican code NFPA 85 demands a strength ‘good for’ 50 psi g That is roughly 344 bar g The reason for demandingSafe operation of coal grinding systems: Raw coal silo protection against fire and explosions Safe operation of coal grinding systems: Raw coal yard management The purchasing process for coal grinding systems needs changes Talk at a virtual seminar, November 2023 Accept the probability that the fire and explosion safety of your coal grinding system is nothing more than a mirageOptimisation of coal mill systems, with fire and explosion Coal mill is an important component of the thermal power pla nt It is used to grind and dry the moisturized raw coal and transport the pulverized coal ± air mixture to the boiler Poor dynamic performance of coal mill will lead to decrease in the overall efficiency of the power plant, slow load take up rate and fr equent shut downModeling and Control of Coal Mill(5) The ambient temperature (temperature of raw coal entering the mill) , coal moisture and latent heat of vaporisation are known constants 797 IFAC DYCOPS 2013 December 1820, 2013 Mumbai, India The pressure drop, across the mill depends on the and the mill differential pressure of the primary air, amount of coal suspended in the air(PDF) Modeling and Control of Coal Mill Academia
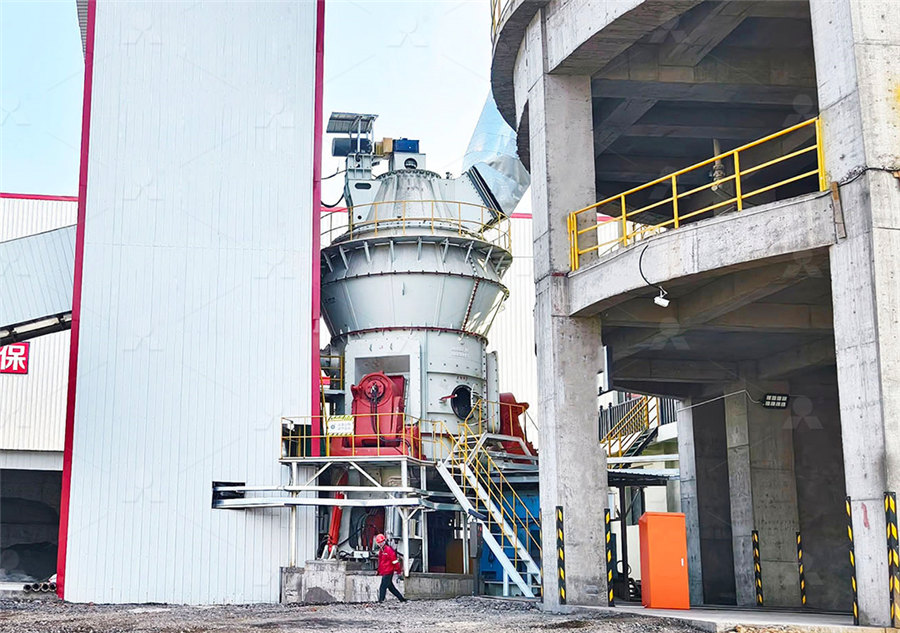
Derivation and validation of a coal mill model for control
The control problems arise from the lack of good sensors for measuring the output of pulverized fuel from each mill The input mass flow of the raw coal to the mill is difficult to measure as well; typically, the conveyor belt speed is used for this purpose Additionally the n Corresponding author Tel: þ45 9940 7527; fax: þ 45 9815 1739Coal mill hot air inlet temperatures should never be more than 600 ° F and the outlet temperature should not exceed 200°F on Raymond coal mills If the flow of raw coal to the coal mill is interrupted for any reason (for example: plugging, failure of the coal feeder, etc), the outlet temperature of the coal mill can quickly climb to coal feeders and coal mill Capabuild2020年4月2日 process the raw coal to becom e as pul verise fuel before enter to the boiler furnace as mill roller, grin der and mill motor was design to suit with the end productAnalysis of the Coal Milling Operations to the Boiler ParametersThe plant is equipped with seven gravimetric raw coal feeders and seven HP 1103 pulverisers with dynamic classifiers The gearboxes that run these coal mills are lubricated with extra highperformance gear oils having outstanding extreme pressure characteristics and loadcarrying properties Mobilgear 600 XP320 high viscosity oilUltraSupercritical Coal Fired Power Plant Coal Mill Pulverizer
.jpg)
Numerical Study of Flow Field and Particle Motion Characteristics
Download Citation On Nov 1, 2024, Hailiang Hu and others published Numerical Study of Flow Field and Particle Motion Characteristics on Raw Coal Vertical Roller Mill Circuits Find, read and Coal vertical mills also called coal mills, which are specialized in superfine grinding of raw coal and bituminous coal materials in cement plant, power plants, steel mills and other fields Capacity :570 t/h fineness :80 mu;mR 3% Power Roller mill GMRC Series coal mill Xinxiang Great effectively represent the midhigh process of coal mill dynamics and estimate the key parameters in coal mills Grudziak et al [ 7] monitored the temperature of a dust–air mixture at the outlet of a coal mill an using additive regression model and data mining techniques, thereby improving the usability of the statistical modeling Hu et al Optimization of the pulverized system of the coalfired power 2014年1月1日 Two mill systems are employed for most coal grinding applications in the cement industry These are, on the one hand, vertical roller mills (VRM) that have achieved a share of almost 90% and, on (PDF) MPS mills for coal grinding ResearchGate
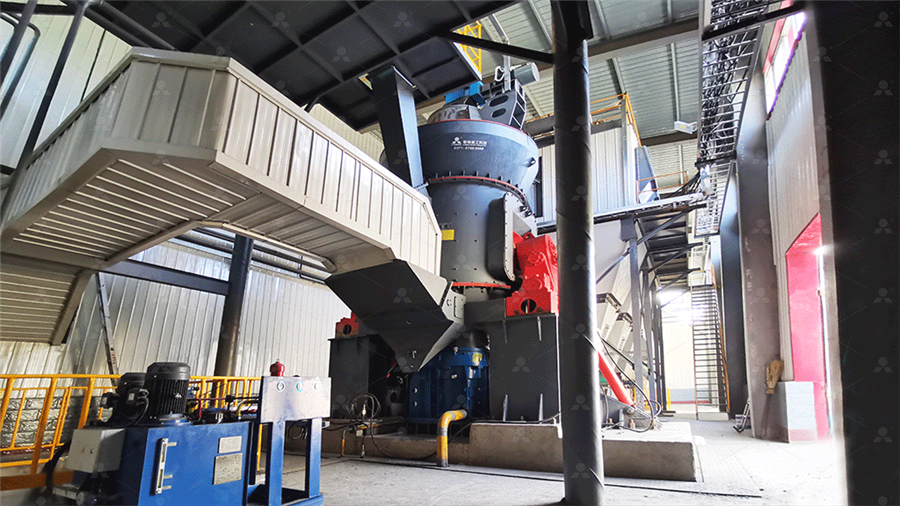
An investigation of performance characteristics and energetic
et al 2017) In a coalfired power plant, one of the main equipment is the coal mill, whose effectiveness influences mainly the whole power plant performance (Shah, Vuthaluru, andWhether grinding raw coal, clinker, cement and/or slag, we have a VRM solution to suit your grinding needs What’s more, our online condition monitoring services enable you to adopt a proactive maintenance strategy for your OK™ and ATOX® mills that eliminates unexpected downtime and ensures continuous high performanceVertical roller mills FLSmidth Cement2020年8月12日 To understand the performance of a vertical roller coal mill, the real operational tests have been performed considering three different coal sources Obtained results indicate that grinding pressure, primary air (PA) temperature and mill motor current have a tendency to rise by increasing coal feeding mass flow rates for all used coalAn investigation of performance characteristics and energetic A compact coal mill solution for grinding virtually any type of raw coal Our ATOX® Coal Mill is a compact vertical roller mill that can grind almost any type of raw coal The coal mill utilises compression and shear force generated between the large rollers and the rotating table to crush and grind raw coal, removing the need for a separate Roller mill ATOX® COAL FLSmidth DorrOliver Eimco
.jpg)
How does a Coal Mill Work? ball mills supplier
The dried coal powder is then transported to the combustion chamber where it is burned to generate heat The process of generating heat from raw coal is similar to that of pulverizer coal mills How Does a Raw Coal Mill Work? Raw coal is fed into the mill through the raw coal feeder The raw coal is then crushed between the roller and the ringCoal Inlet coal is fed to the centre of the grinding table Coal fed to the mill may be raw or pretreated Pulverized Coal Outlet/Discharge pulverized coal flows out of an outlet duct How Vertical Grinding Mills Work The below video is an extract from our Mechanical and Electrical Engineering Explained Online Video CourseVertical Grinding Mill (Coal Pulverizer) Explained saVRee