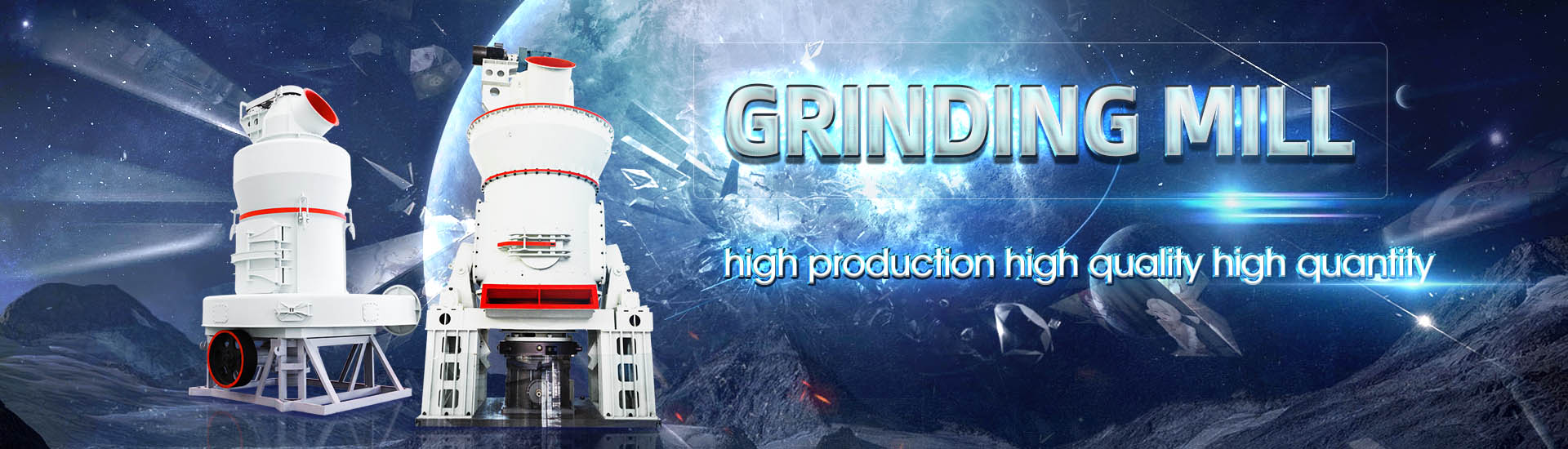
HOME→Cement grinding station production process Cement grinding station production process Cement grinding station production process
Cement grinding station production process Cement grinding station production process Cement grinding station production process
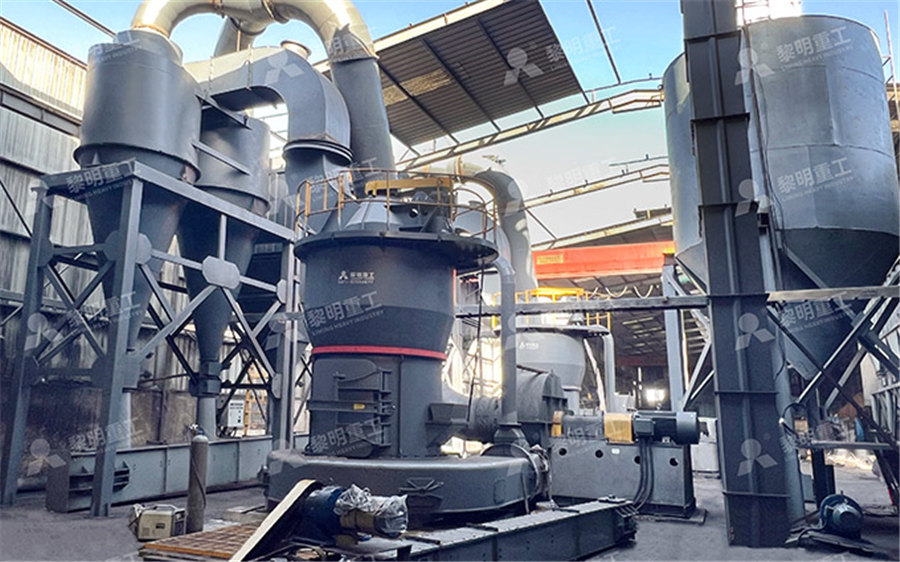
Cement Grinding Plant CHAENG
Cement clinker grinding unit, or called cement grinding plant, cement grinding station, is an individual grinding plant in the finished cement production Cement grinding plants are primarily used to produce finished cement products by Explore Amrit Cement's stateoftheart cement grinding unit Learn about our cement grinding process and plant stages for high quality cementCement Grinding Unit Process High Quality Cement The three broad processes of cement manufacturing are: Raw milling — the preparation of the kiln feed Calcining and burning or clinkering — the conversion process that takes place within The Cement Production ProcessWe master the construction and design schemes of various cement grinding plant systems such as vertical mill system, combined system, and ball mill system No matter what type and strength of cement you want to produce, and what Cement Grinding Plant Expert Cement Grinding
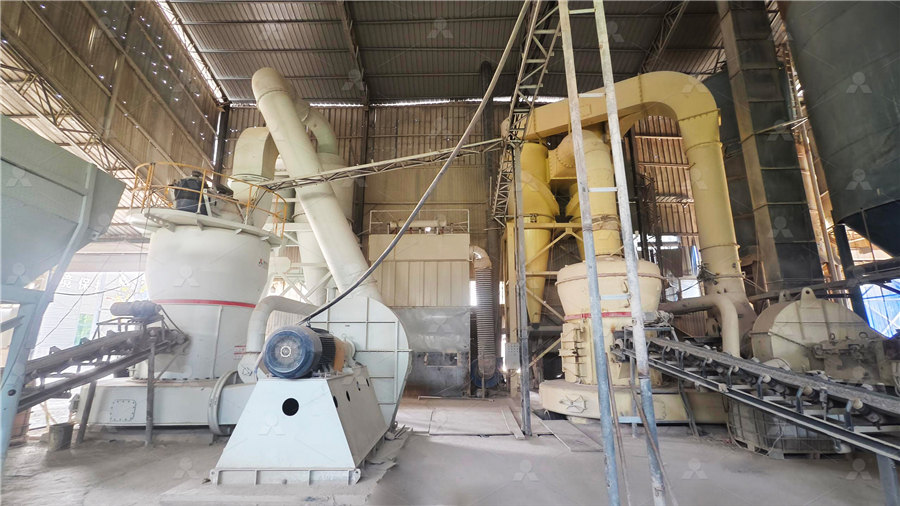
Cement Grinding Plant Overview Cement Grinding
The cement grinding plant is an industry with green benefits What is the equipment needed for the cement grinding plant? And what is the specific work process? As a cement grinding plant manufacturer, AGICO Cement can Highly energy intensive unit operation of size reduction in cement industry is intended to provide a homogeneous and super fine (30004000 Blain) cement Grinding operation is monitored for Cement Grinding Cement Plant OptimizationThe new cement grinding process includes mixed material crushing, cement batching station, pregrinding, high fine grinding, fine powder separation, dust treatment, automatic control and other technologies, so that cement high yield, Cement Grinding Station Solution Ball Mill and 2017年5月19日 PDF Grinding is an essential operation in cement production given that it permits to obtain fine powder which reacts quickly with water, sets in few Find, read and cite all theOverview of cement grinding: fundamentals, additives,
.jpg)
How Is Cement Produced in Cement Plants Cement
Nowadays, the dry process is the most popular cement making process which is widely adopted by cement plants all over the world for its great advantages in energy saving and environmental protection Cement Making Process The With a strong RD team, experienced engineers, and firstclass technical services, we aim to provide users with the most advanced and optimized cement production solutions The main task of the cement grinding plant is to grind the Cement Grinding Plant Expert Cement Grinding Purpose of Grinding in Cement Manufacturing The main goal of grinding in cement manufacturing is to produce a fine powder that will form the basis of the final product Grinding ensures that the raw materials are adequately prepared for the subsequent stages of the cement production process, including blending, heating, and packagingGrinding in Cement Manufacturing: Key Process, Types of Mills, 2023年8月21日 Tushar Khandhadia, General Manager – Production, Udaipur Cement Works, discusses the role of grinding in ensuring optimised cement production and a high quality end product How does the grinding process contribute to the production of highquality cement?The quality of cement depends on its reactive properties and particle size grinding helps to reduce Grinding process is a critical stage in cement production
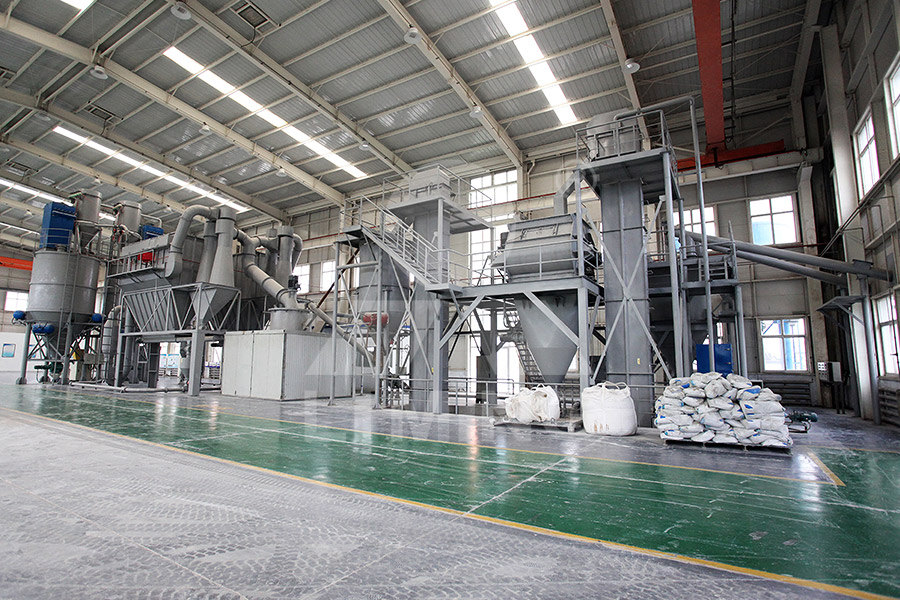
6 Cement Equipment For Dryprocess Cement Production Line
2023年12月26日 As we all know, the dryprocess cement production line is commonly used in the cement industry The new type of dryprocess cement production process includes four main sections: Prehomogenization of raw materials, homogenization of raw materials, clinker firing, cement grinding, etc Raw material conveying system The raw material, including limestone, The Cement Production Process Finish milling — the grinding of clinker to produce cement Rapidsetting cements have smaller particle size than the less reactive low heat of hydration cements Cement is more reactive than clinker and can absorb moisture from the environment leading to some degree of prehydrationThe Cement Production Process2022年8月15日 Cement Grinding Technology in Cement Production Process English VersionIn this session I will explain about Cement Grinding Technology for cement productioCement Grinding Technology In Cement Production Process 2015年8月1日 The results show that approximately 248t, 469t, and 341t of materials are required to produce a ton of the product in raw material preparation, clinker production, and cement grinding stages Analysis of material flow and consumption in cement production process
.jpg)
Cement Manufacturing Process The Engineering Community
2018年8月28日 CEMENT MANUFACTURING PROCESS PHASES Production of cement completes after passing of raw materials from the following six phases These are; Raw material extraction/ Quarry; Grinding, Proportioning and Blending; Preheater Phase; Kiln Phase; Cooling and Final Grinding; Packing Shipping; CEMENT MANUFACTURING PROCESS PHASE 1: Description The cement grinding station with an annual output of 1 million tons adopts the technology of separately grinding clinker and slag, among which the clinker grinding adopts the combined grinding process composed of two Φ 42m × 13m cement mills The production process of the grinding station is stable, achieving the goal of high Cement Production Line,Cement Machine,Rotary Kiln,Cement 2015年10月23日 1 Introduction Cement is an energyintensive industry in which the grinding circuits use more than 60 % of the total electrical energy consumed and account for most of the manufacturing cost []The requirements EnergyEfficient Technologies in Cement Grinding2014年6月10日 Evolution of the cement Process • Wet process easiest to control chemistry better for moist raw materials • Wet process high fuel requirements fuel needed to evaporate 30+% slurry water • Dry process Cement manufacturing process PPT Free Download
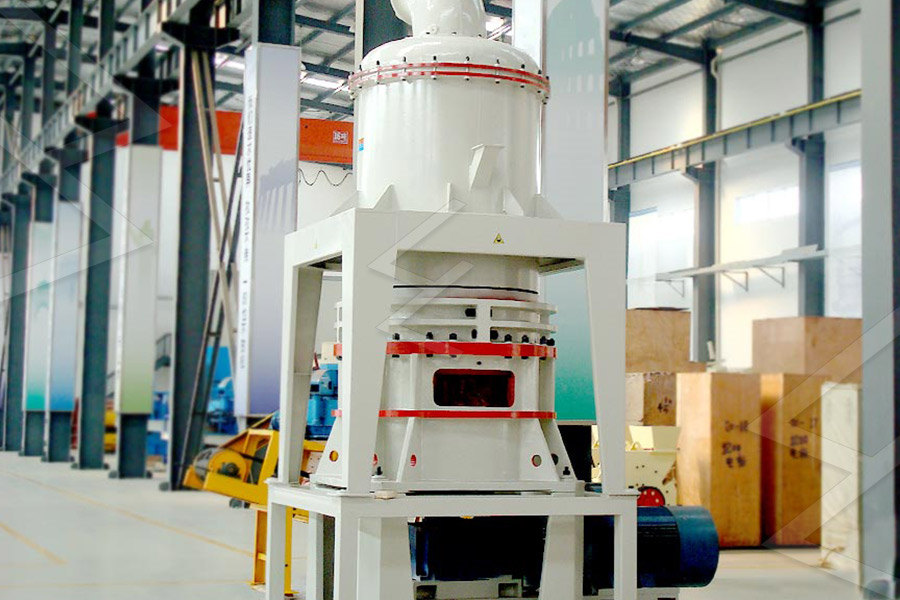
Manufacturing of Portland Cement – Process and
5 天之前 The manufacture of Portland cement is a complex process and done in the following steps: grinding the raw materials, mixing them in certain proportions depending upon their purity and composition, and burning them to sintering in The final manufacturing stage at a cement plant is the grinding of cement clinker from the kiln, mixed with 45% gypsum and possible additives, into the final product, cement In a modern cement plant the total consumption of electrical energy is about 100 kWh/t The cement grinding process accounts for approx 40% if this energy consumptionCEMENT GRINDING SYSTEMS INFINITY FOR CEMENT EQUIPMENT2019年1月3日 Clinker grinding technology is the most energyintensive process in cement manufacturing Traditionally, it was treated as "low on technology" and "high on energy" as grinding circuits use more than 60 per cent of total energy consumed and account for most of the manufacturing cost Since the increasing energy cost started burning the benefits significantly, Clinker grinding technology in cement manufacturingThe use of fossil fuels such as coal, natural gas, and oil is common in cement production, both as a fuel for the kiln and as a source of heat for other parts of the process which leads to CO2 emitted by combustionHowever chemical reactions happening in the kiln (calcination) are also responsible for up to 60% of the total of emissions of the cement production process [PCA]Cement Production Demystified: StepbyStep Process and
.jpg)
Modular Grinding Plant AGICO Cement Machinery
There are two types of mills commonly used in the modular mobile grinding station: ball mill and vertical roller mill (VRM) We will select the appropriate mill module according to the specific needs of customers The mill is the core component of a grinding plant All other equipment in the grinding station serves the purpose of grinding2017年5月19日 Grinding is an essential operation in cement production given that it permits to obtain fine powder which reacts quickly with water, sets in few hours and hardens over a period of weeks i Overview of cement grinding: fundamentals, additives, technologiesEffect of grinding aid on product quality Depends according to the grinding aid and cements concerned; Flowability is improved à improvements or problems for transport and packing; May help reduce the water requirement by acting as plasticisers The reduction in water demand consequently leads to a higher compressive strengthEverything you need to know about clinker/cement Grinding2024年1月17日 According to statistics, the dry cement production line grinding operation consumes Power accounts for more than 60% of the power of the whole plant, of which raw material grinding accounts for more than 30%, coal grinding accounts for about 3%, and cement grinding station account for about 40%What Do You Know About Wet Process Of Cement Production
.jpg)
Cement Manufacturing Process: Know Extraction,
2024年9月10日 Longer Production Time: The wet process generally takes longer for Cement production compared to the dry process, as it involves additional steps such as slurry formation and drying Conclusion This marks 2023年10月19日 Clinker is a critical component in the production of cement and forms the intermediate product during the cement manufacturing process It can be best described as a nodular material, usually grayish in color, which is Understanding the Role of Clinker Grinding in Cement 2024年11月23日 Cement Extraction, Processing, Manufacturing: Raw materials employed in the manufacture of cement are extracted by quarrying in the case of hard rocks such as limestones, slates, and some shales, with the Cement Extraction, Processing, ManufacturingThe cement production process 1 The Quarry: The cement production process begins with the extraction of limestone and clay from the quarry 2 Crusher and PreBlending: The material is then crushed to reduce particle sizes and blended to reduce variability in composition 3 Raw Mill and Kiln: Raw materials and additives areA practical guide to improving cement manufacturing processes

Resistance to Grinding and Cement Paste Performance of Blends
2021年4月19日 Grinding of finished cement is performed in a single stage, intergrinding materials with very different grindabilities This intergrinding process has many different interactions among the different components of the finished cement In a context of developing more sustainable and less energy intensive processes, it is important to understand the 2023年7月10日 Cement manufacturing is a significant industrial activity that plays a vital role in the construction sector However, the process of cement production is associated with various environmental Cement Manufacturing Process and Its Environmental ImpactThe dry process cement production line is widely used in cement industry it is generally divided into the following processes: prehomogenization of raw materials, homogenization of raw materials, clinker firing, cement grinding, and so on Get A free quote! Skip to Clinker will be sent to the cement grinding station for further Dry Process Of Cement Production 3005000TPD AGICO CEMENTA 10 MW cement mill, output 270 tonnes per hour A cement mill (or finish mill in North American usage [1]) is the equipment used to grind the hard, nodular clinker from the cement kiln into the fine grey powder that is cementMost cement is currently ground in ball mills and also vertical roller mills which are more effective than ball millsCement mill Wikipedia
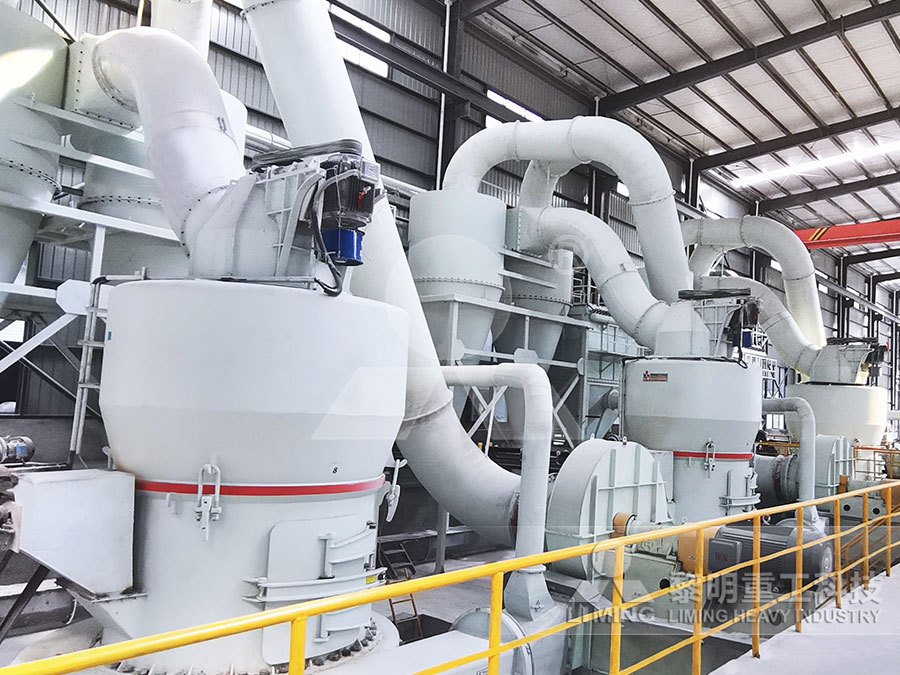
Mining Activities, Cement Production Process and Quality Control
2022年7月4日 grade cement product graded at 425R, responsible for cement production while the rest are subordinates is passed into the grinding unit to assist the drying and grinding processThe cement manufacturing process starts from the mining of raw materials that are used in cement manufacturing, mainly limestone and clays A limestone quarry is inside the plant area and a clays quarry is as far from the plant area as 25 kmManufacturing process LafargeNowadays, the dry process is the most popular cement making process which is widely adopted by cement plants all over the world for its great advantages in energy saving and environmental protection Cement Making Process The How Is Cement Produced in Cement Plants Cement With a strong RD team, experienced engineers, and firstclass technical services, we aim to provide users with the most advanced and optimized cement production solutions The main task of the cement grinding plant is to grind the Cement Grinding Plant Expert Cement Grinding
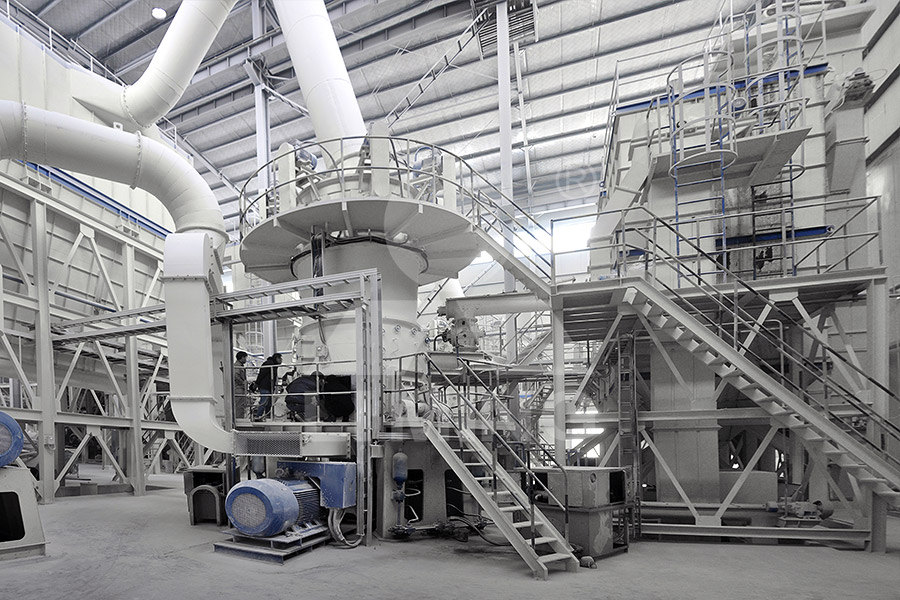
Grinding in Cement Manufacturing: Key Process, Types of Mills,
Purpose of Grinding in Cement Manufacturing The main goal of grinding in cement manufacturing is to produce a fine powder that will form the basis of the final product Grinding ensures that the raw materials are adequately prepared for the subsequent stages of the cement production process, including blending, heating, and packaging2023年8月21日 Tushar Khandhadia, General Manager – Production, Udaipur Cement Works, discusses the role of grinding in ensuring optimised cement production and a high quality end product How does the grinding process contribute to the production of highquality cement?The quality of cement depends on its reactive properties and particle size grinding helps to reduce Grinding process is a critical stage in cement production2023年12月26日 As we all know, the dryprocess cement production line is commonly used in the cement industry The new type of dryprocess cement production process includes four main sections: Prehomogenization of raw materials, homogenization of raw materials, clinker firing, cement grinding, etc Raw material conveying system The raw material, including limestone, 6 Cement Equipment For Dryprocess Cement Production LineThe Cement Production Process Finish milling — the grinding of clinker to produce cement Rapidsetting cements have smaller particle size than the less reactive low heat of hydration cements Cement is more reactive than clinker and can absorb moisture from the environment leading to some degree of prehydrationThe Cement Production Process
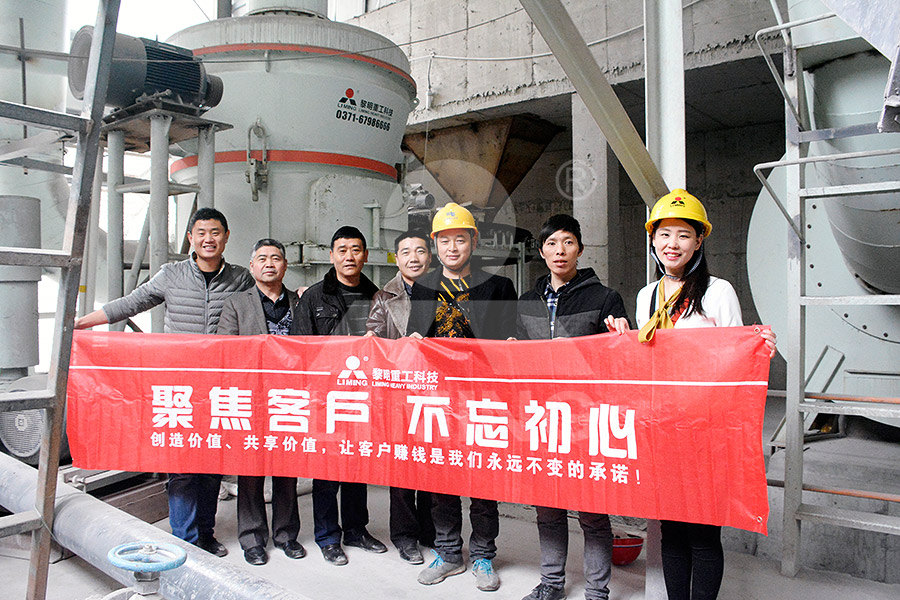
Cement Grinding Technology In Cement Production Process
2022年8月15日 Cement Grinding Technology in Cement Production Process English VersionIn this session I will explain about Cement Grinding Technology for cement productio2015年8月1日 The results show that approximately 248t, 469t, and 341t of materials are required to produce a ton of the product in raw material preparation, clinker production, and cement grinding stages Analysis of material flow and consumption in cement production process2018年8月28日 CEMENT MANUFACTURING PROCESS PHASES Production of cement completes after passing of raw materials from the following six phases These are; Raw material extraction/ Quarry; Grinding, Proportioning and Blending; Preheater Phase; Kiln Phase; Cooling and Final Grinding; Packing Shipping; CEMENT MANUFACTURING PROCESS PHASE 1: Cement Manufacturing Process The Engineering CommunityDescription The cement grinding station with an annual output of 1 million tons adopts the technology of separately grinding clinker and slag, among which the clinker grinding adopts the combined grinding process composed of two Φ 42m × 13m cement mills The production process of the grinding station is stable, achieving the goal of high Cement Production Line,Cement Machine,Rotary Kiln,Cement