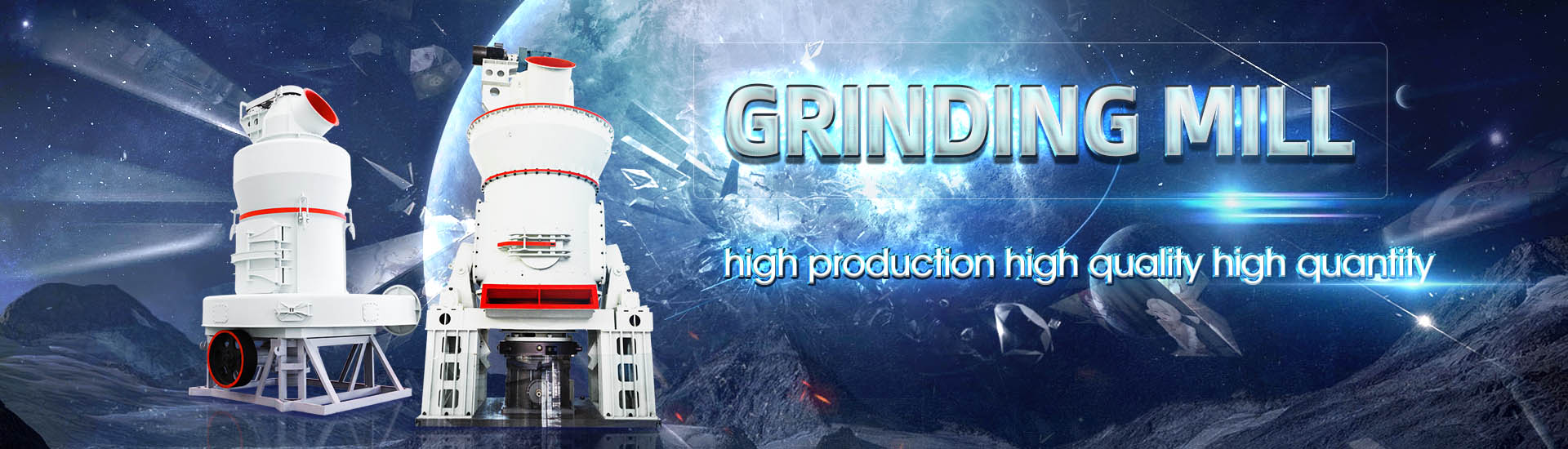
Energy Efficiency Index of Grinding Production Line
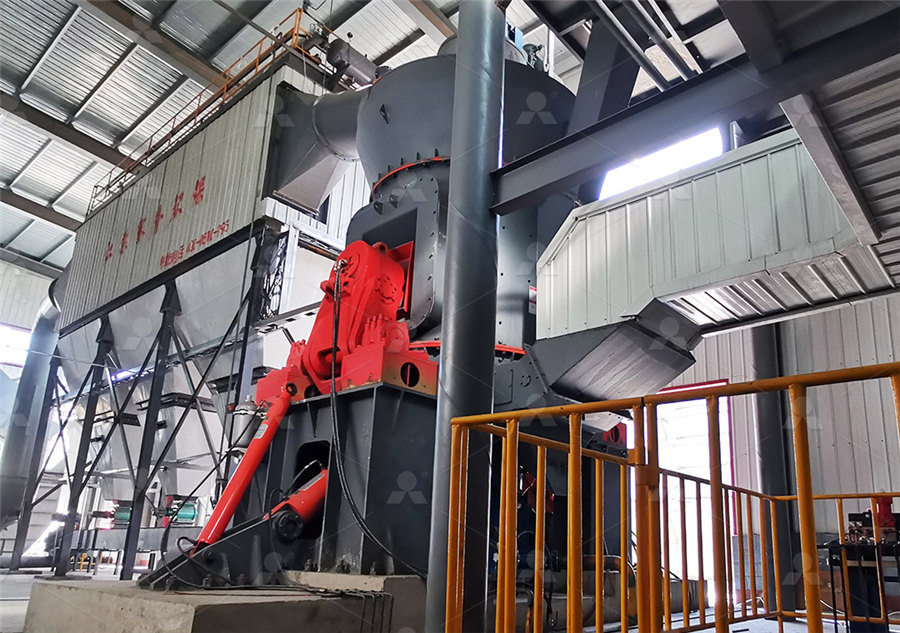
Effect of different parameters on grinding efficiency
2016年11月22日 The grinding zone temperature elevation is dependent on the grinding efficiency and the proportion of grinding energy that enters the workpiece Experimental results (Rowe, Morgan, Black, Mills, Citation 1996 2021年12月10日 The Pareto optimal design method of energy efficiency balancing with product quality and machining time is proposed in this research A nondeterministic adaptive ANN Predictive modelling and Pareto optimization for energy efficient Grinding is a critical surfacefinishing process in the manufacturing industry One of the challenging problems is that the specific grinding energy is greater than in ordinary Energy Prediction Models and Distributed Analysis of the Grinding 2017年7月1日 The grinding process in ball mills is notoriously known to be highly inefficient: only 1 to 2% of the inputted electrical energy serves for creating new surfaces There is therefore Reducing the energy footprint of grinding circuits: the process
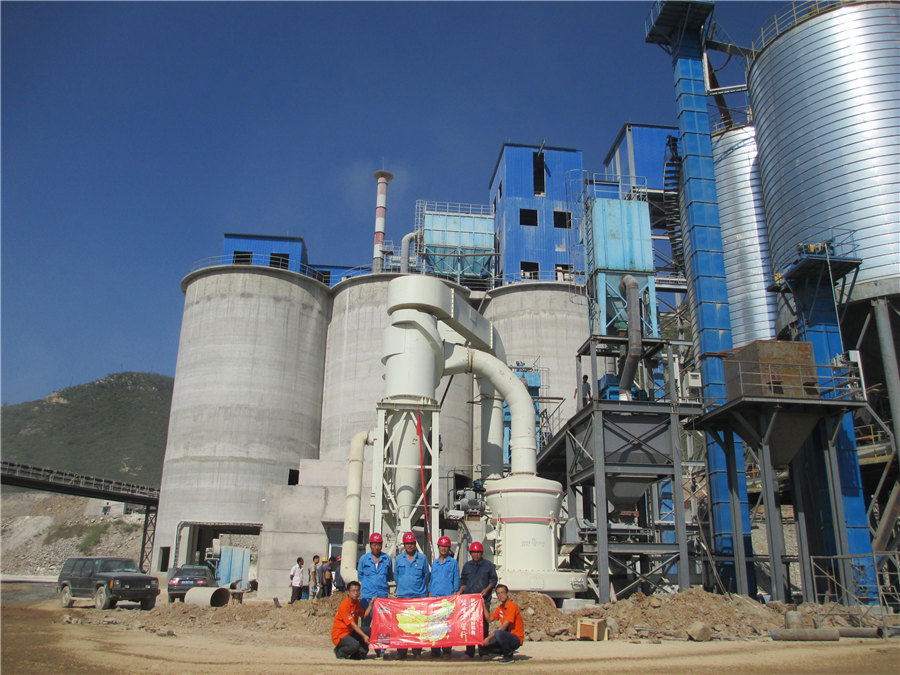
Energy consumption model and energy efficiency
2017年6月15日 Research on the energy efficiency evaluation method of CNC continuous generating grinding machine tools Discussed two methods to evaluation the energy efficiency and highlight the significance of using the 2017年7月14日 Energy efficiency of HSDCCHM and WCCHM are compared and analysed based on energy efficiency models established Through the theory analysis, results show An analytical investigation on energy efficiency of highspeed dry 2021年11月25日 Two of the most popular methods for estimating grinding energy requirements are the Bond operating work index (OWi) and the Morrell specific comminution energy method Both relate the comminution energy to Quantifying the energy efficiency of fine grinding circuits2015年1月1日 The process of grind hardening can potentially increase the energy efficiency of the manufacturing and at the same time reduce the environmental burden The process relies Energy Efficiency and Environmental Impact Implications of Grind

EnergyEfficient Technologies in Cement Grinding
2015年10月23日 In this chapter an introduction of widely applied energyefficient grinding technologies in cement grinding and description of the operating principles of the related equipments and comparisons over each other in 2018年7月1日 In that case, the real data showed that the increase in production rate was 368% and 28Days strength of the cement improved by 29% As a result, the simulation outputs were found to be in agreement with the real data hence the efficiency of the cement production, both quality and energy, for a given circuit was improvedEnergy and cement quality optimization of a cement grinding circuit2023年5月4日 In order to assess the energy efficiency and cutting insert quality after grinding, four lateral faces of square cemented tungsten carbide (WC–5%Co) blanks (Fig 1a), with original dimensions 125 × 125 × 476 mm, were ground in a fouraxes CNC grinding machine Agathon DOM Plus (maximum power of 16 kW and maximum rotation speed of 2400 rpm, Fig 1b) with Energy Efficiency Assessment in PlungeFace Grinding of 2020年3月1日 Manufacturing cement requires energy intensive processes; and consumes almost 15% of the total demand for energy in industry [3]On average, to produce one ton of cement, 34 GJ of thermal energy (in dry process) and 110 kWh of electrical energy are needed [4, 5]Furthermore, manufacturing a ton of cement releases 073–099 tons of CO2 [6] which A decision support tool for cement industry to select energy efficiency
.jpg)
EnergyEfficient Technologies in Cement Grinding IntechOpen
2015年10月23日 In this chapter an introduction of widely applied energyefficient grinding technologies in cement grinding and description of the operating principles of the related equipments and comparisons over each other in terms of grinding efficiency, specific energy consumption, production capacity and cement quality are given A case study performed on a 2021年12月10日 In today's machining production lines, grinding strategies are built for classical economic benefits A considerable amount of electric energy is being wasted due to its low energy efficiency Facing the global energy crisis and environmental pollution, it is essential to develop novel grinding strategies for energy efficient grindingPredictive modelling and Pareto optimization for energy efficient 2012年11月8日 cement production is for material size reduction Increasing the efficiency of particle size reduction could have a large impact on energy consumption in the cement industry Current estimates of grinding power requirements used for equipment sizing are indirect indications often based on industrial experience or scaled up from laboratory testsBreakthrough in Clinker Grinding Massachusetts Institute of 2017年6月15日 Introduction Machine tools are the basic energy consumption devices in manufacturing, whose energy saving cannot be neglected (Liu, Wang, and Liu Citation 2013)The energy yearbook published by the US energy information administration in 2012, showed that machine tools electricity consumption occupied 75% of manufacturing electricity consumption, Energy consumption model and energy efficiency evaluation
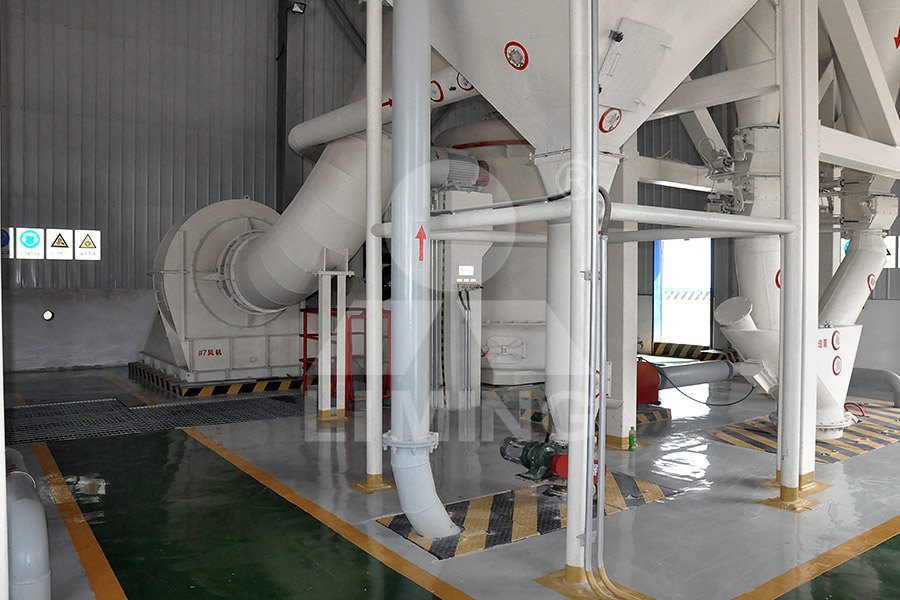
Calculation methods for energy efficiency and energy
With more detailed data on energy consumption available by subsectors or energy uses (eg space heating) or by modes of transport (eg cars), it is possible to assess energy efficiency trends through a more accurate indicator than energy intensity, called “energy efficiency indices”: this is the objective of the second method of calculation presented in this document2021年12月10日 Therefore, facing the enormous energysaving potential and low energy efficiency in grinding production line, (1 − u)] 1 ν + 1, i f u > 05 Where u ∈ [0,1] ν is the distribution index of crossover and mutation algorithms It should Predictive modelling and Pareto optimization for energy efficient Evolution of grinding energy and particle size during dry ballmilling of silica sand Nicolas Blanca, Claire MayerLaiglea, Xavier Franka, Farhang Radjaib, JeanYves Delennea,* aIATE, Univ Montpellier, CIRAD, INRAE, Montpellier SupAgro, Montpellier, France bLMGC, Univ Montpellier, CNRS, Montpellier, France Abstract The energy efficiency of dry fine grinding process of Evolution of grinding energy and particle size during dry ball 2021年9月5日 This experimental work is in line with the Sustainable Responsible Consumption and Production and aims to improve the efficiency of ore grinding and thus reduce energy E, Komnitsas, K Modeling of Bauxite Ore Wet Milling for the Improvement of Process and Energy Efficiency CircEconSust 2, 633 –647 (2022 Modeling of Bauxite Ore Wet Milling for the Improvement of
.jpg)
A New Approach to the Calculation of Bond Work Index with
2024年6月29日 Grinding media influence the energy consumption and efficiency of the grinding process during the calculation of the Bond Work index (BWi), a wellknown method for selecting comminution equipment, evaluating milling efficiency, and calculating required milling power Traditional grinding tests often choose steel balls as the grinding media, but ceramic balls are 2018年3月12日 However, these mills are designed to attain a product size without optimization for energy efficiency For example, the specific energy consumption (SEC) of grinding a sawdust to a median size of 233 µm with a laboratoryscale rotor impact mill was 1844 kWh/kg , which is 46% of the totalEnergy consumption of twostage fine grinding of Douglasfir 2019年12月10日 Energy efficiency represents an important measure for mitigating the environmental impacts of manufacturing processes, and it is the first step towards the implementation of sustainable production (IPCC, 2018)Additionally, from the companies’ points of view, energy efficiency is becoming an important theme in production management due to Energy efficiency of manufacturing systems: A review of energy 2015年1月1日 Salonitis Κ (2012) Efficient grinding processes: an energy efficiency point of view In: Proceedings of the 10th international conference on manufacturing research (ICMR 2012), pp 541–546 Google Scholar Salonitis K (2015) Energy efficiency assessment of grinding strategy Int J Energy Sect Manage 9(1):20–37Energy Efficiency and Environmental Impact Implications of Grind
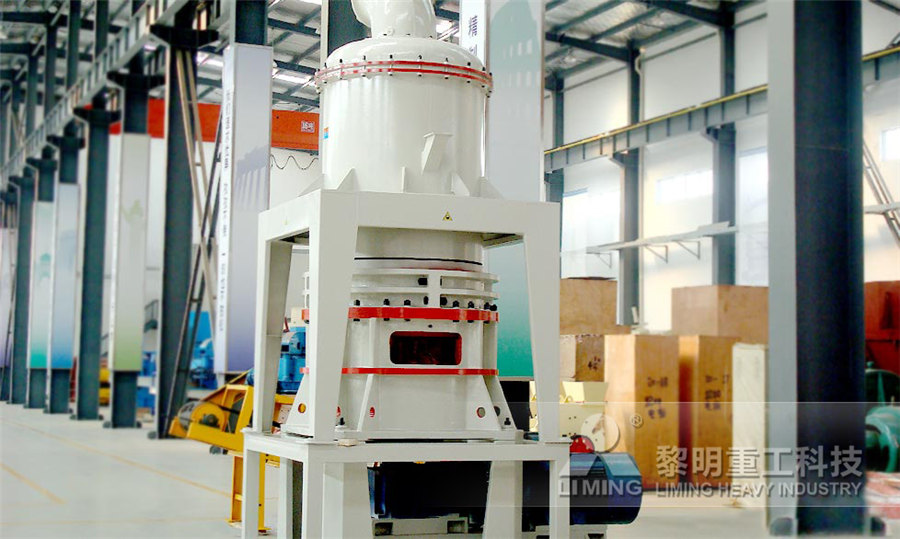
Potential of HighPressure Grinding Roll (HPGR) for Size
2022年3月16日 Abstract HPGR has been found to be efficient size reduction equipment compared to conventional size reduction equipments due to its potential processing benefits in terms of energy savings, improved exposure or liberation and particle weakening The objective of the current work is to study the optimization of different process parameters during grinding 2023年6月15日 The requirements set in MARPOL Annex VI by International Maritime Organization (IMO) have been entered into force on November 1, 2022 Energy Efficiency Existing Ship Index (EEXI) and carbon intensity indicator (CII) calculation and reporting have been mandatory on January 1, 2023 (IMO, 2022)IMO adopted the emission reduction strategy in A scenariobased assessment of the energy efficiency existing 2014年9月1日 The aim of the present work is to understand the reasons for inefficiency and to improve the efficiency of comminution machinery Bond’s Work index coefficients cover almost the entire range of particles to be processed using commercial equipment [4]With this theory, the energy requirements are based on experimental shaft energy measurements of comminution Assessing the energy efficiency of a jaw crusher ScienceDirect2024年1月31日 Additionally, machine breakdowns often pose threats to the safety of workers Consequently, it is crucial to optimise the control of slag grinding systems, whether from a system optimisation control or safety production perspective 6 Researchers such as Johan et al, 7 Kang et al, 8 Umucu et al, 9 Wang K et al, 10 and Lin et al 11 have made significant contributions Intelligent process control system for predicting operating
.jpg)
Towards Sustainable Grinding of DifficulttoCut Alloys—A
2024年3月11日 Grinding, a critical precision machining process for difficulttocut alloys, has undergone continual technological advancements to improve machining efficiency However, the sustainability of this process is gaining heightened attention due to significant challenges associated with the substantial specific grinding energy and the extensive heat generated where λ g is the energy quality coefficient of gas T b u r n g a s is the theoretical combustion temperature of the gas The theoretical combustion temperature of the gas in the gas equipment is generally 1,300°C (1,57315 K), so the An Energy Efficiency Index Formation and Analysis of 2023年1月1日 Sustainable buildings have become a key issue for many developing and developed countries in the twentyfirst century The global population is expected to rise from 77 billion in 2019 to 97 billion in 2050 and will reach more than 109 billion by the end of this century [1]This increase in the global inhabitants will correspondingly increase the demand for water, Energy Efficiency in Sustainable Buildings: A Systematic Review 2023年8月1日 Grinding aids, which, especially in dry grinding, cause a considerable decrease in energy consumption and particle size and an increase in surface area, energy efficiency, prevent the agglomeration or aggregation of ground particles, obstruct grinding media coating and enhance powder fluidity [6, 19, 21, 22, 25, 31, 38]Effective role of grinding aids in the dry grinding performance of
.jpg)
A new approach to assessing the grindability of solids and the energy
1994年11月1日 The performance of grinding mills is evaluated in comparison with the singleparticle breakage mode, which has the highest energy utilization or efficiency of all mechanical grinding routes For a given set of stipulations, the performance index of the commonly used ball mill when grinding dolomite is found to be only 21%, compared to 44% for the highpressure energy consumption forecasting, energy efficiency analysis and energysaving optimisation during the machine tool operation process Introduction Machine tools are the basic energy consumption devices in man ufacturing, whose energy saving cannot be neglected (Liu, Wang, and Liu 2013) The energy yearbook published by the US energyEnergy consumption model and energy efficiency evaluation for 2014年6月5日 European iron and steel producers are working towards increased energy efficiency to meet requirements set by European policies such as the Energy Efficiency Directive In this study, we show that the specific energy consumption (SEC), representing the iron and steel sector in the Odyssee energy efficiency index (ODEX)—the tool for policy evaluation Capturing energy efficiency in European iron and steel production 2021年11月25日 Size Specific Energy (SSE) differs by relating the grinding energy to the quantity of new fines generated For typical circuits that involve AG/SAG, HPGR or ball milling, the generation of 75 µm material (denoted as SSE75) is a suitable marker size with which to benchmark performance because it contains 80% of the surface area generation 1 and energy Quantifying the energy efficiency of fine grinding circuits
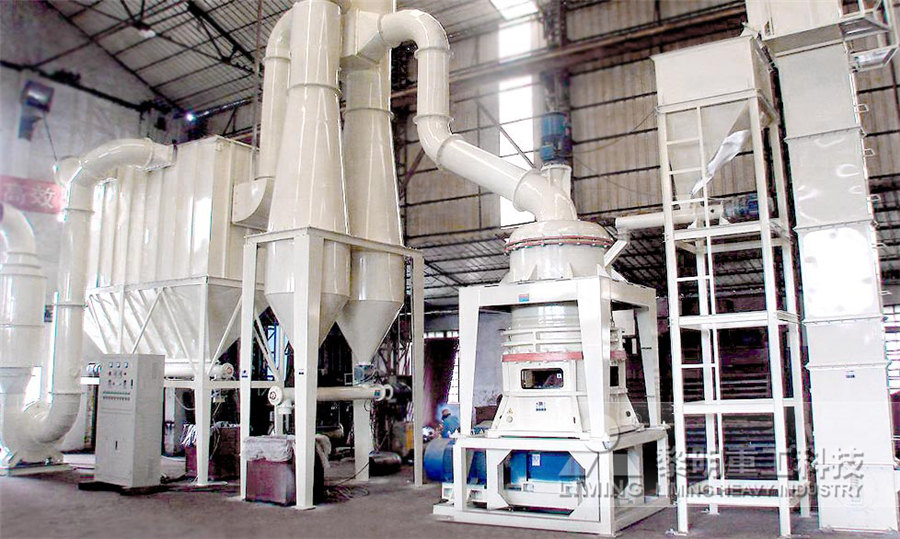
Energy Efficiency of Manufacturing Processes: A Critical Review
2013年1月1日 Energy savings are expected to be achievable from increasing both the energy efficiency of production [8] and the logistic processes, as well as in innovative energy monitoring and management approaches [9], leading industries to a way of producing “more with less†[10] Fig 3 Electricity price in Germany [11]2022年1月1日 A pilotscale grinding technology of ceramic medium stirred mill was proposed in this study Based on the specific productivity and grinding efficiency, the appropriate grinding parameters were ascertained as follows: material ball ratio of 07, ceramic ball medium size ratio (10 mm: 15 mm: 20 mm = 3:2:5), stirring speed of 110 rpm, grinding concentration of 50%, Highefficiency and energyconservation grinding technology using 2021年2月1日 World cement production is about 42 billion tons in 2019 and cement plants consume about 2 percent of world electrical energy in the grinding process [1], [2]The total electrical energy that is consumed in cement companies is about 100 kWh per 1000 kg of cement, and twothird of this amount just consumes in raw material and cement mill units [3]A case study on energy and exergy analyses for an industrialscale 2018年7月1日 In that case, the real data showed that the increase in production rate was 368% and 28Days strength of the cement improved by 29% As a result, the simulation outputs were found to be in agreement with the real data hence the efficiency of the cement production, both quality and energy, for a given circuit was improvedEnergy and cement quality optimization of a cement grinding circuit
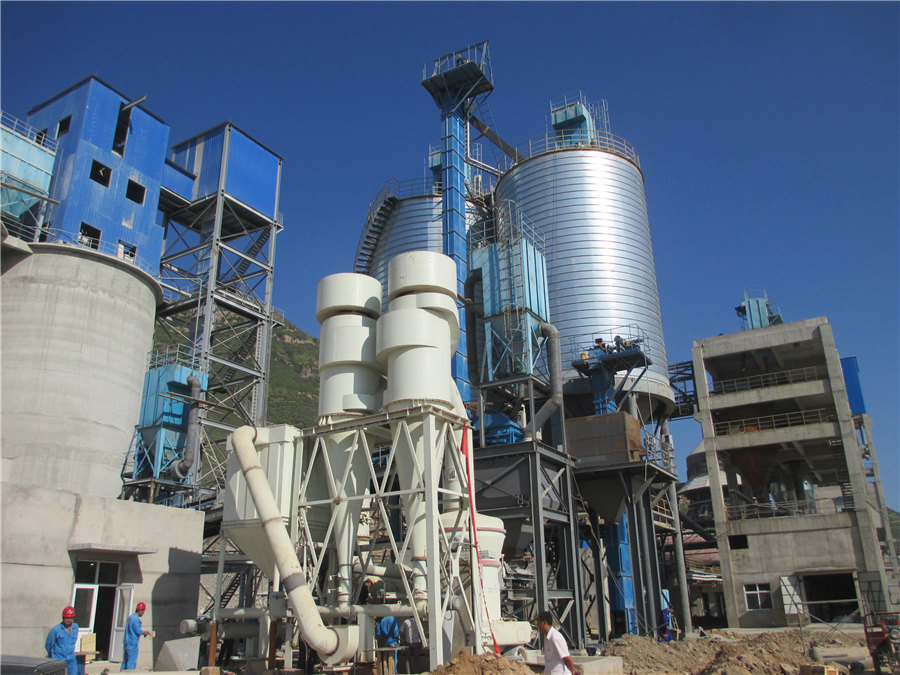
Energy Efficiency Assessment in PlungeFace Grinding of
2023年5月4日 In order to assess the energy efficiency and cutting insert quality after grinding, four lateral faces of square cemented tungsten carbide (WC–5%Co) blanks (Fig 1a), with original dimensions 125 × 125 × 476 mm, were ground in a fouraxes CNC grinding machine Agathon DOM Plus (maximum power of 16 kW and maximum rotation speed of 2400 rpm, Fig 1b) with 2020年3月1日 Manufacturing cement requires energy intensive processes; and consumes almost 15% of the total demand for energy in industry [3]On average, to produce one ton of cement, 34 GJ of thermal energy (in dry process) and 110 kWh of electrical energy are needed [4, 5]Furthermore, manufacturing a ton of cement releases 073–099 tons of CO2 [6] which A decision support tool for cement industry to select energy efficiency 2015年10月23日 In this chapter an introduction of widely applied energyefficient grinding technologies in cement grinding and description of the operating principles of the related equipments and comparisons over each other in terms of grinding efficiency, specific energy consumption, production capacity and cement quality are given A case study performed on a EnergyEfficient Technologies in Cement Grinding IntechOpen2021年12月10日 In today's machining production lines, grinding strategies are built for classical economic benefits A considerable amount of electric energy is being wasted due to its low energy efficiency Facing the global energy crisis and environmental pollution, it is essential to develop novel grinding strategies for energy efficient grindingPredictive modelling and Pareto optimization for energy efficient
.jpg)
Breakthrough in Clinker Grinding Massachusetts Institute of
2012年11月8日 cement production is for material size reduction Increasing the efficiency of particle size reduction could have a large impact on energy consumption in the cement industry Current estimates of grinding power requirements used for equipment sizing are indirect indications often based on industrial experience or scaled up from laboratory tests2017年6月15日 Introduction Machine tools are the basic energy consumption devices in manufacturing, whose energy saving cannot be neglected (Liu, Wang, and Liu Citation 2013)The energy yearbook published by the US energy information administration in 2012, showed that machine tools electricity consumption occupied 75% of manufacturing electricity consumption, Energy consumption model and energy efficiency evaluation With more detailed data on energy consumption available by subsectors or energy uses (eg space heating) or by modes of transport (eg cars), it is possible to assess energy efficiency trends through a more accurate indicator than energy intensity, called “energy efficiency indices”: this is the objective of the second method of calculation presented in this documentCalculation methods for energy efficiency and energy 2021年12月10日 Therefore, facing the enormous energysaving potential and low energy efficiency in grinding production line, (1 − u)] 1 ν + 1, i f u > 05 Where u ∈ [0,1] ν is the distribution index of crossover and mutation algorithms It should Predictive modelling and Pareto optimization for energy efficient
.jpg)
Evolution of grinding energy and particle size during dry ball
Evolution of grinding energy and particle size during dry ballmilling of silica sand Nicolas Blanca, Claire MayerLaiglea, Xavier Franka, Farhang Radjaib, JeanYves Delennea,* aIATE, Univ Montpellier, CIRAD, INRAE, Montpellier SupAgro, Montpellier, France bLMGC, Univ Montpellier, CNRS, Montpellier, France Abstract The energy efficiency of dry fine grinding process of