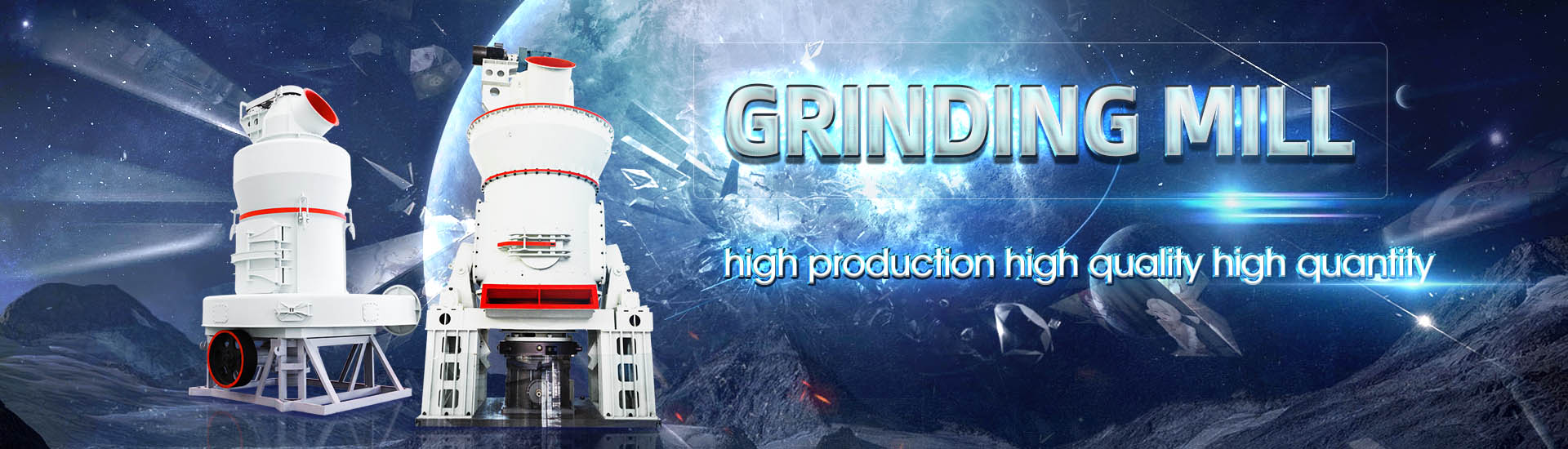
How Much Grinding Can a Ball Mill Do per Hour
.jpg)
Calculate Ball Mill Grinding Capacity 911Metallurgist
2015年10月15日 Learn how to calculate the grinding capacity of your ball mill with 911 Metallurgist This guide provides essential formulas, insights, and tips to optimize your milling process and enhance production efficiency2015年6月19日 A wet grinding ball mill in closed circuit is to be fed 100 TPH of a material with a work index of 15 and a size distribution of 80% passing ¼ inch (6350 microns) The required product size distribution is to be 80% passing Ball Mill Design/Power Calculation 911MetallurgistHow to calculate the grinding efficiency of ball mills? Ball mill grinding efficiency can be calculated using the following equation: Efficiency = (100% Productivity) * 100 Efficiency = Ball mill Grinding efficiency of ball mill calculating equation2016年2月14日 Do you need a quick estimation of a ball mill’s capacity or a simple method to estimate how much can a ball mill of a given size (diameter/lenght) grind for tonnage a product Small Ball Mill Capacity Sizing Table 911Metallurgist
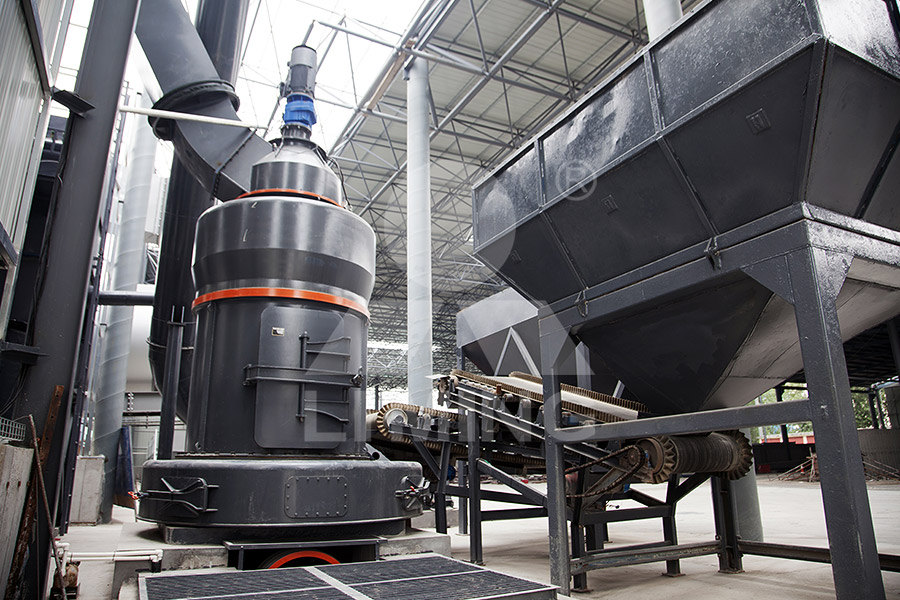
ball mill calculations, grinding media filling degree, ball size, mill
online live calculators for grinding calculations, Ball mill, tube mill, critical speed, Degree of filling balls, Arm of gravity, mill net and gross power Capacity: Determine the required grinding capacity based on the expected throughput of the mill Consider the size of the feed material and the desired product size to select a mill with the Technical specifications and selection guide for ball millsBall mill optimisation As grinding accounts for a sizeable share in a cement plant’s power consumption, optimisation of grinding equipment such as ball mills can provide significant cost BALL MILLS Ball mill optimisation Holzinger ConsultingThis document provides guidance on ball mill grinding processes It covers topics such as ball mill design including length to diameter ratios, percent loading, critical speed, and internals evaluation Methods for assessing ball charge, Ball Mill Grinding Process Handbook
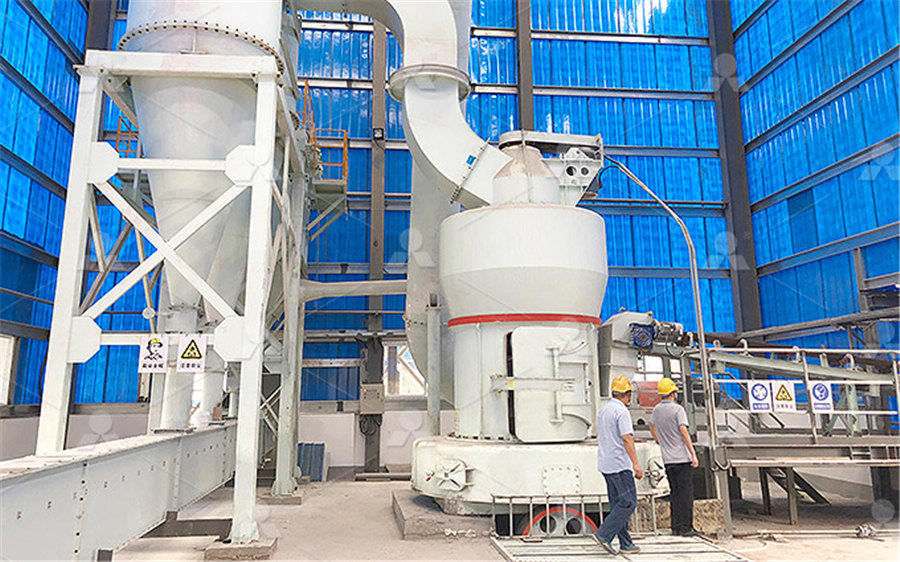
AMIT 135: Lesson 7 Ball Mills Circuits – Mining Mill
For primary grinding, the ratio could vary between 1:1and 18:1 For fine regrinding in open circuit, the ratio ranges from 13:1 to 15:1 Some ball mills are separated in to compartments by grates The grates hold back particles above 2023年3月6日 To calculate the balls needed in a ball mill, you need to know the capacity of the mill and the desired grind size You can then use the following equation to calculate the How to calculate the balls needed in a ball mill?Ball mills are primarily used for grinding ores and other materials, such as cement, silicates Tower Mills were developed to overcome some of the limitations of both ball mills and SAG mills They can handle finer feeds than Understanding the SAG Mill in Copper Ore Mining If a ball mill uses little or no water during grinding, it is a ‘dry’ mill If a ball mill uses water during grinding, it is a ‘wet’ mill A typical ball mill will have a drum length that is 1 or 15 times the drum diameter Ball mills with a drum length to Ball Mill (Ball Mills Explained) saVRee saVRee
.jpg)
Factors Affecting Ball Mill Grinding Efficiency
2017年10月26日 The following are factors that have been investigated and applied in conventional ball milling in order to maximize grinding efficiency: a) Mill Geometry and Speed – Bond (1954) observed grinding efficiency to be a 2023年4月23日 A comparison of the grinding media is given together with the knowledge gaps that still need to be bridged to improve the quality and performance of grinding media used in ball mills(PDF) Grinding Media in Ball MillsA Review ResearchGate2015年2月21日 In practice, circulating loads between ball mills and classifiers are rarely less than 200 per cent and frequently exceed 700 per cent It may appear strange at first sight that the circulating load between a mill and classifier producing, for example, 100 tons of finished product per day can be as much as 400 tons or more, but this will be made clear by Fig 71Circulating Load Calculation Formula 911MetallurgistThe installation, commissioning and training of the mill can be completed in only 2 to 3 weeks, allowing you to start your milling journey in record time It was designed with growth in mind and can easily be expanded on at any time with a range of optional extras Extraction rates 69% 74% for Super or Grade 1 maize mealSP1 650kg to 1 ton per hour maize mill – Roff Milling
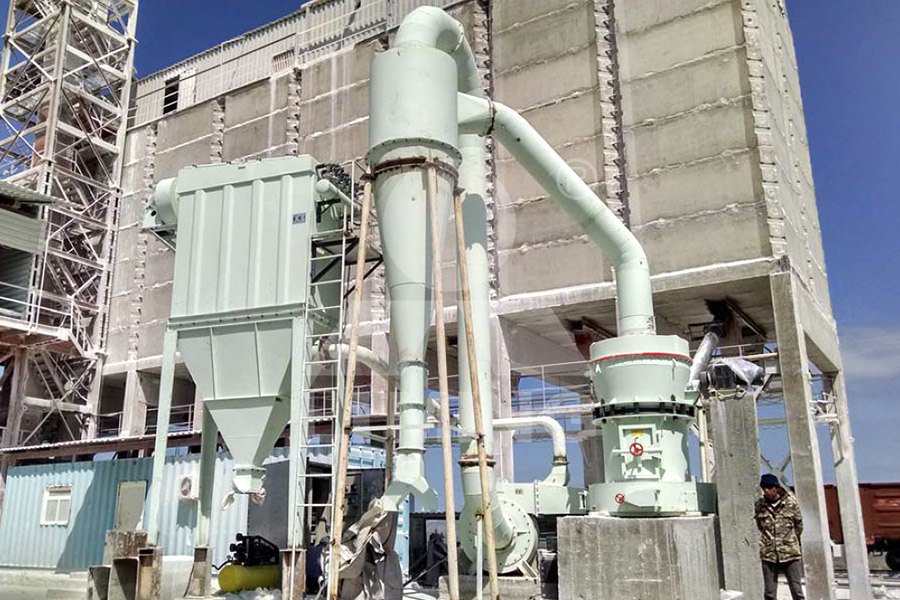
Crusher Operating Costs: How to Optimize and Reduce
2016年1月11日 It is assumed that power is charged to the plant at the rate of 075d per kilowatthour in the case of the smallest plant, decreasing as the capacity increases to a minimum of 05d per kwhr for the largest The power consumption of a machine or installation is usually expressed in kwhours per ton as being the most convenient methodWhen charging a ball mill, ceramic lined mill, pebble mill, jar mill or laboratory jar use on a jar rolling mill it is important to have the correct amount of media and correct amount of product Charging a Dry Mill The general operation of a grinding mill is to have the product impacted between the balls as they tumbleBall Mill Loading Dry Milling Paul O Abbe2015年12月17日 With a typical 6:1 reduction ratio, the power consumption of a large jaw crusher (48 by 60) is approximately 18 tons per horsepowerhour (22 t/kWh) Source: Arthur Taggart; The power consumption of a 42inch gyratory crusher is approximately 24 tons per horsepowerhour (29 t/kWh) Source: Arthur TaggartRock Crushing Rule of Thumb 911MetallurgistBased on the MPT TITAN™ design, the Mills are girth gear dual pinion driven with selfaligned flanged motors, running on hydrodynamic oil lubricated bearings The TITAN design enables you to run full process load 40% Ball charge at 80% critical speed – Max grinding power for every shell size Standard Mill Types Available: Overflow Ball Ball Mills – MechProTech MPT
.jpg)
OPTIMIZATION OF CEMENT GRINDING OPERATION IN BALL MILLS
PEC Consulting Group LLC 10123 Corporate Square Dr, St Louis, MO 63132 +1 314 8780123 peccg OPTIMIZATION OF CEMENT GRINDING OPERATION IN BALL MILLS2017年4月29日 911 Metallurgist is a trusted resource for practical insights, solutions, and support in mineral processing engineering, helping industry professionals succeed with proven expertise Grinding Media Wear Rate Calculation in Ball MillGrinding Media Wear Rate Calculation in Ball Mill2020年7月2日 A properly seasoned charge of grinding media should be able to break large particles and not produce unnecessary ultrafine particles In recent research done by AmanNejad and Barani [93] using DEM (PDF) Effects of Ball Size Distribution and Mill Speed and Their 2023年6月16日 Keep in mind factors such as ball diameter, balltomaterial ratio, and mill speed, as these can affect the grinding kinetics and efficiency Ensure Proper Distribution: Distribute the calculated amount of grinding media evenly within the mill Uneven distribution can lead to inefficient grinding and uneven wear of the mediaHow do you calculate ball mill grinding media?
.jpg)
Ball Mill Grinding Capacity Calculator 911 Metallurgist
Ball Mill Design leftpanel 0 SITUATION : Ore Work Index, kWh (net)/metric ton : Based on Net Power Available Feed Size, F80, microns : Effective Grinding Lenght Mill Speed % Critical : Rotational Mill Speed, expressed as a percentage of the 2017年2月20日 Grinding Mill Specifications Data According to formula 423/√d, where d is equal to internal shell diameter within new liners In this case the thickness used was 60 mm for small mill sizes up to and including 2940 and 80 mm for larger millsGrinding Mill Design Ball Mill Manufacturer 911Metallurgist2012年6月1日 Ball mills can grind a wide range of materials, including metals, ceramics, and polymers, and can operate on a variety of scales, from laboratory to industrial (Monov et al 2013)Grinding in Ball Mills: Modeling and Process ControlOur common calcium carbonate grinding mills include ball mill, micro powder roller mill, Raymond roller mill, vertical mill, wet grinding mill and so on Its output is generally 1 to 30 tons per hour (different finished product fineness will lead to different output)How to Choose a Calcium Carbonate Grinding Mill DASWELL
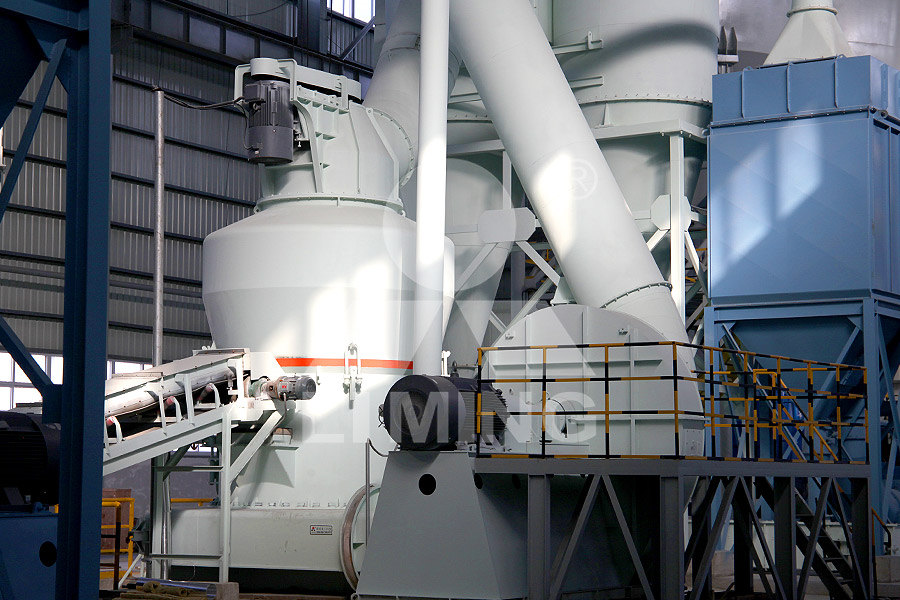
How grinding mill design changed over the last 30 years
2020年6月3日 New grinding mills do not look much different than older mills either The design process has changed dramatically with computers though A typical FEA of a grinding mill that would take about 3 hours on a minicomputer in the late 80’s takes about 3 minutes on a laptop computer todayAmount of fuel used per hour Ball and liner coating can occur in raw as well as finish grinding Ball coating can be a result of the following conditions: Inadequate Grinding Aid; Details of VRM and HPGR are not as much as of Ball mills Loading Reply Mousa Hanaya January 27, 2021 at 9:25 pm Good information about ballEverything you need to know about clinker/cement Grinding2015年4月9日 Autogenous mills are more suited to large installations ie more than 50 tons per hour and have a power requirement ranging from 40 kW up to hundreds of kW This ensures that the smaller particles are attacked by the Grinding Mills and Their Types IspatGuru2024年8月8日 Grinding media, pivotal for the efficacy of the ball milling process, come in various materials, each offering unique characteristics and advantages tailored to specific applications Ceramic Balls: Composed of materials like Ball Mill Success: A StepbyStep Guide to Choosing
.jpg)
How to Ball Mill Chemicals Safely — Skylighter, Inc
2018年2月16日 Lloyds's book is the most complete and practical resource I know for information on ball milling theory and for plans to actually build your own ball mill Here's a shot of a nice, doublebarrel mill I built based on his Grinding Mills: Ball Mill Rod Mill Design PartsCommon types of grinding mills include Ball Mills and Rod Mills This includes all rotating mills with heavy grinding media loads This article focuses on ball and rod mills excluding SAG and AG mills Although their concepts are very similar, they are not discussed herePhotographs of a glass ended laboratory ball mill show Grinding Mills 911MetallurgistBall mills and grinding tools Cement ball mills are typically twochamber mills (Figure 2), where the first chamber has larger media with lifting liners installed, providing the coarse grinding stage, whereas, in the second chamber, medium and fine grinding is carried out with smaller media and classifying linersBALL MILLS Ball mill optimisation Holzinger Consulting2017年4月28日 There were 563 T of minus 200mesh material actually produced per hour and 192 kwhr per ton of minus 200mesh material produced were required The classifier delivered 33 T of sand per hour The total ballmill feed was therefore 4037 T per hr or 550 per cent, of the original feed Two Stage GrindingBall Mill Grinding Theory – Crushing Motion/Action Inside
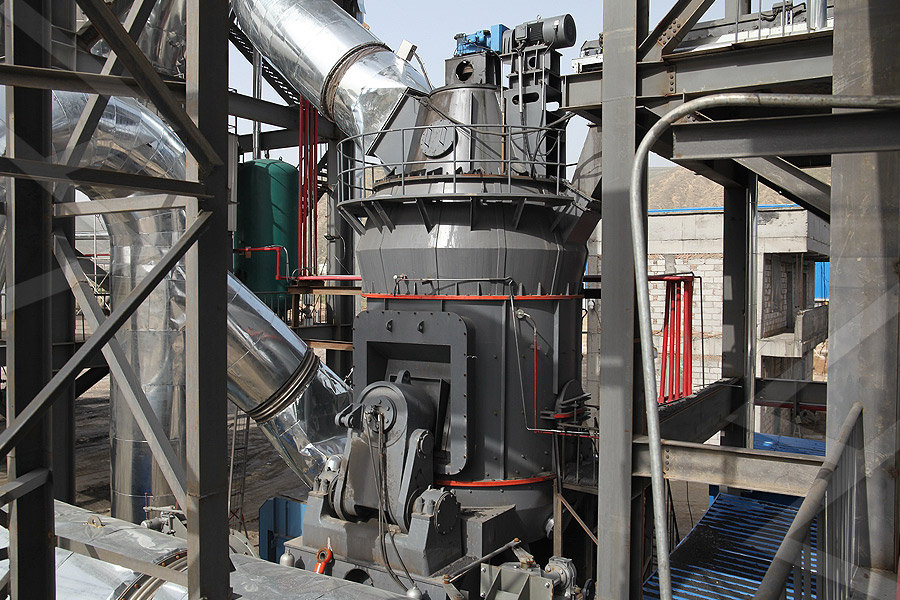
Why use Different Size Balls in a Mill 911Metallurgist
2017年7月3日 The surface tons per hour show, an increase of 45 percent in favor of the rationed ball sizes, and the surface tons per horsepowerhour show a more moderate advantage—37 percent The reason the advantage in capacity was greater than in efficiency is because of the difference in power in the two tests; the smaller balls required more power than the larger ones2017年1月17日 produce 580 000 ounces of gold and 600 000 ounces of silver per year After a 2stage crushing, the o re is The grinding process in ball mills is notoriously known to be highly inefficient: Breaking down energy consumption in industrial grinding mills2018年4月17日 Figures 3a 3b give the power for an autogenous mill Figures 4a and 4b are for the same size mill with a ball charge of 6% of mill volume (290 lbs per cubic foot) In the above example the power was calculated for a 30% volume However, with the same sheets the power can be determined for any volumetric loading from 15% to 35%Autogenous and SAG SemiAutogenous Mill Design Calculations2013年7月15日 The ball mill in closed circuit with hydrocyclones is an industry standard, and well known methodologies exist for equipment sizing, selection and design(PDF) Energy Efficient Ball Mill Circuit – Equipment Sizing
.jpg)
Understanding the SAG Mill in Copper Ore Mining
Ball mills are primarily used for grinding ores and other materials, such as cement, silicates Tower Mills were developed to overcome some of the limitations of both ball mills and SAG mills They can handle finer feeds than If a ball mill uses little or no water during grinding, it is a ‘dry’ mill If a ball mill uses water during grinding, it is a ‘wet’ mill A typical ball mill will have a drum length that is 1 or 15 times the drum diameter Ball mills with a drum length to Ball Mill (Ball Mills Explained) saVRee saVRee2017年10月26日 The following are factors that have been investigated and applied in conventional ball milling in order to maximize grinding efficiency: a) Mill Geometry and Speed – Bond (1954) observed grinding efficiency to be a Factors Affecting Ball Mill Grinding Efficiency2023年4月23日 A comparison of the grinding media is given together with the knowledge gaps that still need to be bridged to improve the quality and performance of grinding media used in ball mills(PDF) Grinding Media in Ball MillsA Review ResearchGate
.jpg)
Circulating Load Calculation Formula 911Metallurgist
2015年2月21日 In practice, circulating loads between ball mills and classifiers are rarely less than 200 per cent and frequently exceed 700 per cent It may appear strange at first sight that the circulating load between a mill and classifier producing, for example, 100 tons of finished product per day can be as much as 400 tons or more, but this will be made clear by Fig 71The installation, commissioning and training of the mill can be completed in only 2 to 3 weeks, allowing you to start your milling journey in record time It was designed with growth in mind and can easily be expanded on at any time with a range of optional extras Extraction rates 69% 74% for Super or Grade 1 maize mealSP1 650kg to 1 ton per hour maize mill – Roff Milling2016年1月11日 It is assumed that power is charged to the plant at the rate of 075d per kilowatthour in the case of the smallest plant, decreasing as the capacity increases to a minimum of 05d per kwhr for the largest The power consumption of a machine or installation is usually expressed in kwhours per ton as being the most convenient methodCrusher Operating Costs: How to Optimize and ReduceWhen charging a ball mill, ceramic lined mill, pebble mill, jar mill or laboratory jar use on a jar rolling mill it is important to have the correct amount of media and correct amount of product Charging a Dry Mill The general operation of a grinding mill is to have the product impacted between the balls as they tumbleBall Mill Loading Dry Milling Paul O Abbe
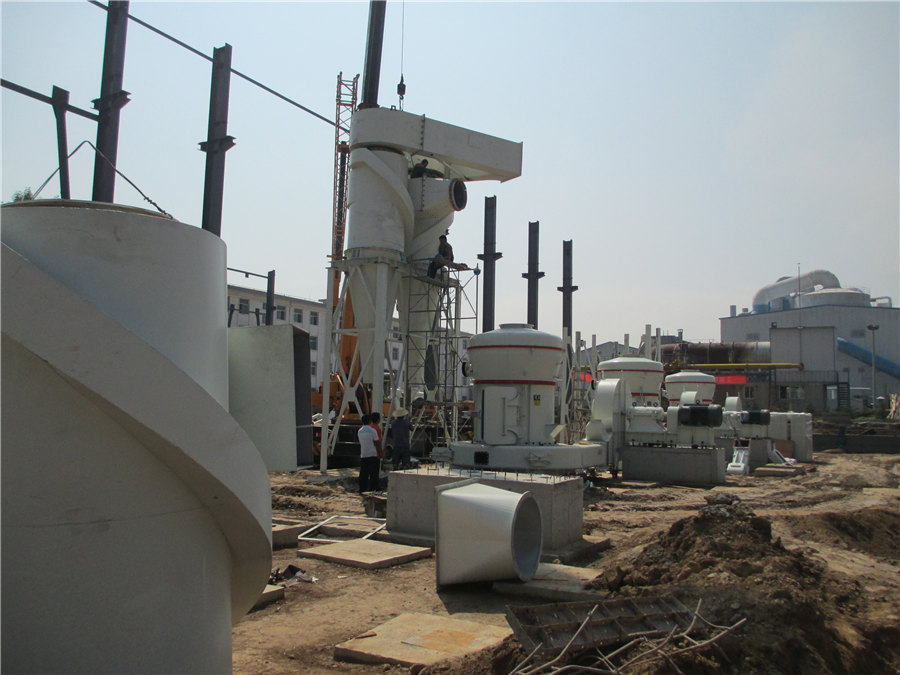
Rock Crushing Rule of Thumb 911Metallurgist
2015年12月17日 With a typical 6:1 reduction ratio, the power consumption of a large jaw crusher (48 by 60) is approximately 18 tons per horsepowerhour (22 t/kWh) Source: Arthur Taggart; The power consumption of a 42inch gyratory crusher is approximately 24 tons per horsepowerhour (29 t/kWh) Source: Arthur TaggartBased on the MPT TITAN™ design, the Mills are girth gear dual pinion driven with selfaligned flanged motors, running on hydrodynamic oil lubricated bearings The TITAN design enables you to run full process load 40% Ball charge at 80% critical speed – Max grinding power for every shell size Standard Mill Types Available: Overflow Ball Ball Mills – MechProTech MPT