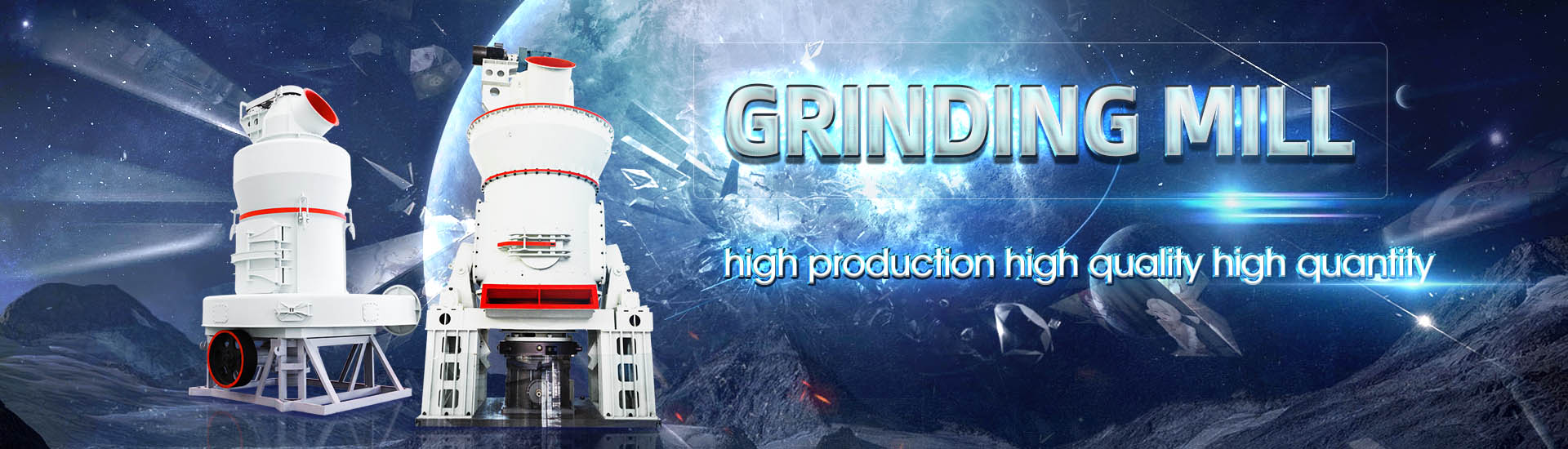
Coal mill control cabinet picture
.jpg)
LOESCHEMILLS
The Loesche coal grinding mill range is divided into two serial types: Small twin mills constructed to individual specifications (LM 122 D to LM 202 D), with table diameters from 1,200 to 2,000 FControlTM dosing control system is used for continuously operating gravimetric feeders like rotor weighfeeders, belt weighfeeders, etc The main structural elements are a control cabinet Product Brochure Pfister DRW COLMEXSectional view of MBF coal mill [] The coal mill used in the coalfired power plants is modeled in view of the controller design rather than the educational simulator The coal mass flowSectional view of MBF coal mill Download Scientific DiagramYour complete mill performance assessment online! The MECONTROL Coal central measurement base station controls all sensors and collates data Two independent Mecontrol coal 2018 3l1 nF RZ
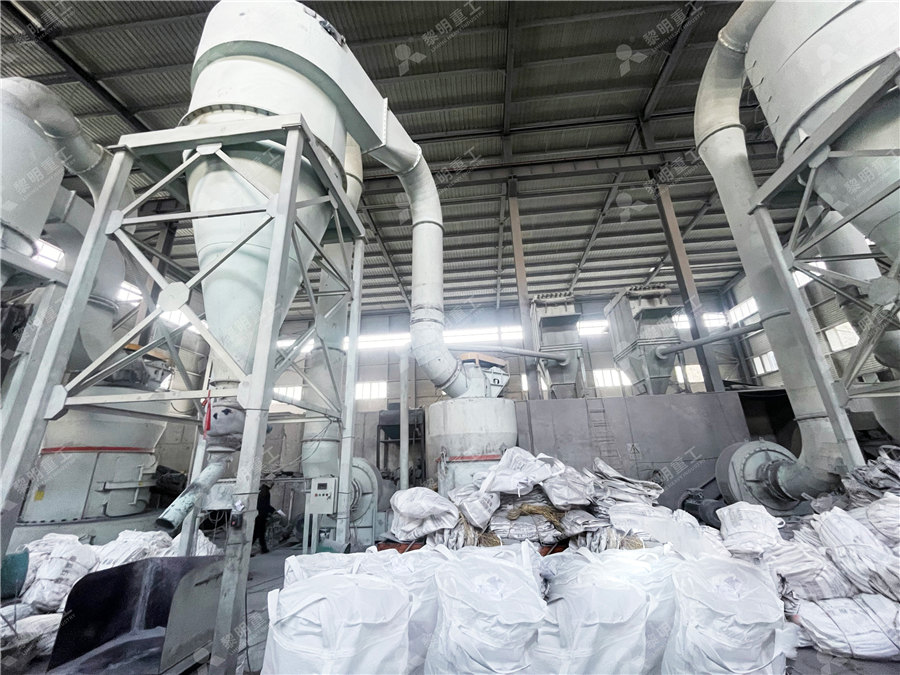
Instrumentation and control in coalfired power plant ICSC
Instrumentation and control is an integral part of a coalfired power station A modern, advanced IC system plays a major role in the profitable operation of a plant by achieving maximum 2013年3月1日 Coal mills are used in coal fired power plants to grind crushed coal lumps with several cm diameters to very fine powder in the order of 50– 100 μ m diameter A further task Nonlinear coal mill modeling and its application to model 2012年5月1日 The paper presents development and validation of a coal mill model to be used for improved mill control, which may lead to a better load following capability of power plants Derivation and validation of a coal mill model for control2015年8月1日 Power plant performance and reliability is highly influenced by coal mills that grind, dry, and transport coal to the furnace This paper presents a review of the current state Review of control and fault diagnosis methods applied to coal
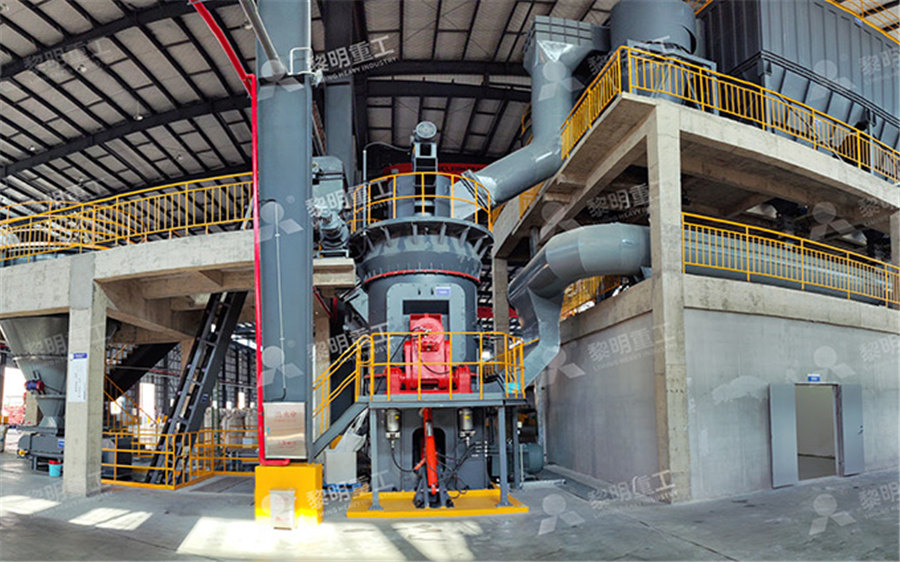
COALFIRED POWER PLANTS Land Instruments International
Using a highresolution sensor, the flexible, optionrich ARC Imager delivers detailed thermal images with excellent stability The ARC Imager’s four lens options allow a clear view of a vertical roller grinding mills for grinding: • Coal • Cement raw material • Clinker / granulated slag • Industrial minerals, and • Ores The core elements of these plants are the Loesche vertical PROCESS OPTIMISATION FOR LOESCHE GRINDING PLANTS: pradeebhamit@gmail, npappa@rediffmail , vasanthi@annauniv Abstract: The paper presents development and validation of coal mill model (including the action of classifier) to be used for improved coal mill control The model is developed by using the mass and heat balance equations of the coal mill(PDF) Modeling and Control of Coal Mill AcademiaCoal Mill Feeding Pfister TRWK The picture below exemplary displays a rotor weighfeeder for dosing pulverised fuel However, the weighing and dosing The control cabinet FCC contains all controllers for dosing and speed This also includes the monitoring of these functionsProduct Brochure Pfister DRW COLMEX
.jpg)
Mill Inerting and Pulverizer/Mill Explosion Mitigation
• Coal characteristics profoundly influence risk – Lower rank coals are generally more easily ignited inside the coal mill – High volatile matter and highly reactive coals encourage preignition inside the mill – Higher moisture content requires temperature extremes inside the mill2024年3月3日 coal mill Feedercoal mill Feeder1 (2) iii) Elimination of breaking losses iv) Better response to automatic control v) Ability to use high combustion air temperature; increasing the overall efficiency of boiler vi) High availability 6 Rollers Coal Entry Hot Air Flow from PA Fan Pictures of Bowl Mill 7coal mill Feedercoal mill Feeder1 (2)ppt Free DownloadAbstract: The paper presents development and validation of coal mill model (including the action of classifier) to be used for improved coal mill control The model is developed by using the mass and heat balance equations of the coal mill Genetic Algorithm is used to estimate the unknown parameters that are used in the model validationModeling and Control of Coal Mill2016年4月1日 Download Citation Modeling and control of ball mill system considering coal moisture This study analyzes the dynamic characteristics of duplex inlet and outlet ball mill direct firing Modeling and control of ball mill system considering coal moisture
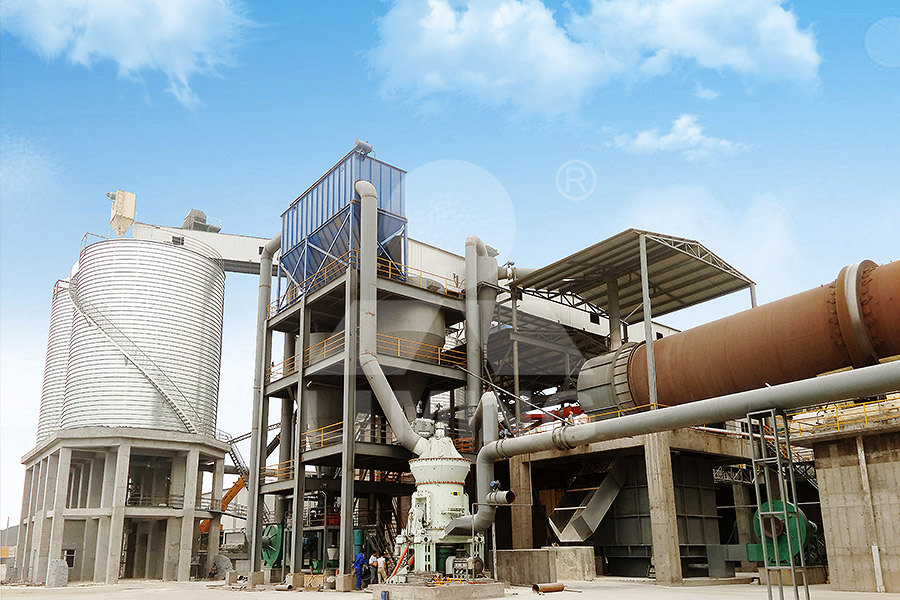
Comparison CO inerting – CO fire extinguishing Coal Mill Safety
Therefore many coal mill manufacturers favourize CO2 inerting systems instead of fire fighting systems 4 Liquid CO2 respectively dry ice cannot be used for injection into silo fluidisation systems or massive problems will be generated Only gaseous CO2 can be injected which is penetrating into coal powder and then extinguishing smoldering fires2015年8月1日 Mill problems originate mainly due to poor controls or faults occurring within the milling system As discussed by GQ Fan and NW Rees [3], the control of mills remains very simple in most of the power plants due to the fact that the mill system is highly nonlinear with strong coupling among the variables and it is very difficult to measure some important Review of control and fault diagnosis methods applied to coal 2006年6月25日 Benson boiler operation and coal mill control, focusing on available measurements etc Then, in Section 3 we present a Kalman filterbased estimator designObserverBased Coal Mill Control Using Oxygen Measurements 45 Coal Plant Control Room Operator jobs available on Indeed Apply to Plant Operator, Control Room Operator, Senior Production Specialist and more!Coal Plant Control Room Operator jobs Indeed
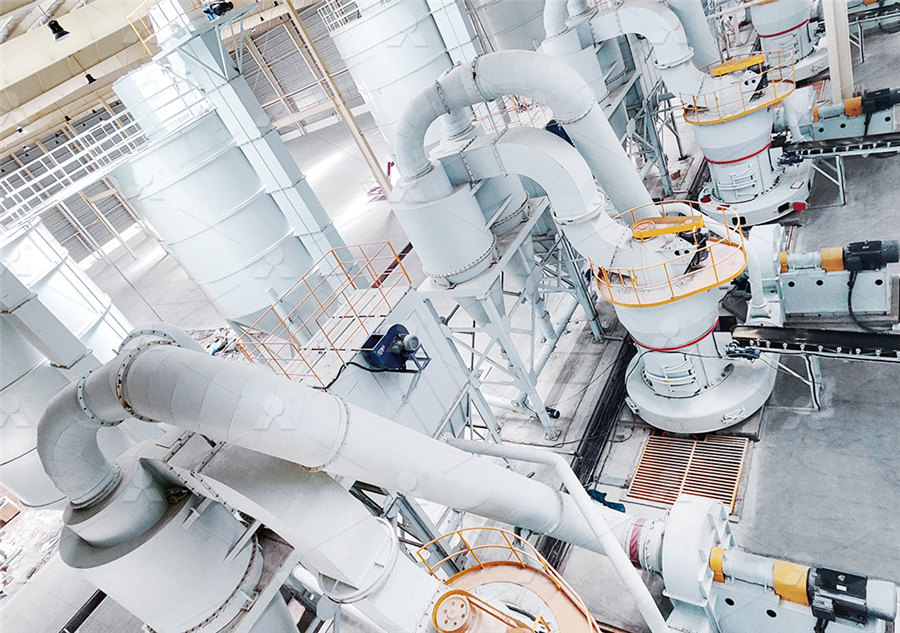
Measurement and Control of Coal Pipe Temperature of Coal Mills
additional field tests, but require suitable modelling techniques which are to be identified properly A novel coal mill modelling technique for Etype coal mill and dynamic behaviour are developed using genetic algorithms [3] Genetic Algorithms (GAs) have been successfully applied to problems in business, engineering, and science2020年8月12日 This study shows the performance of a currently running vertical roller coal mill (VRM) in an existing coalfired power plant In a power plant, the coal mill is the critical equipment, whose An investigation of performance characteristics and 2009年9月1日 The coal mill used in the coalfired power plants is modeled in view of the controller design rather than the educational simulator The coal mass flow and the outlet temperature are modeled by reinvestigating the mass balance and heat balance models physically The archived data from a plant database are utilized to identify the model Modeling and Parameter Identification of Coal Mill2022年8月31日 PDF In order to improve the automatic control effect of fully mechanized mining face in coal mine, (PDF) Design and Application of Automatic Control System for
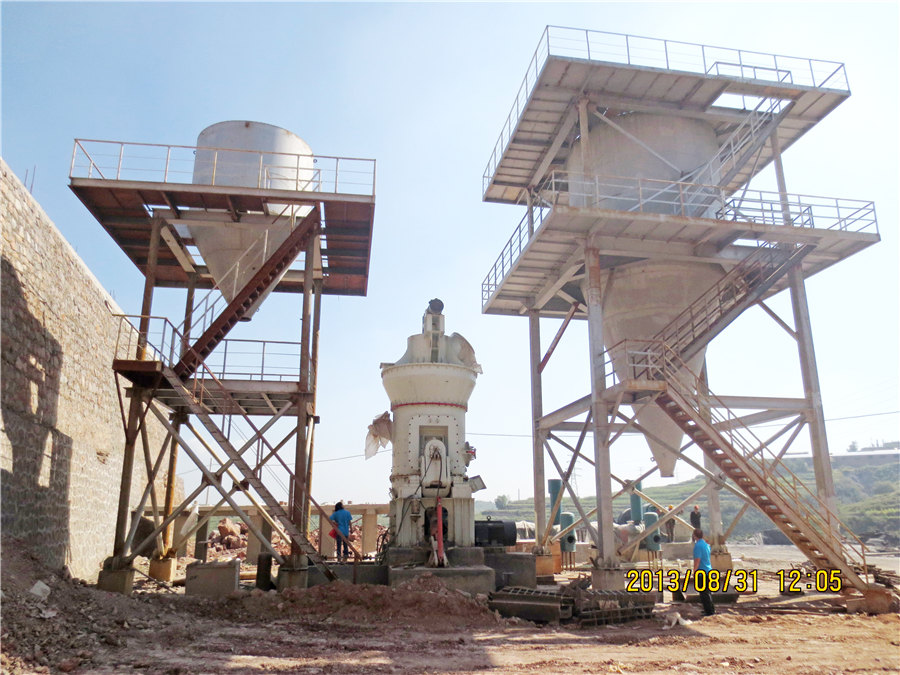
Sectional view of MBF coal mill Download Scientific Diagram
A control oriented model was then developed by Fan (1994) and Fan and Rees (1994) In 2009, coal flow and outlet temperature of mill were modelled using mass and heat balance equations for startup Inputs available for external signals (such as mill feeder, roller pressure etc) Automatic calibration Derived data analysis online, in real time (mill dynamics) Operation through Touch Panel Panel IP 55 rated Control System Junction Box Auxiliary Energy 110 VAC / 230 VAC MECONTROL Coal Measurement Cabinet Control system room Periphery Mecontrol coal 2018 3l1 nF RZZGM type Mediumspeed Rolling coal mill motor and electrical control cabinet 132 Structural features of ZGM medium speed mixed coal mill 1321 The three mills of the coal mill are respectively fixed by hinge shaft and press frame, and rotate under the drive of disc rotation and friction force (only self rotation, no revolution)ZGM type Mediumspeed Rolling coal millpower plant equipmentONLINE COAL FLOW MEASURING AND BALANCING (CONTROL) AND ONLINE COAL FINENESS MEASURING SYSTEM FOR COMBUSTION OPTIMISATION IN A THERMAL BOILER Suresh G Chandwani1, Dr Francesco Turoni2, Reinhardt Kock2, Dr Michael Haug2, Dr Michael Schreiber2 1NSGuzder Company Pty Ltd, Neville House, Currimbhoy Road, ONLINE COAL FLOW MEASURING AND BALANCING (CONTROL) AND ONLINE COAL
.jpg)
Research and Design of Coal PLC Control System in Coalfired
each bunker has 4 coal exports To control the coal fall into the coal bunker according to the coal level of each coal bunker export 41 Upper Coal Control Upper coal control includes automatic, manual and local mode 1 Automatic mode All operations of the automatic mode can be operated by the PC keyboard, operating2022年6月30日 Lakvijaya Power Plant is an operating power station of at least 900megawatts (MW) in Norocholai, Puttalam, North Western, Sri Lanka with multiple units, some of which are not currently operating It is also known as Norocholai Power Station, Norochcholai Coal Power Plant, Puttalam Coal PlantLakvijaya Power Plant Global Energy Monitor2014年1月1日 The emission factors of kiln end, kiln head, coal mill, crushing and cement mill was 0156 clinker g/t, 3914 clinker g/t, 1538 coal g/t, 0016 stone g/t and 0056 cement g/t respectively, the (PDF) MPS mills for coal grinding ResearchGate2020年1月1日 Fuel preparation is the control bottleneck in coalfired power plants due to the unmeasurable nature or inaccurate measurement of key controlled variables(PDF) Modelling and multiloop selective control of
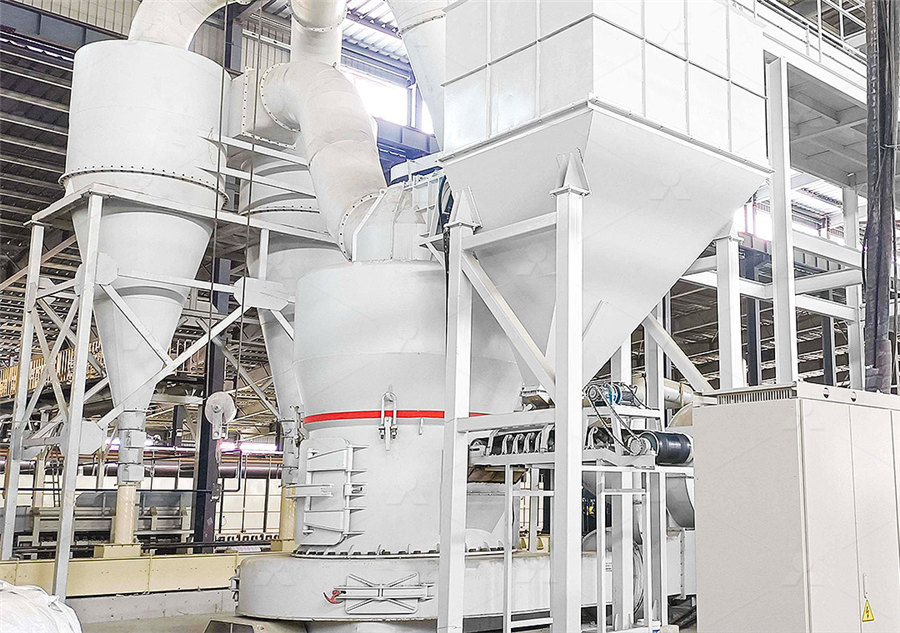
In discussion: Vincent Grosskopf, Coal Mill Safety
GC: What led you to establish Coal Mill Safety? VG: I established Coal Mill Safety (CMS) as a consultancy after I ‘retired’ in 2011 If a cement producer wants to install a new coal grinding system, they can commission CMS to look at the supplier’s design and probe it from a safety angle If it has an existingbe improved by modeling the coal mill properly for control purpose It is necessary to model the coal flow and the pulverized coal temperature [3], [4]Modeling and Parameter Identification of Coal Mill ResearchGate520 P Niemczyk et al / Control Engineering Practice 20 (2012) 519–530 Nomenclature Dpmill mc mpc mcair mass of unground coal on the table (kg) mass of pulverized coal on the table (kg) mass of pulverized coal carried by primary air (kg) wc wpc wout wret mass mass mass mass flow flow flow flow of of of of the dry raw coal to the mill (kg Derivation and validation of a coal mill model for control2015年8月1日 Mill problems originate mainly due to poor controls or faults occurring within the milling system As discussed by GQ Fan and NW Rees [3], the control of mills remains very simple in most of the power plants due to the fact that the mill system is highly nonlinear with strong coupling among the variables and it is very difficult to measure some important Review of control and fault diagnosis methods applied to coal
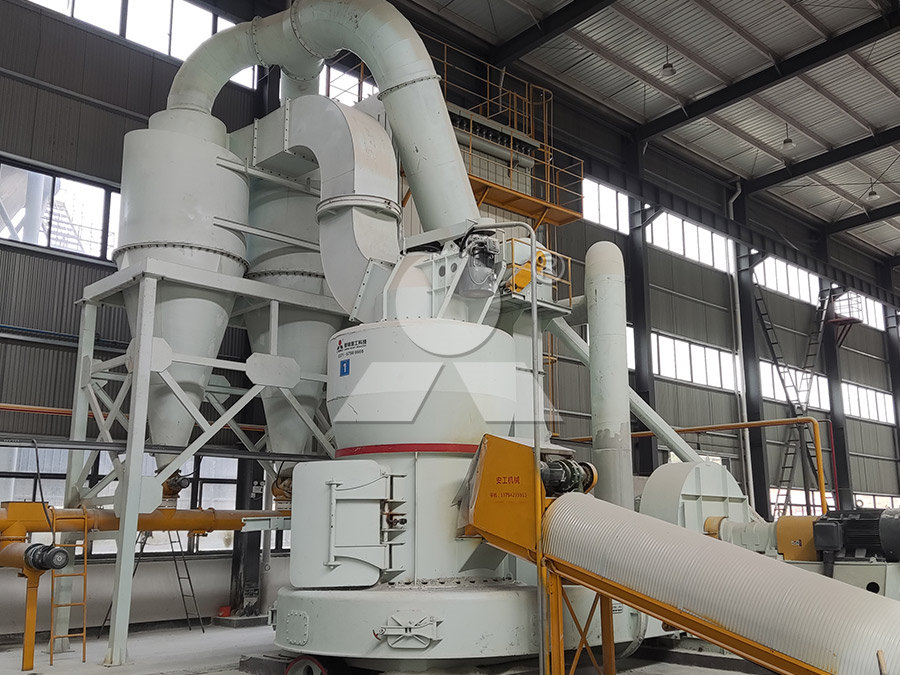
Detection of Malfunctions and Abnormal Working Conditions of a Coal Mill
2018年5月2日 Coal mill malfunctions are some of the most common causes of failing to keep the power plant crucial operating parameters or even unplanned power plant shutdowns Therefore, an algorithm has been developed that enable online detection of abnormal conditions and malfunctions of an operating mill Based on calculated diagnostic signals and defined additional field tests, but require suitable modelling techniques which are to be identified properly A novel coal mill modelling technique for Etype coal mill and dynamic behaviour are developed using genetic algorithms [3] Genetic Algorithms (GAs) have been successfully applied to problems in business, engineering, and scienceMeasurement and Control of Coal Pipe Temperature of Coal Mills 2015年11月1日 Next, the paper estimates the coal outlet mass flow of the coal mill by using extended Kalman filter (EKF), and the result is compared with the coal flow instruction Finally, we take the estimation of coal outlet mass flow as the new controlled variable and use inferential predictive control method to solve the coal mill control problemsThe Inferential predictive control method of coal mill2011年8月28日 Download Citation Coal Mill Modeling for Monitoring and Control The more fluctuating renewable energy sources like solar and wind are integrated into the electric grid, the more it is Coal Mill Modeling for Monitoring and Control ResearchGate
.jpg)
(PDF) Modeling and Control of Coal Mill Academia
: pradeebhamit@gmail, npappa@rediffmail , vasanthi@annauniv Abstract: The paper presents development and validation of coal mill model (including the action of classifier) to be used for improved coal mill control The model is developed by using the mass and heat balance equations of the coal millCoal Mill Feeding Pfister TRWK The picture below exemplary displays a rotor weighfeeder for dosing pulverised fuel However, the weighing and dosing The control cabinet FCC contains all controllers for dosing and speed This also includes the monitoring of these functionsProduct Brochure Pfister DRW COLMEX• Coal characteristics profoundly influence risk – Lower rank coals are generally more easily ignited inside the coal mill – High volatile matter and highly reactive coals encourage preignition inside the mill – Higher moisture content requires temperature extremes inside the millMill Inerting and Pulverizer/Mill Explosion Mitigation2024年3月3日 coal mill Feedercoal mill Feeder1 (2) iii) Elimination of breaking losses iv) Better response to automatic control v) Ability to use high combustion air temperature; increasing the overall efficiency of boiler vi) High availability 6 Rollers Coal Entry Hot Air Flow from PA Fan Pictures of Bowl Mill 7coal mill Feedercoal mill Feeder1 (2)ppt Free Download
.jpg)
Modeling and Control of Coal Mill
Abstract: The paper presents development and validation of coal mill model (including the action of classifier) to be used for improved coal mill control The model is developed by using the mass and heat balance equations of the coal mill Genetic Algorithm is used to estimate the unknown parameters that are used in the model validation2016年4月1日 Download Citation Modeling and control of ball mill system considering coal moisture This study analyzes the dynamic characteristics of duplex inlet and outlet ball mill direct firing Modeling and control of ball mill system considering coal moistureTherefore many coal mill manufacturers favourize CO2 inerting systems instead of fire fighting systems 4 Liquid CO2 respectively dry ice cannot be used for injection into silo fluidisation systems or massive problems will be generated Only gaseous CO2 can be injected which is penetrating into coal powder and then extinguishing smoldering parison CO inerting – CO fire extinguishing Coal Mill Safety 2015年8月1日 Mill problems originate mainly due to poor controls or faults occurring within the milling system As discussed by GQ Fan and NW Rees [3], the control of mills remains very simple in most of the power plants due to the fact that the mill system is highly nonlinear with strong coupling among the variables and it is very difficult to measure some important Review of control and fault diagnosis methods applied to coal
.jpg)
ObserverBased Coal Mill Control Using Oxygen Measurements
2006年6月25日 Benson boiler operation and coal mill control, focusing on available measurements etc Then, in Section 3 we present a Kalman filterbased estimator design45 Coal Plant Control Room Operator jobs available on Indeed Apply to Plant Operator, Control Room Operator, Senior Production Specialist and more!Coal Plant Control Room Operator jobs Indeed