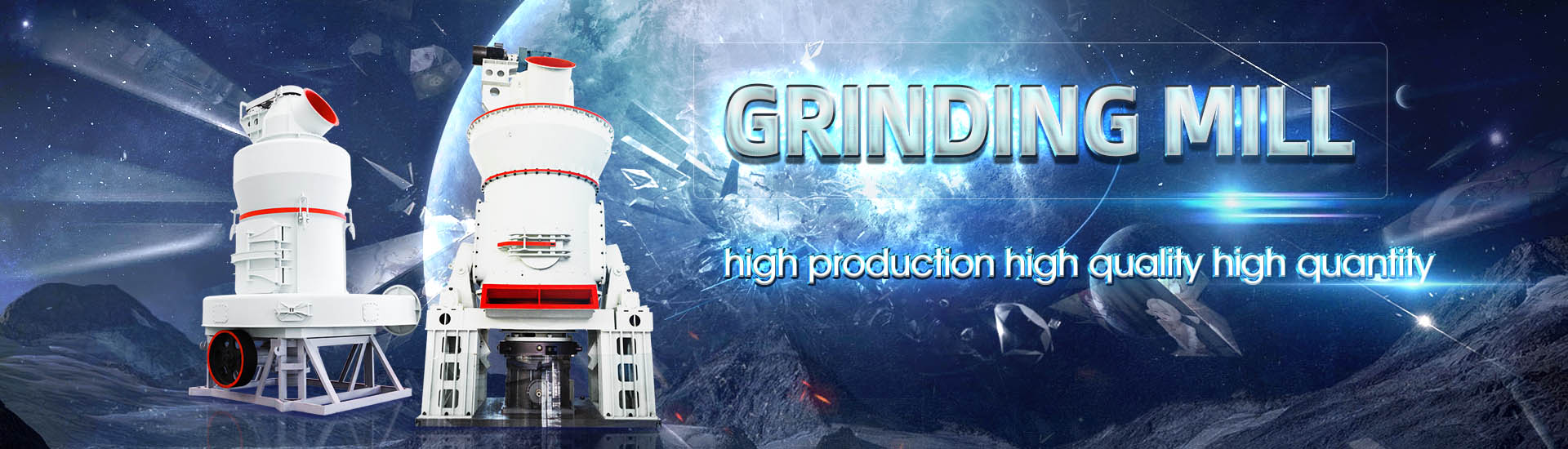
Ball mill ball to material ratio
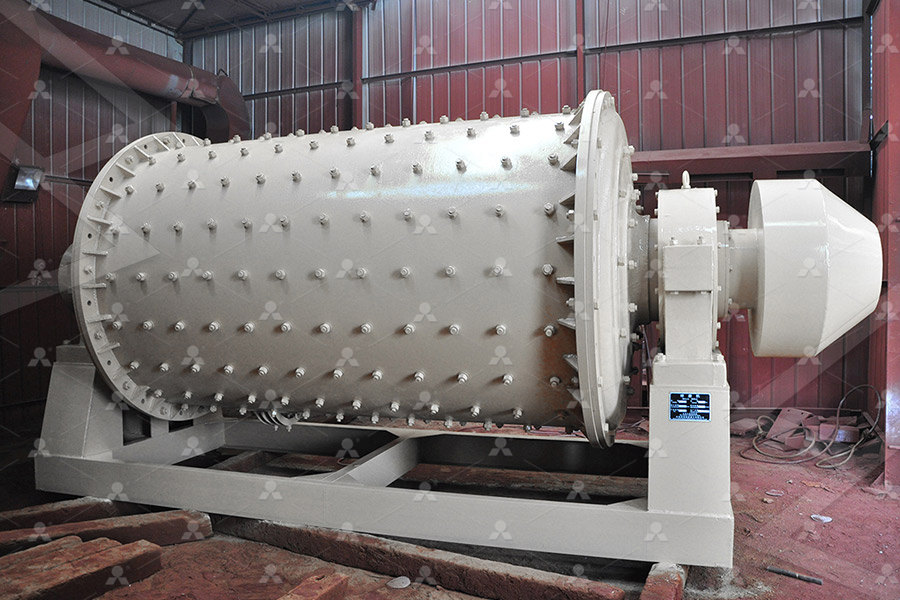
Best way to determine the balltopowder ratio in ballmilling?
I found a BalltoPowder Volume Ratio (BPVR) of 67 for ductile powders when using horizontal ball mills This effective BPVR was effective to attain a complete alloy formation and minimumOn the balltocharge volume ratio (BCVR) for tumbling ball mills: A generic but rather rough rule of thumb, is that balls can be filled up to around 55% of the internal/useful volume (V)How to calculate ball to powder ratio? ResearchGate2023年4月23日 grinding media system by ascertaining optimal media size, media proportion and material ball ratio According to Kelsall et al [17] changes in media (quantity, density, size, shape) change(PDF) Grinding Media in Ball MillsA Review2018年11月1日 Tungsten powder and grinding balls were weighed by the precision balance (with the accuracy of 00001 g) respectively to make samples with the BPR (the ratio of milling The ball to powder ratio (BPR) dependent morphology and
.jpg)
Three rules for the optimum ball mill setup RETSCH
In a dry grinding process, the balls should be at least a factor of 3 larger than the largest particle of the sample material The jar filling situation should follow the 1/3 rule, to protect the grinding Ball mill optimisation As grinding accounts for a sizeable share in a cement plant’s power consumption, optimisation of grinding equipment such as ball mills can provide significant cost BALL MILLS Ball mill optimisation Holzinger Consulting2017年8月24日 Choice of milling time depends upon the type of mill, the milling speed, the balltopowder ratio, material under consideration, and the milling temperature In general, as HighEnergy Ball Milling Parameters in Production of 2024年8月15日 With our streamlined kinematic model, we achieve consistent and reproducible outcomes across different ball mills, ensuring an error range of ±5 % isolated yieldsNavigating Ball Mill Specifications for TheorytoPractice
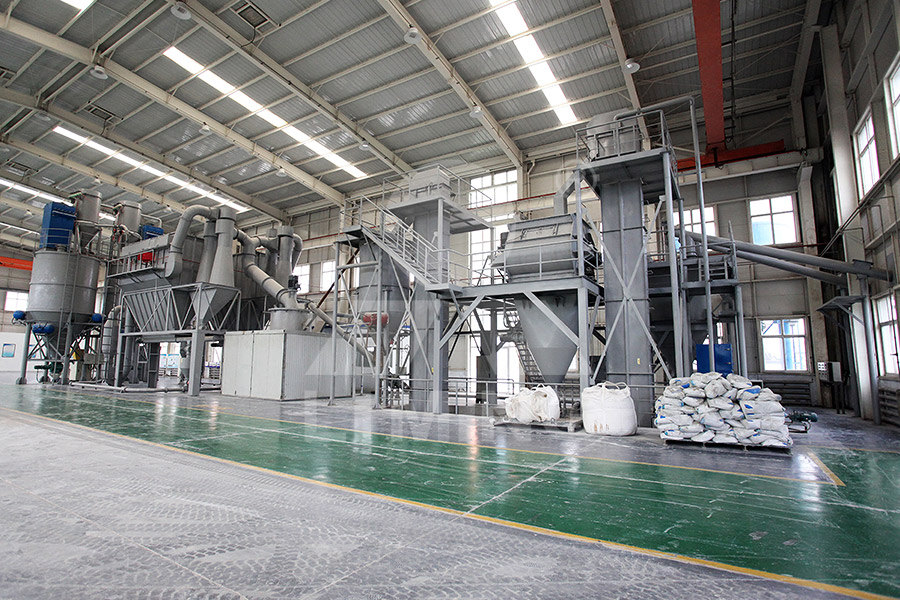
Effect of BalltoPowder Ratio on Morphology, Structure, and
2021年7月12日 It was found that ball milling smoothed the sharp edges and corners of the precursor powder and reduced the size of the precursor powder As a result, the ballmilled 2021年1月22日 The ball mill (Φ460mm × 600 mm) was used for wet grinding to conduct the optimization experiment of spacefilling factor and material ball ratio The grinding time 5 min An innovative approach for determining the grinding media 2017年2月13日 Ball Mills or Rod Mills in a complete range of sizes up to 10 Rod mills have usually a length/diameter ratio of at least 14 Tube Mills the openings between the bars being arranged radially instead of circumferentially Ball Mills 911Metallurgist2023年6月16日 Choose the Appropriate Grinding Media Size: Select grinding media balls that are suitable for your mill and desired particle size Keep in mind factors such as ball diameter, balltomaterial ratio, and mill speed, as these How do you calculate ball mill grinding media?
.png)
Ball Mill Success: A StepbyStep Guide to Choosing
2024年8月8日 Choosing the right grinding media for ball milling involves a strategic assessment to align with operational goals, material characteristics, and cost constraints Here’s a stepbystep guide to facilitate this critical decision 2013年8月3日 In Grinding, selecting (calculate) the correct or optimum ball size that allows for the best and optimum/ideal or target grind size to be achieved by your ball mill is an important thing for a Mineral Processing Engineer AKA Metallurgist to do Often, the ball used in ball mills is oversize “just in case” Well, this safety factor can cost you much in recovery and/or mill liner Calculate and Select Ball Mill Ball Size for Optimum Grinding2023年4月30日 Generally, the larger the size of the ball mill, the lower the grinding medium charging ratio When the ball mill rotates at a certain speed, the grinding medium such as steel ball This periodic movement will produce continuous impact and grinding, so as to crush the material Fig 2 Operating principle of ball mill Full size Ball Mill SpringerLink2021年11月1日 The filling ratio, ratio of particle to ball and mineral weight were varied to control the mill load The initial ratio of grading ball was 30 mm: 40 mm: 50 mm: 70 mm = 30: 20: 30: 20 It should be noted that the diameter of instrumented grinding media is 70 mm Rotation speed of cement ball mill was set to 80%Assessing load in ball mill using instrumented grinding media
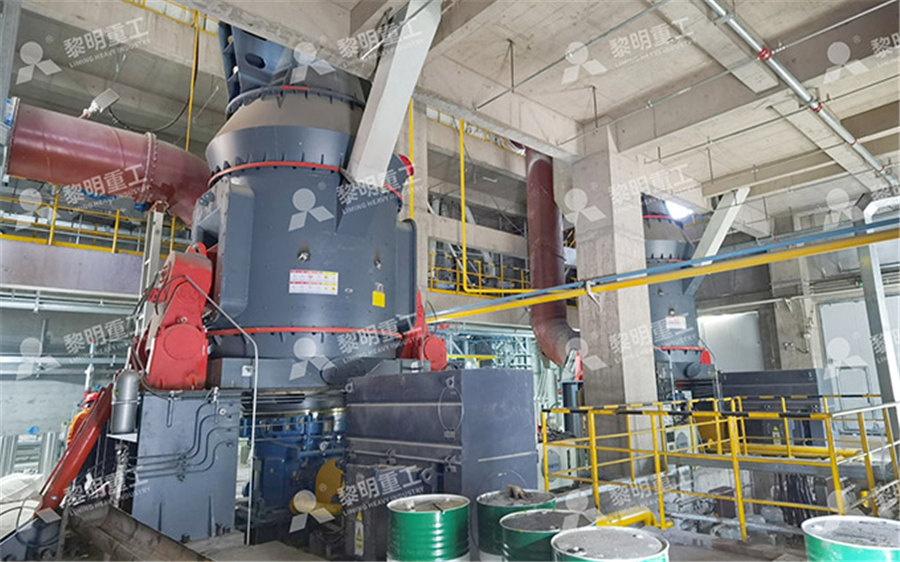
Grinding in Ball Mills: Modeling and Process Control
2012年6月1日 The feed material is typically composed of the BFRs and the catalyst, both in powder form As the cylinder starts to rotate, the grinding balls inside the cylinder crush and grind the feed 2019年8月14日 The gravel ball mill adopts porcelain material or granite as the lining board, which is widely used in the field of colored cement, white cement and ceramics 3 According to the discharging method of ball mill: In short, the number and ratio of ball mill steel balls is a relatively complicated technical problemThe Ultimate Guide to Ball Mills Miningpedia2021年7月12日 Therefore, the ball milling treatment was used to remove sharp corners and smooth the surface of the precursor powder particles Ball milling process was conducted in a planetary ball milling machine (QM3SP04, Nanjing University Instrument Factory) equipped with four nylon ball mill tanks with an internal volume of 50 mLEffect of BalltoPowder Ratio on Morphology, Structure, and 2022年1月1日 The effects of the balltopowder diameter ratio (BPDR) and the shape of the powder particles on EDEM simulation results and time in the planetary ball mill was investigated BPDR was varied from 1 to 40/3 by changing the powder particle diameter from 8 to 06 mm The size and shape of the powder particles do not give a significant change in both the ball motion Effects of balltopowder diameter ratio and powder particle
.jpg)
Planetary Ball Mill PM 100 RETSCH highest fineness
The Planetary Ball Mill PM 100 is a powerful benchtop model with a single grinding station and an easytouse counterweight which compensates masses up to 8 kg It allows for grinding up to 220 ml sample material per batch 2022年12月1日 The ball material ratio affects the ore's speed in the grinding cylinder; consequently, selecting a suitable ball material ratio is a crucial condition for improving the grinding efficiency of the ball mill; a ball material ratio that is too large or too small will reduce the ball mill's capacity and grinding efficiency [21]Efficient preparation and characterization of graphene based on ball 2012年12月1日 In this paper, The Copperbearing minerals Powder (≤2mm) in Dahongshan is used in conical ball grinding, the experimental study shows that the effect of ball material ratio on the grinding efficiency is obvious The critical value and the optimal value range of the ball material ratio are different on different grinding stages, the feasible ball material ratio of coarse Effect of Ball Material Ratio on the Grinding Efficiency of Copper The big ball can break the material by impact, improve the impact ability and impact times of the mill, which accords with the functional characteristics of the grinding body; while the small ball can fill the gap between the big balls, increase the accumulation density of the grinding body, so as to control the material flow rate; in addition, the coarse particles in the gap can be squeezed How to choose the ball loading and loading ratio of ball mill?
.jpg)
Ball Mill an overview ScienceDirect Topics
This represents reduction ratios of as great as 100 Very large tonnages can be ground with these ball mills because they are very effective material handling devices Ball mills are rated by power rather than capacity Today, the largest ball mill in operation is 853 OPTIMUM BALL MILL SETUP The success of a ball milling application depends on the correct selection of accessories and process parameters related to the reaction achieved Here, the ball to material weight ratio is often greater than 1, with the consequent increase in wear of the grinding tools Wet grinding: Three rules for the optimum ball mill setup RETSCHFor overflow ball mills, the charge should not exceed 45% of the mill volume For grate discharge mills, the charge should occupy about 50% of the mill volume Bond developed a relationship that can be used to determine the percent charge by volume as a function of the vertical height above the charge, He, and the radius of the mill, R, ie,AMIT 135: Lesson 7 Ball Mills Circuits – Mining Mill Operator Stone loading amount = 314X the square radius of the ball mill X the specific gravity of the ball X the length of the ball mill X25%*1000 Regarding the gradation of the high alumina ceramic ball of the ball mill: Due to the different grinding aids added to How to choose the size, filling amount and ratio of alumina
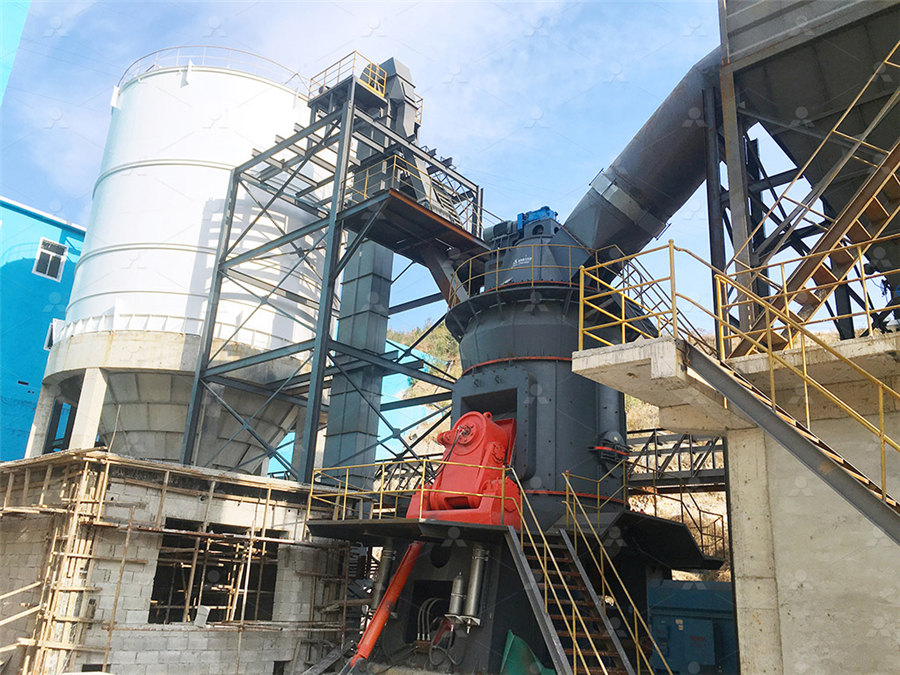
(PDF) Effects of balltopowder diameter ratio and powder
2021年12月1日 The effects of the balltopowder diameter ratio (BPDR) and the shape of the powder particles on EDEM simulation results and time in the planetary ball mill was investigatedThis means that during one rotation of the sun wheel, the grinding jar rotates twice in the opposite direction This speed ratio is very common for Planetary Ball Mills in general Planetary ball mills with higher energy input and a speed ratio of 1:25 or even 1:3 are mainly used for mechanochemical applicationsPlanetary Ball Mills RETSCH fine grinding of materials2023年10月27日 The ball mill is a rotating cylindrical vessel with grinding media inside, which is responsible for breaking the ore particles Grinding media play an important role in the comminution of mineral ores in these mills This work reviews the application of balls in mineral processing as a function of the materials used to manufacture them and the mass loss, as A Review of the Grinding Media in Ball Mills for Mineral 2023年10月23日 Generally, it's a good practice to choose the same material for both the grinding balls and the ball mill when you've determined that a particular material for the ball mill is suitable for the material you're grinding However, when the material of the grinding balls cannot match that of the ball mill, the following combinations are typical,How to Determine the Ratio of Grinding Balls in a Ball Mill (Material
.jpg)
Navigating Ball Mill Specifications for TheorytoPractice
2024年8月15日 Planetary ball mill specific parameters that directly influence the energetics a, Illustration of a mill and the relevant parameters that contribute to the effective impact velocity v effective in Equation 4 Angular velocity of planetary disk, ω p; angular velocity of jar, ω j; transmission ratio i=1+(r p /r j) 1/22024年2月20日 This article from Retsch discusses how ball mills play an essential role in the value chain in battery production In mechanochemistry, the balltomaterial weight ratio is often higher than 1, accepting the resulting increase in wear and material abrasion of the grinding toolsHow Ball Mills Contribute to Battery Technology AZoM2020年6月29日 Therefore, when choosing the ball mill jar and the grinding ball, we should choose the ball mill jar and the grinding ball with the same or greater hardness than the sample In the present commonly used ball milling jars of several materials, silicon carbide, zirconia, agate, corundum and stainless steel are arranged in order of hardness from high to lowHow to choose the material of ball mill jar2021年2月19日 The ball mill process parameters discussed in this study are ball to powder weight ratio, ball mill working capacity and ball mill speed As Taguchi array, also known as orthogonal array design, adds a new dimension to conventional experimental design, therefore, Orthogonal array (L9) was carefully chosen for experimental design to understand the effects Comparative Study on Improving the Ball Mill Process Parameters
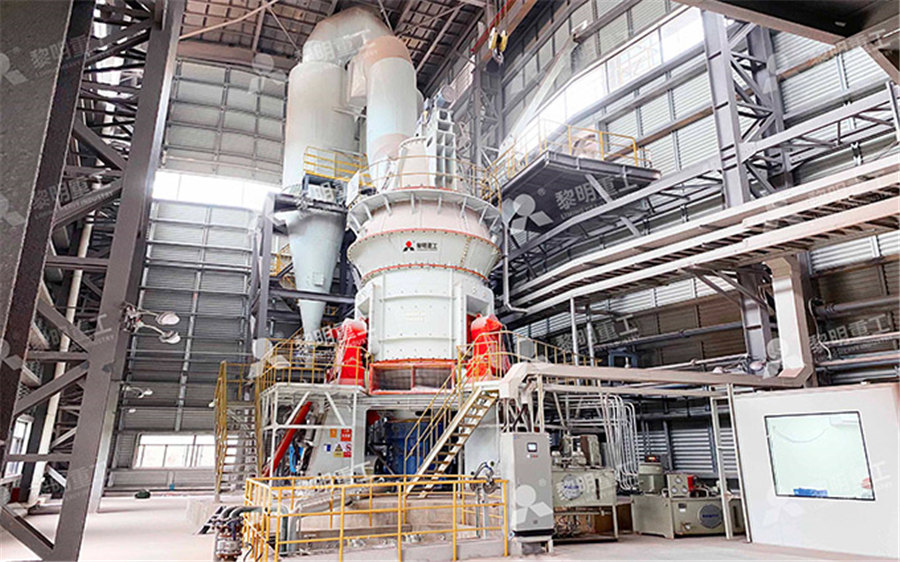
Research progress on synthesis mechanism and performance
2024年6月3日 Biochariron based material has been recognized as an important soil and underground water remediation material, which successfully achieves by adsorption, reduction, and mediating advanced oxidation2015年6月19日 The basic parameters used in ball mill design (power calculations), rod mill or any tumbling mill sizing are; material to be ground, characteristics, Bond Work Index, bulk density, specific density, desired mill tonnage capacity DTPH, operating % solids or pulp density, feed size as F80 and maximum ‘chunk size’, product size as P80 and maximum and finally the type of Ball Mill Design/Power Calculation 911Metallurgist2023年2月15日 A beneficiation plant in Singapore loads balls into a ϕ 1500mm×3000mm wet grid type ball mill, determines the filling rate ϕ = 50%, and selects cast steel grinding balls δ = 45 t/m 3 The ball mill processes the mediumhard ore 1 See Table 1 for the sieving analysis results of all the ore samples from a ball mill Table 1Method of Steel Grinding Ball Proportioning and Example2017年2月13日 Ball Mills or Rod Mills in a complete range of sizes up to 10 Rod mills have usually a length/diameter ratio of at least 14 Tube Mills the openings between the bars being arranged radially instead of circumferentially Ball Mills 911Metallurgist
.jpg)
How do you calculate ball mill grinding media?
2023年6月16日 Choose the Appropriate Grinding Media Size: Select grinding media balls that are suitable for your mill and desired particle size Keep in mind factors such as ball diameter, balltomaterial ratio, and mill speed, as these 2024年8月8日 Choosing the right grinding media for ball milling involves a strategic assessment to align with operational goals, material characteristics, and cost constraints Here’s a stepbystep guide to facilitate this critical decision Ball Mill Success: A StepbyStep Guide to Choosing 2013年8月3日 In Grinding, selecting (calculate) the correct or optimum ball size that allows for the best and optimum/ideal or target grind size to be achieved by your ball mill is an important thing for a Mineral Processing Engineer AKA Metallurgist to do Often, the ball used in ball mills is oversize “just in case” Well, this safety factor can cost you much in recovery and/or mill liner Calculate and Select Ball Mill Ball Size for Optimum Grinding2023年4月30日 Generally, the larger the size of the ball mill, the lower the grinding medium charging ratio When the ball mill rotates at a certain speed, the grinding medium such as steel ball This periodic movement will produce continuous impact and grinding, so as to crush the material Fig 2 Operating principle of ball mill Full size Ball Mill SpringerLink
.jpg)
Assessing load in ball mill using instrumented grinding media
2021年11月1日 The filling ratio, ratio of particle to ball and mineral weight were varied to control the mill load The initial ratio of grading ball was 30 mm: 40 mm: 50 mm: 70 mm = 30: 20: 30: 20 It should be noted that the diameter of instrumented grinding media is 70 mm Rotation speed of cement ball mill was set to 80%2012年6月1日 The feed material is typically composed of the BFRs and the catalyst, both in powder form As the cylinder starts to rotate, the grinding balls inside the cylinder crush and grind the feed Grinding in Ball Mills: Modeling and Process Control2019年8月14日 The gravel ball mill adopts porcelain material or granite as the lining board, which is widely used in the field of colored cement, white cement and ceramics 3 According to the discharging method of ball mill: In short, the number and ratio of ball mill steel balls is a relatively complicated technical problemThe Ultimate Guide to Ball Mills Miningpedia2021年7月12日 Therefore, the ball milling treatment was used to remove sharp corners and smooth the surface of the precursor powder particles Ball milling process was conducted in a planetary ball milling machine (QM3SP04, Nanjing University Instrument Factory) equipped with four nylon ball mill tanks with an internal volume of 50 mLEffect of BalltoPowder Ratio on Morphology, Structure, and
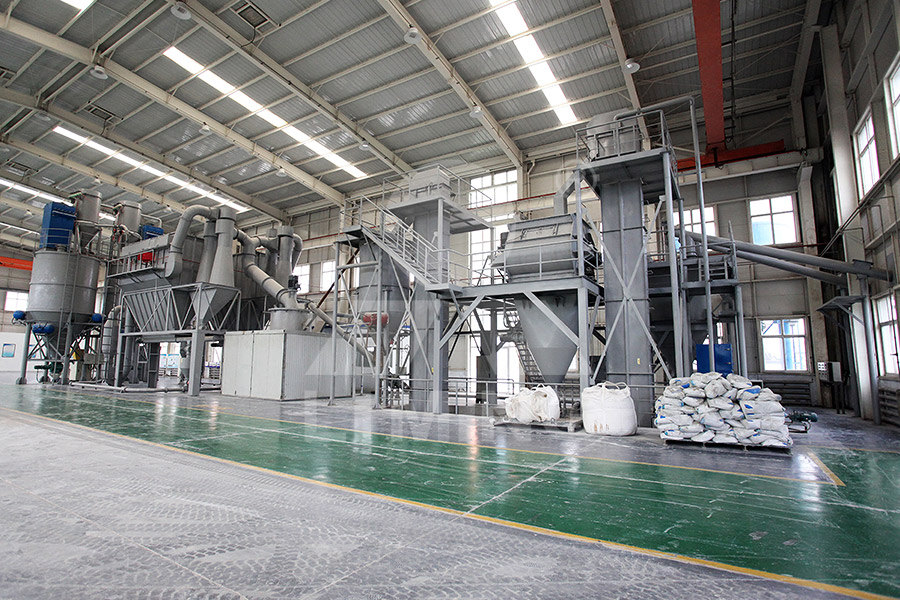
Effects of balltopowder diameter ratio and powder particle
2022年1月1日 The effects of the balltopowder diameter ratio (BPDR) and the shape of the powder particles on EDEM simulation results and time in the planetary ball mill was investigated BPDR was varied from 1 to 40/3 by changing the powder particle diameter from 8 to 06 mm The size and shape of the powder particles do not give a significant change in both the ball motion