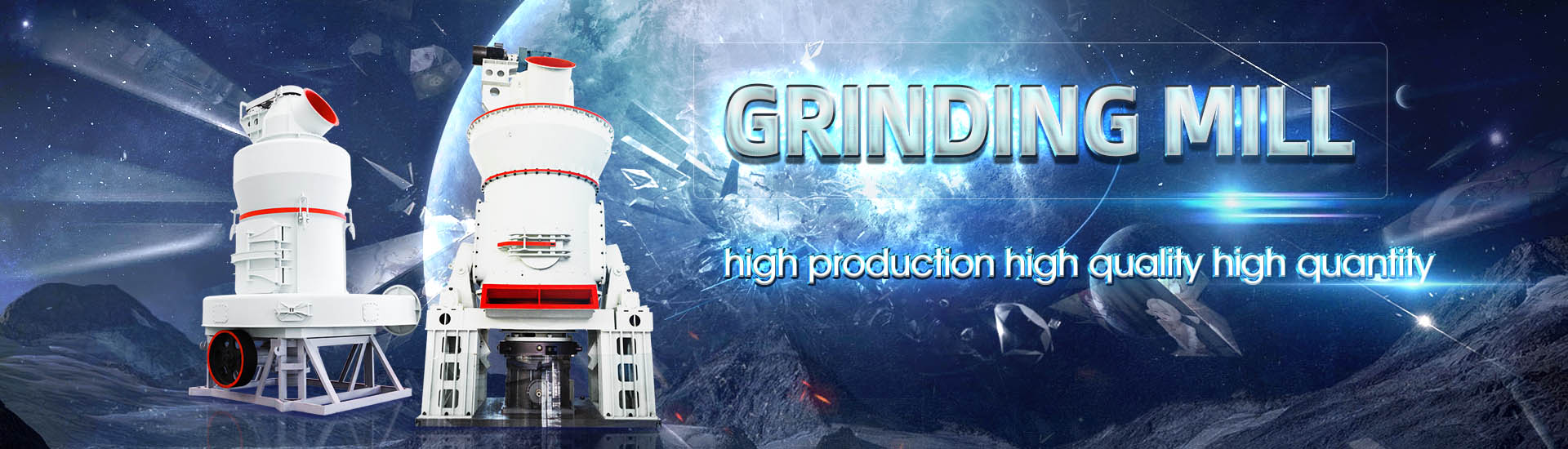
Tin slag refining furnace
.jpg)
Development of onestep process method to separate tin from tin
2023年6月1日 A novel onestep process for separating and recovering tin and copper from tinrefining sulfur slag via vacuum sulfidation and volatilization was developed and presented in 2019年6月18日 Slag produced as a byproduct in industrial processes, contains considerable metals contents, which need to be recovered to avoid environmental contamination In present review, the types,(PDF) Metallurgical Processing Strategies for Metals covery of tin from lowgrade concentrates could be achieved in one pass through the furnace, yielding a discardable slag whose tin content was so low as not to warrant further treatment Tin Smelting in Rotary Furnaces2017年8月21日 Extensive research has been conducted on the recovery of tin from tinbearing alloys, tin anode slime, Ewastes, tinbearing slag, tin middlings, and tinbearing iron Extraction and Separation of Tin from TinBearing Secondary
.jpg)
The metallurgy of tin smelting in a submergedarc furnace
At the Iscor (Vanderbijlpark) works, tin is smelted from a cassiterite concentrate in a submergedarc furnace with a power input of 350 kV A, the electrodes being amplidyne controlled The 2023年6月7日 The lowgrade tin ore generated during mineral processing can be processed in the fuming furnace together with the slag and lowgrade tin material, so as to recover the tin Tin Metallurgy SpringerLink2024年5月1日 Leading enterprises, such as Yunnan Tin Industry Co, Ltd (the world's largest in this sector), utilize electric furnaces to smelt As–Al slag, which produces Sn–As–Sb dust Clean and sustainable elimination of arsenic–aluminum slag from 2021年9月14日 Volatilization is an efficient way to recover tin from middlegrade tin materials, and the form of volatilized tin is SnO (g) in reduction roasting and SnS (g) in sulfuration roasting [12, 13] Carbothermic reduction smelting is The Recovery of Metallic Tin from an Industrial Tin
.jpg)
Advances in Tin Smelting in Yunnan Tin Corporation, China
Progress in tin smelting and process technology at the smelter of the Yunnan Tin Corporation is described together with practical experience in reverberatory furnace treatment of medium Chemical analysis of slag showed that slag contained about 22% Cu and 23% Sn Microscopic examinations of crosssections prepared from slag samples illustrated different structural properties (Giray et al, 1996; 1997) The reason for this was the stockpile, from where the sample was taken, was accumulated during different times of refiningDevelopment of a Flowsheet for Recovering Copper and Tin from 2022年12月10日 Fig 1 (a) shows that the sulfur slag is a black powder with uneven particles The main substances in the sulfur slag are tin, stannous sulfide and cuprous sulfide (Fig 1 (c))The distributions of Sn, Cu and S in the sulfur slag are clear in the scanning electron microscopy (SEM) results, as shown in Fig 1 (d)–(f) Most of the tin in the sulfur slag exists as Separation and recovery of tin and copper from tin refining sulfur slag 2023年6月7日 The lowgrade tin ore generated during mineral processing can be processed in the fuming furnace together with the slag and lowgrade tin material, so as to recover the tin metal Tin Smelting This includes three processes: presmelting treatment of tin concentrate, reduction smelting, and crude tin refining PreSmelting Treatment Tin Metallurgy SpringerLink
.jpg)
Separation and recovery of tin and copper from tin refining sulfur slag
2022年12月10日 Sulfur slag is a highvalue hazardous waste produced during the refining process of crude tin To reduce the emission of wastewater, harmful gas, and hazardous residue, a theoretical and experimental investigation was carried out to develop a new process for converting metal to metal sulfide that utilizes physical differences (saturated vapor pressure) 2024年5月1日 The culmination of this research has led to the development of key technologies aimed at reducing the source of As–Al slag in Sn refining, SchoolEnterprise Cooperation to Improve the Tin Smelting Process and Large Vacuum Furnace to Improve the Production Level (2023) Accessed 8th Dec 2023 Google Scholar Cited by Clean and sustainable elimination of arsenic–aluminum slag from 2024年1月1日 The lowgrade tin ore generated during mineral processing can be processed in the fuming furnace together with the slag and lowgrade tin material, so as to recover the tin metal Tin Smelting This includes three processes: presmelting treatment of tin concentrate, reduction smelting, and crude tin refining PreSmelting Treatment Tin Metallurgy SpringerLinkThe furnace has the function of melting, refining and casting The capacity can be minimal 1t/batch The furnace mainly consists of furnace body, supporting frame, driving device, refractories, heating and combustion, control system and refining system It uses LPG or LNG as fuel and refining agentRotary Reverberatory Furnace (Anode Furnace)Pyrometallurgy
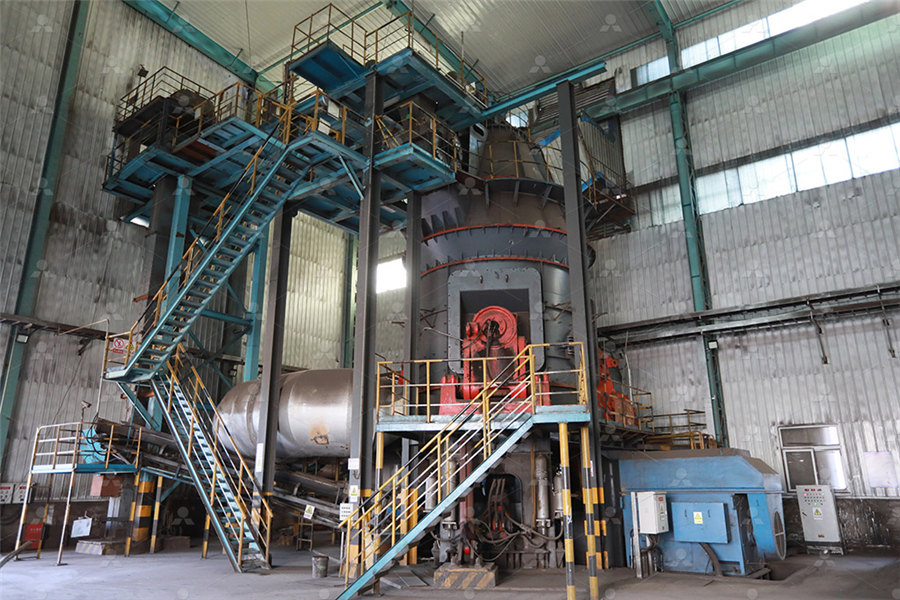
The metallurgy of tin smelting in a submergedarc furnace
off is returned to the furnace so that such losses are minimized The secondary slag, which has a tin content of 2 to 3 per cent, is sold for its (Nb, Ta)20s content, which depends on the source of the concentrate and the percentage concentration; these determine the volume of the slag Fig 4 shows the slag as a function of the tin in the2020年2月3日 In the 1970s, the Single Snorkel Refining Furnace (SSRF) was originally exploited through the reformation of RH to improve refining efficiency for small capacity ladle in China,[] and now it has been developed as a multifunctional vacuum refining equipment for the mass production of special steel[2,3] Subsequently, a similar degasser named Revolutionary Investigation of Circulation Flow and SlagMetal Behavior in an Progress in tin smelting and process technology at the smelter of the Yunnan Tin Corporation is described together with practical experience in reverberatory furnace treatment of mediumgrade concentrates By introducing a fuming process for treating rich slag in place of a blastfurnace process the separation of tin from iron has been solvedAdvances in Tin Smelting in Yunnan Tin Corporation, ChinaIn the current lead refining process, the tin oxidizes to slag, For that reason, the slag from the anode furnace is typically recycled to prior processing steps like the PierceSmith converter90924 PDFs Review articles in TIN ResearchGate
.jpg)
The Recovery of Metallic Tin from an Industrial Tin
2021年9月14日 Tin was recovered in metal from an industrial tinbearing byproduct containing Na2SO4 by carbothermic reduction smelting, and the effects of basicity (Na2O/SiO2), temperature, and reaction time on the recovery of tin 2021年6月23日 All the refining methods are classified into four main groups: 1 Metal–slag processes: In these processes, the less noble metal is oxidized and slagged offThis is commonly known as fire refining Removal of carbon, silicon, manganese, and phosphorus from pig iron during steelmaking falls under this categoryRefining SpringerLink2017年8月21日 The proven global tin reserves were reported to be approximately 47 million tons (Mts) in 2016, and among these resources, only approximately 22 Mts can be recovered economically The original tin deposits will be exhausted in several years, therefore, tinbearing secondary resources, such as tin alloy, tin anode slime, ewastes, tin slag and tinbearing Extraction and Separation of Tin from TinBearing Secondary reverberatory furnace, in copper, tin, and nickel production, a furnace used for smelting or refining in which the fuel is not in direct contact with the ore but heats it by a flame blown over it from another chamber In steelmaking, this process, now largely obsolete, is called the openhearth processThe heat passes over the hearth, in which the ore is placed, and then reverberates backReverberatory furnace Smelting, Refining, Alloying Britannica
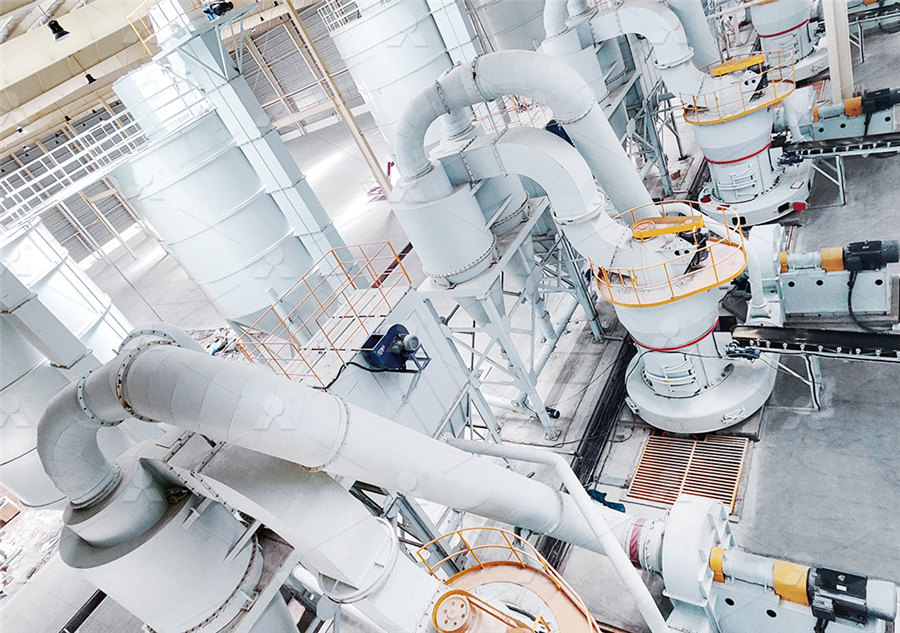
Tin Smelting and Refining in The People's Republic of China
pyrites to provide sulfur for tin fuming The slag, granulated at the smelting furnace, is melted in a reverberatory furnace from which it can be tapped to fill either of the fuming furnaces, as required The slag from the fuming plant assays 01% tin content A larger fuming furnace using modi2013年6月10日 Larger furnaces are suited to foundries specialising in the smelting of drosses and similar materials Monometer’s copper refining rotary furnaces offer the highest possible purity refining of any fire refining technology, achieving up to 999% purity from scraps such as Birch/Cliff Cycle times are typically under 5 hours for a 5 tonne chargeMonometer Copper and Tin Recovery and Refining Rotary Furnaces2011年10月26日 Steel slag is a byproduct of the steelmaking and steel refining processes This paper provides an overview of the different types of steel slag that are generated from basicoxygenfurnace (BOF) steelmaking, electricarcfurnace (EAF) steelmaking, and ladlefurnace steel refining processesChemical, Mineralogical, and Morphological Properties of Steel Slag Title of Publication Edited by TMS (The Minerals, Metals Materials Society), Year Pyrometallurgical Refining of Copper in an Anode Furnace H Antrekowitsch1, C Wenzl1, I Filzwieser2, D Offenthaler2 1 ChristianDopplerLaboratory for Secondary Metallurgy of Nonferrous Metals FranzJosefStraße 18; Leoben, 8700, Austria 2 Department of Nonferrous Pyrometallurgical Refining of Copper in an Anode Furnace
.jpg)
Physical and chemical characteristics of slag produced during Pb
2020年10月13日 Metallurgical waste originating from the Zn and Pb refining process presents varying chemical composition and physical properties and contains varying quantities of pollutants In the study, both fresh and weathered samples of production slag from the final Pb refining process were used to determine its physical parameters and chemical composition as 7 The crude tin from the first furnace is placed in a lowtemperature furnace along with the crude tin recovered from the slag plus the hard head Because tin has a melting temperature much lower than most metals, it is possible to carefully raise the temperature of the furnace so that only the tin melts, leaving any other metals as solidsHow tin is made material, used, processing, steps, product, Extraction of tin consists of three parts, ie tin ore concentration, smelting and refining Cassiterite is the main source of tin ore, with specific gravity of 687g/cm 3, density larger than most of gangueTherefore, 90% of tin concentrate is Extraction of Tin/ StannumTin Metalcess2023年10月20日 The main impurities found in copper scrap are lead, tin, zinc, copper feeds at existing smelting operations was performed in a Pierce–Smith converter and/or anode refining furnace that after up to 9 months in operation the bulk of the refractory block remained unimpregnated by any slag from the anode refining processRecycling Alumina–Chrome Refractory Brick from ScrapRefining

African Furnaces, Smelting, Refining, and Smithing
2021年12月29日 The results indicate that over the last 1500 years, there has been technological change in iron smelting techniques in terms of furnace charging platform, slagpit provision, slag tapping, use of 2015年12月28日 T R A Davey is a professor of metallurgical engineering at Colorado School of Mines, and president of the consulting firm Metacol, Inc He has degrees in science, metallurgical engineering, and applied science from the University of Melbourne, and has worked in industrial R D in Australia, Germany, and EnglandTin Smelting in Rotary Furnaces JOMtogether with scrap in a refining furnace The refined copper is transferred to the anode furnace, where it is deoxidized and cast into copper anodes The slag from the refining furnace is treated in the TBRC slag furnaces where crude Pb/Sn alloy is generated The Pb/Sn alloy is further processed for tin and lead refiningLife Cycle Assessment of Aurubis Tin2019年12月1日 An Assessment of Ladle Furnace Steelmaking The effect of gas stirring on refining reactions and inclusion removal was assessed The slag–metal interactions were examined at every (PDF) An Assessment of Ladle Furnace Steelmaking Reactions in
.jpg)
A Review of Slag Refining of Silicon Alloys JOM
2020年11月19日 Slag refining of silicon has been modified in recent years by combining the process with solvent refining, in which an alloy of silicon is first treated by slag and then solidified under controlled conditions to yield highpurity silicon crystals This paper discusses the effect of alloying elements on the efficiency of slag treatment A set of criteria are established and 2005年1月1日 In order to improve the metal/slag reactions as well as the volatilisation by selective oxidation in the anode furnace, the behaviour of the most important accompanying elements (eg nickel, tin Pyrometallurgical Refining of Copper in an Anode FurnaceChemical analysis of slag showed that slag contained about 22% Cu and 23% Sn Microscopic examinations of crosssections prepared from slag samples illustrated different structural properties (Giray et al, 1996; 1997) The reason for this was the stockpile, from where the sample was taken, was accumulated during different times of refiningDevelopment of a Flowsheet for Recovering Copper and Tin from 2022年12月10日 Fig 1 (a) shows that the sulfur slag is a black powder with uneven particles The main substances in the sulfur slag are tin, stannous sulfide and cuprous sulfide (Fig 1 (c))The distributions of Sn, Cu and S in the sulfur slag are clear in the scanning electron microscopy (SEM) results, as shown in Fig 1 (d)–(f) Most of the tin in the sulfur slag exists as Separation and recovery of tin and copper from tin refining sulfur slag

Tin Metallurgy SpringerLink
2023年6月7日 The lowgrade tin ore generated during mineral processing can be processed in the fuming furnace together with the slag and lowgrade tin material, so as to recover the tin metal Tin Smelting This includes three processes: presmelting treatment of tin concentrate, reduction smelting, and crude tin refining PreSmelting Treatment 2022年12月10日 Sulfur slag is a highvalue hazardous waste produced during the refining process of crude tin To reduce the emission of wastewater, harmful gas, and hazardous residue, a theoretical and experimental investigation was carried out to develop a new process for converting metal to metal sulfide that utilizes physical differences (saturated vapor pressure) Separation and recovery of tin and copper from tin refining sulfur slag 2024年5月1日 The culmination of this research has led to the development of key technologies aimed at reducing the source of As–Al slag in Sn refining, SchoolEnterprise Cooperation to Improve the Tin Smelting Process and Large Vacuum Furnace to Improve the Production Level (2023) Accessed 8th Dec 2023 Google Scholar Cited by Clean and sustainable elimination of arsenic–aluminum slag from 2024年1月1日 The lowgrade tin ore generated during mineral processing can be processed in the fuming furnace together with the slag and lowgrade tin material, so as to recover the tin metal Tin Smelting This includes three processes: presmelting treatment of tin concentrate, reduction smelting, and crude tin refining PreSmelting Treatment Tin Metallurgy SpringerLink
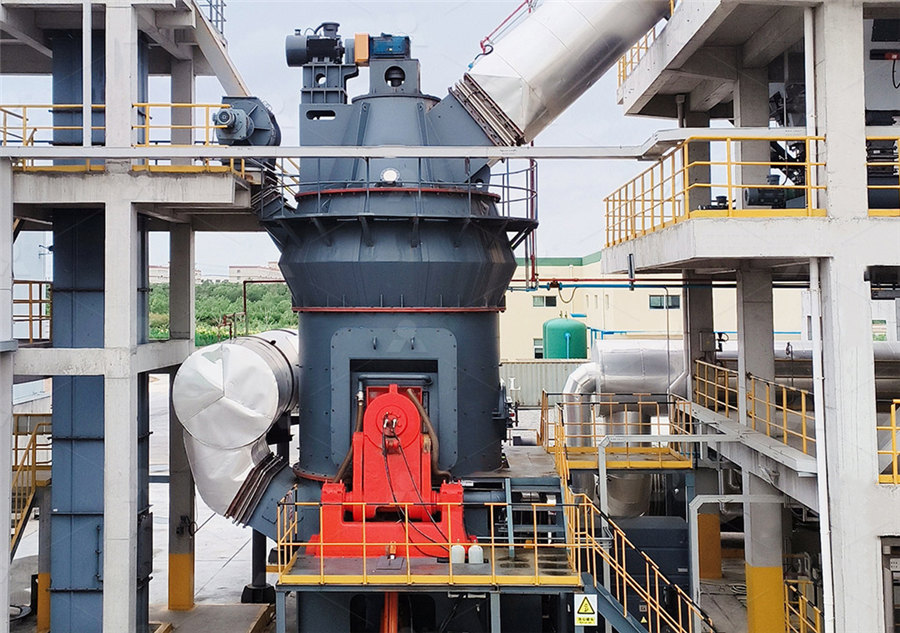
Rotary Reverberatory Furnace (Anode Furnace)Pyrometallurgy
The furnace has the function of melting, refining and casting The capacity can be minimal 1t/batch The furnace mainly consists of furnace body, supporting frame, driving device, refractories, heating and combustion, control system and refining system It uses LPG or LNG as fuel and refining agentoff is returned to the furnace so that such losses are minimized The secondary slag, which has a tin content of 2 to 3 per cent, is sold for its (Nb, Ta)20s content, which depends on the source of the concentrate and the percentage concentration; these determine the volume of the slag Fig 4 shows the slag as a function of the tin in theThe metallurgy of tin smelting in a submergedarc furnace2020年2月3日 In the 1970s, the Single Snorkel Refining Furnace (SSRF) was originally exploited through the reformation of RH to improve refining efficiency for small capacity ladle in China,[] and now it has been developed as a multifunctional vacuum refining equipment for the mass production of special steel[2,3] Subsequently, a similar degasser named Revolutionary Investigation of Circulation Flow and SlagMetal Behavior in an Progress in tin smelting and process technology at the smelter of the Yunnan Tin Corporation is described together with practical experience in reverberatory furnace treatment of mediumgrade concentrates By introducing a fuming process for treating rich slag in place of a blastfurnace process the separation of tin from iron has been solvedAdvances in Tin Smelting in Yunnan Tin Corporation, China