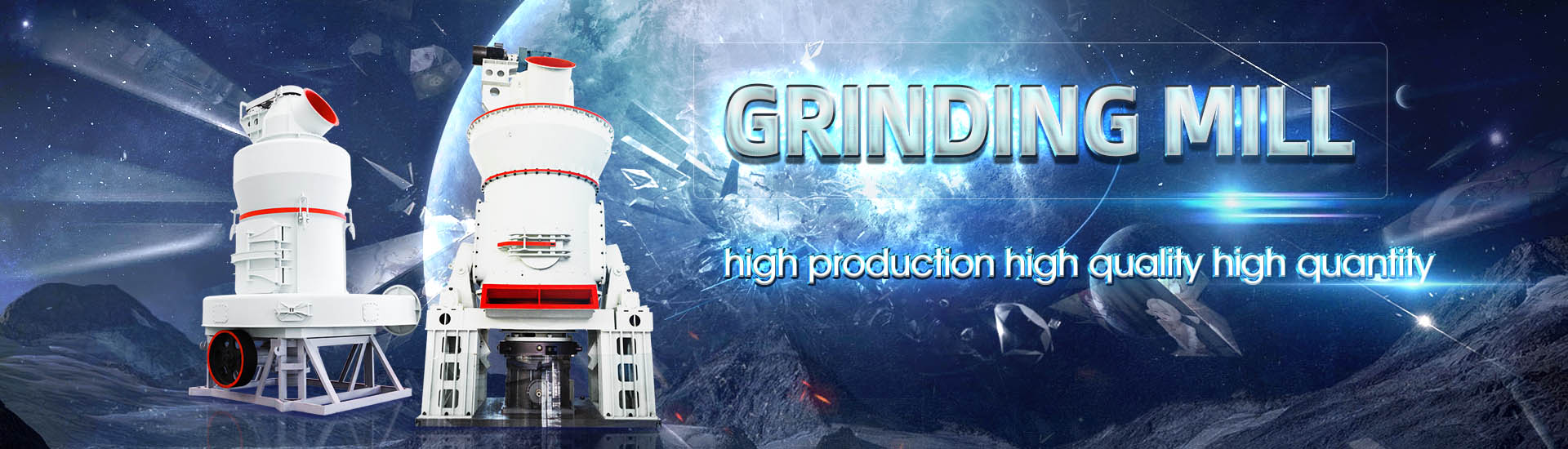
Ore mill outlet particle size ampgt50mm
.jpg)
A comparative study on a newly designed ball mill and the
2020年1月1日 Based on the particle size analysis data, the size above +150 µm was considered as a recirculating load to the mill, the particle size range in −150 µm/+10 µm was considered 2017年9月1日 The objective of this work is to assess the influence of fine grinding in ball mills and stirred mills on valuable mineral liberation and particle shape characteristics of UG2 ore, a Fine grinding: How mill type affects particle shape characteristics 2018年6月1日 In this article, alternative forms of optimizing the milling efficiency of a laboratory scale ball mill by varying the grinding media size distribution and the feed material particle size Effect of ball and feed particle size distribution on the milling 2024年1月1日 The main parameters of grinding and classification process include measurement of millfeeding quantity, mill load measurement, measurement of ore slurry density, Online Measurement and Control for Ore Grinding and Classification
.jpg)
Ore Grinding SpringerLink
2023年7月20日 According to the particle sizes of grinding products, the grinding process is divided into coarse grinding, medium grinding, fine grinding, microfine grinding, and ultrafine 2023年10月27日 Ball sizes that are used in grinding should be large enough to break the largest and hardest ore particles Optimal ball sizes depend on the feed/product size ratio, mill A Review of the Grinding Media in Ball Mills for Mineral Processing simple and novel nonlinear model of a runofmine ore grinding mill circuit, developed for process control and estimation purposes, is validated The model makes use of the minimum number Analysis and validation of a runofmine ore grinding mill circuit 2020年1月3日 Ball mills are progressively used to grind the ores for particle size reduction and to liberate valuable minerals from the ores The grinding of ore is a highly energyintensive Estimation of Grinding Time for Desired Particle Size Distribution
.jpg)
Mining and Minerals Particle Size Analysis Omec
Minerals and Mining Particle Size Analyzers Particle size is critical in mineral grinding, where the target is to reduce the particle size of mined ore sufficiently to enable liberation of the mineral 2021年12月11日 To solve the problem in the precise measurement of grinding ball diameters, this paper carried out magnetite grinding experiments with grinding balls of different diameters The Effect of Grinding Media on Mineral Breakage Properties of intensive process [1–4] In this process, the size of the particle obtained depends on the energy consumption of the ball mill The major challenge encountered in the process of iron ore grinding is to maintain the desired product particle size distribution (PSD) with sufficient liberation of valuable minerals The demand for desiredEstimation of Grinding Time for Desired Particle Size Distribution2018年10月8日 For this purpose, six samples (pure calcite, pure magnetite, pure quartz, marmarite rock, travertine rock, and copper ore) with identical particle size distribution were comminuted by HPGR at (PDF) Iron Ore Concentrate Particle Size Controlling
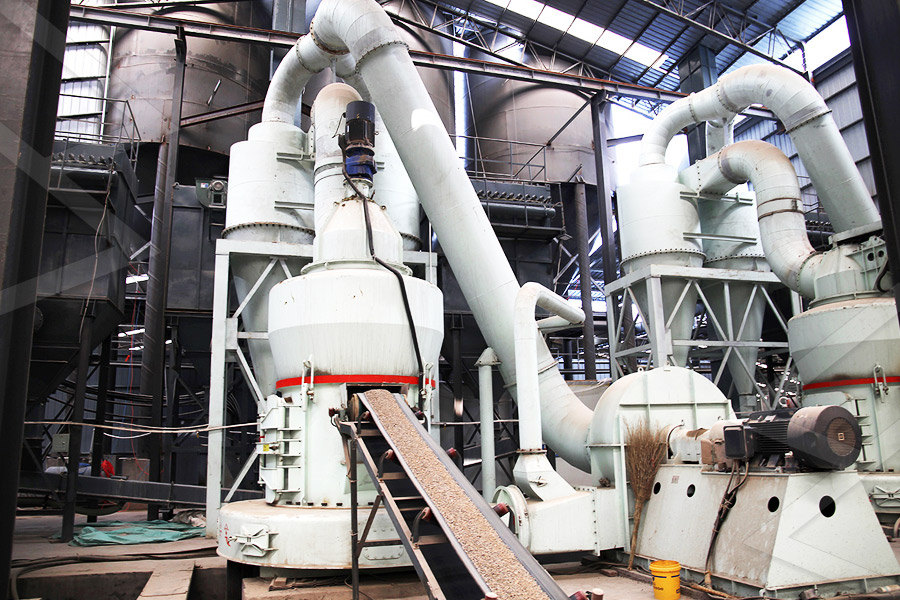
(PDF) Estimation of Grinding Time for Desired Particle Size
Comminution Characterization studies 1 Introduction Ball mills are progressively used to grind the ores for particle size reduction and to liberate valuable minerals from the ores The grinding of ore is a highly energyintensive process [1–4] In this process, the size of the particle obtained depends on the energy consumption of the ball mill2014年4月19日 DOI: 105277/PPMP Corpus ID: ; Investigation on the particle size and shape of iron ore pellet feed using ball mill and HPGR grinding methods @article{Abazarpoor2014InvestigationOT, title={Investigation on the particle size and shape of iron ore pellet feed using ball mill and HPGR grinding methods}, author={Armin Abazarpoor Investigation on the particle size and shape of iron ore pellet 2016年11月25日 An effect of a grinding method, that is ball mill and high pressure grinding rolls (HPGR), on the particle size, specific surface area and particle shape of an iron ore concentrate was studiedOptimization of Particle Size and Specific Surface Area of Pellet 2013年6月1日 Thus, it was established that Itakpe iron ore is best processed using PAX at pH 11 and particle size of 125 µm yielding concentrates assaying 6766% Fe2O3 at a recovery of ~90% while for Agbaja Effect of particles size range on iron ore flotation ResearchGate
.jpg)
Dual particle filters for state and parameter estimation with
2012年4月1日 Request PDF Dual particle filters for state and parameter estimation with application to a runofmine ore mill Measurements are not readily available for grinding mills owing to the nature of Its performance evaluation gave 400kg/h throughput, 96% crushing efficiency and 96% efficiency based on the required particle size The average particle size of flour obtained was 236μm using Self similar distribution of hammer mill product size for iron ore 2020年8月12日 As one of the three major forces of coal mills, the grinding force exerts a significant impact on the working process of coal mills and parameters like mill current and outlet temperatureAn investigation of performance characteristics and energetic 2013年4月1日 Two types of mills commonly found in the minerals processing industry are ball and semiautogenous (SAG) mills, which use both ore and steel balls as grinding media (Wei and Craig, 2009b)In the case of a ball mill the ore is crushed before it enters the mill, whereas a SAG mill receives runofmine (ROM) ore directly (Stanley, 1987)A SAG mill in a singlestage Analysis and validation of a runofmine ore grinding mill circuit
.jpg)
Effect of ball and feed particle size distribution on the milling
Effect of ball and feed particle size distribution on the milling efficiency of a ball mill: An attainable region approach N Hlabangana a, G Danha b, *, E Muzenda b a Department of Chemical Engineering, National University of Science and Technology, P O Box AC 939, Ascot Bulawayo, Zimbabwe b Department of Chemical, Materials and Metallurgical Engineering, College of 2017年9月30日 The ore particle size distribution is an important basis for the evaluation of crushing effect The particle size parameters mainly include the particle area, perimeter, equivalent diameter, shape factor and so on In order to obtain the ore particle size distribution, we mainly study the following aspects: (1)Research of Ore Particle Size Detection Based on Image Processing–5 – Data Presentations The initial output and presentation of 31 particle size classes may be displayed in a wide variety of formats; typical outputs will be shown laterUltrasonic extinction for full concentration, real time particle size PDF On Nov 15, 2019, B Foggiatto and others published Material handling and flowsheet selection considerations for particlebased ore sorting Find, read and cite all the research you need on Material handling and flowsheet selection considerations for particle
.jpg)
Analysis and validation of a runofmine ore grinding mill circuit
PSE product particle size [%] LOAD volume of charge within the mill [m3] SVOL volume of slurry in sump [m3] CFD cyclone feed density [t/m3] mill can be discharged either by over ow or through a discharge screen In the case of the screen, the particle size of the discharged slurry from the mill is limited by the aperture size of the screenSince this is the amount that would pass through a hypothetical sieve of mesh size x, this type of particle size distribution is also called "percent passing Occasionally, the fractions are also summed starting from the largest particle size The resulting particle size distribution is a curve that drops from 100% to 0%Particle Size Distribution: Particle Analyzers MICROTRAC2018年1月1日 Study on Sumbawa gold ore liberation using rod mill: effect of rodnumber and rotational speed on particle size distribution January 2018 IOP Conference Series Materials Science and Engineering Study on Sumbawa gold ore liberation using rod mill: effect of Iron ore particle size distribution 025, and 03 and κ mbgr on the impact effect of load and the drive power of the mill during the dry grinding of iron ore was numerically, Iron ore particle size distribution Download Scientific Diagram
.jpg)
The Ultimate Guide to Ball Mills Miningpedia
2019年8月14日 • Central discharge ball mill: the inlet of medium unloading ball mill is at both ends, and the outlet is in the middle of the ball mill 4 because it is necessary to grind the ore to a suitable selected particle size before extract highgrade concentrate from the oreMori6 *has more recently studied a circulating The fluid eners mill offers a simple and rapid type of F E mill (“JetoMizef) and has shown that grinding takes place in the jet stream in the means for reducing the particle size of poxiders to the bsieve range, free from many of the problems vicinity of the nozzle He has also presented Particle Size Reduction in a Fluid Energy Mill AcademiaPellet feed; HPGR; particle shape; particle size; image analysis; factorial design Introduction Iron ore pellet feed typically needs a size less than 106 µm after fine grinding Magnetic and HPGR effect on the particle size and shape of iron ore pellet feed 2020年5月28日 The feed samples of X, Y, and Z iron ores were ground in the BBM (ball mill refers to a BBM of size 300 mm × 300 mm with smooth liners) to identify the PSD, BWI, and RT of each ore Grinding experiments were Investigation on Iron Ore Grinding based on Particle
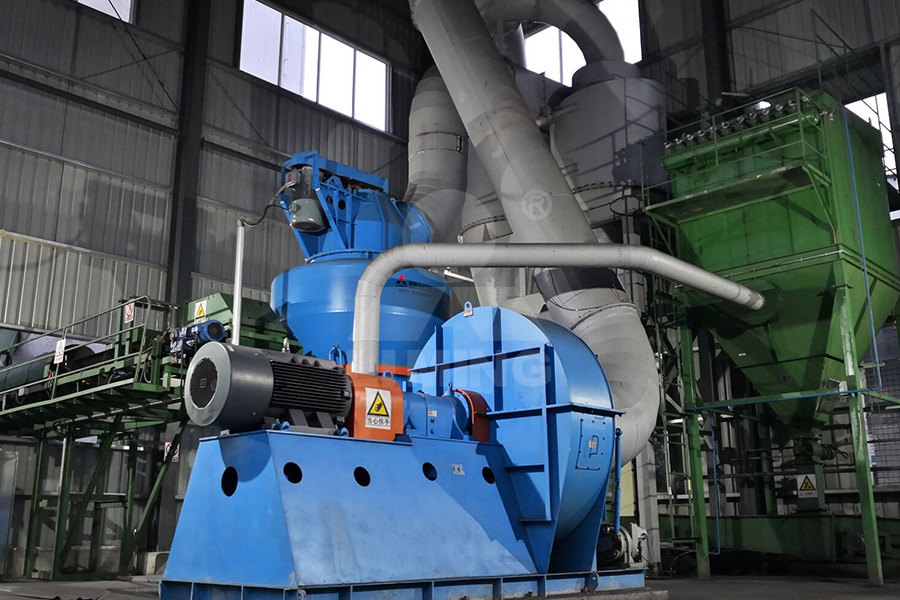
Ore Particle Size SpringerLink
2024年1月1日 A certain division method (ie, screening) is used to divide the broken ore particle group with a wide range of particle size into several grades with narrow particle sizes, and these grades are called grade sizes, with the upper limit size d 1 and lower limit size d 2 of particle in grade size as indication, such as d 1 − d 2, d 1 + d 2, d 2 − d 1, etcPlease use one of the following formats to cite this article in your essay, paper or report: APA Sympatec GmbH (2023, May 15) Monitoring of Grain Size and Concentration in Ore SlurriesMonitoring of Grain Size and Concentration in Ore SlurriesSamples the samples were crushed to 4 mm in jaw and roll crushers and ground in a laboratory rod mill The particle size analysis of ground ore samples was performed by laser particle size Particle size analysis of ore samples ResearchGateThe shape of crushed ore affects the product particle size in a ball mill grinding circuit It has also been proposed that green pellet quality is directly related to the amount of fine particles in a pelletizing plant (Dwarapudi et al, 2008; Umadevi et al, 2008; Gul et al, 2014; Van der Meer, 2015) Particle size distributionInvestigation on the particle size and shape of iron ore pellet feed
.jpg)
Investigation of iron ore particle size and shape on green pellet
2020年2月20日 ABSTRACT Particle size and shape of iron ore concentrate are effective parameters in the production of quality green pellets In this research, the effect of particle morphology on green pellet quality was studied It was concluded that pellet quality improved with increasing specific surface area Drop number and green compression strength of pellets 2021年1月22日 Request PDF Impact of ball filling rate and stirrer tip speed on milling iron ore by wet stirred mill: Analysis and prediction of the particle size distribution Impact of ball filling rate and stirrer tip speed on milling iron ore The basic working principles of a jet mill Micronization is a term used to describe size reduction where the resulting particlesize distribution is less than 10 microns Jet mills are used for Gypsum, Graphite, Mica, Talc, Tentalum ore Paints Carbon black, Fluorescent pigment, Titanium dioxide Pharmaceuticals Amino Acid HOW IT WORKS2013年8月3日 In Grinding, selecting (calculate) the correct or optimum ball size that allows for the best and optimum/ideal or target grind size to be achieved by your ball mill is an important thing for a Mineral Processing Engineer AKA Metallurgist to do Often, the ball used in ball mills is oversize “just in case” Well, this safety factor can cost you much in recovery and/or mill liner Calculate and Select Ball Mill Ball Size for Optimum Grinding
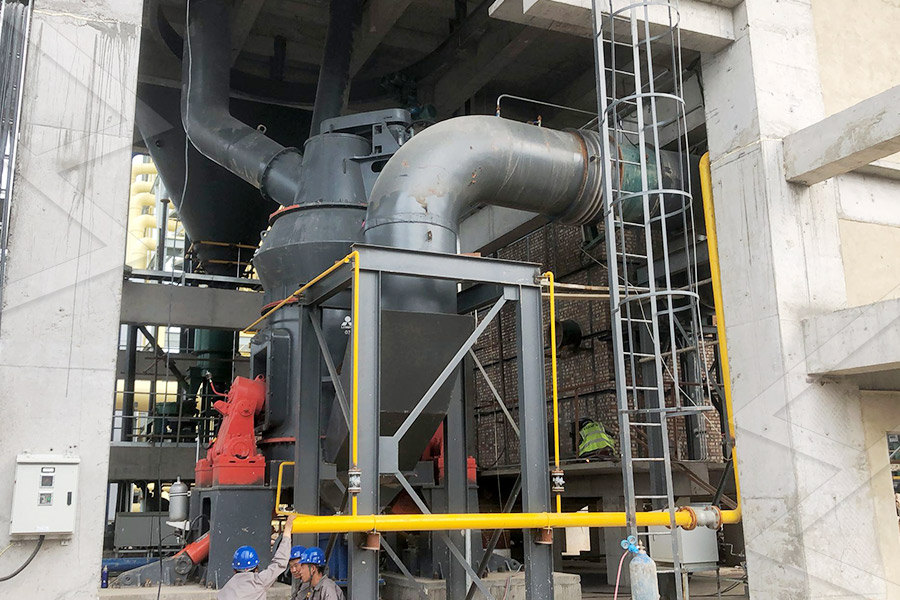
Estimation of Grinding Time for Desired Particle Size Distribution
intensive process [1–4] In this process, the size of the particle obtained depends on the energy consumption of the ball mill The major challenge encountered in the process of iron ore grinding is to maintain the desired product particle size distribution (PSD) with sufficient liberation of valuable minerals The demand for desired2018年10月8日 For this purpose, six samples (pure calcite, pure magnetite, pure quartz, marmarite rock, travertine rock, and copper ore) with identical particle size distribution were comminuted by HPGR at (PDF) Iron Ore Concentrate Particle Size Controlling Comminution Characterization studies 1 Introduction Ball mills are progressively used to grind the ores for particle size reduction and to liberate valuable minerals from the ores The grinding of ore is a highly energyintensive process [1–4] In this process, the size of the particle obtained depends on the energy consumption of the ball mill(PDF) Estimation of Grinding Time for Desired Particle Size 2014年4月19日 DOI: 105277/PPMP Corpus ID: ; Investigation on the particle size and shape of iron ore pellet feed using ball mill and HPGR grinding methods @article{Abazarpoor2014InvestigationOT, title={Investigation on the particle size and shape of iron ore pellet feed using ball mill and HPGR grinding methods}, author={Armin Abazarpoor Investigation on the particle size and shape of iron ore pellet
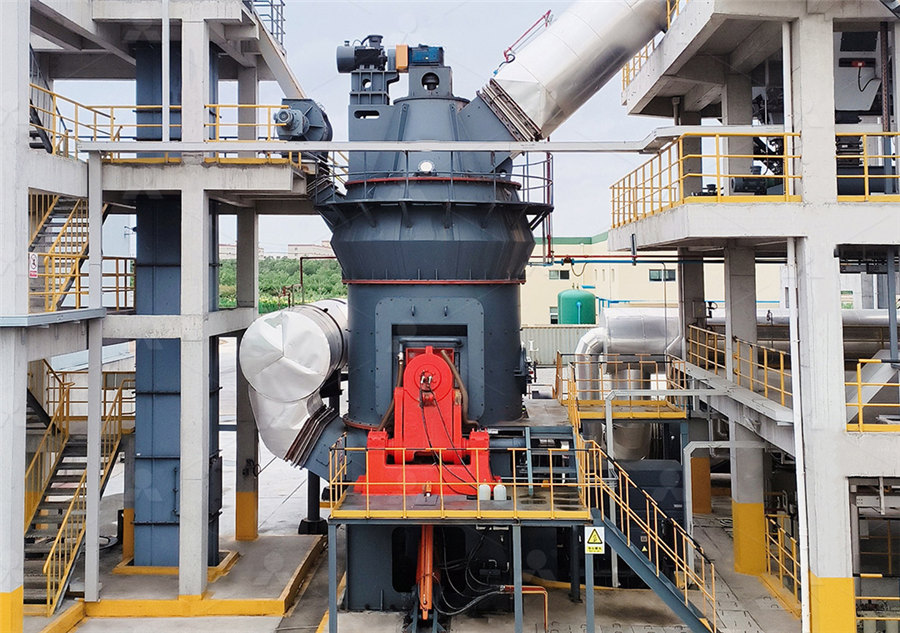
Optimization of Particle Size and Specific Surface Area of Pellet
2016年11月25日 An effect of a grinding method, that is ball mill and high pressure grinding rolls (HPGR), on the particle size, specific surface area and particle shape of an iron ore concentrate was studied2013年6月1日 Thus, it was established that Itakpe iron ore is best processed using PAX at pH 11 and particle size of 125 µm yielding concentrates assaying 6766% Fe2O3 at a recovery of ~90% while for Agbaja Effect of particles size range on iron ore flotation ResearchGate2012年4月1日 Request PDF Dual particle filters for state and parameter estimation with application to a runofmine ore mill Measurements are not readily available for grinding mills owing to the nature of Dual particle filters for state and parameter estimation with Its performance evaluation gave 400kg/h throughput, 96% crushing efficiency and 96% efficiency based on the required particle size The average particle size of flour obtained was 236μm using Self similar distribution of hammer mill product size for iron ore
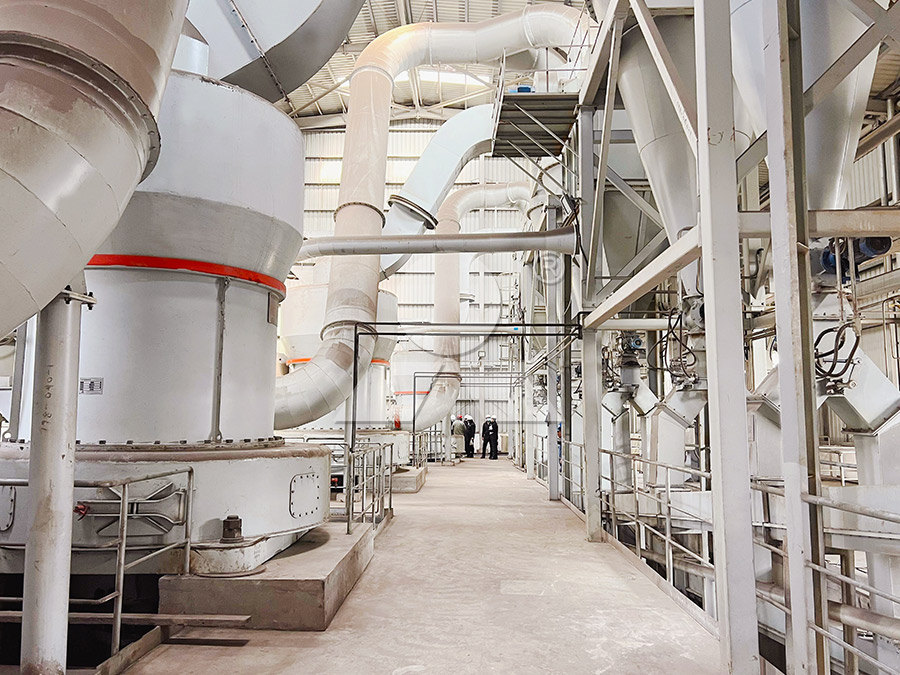
An investigation of performance characteristics and energetic
2020年8月12日 As one of the three major forces of coal mills, the grinding force exerts a significant impact on the working process of coal mills and parameters like mill current and outlet temperature2013年4月1日 Two types of mills commonly found in the minerals processing industry are ball and semiautogenous (SAG) mills, which use both ore and steel balls as grinding media (Wei and Craig, 2009b)In the case of a ball mill the ore is crushed before it enters the mill, whereas a SAG mill receives runofmine (ROM) ore directly (Stanley, 1987)A SAG mill in a singlestage Analysis and validation of a runofmine ore grinding mill circuit