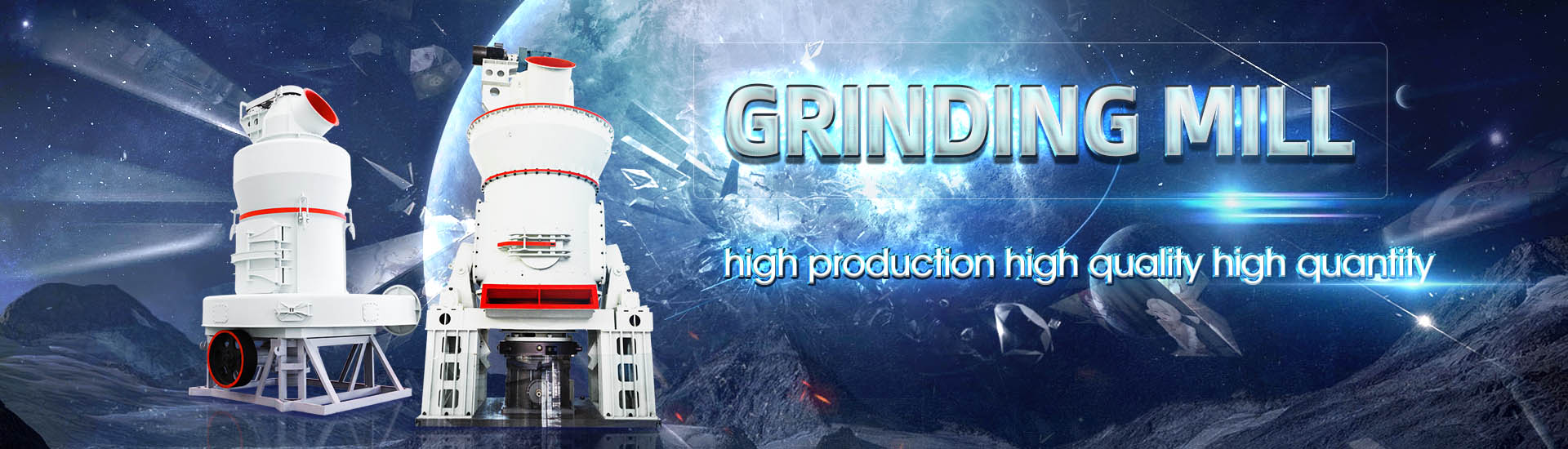
The impact of reversing the direction of the ore grinding mill
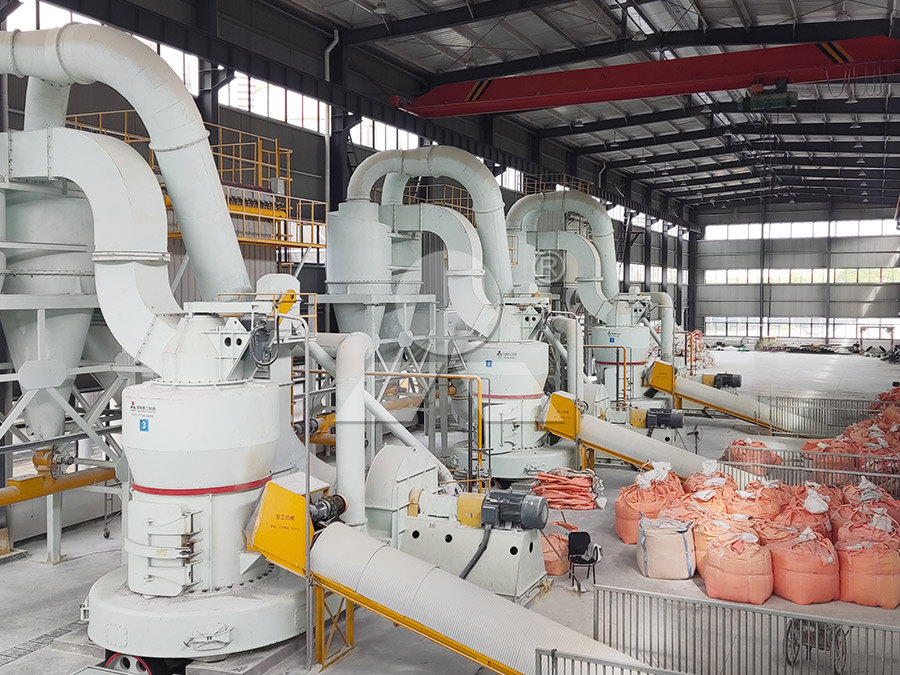
Steadystate and dynamic simulation of a grinding mill using grind
2020年6月15日 Grind curves give the steadystate values of the performance variables throughput, power draw, and grind in terms of the mill filling and critical mill speed The grind curves indicate the operable region of the grinding mill An analysis and dynamic simulation of 2024年4月1日 Disc designs are effective for horizontal mill orientation, while pin designs are effective for vertical mill orientation The primary objective of this research is to examine the The impact of different stirrer designs and mill orientations on the 2017年4月1日 Pilot plant test results with various ores showed that low energy consumption feature of vertical roller mills is applicable to the ore industry Grinding test results for zinc ore Operational parameters affecting the vertical roller mill 2016年11月22日 Focusing on the core issues of grinding process, the paper presents some fundamental research findings in relation to grinding material removal mechanisms The grinding efficiency is analysed by considering the Effect of different parameters on grinding efficiency
.jpg)
Grinding Contribution and Quantitative Separation of Impact and
2023年8月3日 In this study, grinding contribution and quantitative separation of impact and grinding mechanism in cylindrical mill were creatively researched, and the grinding technical 2023年7月20日 Ore grinding process falls into opencircuit and closedcircuit grinding The grinding products of the former are directly processed in the next processing procedure Ore Grinding SpringerLinkFirst, we proved by milling experiments that the media stirring mill with the horizontal direction of the agitator shaft can provide better grinding performances Then, we further elucidated this Effect of Agitator Shaft Direction on Grinding Performance in 2012年6月1日 The paper presents an overview of the current methodology and practice in modeling and control of the grinding process in industrial ball mills Basic kinetic and energy Grinding in Ball Mills: Modeling and Process Control ResearchGate
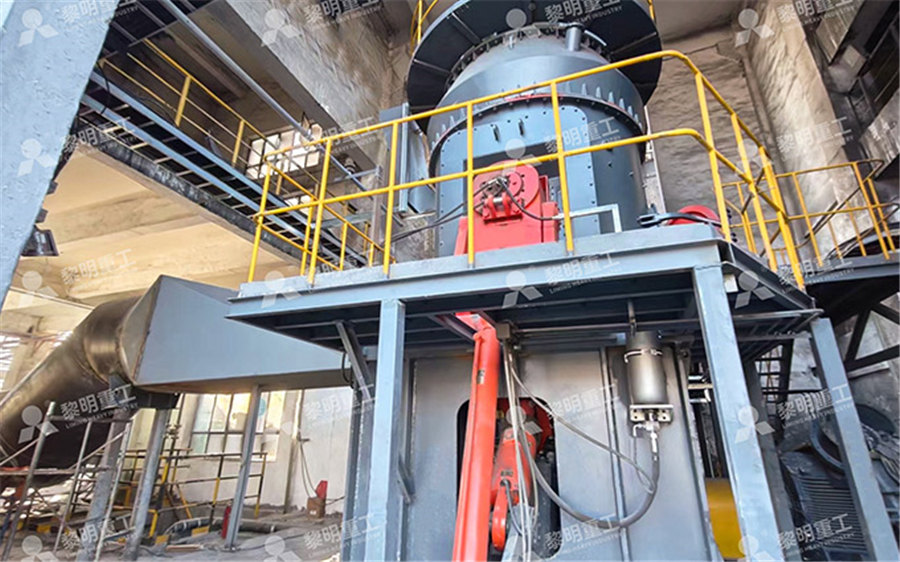
Reengineering of the ore preparation production process in the
The process of material pieces or grains reduction by destruction under the influence of external mechanical forces, depending on the size of the final product, is called crushing or grinding 2022年6月24日 Grinding is a manufacturing process which significantly contributes in producing high precision and durable components required in numerous applications such as aerospace, (PDF) A comprehensive review on the grinding process: finish with respect to manual surface grinding machine, its traverse movement of table is controlled by hydraulic system The table with magnetic chuck have reciprocating motion The table speed of grinding machine is controlled by mechanical flow control valve; and reversing of the table is controlled either by mechanical direction controlMETHODS TO REDUCE THE VIBRATIONS OF HYDRAULIC SURFACE GRINDING 2015年8月6日 Rubber liners absorb the impact of the larger grinding media and thus protecting – the mill structure and prolonging it’s life Weight : Rubber weighs about 15% of an equivalent volume of steel This means that a rubber liner Grinding Mill Liners 911Metallurgist
.jpg)
Factors affecting ores grinding performance in ball mills
Impact mills are the most common type of mill, and use a hammer to hit the grinding media against a stationary steel disc This action causes the media to break down into smaller pieces Vertical mills operate in a similar way, but the media is instead forced down by gravity toward the grinding surface2018年12月24日 ABSTRACT In this study, simulation aided design of grinding circuit for a gold mine in Iran is presented The main parameters for the design of the grinding circuit are the ore specifications and EVALUATION OF THE ALTERNATIVES FOR GOLD ORE GRINDING 2015年4月9日 Grinding Mills and Their Types satyendra; April 9, 2015; 12 Comments ; autogenous grinding, ball mill, grinding mills, hammer mill, rod mill, roller mill, SAG,; Grinding Mills and Their Types In various fields of the process industry, reduction of size of different materials is a basic unit operationGrinding Mills and Their Types – IspatGuru2017年10月18日 Eventually, the best type of ball can be selected for a given mill, ore, and operating condition Recommendations To reduce the consumption of grinding media, the following are recommended Ball manufacturers should strive for greater consistency in their product Adoption of standards would drive manufacturers in this directionGrinding Ball Wear Breakage by Impact Abrasion Tests
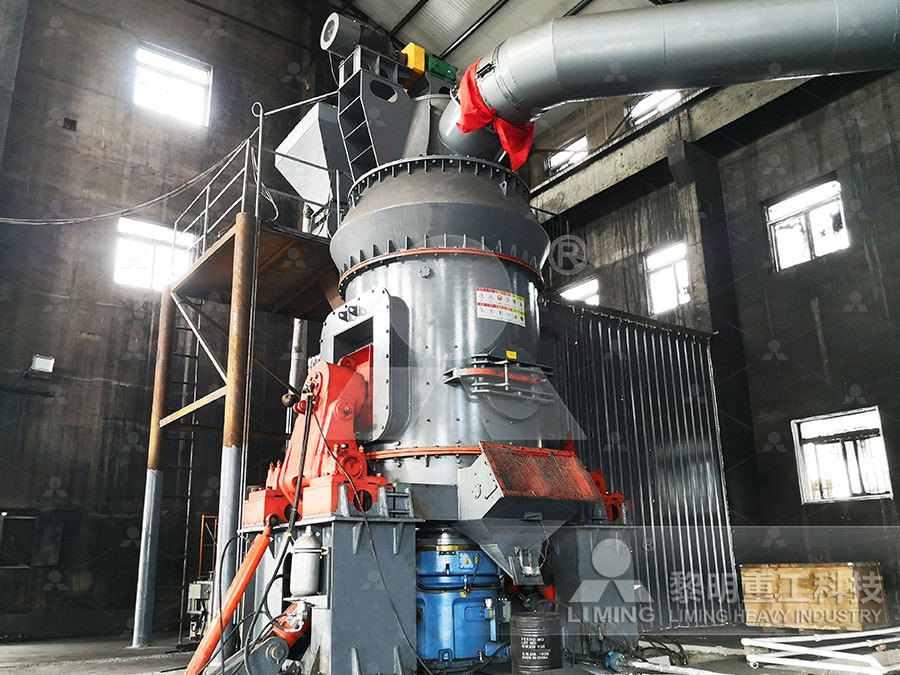
(PDF) A comprehensive review on the grinding process:
June 2022; ARCHIVE Proceedings of the Institution of Mechanical Engineers Part C Journal of Mechanical Engineering Science 19891996 (vols 203210) 236(2):年7月1日 The impact of grinding environment on flotation has been investigated for different ores In the flotation of platinumgroup minerals (PGMs) from the Overysel ore (Bushveld complex in South Africa), dry grinding produced more fine particles, led to a higher degree of liberation for the PGMs but lower recoveries than wet grinding [11]For a Merensky Reef ore, dry grinding On the impact of grinding conditions in the flotation of semi The working principle of a ball mill is based on the impact and attrition between the balls and the grinding media As the mill rotates, the grinding media (usually steel or ceramic balls) are lifted to a certain height and then allowed to fall freely, causing the materials to be reduced in size by the impact and abrasive forces generated between the balls and the particlesBall Mill Grinding Machines: Working Principle, Types, Parts 2011年7月1日 Request PDF Grinding in an air classifier mill Part I: Characterisation of the onephase flow In this and the related second paper [1], we present an indepth study of the twophase flow and Grinding in an air classifier mill Part I: Characterisation of the
.jpg)
Grinding in Ball Mills: Modeling and Process Control
2012年6月1日 As the cylinder starts to rotate, the grinding balls inside the cylinder crush and grind the feed material, generating mechanical energy that aids in breaking bonds, activating the catalyst, and 2020年1月16日 This could be achieved through closer monitoring of the primary crusher performance and proper control of the ratios for the SAG mill feeders drawing the ore from the stockpile The ball mill (PDF) Optimization and performance of grinding The second primary function of a liner is to transfer rotary motion of the mill to the grinding media and charge After all, it is the interface between the mill and the grinding charge Although work on the grinding action in mills was published 100 years ago (White 1905 and Davis 1919), the firstThe Selection and Design of Mill Liners 911 Metallurgist2022年12月30日 Purpose The purpose of this paper is to evaluate the efficiency of grinding operations in terms of how mechanical properties (eg, strength properties and ore texture) affect the Bond Work Index(PDF) Evaluation of gold ore properties and their impact on grinding
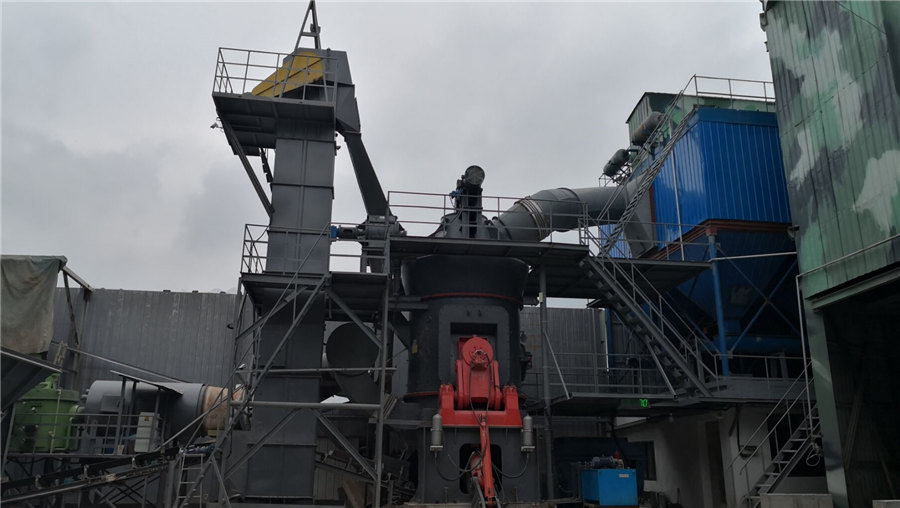
The study of the lining layer abrasing wear in the semiautogenous
*Corresponding author: The study of the lining layer abrasing wear in the semiautogenous grinding mill Mykola Sokur1, Volodymyr Biletskyi2,*, Mykhailo Fyk2, Oleksandr Fyk3, and Igor Zaselskiy4 1Kremenchuk Mykhailo Ostrohradskyi National University, Marketing Department, 20 Pershotravneva Str, Kremenchuk, 39614, Ukraine 2National Technical 1 Grindability: The grindability of the ore affects the efficiency of the grinding mill Harder ores require more energy and longer grinding times, which can impact the mill's performance and operational costs 2 Media andliner Wear: The condition of the grinding media and liners affects the mill's efficiencyUnderstanding the operation of grinding mills in the mining and 2024年6月14日 The grinding process plays a crucial role in industry, allowing for the reduction of particle sizes of raw materials and substances to the required fineness—either as a finished product or for further technological processes The high demand for micro and nanopowders or suspensions is associated with the high energy consumption of the milling process Therefore, The Influence of the Grinding Media Diameter on Grinding 2023年10月27日 The ball mill is a rotating cylindrical vessel with grinding media inside, which is responsible for breaking the ore particles Grinding media play an important role in the comminution of mineral A Review of the Grinding Media in Ball Mills for Mineral Processing
.jpg)
EnergyEfficient Advanced Ultrafine Grinding of Particles Using
2023年7月10日 The present literature review explores the energyefficient ultrafine grinding of particles using stirred mills The review provides an overview of the different techniques for size reduction and the impact of energy requirements on the choice of stirred mills It also discusses the factors, including the design, operating parameters, and feed material properties, 2017年3月4日 Ball mills are used for wet grinding iron ore, g old/copper ore, nickel ore and other ores, as wel l as lime/limestone for flue gas desulphurisat ion systems, coal and other raw materials Rod mill :SIZE REDUCTION BY GRINDING METHODS ResearchGate2006年1月1日 The relining time also reduced by 375% with the new liners Powell et al, 2006; Rajamani, 2006;Yahyaei et al, 2009;MalekiMoghaddam et al, 2013;MalekiMoghaddam et al, 2015;Cleary and Owen (PDF) Selection and design of mill linersOptimization of stirred mill parameters for fine grinding of PGE bearing chromite ore, Particulate Science and Technology, DOI: 101080/2020 To link to this article: https://doi Optimization of stirred mill parameters for fine grinding of PGE
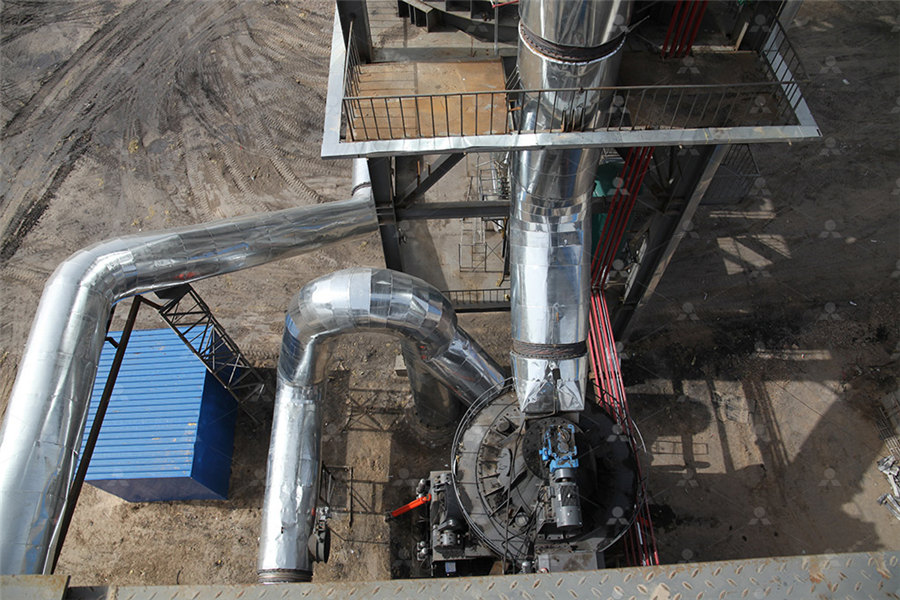
Simulating the Impact of Ore Competence Variability
2019年9月24日 There are numerous examples in the literature, some of which are quantifying the effect of Mine to Mill Grundstrom et al, 2001;Hart et al, 2001;Scott et al, 2002;Burger et al, 2006;Jankovic et al 2018年8月17日 The concept of ore blending is a very relevant notion in modern high tonnage production mines It is not only essential for the prolongation of the mine life of the concerned mine but as well as a The effects of ore blending on comminution behaviour and 2023年10月27日 The ball mill is a rotating cylindrical vessel with grinding media inside, which is responsible for breaking the ore particles Grinding media play an important role in the comminution of mineral ores in these mills This work reviews the application of balls in mineral processing as a function of the materials used to manufacture them and the mass loss, as A Review of the Grinding Media in Ball Mills for Mineral 2021年8月2日 reversing the direction of the grinding wheel; reversing the direction of the grinding wheel Started by mptvexl, August 02, 2021, 10:53:35 AM Previous topic Next topic Print Go Down Pages 1 User actions mptvexl Newbie; reversing the direction of the grinding wheel Tormek
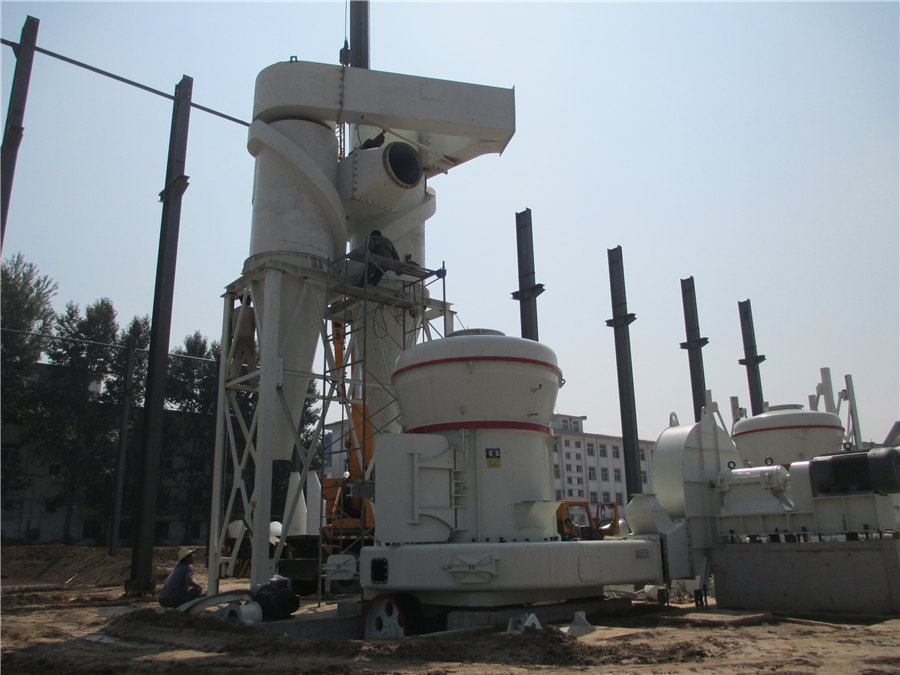
(PDF) The Effects of Blasting on Crushing and Grinding Efficiency
2003年1月1日 The impact of dynamic forces in rockblast fragmentation process has been the subject of investigation for years Nevertheless, while the influence of the macrofragmentation in downstream 2020年7月23日 The depletion of highgrade ores has forced the utilization of lowgrade ores The small liberation sizes in the lowgrade ores require fine grinding which is an energy intensive operationOptimization of stirred mill parameters for fine grinding of PGE 2022年2月17日 minerals1200258An Evaluation on the Impact of Ore Fragmented by Blasting on Mining Performancepdf minerals1200258pdf Content uploaded by Ahmad HassanzadehAn Evaluation on the Impact of Ore Fragmented by Blasting on A section cutthrough of ball mills A ball mill is a type of grinder filled with grinding balls, used to grind or blend materials for use in mineral dressing processes, paints, pyrotechnics, ceramics, and selective laser sinteringIt works on the principle of impact and attrition: size reduction is done by impact as the balls drop from near the top of the shellBall mill Wikipedia
.jpg)
METHODS TO REDUCE THE VIBRATIONS OF HYDRAULIC SURFACE GRINDING
finish with respect to manual surface grinding machine, its traverse movement of table is controlled by hydraulic system The table with magnetic chuck have reciprocating motion The table speed of grinding machine is controlled by mechanical flow control valve; and reversing of the table is controlled either by mechanical direction control2015年8月6日 Rubber liners absorb the impact of the larger grinding media and thus protecting – the mill structure and prolonging it’s life Weight : Rubber weighs about 15% of an equivalent volume of steel This means that a rubber liner Grinding Mill Liners 911MetallurgistImpact mills are the most common type of mill, and use a hammer to hit the grinding media against a stationary steel disc This action causes the media to break down into smaller pieces Vertical mills operate in a similar way, but the media is instead forced down by gravity toward the grinding surfaceFactors affecting ores grinding performance in ball mills2018年12月24日 ABSTRACT In this study, simulation aided design of grinding circuit for a gold mine in Iran is presented The main parameters for the design of the grinding circuit are the ore specifications and EVALUATION OF THE ALTERNATIVES FOR GOLD ORE GRINDING
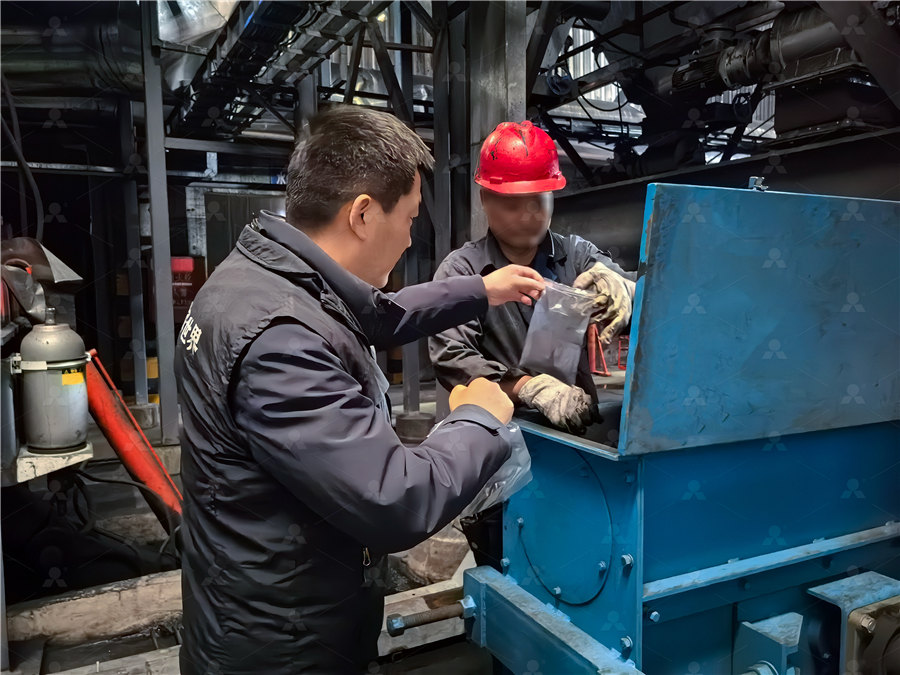
Grinding Mills and Their Types – IspatGuru
2015年4月9日 Grinding Mills and Their Types satyendra; April 9, 2015; 12 Comments ; autogenous grinding, ball mill, grinding mills, hammer mill, rod mill, roller mill, SAG,; Grinding Mills and Their Types In various fields of the process industry, reduction of size of different materials is a basic unit operation2017年10月18日 Eventually, the best type of ball can be selected for a given mill, ore, and operating condition Recommendations To reduce the consumption of grinding media, the following are recommended Ball manufacturers should strive for greater consistency in their product Adoption of standards would drive manufacturers in this directionGrinding Ball Wear Breakage by Impact Abrasion TestsJune 2022; ARCHIVE Proceedings of the Institution of Mechanical Engineers Part C Journal of Mechanical Engineering Science 19891996 (vols 203210) 236(2):1107(PDF) A comprehensive review on the grinding process: 2023年7月1日 The impact of grinding environment on flotation has been investigated for different ores In the flotation of platinumgroup minerals (PGMs) from the Overysel ore (Bushveld complex in South Africa), dry grinding produced more fine particles, led to a higher degree of liberation for the PGMs but lower recoveries than wet grinding [11]For a Merensky Reef ore, dry grinding On the impact of grinding conditions in the flotation of semi
.jpg)
Ball Mill Grinding Machines: Working Principle, Types, Parts
The working principle of a ball mill is based on the impact and attrition between the balls and the grinding media As the mill rotates, the grinding media (usually steel or ceramic balls) are lifted to a certain height and then allowed to fall freely, causing the materials to be reduced in size by the impact and abrasive forces generated between the balls and the particles2011年7月1日 Request PDF Grinding in an air classifier mill Part I: Characterisation of the onephase flow In this and the related second paper [1], we present an indepth study of the twophase flow and Grinding in an air classifier mill Part I: Characterisation of the