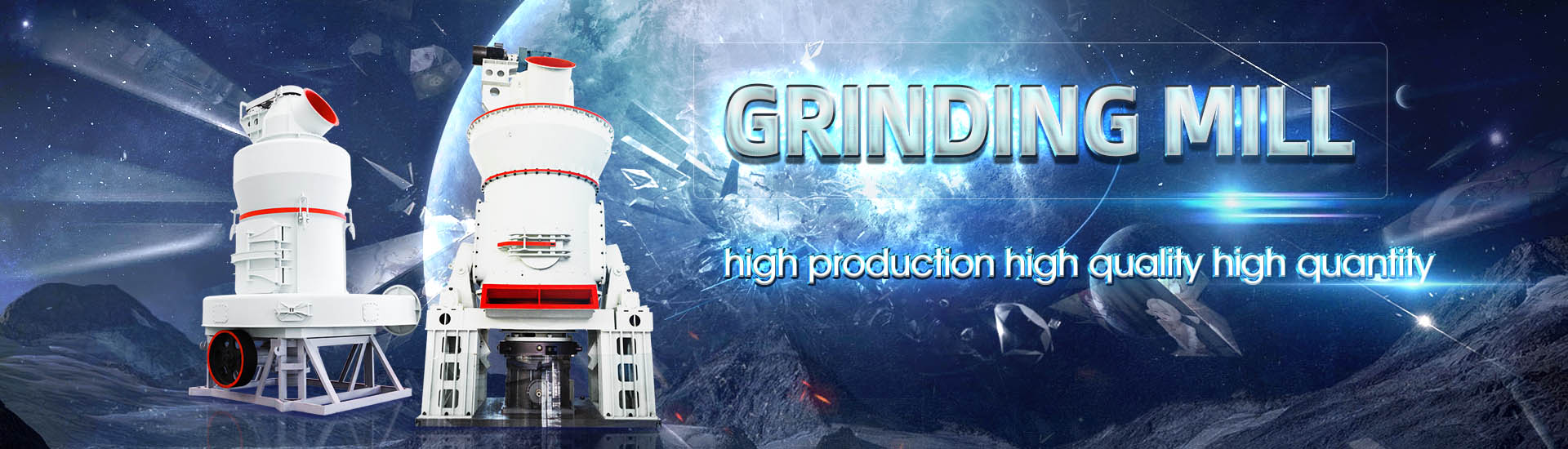
Main raw materials for producing silicate cement
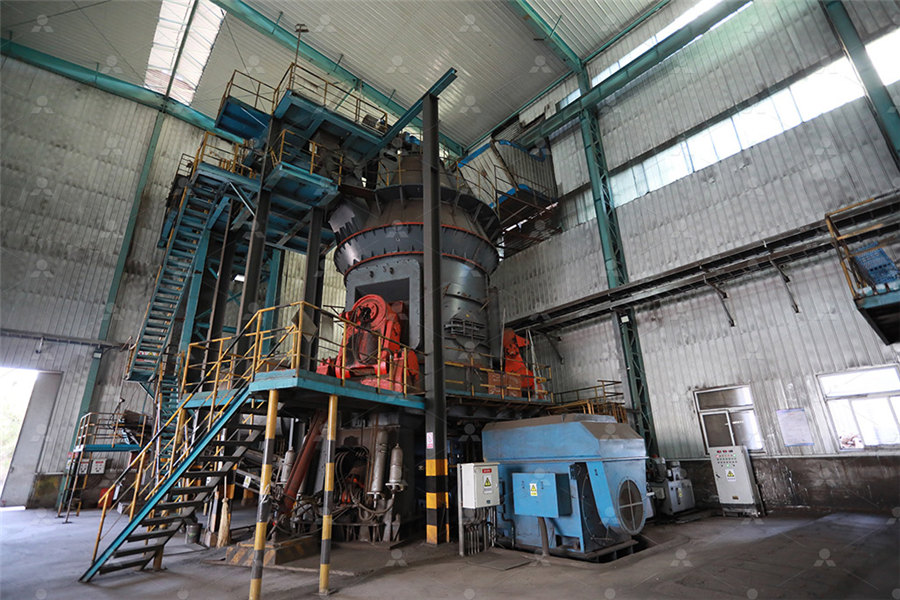
Composition and production process of silicate cement
The lime raw materials are natural limestone, tuff and shells, which mainly provide CaO in cement; the clay raw materials are primarily clay (or shale, mudstone, siltstone, and river 2024年11月23日 Portland cement is made up of four main compounds: tricalcium silicate (3CaO SiO 2), dicalcium silicate (2CaO SiO 2), tricalcium aluminate (3CaO Al 2 O 3), and a tetracalcium aluminoferrite (4CaO Al 2 O The major cements: composition and propertiesThe raw materials are firstly crushed and made into powdered form and stored in silos The clay is then washed in washing mills to remove adhering organic matters found in clay The powdered limestone and water washed clay are Manufacture of Cement Materials and Manufacturing Minerals of natural origin as well as industrial products/byproducts can be used for cement production as long as the main components of cement (Cao, SiO2,Al2O3,Fe2O3)are present Raw materials for cement manufacturing Cement Plant
.jpg)
StepbyStep Guide to the Manufacturing of Cement
The primary raw materials used in the manufacturing of cement include calcium carbonate, silica, alumina, and iron ore Predominantly, people extract these materials from limestone, clay, shale, and marl Limestone is the principal Silica fume, also known as MicroSilica, is a byproduct of producing silicon metal or ferrosilicon alloys The main ingredient of silica fume is amorphous (noncrystalline) silicon dioxide The CEMENT MANUFACTURING RAW MATERIALS CharahAs typically 80% of the raw mix consists of limestone, it is referred to as the primary raw material The secondary raw material, which provides the necessary silica, alumina and iron oxide, is Cements Elsevier2021年3月3日 Since the main oxides to manufacture Portland cement are lime (CaO), silica (SiO 2), alumina (Al 2 O 3), and iron (Fe 2 O 3), the raw mix for making cement clinker is generally Cement SpringerLink
.jpg)
Cement: Materials and manufacturing process
Materials are extracted / quarried / recovered and transported to the cement plant The raw materials, limestone, shale, silica and iron oxice are crushed and milled into fine powders The powders are blended (the ‘raw meal’) and 2024年8月20日 The first cement manufacturing plant was set up in Madras in 1904 in India In terms of cement production, The silicate phase contributes to the strengthening of the cement This contributes to 05–6% of the cement Understanding the Raw Materials for Manufacturing 2023年3月16日 This paper presents the development of composite silicate mass compositions based on manmade waste for the production of autoclave hardening products, as well as the results of physicochemical studies of ManMade Raw Materials for the Production of 2022年9月30日 Cement production has more than doubled over the last two decades, from 180 Gt in 2002 to 405 Gt in 2018 (Fig 2), due mainly to socioeconomic development in China (064 Gt in 2002 to 22 Gt in Cement substitution with secondary materials can reduce annual
.jpg)
Recent Progress in Green Cement Technology Utilizing LowCarbon
2019年1月21日 The cement industry is facing numerous challenges in the 21st century due to depleting natural fuel resources, shortage of raw materials, exponentially increasing cement demand and climate linked environmental concerns Every tonne of ordinary Portland cement (OPC) produced releases an equivalent amount of carbon dioxide to the atmosphere In this The principal raw materials used in the manufacture of Ordinary Portland Cement are: Argillaceous or silicates of alumina in the form of clays and shales Calcareous or calcium carbonate, in the form of limestone, chalk and marl which is a Ordinary Portland Cement Constituents, Properties, Types Building Decorative Cement In Building Decorative Materials, 2011 521 Colored Cement Colored silicate cement, shortened as colored cement, is a kind of hydraulic cementing material made in these two ways: mix white silicate cement clinker, super white gypsum, mineral pigment and additives (water proofing agent, water retaining agent and plasticizer etc) together and Silicate Cement an overview ScienceDirect Topics2022年7月1日 The bulk of the cement industry's environmental burden is from the calcareous source Calcium is mostly available naturally as limestone (CaCO 3), where almost half of the mass is eventually released as CO 2 during clinker manufacture Iron (Fe) is the fourth most common element in the Earth's crust surpassed only by oxygen, silicon, and aluminium; Sustainable ironrich cements: Raw material sources and binder
.jpg)
CEMENT MANUFACTURING RAW MATERIALS Charah
Pozzolans are silicatebased noncrystalline materials that react with the calcium hydroxide generated by hydrating cement to form additional cementitious materials Depending upon the particle size, chemical composition and dosage, different pozzolans will affect the concrete strength and performance differently and at different times during curingThe improvement of novel bioactive/biomimetic ionleaching restorative materials poses one of the main objectives in research to increase the quality and the longevity of the restorations (Tay and Pashley, 2008; Ryou et al, 2012; Profeta et al, 2012)Two experimental calcium silicatebased microfillers (TCS) modified with βtricalcium phosphate (TCP) or βTCP Calcium Silicate Cement an overview ScienceDirect TopicsRaw Material Preparation and Raw Meal Design Part One: Raw Material Preparation General; The production of cement is started from quarrying the raw material The main raw materials are limestone, basalt, sand stone, pumice, gypsum Site Exploration of suitable deposits, for the raw material has three main aims:Cement Manufacturing Process INFINITY FOR CEMENT EQUIPMENT2023年5月1日 Cement industries are one of the largest CO 2 emitters responsible for 5% of anthropogenic CO 2 emissions [5], [6] Nearly 90% of the CO 2 released during cement production is a result of the calcination and combustion of fossil fuels The remaining 10% is generated by the transport of raw materials [7]Exploring reaction and carbonation products of calcium silicate cement
.jpg)
How Cement is Made Cement Manufacturing Process
Stage of Cement Manufacture There are six main stages of the cement manufacturing process Stage 1: Raw Material Extraction/Quarry The raw cement ingredients needed for cement production are limestone (calcium), sand and clay (silicon, aluminum, iron), shale, fly ash, mill scale, and bauxite The ore rocks are quarried and crushed into smaller pieces of about 6 inches2018年12月18日 Main components of cement are all minerals provided in clinker and raw materials These experiments were carried out in the Holding Company Cement Plant in Lukavac, Bosnia and Herzegovina Mineral Characterization of raw materials and final product 2020年9月29日 Raw materials chemistry Cement manufacture requires a source of calcium, such as CaCO 3 or CaMg (CO 3) 2, which comprises almost 80–90% of the total and the rest is iron oxide (Fe 2 O 3, Fe 3 O 4), quartz (SiO 2), and clay/bauxite (Alsilicates) (Aïtcin and Flatt Citation 2015; Hewlett Citation 2003; Peray and Waddell Citation 1986)Traces of Na 2 O, K 2 An overview of alternative raw materials used in cement and This paper aims to characterize basaltic rocks as alternative raw materials for Portland cement clinker production and evaluate its possible use as an addition for the cement industry It describes the physical, chemical and microstructural characterization of the basalt clinker as well as the effect of its addition to Portland cements on the hydration, water demand, setting and Characterization and technological behavior of basalt raw materials
.jpg)
An Insight into the Chemistry of Cement—A Review MDPI
2022年12月23日 Cement is a hydraulic binder; it consists of a finely ground inorganic material which forms a paste when mixed with water, is able to set and harden because of numerous exothermic hydration reactions (and processes), and is thus capable of binding fragments of solid matter to form a compact whole solid [1,2,3]After hardening, cement retains its strength and 2015年8月1日 This paper aims to characterize basaltic rocks as alternative raw materials for Portland cement clinker production and evaluate its possible use as an addition for the cement industryCharacterization and technological behavior of basalt raw materials Chemical Properties of Cement The raw materials for cement production are limestone (calcium), sand or clay (silicon), bauxite (aluminum) and iron ore, and may include shells, chalk, marl, shale, clay, blast furnace slag, slate Chemical analysis of cement raw materials provides insight into the chemical properties of cement Tricalcium Properties of Cement Physical Chemical Civil EngineeringThe major raw material for the clinkermaking is usually limestone The International Energy Agency has estimated that cement production will increase by between 12 and 23% by 2050 to meet the needs of the world's growing population Calcium silicate hydrate – Main product of the hydration of Portland cement;Portland cement Wikipedia
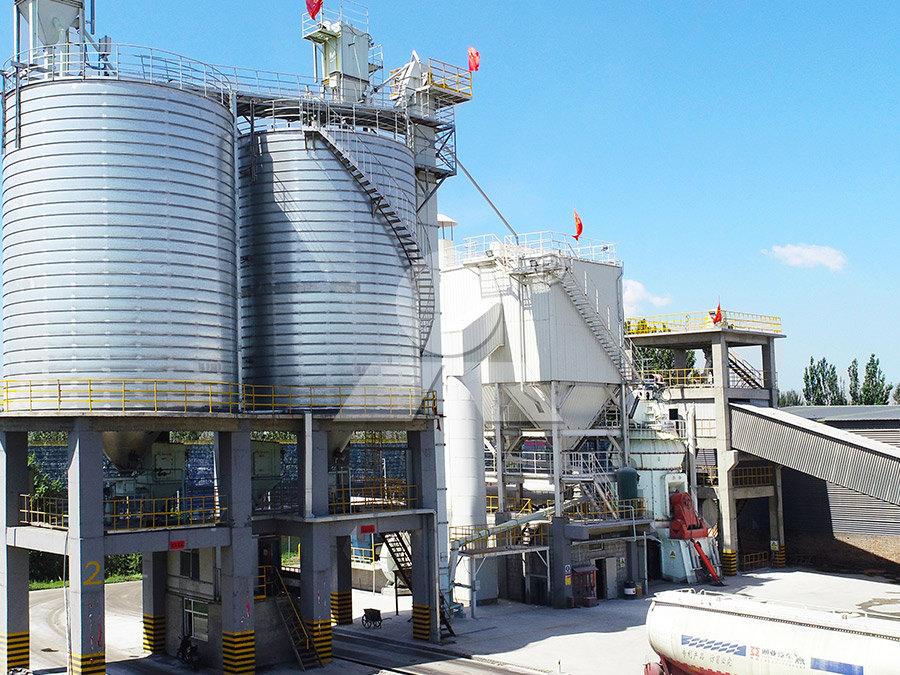
Cement clinker Wikipedia
The Portland clinker essentially consists of four minerals: two calcium silicates, alite (Ca 3 SiO 5) and belite (Ca 2 SiO 4), along with tricalcium aluminate (Ca 3 Al 2 O 6) and calcium aluminoferrite (Ca 2 (Al,Fe) 2 O 5)These main mineral phases are produced by heating at high temperature clays and limestone [3]The major raw material for the clinkermaking is usually limestone KEYWORDS ABSTRACT Cement, a mixture of aluminates, silicates and clay, is an important material in construction of housing; roads and development of infrastructure and a key to economic growthRaw materials for cement production ResearchGate2023年10月16日 World cement production is about 43 billion tons per year 1, with an average consumption of raw materials of about 16 tonnes for each tonne of cement manufactured 2Valorisation of waste or by Thermodynamic modelling of cements clinkering process as a tool 2020年1月2日 A cement production plant consists of three major processes such as quarry and raw material preparation, clinker production and cement grinding and distribution [2] During raw material preparation first, limestone and other raw materials are extracted using drilling and blasting techniques Afterward, the quarried material isCement Industry in Sri Lanka JRTE
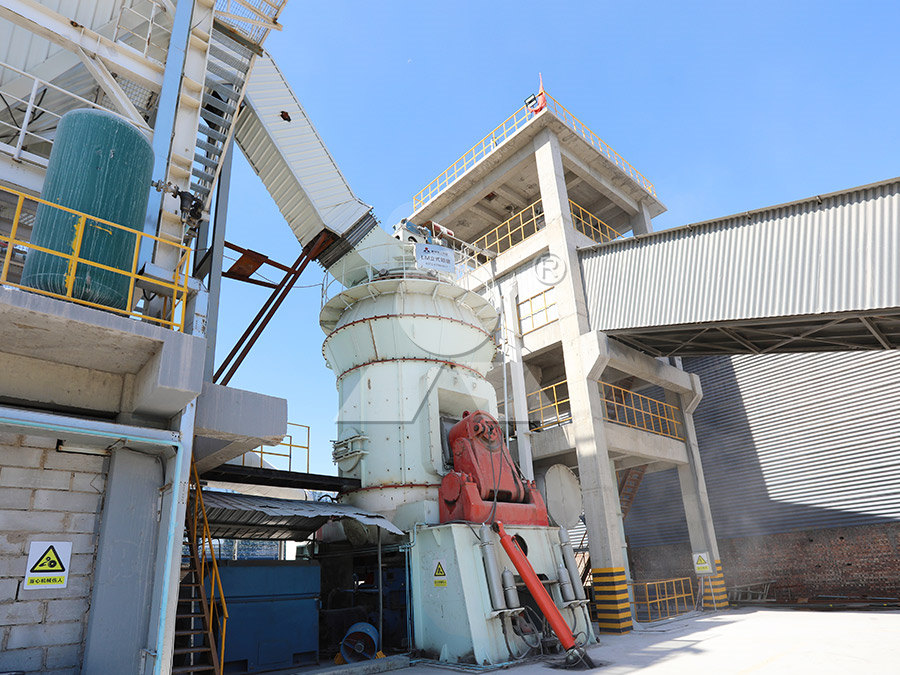
116 Portland Cement Manufacturing US EPA
1971年8月17日 States The balance of domestic cement production is primarily masonry cement Both of these materials are produced in portland cement manufacturing plants A diagram of the process, which encompasses production of both portland and masonry cement, is shown in Figure 1161 As shown in the figure, the process can be divided into the following Only by strictly limiting the content of Fe 2 O 3 in raw materials and fuels can we meet the production requirements of white cement Therefore, white cement plants often use highquality limestone as raw materials and mix with silica raw materials such as pyrophyllite, feldspar, silica, kaolinite, and quartz sand to produce white cementRaw Material Requirement in White Cement ProductionAs an alternative replacement of clay, sewage sludge is also combined with other solid waste in cement production Lin and Lin (2004; 2005) used different types of waste sludge ash, including sewage sludge ash, water purification sludge ash and steel slag and limestone, as raw components for the production of ecocement clinkers by burning at 1400 °C for 6 hCement Clinker Production an overview ScienceDirect TopicsSilica: Silicon dioxide is known as silica, chemical formula SiO 2 A sufficient quantity of silica should be present in cement to dicalcium and tricalcium silicate Silica imparts strength to cement Silica usually presents to the extent of about 30 percent cement Alumina: Alumina is Aluminium oxideThe chemical formula is Al 2 O 3 Alumina imparts quick setting property to the cement8 Main Cement Ingredients Their Functions Civil Engineering

(PDF) The key to white cement ResearchGate
2015年8月1日 There is ongoing interest in applying kaolin in the construction industry as a raw material in the production of white cement clinker and as an artificial pozzolanic additive for concrete (in the 2022年12月23日 Even if cement is a wellconsolidated material, the chemistry of cement (and the chemistry inside cement) remains very complex and still nonobvious(PDF) An Insight into the Chemistry of Cement—A Review2023年2月1日 Raw material blending is an important process affecting cement quality The aim of this process is to mix a variety of materials such as limestone, shale (clay), sandstone and iron to produce CEMENT RAW MATERIALS BLENDING PROCESS BY USING However, as from 2021 China’s cement production will decline and so will China’s share on the global market Accordingly, global cement production will decline to 4081 Mt/a by 2030 with China’s share at 417% The Rest of the World (RoW) Availability of cement raw materials Cement Lime
.jpg)
Use of Slags in the Production of Portland Cement Clinker
2019年8月28日 Kopeliovich VM, Zdorov AI, Zlatkovsky AB (1998) Utilization of industrial wastes in cement production Cement 3:174 Google Scholar Kougiya MV, Ugolkov VL (1981) Differential thermal analysis of portland cement raw mixes Cement 11:19–21 Google Scholar2023年5月26日 In this work, iron ore tailing (IOT) was used for the production of two different materials: sodium silicate and geopolymers Initially, reactions of IOT with NaOH were carried out by hydrothermal Use of Iron Ore Tailing as Raw Material for Two 2023年6月13日 Limestone: The Backbone of Cement Raw materials Production Limestone, a sedimentary rock composed mainly of calcium carbonate (CaCO3), Limestone plays a crucial role in the formation of calcium silicates, which are the main compounds responsible for providing strength to cementCement raw materials Aryiatas company23 Preparation of raw mix cement clinker The raw mix for the production of cement clinker comprises calcareous and basalt materials The basalt raw material is a source of both aluminum and silica It may contain one or more types of silicate minerals Other sources of silica are quartz, sand, chalcedony, opal and feldspar They are Characterization and technological behavior of b asalt raw materials
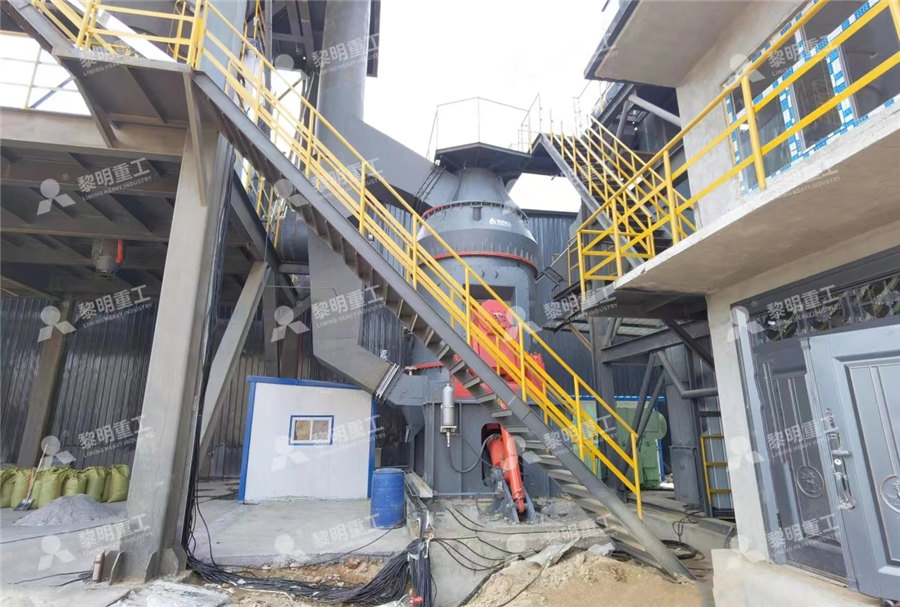
Everything you need to know about cement Raw Materials
In the cement production process, since there are quite a few unit operations employing different hardware systems, it is important to examine the role of raw materials in this perspective For example, a full understanding of the characteristics of the limestone to be used in a given situation will help in selecting the right type of crusher2014年11月15日 The main compositions of MSS and some raw materials in cement production are CaO, Al 2 O 3, Fe 2 O 3 and SiO 2, while the composition of LDS is closer to the traditional raw material As a consequence, LDS can be theoretically used as an alternative for raw materials in cement productionThe utilization of limedried sludge as resource for producing cement In the selection of raw materials, the feasibility of attaining such particle size distribution patterns requires specific attention All in all, it should be realized that the production of cement is solely dependent on natural raw materials and, more specifically, on the quality Basics of mineral resources for cement production4Main ingredients and formula: Calcium silicate production raw materials and technological process Step 1: Raw Material Processing cement, quartz powder, etc are added in turn, fully mixed by the counterflow mixer to make a flow slurry of a certain concentration, News Calcium Silicate Production Raw Materials And
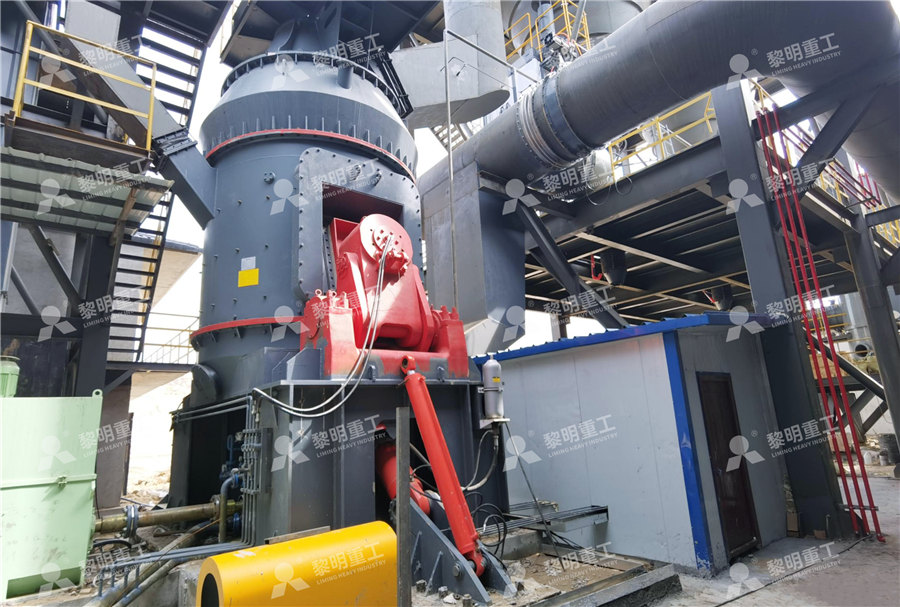
ManMade Raw Materials for the Production of Composite Silicate
2023年3月16日 Thus, the purpose of these studies was to develop a composite material: silicate brick with the use of technogenic waste as a secondary raw material 2 Materials and Methods In order to obtain a composite material in the form of silicate bricks, the following technogenic wastes were used as raw materials: dolomitebarium tailings of JSC “Ach