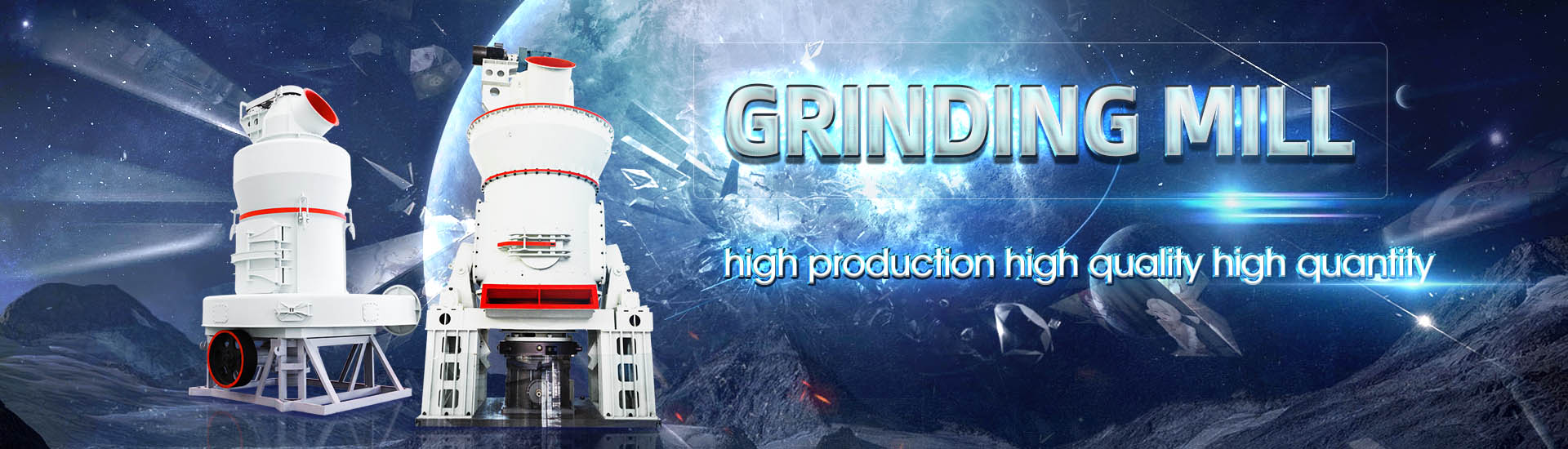
Rare earth ore limestone ore powder processing plant process flow chart
.jpg)
A generalized process flow diagram of rare earth
Figure 1 shows an abridged diagram of the conventional process route of REE ores to REE metal The primary steps involved are as follows: Process flow diagram for limestone processing operations Processing commences with transportation of the (raw) stone from the quarry to the processing facility, as depicted by Limestone Quarrying and Processing: A LifeCycle InventoryA typical example of a rare earth processing flowsheet is shown below: EXPERIENCE • Recovery of rare earths, CeO 2, mixed rare earths, polishing powder from an Australian deposit • SGS MINERALS SERVICES – T3 SGS 302 102013This SuperPro Designer example analyzes a process for the extraction, separation, purification, and recovery of light rare earth oxides from a fluorocarbonaterich ore The processRare Earth Elements (REE) Production Process
.jpg)
Flow diagram and system boundaries of limestone
The analysis was performed through process modelling of the CaL plant using 4 different supplementary fuels in the calciner, namely, biomass charcoal (BC), solid recovered fuel (SRF), coal, and2024年11月21日 All rareearth ores contain less than 10 percent REO and must be upgraded to about 60 percent in order to be processed further They are first ground to a powder and then Rareearth element Processing Ores Britannica2020年3月26日 The present chapter highlights the world distribution of rare earth deposits, occurrences, processing methodologies, and plant practices of few economic minerals The Mineral Processing of Rare Earth Ores SpringerLink2015年12月25日 This chapter is about mineral processing of the rare earths (making the mined ore into a concentrate of the valuable minerals), and extractive metallurgy of the rare earths (how to get the metals out of the concentrate) Mineral Processing and Extractive Metallurgy of the
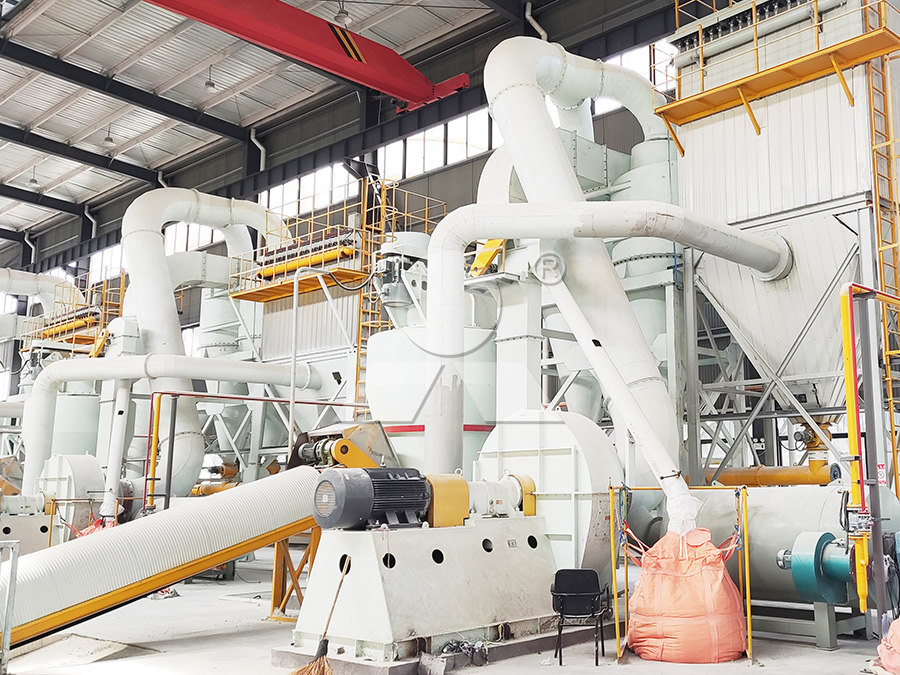
Rare Earth Elements: A Review of Production, Processing,
2012年5月21日 • Resource extraction and processing (hard rock example) – Mining = Overburden, Waste Rock, SubOre, and Ore • Ore up to 13 percent REE or greater • Tailings The limestone grinding production line is a production process for the fine processing of limestone raw materials The limestone grinding production line grinds limestone into powders of different fineness through crushing, grinding, classification, and other processes to meet the needs of different fields This production line covers the complete process from raw material processing Limestone Grinding Mill Plant TAYMACHINERY2015年8月31日 The escalating demand of rare earth metals (REMs) in various applications and their continuous depleting ores have laid emphasis to produce metals from their complex resources by developing energy (PDF) Process development to recover rare earth metals from 2023年11月9日 Rare earth ore processing cases The following takes the most common bastnaesite and beach mineral sand as examples to provide a reference for your rare earth processing Case 1 American bastnaesite processing Unlocking Potential: Rare Earth Elements Processing
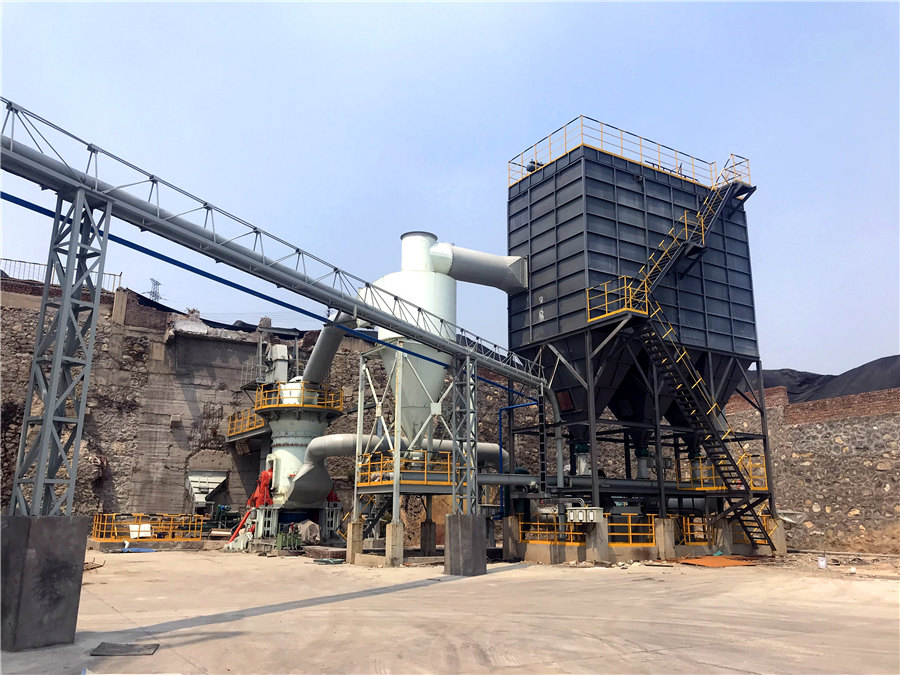
Diamond Processing Flow Chart of Beneficiation
2016年4月14日 Diamond Processing Flow Chart #3 This flowsheet illustrates a more complex diamond recovery method developed in recent years With variations it can be used to process 100 to 500 tons per hour of Kimberlite ore and is also arranged to handle weathered or soft oresRare Earths mining process, how to extract mineral from rock and placer deposit, related processing plant flow chart and layout design read more Skip to content Menu Home; 100TPH Tantalite Ore Processing Plant in Sierra Leone 150TPH Coltan Ore Processing Plant in GhanaLead, zinc, iron, manganese, etcRare Earths Mining Processing Equipment Flow Chart JXSC2015年12月25日 In Chap 2, the most important occurrences of the rare earths were describedThis chapter will deal with what happens when the rare earths have been mined It answers the question: how are the ores processed? Mineral processing (sometimes called mineral dressing or ore dressing) is the preparation of ore from the stage that the material is Mineral Processing and Extractive Metallurgy of the Rare EarthsKalgoorlie Rare Earths Processing Facility Project FAQs What are Rare Earths and why are they important? Rare Earths are a group of 15 elements in the periodic table known as the Lanthanide series Rare Earths are used in the manufacture of many things we use every day – from smart phones to cars, electrical appliances, and green technologiesKalgoorlie Rare Earths Processing Facility Project FAQs Lynas
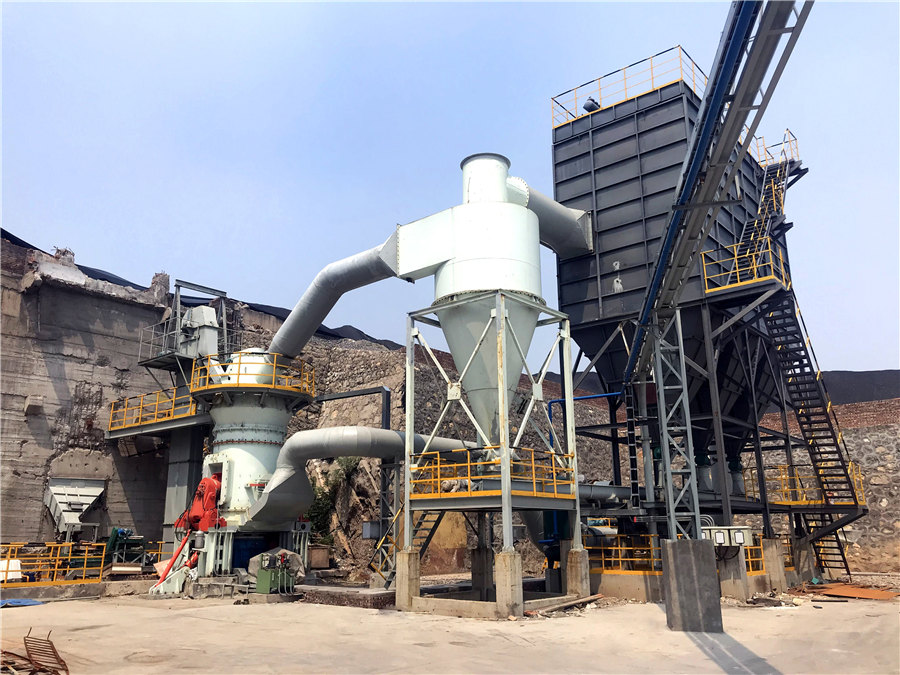
Iron Ore Pelletizing Process: An Overview ResearchGate
PDF On Jul 11, 2018, Sandra Lúcia de Moraes and others published Iron Ore Pelletizing Process: An Overview Find, read and cite all the research you need on ResearchGateHighgrade ores worldwide are depleting due to the increasing demand for valuable metal (eg, copper, gold, rare earth elements) to satisfy technological advancement and applications in A typical flowsheet for processing refractory gold ore (Sulphidic 2017年9月10日 The purpose of this paper is to comprehensively review and summarize the rare earth processing routes, the mostly employed rare earth separation methods, supply and demand of rare earth around the (PDF) A Review of Rare Earth Mineral Processing Technologyconomic analysis of rare earth element processing methods for Mountain Pass ore 408 ULY 2022 VOLUME 122 The Journal of the Southern African Institute of Mining and Metallurgy separation of REE minerals with relatively high densities (47 g/cm3) and gangue minerals with low specific gravity such as quartz, calcite and fluorite (Ferron, Bulatovic and Salter, 1991)Economic analysis of rare earth element processing methods for
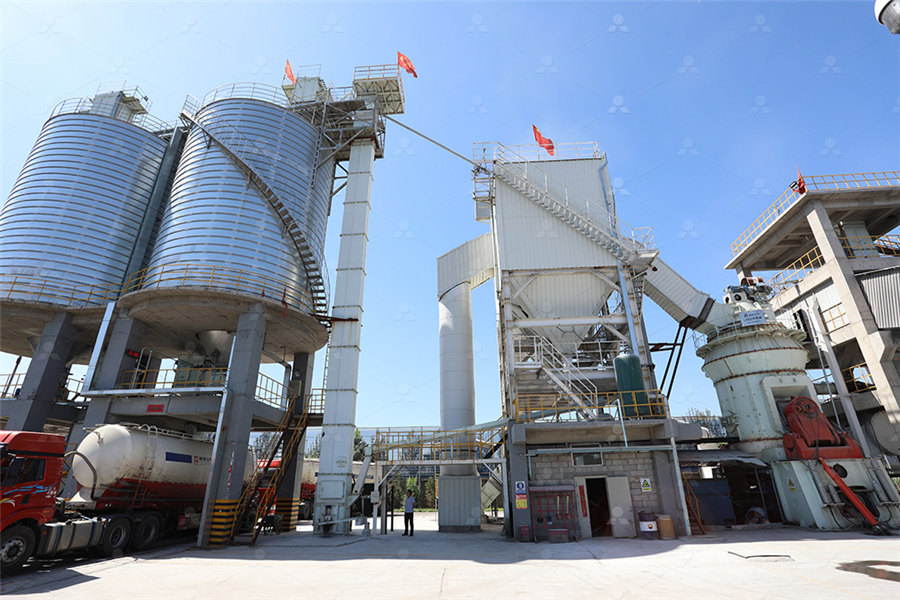
Iron Ore Processing, General SpringerLink
2022年10月20日 Iron ore handling, which may account for 20–50% of the total delivered cost of raw materials, covers the processes of transportation, storage, feeding, and washing of the ore en route to or during its various stages of treatment in the mill Since the physical state of iron ores in situ may range from friable, or even sandy materials, to monolithic deposits with hardness of 2017年2月16日 PDF Sintering is a thermal agglomeration process that is applied to a mixture of iron ore fines, recycled ironmaking products, fluxes, slagforming Find, read and cite all the research you (PDF) Iron Ore Sintering: Process ResearchGate2024年4月1日 This technique has a high utilization rate of RE resources and has been applied to industrialscale production of ores from Bayan Obo, Mountain Pass and Weishan Lake with the process flow charts in Fig 4 55, 61 It is worth mentioning that the flotation feed of Mountain Pass and Weishan Lake is the raw ore, while the flotation feed of Bayan Obo is derived from iron Recent process developments in beneficiation and metallurgy of rare Rare earth elements (REEs) are a group of 15 chemical elements in the periodic table, specifically the lanthanides Two other elements, scandium and yttrium, have a similar physiochemistry to the lanthanides, are commonly found in the same mineral assemblages, and Processing the ores of rareearth elements Academia
.jpg)
(PDF) Process development to recover rare earth metals from
Among 250 recognized REEs minerals, only three are considered to be the major ore that is most viable for REMs extraction: bastnasite, monazite and xenotime However, weathered crust elutiondeposited rare earth ores commonly known as ionadsorbed rare When iron ore is extracted from a mine, it must undergo several processing stages Six steps to process iron ore 1 Screening We recommend that you begin by screening the iron ore to separate fine particles below the crusher’s CSS before the crushing stage A static screen is used to divert the fine particles for crushingThe six main steps of iron ore processing Multotec2024年8月15日 Comminution involves both crushing and grinding As the first step in mineral processing, comminution is to process large pieces of ore into smaller pieces with the help of crushers and grinders 2 Sizing/Screening Sizing refers to the process of separating ore particles based on their sizeMineral Processing Plants: What You Need to Know2024年4月26日 Iron ore processing is a crucial step in the production of steel, one of the most essential materials in modern society Iron ore, a naturally occurring mineral composed primarily of iron oxides, is mined and processed to extract iron for various industrial applicationsIron Ore Processing: From Extraction to Manufacturing
.jpg)
Rare Earth Elements (REE) Production Process Flowsheet (Flow Chart
Download scientific diagram Rare Earth Elements (REE) Production Process Flowsheet (Flow Chart) from publication: Rare Earth Elements (REE) Extraction from a fluorocarbonaterich ore Process Download scientific diagram Schematic flow diagram for separation of rare earth elements from rare earth polishing powder wastes via a devised hydrometallurgical process (Um and Hirato, 2016) [16]Schematic flow diagram for separation of rare earth Rare earth ore flotation process is one of the main methods of rare earth ore beneficiation It uses the difference in the physical and chemical properties of the surface of rare earth minerals and associated minerals to separate them from Rare Earths Processing Equipment, Process Flow, 2015年8月1日 However, weathered crust elutiondeposited rare earth ores commonly known as ionadsorbed rare earth ore is also feasible for RE recovery These ores were first discovered as a novel exogenous ore in Jiangxi province of China in 1969 and have widespread distribution, rich reserves, low radioactivity, complete RE partitioning and is rich in middle and heavy rare earthProcess development to recover rare earth metals from monazite
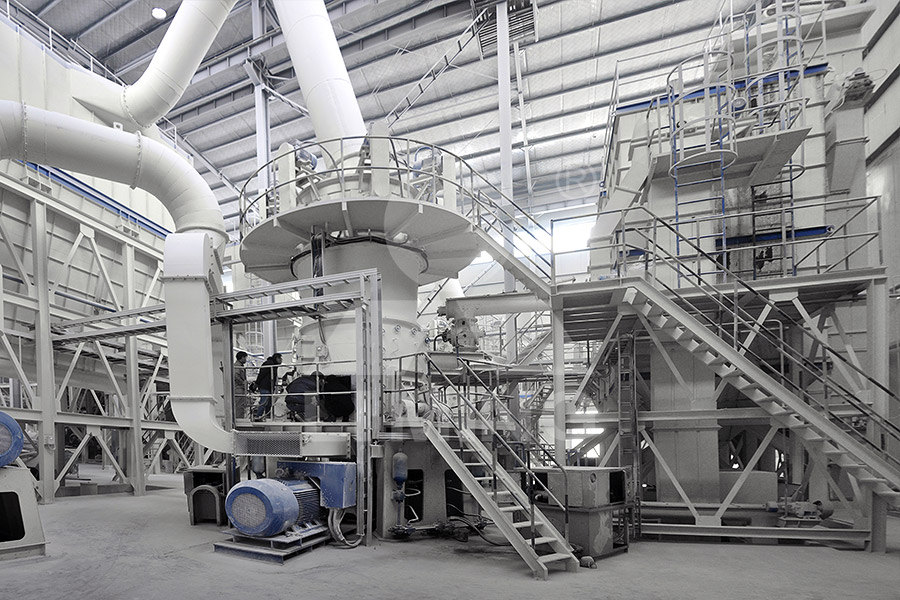
Development of a Process for Recovery of Rare Earths from the
Bench and pilot plant studies were carried out at ANSTO to develop a process for rare earth recovery from the Mt Weld deposit near Laverton, Western Australia This paper describes the development of the flowsheet, which is similar to conventional monazite processing, but with the introduction of several innovative steps to account for the complex rare earth mineralisation This chapter gives an overview of the major and minor local rare earth (RE) minerals which are being studied in Malaysian Nuclear Agency (Nuklear Malaysia) Since the minerals discussed are mined locally, differences in the rare earth element (REE) content may arise because the same metal ore deposits also occur in several other parts of the worldRARE EARTHS PROCESSINGto increase efciency in future REE processing Introduction Rareearth elements (REEs) are required for use in modern hightech applications and demand has increased signicantly over the last decade 1 However, processing of REE ores poses potential hazards to human health and the environment due toProcessing the ores of rareearth elements2024年3月12日 Abstract The author investigated the modes of thermal and heatandradiation treatment of ferruginous bauxite from Vezhayu–Vorykva deposit and revealed different mechanisms of mineral transformations Under thermal treatment, oxohydroxides transform into anhydrous iron and aluminum oxides, while under heatandradiation treatment, scattered Process Flow Charts and Recommendations for Processing of
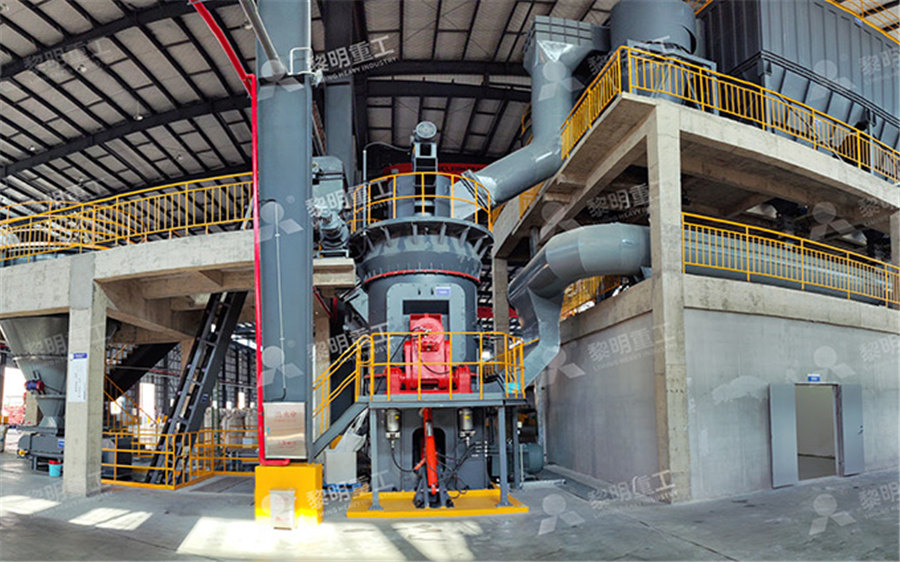
Rare Earth Ores an overview ScienceDirect Topics
The development of the process of leaching ionabsorbed rare earth ores has experienced three stages The first stage of leaching process was to leach ionabsorbed rare earth ores with the solution of sodium chloride, and the leaching process was firstly carried out in a tank, later in a pool Fig 168 shows the process flow sheet2015年5月1日 This paper explores flows and stocks, at the scale of the European Union (EU), of certain rare earth elements (REEs; Pr, Nd, Eu, Tb, Dy and Y) which are associated with products that are important Material flow analysis applied to rare earth elements in Europe2024年11月24日 OWP set to Chemical Bath mode with a screwdriver to process Rare Earth dusts with sulfuric acid and get Crushed Rare Earth ores Feed these into the ore processing network to eventually recover Rare Earth (I) dusts which can be dehydrated to recover useful dusts (namely Yttrium) Platinum Processing Line, fed with the Platinum Metallic Powder DustOre Processing Concepts GT New HorizonsThe limestone grinding production line is a production process for the fine processing of limestone raw materials The limestone grinding production line grinds limestone into powders of different fineness through crushing, grinding, classification, and other processes to meet the needs of different fields This production line covers the complete process from raw material processing Limestone Grinding Mill Plant TAYMACHINERY
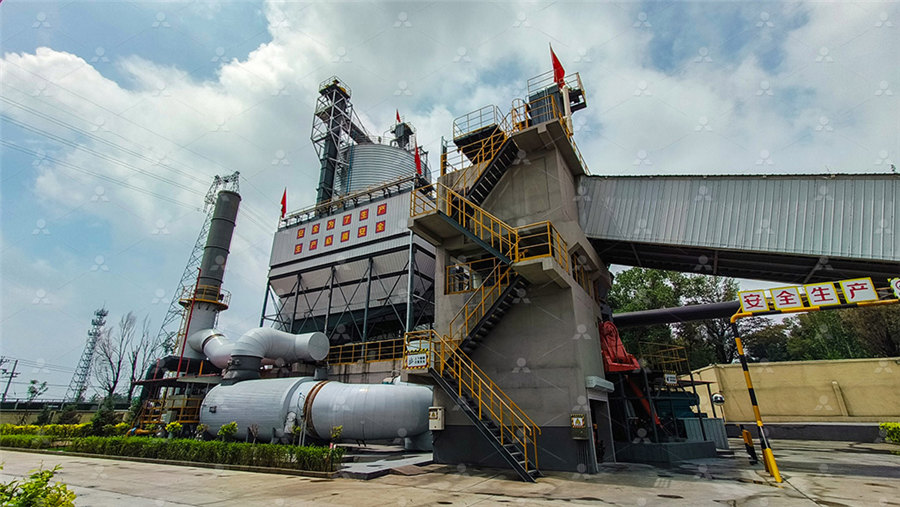
(PDF) Process development to recover rare earth metals from
2015年8月31日 The escalating demand of rare earth metals (REMs) in various applications and their continuous depleting ores have laid emphasis to produce metals from their complex resources by developing energy 2023年11月9日 Rare earth ore processing cases The following takes the most common bastnaesite and beach mineral sand as examples to provide a reference for your rare earth processing Case 1 American bastnaesite processing Unlocking Potential: Rare Earth Elements Processing 2016年4月14日 Diamond Processing Flow Chart #3 This flowsheet illustrates a more complex diamond recovery method developed in recent years With variations it can be used to process 100 to 500 tons per hour of Kimberlite ore and is also arranged to handle weathered or soft oresDiamond Processing Flow Chart of BeneficiationRare Earths mining process, how to extract mineral from rock and placer deposit, related processing plant flow chart and layout design read more Skip to content Menu Home; 100TPH Tantalite Ore Processing Plant in Sierra Leone 150TPH Coltan Ore Processing Plant in GhanaLead, zinc, iron, manganese, etcRare Earths Mining Processing Equipment Flow Chart JXSC
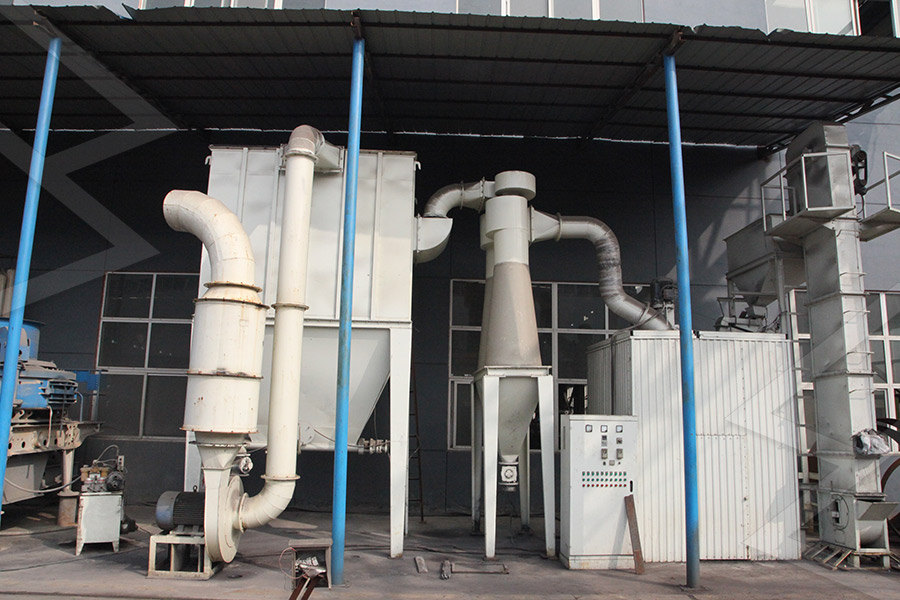
Mineral Processing and Extractive Metallurgy of the Rare Earths
2015年12月25日 In Chap 2, the most important occurrences of the rare earths were describedThis chapter will deal with what happens when the rare earths have been mined It answers the question: how are the ores processed? Mineral processing (sometimes called mineral dressing or ore dressing) is the preparation of ore from the stage that the material is Kalgoorlie Rare Earths Processing Facility Project FAQs What are Rare Earths and why are they important? Rare Earths are a group of 15 elements in the periodic table known as the Lanthanide series Rare Earths are used in the manufacture of many things we use every day – from smart phones to cars, electrical appliances, and green technologiesKalgoorlie Rare Earths Processing Facility Project FAQs LynasPDF On Jul 11, 2018, Sandra Lúcia de Moraes and others published Iron Ore Pelletizing Process: An Overview Find, read and cite all the research you need on ResearchGateIron Ore Pelletizing Process: An Overview ResearchGateHighgrade ores worldwide are depleting due to the increasing demand for valuable metal (eg, copper, gold, rare earth elements) to satisfy technological advancement and applications in A typical flowsheet for processing refractory gold ore (Sulphidic
.jpg)
(PDF) A Review of Rare Earth Mineral Processing Technology
2017年9月10日 The purpose of this paper is to comprehensively review and summarize the rare earth processing routes, the mostly employed rare earth separation methods, supply and demand of rare earth around the