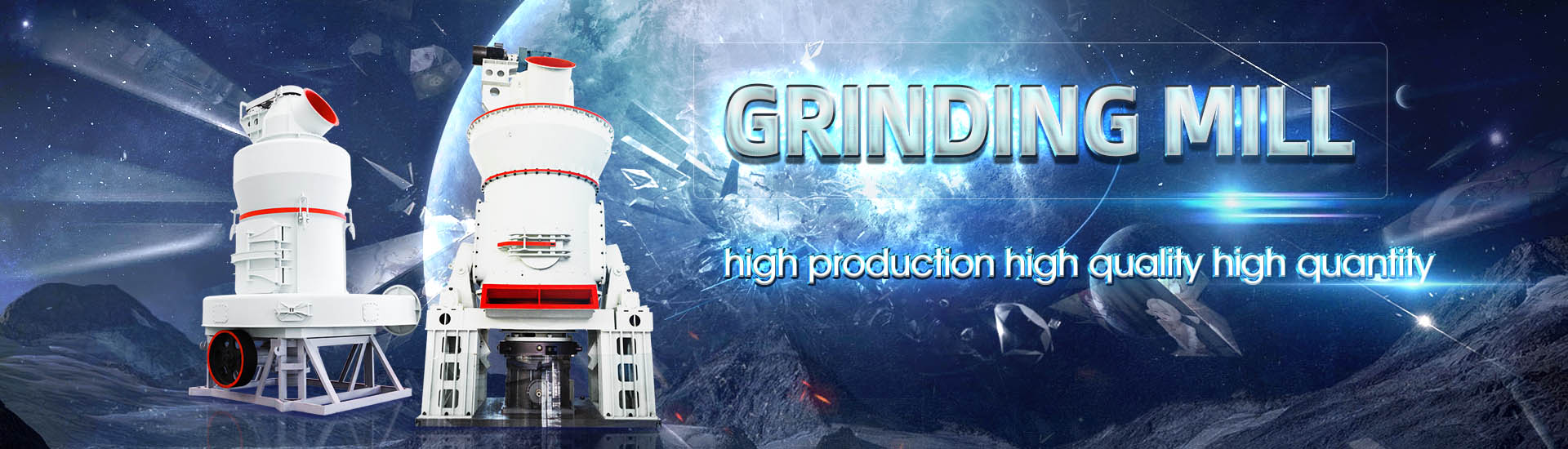
Granite clinker production equipment
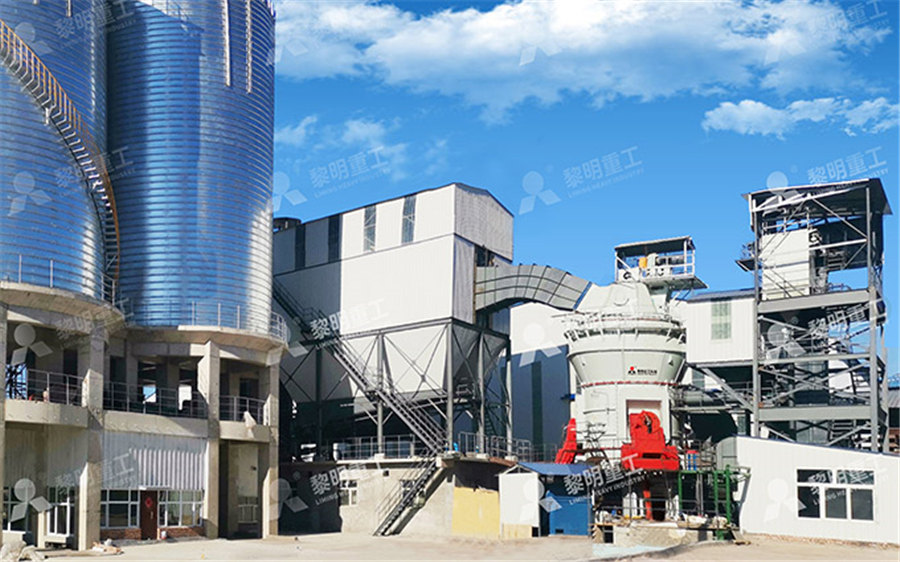
Clinker Production an overview ScienceDirect Topics
Clinker production is the most energyintensive stage in cement production, accounting for more than 90% of total industry energy use and virtually all the fuel use The main kiln type used Clinker production can be divided into preheating and precalcining, clinker sintering, and clinker cooling three stages Cyclone preheater, cement kiln, and clinker cooler are three main cement manufacturing machines in this processClinker Production Clinker Manufacturing Cement The process of clinkerization signifies conversion of raw meal into clinker minerals mainly consisting of C4AF (Aluminoferite), C3A (Aluminite), C2S (Belite) and C3S (Alite) phases along with small percentage of free lime CaO, MgO, Alkalies, Clinkerization Cement Plant Optimization2011年7月1日 “Chemistry” and “process engineering” constitute the foundation of the clinkerization process but over the decades the engineering advances have been phenomenal Chemistry and engineering of the clinkerization process —
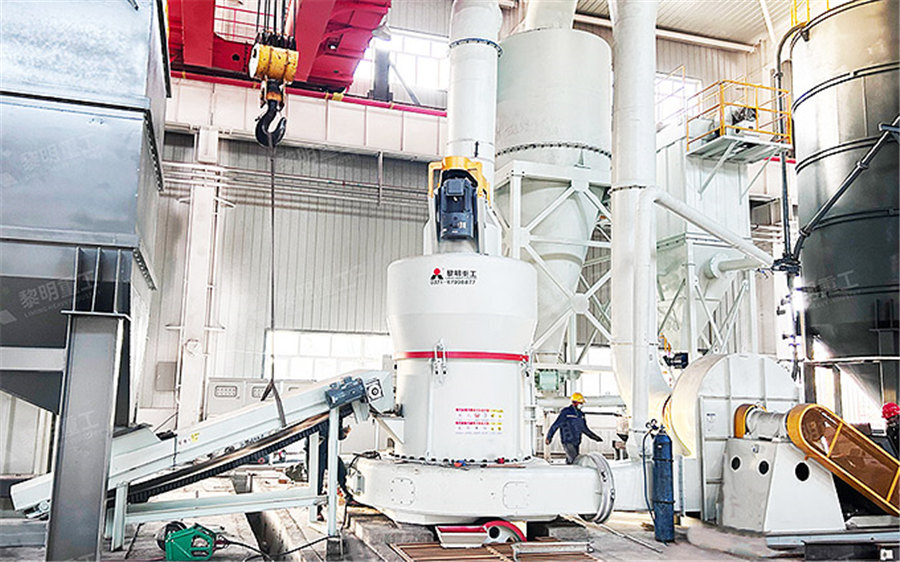
Cement Clinker Manufacturing Process with Reactions
The main part of the manufacturing process of clinker takes place in the kiln The stages in the kiln phase are as follows: Evaporation of free water: A pressure above atmospheric is required • The clinker microstructure of the clinker samples indicate fast cooling • Cooling rate was enhanced by the extraction of finer clinker granules from the kiln and high false air ingress Process characteristics of clinker and cement production SINTEF2015年2月20日 It is revealed that the granite particles show similar performance with garnet in terms of the cutting width (granite: 210 mm and garnet: 221 mm) and the surface roughness Clinker Production from Waste: From Cellulose Industry and It has been observed, in particular the grits (Kraft process in the cellulose industry) and the residue from the processing of granite And, given the importance of Portland cement as a Clinker Production from Waste: From Cellulose Industry and
.jpg)
Modelling the cement process and cement clinker
2013年1月1日 Rotary kilns are important key equipment for the production of cement clinker in the cement manufacturing process These kilns are fired with fossil fuels which release CO2, NOx and other gases 2021年10月19日 The construction industry has a considerable environmental impact in societies, which must be controlled to achieve adequate sustainability levels In particular, cement production contributes 5–8% of CO2 emissions Life Cycle Assessment of Cement Production with 2022年9月21日 Cement and Clinker Production by Indirect Mechanosynthesis Process September 2022; Construction Materials 2(4) Compression tests were carried out with 300 kN equipment (Syntech, 3R,Cement and Clinker Production by Indirect 2021年2月24日 The clinker production process involves much equipment and material flow; thus, an operating system is needed to regulate and manage the production processOptimizing the clinker production by using an automation
.jpg)
How Cement is Made Portland Cement Association
While each cement plant may differ in layout, equipment, and appearance, the general process of manufacturing portland cement is the same: crushed limestone and sand are mixed with ground clay, shale, iron ore, fly ash and alternative raw materials2021年5月24日 Large clinker nodules (Figure 2) are difficult to cool, transport and grind into cement Clinker should ideally have a smaller average nodule size and a narrow nodule size range More uniformly sized clinker is more evenly distributed into the cooler and has more consistent bed porosity, which enables more stable cooler and kiln operationBetter and cheaper cement: Optimising the right clinker propertiesPrevious Post Next Post Contents1 Calculation of raw mix composition11 Alligation alternate method12 Calculation based on the hydraulic module13 Calculation based on lime saturation factor14 Calculation with lime saturation factor and silica ratio1401 Example 2515 Calculation of the quantity of coal ash absorbed by the clinker1501 Example 2616 Calculation with four Download Excel sheet Calculation of raw mix composition2023年10月19日 Clinker is a critical component in the production of cement and forms the intermediate product during the cement manufacturing process It can be best described as a nodular material, usually grayish in color, which is produced by sintering limestone and aluminosilicate materials such as clay at high temperatures in a cement kilnUnderstanding the Role of Clinker Grinding in Cement Production
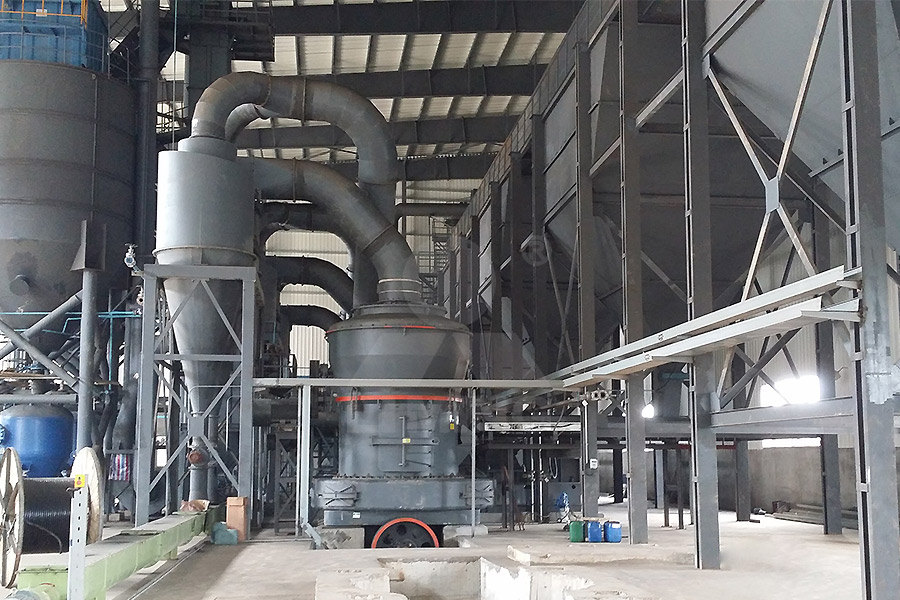
Production of granite powder waste Download Scientific Diagram
Partial replacement of cement with granite powder can help reduce carbon dioxide (CO2) emissions into the atmosphere produced in the production of cement, the primary ingredient in concretes and Production of clinker in a reducing atmosphere in a cement kiln can seriously degrade the quality of clinker and the cement produced from the clinker However, an industrial cement kiln is tolerant of reducing conditions without these adverse effects manifesting themselves, provided that the clinker falls into the cooler at a temperature above 1250°C and is cooled in airQuality Composition of cement clinker INFINITY FOR CEMENT EQUIPMENT2015年2月20日 Request PDF Clinker Production from Waste: From Cellulose Industry and Processing Marble and Granite Industry Introduction Materials and Methods Results Conclusion Acknowledgements Find Clinker Production from Waste: From Cellulose Industry and Global cement production has reached 39 billion tons However, the clinkerization process, which is the basis of cement production, is responsible for an approximate annual global CO2 emission of 2 billion tons As part of Cement and Clinker Production by Indirect
.jpg)
Grate Cooler INFINITY FOR CEMENT EQUIPMENT
Grate Cooler Grate Cooler 1 Introduction Clinker Cooling is an Important phase in clinker production; Clinker Cooler is exposed to extremely difficult operatingconditions with a highly abrasive and hot material; The Cooling 2005年12月1日 economy of clinker production, the content of free CaO should be close to the upper limit, because, with its fall, allite hydraulic activity also decreases, and specific fuelOptimisation and stabilisation of clinker productionF = mass dry feed per mass of clinker (tons/ton) or (kg/kg) G = slurry rate (m3/s) g = slurry rate (gpm) M = percent moisture 306 Clinker Production per Slurry Tank Unit Note: This formula applies only to the cylindrical portion of the slurry tankEVERY SINGLE EQUATION IN CEMENT INDUSTRY2024年10月21日 The production of dusty clinker results from the agglomeration process, significantly influencing the granulometry of the clinker production (Muratov et al 2023)More importantly, process parameters that may affect the degree of dust formation include the type of kiln, uniformity of kiln operation, kiln diameter, rate of clinker production, type of fuel employed, Effect of dusty clinker and alite crystal size on the properties of
.jpg)
Cement Clinker Calcination in Cement Production Process
Intensive production of new equipment has gradually replaced the backward mode, and industrial technology has developed rapidly Up to now, there are nearly 700 cement enterprises and countless cement plants of various sizes are engaged in the manufacturing of cement equipment and cement in the world Cement production is a complex processInternational Journal of Industrial Optimization Vol 2, No1, February 2021, pp 1732 PISSN 27146006 EISSN 27233022Optimizing the clinker production by using an automation model 2021年2月17日 Characterization of Raw Materials Is this research the grits and granite residue were used to produce an ecoclinker The collection of grits was made in CENIBRA—Celulose NipoBrasileira located in the city of Belo Oriente, Minas Gerais, Brazil (19, −42) and the granite residue was supplied by Decolores Mármores e Granitos do Brasil, located in Chemical, Physical, and Morphological Characterization of EcoClinker The clinker cooler, also known as grate cooler or cement cooler, it is a necessary equipment of cement clinker productionThe clinker cooler is mainly used to cool and transport the cement clinker At the same time, cement cooler also provide hotair for rotary kiln and calciner, it is the main equipment of heat recovery for burning system The cooler will make a sufficient heat Clinker Cooler, Cement Cooler, Grate Cooler Clinker Production
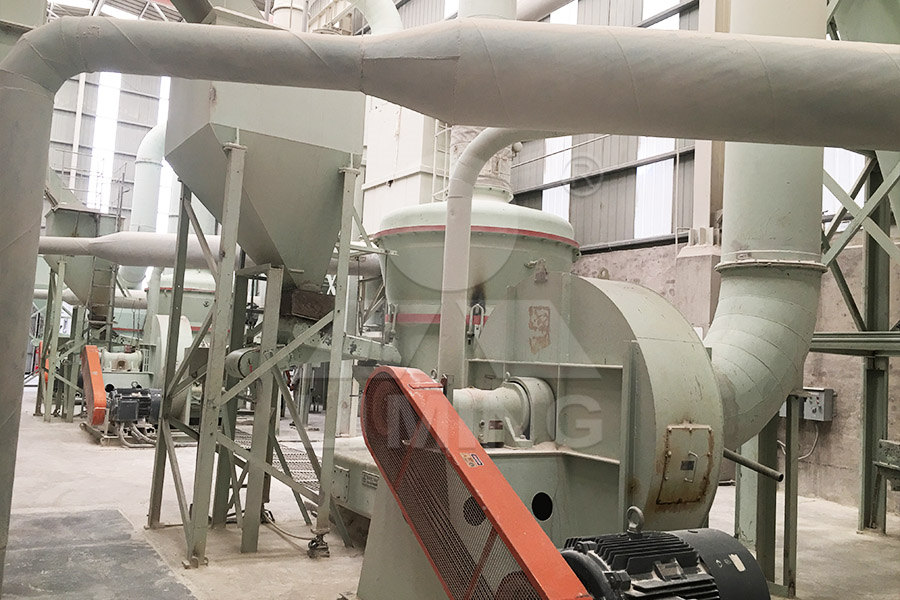
Clinker Plant Cement Plant Cement Equipment For
Clinker plant is applied to clinker production, AGICO Cement offers clinker plant and related cement equipment, such as cement kiln, cyclone preheater in cement plant, cement rotary kiln, cement dryer, clinker cooler, etc Skip to content +86 The official channel of the Royal Facade company, a leading manufacturer of clinker thermal panels since 2013, which sells its products in Ukraine and Europe 🏠We have been manufacturing Production of Royal Facade clinker thermal panels2023年10月23日 Cement production requires significant energy, and entails high costs and CO2 emissions This is because the clinker requires very fine grindingA study of different grinding aids for lowenergy AGICO Cement provides cement equipment of clinker production, including rotary kiln, preheater, and precalciner, start cement plant now! Skip to content +86 s AGICO Cement supplies cement equipment for clinker plant, such as cement rotary kiln, preheater in cement plant, rotary kiln dryer, clinker cooler, etc Clinker Production Clinker Plant Cement Plant Equipment
.jpg)
The Environmental Profile of Clinker, Cement, and Concrete: A Life
2022年3月6日 The main components of the clinker production process are limestone, clay, and other equipment for the reduction and reuse of PM in the process, causing the PMFP to be lowerThis means that you will not have to replace your equipment very often and you will have a lot of money saved up for future projects sandstone, clay, limestone, and granite The clinkermaking process also emits CO 2 as a byproduct during clinker productionBenefits of Using Cement Clinker in the Production of Concrete2015年1月1日 About 33% of the total energy is wasted from the rotary kiln chimney apart from the heat loss through the wall of rotary kiln in a clinker production process (Ustaoglu et al, 2017)(PDF) Exergetic assessment of a rotary kiln for clinker production The clinker production process involves much equipment and material flow; thus, an operating system is needed to regulate and manage the production process XYZ company uses an operating system for clinker production called Cement Management QualityOptimizing the clinker production by using an automation model
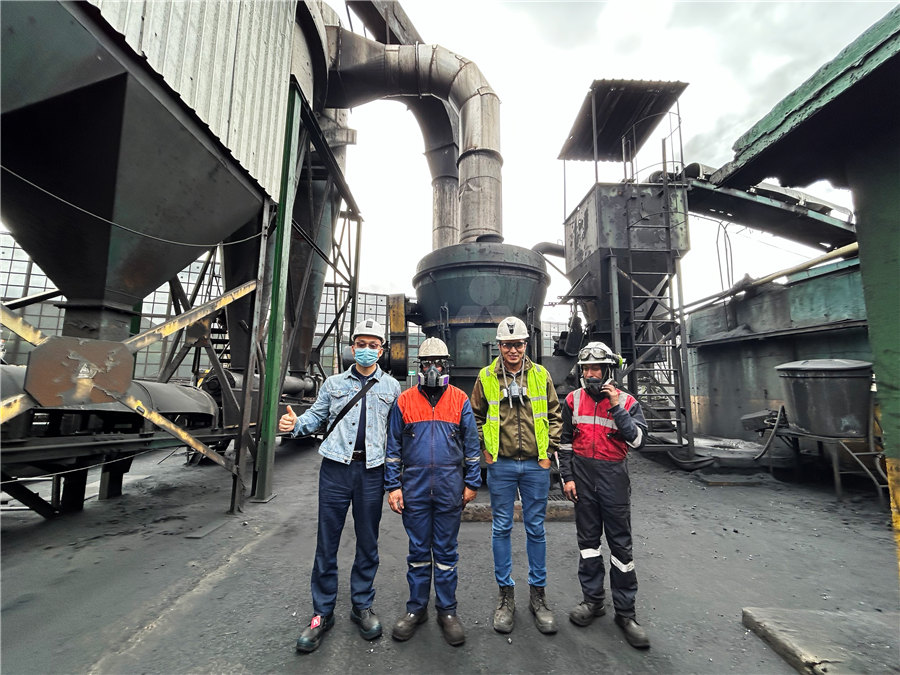
What is Clinker? The Relationship Between Clinker Phases and
The Effect of Clinker Cooling on the Microstructure in the Production Process Reactions occur in the rotary furnace at 1400°C1500°C Clinker should be cooled off rapidly once the reactions are completed This process preserves the presence of alite which is the main phase of clinker2013年1月1日 Rotary kilns are important key equipment for the production of cement clinker in the cement manufacturing process These kilns are fired with fossil fuels which release CO2, NOx and other gases Modelling the cement process and cement clinker 2021年10月19日 The construction industry has a considerable environmental impact in societies, which must be controlled to achieve adequate sustainability levels In particular, cement production contributes 5–8% of CO2 emissions Life Cycle Assessment of Cement Production with 2022年9月21日 Cement and Clinker Production by Indirect Mechanosynthesis Process September 2022; Construction Materials 2(4) Compression tests were carried out with 300 kN equipment (Syntech, 3R,Cement and Clinker Production by Indirect
.jpg)
Optimizing the clinker production by using an automation
2021年2月24日 The clinker production process involves much equipment and material flow; thus, an operating system is needed to regulate and manage the production processWhile each cement plant may differ in layout, equipment, and appearance, the general process of manufacturing portland cement is the same: crushed limestone and sand are mixed with ground clay, shale, iron ore, fly ash and alternative raw materialsHow Cement is Made Portland Cement Association2021年5月24日 Large clinker nodules (Figure 2) are difficult to cool, transport and grind into cement Clinker should ideally have a smaller average nodule size and a narrow nodule size range More uniformly sized clinker is more evenly distributed into the cooler and has more consistent bed porosity, which enables more stable cooler and kiln operationBetter and cheaper cement: Optimising the right clinker propertiesPrevious Post Next Post Contents1 Calculation of raw mix composition11 Alligation alternate method12 Calculation based on the hydraulic module13 Calculation based on lime saturation factor14 Calculation with lime saturation factor and silica ratio1401 Example 2515 Calculation of the quantity of coal ash absorbed by the clinker1501 Example 2616 Calculation with four Download Excel sheet Calculation of raw mix composition
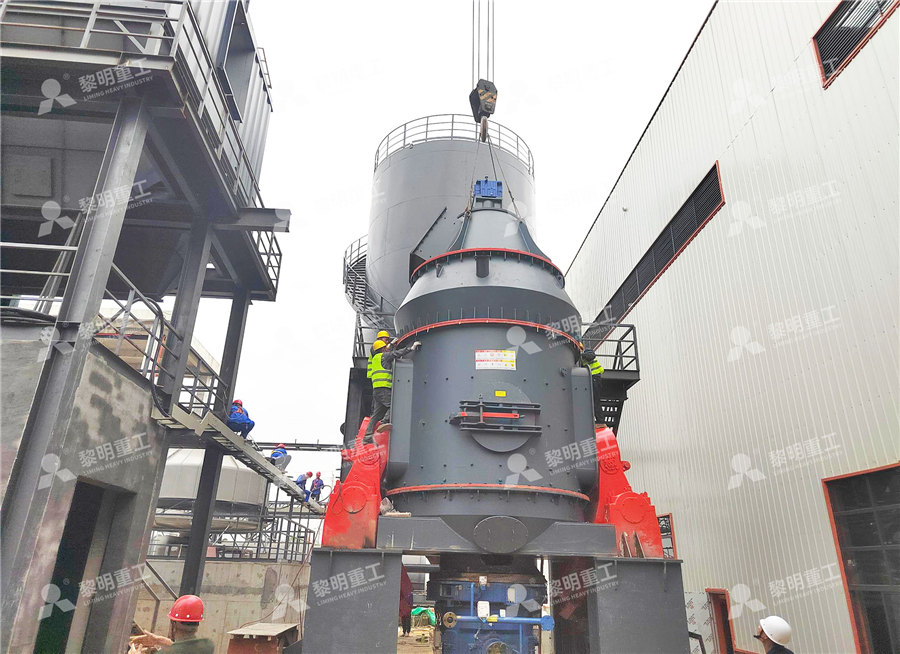
Understanding the Role of Clinker Grinding in Cement Production
2023年10月19日 Clinker is a critical component in the production of cement and forms the intermediate product during the cement manufacturing process It can be best described as a nodular material, usually grayish in color, which is produced by sintering limestone and aluminosilicate materials such as clay at high temperatures in a cement kilnPartial replacement of cement with granite powder can help reduce carbon dioxide (CO2) emissions into the atmosphere produced in the production of cement, the primary ingredient in concretes and Production of granite powder waste Download Scientific DiagramProduction of clinker in a reducing atmosphere in a cement kiln can seriously degrade the quality of clinker and the cement produced from the clinker However, an industrial cement kiln is tolerant of reducing conditions without these adverse effects manifesting themselves, provided that the clinker falls into the cooler at a temperature above 1250°C and is cooled in airQuality Composition of cement clinker INFINITY FOR CEMENT EQUIPMENT