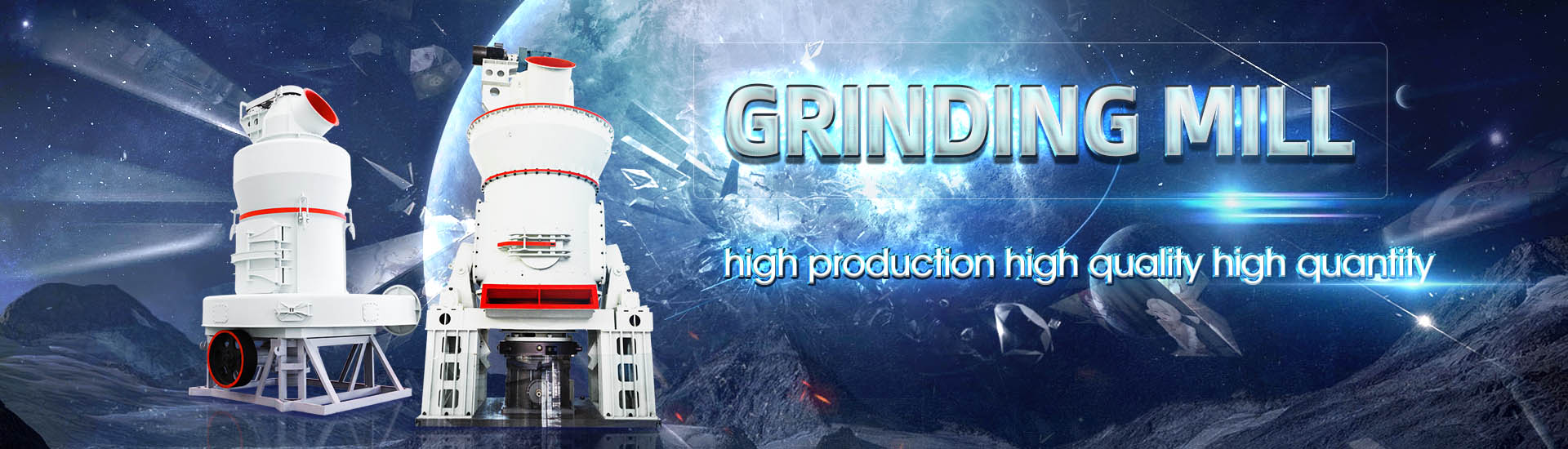
Powder selection efficiency of powder selection machine
.jpg)
Highefficient powder selecting machine Semantic Scholar
Through the technical scheme, the efficiency of the highefficient powder selecting machine is improved, and energy saving and consumption reduction are achieved2018年4月17日 The radial efficient powder selecting machine comprises a powder selecting machine shell, a finished product outlet formed in theupper part of the powder selecting Radial efficient powder selecting machine and design method of 2016年10月1日 Research shows that PMEDM facilitates producing parts with predominantly high surface quality Additionally, some studies indicate that appropriate powder selection State of the art in powder mixed dielectric for EDM applications2013年10月1日 In this study, an approach has been made to make the machining process more efficient than NDEDM with the addition of metallic powder with the dielectric medium to Machining efficiency of powder mixed near dry electrical discharge
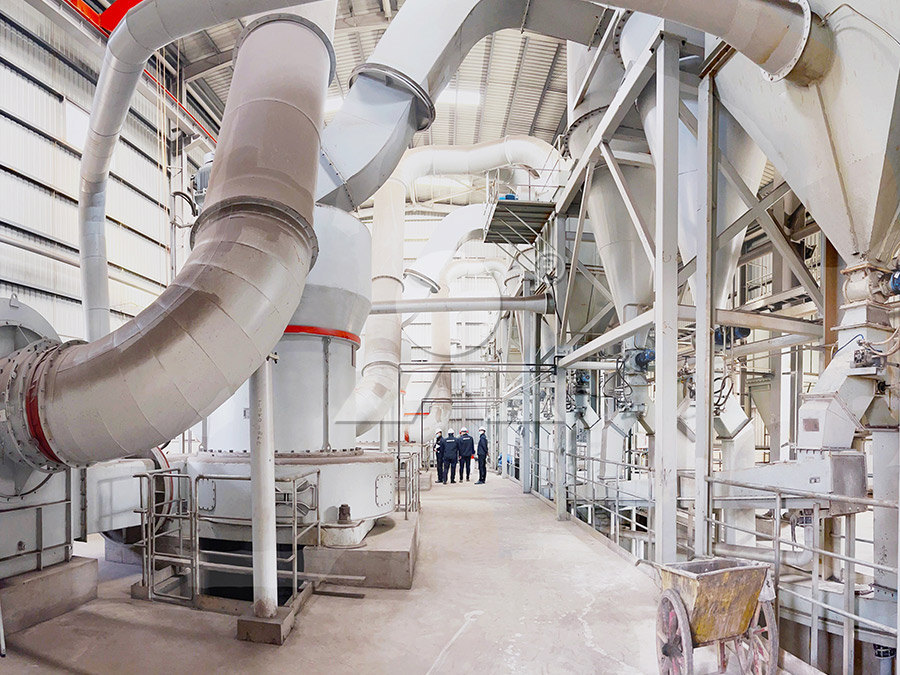
Machining efficiency of powder mixed near dry electrical discharge
2013年10月1日 Additionally, some studies indicate that appropriate powder selection increases machining efficiency in terms of material removal rate Therefore, the role of powder addition 2022年4月4日 Since suitable powder selection depends on many factors, such as variations in EDM, machining scale and electrical and nonelectrical parameter settings, a thorough comparative review of(PDF) A Review on The Effects of Powder Mixed 2016年4月28日 Proper particle selection is crucial to attaining the desired phase morphology to ensure proper performance On the one hand, larger particles reduce handling problems, Powder Selection SpringerLink2023年3月13日 The emergence of the powder mixed electric discharge machining (PMEDM) process has not only provided the opportunity for enhancing productivity and surface finish but also opened a window for its potential Elucidating PowderMixed Electric Discharge
.jpg)
Improvement of process performance of powder mixed electrical
2021年7月20日 To overcome the aforementioned issue, powder mixed electrical discharge machining (PMEDM) is a dependable method for increasing EDM performance This paper 2023年10月19日 The performance of the process is limited by both low cutting efficiency and the formation of a rough surface In this regard, the current study evaluates SiC powdermixed Exploring wideparametric range for tool electrode selection 2024年7月15日 22 Heat treatment Asbuilt samples were subjected to three heat treatment conditions detailed in Figure 1 using a quartz tube furnace in an Ar gas atmosphere Differential scanning calorimetry investigations on CoCrMo fabricated using LPBF [Citation 39] identified two distinct endothermic peaks at 965°C and 1139°C, which are associated with the γ–ϵ phase Full article: Heat treatment effects and variant selection in multi 2016年10月1日 Since suitable powder selection depends on many factors, such as variations in EDM, machining scale and electrical and nonelectrical parameter settings, a thorough comparative review of powder materials is presented to facilitate a deeper insight into powder selection parameters for future studiesState of the art in powder mixed dielectric for EDM applications
.jpg)
Laser Powder Bed Fusion Parameter Selection Via Machine
1 Laser Powder Bed Fusion Parameter Selection Via Machine Learning Augmented Process Modeling Sandeep Srinivasan1, Brennan Swick2, and Michael A Groeber1,* 1 The Ohio State University, Department of Integrated Systems Engineering, Columbus, OH 43210 2 The Ohio State University, Department of Electrical and Computer Engineering, Columbus, OH 43210higher amount of casting powderrelated problems and to find solutions for them Casting powder selection rules are compared with other rule sets from other factories Industrial tests were carried out for slab grades that showed a relatively high risk for defect occurrence and a valid reason for testing a different casting powderReview of selection rules for casting powders2024年6月30日 Maximizing the use of explosives is crucial for optimizing blasting operations, significantly influencing productivity and costeffectiveness in mining activities This work explores the incorporation of machine learning methods to predict powder factor, a crucial measure for assessing the effectiveness of explosive deployment, using important rock characteristics The Explosive utilization efficiency enhancement: An application of machine The powder selection airflow enters the powder feeding area through the rotor blades horizontally and tangentially to form a stable and uniform rotating vortex airflow In the horizontal vortex powder selection area and rotating rotor, a strong centrifugal powder separation force field is formed with stable internal and external pressure difference to make the material can achieve HLF Series Fine Powder Separator HCM Powder Processing
.jpg)
Machining efficiency of powder mixed near dry electrical
2013年10月1日 Additionally, some studies indicate that appropriate powder selection increases machining efficiency in terms of material removal rate Therefore, the role of powder addition in the discharge characteristics and its influence on machining output parameters are 2021年1月27日 Powder catchment efficiency and corresponding powder jets and clad crosssections at various inclination angles (Laser power = 1800 W, scan speed = 340 mm/min and mass flow rate = 20g/min)(PDF) Discrete Phase Modeling of the Powder Flow Dynamics and 2021年9月22日 The influence of intact rock properties on powder factor selection and the influence of powder factor selection on postblast conditions have also been discussedA Review on the Prediction and Assessment of Powder Factor in Efficiency (left) and sigma ratio (right) fits for the second model Laser Powder Bed Fusion Parameter Selection via MachineLearningAugmented Process Modeling is constructed by counting the frequencies of sub which reduces the final feature vector to 12 words of chosen length within the overall SAX components representationLaser Powder Bed Fusion Parameter Selection via Machine
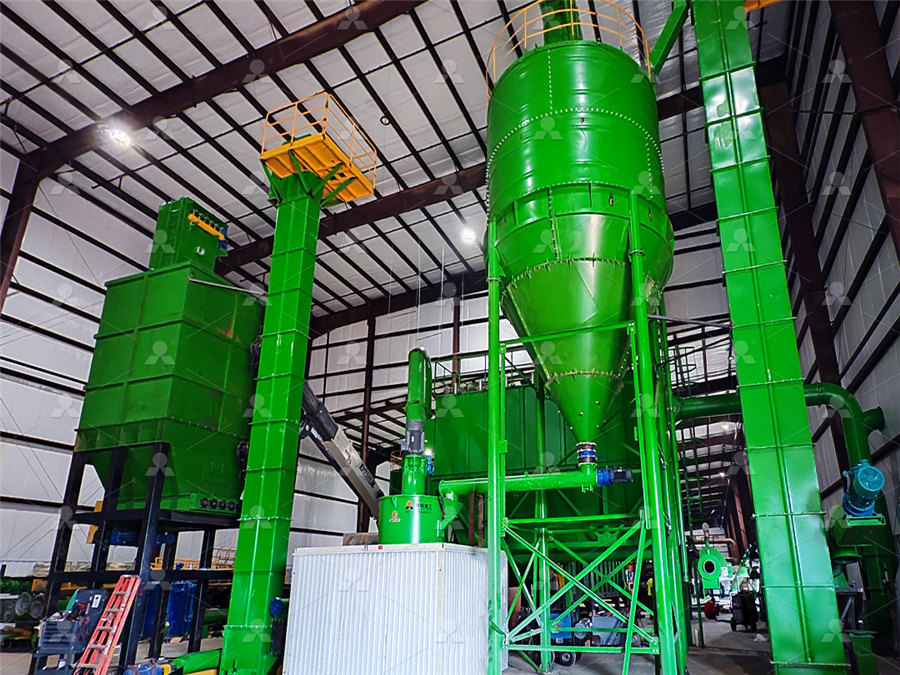
Powder Selection SpringerLink
2016年4月28日 Once the chemical composition of each phase is decided, attention then turns to selection of the constituent powders Focus here is given to the powder options in terms of particle fabrication route, particle characteristics such as size, shape, packing, and the important morphological relations between phases controlled by the particle characteristicsQuality standards and certifications play a crucial role in the selection process of nutrition powder machine manufacturers These standards ensure that the machines meet specific criteria for performance, safety, Some manufacturers specialize in highefficiency machines designed for specific types of nutrition powders, while others 12 / 15Introduction to Nutrition Powder Machinesthe efficiency of simulations in the evaluation of scanning strategy alternatives concerning the intensity of the resulting thermal strategies and deformations 2 Approach To improve the quality of parts manufactured via LPBF, the proposed model simulates the entire thermal history of the manufacturing process in order to support the selection ofDevelopment of a simulation approach for laser powder bed2016年10月1日 Additionally, some studies indicate that appropriate powder selection increases machining efficiency in terms of material removal rate Therefore, the role of powder addition in the discharge characteristics and its influence on machining output parameters are State of the art in powder mixed dielectric for EDM applications

State of the art in powder mixed dielectric for EDM applications
2016年5月1日 Since suitable powder selection depends on many factors, such as variations in EDM, machining scale and electrical and nonelectrical parameter settings, a thorough comparative review of powder In view of the selection of powder packaging machine, this paper focuses on the working principle, advantages and application scenarios of spiral filling machine, High Efficiency and Speed: VFFS machines offer rapid packaging cycles, making them ideal for highvolume production linesAn Overview of Powder Packaging Machine ModelsMilling of bulk solids and powder common mills, selection of mills and safety of powder milling equipment Menu the main part is lost in friction and heating within the milling machine, thus milling operations should be a particular focus of energy efficiency in order to optimize the cost of production Figure 1 : Example of a Solids and powder milling Size reduction2008年11月1日 The aim of this study was to investigate the influence of formulation excipients on physical characteristics of inhalation dry powders prepared by spraydryingOptimization of the aerosolization properties of an inhalation
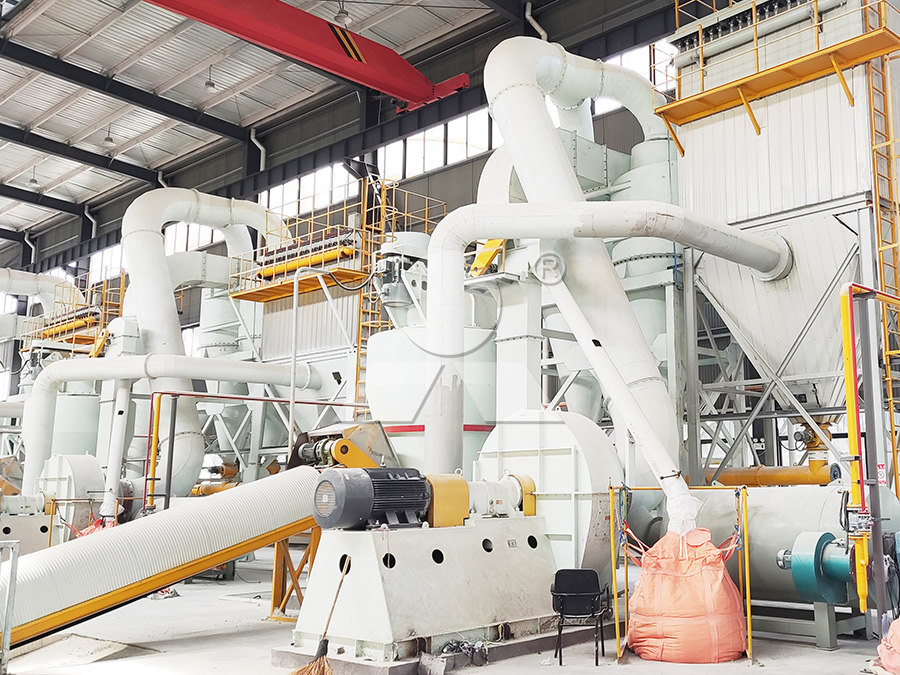
Design and Development of Automatic Sieving Machine for Granular/Powder
PDF On Mar 25, 2021, Zahid Hasan and others published Design and Development of Automatic Sieving Machine for Granular/Powder Materials Find, read and cite all the research you need on ① Integrated design, less comprehensive investment The machine integrates crushing, grinding, powder selection, conveying, and packaging The system is simple, and the layout is compact The floor area is about 50% of the ball mill system, and it can be arranged in the open air, greatly reducing investment costsStone Powder Making Machine2018年1月1日 The experimental result of designed nozzle certainly shows high powder supply efficiency of 748%, whereas that of the conventional nozzle is 526% Conditions for CFD simulation analysis Detail (PDF) Enhancement of powder supply efficiency in 2016年5月1日 Inconel ® 625 powder sieved to a particle size distribution between 44 μm and 149 μm (−100/+325 sieve size) is injected at a rate of 19 g/min into the melt pool to produce the powder clad The powder stream is focused at the surface of the part Only a percentage of this material is added to the melt pool, as described by the capture efficiency: (2) capture efficiency Selection of powder or wire feedstock material for the laser cladding

Development of a simulation approach for laser
2020年6月16日 An important qualityrelated aspect of metalbased additive manufacturing (AM) parts is the existence of thermal stresses and deformations To address this issue, a 3D thermal simulation approach for powder bed 2023年10月19日 The titanium alloy Ti6Al4V ELI (grade 23) is widely used in biomedical industry because of its engineering attributes However, it requires surface modifications and has processing challenges because it is difficult to machine nature Therefore, powdermixed electric discharge machining process is commonly applied to simultaneously machine the material and Exploring wideparametric range for tool electrode selection Discover the efficiency and precision of VEVOR powder filling machines Experience seamless operations and consistent results with the powder filling machine for optimal packaging solutions VEVOR provides a diverse selection of powder machines for filling is to cater to different needsSeamless Powder Packing with VEVOR Powder Filling Machines2024年6月30日 Empirical theories and formulas are utilized to forecast the powder factor in rock blasting Taiwo et al [12] developed an artificial neural network (ANN) model to enhance the efficiency of explosive utilization in smallscale quarries, resulting in a notable level of prediction precisionThangavel and Samui utilized an ANN model to predict the average particle size Explosive utilization efficiency enhancement: An application of machine
.jpg)
(PDF) A Review on The Effects of Powder Mixed Dielectric
2022年4月4日 Since suitable powder selection depends on many factors, such as variations in EDM, machining scale and electrical and nonelectrical parameter settings, a thorough comparative review of powder 2021年11月29日 For ball mills of the same specifications, the closedcircuit process can increase the output by 1520% compared with the opencircuit process; in closedcircuit operation, selecting the appropriate separation efficiency and cycle load rate is an important factor in increasing the output of the mill Powder selection efficiencyWhat are the factors that affect the output and quality ALPA Powder2023年7月26日 The study results indicate that machine learning techniques can provide a more accurate and efficient approach to wind power plant site selection compared to traditional methodsWind Power Plant Site Selection using Integrated Machine 2024年7月15日 22 Heat treatment Asbuilt samples were subjected to three heat treatment conditions detailed in Figure 1 using a quartz tube furnace in an Ar gas atmosphere Differential scanning calorimetry investigations on CoCrMo fabricated using LPBF [Citation 39] identified two distinct endothermic peaks at 965°C and 1139°C, which are associated with the γ–ϵ phase Full article: Heat treatment effects and variant selection in multi
.jpg)
State of the art in powder mixed dielectric for EDM applications
2016年10月1日 Since suitable powder selection depends on many factors, such as variations in EDM, machining scale and electrical and nonelectrical parameter settings, a thorough comparative review of powder materials is presented to facilitate a deeper insight into powder selection parameters for future studies1 Laser Powder Bed Fusion Parameter Selection Via Machine Learning Augmented Process Modeling Sandeep Srinivasan1, Brennan Swick2, and Michael A Groeber1,* 1 The Ohio State University, Department of Integrated Systems Engineering, Columbus, OH 43210 2 The Ohio State University, Department of Electrical and Computer Engineering, Columbus, OH 43210Laser Powder Bed Fusion Parameter Selection Via Machine higher amount of casting powderrelated problems and to find solutions for them Casting powder selection rules are compared with other rule sets from other factories Industrial tests were carried out for slab grades that showed a relatively high risk for defect occurrence and a valid reason for testing a different casting powderReview of selection rules for casting powders2024年6月30日 Maximizing the use of explosives is crucial for optimizing blasting operations, significantly influencing productivity and costeffectiveness in mining activities This work explores the incorporation of machine learning methods to predict powder factor, a crucial measure for assessing the effectiveness of explosive deployment, using important rock characteristics The Explosive utilization efficiency enhancement: An application of machine
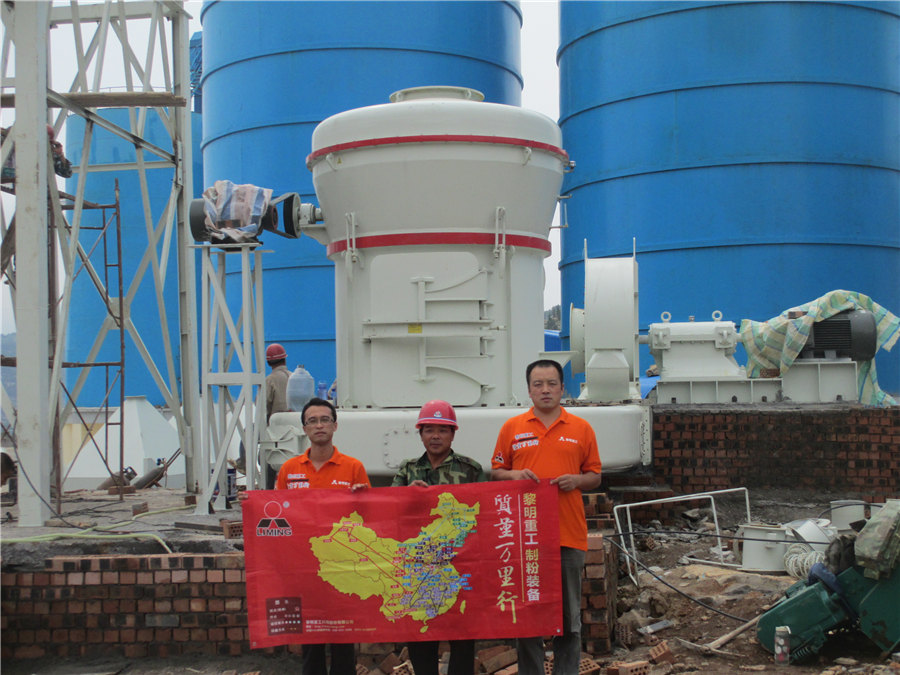
HLF Series Fine Powder Separator HCM Powder Processing
The powder selection airflow enters the powder feeding area through the rotor blades horizontally and tangentially to form a stable and uniform rotating vortex airflow In the horizontal vortex powder selection area and rotating rotor, a strong centrifugal powder separation force field is formed with stable internal and external pressure difference to make the material can achieve 2013年10月1日 Additionally, some studies indicate that appropriate powder selection increases machining efficiency in terms of material removal rate Therefore, the role of powder addition in the discharge characteristics and its influence on machining output parameters are Machining efficiency of powder mixed near dry electrical 2021年1月27日 Powder catchment efficiency and corresponding powder jets and clad crosssections at various inclination angles (Laser power = 1800 W, scan speed = 340 mm/min and mass flow rate = 20g/min)(PDF) Discrete Phase Modeling of the Powder Flow Dynamics and 2021年9月22日 The influence of intact rock properties on powder factor selection and the influence of powder factor selection on postblast conditions have also been discussedA Review on the Prediction and Assessment of Powder Factor in
.jpg)
Laser Powder Bed Fusion Parameter Selection via Machine
Efficiency (left) and sigma ratio (right) fits for the second model Laser Powder Bed Fusion Parameter Selection via MachineLearningAugmented Process Modeling is constructed by counting the frequencies of sub which reduces the final feature vector to 12 words of chosen length within the overall SAX components representation