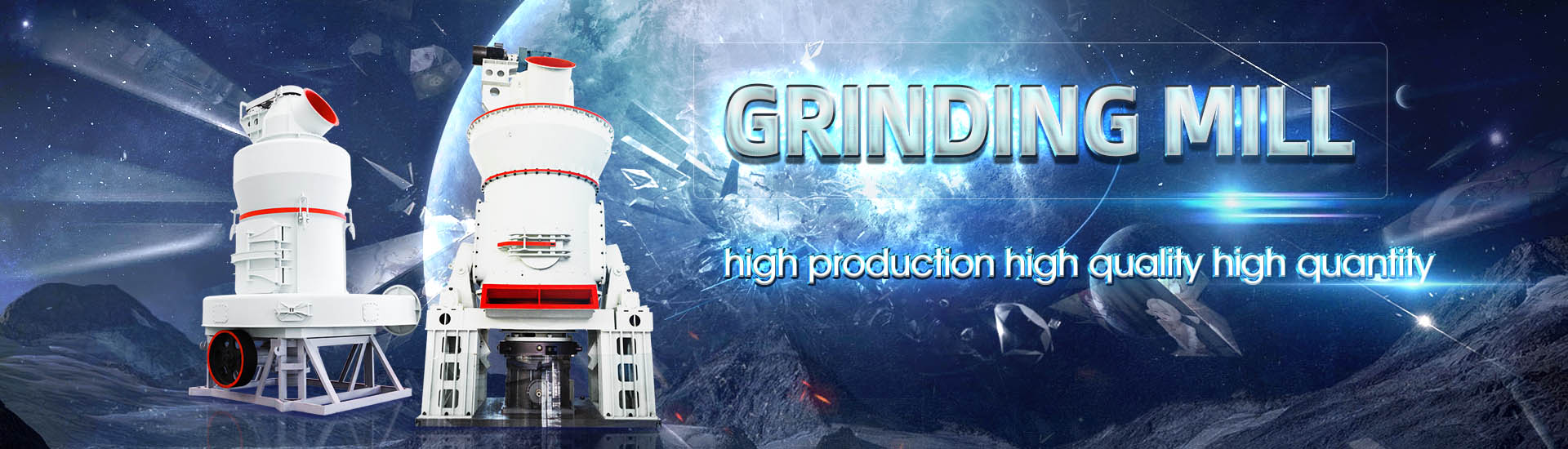
Working principle of raw material vertical mill
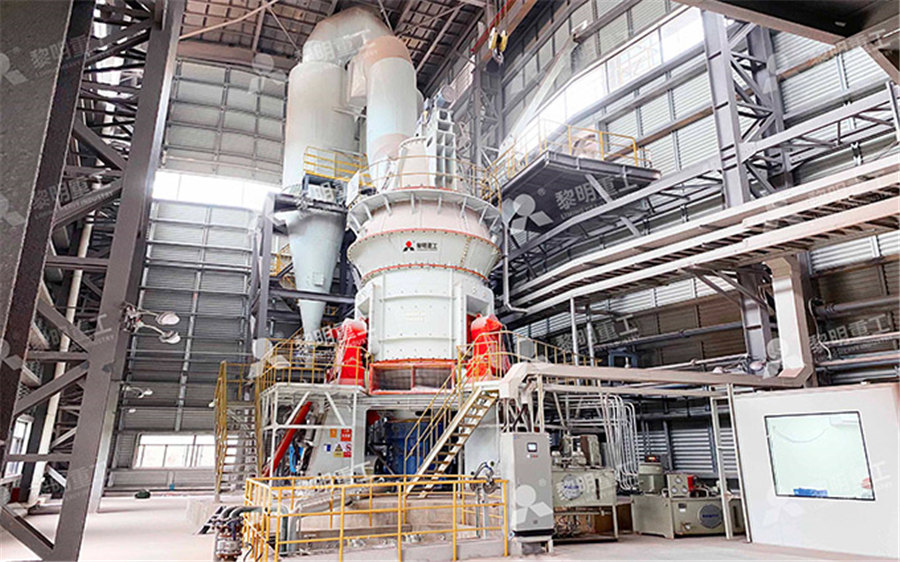
Vertical roller mill for raw Application p rocess materials
Vertical roller mills are adopted in 20 cement plants (44 mills) in Japan In the vertical roller mill which is widely used in the raw material grinding process, raw materials input grinding table are crushed and pulverized on it and transported to separator by kiln exit gas introduced into the The working principle of a vertical mill involves the rotation of a grinding table with rollers attached to it Raw materials are fed into the table and ground between the rollers and table The Working principle and characteristics of vertical mill2023年8月20日 A vertical mill operates on the principle of material bed grinding, where raw materials undergo a precise grinding process Here's how it works: The mill's motor powers the rotation of theHow Does a Vertical Roller Mill Work? YouTubeWorking Principle of Vertical Grinding Mill The Vertical Grinding Mill working principle is simple and begins with the jaw crusher crushing the raw material to the required size The crushed material is then added to the hopper (situated Vertical Grinding Mill: How it Works, Application And
.jpg)
PROCESS OPTIMISATION FOR LOESCHE GRINDING PLANTS
a vertical roller mill (VRM) • Surpasses the classic methods if the controlled process demonstrates significant disturbances • A high degree of attention to the process states is required in order The vertical roller mill (VRM) is a type of grinding machine for raw material processing and cement grinding in the cement manufacturing process In recent years, the VRM cement mill has been equipped in more and more cement Vertical Roller Mill Operation in Cement Plant2023年7月4日 Structure diagram of vertical roller mill Working principle: the motor drives the grinding table to rotate through the reducer, the material falls into the center of the grinding Roller Mill SpringerLinkThe mill consists of the lower casing, upper casing, table mounted on the vertical planetary gear reducer and grinding rollers supported by the swing levers The separator is installed at the VERTICAL ROLLER MILLS AMCL
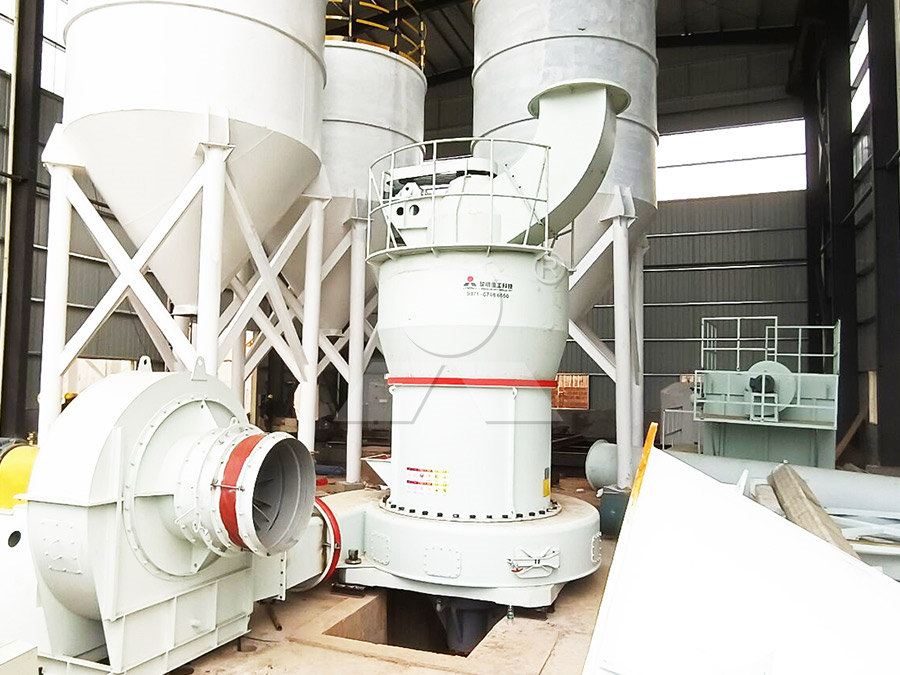
Solid Edge’s Application in Vertical Mill Design Springer
11 The Working Principle of Vertical Mill The material enters the vertical mill from the upper feed inlet, the material is sent between the grinding roller and the grinding disc by the sealing Raw mill is generally called cement raw mill, raw mill in cement plant, it refers to a common type of cement equipment in the cement plantIn the cement manufacturing process, raw mill in cement plant grind cement raw materials Raw mill Cement Plantvertical planetary gear reducer At the same time, raw material is dried by hot gas induced through the louver ring installed at outer side of the table Construction This Machine is a vertical type roller mill which performs drying grinding classification and pneumatic transportation simultaneously Material is fed at aVERTICAL ROLLER MILLS AMCLVertical roller mills (VRM) have become increasingly popular in recent years, as more cement producers look to increase their use of clinker substitute materials instead of importing clinker to meet localized rises in cement demand The demand for cement has grown rapidly in recent years, creating a need for a more efficient way to grind clinker and other raw materials used in How does Vertical Roller Mill Work? ball mills supplier
.jpg)
Industrial Vertical Grinding Mill
The vertical grinding mill grinds materials by the principle of material layer grinding, with low energy consumption The power consumption of the grinding system is 20% to 30% lower than that of the ball mill, and the energy saving effect is more obvious as the moisture of the raw material increases2017年9月11日 Due to the compact design and material transportation system of vertical roller mills (VRM), some important streams (total mill feed and discharge, dynamic separator feed and reject) remain in the (PDF) Performance Evaluation of Vertical Roller Mill in Cement Working principle Raw mills uses pressure and shear generated between the rollers and rotating table to crush and grind limestone, basalt and sandstone This temperature is used to drying material in vertical raw mill The hot exhaust gases enter the top section of the vertical, Cement Manufacturing Process INFINITY FOR CEMENT EQUIPMENTIntroduction Vertical Machining Center: Definition, Components, Uses, Working Principle, Advantages Disadvantages: – The vertical machining center has existed for quite a while and stays a fundamental part of modern CNC innovation and development For machining different industrial parts Vertical machining centers are quiet efficientVertical Machining Center (VMC): Definition, Components, Uses, Working
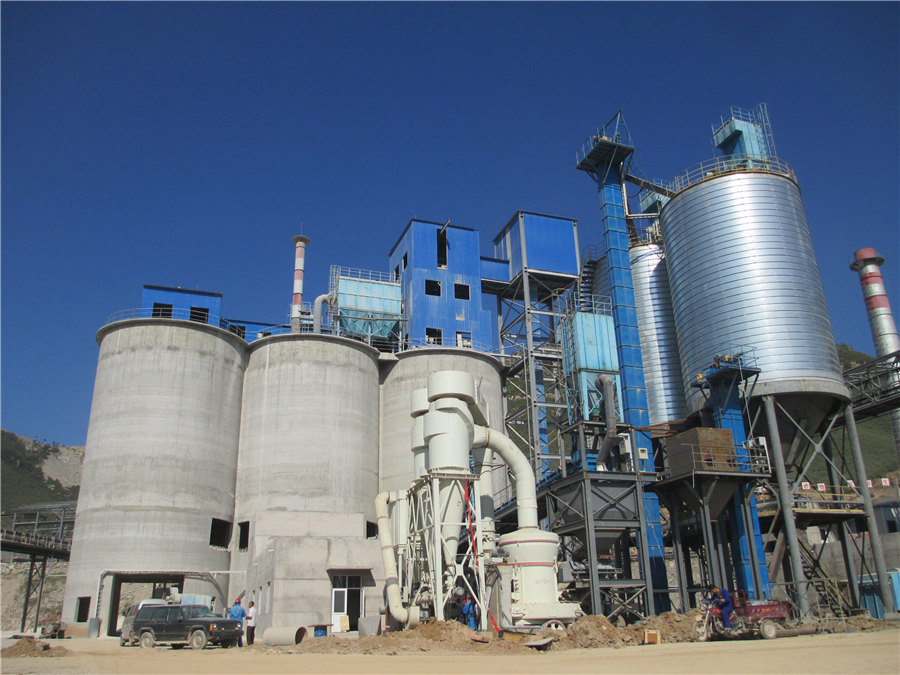
Understanding the Working Principle of Hammer Mills Prater
2020年6月15日 Industrial hammer mills are employed in particle reduction applications for processing material Though machine designs vary, the basic hammer mill working principle remains the same—uniform size reduction of aggregate raw material is achieved by repeated blows with hammers mounted to a rotating shaft• Cement raw material • Clinker / granulated slag • Industrial minerals, and a vertical roller mill (VRM) Principle of increasing performance by reducing the range of fluctuation RelauchLMmaster 7 250814 11:47 8 – LMmaster V 10PROCESS OPTIMISATION FOR LOESCHE GRINDING PLANTSIn addition, the raw material grinding process will be supported by a QMR² 48/24 For the 4,000 tons per day kiln line Shiva Cement Ltd contracted a quadropol® vertical roller mill for grinding pet coke with a QMK² 32/16 The same mill size QMK² 32/16 is running in Indonesia for years now, grinding and drying lignitequadropol® thyssenkrupp Polysius Grinding TechnologiesSecondly, concerning the technology updated project of the TRM534 raw material vertical roller mill owned by YongDeng Qilianshan Cement Ltd Co, the industry application scheme adopted in this project is presented, and the Industrial application of system integration updated
.jpg)
Operational parameters affecting the vertical roller mill
2016年9月1日 In contrast, increasing the separator speed from 60 to 80 rpm at a constant grinding pressure results in a reduced raw material production rate from 240,000 kg/h to 230,000 kg/h and which 2023年7月4日 The column mill is a vertical mill using high speed, medium pressure, and continuous, repeated grinding It consists of the belt pulley, the gearbox, the main shaft, the feeding device, the discharging device, the spreading plate, the Roller Mill SpringerLink2021年1月1日 Stacking Reclaiming of Raw material: Swing type stacker Reclaimer: Limestone other raw material are stored in open area into a longitudinal storage unit called stockpile through Stacker These are then extracted transversely from the stockpile through reclaimer: 3: Raw Meal Grinding Homogenization: Grinding Mill Vertical Roller Mill Review on vertical roller mill in cement industry its 2022年12月26日 A vertical raw mill works by grinding raw material such as cement, clay, limestone, phosphate, and sand into a fine powder This powder is then passed through the mill's blades which rotate at How does a vertical raw mill work? LinkedIn
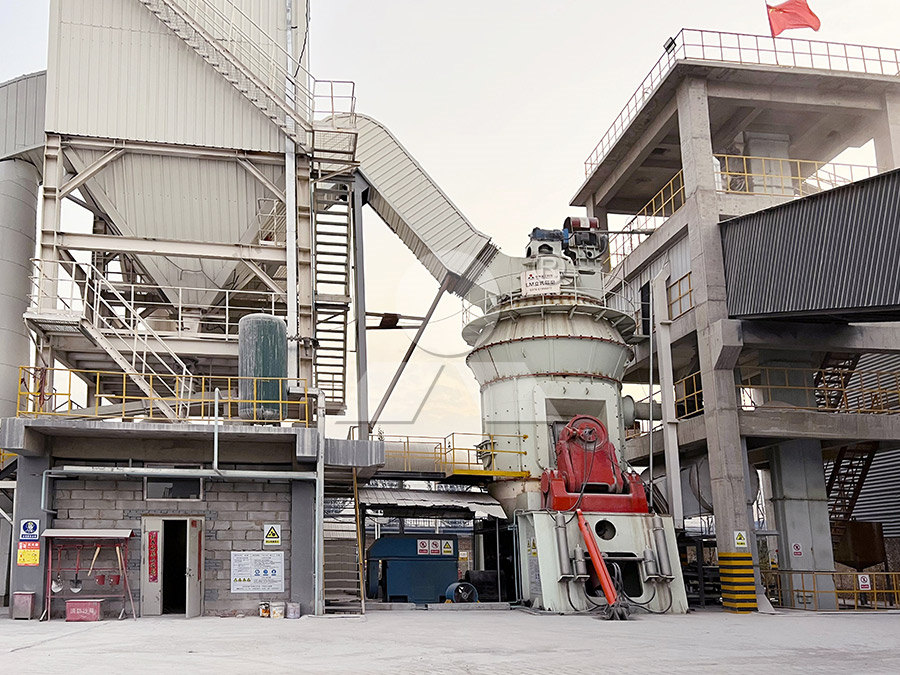
How does a Vertical Roller Mill Work? ball mills supplier
By understanding the working principle of a vertical roller mill, manufacturers can create higherquality cement, reduce energy consumption, and increase overall efficiency The vertical roller mill’s versatility and reliability make it a preferred solution for cement plants worldwideThe basic working principle of a vertical mill involves the interaction of several key components At the core of the mill is a large vertical grinding table, which rotates at a controlled speed Above the grinding table, there are several rollers that apply pressure onto the material being groundIndepth understanding of the working principle of vertical millsWith advanced technology and innovative design, this mill offers a unique approach to material processing The Working Principle of LUM Ultrafine Vertical Mill: 1 Material Feeding: The process begins with the feeding of raw materials into the mill The materials are typically fed into the mill from the top, where they enter a central feeding Understanding the working principle of lum ultrafine vertical millMPS vertical mill from Pfeiffer is the ideal allrounder Grinding of coal, petcoke, clay, limestone, quicklime, gypsum, Working principle MPS 5000 B mill for raw material grinding, Turkey Tracim, TurkeyCoal mill, gypsum mill, clay mill, etc Pfeiffer MPS mills
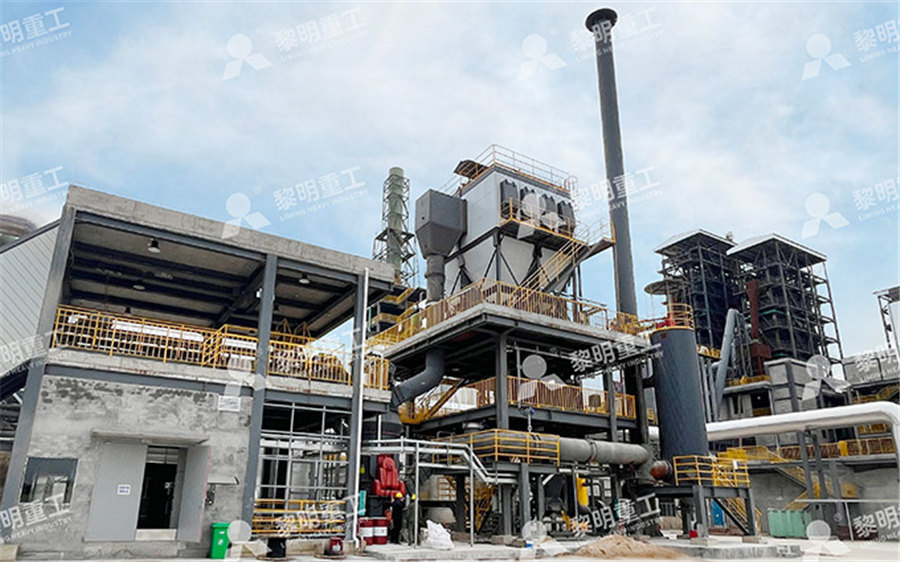
Rawmill Wikipedia
A raw mill is the equipment used to grind raw materials into "rawmix" during the manufacture of cement In principle, any material that can contribute any of these oxides can be used as a rawmix component occasionally called vertical spindle mills In a typical arrangement, I INTRODUCTION AND PRINCIPLES In this presentation we will discuss the principle of the Attritor and its applications The Attritor is a grinding mill containing internally agitated media It has been generically referred to as a “stirred ball mill” There are quite a few types of Attritors; we can categorize them as dry grindWe will discuss the principle of the Attritor and its applicationsThe cement raw materials (lime, silica and iron ore) enter the circuit through two apron feeders The raw materials are crushed in a hammer crusher to D 95 of 80mm The raw materials are mixed in a certain proportion and fed into a vertical roller mill (LOESCHE mill) The vertical roller mill grinds the marital to D 85 of 90µmModeling and simulation of vertical roller mill using population 2018 In this chapter an introduction of widely applied energyefficient grinding technologies in cement grinding and description of the operating principles of the related equip‐ ments and comparisons over each other in terms of grinding (PDF) CEMENT RAW MATERIAL GRINDING ;
.jpg)
Raw Mill – Raw Mill In Cement Plant AGICO Cement Raw Mill
AGICO Cement Vertical Mill AGICO Cement Ball Mill Cement Vertical Mill Grinding System Cement vertical mill, also called roller mill, is another raw mill commonly used in cement pared with the cement ball mill, it has a great difference in structure, grinding principle, process layout, automatic control, and energy consumption, which play an important role in the vertical mill Combined drive In this classifier mill, as shown in Figure 2b, the classifier wheel and rotor disc are mounted on one shaft and rotate at the same speed As a result, the mill is smaller, has a lower purchase cost, and requires less installed horsepower than the vertical mill However, the apFigure 1 Vertical air classifier How to operate an air classifier mill to meet your fine grinding goalsIn order to address this issue, the industry has been exploring new technologies and innovations to improve energy efficiency, reduce emissions, and lower production costs One such technology that has gained popularity in recent years is the vertical roller mill (VRM) Working Principle of Vertical Roller MillVertical Roller Mill in Cement Plant ball mills supplierWorking Principle Of Vertical Raw Mill The vertical raw material mill in the cement plant starts to run, the material enters the mill through the feed port on the upper side of the mill, and then falls in the center of the millstone The transmission drives the millstone to rotate, Raw Mill Feeder Designer Manufacturer
.jpg)
Analysis of vertical roller mill performance with changes in material
2022年5月31日 Mineral crushing is the main source of energy consumption in mineral processing According to statistics, this consumption accounts for about 35–50% of the total cost of the mine (Curry et al, 2014), or even higherIt may also account for 18% of the global electrical energy consumption (NapierMunn, 2015)More efficient crushing equipment needs to be Vertical cement mill has high grinding efficiency and low power consumption (20% – 30% less than ball mill) The granularity of the feeding material is larger(VRM cement mill is 80mm120mm, cement ball mill is less than or equal to 30mm)Vertical Cement Mill Cement Clinker Grinding Equipment in Raw mill is generally called cement raw mill, raw mill in cement plant, it refers to a common type of cement equipment in the cement plantIn the cement manufacturing process, raw mill in cement plant grind cement raw materials Raw mill Cement Plantvertical planetary gear reducer At the same time, raw material is dried by hot gas induced through the louver ring installed at outer side of the table Construction This Machine is a vertical type roller mill which performs drying grinding classification and pneumatic transportation simultaneously Material is fed at aVERTICAL ROLLER MILLS AMCL
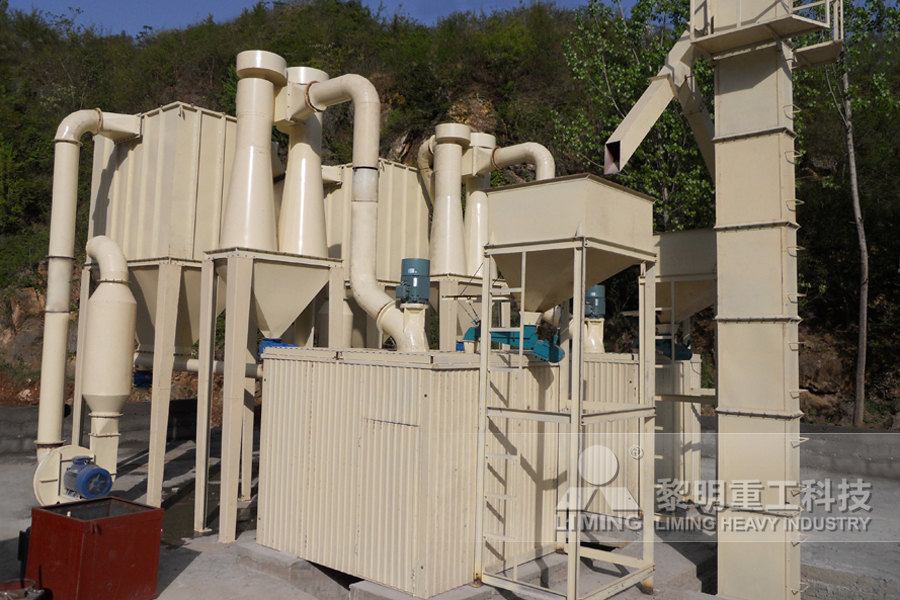
How does Vertical Roller Mill Work? ball mills supplier
Vertical roller mills (VRM) have become increasingly popular in recent years, as more cement producers look to increase their use of clinker substitute materials instead of importing clinker to meet localized rises in cement demand The demand for cement has grown rapidly in recent years, creating a need for a more efficient way to grind clinker and other raw materials used in The vertical grinding mill grinds materials by the principle of material layer grinding, with low energy consumption The power consumption of the grinding system is 20% to 30% lower than that of the ball mill, and the energy saving effect is more obvious as the moisture of the raw material increasesIndustrial Vertical Grinding Mill2017年9月11日 Due to the compact design and material transportation system of vertical roller mills (VRM), some important streams (total mill feed and discharge, dynamic separator feed and reject) remain in the (PDF) Performance Evaluation of Vertical Roller Mill in Cement Working principle Raw mills uses pressure and shear generated between the rollers and rotating table to crush and grind limestone, basalt and sandstone This temperature is used to drying material in vertical raw mill The hot exhaust gases enter the top section of the vertical, Cement Manufacturing Process INFINITY FOR CEMENT EQUIPMENT
.jpg)
Vertical Machining Center (VMC): Definition, Components, Uses, Working
Introduction Vertical Machining Center: Definition, Components, Uses, Working Principle, Advantages Disadvantages: – The vertical machining center has existed for quite a while and stays a fundamental part of modern CNC innovation and development For machining different industrial parts Vertical machining centers are quiet efficient2020年6月15日 Industrial hammer mills are employed in particle reduction applications for processing material Though machine designs vary, the basic hammer mill working principle remains the same—uniform size reduction of aggregate raw material is achieved by repeated blows with hammers mounted to a rotating shaftUnderstanding the Working Principle of Hammer Mills Prater• Cement raw material • Clinker / granulated slag • Industrial minerals, and a vertical roller mill (VRM) Principle of increasing performance by reducing the range of fluctuation RelauchLMmaster 7 250814 11:47 8 – LMmaster V 10PROCESS OPTIMISATION FOR LOESCHE GRINDING PLANTSIn addition, the raw material grinding process will be supported by a QMR² 48/24 For the 4,000 tons per day kiln line Shiva Cement Ltd contracted a quadropol® vertical roller mill for grinding pet coke with a QMK² 32/16 The same mill size QMK² 32/16 is running in Indonesia for years now, grinding and drying lignitequadropol® thyssenkrupp Polysius Grinding Technologies