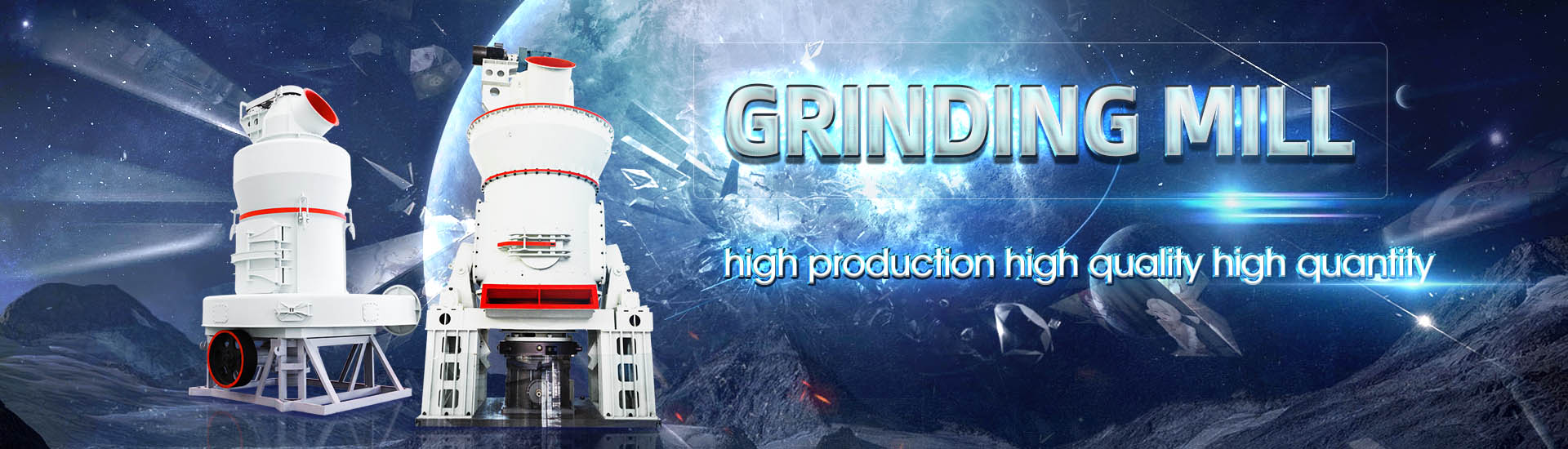
How much is the price of coal powder furnace ball mill steel ball
.jpg)
Steel production costs in blast furnaces Thunder Said
2021年11月25日 Our base case for steel production, via the blast furnace and basic oxygen furnace route, is at a marginal cost of $550/ton and with 24 tons of CO2 emitted per ton of steel This datafile breaks down the costs of steel The Global Steel Cost Tracker (GSCT) is an open data product that estimates the plantlevel steel production costs of blast furnace (BF), basic oxygen furnace (BOF) and electric arc furnace (EAF) production routes representing around 90% of global production The cost estimates are broken down by raw materials, energy, labour, and other costsGlobal Steel Cost Tracker TransitionZeroOperating cost including iron ore, coke, energy, labour, and services, is around 415 €/ton for a conventional steel mill, and the share of a reducing agent (coal) is around 84 €/ton (MayerUnit costs of different iron and steel production ResearchGate2013年1月1日 This chapter discusses the role of coal in iron and steel metallurgy The chapter first gives information about routes for steel manufacture, current levels of steel production and forecasts for the futureCoal use in iron and steel metallurgy ScienceDirect
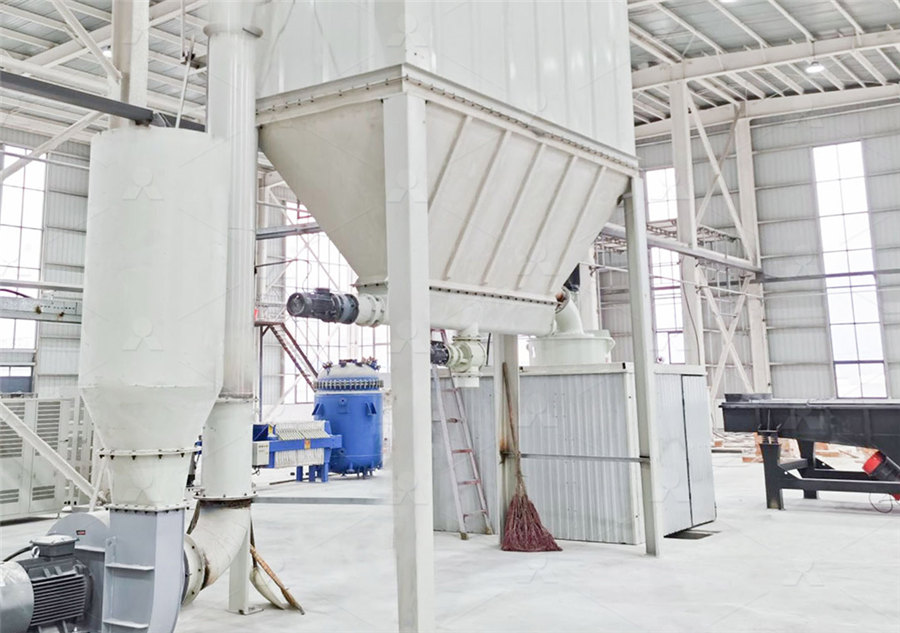
Fact sheet Energy use in the steel industry
Steel is produced via two main routes: the blast furnacebasic oxygen furnace (BFBOF) route and electric arc furnace (EAF) route Variations and combinations of production routes also exist The BFBOF route produces steel using raw materials such as iron ore, coal, limestone and steel scrap About 75% of steel is produced using the BFBOF route2024年2月19日 Let’s look at how to obtain a reasonable gradation of ball mill grinding body steel ball media and how to select ball mill steel balls Determine the steel ball gradation based on the particle size, hardness, grindability of the grinding materials, and the fineness requirements of Ball Mill Steel Balls: Quality And Gradation JXSC Mineral2021年4月21日 The technoeconomic comparison shows that capital cost and energy cost dominate the CO 2 avoidance cost (over 80%), making the cost per tonCO 2 sensitive to both fuel prices and interest rates If a zeroC electricity supply operates the system, the integrated process reduction should abate ∼57% CO 2 emissionLowcarbon production of iron and steel: Technology options, The Ball Tube Mill (BTM) is a cylindrical lowspeed grinding mill It consists of a steel barrel, lined with cast abrasionresistant liners and partially filled with hardened steel balls Coal and preheated primary air enter one or both ends of the mill from a crusher/dryer or feeder As the mill rotates, the balls cascade and pulverize the A Comparison of Three Types of Coal Pulverizers Babcock Power
.jpg)
Ball Mill an overview ScienceDirect Topics
Ball mills are commonly used for crushing and grinding the materials into an extremely fine form The ball mill contains a hollow cylindrical shell that rotates about its axis This cylinder is filled with balls that are made of stainless steel or rubber to the material contained in itSteel is produced via two main routes: the blast furnacebasic oxygen furnace (BFBOF) route and electric arc furnace (EAF) route Variations and combinations of production routes also exist The BFBOF route produces steel using raw materials such as iron ore, coal, limestone and steel scrap About 75% of steel is produced using the BFBOF routeFact sheet Energy use in the steel industry2010年3月1日 Evaluation of Four Coals for Blast Furnace Pulverized Coal Journal of Iron and Steel Research International 17(3):820; DOI:101016 were crushed by ball mill and sieved to 57125 pm 1 1Evaluation of Four Coals for Blast Furnace Pulverized 2020年8月12日 All content in this area was uploaded by Mehmet Tontu on Aug 13, 2020An investigation of performance characteristics and
.jpg)
How Is Coal Pulverized in a Ball Mill?
How does the ball mill work? The ball mill rotates around its axis, causing the steel balls to tumble and grind the material into a fine powder Why is coal pulverized in a ball mill? Coal is pulverized to increase its surface area, enabling it to be burned more efficiently It also ensures that the coal is uniformly sized, making it easier to viii) Pulvarised coal Injection: In this section coal is pulvarised to fine dust in mills and injected in the furnace Some of critical Equipments/ facilities in Blast Furnace Department are as follows: Sl No Area Major equipments / facilities 1 Blast Furnace RECOMMENDED GUIDELINE FOR IRON STEEL SECTOR MINISTRY OF STEEL2013年8月3日 In Grinding, selecting (calculate) the correct or optimum ball size that allows for the best and optimum/ideal or target grind size to be achieved by your ball mill is an important thing for a Mineral Processing Engineer AKA Metallurgist to do Often, the ball used in ball mills is oversize “just in case” Well, this safety factor can cost you much in recovery and/or mill liner Calculate and Select Ball Mill Ball Size for Optimum GrindingMild steel: Mild steel is iron containing up to about 025% of carbon The presence of the carbon makes the steel stronger and harder than pure iron The higher the percentage of carbon, the harder the steel becomes Mild steel is used for lots of things nails, wire, car bodies, ship building, girders and bridges amongst others233: Metallurgy of Iron and Steel Chemistry LibreTexts
.jpg)
Optimization and transformation of 300MV units steel ball coal mill
2019年11月7日 Comprehensive treatment,we should have a test on the 300 MV unit steel ball coal mill pulverizing systemAt the same time,analyze the main operating parameters before modificationTransform the Review of control and fault diagnosis methods applied to coal mills V Agrawal, PMV Subbarao, in Journal of Process Control, 2015 1 Introduction Coal mills or pulverizers play a very essential part in the coalfired power production system Coal mills grind the coal into fine powder, and the primary air entering the mill dries and drives the coal into the power plant furnace for Coal Mill an overview ScienceDirect Topics2015年6月19日 The basic parameters used in ball mill design (power calculations), rod mill or any tumbling mill sizing are; material to be ground, characteristics, Bond Work Index, bulk density, specific density, desired mill tonnage capacity DTPH, operating % solids or pulp density, feed size as F80 and maximum ‘chunk size’, product size as P80 and maximum and finally the type of Ball Mill Design/Power Calculation 911MetallurgistSteel decreased 588 Yuan/MT or 1497% since the beginning of 2024, according to trading on a contract for difference (CFD) that tracks the benchmark market for this commodity Steel values, historical data, forecasts and news updated on December of 2024Steel Price Chart Historical Data News
.jpg)
How to Process Coal into Pulverized Coal in 5 Steps?
2024年1月11日 That is more than 10 times the performance of the ball mill With a ball mill 1 To pulverize crushed coals in a ball mill, you start by feeding the mill with crushed coal Then the grinding media crushes and grinds the coal in the 2012年11月17日 20 131Fineness Fineness is an indicator of the quality of the pulverizer action Specifically, fineness is a measurement of the percentage of a coal sample that passes through a set of test sieves usually designated at 50, Coal mill pulverizer in thermal power plants PPT2 Heating: Steel ball billets are heated to an appropriate temperature in a continuous heating furnace; 3 Forging (rolling) into balls: The redhot billets are sent to steel ball mills, then rotates forward between two rolls with spiralshaped holes to be continuously rolled into balls Each steel ball mill can roll 60 to 360 balls per minute;Choose the Best Grinding Steel Balls for Your Ball Mill Fote the steel sector can lead to synergies with decarbonisation efforts in other sectors such as transport (hydrogen powered trains, trucks, cars, ships, airplanes), heating (eg replacing natural gas), and industrial processes such as ammonia produ ction • Higher steel prices would dampen the demand for steel in many other sectors of theThe potential of hydrogen for decarbonising steel production
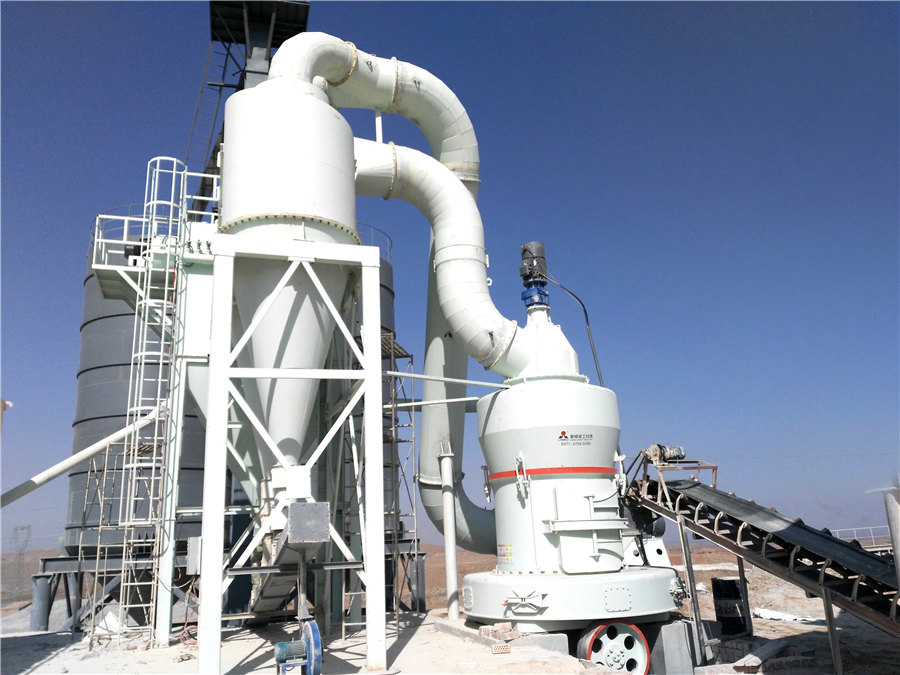
Calculate Ball Mill Grinding Capacity 911Metallurgist
2015年10月15日 Learn how to calculate the grinding capacity of your ball mill with 911 Metallurgist This guide provides essential formulas, insights, and tips to optimize your milling process and enhance production efficiencyTo convert raw coal into fine coal powder, coal grinding mills are essential Coal grinding mills are specialized equipment designed to break down coal into fine particles suitable for combustion The coal grinding process involves crushing and grinding coal into small particles, which are then heated to high temperatures in a furnace, producing steam that drives a turbine to generate What is a Coal Grinding Mill2021年11月25日 Steel scrap abounds after more than a century of industrialscale steel production However, it is still a large part of the cost of reusing steel In the US, steel scrap ranges from $ 160280 ($ 400450) per ton at the time of writingThe Costs Of Producing Steel With Electric Arc Furnaces2021年2月9日 Steel is typically made by either using a blast furnace or an electric arc furnace The blast furnace uses coal, ground up into a powder The coal is cooked and turned into “coke” The coke is then used to melt the iron ore The electric arc furnace is a newer process This way uses an electrical current to melt scrap steel and produce A Definitive Buying Steel Guide: An Overview of the Global Steel
.jpg)
Impact of PCI Coal Quality on Blast Furnace Operations
2003年1月1日 Ash behaviour in and near the raceway ( after Ichida and others, 2002) If you’re in the market for a ball mill, you’re likely looking for a reliable and highquality machine that can handle a wide range of materials and processesBall mills are used for grinding and mixing materials, and they can be found in a variety of industries, from mining and construction to pharmaceuticals and ceramicsA Comprehensive Guide to Finding the Best Ball Mill for Sale2021年4月21日 Japanese research suggests that pressed woody biomass can be used to prepare metallurgical coke after mixing with coal, achieving partial decarbonization 61 German research indicates that when using biomass coke powder to completely replace coal powder, the amount of carbon dioxide input in the blast furnace has been reduced by up to 45% 62 Lowcarbon production of iron and steel: Technology options, economic 2023年1月1日 Generally, a value of 55 represents an average grinding coal When switching to lower HGI coal, the capacity of the coal mill system should be assessed A key element in understanding a mill’s ability to handle lower HGI coals is Coal utilization in the cement and concrete industries
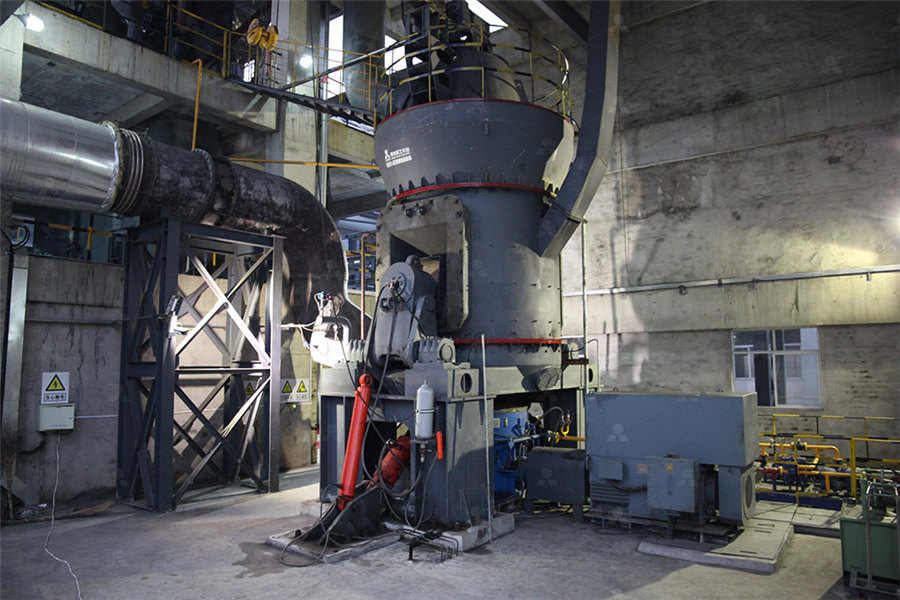
© IEA ETSAP Technology Brief I02 May 2010 etsap
processed in an electric arc furnace (EAF) to obtain steel Today most used steelmaking processes consist of a combination of a blast furnace and basic oxygen furnace Some SRI processes can produce steel directly Direct Fig 1 Iron and steel production technologies [2] IRON PRODUCTION Blast Furnace (pig iron) – Blast furnace (Figure 2) is aBall Mill Price Select 2024 high Ball Mill Price for Beneficiation Steel Slag Ball Mill Power Plant Overflow Type Ball Mill US$ 6800 / set 1 set (MOQ) Gold Mining Machine Professional Mining Ore Gold Copper Lead Manganese Iron Slag Sliver Aluminum Limestone Gypsum Powder Grinding Wet and Dry Ball Mill Price US$ 500010000 / Piece Ball Mill Price MadeinChina2024年2月19日 The ratio of steel balls in the ball mill depends on the effective length of your mill, whether it has a roller press, the size of the feed particles, the lining and structure used, the expected sieve residue fineness and ratio, how many chromium balls to operate, and the rotation speed How much and other factors make a comprehensive judgmentBall Mill Steel Balls: Quality And Gradation JXSC MineralThe coal is crushed and ground into a powder and then charged into an oven where it is heated to approximately 1800°F in the absence of oxygen The EAF is different from the blast furnace as it produces steel by using an electrical current to melt scrap steel, direct reduced iron, and/or pig iron, to produce molten steelSteel Production American Iron and Steel Institute
.jpg)
Steel production costs in blast furnaces Thunder Said Energy
Our base case for steel production, via the blast furnace and basic oxygen furnace route, is at a marginal cost of $550/ton and with 24 tons of CO2 emitted per ton of steel This datafile breaks down the costs of steel from blast furnaces, across a dozen input variables, such as capex, opex, iron ore prices, coke prices, coal prices, gas prices, electricity prices, limestone prices, labor Figure 2 shows the transition of the annual average price of steel scrap (H2) in the Tokyo area Driven by a decreased amount of steel scrap generation resulting from reduced automobile production, demolition of buildings, etc during the coronavirus crisis, as well as increased imports of steel scrap by China toward achievement of its “30–60 Targets,” the price of steel scrap Production and Technology of Iron and Steel in Japan during • Steel industry currently emits approximately 26 Gt direct CO2 emissions and 11 Gt indirect CO2 emissions from the power sector and combustion ofDecarbonizing Steel How the steel industry is cutting coalSteel is produced via two main routes: the blast furnacebasic oxygen furnace (BFBOF) route and electric arc furnace (EAF) route Variations and combinations of production routes also exist The BFBOF route produces steel using raw materials such as iron ore, coal, limestone and steel scrap About 75% of steel is produced using the BFBOF routeFact sheet Energy use in the steel industry
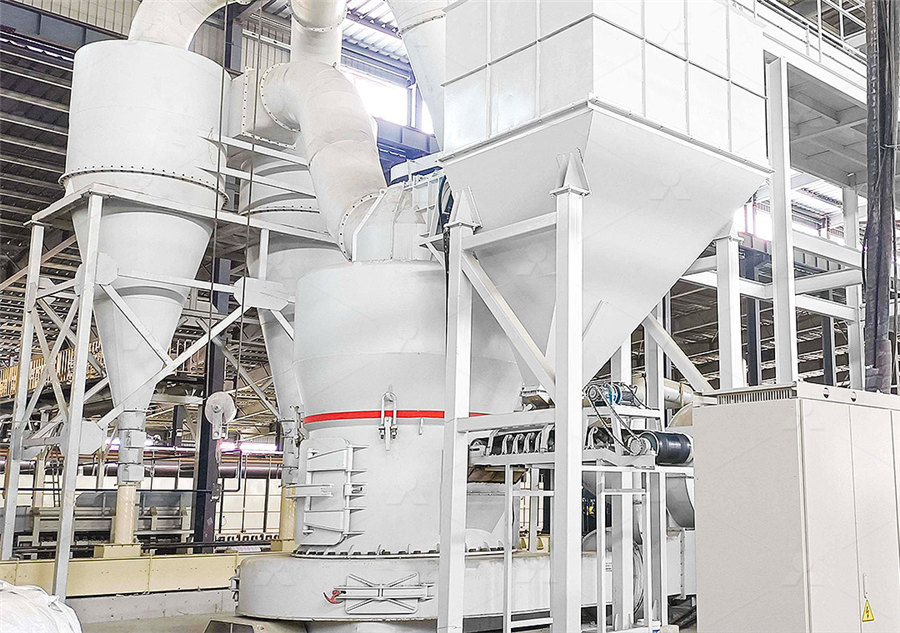
Evaluation of Four Coals for Blast Furnace Pulverized
2010年3月1日 Evaluation of Four Coals for Blast Furnace Pulverized Coal Journal of Iron and Steel Research International 17(3):820; DOI:101016 were crushed by ball mill and sieved to 57125 pm 1 12020年8月12日 All content in this area was uploaded by Mehmet Tontu on Aug 13, 2020An investigation of performance characteristics and How does the ball mill work? The ball mill rotates around its axis, causing the steel balls to tumble and grind the material into a fine powder Why is coal pulverized in a ball mill? Coal is pulverized to increase its surface area, enabling it to be burned more efficiently It also ensures that the coal is uniformly sized, making it easier to How Is Coal Pulverized in a Ball Mill?viii) Pulvarised coal Injection: In this section coal is pulvarised to fine dust in mills and injected in the furnace Some of critical Equipments/ facilities in Blast Furnace Department are as follows: Sl No Area Major equipments / facilities 1 Blast Furnace RECOMMENDED GUIDELINE FOR IRON STEEL SECTOR MINISTRY OF STEEL
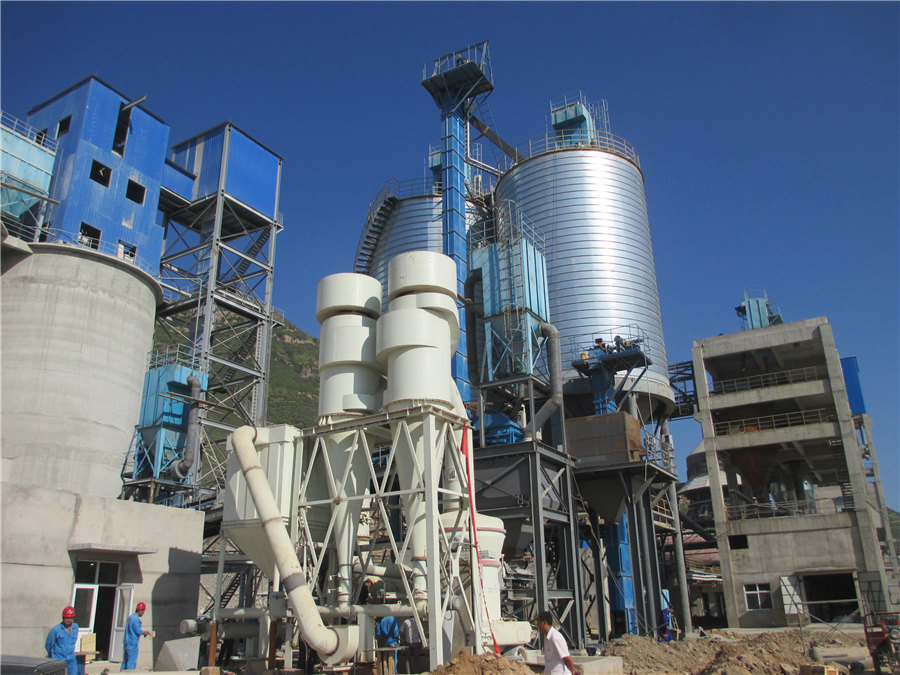
Calculate and Select Ball Mill Ball Size for Optimum Grinding
2013年8月3日 In Grinding, selecting (calculate) the correct or optimum ball size that allows for the best and optimum/ideal or target grind size to be achieved by your ball mill is an important thing for a Mineral Processing Engineer AKA Metallurgist to do Often, the ball used in ball mills is oversize “just in case” Well, this safety factor can cost you much in recovery and/or mill liner Mild steel: Mild steel is iron containing up to about 025% of carbon The presence of the carbon makes the steel stronger and harder than pure iron The higher the percentage of carbon, the harder the steel becomes Mild steel is used for lots of things nails, wire, car bodies, ship building, girders and bridges amongst others233: Metallurgy of Iron and Steel Chemistry LibreTexts2019年11月7日 Comprehensive treatment,we should have a test on the 300 MV unit steel ball coal mill pulverizing systemAt the same time,analyze the main operating parameters before modificationTransform the Optimization and transformation of 300MV units steel ball coal mill Review of control and fault diagnosis methods applied to coal mills V Agrawal, PMV Subbarao, in Journal of Process Control, 2015 1 Introduction Coal mills or pulverizers play a very essential part in the coalfired power production system Coal mills grind the coal into fine powder, and the primary air entering the mill dries and drives the coal into the power plant furnace for Coal Mill an overview ScienceDirect Topics
.jpg)
Ball Mill Design/Power Calculation 911Metallurgist
2015年6月19日 The basic parameters used in ball mill design (power calculations), rod mill or any tumbling mill sizing are; material to be ground, characteristics, Bond Work Index, bulk density, specific density, desired mill tonnage capacity DTPH, operating % solids or pulp density, feed size as F80 and maximum ‘chunk size’, product size as P80 and maximum and finally the type of