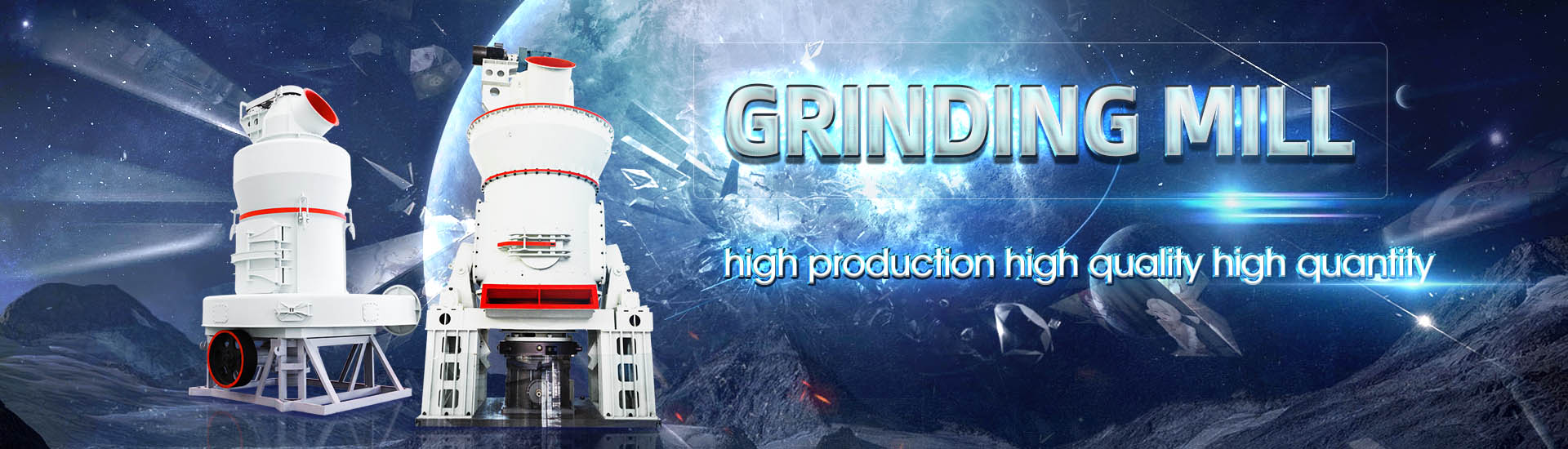
What is zinc concentrate processed from
.jpg)
Zinc Concentrate Comprehensive Guide and Applications MP
2024年10月1日 Zinc concentrate is a product derived from the beneficiation of zinccontaining ores, particularly sphalerite (zinc sulfide) It represents a critical step in the extraction of zinc The world primary zinc smelting industry employs five distinctive processes: Region Distribution of Mines Distribution of Smelters Europe (including Eastern Europe) 10% 27%The Extractive Metallurgy of Zinc AusIMMZinc smelting is the process of converting zinc concentrates (ores that contain zinc) into pure zinc The most common zinc concentrate processed is zinc sulfide, which is obtained by concentrating sphalerite using the froth flotation methodZinc: smelting, producing and classificationMetalpedia2023年1月25日 The principal ore of zinc used for its extraction is Zinc blend \(({\rm{ZnS}})\) As Zinc blend is a sulphide ore, the process used for its concentration is the Froth Floatation Extraction of Zinc: Process, Ores, Diagram EMBIBE
.jpg)
Zinc Mining and Processing: Everything you Need to
2014年3月7日 Eight percent of zinc is mined in open pits, with the remaining 12 percent being mined through both methods Once it’s removed from the earth, the concentrate is roasted at a temperature of 950 degrees Celsius, causing zinc, 2023年1月22日 The process is a variant of the conventional furnace technology, which allowed to sintering of the Zn and Pb concentrates at high temperatures to remove sulfur and other Zinc Extraction; In Brief Review from Past to Present2023年6月7日 The zinc smelting processes using zinc sulfide concentrate come in two types: hydrometallurgical zinc making and pyrometallurgical zinc making Hydrometallurgical zinc Zinc Metallurgy SpringerLink[111]: 7 The ore is finely ground, then put through froth flotation to separate minerals from gangue (on the property of hydrophobicity), to get a zinc sulfide ore concentrate [111]: 16 consisting of about 50% zinc, 32% sulfur, 13% iron, and Zinc Wikipedia
.jpg)
Zinc Mining and Processing: Everything you Need
2014年3月7日 Once it’s removed from the earth, the concentrate is roasted at a temperature of 950 degrees Celsius, causing zinc, sulfur and iron oxidization After the zinc and iron oxides are reduced to powder form and leached with 2023年7月20日 Leadzinc ore beneficiation is the process of treating ore containing lead and zinc to extract valuable metals such as lead and zinc This process typically involves several steps, includingWhat Is LeadZinc Ore Beneficiation Process? by Ch2016年3月21日 Pulp Densities Pulp densities indicate by means of a tabulation the percentages of solids (or liquidtosolid ratio) in a sample of pulp This figure is valuable in two ways—directly, because for each unit process and operation in milling the optimum pulp density must be established and maintained, and indirectly, because certain important tonnage calculations are Common Basic Formulas for Mineral Processing Calculations2005年2月13日 1 Zinc roasting process Zinc roasting chemistry The zinc roasting process is a process stage where in the presence of oxygen and high temperature (about 920950ºC) zinc sulphide concentrates react to zinc oxideThe zinc sulphide (ZnS, sphalerite) concentrates include also various amounts of other metal sulphidesWhat is the zinc roasting process? IFRF
.jpg)
Extraction of Zinc: Process, Ores, Diagram EMBIBE
2023年1月25日 Metal from Concentrated Ore Roasting: After the Froth Floatation method, the next step in the extraction of zinc is roastingRoasting is the process of heating a sulfide ore to a very high temperature in the presence of air This process is generally applied to sulfide mineralsDownload scientific diagram Flowchart of zinc concentrate production from publication: A global life cycle assessment for primary zinc production Purpose The purpose of this study was to Flowchart of zinc concentrate production ResearchGateZinc ores contain 515% zinc To concentrate the ore it is first crushed and then ground to enable optimal separation from the other minerals Typically, a zinc concentrate contains about 55% of zinc with some copper, lead and iron Zinc concentration is usually done at the mine site to keep transport costs to smelters as low as possibleProduction Zinc IndiaZinc is produced from ore mining, mineral processing, concentration, roasting, leaching, purification and electrolysis Table 14 describes the major findings and recommendations from the research conducted related to LCA of this metal Genderen et al analysed the cradletogate LCA of zinc concentrate and special highgrade zincZinc Ore an overview ScienceDirect Topics
.jpg)
Zinc concentrate chemeurope
Zinc concentrate is a highly hazardous product used in the production of zinc metal and zinc alloys, which is the result of a flotation process after the zinc ore has been mined and milled The zinc ore contains 115% zinc whereas the concentrate typically contains approximately 55% zinc, 65% iron and 32% sulfur together with other elements at much lower levels2018年5月17日 Zinc is extracted from this solution electrolytically to produce cathode zinc, which melted in furnaces to produce ingots Risdon is Australia's largest zinc refinery and also one of the largest in the worldLess than half of Zinc Geoscience AustraliaApproximately 450,000 tonnes of zinc concentrates are processed each year The concentrates are fed into the fluidised bed roaster and roasted with oxygen at 950°C The objective of the Roasting process is to convert zinc sulphide to acid soluble zinc oxide and sulphur dioxide gasThe Refining Process Sun MetalsPrimary lead was processed at smelterrefineries in Missouri and in Montana1 Zinc Ore Zinc is a shiny, bluishwhite metal Zinc metal is never found pure in nature Zinc minerals are generally associated with other metal minerals, the most common associations in ores being zinclead, leadzinc, zinccopper, copperzinc, zincsilver, or zinc onlyLead and Zinc Department of Energy
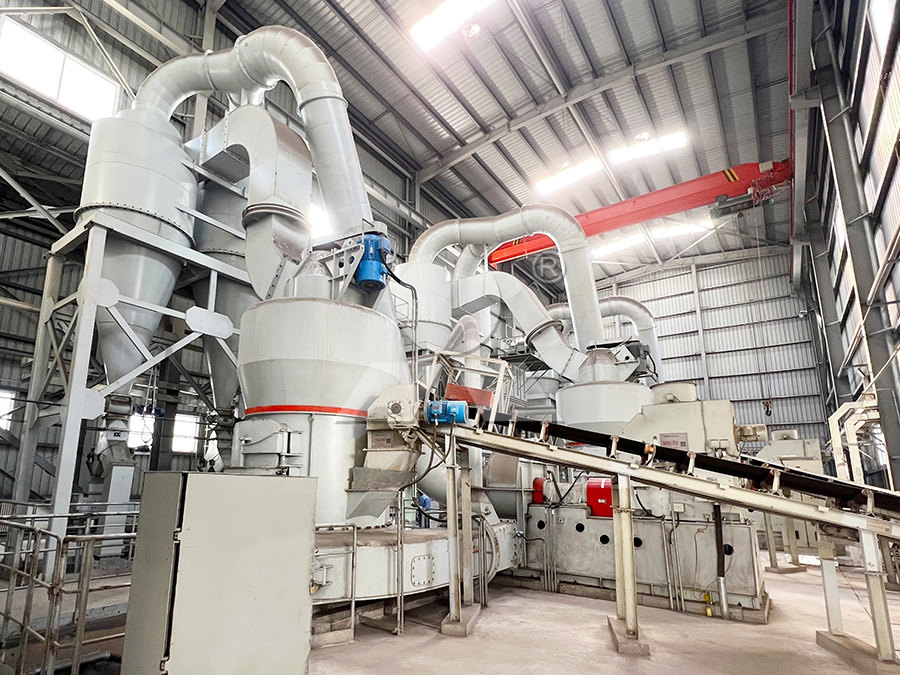
Effects of Various Precipitants on Iron Removal from a Zinc Concentrate
Autoclave leaching of zinc concentrate (Sphalerite) is an environmentally friendly process compared to roasting, which discharges pollutants into the atmosphere Due to the amount of iron in the final product, a study is proposed to evaluate different reagents for eliminating iron from the autoclave outcome, minimizing Zn losses The colloid formation, zinc losses, iron removal, Copper concentrates are typically processed via pyrometallurgyhydrometallurgy consisting of smelting, converting, firerefining and electrorefining (Fig 4 and Table 6)Saganoseki smelter and refinery in Japan, for example, processes copper concentrates from Chile and generates three products: (i) copper cathode (>9999% Cu), (ii) anode slime containing silver, gold, PGMs, Copper Concentrate an overview ScienceDirect TopicsZinc processing Ores, Refining, Alloying: Zinc ores are widely distributed throughout the world, although more than 40 percent of the world’s output originates in North America and Australia The common zinccontaining minerals are the zinc sulfide known as zinc blende or sphalerite (ZnS), a ferrous form of zinc blende known as marmatite [(ZnFe)S], and a zinc carbonate Zinc processing Ores, Refining, Alloying Britannica2020年1月25日 This zinc ore is commercially treated and processed through a hydrometallurgical and solvent extraction technology in two places flotation , thickening and filtration The result is a concentrate with 40% zinc content and 15% humidity, on average At Três Marias’ site, the concentrate is repulped with a solution Increase in Zinc Recovery from a Silicate Concentrate by Pre
.jpg)
Zinc Concentrate Stiloma
Typically, a zinc concentrate contains about 55% of zinc with some copper, lead and iron The most common zinc concentrate processed is zinc sulfide, which is obtained by concentrating sphalerite using the froth flotation method Preparation of zinc concentrate typically involves the removal of water from a zinc solutionZinc production increased over the years from an initial 37 000 t/a to the current 110 000 t/a zinc slab By the end of 1970, production of zinc from Waelz oxides decreased to virtually nothing, with zinc sulphide concentrates being introduced to make up the difference With the increased treatment of zinc sulphide concentrates, zinc recoveriesAn Overview of the Zincor ProcessA processed product and concentrates are now ready to transport offsite to be smelted into zinc and lead metals, used in a wide range of commercial and household products We place the lead concentrate in large, lined bulk bags packed into steel containers and truck it 800 kilometres to our lead smelter at Mount Isa MinesOur process Glencore3 Zinc Extraction; In Brief Review from Past to Present 55 Before the development of the Imperial Smelting Furnace (ISF), the production of Zn from ores begin with the selective separation of Zn concentrate (ZnS) by flotation methods, as it is often found in combination with PbS in ore The concentrates areZinc Extraction; In Brief Review from Past to Present Springer
.jpg)
Explain the extraction of zinc from its important ore
Reduction: Zinc oxide is mixed with powdered coke and heated to 1673 k in a fire clay retort in which Z n O is reduced to zinc metal Z n O + C 1673 K → Z n + C O; Purification: Zinc is purified by electrolytic refining In this process, impure zinc is anode and cathode is of pure thin sheet of zinc The electrolyte is Z n S O 4 solution Extraction of Zinc Zinc Mining The most commonly available ore used in the extraction of zinc is called zinc blende also known as zinc sulphide (ZnS) Historically extraction of zinc has been more difficult than the extraction of other metals because, at temperatures where metals such as iron typically begin to melt, zinc is a gasExtraction of Zinc Application Of Zinc Refining Process BYJU'S2024年11月3日 4 Zinc Concentrate: Zinc concentrate is a processed form of raw zinc ore, which is produced through mining, crushing, grinding, and beneficiation It is an essential raw material for various industries and plays a critical role in the global economyBulk Concentrates Shipping HandyBulk2016年5月31日 Recognized in India as a metal in the fourteenth century, zinc and zinc oxides have been used for centuries for a variety of applications Currently, over 13 × 10 6 MT of refined zinc are produced annually from ores, concentrates, and recycled materials (ILZSG 2016)The predominant application for zinc is in the galvanization process to protect steel by increasing A global life cycle assessment for primary zinc production
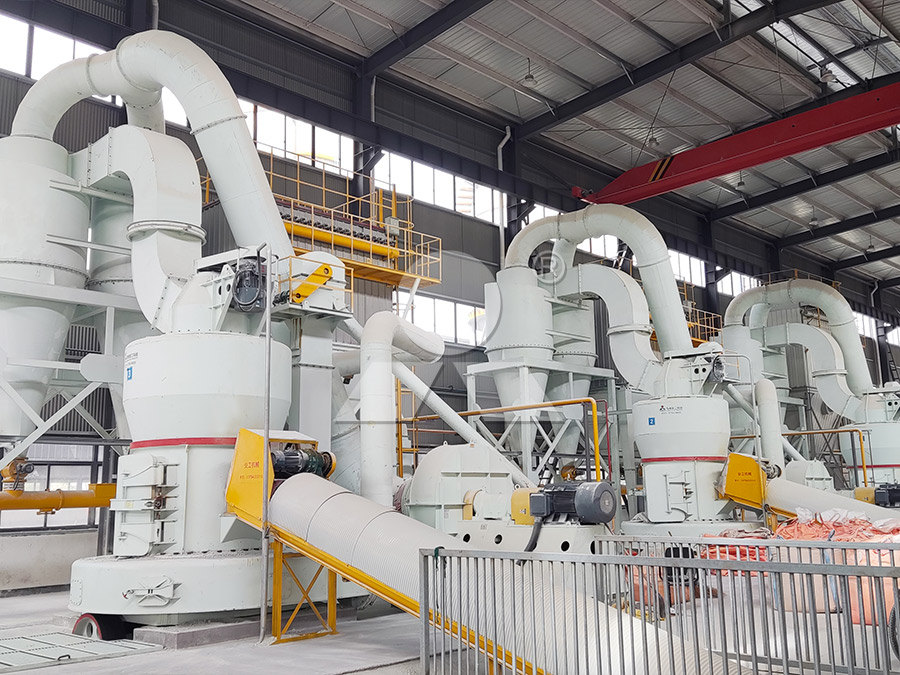
Zinc production Galvanizers Association
Zinc concentrates are then roasted or sintered to convert zinc sulphide to zinc oxide Zinc oxides are then processed in either pyrometallurgical, or more commonly, hydrometallurgical processes to produce zinc metal The most common products are High Grade Zinc (9995%) and Special High Grade Zinc (9999%)Zinc concentrates are roasted and then leached with sulfuric acid to dissolve their zinc content, leaving a residue that contains lead, silver, and gold—along with 5 to 10 percent of the zinc content of the concentrates This is processed by slag fuming, Silver processing Refining, Mining Uses Britannica2024年3月1日 Canadian smelters imported 604,026 tonnes of zinc in concentrates in 2022, a 25% increase compared to 484,058 tonnes in 2021 Zinc concentrates accounted for 67% of the value of Canada’s zinc imports Concentrates were imported mainly from the United States (55%), followed by Peru (12%), Australia (9%), Mexico (7%) and Bolivia (5%)Zinc facts Canada2010年5月1日 Recently a new application of the Outotec Zinc Concentrate Direct Leaching Process has been started up in PR ChinaThis process can case by case be combined with all the other zinc technologies Outotec atmospheric zinc concentrate direct leaching process
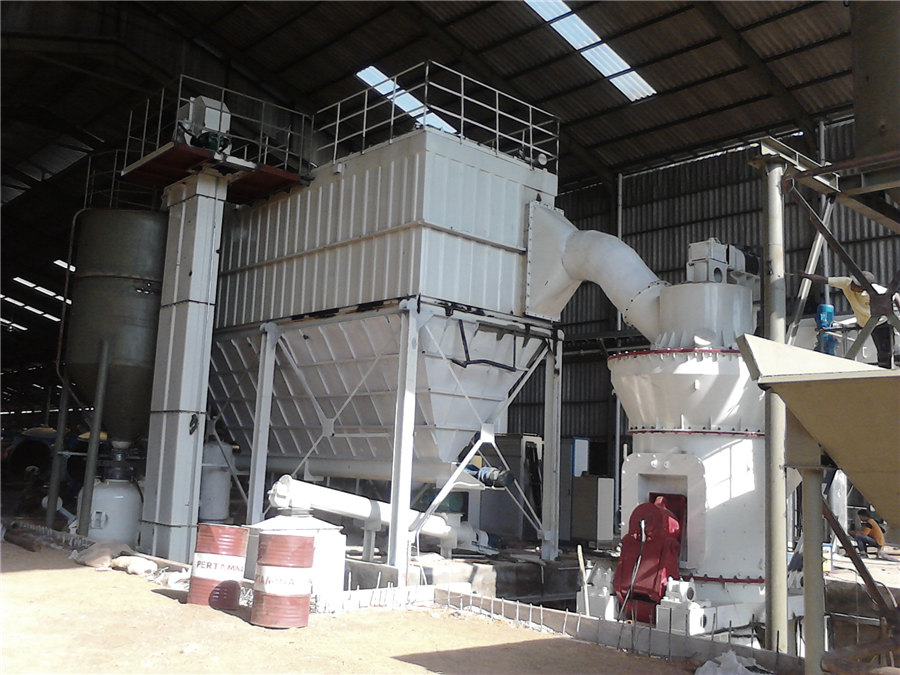
Oxidative Roasting of Low Grade Zinc Sulfide Concentrate from
deadroasted zinc concentrate to produce zinc oxide in the gas phase and partially reduced iron oxide compounds in the residue phase Thus, the process has a benefit of extracting zinc and iron from low grade zinc sulfide concentrate Many researches for the oxidative roasting of zinc sulfide concentrate were performed6–9) The oxidative [111]: 7 The ore is finely ground, then put through froth flotation to separate minerals from gangue (on the property of hydrophobicity), to get a zinc sulfide ore concentrate [111]: 16 consisting of about 50% zinc, 32% sulfur, 13% iron, and Zinc Wikipedia2014年3月7日 Once it’s removed from the earth, the concentrate is roasted at a temperature of 950 degrees Celsius, causing zinc, sulfur and iron oxidization After the zinc and iron oxides are reduced to powder form and leached with Zinc Mining and Processing: Everything you Need 2023年7月20日 Leadzinc ore beneficiation is the process of treating ore containing lead and zinc to extract valuable metals such as lead and zinc This process typically involves several steps, includingWhat Is LeadZinc Ore Beneficiation Process? by Ch
.jpg)
Common Basic Formulas for Mineral Processing Calculations
2016年3月21日 Pulp Densities Pulp densities indicate by means of a tabulation the percentages of solids (or liquidtosolid ratio) in a sample of pulp This figure is valuable in two ways—directly, because for each unit process and operation in milling the optimum pulp density must be established and maintained, and indirectly, because certain important tonnage calculations are 2005年2月13日 1 Zinc roasting process Zinc roasting chemistry The zinc roasting process is a process stage where in the presence of oxygen and high temperature (about 920950ºC) zinc sulphide concentrates react to zinc oxideThe zinc sulphide (ZnS, sphalerite) concentrates include also various amounts of other metal sulphidesWhat is the zinc roasting process? IFRF2023年1月25日 Metal from Concentrated Ore Roasting: After the Froth Floatation method, the next step in the extraction of zinc is roastingRoasting is the process of heating a sulfide ore to a very high temperature in the presence of air This process is generally applied to sulfide mineralsExtraction of Zinc: Process, Ores, Diagram EMBIBEDownload scientific diagram Flowchart of zinc concentrate production from publication: A global life cycle assessment for primary zinc production Purpose The purpose of this study was to Flowchart of zinc concentrate production ResearchGate
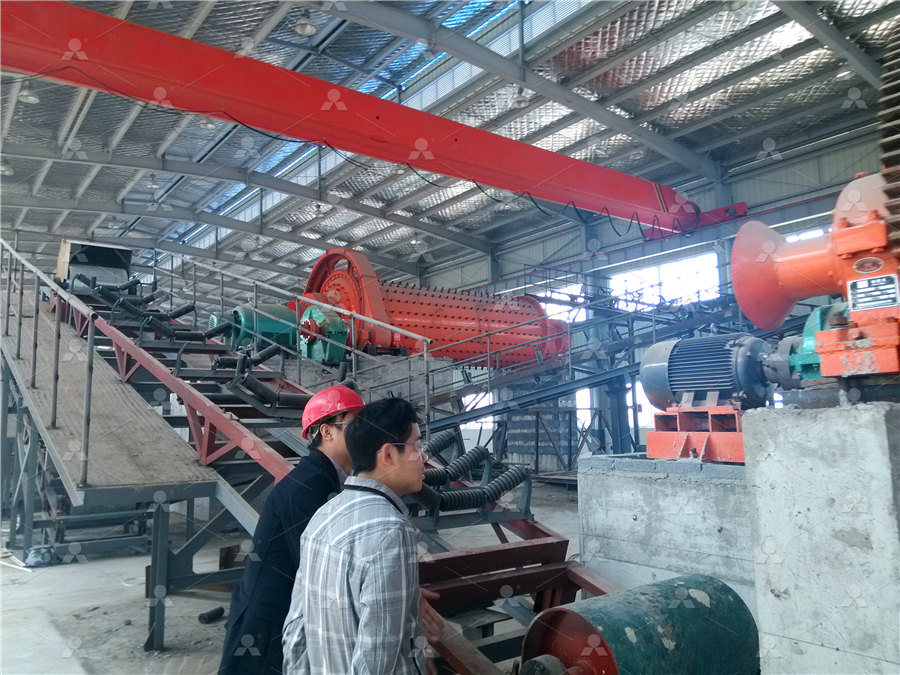
Production Zinc India
Zinc ores contain 515% zinc To concentrate the ore it is first crushed and then ground to enable optimal separation from the other minerals Typically, a zinc concentrate contains about 55% of zinc with some copper, lead and iron Zinc concentration is usually done at the mine site to keep transport costs to smelters as low as possibleZinc is produced from ore mining, mineral processing, concentration, roasting, leaching, purification and electrolysis Table 14 describes the major findings and recommendations from the research conducted related to LCA of this metal Genderen et al analysed the cradletogate LCA of zinc concentrate and special highgrade zincZinc Ore an overview ScienceDirect TopicsZinc concentrate is a highly hazardous product used in the production of zinc metal and zinc alloys, which is the result of a flotation process after the zinc ore has been mined and milled The zinc ore contains 115% zinc whereas the concentrate typically contains approximately 55% zinc, 65% iron and 32% sulfur together with other elements at much lower levelsZinc concentrate chemeurope